Remember that time your pet eagerly wagged their tail over a meal? There's a fascinating process behind creating those pet foods.
A pet food extruder is a machine used to process raw ingredients into pet food products by applying heat, pressure, and mechanical shear to mix and shape the food. This process helps to enhance nutritional quality and palatability, making it a crucial tool for manufacturers.
I remember watching my dog gobble up his kibble with such enthusiasm, and it made me curious. Just like us humans have chefs and kitchens, our pets have these amazing machines called extruders that whip up their meals. Understanding how an extruder works isn't just about the nuts and bolts; it's about ensuring our furry friends get nutritious, delicious food every day. Let's take a closer look at what makes these machines so pivotal in creating high-quality pet foods.
Pet food extruders use heat to shape pet food.True
Heat is applied to raw ingredients in extruders to mix and shape food.
Extruders reduce the nutritional quality of pet food.False
Extruders enhance nutritional quality by improving digestibility and palatability.
How Does a Pet Food Extruder Work?
Ever looked at your pet’s kibble and wondered how it gets that perfect shape and texture?
A pet food extruder functions by mixing, cooking, and shaping ingredients under controlled conditions. This process uses heat and pressure to create the desired texture and form, ensuring the food meets nutritional and safety standards.
Components of a Pet Food Extruder
Imagine this: you’re watching your favorite cooking show, but instead of a chef, there's a sleek machine handling all the action. The pet food extruder is like that—an all-in-one marvel. It starts with a Feeder, which might remind you of pouring flour into a mixer when baking cookies. It introduces the raw materials, setting the stage for the magic.
Then, the Preconditioner steps in, similar to how I would let dough rise before baking. It moistens and partially cooks those ingredients to get them ready for the spotlight. Next comes the Extrusion Barrel, where the real transformation happens—mixing, cooking, and shaping our concoction into something extraordinary.
The Die is next, and it's akin to pressing cookie cutters into dough, determining the final shape. Finally, the Cutter slices each piece with precision. Each component works seamlessly together, like a well-coordinated dance, ensuring consistent quality.
Component | Function |
---|---|
Feeder | Introduces raw materials |
Preconditioner | Moistens and pre-cooks |
Extrusion Barrel | Cooks and shapes |
Die | Shapes product |
Cutter | Slices to size |
The Extrusion Process
Mixing and Conditioning
Have you ever watched a cooking show where everything just seems to fall into place? That's how I imagine the mixing and conditioning stage. Ingredients like meat, grains, and vitamins are mixed with steam and water. The preconditioner is like a sous-chef, ensuring everything reaches the right moisture content for perfect extrusion.
Cooking and Forming
Picture this: inside the extrusion barrel1, ingredients face high temperatures and pressure—a bit like a pressure cooker on steroids. This process does it all—gelatinizes starches, denatures proteins, and kicks out harmful microorganisms.
Shaping and Cutting
As the mixture pushes through the die, it feels almost magical. It's like watching pasta get its shape in an Italian kitchen. A cutter then slices everything into those perfectly uniform pieces.
Drying and Coating
After all that hard work, products are dried to just the right moisture level. And just like adding a final glaze to pastries, a coating of fats or flavors is applied to enhance taste and shelf life.
Quality Control Measures
I can't stress enough how crucial quality control is in this whole process. Just like you'd check cookies for doneness in an oven, manufacturers ensure each batch of pet food meets rigorous standards such as temperature checks, moisture levels, ingredient consistency—all scrutinized carefully.
Moreover, adherence to global standards2 like CE and ISO certifications ensures that what goes into our pets' bowls is safe and nutritious. This attention to detail makes me proud of every batch we produce.
The die shapes the final pet food product.True
The die is responsible for shaping the extruded mixture into kibble or treats.
The cutter preconditions the ingredients in a pet food extruder.False
The cutter slices the shaped product; preconditioning is done by the preconditioner.
What Are the Key Components of a Pet Food Extruder?
Ever wondered what makes your pet's kibble so perfectly shaped and delicious? It's all about the magic happening inside a pet food extruder.
The key components of a pet food extruder include the feeder, extruder barrel, screws, die, cutter, and control system. Each plays a crucial role in processing ingredients into consistent, quality pet food products.
The Feeder: Gateway to the Extrusion Process
Imagine the feeder as the unsung hero of the pet food world. I remember the first time I saw it in action—it was like watching a well-oiled machine hum in perfect harmony. The feeder ensures that raw materials are introduced at a steady pace, which is crucial for creating that consistent crunch or chewiness our pets love. These feeders often come with advanced technologies3 that optimize how ingredients are added, making the entire extrusion process smoother.
