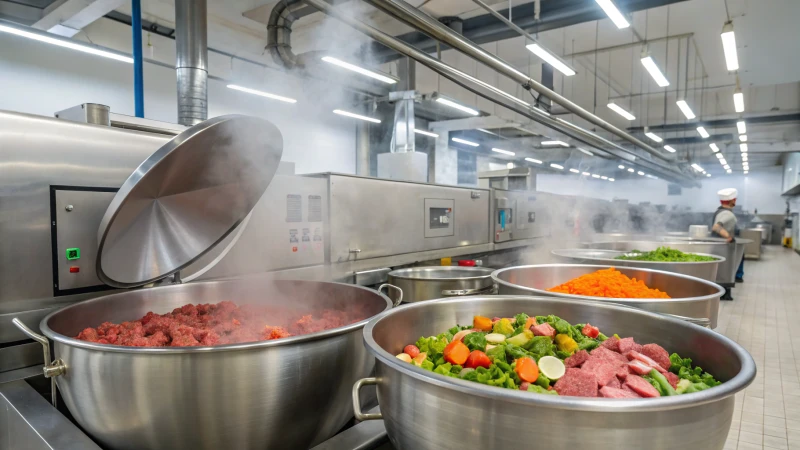
Які сировинні матеріали використовуються для виробництва корму для домашніх тварин?
Приготування домашнього сухого корму для собак – це корисний спосіб забезпечити збалансоване харчування вашої тварини
As an industry-leading supplier of pet food machinery, Darin® offers the Rawhide Rolling Line—a dedicated, fully automatic solution for the industrial-scale processing of pressed and rolled rawhide chews.
Designed to meet international food safety standards, this line is ideal for manufacturers of natural dog treats who require precise shaping, strong bonding, and minimal labor input. The line automates every step from rawhide soaking to final rolling and shaping, enabling high-volume, uniform production.
Used for rawhide rolls Production.
Модель | Output Capacity | Installed Power |
---|---|---|
DR-R3 | 300 kg/h | 90 kW |
Looking to create a unique pet food product? We provide full customization services, from concept to finished machine. Our engineering team uses CAD and 3D modeling to bring your ideas to life—fast and accurately. Let’s work together to build your next best-seller.
The Darin ® Rawhide Rolling Line includes ten essential components: Control Cabinet, Extruder, Cutter, Rolling Machine, Sorting Conveyor, Dryer A, Cooler A, Gravy Coater, Dryer B, and Cooler B. This fully automated line efficiently processes rawhide into uniform, flavorful pet chews through shaping, rolling, drying, coating, and cooling — ensuring high output and consistent quality.
① Control Cabinet
② Extruder
③ Cutter
④ Rolling Machine
⑤ Sorting Conveyor
⑥ Dryer A
⑦ Cooler A
⑧ Gravy Coater
⑨ Dryer B
⑩ Cooler B
The Rawhide Rolling Line is an automated production system that processes rawhide into high-quality pet chews through a series of steps including extrusion, cutting, rolling, drying, coating, and cooling. With precise control and efficient design, it ensures uniform thickness, enhanced flavor, and consistent product quality — ideal for mass production in the pet treat industry.
The main process of the Rawhide Rolling Line is as follows:
Extrusion → Cutting → Rolling → Sorting → First Drying → First Cooling → Gravy Coating → Second Drying → Second Cooling → Packaging
This streamlined and automated workflow ensures consistent shape, improved palatability, and stable quality of rawhide pet chews from start to finish.
The Rawhide Rolling Line works through a fully automated process designed to transform rawhide and related ingredients into high-quality pet chews. Here’s how it works step by step:
1. Raw Material Extrusion: The Extruder processes rawhide or blended ingredients into a soft, moldable texture suitable for forming.
2. Cutting: The Cutter slices the extruded material into uniform lengths for the next step.
3. Rolling: The Rolling Machine flattens each piece into consistent thickness, improving chewability and appearance.
4. Sorting: The Sorting Conveyor organizes and aligns the products for smooth downstream processing.
5. Primary Drying & Cooling: Dryer A removes initial moisture, and Cooler A brings the temperature down to stabilize the product.
6. Gravy Coating: The Gravy Coater evenly applies meat-based coating for enhanced flavor and aroma.
7. Final Drying & Cooling: Dryer B completes moisture removal to ensure shelf stability, while Cooler B prepares the product for packaging.
