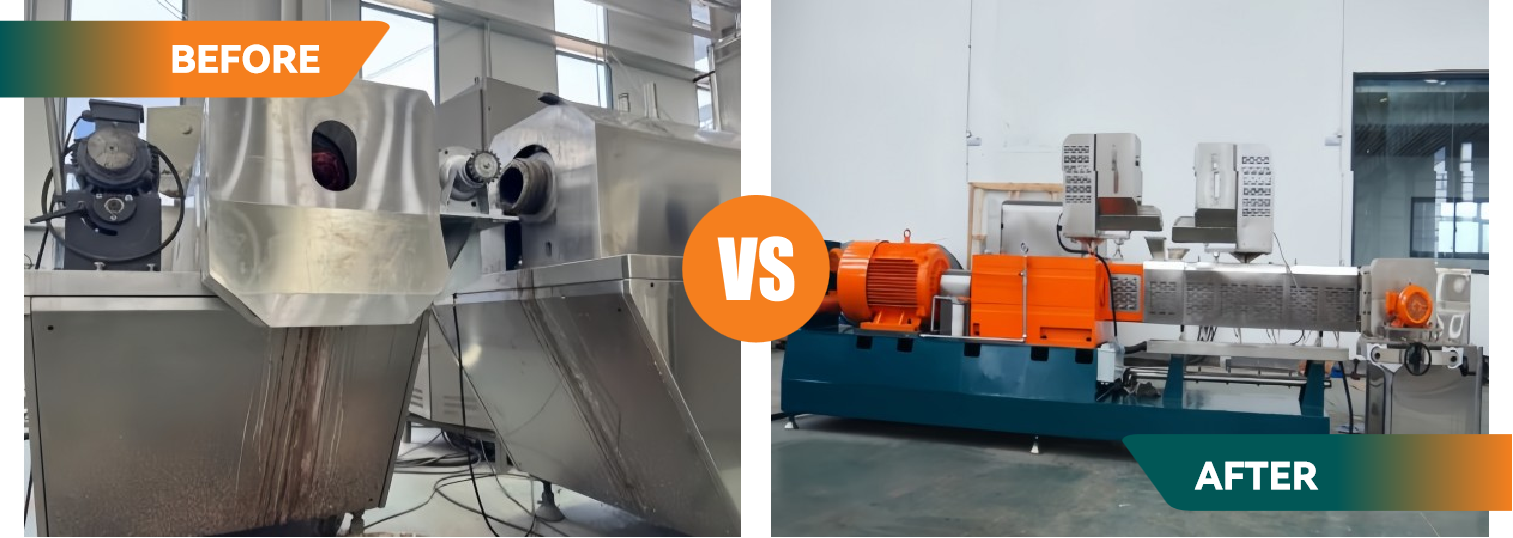
Pet food manufacturers often face significant productivity losses, increased maintenance costs, and even product safety risks due to aging or underperforming equipment. Over time, wear and tear, obsolete controls, and inconsistent output can jeopardize not just operational efficiency but also regulatory compliance. This leads many companies to ask: when is the right time to replace pet food processing machinery? Fortunately, there are clear technical, financial, and quality-driven indicators that help determine the ideal timing for equipment replacement. This article will walk you through each one in depth.
Pet food equipment should be replaced when it no longer meets production capacity, shows signs of mechanical wear affecting output quality, causes frequent downtime, fails to comply with updated food safety regulations, or becomes too costly to maintain versus replacing with modern automated alternatives. Typical replacement intervals range from 8–15 years, depending on usage intensity and maintenance.
If you're unsure whether it's time to upgrade your pet food extruder, dryer, mixer, or packaging line, continue reading. This guide will help you assess equipment performance based on productivity, compliance, maintenance records, and energy efficiency—saving you money and protecting your brand reputation.
Pet food machinery generally lasts more than 20 years if maintained properly.False
While some components may last decades, the average lifecycle of industrial pet food equipment is 8–15 years due to evolving technology, hygiene standards, and production needs.
Key Indicators for Replacing Pet Food Equipment
📉 1. Declining Output Efficiency or Capacity
Over time, even high-quality machinery begins to experience reduced output due to mechanical fatigue, aging control systems, or structural degradation. If your line is no longer reaching its rated capacity despite proper maintenance, it’s time to evaluate replacement.
Original Capacity (kg/h) | Current Output (kg/h) | Deviation | Comment |
---|---|---|---|
1000 | 750 | -25% | May indicate wear or motor issues |
500 | 400 | -20% | Replace nozzles or check extruder screws |
800 | 580 | -27.5% | Likely performance loss due to age |
If consistent deviation exceeds 15–20%, it becomes uneconomical to continue repairs.
🧯 2. Frequent Breakdowns and Rising Maintenance Costs
Maintenance logs are among the clearest indicators. If maintenance costs exceed 10% of the machine’s initial value per year, or if unplanned downtime exceeds 5% of production time, replacement is typically more cost-effective than repair.
