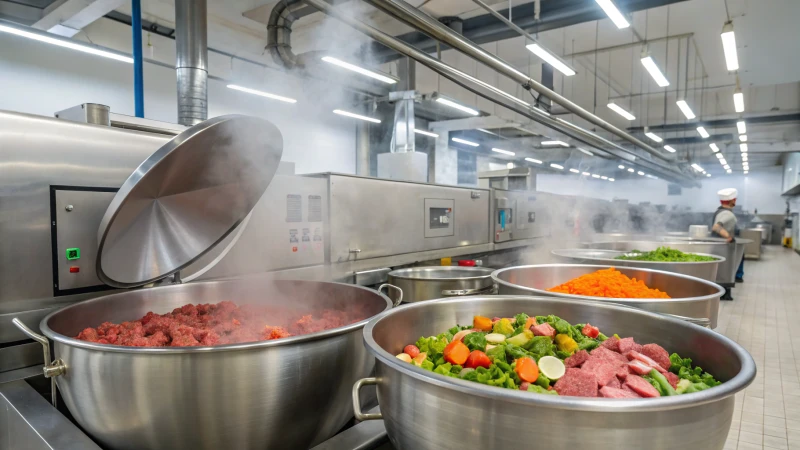
Nguyên liệu thô để sản xuất thức ăn cho thú cưng là gì?
Making homemade dry dog food is a rewarding way to ensure your pet receives balanced nutrition
Darin® Pet Food Extruder is a cutting-edge solution designed for producing high-quality pet food with superior consistency, nutritional value, and palatability. Engineered with advanced extrusion technology, it efficiently processes diverse ingredients into appealing and healthy pet food products. Ideal for manufacturers aiming for enhanced productivity and product excellence, the Darin® Extruder ensures reliable operation, flexibility, and cost-effectiveness.
■ All machinery is certified with European CE Approval & ISO 9001 Certification.
■ Run in 90+ countries including USA, Germany, Japan, Italy, UAE, Australia etc.
■ Machinery Supplier of General Mills, Kelloggs, Melinda, Bill Gates foundation & Wanpi.
Maximize production efficiency with the Darin® Pet Food Extruder. Advanced automation, precision extrusion, multi-shape customization, and energy-saving technology ensure consistent, high-quality pet food. Ideal for dog, cat, and aquatic feed. Contact us now for a production upgrade!
Darin Machinery provides a full-cycle, one-stop production equipment solution for all types of pet food and pet snacks, including production lines for pet dry food, pet wet food, pet semi-moist food, pet freeze-dried food, and pet raw food, as well as common pet treats production processing equipment such as pet biscuits, pet jerky, pet dental chews, pet rawhide chews, and pet training treats.
Produces low-moisture (<12%) kibble such as dog and cat food.
Produces soft pellets or treats with 15–30% moisture content.
Produces high-moisture (>50%) products, typically for canned or pouched packaging.
Specially designed for unique shapes and textures, such as dental chews or training treats.
Capacity < 500 kg/h. Suitable for small businesses, startups, or R&D purposes.
Capacity of 500–2,000 kg/h. Ideal for regional manufacturers.
Capacity > 2,000 kg/h. Designed for large-scale pet food brands and export-oriented factories.
Darin® Pet Food Production Line supports diverse applications, including dog food, cat food, fish feed, and exotic animal feed. Its advanced customization and automation ensure versatile production to meet diverse market demands. Contact us today to expand your pet food offerings!
Consult Our Experts !Let’s work together to build your next best-seller.
Suitable for small-sized kibble and feline-specific nutritional needs.
Tailored for rabbits, guinea pigs, and other small mammals with high-fiber dietary requirements.
Darin® Pet food extruder is a state-of-the-art solution designed to streamline pet food manufacturing. Equipped with cutting-edge automation technology, precision extrusion, and customizable mold systems, this production line ensures consistent output of high-quality pet food products for dogs, cats, and aquatic animals.
Darin® Pet food extruder allows producers to diversify their product range, attract new customers, and increase market share. By leveraging its modular design, companies can easily upgrade or expand capacity as demand grows. For pet food manufacturers seeking precision, speed, and adaptability, this is the ultimate production solution.
Contact us today for specifications, customization options, and expert support to optimize your pet food production line!
When purchasing the pet food extruder, you might be interested in the following Technical Parameters.
Model | Capacity | Power | Dimension |
---|---|---|---|
DR-65 | 120-150kg/h | 80kw | 18*5*3m |
DR-70 | 200-300kg/h | 90kw | 20*5*3m |
DR-85 | 500-600kg/h | 150kw | 30*5*4m |
DR-90 | 800-1000kg/h | 200kw | 35*5*5m |
DR-95 | 2000kg/h | 250kw | 40*10*16m |
DR-120 | 3000kg/h | 350kw | 50*10*20m |
DR-135 | 5000kg/h | 450kw | 60*10*24m |
Choosing the Darin pet food extruder means investing in performance, reliability, and innovation—all backed by years of experience in food processing machinery. Here’s why leading pet food and snack manufacturers worldwide choose Darin:
Motors from Darin Machinery are sourced from WEG with a 3-year worldwide guarantee or Siemens.Enjoy a reliable global after-sales service system.
Electric parts are from ABB or Schneider, easy to find replacments at local market.
PLC and touch screens from Siemens, Germany, are used by Darin Machinery to ensure easier operation and reduced labor requirements.
When faults occur, Darin Machinery’s touch screens display relevant information, making it easy to diagnose and resolve issues quickly.
Darin Machinery control cabinets are equipped with 24V safe voltage, ensuring operator safety even electrical leakage occurred.
Darin Machinery includes three types of protectors over-current, over-voltage, over-heat to ensure machine and operator safety.
Servo follows the cutting size more accurately, rolling cutting can cut products with strong toughness, such as cowhide products, and the cutter does not cut the conveyor belt.
The end of the conveyor belt has a small turning radius, which makes material transportation smoother.
Its components are arranged for quick disassembly, ensuring efficient upkeep and hygienic operation.
All cover bodies, mesh belts, and parts in contact with materials at Darin Machinery are made of food-grade stainless steel 304, providing superior durability and safety.
Keeping automation, quality and service in mind, always based on the diverse needs of customers, Darin will be dedicated to providing clients with satified product and full life after sales service.
Darin machines run in more than 70 countries including USA, UEA, Germany, Japan, Italy, Spain, Holland, Australia, Brazil, Mexico, Indonesia, Thailand, Canada etc.
Keeping automation, quality and service in mind, always based on the diverse needs ofcustomers, Darin will be dedicated to providing clients with satified product and full life after salesservice.