8. Control System: The Control Cabinet oversees the entire process, ensuring consistent quality, efficiency, and easy operation.
This streamlined workflow ensures that every chew is flavorful, durable, and safe for pets.
Darin Triflavor Kabobs Processing Line an ideal choice for businesses looking to enhance efficiency, quality, and versatility in kabob production.
Двигуни від Darin Machinery постачаються компанією WEG з 3-річною гарантією по всьому світу або Siemens. Насолоджуйтесь надійною глобальною системою післяпродажного обслуговування.
Електричні деталі від ABB або Schneider, їх легко знайти на місцевому ринку.
ПЛК і сенсорні екрани від Siemens, Німеччина, використовуються компанією Darin Machinery для забезпечення більш простого управління і зниження трудомісткості.
При виникненні несправностей сенсорні екрани Darin Machinery відображають відповідну інформацію, що дозволяє легко діагностувати і швидко вирішувати проблеми.
Шафи управління Darin Machinery оснащені безпечною напругою 24 В, що забезпечує безпеку оператора навіть у разі витоку електрики.
Darin Machinery включає в себе три типи захистів від перевантаження по струму, перенапруги та перегріву, щоб забезпечити безпеку машини та оператора.
Servo follows the cutting size more accurately, rolling cutting can cut products with strong toughness, such as cowhide products, and the cutter does not cut the conveyor belt.
The end of the conveyor belt has a small turning radius, which makes material transportation smoother.
Its components are arranged for quick disassembly, ensuring efficient upkeep and hygienic operation.
Всі корпуси кришок, сітчасті ремені та деталі, що контактують з матеріалами, виготовлені компанією Darin Machinery з харчової нержавіючої сталі 304, що забезпечує чудову довговічність і безпеку.
Darin® Machinery is global leading manufacturer of pet food production lines, Darin® provide full-cycle, one-stop production equipment solutions for all types of pet food, pet treats & pet health products.
Вся техніка сертифікована європейським сертифікатом CE та ISO 9001.
■ Run in 99+ countries including USA, Germany, Japan, Italy, UAE, Australia etc.
Постачальник обладнання для General Mills, Kelloggs, Melinda, Фонду Білла Гейтса та Wanpi.
■ 290+ Invention patents & utility model patents.
■ Government-certified high-tech enterprise.
■ Member of APPA (USA) & Deputy President Unit of SDPIA.
■ Professional food machinery manufacturer with 18 years of experience.
Наш широкий асортимент продукції включає лінії для виробництва сухих, вологих, напіввологих і сирих кормів, а також звичайних ласощів для домашніх тварин, таких як печиво, в'ялене м'ясо, зубні жуйки, жуйки з сирої шкіри та ласощі для дресирування. Крім того, ми пропонуємо різні лінії для виробництва харчового обладнання, машини для листкових снеків, машини для енергетичних мюслі та допоміжне обладнання.
Darin Machinery’s equipment is operational in over 99 countries and regions, including the USA, Germany, Japan, Italy, Spain, the Netherlands, Australia, Canada, Holland, Saudi Arabia, Brazil, Mexico, Indonesia, Thailand, and more. Darin Machinery serves renowned clients worldwide, including General Mills, Kellogg’s, and the Bill & Melinda Gates Foundation, among top-tier pet food suppliers.
When purchasing the Rawhide Rolling Line, you might be interested in the following questions.
У "The Rawhide Rolling Line typically has a production capacity range of 500 kg/h to 2000 kg/h, depending on the specific model, line configuration, and the thickness and width of the rawhide being processed.
Yes, the Rawhide Rolling Line can be fully customized to meet your production requirements. Customization options include:
Production Capacity Adjustments
Light-duty: 300–500 kg/h
Standard: 800–1000 kg/h
Heavy-duty: 1500–2000+ kg/h
Higher capacities available on request (e.g., industrial-grade >3000 kg/h)
Roller Configuration
Number of rollers
Roller diameter and length
Pressure and speed control options
Feeding and Discharge Systems
Manual or automatic feeding conveyors
Discharge conveyor with sorting or stacking
Рівень автоматизації
Semi-automatic or fully automatic systems
Integrated PLC control with touch screen
Сумісність матеріалів
For different rawhide thicknesses, moisture levels, and end-product requirements (e.g., pet chew production)
Factory Layout Matching
Custom design to match available factory space or integrate with existing pet food production lines.