Year | Maintenance Cost (USD) | Unplanned Downtime (%) | Comment |
---|---|---|---|
1 | \$1,200 | 1% | Normal for a new system |
5 | \$4,500 | 3% | Needs preventive measures |
9 | \$12,000 | 8% | Replacement recommended |
Breakdowns also create cascading delays across entire production cycles and disrupt consistency in pet food quality.
🏭 3. Incompatibility with Modern Safety & Hygiene Standards
If your pet food equipment can no longer meet current GMP, FDA, EU CE, or HACCP hygiene standards, then replacement becomes a regulatory necessity.
Examples of non-compliance include:
- Manual cleaning instead of CIP (Clean-in-Place)
- Open conveyors lacking contamination shields
- Legacy systems with untraceable control logs
Upgrading to stainless steel components, full enclosure designs, and PLC-integrated traceability can solve these issues while future-proofing your facility.
⚡ 4. High Energy Consumption and Lack of Automation
Older pet food equipment tends to be inefficient compared to modern energy-saving systems and servo-controlled machines.
Machine | Year Built | Energy Efficiency | Automation Level | Recommendation |
---|---|---|---|---|
Twin-Screw Extruder | 2005 | Low | Manual | Replace immediately |
Batch Dryer | 2010 | Medium | Semi-Auto | Consider retrofit |
Robotic Packer | 2020 | High | Fully Automated | No replacement needed |
Switching to newer models can yield 15–30% energy savings annually and reduce labor dependency significantly.
📊 5. Obsolete Components and Lack of Spare Parts
If replacement parts for motors, gearboxes, or PLCs are discontinued, your downtime risks multiply. In many cases, local suppliers may no longer support legacy brands.
Checklist for obsolete equipment:
- Outdated PLC or relay control logic
- Non-touchscreen HMI
- No remote monitoring or diagnostics
- Unavailable bearings, shafts, or motors
Upgrading to an Industry 4.0-ready solution ensures continued support and diagnostic efficiency.
🔧 6. Product Diversification Requirements
Market trends in pet food (e.g., grain-free, high-meat, or novel protein recipes) require flexibility in extrusion, coating, and shaping technology.
If your machine cannot accommodate variable recipes, die shapes, or production settings, it limits your ability to launch new SKUs.
Requirement | Legacy Machine | Modern Machine |
---|---|---|
Adjustable moisture range | ❌ | ✅ |
Quick die change system | ❌ | ✅ |
Multi-protein formulation | ❌ | ✅ |
🧾 7. Economic Lifecycle and Depreciation Review
A proper ROI analysis should consider:
- Annual maintenance
- Downtime costs
- Utility usage
- Labor hours saved by automation
- Market demand growth
Most food equipment is depreciated over 7–10 years. After this point, replacement may provide tax advantages and unlock operational scalability.
When to Upgrade Specific Pet Food Machines?
Equipment Type | Average Lifespan | Key Replacement Signs |
---|---|---|
Twin-Screw Extruder | 8–12 years | Capacity drop, mechanical wear, outdated PLC |
Conveyor Systems | 10–15 years | Belt slippage, loud noise, hygiene risks |
Coating Drums | 6–10 years | Uneven coating, rust, hard-to-clean zones |
Dryers (Electric/Gas) | 10–15 years | Temperature fluctuation, high energy use |
Mixers | 10–12 years | Uneven mix, bearing wear |
Packaging Systems | 8–12 years | Slower throughput, missed seals, print misalignments |
Best Practices Before Replacing
- Perform an equipment audit: Use a standardized checklist to assess each machine’s condition.
- Get ROI analysis from vendors: Darin Machinery offers free lifecycle ROI simulation reports.
- Consider phased replacement: Start with the bottleneck area—typically the extruder or dryer.
- Evaluate retrofit kits: In some cases, an automation upgrade or energy module retrofit may delay full replacement.
- Check resale or trade-in value: Some manufacturers offer buy-back programs.