Extruder Barrel and Screws: The Heart of the Extrusion
The barrel and screws are where the magic truly happens. Picture this: inside the extruder, these components work tirelessly, mixing and heating the ingredients under high pressure. It's akin to kneading dough but on an industrial scale. I once watched in fascination as the screws turned, transforming a jumble of raw materials into a smooth, pliable mixture. Innovations in screw design4 have made this process even more efficient, maximizing heat transfer and cutting down on energy use.
Component | Function |
---|---|
Feeder | Controls input flow |
Barrel | Houses mixing screws |
Screws | Mix and heat materials |
The Die: Shaping the Final Product
The die is like the artistic touch at the end of a long process. By adjusting its specifications, manufacturers can create different shapes and sizes—from classic kibble to fun, novel treats. I’ve seen how die customization5 allows for creativity in product design, catering to both pets' and their owners' preferences.
Cutter: Ensuring Precision
After all that hard work in the extruder, precision is key. The cutter comes in to ensure that each piece is just right. I recall watching a cutter at work; it was like an orchestra conductor, slicing each piece with immaculate precision. This is crucial not only for packaging but also for keeping pets happy with consistent treats. With advances in cutting technology6, there's even more room for creativity in product design.
Control System: The Brain of the Operation
The control system is the mastermind behind it all, ensuring everything runs smoothly. I’ve seen how these sophisticated systems regulate temperature, pressure, and speed to perfection. Modern control systems are like the brains of our operations—they enhance operational efficiency7 and make sure each batch meets high-quality standards. Upgrading these systems can drastically reduce downtime and improve product consistency.
Understanding these components is like having a secret recipe for success in pet food production. They not only help in optimizing production but also inspire innovation, enabling us to meet evolving consumer demands.
The feeder controls the input flow in a pet food extruder.True
The feeder ensures a steady flow rate, critical for uniform product quality.
The cutter is responsible for mixing ingredients in the extruder.False
The cutter slices the product post-extrusion; screws mix ingredients.
Why Are Pet Food Extruders Important for Nutritional Quality?
Ever wondered how your pet's meal transforms from raw ingredients into a delicious, nutritious dish?
Pet food extruders play a critical role in ensuring nutritional quality by improving digestibility, nutrient retention, and palatability. They help create balanced diets that cater to pets' dietary needs.
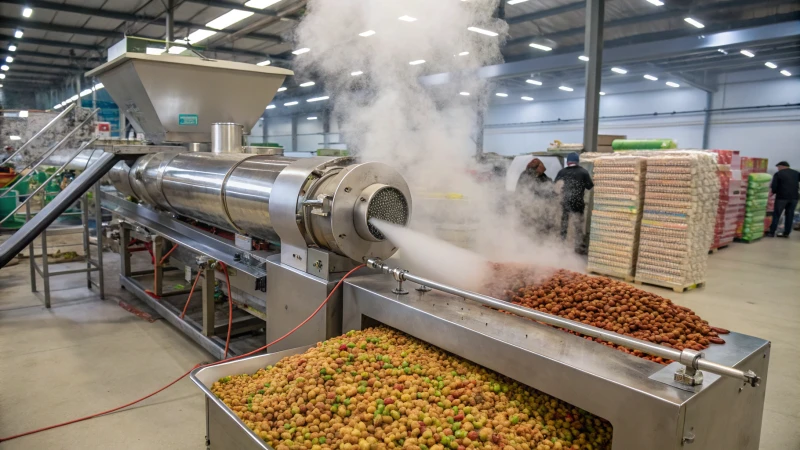
Understanding Pet Food Extrusion
I remember the first time I peeked behind the scenes of pet food production—it was fascinating! The process, called extrusion, felt like discovering the magic trick behind making food both tasty and healthy for our furry friends. It's all about using heat, pressure, and mechanical force to turn raw ingredients into something that looks and smells delightful. But there's more to it than just shaping and cooking. It's about enhancing the nutritional quality, too. Imagine breaking down complex carbs and proteins into forms that your pet's tummy can easily handle—that's what extrusion does.
Nutrient Retention and Digestibility
When I first learned about how extrusion helps retain nutrients, it was like finding out my favorite smoothie kept all its vitamins even after blending. The process keeps those essential nutrients—like vitamins and amino acids—intact, much better than traditional cooking methods. It's reassuring to know that when my pet chomps down on their meal, they’re getting all the goodness they need. Studies show that nutrient retention is significantly higher with extrusion, which makes me feel like I’m doing the right thing for my pet’s health. For further details on nutrient retention benefits8, explore recent research findings.