Would you like a recommended configuration based on your target output and product type (e.g., rawhide chips, rolls, bones)?
У "The Rawhide Rolling Line requires the following сировина і pre-processing inputs to operate efficiently:
Rawhide Sheets or Pieces
Derived mainly from cowhide, but can also include buffalo, pigабо horse hide depending on product type and regional supply.
Typically sourced wet salted, limedабо dry — then soaked and softened prior to rolling.
Вміст вологи: Ideally 40%–60% for rolling
Thickness: Around 3–6 mm (depending on final product size)
Cleanliness: Free from excessive fat, flesh, or hair for optimal rolling
Yes, we offer a full rawhide pretreatment line to support your production. This ensures your rawhide meets rolling specs and enhances final product quality.
Soaking Tanks / Washing Drums
Rehydrate dry or salted hides
Remove dirt, blood, and salt residues
Hair Removal Machines
Dehairing of rawhide (if supplied with hair)
Can be rotary or drum-type depending on volume
Fleshing Machines
Remove residual fat and muscle tissues
Improve hide consistency for rolling
Splitting Machines (Optional)
To get uniform thickness across the hide
Ideal if you're producing standardized rawhide products
Softening & Drying Systems
Prepares hides to desired pliability and moisture for easier rolling
Would you like us to quote a complete pretreatment + rolling line solution based on your daily capacity and rawhide input format (e.g. wet salted, dry, etc.)?
У "The Rawhide Rolling Line complies with the following international certifications and standards, ensuring quality, safety, and compliance for global markets:
CE Certification (Conformité Européenne)
Ensures compliance with EU safety, health, and environmental protection requirements
Applicable for electrical systems, safety guards, emergency stops, and operator interfaces
Valid for export to the Європейський Союз and CE-recognizing countries
ISO 9001:2015 – Quality Management System
Guarantees that the machinery is manufactured under a certified quality management system
Covers all stages from design, machining, assembly, to final testing
Ensures consistency and product traceability
SGS / TÜV / BV Inspection Certificates (Available upon request)
Third-party factory audit reports or product inspection services can be arranged before shipment
Commonly requested by customers in the Middle East, South America, and Southeast Asia
Custom Certifications (Optional)
UL (for the U.S. market)
CSA (for Canada)
GOST / EAC (for Russia, Kazakhstan, etc.)
We can support documentation and modifications to meet these standards if required.
CE Declaration of Conformity
ISO Certificate copy
Factory test reports
Electrical and mechanical drawings
User manual and maintenance guide
Export packing list and commercial invoice
Would you like me to prepare a compliance pack sample or quote with inspection and certification service costs included?
У "The standard delivery lead time for the Rawhide Rolling Line after placing an order is typically:
Standard Configuration: 25–30 working days
For machines with no major customization
Includes final quality testing and standard wooden export packaging
Customized Configuration: 35–45 working days
For special roller sizes, automation upgrades, integration with pretreatment or drying lines
Includes design confirmation, layout approval, and factory acceptance test (FAT)
Full Production Line with Rawhide Preparation: 45–60 working days
Includes soaking, dehairing, fleshing, rolling, drying, cutting, and packaging sections
Ideal for turnkey projects
FOB, CFRабо CIF terms available
Container loading typically requires:
1×20GP or 1×40HQ, depending on the size of the rolling line and auxiliary equipment
Custom certifications (e.g. UL, GOST)
Voltage/frequency adjustments (e.g. 415V/50Hz, 220V/60Hz)
On-site installation support scheduling
Would you like a detailed production schedule with key milestones (e.g., design confirmation, testing, shipping)?
Так, у Rawhide Rolling Line can be seamlessly integrated into an existing pet treat production system, and we offer modular or fully customized integration solutions to match your current setup.
Feeding Conveyor Adaptation:
Can be aligned with your upstream rawhide preparation unit або cutting/slicing module
Output Conveyor Customization:
Tailored to link with shaping, drying, or forming machines downstream (e.g., bone press, mold former)
PLC Compatibility:
Our control system can interface with your existing Siemens, Mitsubishi, or Delta PLCs
Centralized or Decentralized Control:
Optional master-slave programming for unified operation or standalone units
HMI Touchscreen Settings can be configured to match your production logic and recipe settings
Production Monitoring: Optional integration with SCADA systems or ERP for line-wide reporting
Rawhide Soaking + Rolling + Bone Press Forming
Rolling Line + Manual/Auto Cutter + Hot Air Dryer
Full Line with Automated Weighing + Packing
We provide 3D factory layout drawings and offer remote or on-site engineering support to:
Match equipment dimensions
Align conveyor heights
Optimize space utilization
Would you like to share your existing line layout or equipment list so we can propose a tailored integration plan with mechanical and control matching?