When purchasing the Pet Food Extruder, you might be interested in the following questions.
The key technical specifications of a pet food extruder vary based on the model and capacity. Below are the main parameters to consider:
Small-scale extruders: 100-300 kg/h
Medium-scale extruders: 300-1000 kg/h
Large-scale extruders: 1000-5000 kg/h or more
Main motor power: 22 kW to 250 kW, depending on the production capacity
Heating power: 5 kW to 50 kW (depends on barrel heating zones)
Total installed power: 30 kW to 300 kW
Range: 1 mm to 15 mm
Adjustable die molds allow for various pellet sizes suitable for small pets to large breeds
Compatible with corn, wheat, soybean meal, meat meal, fish meal, bone meal, vitamins, and additives
Moisture content: Usually 20-30% before extrusion and 8-12% after drying
Single-screw or twin-screw options available
Twin-screw models provide better mixing and cooking uniformity
Barrel heating system: Electric heaters or steam heating
Temperature range: 100-200°C, adjustable for different recipes
Rotary cutter with variable speed to adjust pellet length
Stainless steel blades for high durability
PLC touch screen control for automation
Adjustable speed and temperature settings
Small models: ~2.5m × 1.2m × 1.8m
Large models: ~5m × 2m × 2.5m
Would you like a quote or additional details on a specific model?
Darin Machinery advanced pet food extruder can create a wide variety of pet foods. Here’s a detailed and comprehensive breakdown:
Dog Food
Puppy food
Adult dog food
Senior dog food
Breed-specific dog food
Dental care food
Weight management dog food
Cat Food
Kitten food
Adult cat food
Senior cat food
Hairball control food
Urinary tract care food
Breed-specific cat food
Small Animal Food
Rabbit food
Hamster food
Guinea pig food
Rat and mouse food
Bird Food
Parrot pellets
Finch and canary pellets
Pigeon feed pellets
Fish Feed
Floating fish feed (aquarium fish, pond fish)
Sinking fish feed (catfish, shrimp)
Soft and chewy treats
Training snacks and rewards
Moist, shaped pet food for enhanced palatability and digestibility
Dental care treats (teeth cleaning and gum massage)
Functional snacks (supplemented with vitamins, minerals, probiotics)
Jerky-style pet snacks (meat-based)
Vegetarian pet treats
Filled snacks (co-extruded snacks with soft filling)
Extruded pet chews (rawhide alternatives)
Diet-specific extruded pet food:
Hypoallergenic pet foods (limited-ingredient diets)
Grain-free diets
Gluten-free diets
Organic or natural pet food
Low-calorie, weight control formulations
Therapeutic foods (prescription diet foods recommended by veterinarians):
Kidney health diets
Liver care diets
Diabetic diets
Digestive sensitivity foods
Shaped extruded foods with customized shapes, sizes, textures:
Bone-shaped treats
Fish-shaped pellets
Paw-shaped snacks
Colored extruded products (using natural colorants)
Functional extruded products with additives (such as joint care ingredients like glucosamine, omega fatty acids for skin and coat)
A high-quality pet food extrusion line typically includes capabilities such as:
Single-screw and Twin-screw Extruders:
Single-screw extruders for simpler formulations.
Twin-screw extruders offering superior mixing, cooking, and shaping, ideal for complex, functional, and high-quality products.
Versatile Control Systems:
Precise control of temperature, moisture, pressure, and cooking time for consistent quality and texture.
Post-Extrusion Processing:
Drying and cooling equipment
Flavor coating and oil/fat spraying systems
Packaging and weighing systems
The extruder is capable of processing various raw materials including:
Meat and poultry meals (chicken, beef, lamb, fish meal)
Plant proteins (soybean meal, pea protein, chickpea protein)
Cereals (corn, wheat, rice, barley, oats)
Vegetables and fruits (carrots, sweet potatoes, pumpkin, apple, blueberry)
Nutritional supplements (vitamins, minerals, probiotics, prebiotics)
In summary, the pet food extruders produced by Darin Machinery or similar top-tier manufacturers are highly versatile, capable of producing a comprehensive range of pet food products tailored to diverse market needs, dietary preferences, and health requirements.
The pet food extruder is compatible with a wide range of raw materials, depending on the type of pet food being produced. Here are the main categories of raw materials that can be used:
Corn flour
Rice flour
Wheat flour
Potato starch
Cassava/Tapioca starch
Sorghum flour
Meat meal (chicken meal, beef meal, fish meal, lamb meal, etc.)
Bone meal
Blood meal
Soy protein concentrate
Textured vegetable protein (TVP)
Defatted soybean meal
Pea protein
Insect meal (black soldier fly larvae, cricket meal, etc.)
Animal fats (poultry fat, tallow, fish oil, etc.)
Vegetable oils (soybean oil, palm oil, sunflower oil, flaxseed oil, etc.)
Beet pulp
Cellulose fiber
Rice bran
Oat fiber
Pea fiber
Lecithin
Gums (xanthan gum, guar gum)
Gelatin
Egg powder
Vitamin premix (A, D, E, K, B-complex, etc.)
Mineral premix (calcium, phosphorus, magnesium, zinc, etc.)
Flavor enhancers (yeast extract, hydrolyzed protein, etc.)
Probiotics & Prebiotics
Antioxidants (tocopherols, ascorbic acid)
The extruder can process these materials in different formulations to create dry kibble, semi-moist pet food, or specialized diets. Let me know if you need recommendations for a specific pet food formulation!
Dry Kibble:
Wet Food:
Treats & Biscuits:
Specialty Diets (e.g., Raw or Freeze-Dried):
Yes, a modern pet food production line is highly adaptable for producing a wide range of shapes, sizes, and formulations for different types of pet food products, from kibble and wet food to treats and biscuits. This customization ensures that the production line can meet the specific needs of your target market, whether you're focused on a single product type or a broad variety of formulations.
Would you like more information on a specific customization option or assistance with configuring a line for your product needs?
Yes, the Darin pet food extruder supports different shapes and sizes of pet food. The shape of the pet food is determined by the extruder die and cutting system, which can be easily changed to produce a variety of shapes and sizes.
Changing the Die Mold
The extruder die is a metal plate with specific hole patterns that determine the shape of the pet food.
By replacing the die with a different design, you can produce various shapes such as round, bone-shaped, heart-shaped, star, triangle, or square pellets.
Die changes are simple and take minimal time, allowing flexibility in production.
Adjusting the Cutting Blade
The rotary cutter located at the die exit determines the length of the pet food.
