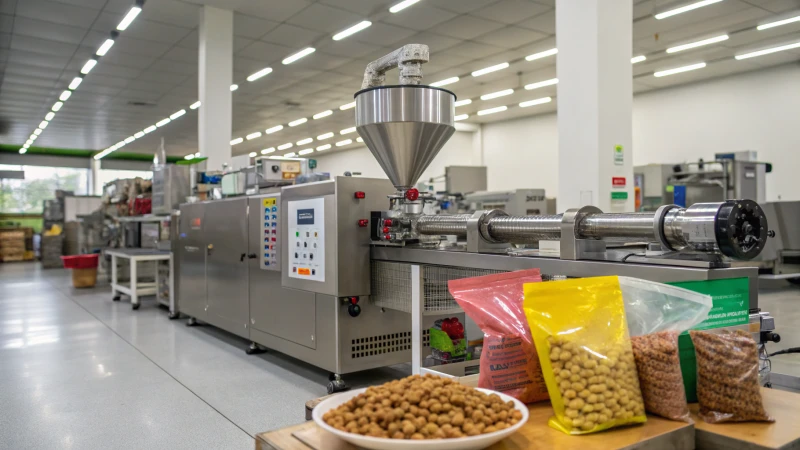
Maintaining pet food production machinery is crucial for ensuring that the equipment runs efficiently, produces high-quality products, and minimizes downtime. However, like any industrial machinery, pet food production equipment faces a variety of maintenance issues over time. Neglecting these problems can lead to costly repairs, compromised product quality, and even safety hazards. Identifying the most common issues early on is key to developing an effective maintenance strategy that minimizes disruptions. This article highlights the most frequent maintenance challenges faced by pet food manufacturers and offers practical solutions to mitigate them.
The most common maintenance issues in pet food production machinery include motor malfunctions, worn-out seals and gaskets, clogged conveyors, lubrication failures, overheating, and contamination buildup. Regular inspections, preventive maintenance, and timely repairs can help address these issues and ensure optimal machine performance.
Pet food production machinery is subject to heavy-duty operations, as it processes large volumes of ingredients, mixes, extrudes, and packages products. With such continuous use, it’s not surprising that equipment suffers from wear and tear. However, understanding the most common problems and addressing them proactively can drastically reduce costly repairs and downtime.
Most Common Maintenance Issues in Pet Food Production Machinery
1. Motor Malfunctions
Motors are the driving force behind most machines in the pet food production process, powering mixers, conveyors, extruders, and other equipment. Over time, these motors can develop issues such as overheating, electrical failures, or worn-out components like bearings.
Common Causes:
- Overheating: Excessive heat can cause motor failure if ventilation is inadequate or if the motor is under heavy load for extended periods.
- Electrical issues: Faulty wiring, electrical surges, or motor overloads can result in malfunction.
- Wear on bearings and shafts: As the motor components wear down, they lose efficiency and may eventually fail.
Solutions:
- Regularly inspect motor bearings for wear and replace them as needed.
- Ensure proper ventilation around motors and avoid overloading.
- Conduct periodic checks on electrical connections and wiring to prevent shorts or overloads.
2. Worn-out Seals and Gaskets
Seals and gaskets are used to prevent the leakage of raw materials, oils, and liquids, which could contaminate the product or damage equipment. Over time, seals can deteriorate due to constant exposure to harsh cleaning chemicals, high temperatures, or abrasive materials.
Common Causes:
- Exposure to harsh chemicals or heat.
- Abrasive ingredients, especially in the case of dry kibble or heavy-duty mixing.
- Infrequent maintenance checks leading to delayed identification of worn-out parts.
Solutions:
- Regularly inspect seals and gaskets for cracks or wear, and replace them promptly.
- Use high-quality, temperature-resistant materials that are compatible with the machine’s operating conditions.
- Perform regular cleaning and maintenance to avoid material buildup, which can cause gaskets to break down prematurely.
3. Clogged Conveyors
Conveyor systems are used throughout the production process to move ingredients and finished products from one stage to the next. Clogs in conveyor systems are common, especially in systems transporting powders, pellets, or sticky materials.
