Ever wondered what goes into creating the perfect pet meal?
Pet food production lines are categorized based on the process used: dry food production lines often use extrusion or baking, wet food lines involve canning or pouching, semi-moist lines use soft extrusion, and specialized lines cater to niche markets like freeze-dried or raw foods.
I remember the first time I walked through a bustling pet food factory, the air rich with the scent of fresh ingredients. It was then I realized how much artistry and precision go into crafting the meals we serve our pets. Each production line has its unique charm—be it the meticulous extrusion of dry kibble or the careful canning of wet food. Understanding these processes not only deepens my appreciation but also ensures our furry friends get the nutrition they deserve. Let me take you through these fascinating methods and their benefits.
Dry pet food is produced using extrusion.True
Extrusion is a common method for producing dry pet food.
Wet pet food lines use baking as a primary process.False
Wet pet food lines primarily use canning or pouching, not baking.
How Does the Extrusion Process Work for Dry Pet Food?
Have you ever stopped to ponder how your pet's dry kibble gets those fun shapes and irresistible crunch?
The extrusion process in dry pet food production involves cooking raw materials at high temperatures and pressures to form uniform kibble. The mixture is then cooled and dried, ensuring extended shelf life.
Understanding the Extrusion Process
I remember when I first walked into a pet food manufacturing plant; the sight of ingredients transforming into perfectly shaped kibbles was nothing short of mesmerizing. The extrusion process1 is truly the heart of this transformation. It all starts with mixing an array of raw materials—proteins, carbohydrates, fats, and vitamins—into a blend that would make any pet drool. This concoction is then ground until everything reaches a fine, uniform consistency.
Next, this mix enters the extruder, where it undergoes intense heat and pressure, akin to the way my grandma would pressure-cook her famous stew. This phase is crucial as it not only cooks the ingredients but also alters their nutritional profile, making them easier for our furry friends to digest while enhancing the flavors they can't get enough of.
Once the mix reaches just the right consistency, it's pushed through a die, much like squeezing toothpaste out of a tube, but way more exciting! The die can be adjusted to give the kibble various shapes and sizes, catering to even the fussiest of pets.
Cooling and Drying
After this culinary ballet, the kibble exits at a high temperature and needs some time to chill out—literally. Cooling is vital because it locks in its shape and texture while preventing spoilage. Picture this step as letting a freshly baked loaf of bread cool on the counter. The moisture content is reduced, securing the kibble's shelf life.
Once cooled, it's off to the dryer. This part reminds me of those days when I forgot my clothes in the dryer for just a bit too long—they'd come out dry as a bone. This stage ensures no moisture remains, safeguarding against mold or bacterial growth. The drying cycle might involve several stages to evenly reduce moisture across all the pieces.
Flavoring and Packaging
To make sure each bite is as delicious as possible, flavoring agents are often added. Imagine sprinkling your favorite seasoning over popcorn—that's what happens here but with oils or powder coatings that are designed to tickle your pet's taste buds. Finally, packaging seals in all that goodness until it’s ready to delight your pet’s palate.
Table: Key Stages in Extrusion Process
Stage | Function |
---|---|
Mixing | Combines raw ingredients |
Grinding | Ensures uniform size |
Cooking | Utilizes heat/steam for cooking |
Shaping | Forms kibble through a die |
Cooling | Reduces temperature |
Drying | Removes excess moisture |
Flavoring | Enhances taste with coatings |
Packaging | Protects and preserves product |
Technological Innovations
It's fascinating to see how modern extrusion technologies have evolved. With advanced control systems now managing temperature and pressure2 with pinpoint precision, we can ensure that every batch of kibble is consistently top-notch in quality. As consumer awareness around grain-free or organic options grows, manufacturers are innovating constantly to adapt to these preferences, often requiring specialized equipment tweaks.
Understanding these intricate steps helps one appreciate the complexity involved in crafting dry pet food that not only meets nutritional standards but also caters to our pets' discerning tastes. As the industry continues to innovate, focusing on sustainability and health benefits will be key in keeping our furry friends happy and healthy.
Extrusion enhances pet food digestibility.True
High temperature and pressure in extrusion alter nutrients, improving digestibility.
Cooling kibble increases its moisture content.False
Cooling reduces moisture to prevent spoilage and extend shelf life.
What Are the Advantages of Baking Process Lines?
Have you ever wondered how the cookies in your favorite bakery taste so consistently delicious?