Adjusting the cutting speed and blade position changes the final size (length) of the kibble.
For softer, semi-moist pet food, a different blade type may be used to ensure clean cuts without crumbling.
Control Through PLC System
Some Darin extruders come with a PLC control system that allows fine-tuning of pressure, temperature, and feed rate, ensuring optimal shaping.
Standard die molds for dogs, cats, fish, and small animals are available.
Custom die designs can be manufactured based on specific brand requirements.
Special twin-screw extruders can create co-extruded pet food (two-color or filled treats).
Would you like recommendations on specific shapes for your production needs?
The processing temperature range for the Darin pet food extruder typically falls between 100°C to 180°C (212°F to 356°F), depending on the formulation, moisture content, and product type. Here's how the temperature impacts the process and nutrient retention:
Process Stage | Typical Temperature (°C) |
---|---|
Pre-conditioning | 70–100°C |
Extrusion (Cooking Zone) | 100–180°C |
Die/Exit Zone | 90–130°C |
Proteins:
Moderate to high temperatures (above 120°C) denature proteins, improving digestibility.
Excessive heat (>160°C) may cause Maillard reactions, reducing amino acid (lysine) bioavailability.
Vitamins:
Heat-sensitive vitamins (A, C, E, B-complex) can degrade during high-temperature extrusion.
These are often added post-extrusion via coating or spraying to preserve potency.
Starches:
High temperature and pressure gelatinize starches, which enhances energy availability and digestibility.
Fats and Oils:
Can oxidize under high heat. Typically added after extrusion during the coating phase to preserve quality.
Minerals:
Generally stable under extrusion temperatures.
Use precise temperature and moisture control to balance cooking efficiency and nutrient preservation.
Apply vacuum or drum coating systems for post-extrusion application of sensitive nutrients.
Use encapsulated vitamins where needed to withstand partial heat exposure.
Let me know if you’d like a detailed temperature-nutrient retention chart or formulation guidance for specific nutrition targets.
The Darin pet food extruder consists of several key components, each made from high-quality materials to ensure durability, hygiene, and efficiency. Here’s a breakdown of the main components and their materials:
Material: Food-grade stainless steel (SS304 or SS316)
Function: Houses the screw(s) and withstands high pressure and temperature.
Material: Alloy steel (38CrMoAlA) with nitriding treatment
Function: Mixes, shears, and cooks the raw materials while pushing them forward.
Material: Hardened stainless steel or tungsten carbide
Function: Determines the final shape and size of pet food.
Material: High-speed tool steel (HSS) or stainless steel
Function: Cuts the extruded pet food into precise sizes.
Material: Stainless steel heating elements
Function: Provides controlled heat for the cooking process.
Material: Stainless steel with alloy steel paddles
Function: Pre-mixes and pre-cooks ingredients with steam before extrusion.
Material: Hardened steel gears & high-strength aluminum housing
Function: Powers the screw rotation and maintains torque.
Material: Electronic components & stainless steel housing
Function: Automates control of temperature, speed, and ingredient flow.
Material: Food-grade lubricants & stainless steel components
Function: Ensures smooth operation and reduces wear.
💡 Conclusion:
The Darin pet food extruder is built with durability, hygiene, and efficiency in mind. Stainless steel ensures food safety, while hardened alloy materials improve lifespan under high-pressure conditions.
Would you like recommendations on spare parts or maintenance guidelines?
The Darin pet food extruder offers different levels of automation to meet various production needs:
Control: Some automatic features, but requires operator adjustments.
Best For: Medium-scale production.
Features:
Automated temperature and pressure control.
Requires manual ingredient loading.
Output control via user-set parameters.
Control: Complete automation via PLC (Programmable Logic Controller) & HMI (Human-Machine Interface).
Best For: Large-scale commercial production.
Features:
✅ Automatic raw material feeding & mixing.
✅ PLC system controls temperature, pressure, screw speed.
✅ Recipe programming for consistent quality.
✅ Automatic cutting & shaping of pet food.
✅ Real-time monitoring and fault detection.
✅ Integration with drying, oil coating, and cooling systems.
💡 Which option fits your production scale? I can provide recommendations based on your capacity needs. 🚀
The power requirements depend on the model and production capacity of the extruder. Below is a general breakdown of power specifications:
Model | Capacity (kg/h) | Main Motor Power | Heating Power | Total Power Requirement |
---|---|---|---|---|
Small (DR-65) | 100-150 kg/h | 22 kW | 8 kW | ~30 kW |
Medium (DR-70) | 200-300 kg/h | 30 kW | 10 kW | ~40 kW |
Large (DR-85) | 500-800 kg/h | 75 kW | 15 kW | ~90 kW |
Industrial (DR-95) | 1000-1500 kg/h | 110 kW | 20 kW | ~130 kW |
🔹 Voltage Options:
Standard: 380V, 50Hz, 3-phase (common in Europe, Asia, Africa).
Customizable: 220V, 60Hz, 3-phase (for North & South America).
Other voltages: Available upon request.
✅ Energy Efficiency: The extruder is designed with high-efficiency motors and optimized heating elements to reduce power consumption.
✅ CE Certification (Europe): Complies with EU energy standards.
✅ UL/CSA (North America): Available upon request to meet USA & Canada safety and energy efficiency standards.
✅ ISO 9001 Certified: Ensures quality manufacturing and compliance with international regulations.
💡 Do you have a specific voltage or energy regulation requirement for your region? I can confirm compliance or suggest modifications. 🚀
The Darin pet food extruder utilizes a multi-stage cooling system designed to preserve product quality, maintain structural integrity, and ensure safe packaging and storage. Here's how it works and its impact:
Location: Around the barrel sections of the extruder.
Function: Controls barrel temperature during high-shear operations.
Effect:
✅ Prevents overheating of raw materials.
✅ Enhances consistent cooking.
✅ Improves product uniformity and reduces nutrient loss.
Location: After the cutter, before drying or coating.
Components:
Stainless steel mesh belt
High-efficiency fans
Function: Rapidly cools extruded pet food after cutting.
Effect:
✅ Prevents sticking and deformation of hot pellets.
✅ Stabilizes moisture content before drying.
✅ Reduces surface oil absorption if applied before coating.
Often combined with multi-layer belt dryers with built-in air exchange systems.
Maintains ideal post-drying temperature before packaging.
Shape & Texture Stability: Rapid cooling ensures shapes don’t collapse or crack.
Nutrient Preservation: Slows oxidation and thermal degradation.
Safety: Prevents microbial growth from residual heat/moisture.
Packaging Efficiency: Ensures pet food reaches ambient temperature, preventing condensation in sealed bags.