У "The Rawhide Rolling Line can be paired with a wide variety of molds and shaping tools, especially when integrated with a bone press machine or cutting/forming system. These molds are used to shape rolled rawhide into popular pet treat formats.
Bone-Shaped Molds
Most popular style for pet chews
Sizes:
Small: 2–3 inches (5–7.5 cm)
Medium: 4–5 inches (10–12.5 cm)
Large: 6–8 inches (15–20 cm)
Available in single-cavity or multi-cavity formats for mass production
Knot Bone Molds
For tied-end rawhide bones
Typically used with semi-automatic shaping tools
Stick and Twist Shapes
Round or flat rods (sticks): 6–15 mm diameter
Twisted braid molds for decorative chew products
Donut & Ring Shapes
Circular forms with a central hole
Often used for novelty or flavored chews
Custom Logo or Novelty Molds
Shapes like hearts, stars, paws, or branded patterns
Custom engraving or laser-cut molds can be made to order
Hardened Stainless Steel (SUS304/316) – Durable, food-safe, corrosion-resistant
Chrome-plated Alloy Steel – For high-pressure hydraulic mold presses
Custom CNC Aluminum Molds – Lightweight and suitable for low-volume or special designs
Quick-change mold base design available for efficient switch between sizes or shapes
Molds are interchangeable on most bone press and forming units connected to the Rawhide Rolling Line
Would you like a mold catalog with images and dimensions, or would you prefer to develop a custom shape based on your brand or product concept?
Yes, we provide comprehensive operator training for the Rawhide Rolling Line to ensure smooth installation, commissioning, operation, and maintenance. This is a standard part of our service package for both domestic and international customers.
Our technicians travel to your facility for equipment installation and commissioning
Training sessions cover:
Equipment startup and shutdown procedures
Rawhide feeding, rolling adjustments, and mold usage
Troubleshooting and safety protocols
Daily and periodic maintenance
Duration: 3–5 days (depending on line complexity)
Via Zoom / Teams / WeChat / WhatsApp video call
Live demonstration during our in-house test runs
Real-time Q&A and documentation support
You are welcome to send your staff to our factory for hands-on training
We'll demonstrate the complete working process and train your team in advance
User operation manual (English or multilingual)
Maintenance checklist & lubrication schedule
Troubleshooting guide with error codes and solutions
Video tutorials and SOPs (Standard Operating Procedures)
Line operators
Maintenance technicians
Production supervisors
Would you like us to include on-site training and commissioning service in the quotation, and do you need support for multi-language training (e.g., Russian, Spanish, Arabic)?
У "The Rawhide Rolling Line requires the following utilities for efficient operation, depending on the configuration and level of automation:
Компонент | Напруга | Phase | Частота | Power Range |
---|---|---|---|---|
Main rolling machine | 380V (or 220V/415V on request) | 3-phase | 50/60 Hz | 3–7.5 kW |
Conveyor system | 0.75–1.5 kW | 3-phase | 50/60 Hz | Змінна |
Auxiliary equipment (if included: mold press, dryer) | up to 15–20 kW total (varies by model) |
🔧 Customization Available:
We can tailor the electrical system to match your country's voltage/frequency standards (e.g., 220V/60Hz for the U.S., 415V/50Hz for Australia).
Pressure: 0.6–0.8 MPa (6–8 bar)
Consumption: 300–500 L/min (depending on mold/cutter type)
Compressor: We can supply or recommend a suitable air compressor (7.5–11 kW typical)
Cooling Water (If included in forming or drying systems):
For hydraulic mold presses or water-jacketed systems
Flow: 50–100 L/h, Closed-loop system preferred
Pressure: ≥0.2 MPa
Washing/Soaking Tanks (If pretreatment is integrated):
Requires clean water connection and drainage system
May include recirculation or filtration options
Utility | Вимога |
---|---|
Електрика | 380V, 3-phase, 50/60Hz, 5–20 kW total |
Air | 0.6–0.8 MPa, 300–500 L/min |
Вода | Optional, based on auxiliary equipment |
Would you like us to provide a detailed utility layout plan with power/water/air inlet points for your engineering team?