Common Causes:
- Material buildup on conveyor belts or inside tubes.
- Malfunctioning or misaligned conveyor parts.
- Improper cleaning that leaves debris behind.
Solutions:
- Schedule frequent cleaning and inspection of the conveyor system to remove any residue that may cause blockages.
- Check for misaligned parts, and ensure that belts or rollers are properly aligned and tensioned.
- Use conveyors with self-cleaning systems or adjustable speeds to reduce the chances of clogging.
4. Lubrication Failures
Many of the moving parts in pet food production machinery, such as gears, mixers, and extruders, rely on proper lubrication to function smoothly. When lubrication fails, it can lead to increased friction, wear, and even equipment breakdown.
Common Causes:
- Insufficient or improper lubrication.
- Contaminated or degraded lubricant.
- Infrequent maintenance checks.
Solutions:
- Regularly check lubricant levels and replace with the recommended type and amount of oil or grease.
- Clean lubrication systems to remove contaminants and ensure efficient operation.
- Train operators to monitor lubrication systems for signs of leakage or failure and address issues immediately.
5. Overheating and Cooling System Failures
Overheating is a common issue in many pet food production machines, especially those with motors, extruders, and dryers. When equipment overheats, it can lead to system failures, reduced efficiency, and even dangerous conditions in the workplace.
Common Causes:
- Insufficient cooling systems, such as fans or heat exchangers.
- Overuse of machines or prolonged operation at high temperatures.
- Inadequate maintenance of cooling components, such as filters or fans.
Solutions:
- Ensure that cooling systems are functioning properly by checking airflow and cleaning filters regularly.
- Install temperature sensors or alarms to monitor and alert operators of overheating issues.
- Establish scheduled downtimes to allow machines to cool and prevent prolonged use under high-temperature conditions.
6. Contamination Buildup
Contamination in production lines is a critical concern, especially when manufacturing pet food. Buildup of ingredients, oils, or other contaminants can result in poor product quality, safety violations, and machinery malfunctions.
Common Causes:
- Residue from raw materials sticking to machine parts.
- Infrequent or inadequate cleaning routines.
- Use of incompatible materials or improper handling of raw ingredients.
Solutions:
- Establish strict cleaning protocols, especially for machines in direct contact with food.
- Use machines designed for easy disassembly and cleaning.
- Ensure raw materials are properly stored and handled to prevent contamination before reaching the machines.
A bustling modern facility dedicated to pet food production.
Proactive Strategies for Addressing Maintenance Issues
1. Implementing a Preventive Maintenance Program
Preventive maintenance (PM) helps identify issues early before they evolve into larger, more expensive problems. Regularly scheduled checks for wear and tear, lubrication, cleaning, and part replacement can greatly reduce the occurrence of the above-mentioned issues.
PM Tasks:
- Daily visual inspections.
- Monthly deep cleaning of components.
- Annual parts replacement schedule for critical components.
2. Using Automated Monitoring and Diagnostics
Many modern pet food production machines are equipped with diagnostic tools and sensors that provide real-time performance data. These tools can alert operators to irregularities, such as unusual vibrations or temperature fluctuations, enabling quick intervention before a breakdown occurs.
Вигоди:
- Early identification of potential issues.
- Reduced downtime by preventing unplanned repairs.
- Improved overall efficiency of the production line.
Висновок
Understanding the most common maintenance issues in pet food production machinery and addressing them proactively can significantly reduce downtime, repair costs, and production inefficiencies. By focusing on regular inspections, lubrication, cooling, and contamination control, manufacturers can ensure that their equipment runs smoothly and that the final product is of the highest quality. Implementing a comprehensive preventive maintenance program, coupled with operator training, is essential for keeping machinery in optimal condition.
CTA: Contact Us
For more expert advice on maintaining your pet food production equipment or to schedule a consultation for custom maintenance solutions, contact us today. Our team is committed to helping you keep your machinery in top shape and ensuring the continued success of your production line.