Would you like to know more about water or air cooling specs, or how this system integrates with the dryer and oil sprayer?
Under normal use and with proper maintenance, the Darin pet food extruder has an estimated operational lifespan of 8 to 15 years.
Main Extruder Body: Stainless Steel (SS304/SS316) – corrosion-resistant, ensuring long durability.
Screws & Barrels: 38CrMoAlA alloy steel with nitriding treatment – highly wear-resistant, lasting 3-5 years before replacement.
Cutting Blades & Die Plates: Hardened stainless steel or tungsten carbide – replace every 1-2 years based on wear.
Consistent moderate loads extend lifespan.
Overloading or improper ingredient moisture can increase wear on screws and barrels.
✅ Daily Cleaning & Lubrication – Prevents residue buildup and friction damage.
✅ Regular Screw & Barrel Inspection – Detects early wear, preventing costly failures.
✅ Cooling System Check-ups – Ensures consistent operation and prevents overheating.
Stable power supply prevents motor damage.
Using a voltage regulator in regions with fluctuations can extend motor life.
Screw & Barrel: Replace every 3-5 years under heavy use.
Cutting Blades & Die Plate: Every 1-2 years, depending on wear.
Motors & Gearboxes: Properly maintained, they last 10+ years.
💡 Conclusion:
With proper maintenance, a Darin pet food extruder can last well over a decade. Would you like recommendations on maintenance schedules or spare part replacements? 🚀
The lead time for manufacturing and delivering a Darin pet food extruder typically ranges from 28 to 60 working days, depending on the specific model and customization requirements. This timeframe encompasses the entire process from order confirmation to the machine's readiness for shipment.
Factors Influencing Lead Time:
Model Selection: Standard models may have shorter production times, while specialized or larger-capacity models might extend the lead time.
Customization: Tailoring the extruder to specific production needs, such as unique shapes, sizes, or formulations, can add to the manufacturing duration.
Current Production Schedule: The manufacturer's existing workload and order queue can influence the delivery timeline.
Delivery Considerations:
Shipping Duration: After manufacturing, the shipping time varies based on the destination. For instance, delivery to Singapore may take approximately 1 to 2 weeks via sea freight, subject to shipping schedules and customs clearance.
Installation and Commissioning: Darin offers overseas commissioning services, where technicians assist with installation and training. Scheduling this service may affect the overall timeline and should be coordinated in advance.
Recommendations:
Advance Planning: To align with your production schedule, it's advisable to place orders well ahead of the intended operational date, accounting for both manufacturing and shipping times.
Direct Consultation: Engage directly with Darin to obtain a precise lead time based on your specific requirements and location.
If you have further questions or need assistance with the ordering process, feel free to ask!
Yes, the Darin pet food extruder comes with several key certifications that ensure safety, quality, and international compliance:
Region: European Union & EEA
Scope: Electrical safety, mechanical integrity, and environmental standards.
Significance: Ensures the machine complies with EU machinery directives, making it eligible for use across Europe.
Type: Quality Management System (QMS)
Scope: Covers design, manufacturing, and service processes.
Significance: Assures that the equipment is built using international quality control standards and consistent production practices.
While FDA certification is not issued for machines, Darin uses FDA-compliant food-contact materials, such as:
Stainless steel SS304/SS316 in food-contact parts
Food-grade gaskets, belts, and lubricants
Scope: Enables compliance with U.S. food production standards, especially important if you produce pet food for U.S. export or domestic distribution.
Available on request for third-party factory inspection or pre-shipment evaluation, often required for international buyers or government procurement contracts.
💡 In Summary:
Darin extruders meet global safety and quality standards, making them suitable for export to Europe, North America, Asia, Africa, and beyond.
Would you like to see sample certificates or confirm compliance for a specific market?
When purchasing a Darin pet food extruder, the standard package includes everything needed to set up and begin production, along with essential accessories and support materials. Here's a detailed breakdown:
Pet Food Extruder Unit (single- or twin-screw depending on model)
Feeding system
Cutting system (rotary cutter with speed adjustment)
Control panel (PLC & HMI touch screen)
Set of standard molds for basic shapes (bone, round, square, triangle)
Custom molds available upon request
Quick-change mold mounting system
Screws & washers
Cutting blades
Die plate seals
Temperature sensors & fuses
Tool kit for routine maintenance
PLC program pre-installed and configured
User manual and operation software (USB or digital download)
Recipe storage function for multiple product settings
Optional remote support access
Operation & Maintenance Manual
Electrical schematics
Wiring diagrams
CE Certificate
Test report & factory inspection certificate
Drying oven or multi-layer belt dryer
Oil spraying machine
Cooling conveyor
Flavoring drum
Vacuum feeding system
💡 Note: Shipping, installation guide, and training services are typically included or quoted separately depending on the order terms.
Would you like a quote with optional accessories included or details about the recommended spare parts stock for a 12-month production cycle?
The standard warranty period for the Darin pet food extruder is 12 months (1 year) from the date of installation or commissioning, or 15 months from the date of shipment—whichever comes first.
Extruder barrel
Screw shaft and segments
Gearbox and drive system
Die head and frame
Rotary cutting system
🔧 Covers: manufacturing defects, material faults, structural failures
Main motor
PLC (Programmable Logic Controller)
Touch screen (HMI)
Temperature controllers & sensors
Power control cabinet
🔌 Covers: factory faults or failure due to normal operation, not surge damage or operator misuse
Normal wear-and-tear parts (e.g., cutting blades, die plates, gaskets, seals, belts)
Damage due to improper operation, overloading, or lack of maintenance
Electrical failure due to voltage instability or power surges
Consumables and user-applied coatings or lubricants
Lifetime technical support via email, phone, or remote assistance
Spare parts available at factory price
On-site service (engineer dispatch) available at buyer's cost
Would you like a spare parts forecast or recommended maintenance schedule for post-warranty operation?
Yes, Darin offers on-site installation and training services to ensure proper setup, operation, and maintenance of the extruder. Here’s what’s included:
✅ Engineer Dispatch: Darin can send experienced technicians to your facility.
✅ Machine Assembly: Proper installation of the extruder, including electrical connections and alignment.
✅ System Calibration: Adjusting parameters like temperature, screw speed, and cutting speed for optimal performance.
✅ Test Production Run: Running trial batches to fine-tune settings and verify quality.
Darin provides comprehensive training for operators and maintenance teams, covering:
🔹 Machine Operation:
Setting up and starting the extruder.
Adjusting parameters for different recipes.
Troubleshooting basic issues.