У "The Rawhide Rolling Line comes with a standard warranty period of 12 months (1 year) from the date of equipment arrival at your site або commissioning, whichever comes first.
Mechanical Parts:
Rolling rollers
Shafts, gearboxes, and drive units
Conveyor frames and belt assemblies
Molds and pressing dies (standard wear covered under normal use)
Electrical Components:
Motors and inverters (VFDs)
PLC control system
HMI touchscreen
Sensors and limit switches
Relays, contactors, and breakers
Pneumatic and Hydraulic Systems (if included):
Air cylinders
Solenoid valves
Hydraulic pumps and control valves
Consumables (e.g., belts, gaskets, seals, lubricants)
Damage caused by improper operation, lack of maintenance, or non-original spare parts
Electrical issues from power surges or unstable supply (unless otherwise agreed)
Free replacement of faulty parts (shipping included for standard courier)
Remote technical support via video, call, or email
On-site service available (travel & lodging at buyer’s cost, labor free if under warranty)
You may request extended warranty (18 or 24 months) with a small added cost
Includes priority parts shipping and optional annual maintenance check
Would you like a sample warranty policy document or details on the spare parts package we typically supply with the line?
Так, у Rawhide Rolling Line offers a range of optional accessories and automation upgrades to boost efficiency, reduce labor, and enhance product consistency. These can be added based on your production scale, budget, and automation goals.
Feeding Conveyor System
Automatic feeding of rawhide sheets to the rollers
Adjustable speed and alignment guides
Reduces manual handling and increases throughput
Auto Thickness Controller
Digital adjustment and display of roller gap
Ensures consistent rawhide thickness across batches
Rolling Pressure Monitoring System
Real-time monitoring of roller pressure
Alerts for overload or under-pressure situations
Hydraulic or Pneumatic Press Mold (For Bone or Custom Shapes)
With quick-change mold feature
Custom shapes and logo imprint options
Cutting Unit (Manual or Automatic)
Inline rotary cutter or guillotine-style blade
Adjustable length cutting of rawhide strips after rolling
Drying Tunnel Integration (Hot Air or Microwave)
Direct connection to drying chamber after rolling
Reduces transfer time and improves line flow
Dust Collector / Dehairing Brush Unit
Optional cleaning unit for removing fine particles after rolling
PLC + HMI Centralized Control System
Synchronize all machine parameters and interlocks
Touchscreen interface with language options and recipe presets
SCADA or Remote Monitoring System
Real-time data logging and remote fault diagnostics
Great for larger factories or multi-line operations
Robotic Pick & Place (Post-Rolling Handling)
For stacking, sorting, or positioning before pressing or drying
Increases hygiene and labor savings
Auto Lubrication System
Extends roller and gear life with controlled oiling cycles
Energy-Saving Drives
High-efficiency motors and variable frequency drives (VFDs)
Reduces power consumption, especially in 24h operations
Package | Ідеально підходить для | Includes |
---|---|---|
Basic Automation | Startups & small factories | HMI control, feeding conveyor |
Standard Line+ | Medium production | Auto cutter, press mold, dryer integration |
Full Automation Pro | Large-scale producers | PLC+HMI, auto feed/cut, SCADA, robotic handling |
Would you like a proposal with upgrade options bundled by production capacity or a 3D layout showing how these accessories integrate into your factory line?
Так, у Rawhide Rolling Line is designed for containerized shipping, and all components are safely packed in standard export-grade wooden cases or steel frames, making it suitable for 20-foot or 40-foot containers, depending on the configuration.
1 × 20-foot container
Total Volume: approx. 12–18 m³
Total Gross Weight: approx. 2,000–3,000 kg
1 × 40-foot container (may use High Cube if dryer or bone press is large)
Total Volume: approx. 25–35 m³
Total Gross Weight: approx. 5,000–8,000 kg
Main rolling machine: steel-frame fixed or wooden crate
Conveyors, motors, electrical cabinets: individually packed
Molds and accessories: packed separately with clear labels
Waterproof & shockproof protection used for sea freight
FOB, CIF, or DDP terms available
Export customs clearance support
Container loading list and photos for your reference
SGS / BV inspection and fumigation certificate (if required)
Would you like a container loading diagram or packing list sample with weights and dimensions of each major component?