Enhancing Palatability and Texture
Just like us, pets are picky eaters! The ability to create textures and flavors that entice even the fussiest eaters is a game-changer. The first time I saw my dog wagging his tail at mealtime because of these enhancements, I knew we were onto something great. Extruders allow manufacturers to add fats, flavors, and coatings that make every bite irresistible.
Benefits of Extrusion | Description |
---|---|
Improved Digestibility | Breaks down complex nutrients for easier absorption |
Nutrient Retention | Preserves vitamins and amino acids |
Enhanced Palatability | Creates appealing textures and flavors |
Customizing Nutritional Profiles
One of the coolest things I've found about using extruders is the ability to customize meals. We can tweak formulations to meet specific dietary needs—whether it's for allergies or weight management. It’s like having a personal chef for your pet who knows exactly what they need! This ensures our pets not only enjoy their meals but thrive on them. Learn more about how customized pet diets9 are developed using extrusion technology.
Environmental Considerations
It's not just about the food; it's also about being mindful of our planet. I admit, learning that extrusion is energy-intensive made me pause. However, ongoing innovations are promising—they aim to make the process more eco-friendly. I'm optimistic about the future as researchers continue exploring sustainable extrusion practices10 to reduce its environmental impact.
Extrusion enhances pet food nutrient retention.True
Extrusion minimizes nutrient loss, preserving vitamins and amino acids.
Extruders reduce the environmental impact of pet food production.False
Extrusion is energy-intensive, potentially increasing carbon emissions.
What Types of Pet Foods Can Be Made with Extruders?
Ever wondered how your pet's kibble or favorite treat is made? Join me as we dive into the fascinating world of extruders and their role in crafting diverse pet foods.
Extruders can produce various pet foods, including dry kibble, semi-moist foods, and specialty treats like dental chews and jerky. This versatility supports diverse pet dietary needs and preferences.
Dry Kibble: A Staple in Pet Nutrition
When I first stepped into the world of pet food manufacturing, I was amazed by the role extruders play in creating dry kibble. It's a staple in pet nutrition, offering not just convenience but a well-balanced diet for our furry friends. Watching the ingredients mix and transform into those crunchy pellets made me realize how this process enhances digestibility and nutrient retention. It's like magic! And let's be honest, who doesn't appreciate a pet food with a long shelf life?
Semi-Moist Foods: A Tasty Alternative
I remember experimenting with different moisture levels to create semi-moist foods that pets would love. These foods sit perfectly between dry kibble and canned options, offering a texture that's irresistible to many pets. The extrusion process allows me to control moisture precisely, resulting in products that are not only tasty but also packed with nutrients. It’s incredibly satisfying to see pets enjoy these delicious meals.
Specialty Treats: From Dental Chews to Jerky
Creating specialty treats like dental chews and jerky is where things get really interesting. I once spent days refining the textures of dental chews to ensure they helped reduce plaque and maintain oral health. Extruders allow for incredible creativity, incorporating various ingredients and textures into these treats. And crafting jerky treats? It's all about providing a high-protein snack that pets can't resist.
Custom and Nutritional Formulations
One of the most exciting aspects of using extruders is developing custom formulations. Whether it's grain-free recipes or allergen-sensitive diets, extruders give me the flexibility to tailor products to specific dietary needs. And with the growing demand for functional pet foods11 that offer joint support or digestive aids, I find myself constantly innovating to meet these evolving needs.
Innovations in Extruded Pet Foods
Extrusion technology is always evolving, and it's thrilling to be part of this journey. From raw food alternatives to eco-friendly packaging solutions, I’m continually exploring new ways to push the boundaries. By tweaking processing parameters, I can craft unique products that align with emerging trends12 in pet nutrition, ensuring our furry companions get the best.
Pet Food Type | Key Characteristics |
---|---|
Dry Kibble | Long shelf life, convenient, balanced nutrition |
Semi-Moist Foods | Soft texture, enhanced palatability |
Dental Chews | Oral health benefits, varied textures |
Jerky Treats | High-protein content, chewy texture |
Custom Formulations | Tailored nutrition, allergen-sensitive recipes |
Extruders produce only dry kibble for pets.False
Extruders can make dry kibble, semi-moist foods, and specialty treats.
Semi-moist pet foods have more moisture than dry kibble.True
Semi-moist foods contain higher moisture levels than dry kibble.