🔹 Maintenance & Cleaning:
Proper lubrication schedule to extend equipment lifespan.
Die & blade changes for shape adjustments.
Cleaning procedures to ensure food safety.
🔹 Safety Training:
Safe handling of electrical and mechanical parts.
Emergency stop procedures.
🔹 Recipe & Process Optimization: (Optional)
Training on adjusting formulations to achieve desired pet food textures, densities, and moisture levels.
🕒 Typical duration: 5–7 days (varies by extruder size and plant setup).
💲 Installation & training costs:
Free remote guidance via video or online support.
On-site service: Travel & accommodation for engineers covered by the buyer.
Additional training sessions available upon request.
For areas where on-site service isn’t feasible, Darin provides:
✅ Video call assistance for step-by-step guidance.
✅ Instructional manuals & videos for self-installation.
✅ Remote PLC troubleshooting via internet connection.
💡 Would you like a detailed cost breakdown for on-site installation, or do you prefer remote setup guidance? 🚀
Darin provides a comprehensive after-sales service package to ensure smooth operation, minimize downtime, and support long-term success. Here's what you get:
24/7 technical assistance via email, phone, or messaging platforms.
Prompt responses to technical queries, performance tuning, or configuration changes.
Multilingual support available based on region.
Remote diagnosis and troubleshooting through:
PLC remote access (if connected to the internet)
Video call support (via Zoom, WhatsApp, or Skype)
Software upgrades or parameter adjustments made remotely.
Technician dispatch for complex repairs, maintenance training, or system upgrades.
Buyer covers travel expenses and accommodation.
Flexible scheduling based on production needs.
Original spare parts available at factory-direct pricing.
Fast shipping of critical wear-and-tear components (blades, die plates, belts, etc.)
Recommended 12-month spare parts kit offered with initial purchase.
Comprehensive operation and maintenance manual (hard and digital copy).
Video tutorials for troubleshooting, cleaning, and component replacement.
Recipe guides and process optimization tips for different pet food types.
Free replacement of faulty parts under the 12-month warranty (excluding wear parts).
Warranty claim processing within 48 hours of issue report.
Priority assistance for emergency breakdowns during production.
Backup support from Darin’s global service partners or regional agents (where available).
💡 Would you like me to prepare a post-purchase support plan or recommended spare parts list tailored to your production scale?
Darin provides transparent pricing, but like any industrial equipment, there are additional costs that buyers should consider. Here’s a full breakdown:
✅ Free:
Remote installation support (via video call, manuals, and guides).
Online training for operators and maintenance staff.
💲 Additional Costs (if required):
On-site installation: Technician travel, visa, accommodation, and daily allowance (~$100–$150 per day).
Extended training programs: If additional in-depth training is needed beyond the standard package.
✅ Included:
Free basic spare parts kit (cutting blades, gaskets, fuses, etc.).
12-month warranty for non-wear components.
💲 Ongoing Costs:
Wear parts replacement: (varies by usage frequency)
Screws & barrels: $1,000–$5,000 every 3-5 years
Cutting blades & die plates: $200–$1,000 per 1-2 years
Seals, bearings, and gaskets: Minor yearly expenses (~$100–$500)
Lubricants and cleaning agents: Typically $200–$500 per year
✅ Included:
PLC software pre-installed with machine purchase.
Free basic software updates during warranty.
💲 Additional Costs (if required):
Advanced custom programming (~$500–$2,000) for special recipes or automation upgrades.
PLC replacement (after 5+ years if required) ~$1,500–$5,000.
💡 Power usage depends on extruder size:
Small models (~30 kW total) = ~$2–$5/hour
Large industrial models (~100 kW total) = ~$10–$20/hour
Cost depends on local electricity rates
💲 Variable Costs:
Shipping (by sea or air) depends on destination (~$1,000–$10,000).
Import duties/taxes vary by country (0%–20% based on local regulations).
Cost Category | Estimated Annual Cost |
---|---|
Installation (one-time) | $0 – $5,000 |
Wear parts & maintenance | $1,000 – $5,000 |
Energy consumption | $5,000 – $30,000 |
Software/PLC upgrades (if needed) | $0 – $2,000 |
Shipping/customs (one-time) | $1,000 – $10,000 |
Darin does not charge hidden fees, but buyers should budget for maintenance, energy, and potential upgrades.
Would you like a cost analysis specific to your production needs? 🚀
Feel free to contact us for more information.
Darin offers flexible payment terms to accommodate different business needs. Below is a detailed breakdown:
T/T (Telegraphic Transfer) – Most Common
40% deposit upon order confirmation.
60% balance before shipment after factory inspection or testing.
L/C (Letter of Credit) – For Large Orders
100% irrevocable L/C at sight from a reputable bank.
Typically used for international bulk purchases.
Western Union / PayPal (For small orders or spare parts only)
Used for transactions below $5,000 (such as spare parts or minor customizations).
Financing / Leasing (On Approval)
Available through third-party financial institutions or Darin’s partner banks.
Currency: USD, EUR, or RMB (CNY) accepted.
Processing Fees: Bank charges for L/C or international wire transfers are the buyer’s responsibility.
Order Confirmation: Production starts only after the deposit is received.
Lead Time: 45-60 working days after deposit.
Incoterms: FOB, CFR, CIF, EXW (as per buyer’s request).
Pre-Shipment Inspection: Allowed at the factory before balance payment.
Deposits are non-refundable once production has started.
Any order changes after confirmation may result in additional charges.
💡 Would you like a customized payment schedule based on your order size? 🚀
Feel free to contact us for more information.
Darin ensures smooth international shipping by handling freight arrangements and customs documentation. Below is a step-by-step breakdown of the process:
✅ FOB (Free on Board) – Darin delivers the extruder to the port; the buyer arranges shipping.
✅ CIF (Cost, Insurance, and Freight) – Darin arranges shipping, including freight costs & insurance, to the buyer's designated port.
✅ DDP (Delivered Duty Paid) – Darin handles everything, including customs clearance and delivery to the buyer’s facility (available in select countries).
✅ EXW (Ex-Works) – Buyer arranges pickup from Darin’s factory.
🚚 Shipping Modes:
Sea Freight (Most Common): 20ft or 40ft containers, depending on extruder size.
Air Freight: For urgent small equipment or spare parts.
Rail or Road Transport: Available for nearby countries.
Darin provides all necessary documents for smooth customs clearance:
✅ Commercial Invoice – Includes product details, value, and Incoterms.
✅ Packing List – Lists the contents, dimensions, and weight.
✅ Bill of Lading (B/L) or Airway Bill (AWB) – Proof of shipment.