Yes, we provide professional installation and commissioning services for the Rawhide Rolling Line at the buyer’s site, ensuring that your equipment is fully operational, fine-tuned, and your team is trained for optimal use.
Assembly and positioning of the entire line
Electrical and pneumatic connections
Conveyor and mold alignment
Integration with existing equipment (if applicable)
Dry-run testing of all motors, controls, and interlocks
Load testing with actual rawhide materials
Adjustment of rolling thickness, feeding speed, pressure, and mold settings
Safety check and system calibration
Full training on startup/shutdown, product changeover, and cleaning
Fault diagnosis and emergency procedures
Routine maintenance and lubrication procedures
Our engineers will travel to your site after:
Equipment arrives
Utilities (electricity, air, water) are ready
Typical duration: 3–7 working days depending on system complexity
Installation labor: Free under warranty (within agreed scope)
Buyer covers:
Round-trip airfare
Local accommodation and meals
Daily service fee (if not bundled in contract – can be waived for full-line orders)
Installation guide (English or multilingual)
Factory Acceptance Test (FAT) checklist
Site Acceptance Test (SAT) report
Operator certification (optional)
Would you like the installation and commissioning to be included in the quotation, and do you have a preferred timeframe or site readiness date?
To provide an accurate total price for the Rawhide Rolling Lineв тому числі transport, installation, and training, we need to confirm a few key details first, as pricing depends on your required configuration and destination.
Production Capacity Requirement:
(e.g. 500 kg/h, 1000 kg/h, 2000 kg/h?)
Configuration:
Basic rolling only
Rolling + pressing
Full line (rawhide soaking → rolling → shaping → drying → packing)
Shipping Destination:
Country and nearest sea port or delivery address
Preferred Trade Term:
FOB, CIFабо DDP (door-to-door)?
Do you need us to arrange shipping?
Installation Location & Language Preferences:
Will you require on-site installation and training at your facility?
Any language preference for manuals and training (e.g. English, Spanish, Russian)?
Пункт | Unit Price (USD) |
---|---|
Rawhide Rolling Line | $22,000–$28,000 |
CIF Sea Freight (to EU Port) | $2,000–$3,000 |
On-Site Installation & Training (5 days) | $2,500–$3,500 |
Estimated Total | $26,500–$34,500 |
📌 This is just a reference. Exact pricing will vary based on technical specs, destination, and service options.
Would you like a formal quotation (Proforma Invoice) customized to your required capacity and destination? I can prepare it immediately if you confirm the points above.
У "The payment structure and terms for purchasing the Rawhide Rolling Line are flexible and structured to support smooth transactions for international buyers. Below is our standard arrangement, which can be adjusted based on order size, project scope, and customer profile.
30% deposit upon order confirmation and signing of sales contract
70% balance before shipment after equipment passes factory testing and buyer receives photos/videos or completes factory inspection
40% deposit to start production
20% progress payment after machine frame and key modules are completed
40% balance before shipment
Accepted for large orders (typically above $100,000)
Subject to approval by our finance department
L/C must be irrevocable and confirmed by a top-tier bank
Machine cost
Standard wooden packing
CE/ISO documentation
CIF shipping (if required)
Installation & training (if included)
Signed Commercial Invoice
Packing List
Bill of Lading / Air Waybill
Certificate of Origin (Form E, FTA, etc. if applicable)
CE Declaration, Test Report, Warranty Card
For long-term clients or strategic partners, custom installment plans may be arranged
Spare parts і extended warranties can be paid separately
Would you like us to include a payment schedule with milestone dates and documentation flow in your formal quote or proforma invoice?
Так, у Rawhide Rolling Line can be fully customized to match your local voltage, frequency, and national safety standards, ensuring smooth and compliant operation in your country.
We support all common industrial power standards:
Напруга | Phase | Частота | Supported? |
---|---|---|---|
380V | 3-phase | 50Hz | ✅ Standard |
220V | 3-phase | 60Hz | ✅ On request |
415V | 3-phase | 50Hz | ✅ Common for EU, AU |
440V | 3-phase | 60Hz | ✅ For USA / Canada |
Other voltages (e.g. 400V, 480V) | ✅ Fully supported with motor/inverter adjustments |
🔧 All motors, control panels, and protection devices are configured accordingly.