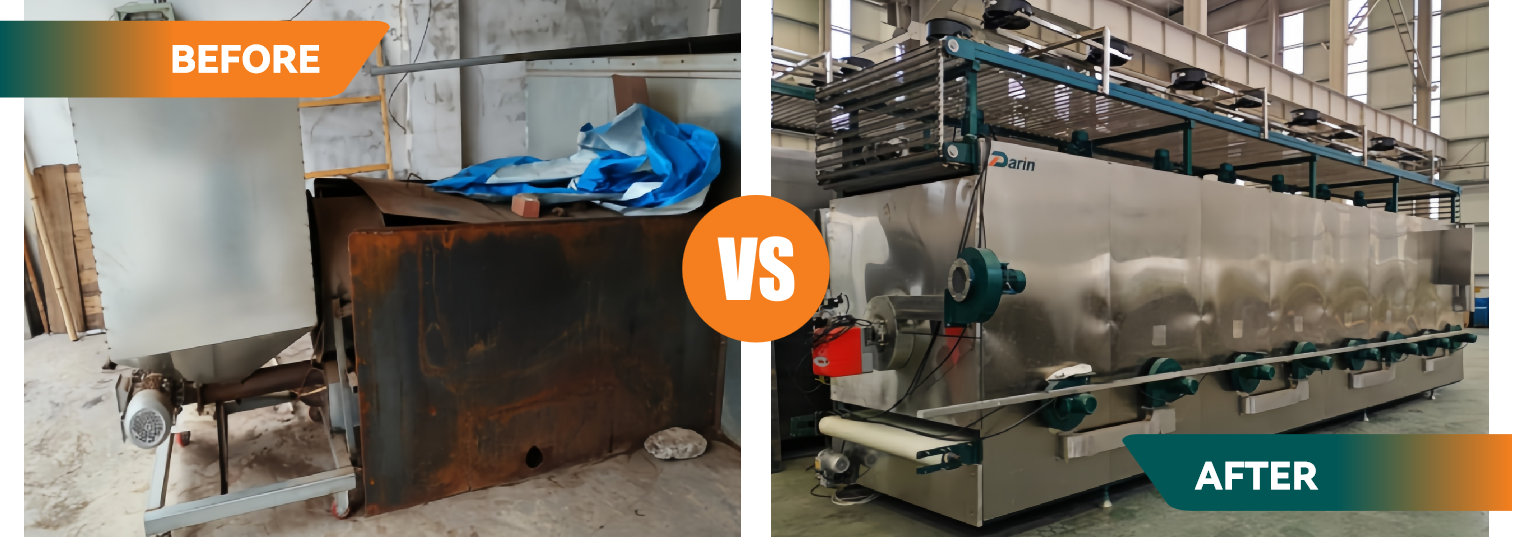
Final Thoughts
Pet food machinery doesn’t have to “break down” to justify replacement. More often, it's the slow creep of inefficiency, rising cost, or limited flexibility that makes continued use uneconomical. Regular equipment health checks, paired with smart capital planning, ensure you’re never caught off guard by a sudden failure or regulatory compliance issue.
📞 Ready to Upgrade Your Pet Food Equipment?
At Darin Machinery, we offer intelligent, fully automated, hygienic pet food production lines with global support and decades of experience. Whether you need a complete production line replacement or just a twin-screw extruder upgrade, our engineers can assess your current setup and recommend the most cost-effective solution.
👉 Contact Darin Machinery today for a free lifecycle assessment and equipment modernization proposal. Let us help you stay ahead in the competitive pet food market!
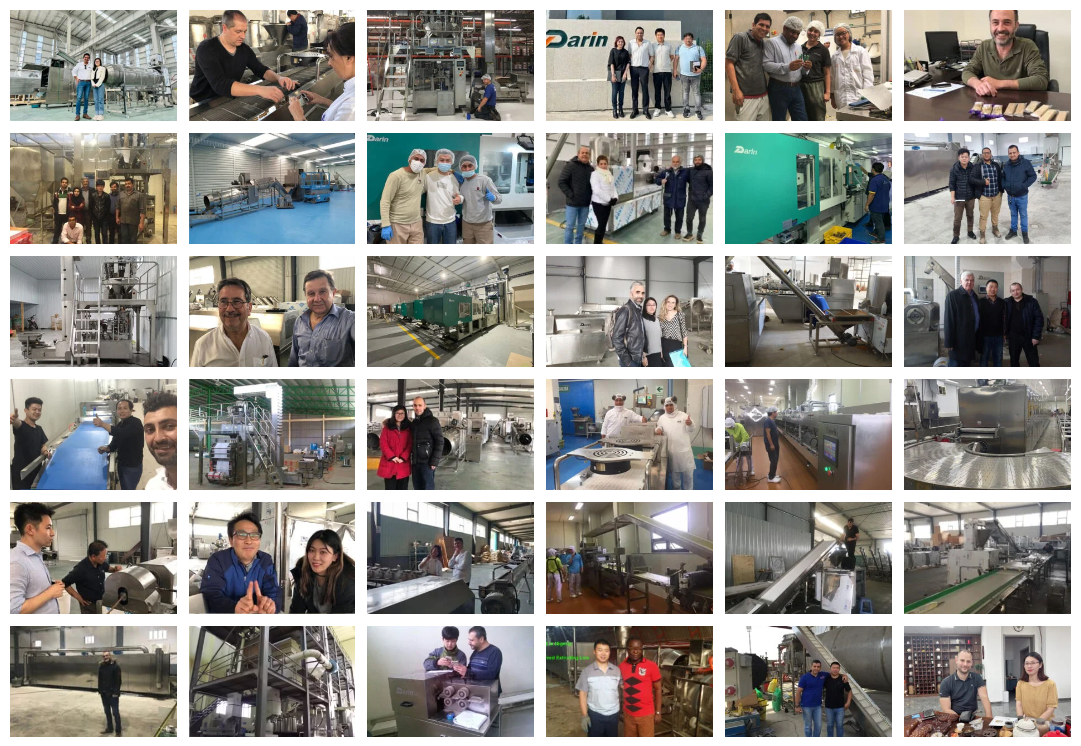