✅ Certificate of Origin – Required for some countries to qualify for lower tariffs.
✅ CE, ISO, or FDA Compliance Certificates – If needed for import approvals.
✅ Insurance Policy (for CIF shipments) – Covers damage or loss during transit.
📌 Step 1: The freight forwarder notifies the buyer upon arrival at the destination port.
📌 Step 2: Buyer submits documents to local customs authorities.
📌 Step 3: Customs may inspect the cargo (if required).
📌 Step 4: Buyer pays import duties & taxes (varies by country).
📌 Step 5: Customs releases the shipment, and final delivery is arranged.
💲 Import Duties & Taxes – Based on local tariffs for industrial machinery.
💲 Customs Broker Fees – If using an agent for clearance assistance.
💲 Port Storage & Handling Fees – If the shipment is not collected on time.
✔ Freight coordination with trusted carriers.
✔ Customs documentation assistance to prevent delays.
✔ Recommended customs brokers in select countries.
✔ Remote support for import clearance issues.
💡 Would you like an estimated shipping cost based on your location? 🚀
To ensure optimal performance and long lifespan (8–15 years), the Darin pet food extruder requires regular maintenance based on usage intensity.
Frequency | Maintenance Tasks |
---|---|
Daily | ✅ Clean extruder barrel & die plate after each shift. ✅ Check for ingredient buildup in feeding system. ✅ Lubricate moving parts (except areas in contact with food). |
Weekly | ✅ Inspect screws & barrel for wear or residue. ✅ Check alignment of cutting blades & adjust if necessary. ✅ Inspect motor & gearbox for unusual noise or vibration. |
Monthly | ✅ Tighten loose bolts & electrical connections. ✅ Clean or replace air filters in cooling system. ✅ Check oil levels in gearbox & top up if needed. |
Every 3–6 Months | ✅ Perform deep cleaning of extruder components. ✅ Check heating elements & temperature sensors. ✅ Inspect die plate for blockages or wear. |
Annually | ✅ Replace worn screws & barrel segments if needed. ✅ Replace seals, gaskets, & lubricants. ✅ Test and recalibrate PLC controls for accuracy. |
Use food-grade cleaning agents to remove food residue.
Avoid high-pressure water spray on electrical parts.
Use high-temperature food-grade lubricants.
Check & replace gearbox oil every 6 months.
🔹 Screws & Barrel: Inspect every 3–6 months, replace every 3–5 years.
🔹 Cutting Blades & Die Plates: Replace every 1–2 years based on wear.
🔹 Seals & Bearings: Check every 6 months, replace if worn.
Inspect wiring & connections to prevent overheating.
Test PLC & sensors for temperature accuracy.
🚨 Uneven pet food shape → Possible die plate blockage.
🚨 Excess noise/vibration → Check screws & motor alignment.
🚨 Reduced output rate → Possible screw wear or barrel residue buildup.
🚨 Temperature fluctuations → Inspect heating elements & sensors.
💡 Would you like a recommended spare parts kit or maintenance checklist tailored to your production schedule? 🚀
To ensure your Darin pet food extruder operates efficiently, sourcing genuine replacement parts is essential. Here's how you can obtain them:
Directly from Darin Machinery:
**Official Website:**Visit Darin's official site to request spare parts
Contact Information:
Email: darin@darin.cn
Phone: +86-531-82983199 / 82983299 / 82983399
WhatsApp: +86-13805312637
**Process:**Provide your machine model and the specific parts required. Darin's team will assist with identification and ordering
Authorized Distributors: -Darin collaborates with distributors worldwide Contact Darin directly to find a local distributor in your region
**Processing Time:**Orders are typically processed within 1-3 business days
Shipping Duration:
**Express Shipping (e.g., DHL, FedEx):**Approximately 3-7 business days worldwide
**Standard Shipping:**Delivery times vary based on location and customs but generally range from 7-15 business days
**Customs Clearance:**Delays may occur due to customs procedures in your country
*Maintain an Inventory: Keep essential spare parts on hand to minimize downtim.
*Consult Darin: For guidance on critical spare parts and maintenance schedules, reach out to Darin's support tea.
For personalized assistance or further inquiries, feel free to contact Darin directl.
Even high-quality extruders like Darin's pet food extruder may face occasional issues. Here’s a troubleshooting guide to resolve the most common problems efficiently.
Possible Causes:
✔ Die plate clogged with material buildup.
✔ Feed rate too low or too high.
✔ Excess moisture in raw materials.
✔ Worn-out screw segments.
Solutions:
🔹 Clean the die plate with hot water or a brush after every batch.
🔹 Adjust feed rate to match screw speed.
🔹 Reduce moisture content in ingredients (ideal: 10-12%).
🔹 Inspect screws & barrel, replace worn-out parts.
Possible Causes:
✔ Insufficient lubrication of gearbox.
✔ Clogged cooling system (water-cooled jacket).
✔ High-pressure buildup due to ingredient imbalance.
Solutions:
🔹 Check lubrication oil levels and refill if low.
🔹 Clean cooling system and ensure proper water flow.
🔹 Adjust ingredient formulation to avoid excessive starch buildup.
Possible Causes:
✔ Worn or misaligned cutting blades.
✔ Die plate holes blocked or uneven.
✔ Screw wear leading to inconsistent material flow.
Solutions:
🔹 Replace cutting blades every 6-12 months.
🔹 Clean or replace die plate to ensure even extrusion.
🔹 Inspect screws for wear, replace if needed.
Possible Causes:
✔ Loose bolts in motor or gearbox.
✔ Misalignment of screw shaft.
✔ Worn-out bearings.
Solutions:
🔹 Tighten all bolts & fasteners regularly.
🔹 Check screw shaft alignment, realign if needed.
🔹 Replace worn-out bearings every 1-2 years.
Possible Causes:
✔ Improper temperature settings.
✔ Incorrect moisture level in raw materials.
✔ Wrong screw configuration.
Solutions:
🔹 Adjust extruder barrel temperature based on product type.
🔹 Modify ingredient moisture content (optimal range: 10-20%).
🔹 Change screw setup to match the desired texture.
Possible Causes:
✔ Power fluctuations or unstable voltage.
✔ PLC software error or misconfiguration.
✔ Sensor failure.
Solutions:
🔹 Use a voltage stabilizer to protect electrical components.
🔹 Restart PLC system, reload software if needed.
🔹 Replace faulty sensors (temperature, pressure).
✅ Daily cleaning of extruder components.
✅ Lubricate gearbox & moving parts every week.
✅ Inspect and replace wear parts every 3-12 months.