Compliant with IEC standards (or UL/CSA upon request)
Правильно grounding, overload protection, emergency stop included
Optional: thermal protection, phase failure relay, door interlock
Moving parts fully guarded with safety covers
Limit switches and interlocks prevent accidental operation
Emergency stop buttons at key locations
CE (standard for EU)
ISO 9001:2015 certified manufacturing process
UL / CSA / GOST / EAC optional depending on your country
Electrical layout with local standard wiring
Single-line diagrams with labeled terminal blocks
Operation manual in English (or translated as needed)
Declaration of Conformity and test reports
Would you like us to tailor the electrical system to your country’s standard (please share your local voltage/frequency), and include compliance with UL, GOST, or other specific standards in your quote?
We provide comprehensive after-sales support for the Rawhide Rolling Line, ensuring your production runs smoothly long after delivery. Our services include technical assistance, spare parts, remote diagnosticsі long-term maintenance support.
24/7 support via WhatsApp, WeChat, Email, or Video Call
Quick-response team for troubleshooting, parameter settings, and process optimization
For complex issues or major upgrades
Available globally—travel & accommodation to be covered by buyer
Discounted service fees for returning customers or full-line projects
Includes critical wear parts:
Conveyor belts
Roller bearings
Seals and gaskets
Sensors and switches
Fuses, relays, and contactors
Guaranteed 10+ years availability of standard parts
Fast dispatch of stocked items within 24–48 hours
Custom or CNC parts made to order in 5–10 days
Full parts list with exploded drawings
Part codes for easy reordering
Replacement cycles and compatibility info
Lifetime free PLC program backups
Firmware upgrades for HMI, control units, or smart modules
Optional cloud-based monitoring integration support
Package | Includes | Термін |
---|---|---|
Basic Annual Plan | Remote checkup + replacement advice | 1 year |
Premium Plan | Remote + 1 on-site visit/year | 1–2 years |
Turnkey OEM Support | Custom service contract | Multi-year |
Full operation & maintenance manuals
Preventive maintenance schedule
Online training refreshers (if needed)
Would you like us to include a recommended spare parts list and quote for an optional service contract with your Rawhide Rolling Line proposal?
У "The lead time for ordering spare parts for the Rawhide Rolling Line depends on the type of part and whether it is a standard in-stock item or a custom-made component. Here's a detailed breakdown:
These include:
Conveyor belts
Bearings, seals, belts
Sensors, switches
Electrical components (relays, contactors, fuses)
Pneumatic fittings and valves
⏱ Lead Time: 1–3 working days for dispatch
📦 Delivery:
Express courier (DHL/FedEx/UPS): 4–8 days internationally
Air cargo or sea freight: available for bulk orders
These include:
Rollers with custom dimensions
Mold sets and shaping dies
Structural frames or special brackets
Control panel upgrades or PLC/HMI modifications
⏱ Production Time: 5–12 working days
📦 Shipping: Similar to above; expedited options available
Send part code or photo (we provide a parts manual for easy ID)
Quotation and confirmation within 24 hours
Immediate dispatch if in stock or production starts same day
Tracking number and customs documents provided
Can be pre-packed and shipped with your machine
Includes all key wear parts and backup electronics
Minimizes downtime and avoids overseas shipping delays
Would you like a recommended spare parts kit list and price quote based on your selected configuration and expected daily runtime?
Yes, we offer remote diagnostics and online technical support for the Rawhide Rolling Line, ensuring fast and effective troubleshooting in case of breakdowns or performance issues—no matter where your facility is located.
Available 24/7 via:
WhatsApp / WeChat
Zoom / Teams / Google Meet
Email with video/photo diagnostics
Our engineers guide your team through:
Error code interpretation
Motor/roller reset procedures
HMI & PLC parameter adjustments
Sensor and actuator checks
с internet-enabled PLC or VPN connection, we can:
Access your control system remotely
Run diagnostics and edit programs live
Upload new firmware or recipes
🔐 Secure connection via TeamViewer, AnyDesk, or cloud SCADA
Troubleshooting flowcharts in the manual
Error code list with solutions
Video tutorials for mechanical adjustments or part replacement
Live video calls with bilingual engineers (English/Spanish/Chinese/Russian available)
If replacement parts are needed during breakdowns, we:
Identify the fault remotely
Confirm the part code
Ship express from our warehouse or produce urgently
Guide your team through the installation
Would you like to include the remote diagnostics module (with PLC access) in your system quote, or would basic online video support be sufficient for your technical team?