Who Are the Leading Manufacturers of Pet Food Extruders?
When I first ventured into the world of pet food manufacturing, I quickly learned that the right extruder could make all the difference. Let's dive into the top manufacturers that set the standard for quality and innovation.
Leading manufacturers of pet food extruders include Bühler, Clextral, Diamond America, and Wenger. These companies are renowned for their advanced technology, extensive product lines, and commitment to quality standards in the pet food industry.
Key Players in the Pet Food Extrusion Market
Reflecting on my journey into pet food manufacturing, it was crucial to find partners who understood both the art and science of making quality pet food. That's when I discovered some of the industry's top innovators.
Bühler Group instantly stood out with their reputation for innovative solutions13. Their extruders are like the Swiss army knives of the industry—versatile and reliable, capable of crafting a variety of pet foods with precision.
Clextral was another name that kept cropping up. Renowned for their continuous innovation14, they seem to always be one step ahead, tailoring their extrusion technology to the ever-evolving needs of our sector. Their machines epitomize efficiency and adaptability.
Manufacturer | Special Features | Location |
---|---|---|
Bühler | Advanced technology, global reach | Switzerland |
Clextral | Continuous innovation, high efficiency | France |
Diamond America | Customizable extruders, user-friendly designs | United States |
Wenger | Pioneers in extrusion technology, extensive support | United States |
Diamond America impressed me with their focus on customization. Their extruders are built with the user in mind—straightforward yet sophisticated, with robust technical support15 to back it all up.
Wenger Manufacturing has been a beacon in extrusion technology for years. They offer comprehensive solutions that encompass everything from installation to after-sales services16, ensuring your operations run smoothly and efficiently.
Factors Contributing to Leadership
Innovation and Technology
One thing I've learned is that innovation is key. Leading manufacturers pour resources into R&D to push the boundaries of what's possible. Take Bühler, for instance—their dedication to sustainability and precision engineering is evident in every product they launch.
Global Reach and Support
A global presence is not just about prestige; it's about offering localized support. Companies like Clextral and Wenger have made it their mission to be wherever you need them, ensuring their machinery meets international standards, which is crucial when operating across multiple markets.
Versatility and Customization
In this business, no two production lines are alike. That's where companies like Diamond America excel. Their ability to tailor extruders to specific needs or scales makes them a go-to choice for manufacturers seeking flexibility and efficiency.
By understanding these key players and their strengths, I could make informed decisions about selecting equipment that best fit my production needs. To learn more about their latest technologies or hear customer testimonials firsthand, exploring their websites was incredibly enlightening.
Choosing the right extruder manufacturer has had a profound impact on my production quality and efficiency. Whether it's Bühler's groundbreaking innovation or Wenger's extensive support network, each company brings something unique and valuable to the table.
Bühler Group is based in Switzerland.True
Bühler is a Swiss company known for its global reach and advanced technology.
Clextral extruders are known for low efficiency.False
Clextral is recognized for high efficiency and continuous innovation in extruders.
Conclusion
A pet food extruder processes raw ingredients into nutritious pet food using heat, pressure, and mechanical shear, enhancing quality and palatability for various pet diets.
Discover how extrusion barrels mix and cook pet food ingredients efficiently. ↩
Learn about the importance of CE and ISO certifications in ensuring pet food quality. ↩
Discover how cutting-edge feeder technologies can optimize input and enhance the extrusion process. ↩
Learn about screw design improvements that increase efficiency and reduce energy consumption. ↩
Explore how customizing dies can lead to diverse product shapes and sizes. ↩
Understand new cutting technologies that offer flexibility in product design. ↩
Find out how modern control systems enhance production efficiency and product quality. ↩
Explore how extrusion technology enhances nutrient retention in pet foods, ensuring pets receive optimal nutrition. ↩
Discover how extrusion technology allows for the creation of specialized pet diets tailored to unique nutritional needs. ↩
Learn about innovations in extrusion that aim to reduce environmental impact and promote sustainability. ↩
Discover how functional pet foods can address specific health issues like joint pain or digestive problems in pets. ↩
Stay updated on the latest trends shaping the pet food industry, including sustainability and novel ingredients. ↩
Explore Bühler’s innovations in pet food extrusion technology to understand their market-leading position. ↩
Learn about Clextral’s continuous innovations that drive efficiency and versatility in pet food manufacturing. ↩
Discover how Diamond America's customizable extruders cater to specific production needs. ↩
Understand Wenger’s comprehensive after-sales support that ensures operational efficiency. ↩