✅ Keep spare parts on hand to reduce downtime.
💡 Would you like a recommended maintenance kit or spare parts list based on your production scale? 🚀
Dry Kibble:
Wet Food:
Treats & Biscuits:
Specialty Diets (e.g., Raw or Freeze-Dried):
Yes, a modern pet food production line is highly adaptable for producing a wide range of shapes, sizes, and formulations for different types of pet food products, from kibble and wet food to treats and biscuits. This customization ensures that the production line can meet the specific needs of your target market, whether you're focused on a single product type or a broad variety of formulations.
Would you like more information on a specific customization option or assistance with configuring a line for your product needs?
Yes, Darin pet food extruders come with remote monitoring and diagnostic capabilities, allowing for efficient troubleshooting and real-time performance tracking.
✅ PLC-Based System with HMI
The extruder is equipped with a Programmable Logic Controller (PLC) and a Human-Machine Interface (HMI) touchscreen for real-time data tracking.
✅ Internet-Connected Remote Access (Optional)
Wi-Fi or Ethernet connection enables remote support from Darin engineers.
Allows for real-time monitoring, parameter adjustments, and software updates without on-site intervention.
✅ Key Parameters Monitored
Temperature & pressure levels
Motor speed & power consumption
Product consistency & feed rate
Error logs & system alerts
✅ Remote PLC Troubleshooting
Darin technicians can access the PLC system remotely to diagnose and fix software-related issues.
✅ Error Detection & Alerts
The system logs error codes & alerts in case of malfunctions, making it easier to pinpoint issues.
Operators receive notifications on the HMI display or via email/SMS alerts (if connected).
✅ Live Video Assistance (Optional)
Video call support via WhatsApp, Zoom, or Skype to guide operators through repairs.
Step-by-step video tutorials & digital manuals available.
✅ Automatic Software Updates (For internet-connected models)
✅ Custom Software Modifications (Available upon request)
✅ Data Logging & Performance Reports (Optional for large-scale operations)
📌 Internet connection (Wi-Fi or LAN) required for full remote access.
📌 Some advanced remote support features may be optional add-ons.
💡 Would you like details on enabling remote monitoring for your specific extruder model? 🚀
Darin offers reliable and professional on-site support when remote assistance isn’t sufficient. Here's how you can request it:
Email: darin@darin.cn
Phone/WhatsApp: +86-13805312637
Provide the following:
Machine model and serial number
Description of the issue (with error codes, if any)
Photos or videos of the malfunction
Your location and preferred service dates
✅ Darin's team will first diagnose the issue remotely via:
Video call (Zoom, WhatsApp, Skype)
Remote PLC access (if internet connected)
Review of operation logs, system alerts, or visuals
If the issue can't be resolved remotely, on-site service is scheduled.
✔ If required, Darin will:
Assign a qualified technician or engineer
Coordinate travel arrangements, visas, and schedule
Send official service confirmation with estimated duration and cost
📝 Buyer’s Responsibility:
Cover travel expenses, visa fees, accommodation, and a daily service fee (typically ~$100–$150/day)
Provide local transport and tools, if needed
The technician will:
Inspect, repair, and test the machine
Replace faulty parts, if needed
Train local staff on preventive measures
Issue a service report upon completion
If the repair falls under warranty, the service labor and parts are free (travel costs still apply)
Post-repair remote follow-up is provided to ensure issue resolution
💡 Tip: For faster service, maintain a stock of recommended spare parts to avoid delays.
Would you like a sample service request form or estimate based on your location?
Yes, Darin provides software updates and process optimizations to ensure your extruder remains efficient, up-to-date, and capable of producing high-quality pet food.
✅ Firmware & Control System Updates (Free during warranty period, available post-warranty for a fee)
Enhancements to PLC logic for better automation.
Bug fixes and stability improvements.
New energy-saving algorithms to reduce power consumption.
✅ Recipe & Parameter Optimization
Updated preset extrusion settings for different pet food types.
Improved temperature, moisture, and screw speed control for better texture & digestibility.
✅ Remote Software Updates (Available for internet-connected models)
Can be applied remotely via Ethernet or Wi-Fi.
Manual USB updates available for offline machines.
✅ Production Efficiency Analysis (Optional Service)
Darin engineers analyze your extrusion process and suggest screw configuration, moisture, and ingredient adjustments to maximize yield.
✅ Customization for New Product Development
Need to produce grain-free kibble, high-protein diets, or unique pet food textures?
Darin offers custom screw designs, die plate modifications, and process tuning for new formulations.
✅ Training on New Features (Available on request)
Operators can receive updated training to ensure they understand new process improvements.
✔ Software updates during the warranty period are FREE.
✔ Post-warranty updates and customization require a one-time service fee (varies by update type).
✔ Custom process optimizations may require on-site or remote consultation.
💡 Would you like a specific software update package or process consultation based on your production needs? 🚀
Yes, Darin pet food extruders are designed with scalability in mind, allowing for future upgrades and expansions to increase production capacity. Here’s how:
✅ Screw & Barrel Modification
Upgrade to a longer barrel for better cooking and increased throughput.
Replace screws with higher compression ratio designs to handle more material efficiently.
✅ Die & Cutter Upgrades
Multi-hole die plates can increase kibble output per cycle.
High-speed rotary cutters can handle faster extrusion rates.
✅ Motor & Gearbox Enhancements
Higher horsepower motors available for increased screw speed.
Stronger gearboxes to handle higher torque loads.
✅ Automation & PLC Upgrades
Advanced PLC systems allow for automated process adjustments, improving efficiency.
New recipe storage & process optimization features can be added.
If a single extruder upgrade isn’t enough, you can expand your entire production capacity by integrating:
✅ Additional Extruder Units
Running two or more extruders in parallel doubles or triples production output.
✅ Larger Drying & Cooling Systems
If upgrading the extruder, a bigger multi-layer belt dryer may be needed to handle higher output.
Enhanced cooling conveyors ensure faster stabilization of pet food before packaging.
✅ Automated Ingredient Handling & Feeding
Vacuum or screw feeders can increase raw material input speed.
Larger mixers & pre-conditioners improve consistency in high-volume production.
✅ Oil Coating & Flavoring Enhancements
Upgrade to vacuum coating systems for even oil distribution in high-fat pet foods.
Increase drum size or add additional sprayers for better efficiency.
🚀 If your production demand increases by 30% or more, consider an upgrade.
🔧 If your extruder is running at maximum capacity consistently, expansion is the best option.
⚙️ If your product line changes (e.g., adding new kibble sizes or formulations), a modular upgrade may be needed.