Yes, we provide comprehensive maintenance manuals and troubleshooting guides with every Rawhide Rolling Line. These documents are essential tools to help your team operate, service, and repair the machine efficiently.
Step-by-step startup and shutdown procedures
Detailed instructions for:
Roller gap adjustment
Mold change and alignment
Conveyor speed settings
Lubrication schedule and diagram
Daily, weekly, and monthly maintenance checklists
Complete list of error codes and alarm messages
Common issues and step-by-step solutions:
Motor not starting
Uneven rolling or jamming
Sensor faults or misalignment
Electrical and pneumatic fault flowcharts
How to reset the PLC or HMI interface
Exploded diagrams of all major assemblies
Part numbers for reordering
Replacement intervals and compatibility notes
Electrical single-line diagrams
PLC input/output maps
Control panel layout with terminal labeling
English (standard)
Optional: Spanish, Russian, Arabic, or Chinese upon request
Printed copy shipped with equipment
Digital PDF copies provided via email or USB drive
Video tutorials for key operations (e.g., mold change, sensor alignment)
Would you like a sample section of the manual or troubleshooting guide to review before ordering? I can also tailor the language and format based on your operators’ preferences.
Yes, we provide a recommended preventive maintenance schedule for the Rawhide Rolling Line to ensure long-term, stable operation and minimize downtime. The schedule is designed based on operating hours and component wear patterns.
✅ Check for unusual noises or vibrations
✅ Clean rawhide residue from rollers and conveyor
✅ Inspect and clean sensors and photoelectric eyes
✅ Wipe down electrical panel (no water spray)
✅ Drain air filters (if pneumatic)
✅ Check emergency stop function
✅ Lubricate roller bearings and gearboxes
✅ Tighten bolts, fasteners, chain drives
✅ Inspect conveyor belt tracking and tension
✅ Check mold press alignment (if included)
✅ Test HMI and PLC response speed
✅ Clean and check motor vents and fans
✅ Inspect pneumatic solenoids and air cylinders for leaks
✅ Check all electrical terminals and wiring for heat discoloration
✅ Calibrate roller thickness and pressure setting if necessary
✅ Review PLC data logs or alarm history
✅ Replace belts if worn
✅ Flush and replace gearbox oil if running under heavy load
✅ Check mold surfaces for wear or corrosion
✅ Inspect rollers for pitting, scratches, or uneven pressure marks
✅ Review production consistency (dimensions, shape quality)
Maintenance checklist logs (printable & digital)
Lubrication chart with grease/oil types and points
Maintenance training video for operators and technicians
Spare parts wear rate guide to forecast replacement needs
Would you like a customized maintenance calendar based on your expected daily operating hours (e.g. 8h/day, 16h/day), and should we include a spare parts kit tailored to that cycle?
Explore trends, tips, and innovations in Rawhide Rolling Line. Enhance efficiency and quality with expert insights.
Приготування домашнього сухого корму для собак – це корисний спосіб забезпечити збалансоване харчування вашої тварини
Приготування домашнього сухого корму для собак – це корисний спосіб забезпечити збалансоване харчування вашої тварини
Приготування домашнього сухого корму для собак – це корисний спосіб забезпечити збалансоване харчування вашої тварини
Приготування домашнього сухого корму для собак – це корисний спосіб забезпечити збалансоване харчування вашої тварини
Приготування домашнього сухого корму для собак – це корисний спосіб забезпечити збалансоване харчування вашої тварини
Приготування домашнього сухого корму для собак – це корисний спосіб забезпечити збалансоване харчування вашої тварини
давайте поговоримо про те, як ми можемо допомогти вам досягти ваших цілей і вивести ваш бізнес на новий рівень!
Розкажіть нам про свої потреби якомога конкретніше.
Ми знайдемо найкраще рішення і зробимо пропозицію відповідно до ваших вимог.
Ми почнемо виробництво після отримання вашого схвалення та депозиту, а також організуємо відвантаження.
- Не хвилюйтеся, ми теж ненавидимо спам!
- Телефонуйте лише тоді, коли кілька листів залишилися без відповіді!