✔ Screw, die, and motor upgrades are low-cost and quick to implement.
✔ Adding secondary extruders or dryers requires higher investment but massively increases output.
✔ Darin provides full consultation on choosing the best upgrade/expansion plan.
💡 Would you like recommendations on the best upgrade path based on your current production capacity? 🚀
Yes, Darin provides training for new employees even after the initial setup and commissioning. We understand that staff turnover or expanding operations may require additional training sessions.
✅ On-Site Training (Optional)
A Darin engineer can visit your facility for hands-on training.
Covers machine operation, troubleshooting, and maintenance.
Ideal for large-scale operations or when multiple new employees need training.
✅ Remote Training (Standard & Free)
Video call training sessions via Zoom, WhatsApp, or Skype.
Step-by-step screen sharing on PLC & control system.
Perfect for training 1-2 new employees quickly.
✅ Training Manuals & Video Tutorials (Always Available)
Digital training guides & videos are provided for self-paced learning.
Covers everything from startup procedures to troubleshooting common issues.
✅ Refresher Training (As Needed)
If an operator forgets key processes or needs help with new recipes & settings, we provide customized refresher training.
📌 Contact Darin Support via email (darin@darin.cn) or WhatsApp (+86-13805312637).
📌 Specify machine model, training type (on-site or remote), and topics needed.
📌 Darin schedules the training based on availability and urgency.
✔ Remote training & video guides → FREE for lifetime support.
✔ On-site training → Travel & daily service fee applies ($100–$150 per day).
💡 Would you like a personalized training program for your team? 🚀
To ensure a safe working environment, operators must follow strict safety protocols when using the extruder. Below are essential safety measures to prevent accidents.
✅ Wear appropriate safety gear at all times:
Heat-resistant gloves when handling hot components.
Safety goggles to protect eyes from ingredient dust or splashes.
Hearing protection (earplugs or earmuffs) in high-noise areas.
Steel-toe safety shoes to prevent foot injuries from heavy parts.
Dust masks if handling powdered ingredients.
✅ Before Starting the Extruder:
Ensure all guards and safety covers are in place.
Check for loose bolts, leaks, or obstructions in the system.
Verify that emergency stop buttons are functional.
Confirm correct ingredient moisture levels to avoid blockages.
✅ During Operation:
NEVER insert hands or tools into the extruder while running.
Maintain a safe distance from the die head and cutter.
Monitor temperature and pressure levels on the control panel.
Stop operation immediately if there are unusual vibrations or noises.
✅ After Stopping the Machine:
Allow the extruder to cool down before maintenance.
Lock out and tag out (LOTO) before cleaning or servicing.
Regularly clean the die plate, screws, and barrel to prevent buildup.
✅ Ensure proper grounding of the machine to prevent electrical shocks.
✅ Avoid using wet hands when operating electrical panels.
✅ Keep fire extinguishers nearby, especially when handling oil-based ingredients.
✅ Use a stable power supply with a voltage regulator to prevent motor damage.
✅ Emergency Stop Button:
Located on the control panel and near the extruder.
Press immediately if an operator’s safety is at risk.
✅ First Aid Readiness:
Have a first aid kit accessible in the work area.
Train staff on burn treatment and emergency response.
✅ Fire & Electrical Shutdown:
Know the main power switch location for emergency shutdown.
If a fire occurs, use a CO₂ or dry chemical extinguisher, NOT water.
✔ Conduct monthly safety briefings for operators.
✔ Schedule preventative maintenance to reduce accident risks.
✔ Ensure only trained personnel operate the extruder.
💡 Would you like a customized safety checklist or training program for your team? 🚀
To ensure food safety compliance (HACCP, FDA, EU standards), regular cleaning and sanitation of the pet food extruder is essential. Below is a detailed guide.
Frequency | Cleaning Tasks |
---|---|
After Each Shift | ✅ Wipe down surfaces and remove leftover materials. ✅ Flush the extruder with warm water (if formula allows). |
Daily | ✅ Clean die plate and cutter blades. ✅ Wipe down conveyor belts and feeding hoppers. |
Weekly | ✅ Disassemble and deep-clean the screws, barrel, and feeding system. ✅ Sanitize surfaces with food-grade disinfectant. |
Monthly | ✅ Inspect and clean cooling & drying systems. ✅ Check for mold, bacteria buildup, or oil residues. |
✅ Turn off and unplug the machine.
✅ Wait for the extruder to cool down before cleaning.
✅ Remove loose ingredients from the hopper and screw barrel.
✅ Die Plate & Cutter System:
Remove the die plate and soak it in hot water (60–80°C / 140–176°F).
Use a brush or compressed air to clear clogged holes.
✅ Screws & Barrel: (Weekly Cleaning)
Remove the screws and barrel lining.
Scrub with a food-safe detergent and rinse thoroughly.
If fatty ingredients were used, use warm water & mild alkaline cleaner to break down oil residues.
✅ Feeding & Conveyor System:
Wipe with sanitizing solution to remove buildup.
Check for ingredient clumps that could cause contamination.
✅ Use food-grade disinfectants (e.g., peracetic acid, chlorine-based solutions).
✅ Rinse thoroughly with clean water to prevent chemical residues.
✅ Dry completely to prevent mold growth.
✅ Ensure all parts are completely dry before reassembling.
✅ Check for wear & tear on seals, gaskets, and blades.
✅ Record the cleaning in a sanitation logbook (for HACCP/FDA compliance).
🚫 Skipping cleaning schedules – leads to product contamination.
🚫 Using harsh chemicals – can damage machine components.
🚫 Reassembling wet parts – causes mold and bacterial growth.
💡 Would you like a customized cleaning checklist or food safety compliance guide? 🚀
Explore trends, tips, and innovations in Pet Food Extruder. Enhance efficiency and quality with expert insights.
Making homemade dry dog food is a rewarding way to ensure your pet receives balanced nutrition
Making homemade dry dog food is a rewarding way to ensure your pet receives balanced nutrition
Making homemade dry dog food is a rewarding way to ensure your pet receives balanced nutrition
Making homemade dry dog food is a rewarding way to ensure your pet receives balanced nutrition
Making homemade dry dog food is a rewarding way to ensure your pet receives balanced nutrition
Making homemade dry dog food is a rewarding way to ensure your pet receives balanced nutrition
let’s talk about how we can help you achieve your goals and take your business to increase !
Tell us as specific as possible of your needs.
We will work on the best solution & quote according to your requirements.
We will start production after getting your approval and deposit, and we will handle the shipment.
· Don’t worry, we hate spam too !
· Call only when multiple emails unanswered !