Baking process lines streamline food production by automating tasks, improving consistency, and ensuring quality. They reduce labor costs, increase throughput, and support diverse product ranges, making them vital in competitive markets.
Enhanced Efficiency and Automation
I remember the first time I walked into a bustling bakery, the aroma of freshly baked bread filled the air. It was mesmerizing to see how seamlessly everything flowed. That's what baking process lines bring to the table—efficiency and automation. These systems cut down on manual labor and let production run continuously3 with minimal human intervention. This means you can bake more goodies faster and without breaking the bank.
Consistency in Product Quality
It's always a letdown when your favorite treat doesn't taste the same as last time, right? That's why consistency is king. Baking lines ensure each batch of cookies, bread, or pastries meets the same high-quality standards. With precise control over baking parameters like temperature and timing, your products will look, taste, and feel just as they should every single time. By using advanced sensor technologies4, manufacturers can monitor and adjust processes in real-time.
Flexibility and Product Diversification
If there's one thing I've learned, it's that the market never stands still. Tastes change, and new trends pop up all the time. Modern baking lines are like culinary chameleons—they can adapt to different recipes and formats with ease. This flexibility allows you to keep up with consumer demands without overhauling your entire setup.
Feature | Description |
---|---|
Automation | Reduces manual labor; increases speed and precision |
Consistency | Uniform product quality through controlled processes |
Flexibility | Adaptable to diverse products with modular systems |
Cost Reduction and Energy Efficiency
Initially, setting up a baking line might seem pricey, but believe me, it's an investment that pays off. By optimizing energy use with advanced energy management systems5, you save on resources and reduce waste. This not only cuts costs but also helps you run a more sustainable operation.
Improved Safety and Hygiene Standards
In food production, safety and hygiene aren't just optional extras—they're essential. Baking lines are designed to minimize contamination risks with closed systems and automated cleaning functions. This ensures everything stays spotless without bringing production to a halt.
Investing in a baking process line is like having a secret weapon in your culinary arsenal. It boosts product quality, trims costs, and elevates efficiency. Tailor these systems to your specific needs, and watch your business rise like dough in a warm oven.
Baking lines reduce manual labor significantly.True
Automation in baking lines decreases the need for human intervention.
Baking process lines cannot handle diverse products.False
Modern lines are flexible, accommodating various recipes and formats.
How Are Canned Wet Foods Manufactured Safely?
Ever wondered how that trusty can of pet food is made safe for your furry friend? Let's take a closer look at the journey from raw ingredients to sealed can.
Canned wet foods are manufactured safely through processes including ingredient pre-treatment, mixing, filling, sealing, and sterilization. These steps ensure that the final product is free from harmful microorganisms, preserving its safety and nutritional value.
Ingredient Pre-Treatment
When I think about the beginning of the pet food manufacturing process, it reminds me of prepping dinner in my own kitchen. Just like I rinse and chop vegetables to remove dirt and unwanted bits, pet food manufacturers start by meticulously cleaning and cutting raw materials. This step is essential—it's all about making sure that nothing harmful sneaks into your pet’s meal right from the get-go.
Mixing and Formulation
Next, the ingredients are mixed with precision, similar to following a favorite recipe to ensure the perfect balance of flavor and nutrition. Advanced machines take over this process, blending everything to ensure that every bite your pet takes is just as delicious and nutritious as the last. I can imagine it like using my trusty mixer to whip up a smooth cake batter without lumps.
Filling and Sealing
The mixed concoction then heads to filling and sealing—think of it as carefully ladling soup into jars for canning at home. This stage happens under strict hygiene conditions, sealing in freshness while keeping out unwanted guests like bacteria. It's comforting to know that each can is tightly sealed, locking in all that goodness until it’s ready to be served.
Process | Purpose |
---|---|
Ingredient Pre-Treatment | Remove contaminants before processing |
Mixing and Formulation | Ensure consistency and nutritional balance |
Filling and Sealing | Maintain freshness and prevent contamination |
Sterilization for Safety
Sterilization is akin to pressure cooking—a bit like how I make sure my homemade preserves last through the winter months. The cans are subjected to high-temperature steam or pressure cooking, ensuring that anything harmful is eliminated. This process not only extends the shelf life but also means no artificial preservatives are necessary.
Quality Control Measures
Quality checks throughout each stage remind me of taste-testing meals before serving them to guests. Automated systems ensure everything meets the highest standards, giving us peace of mind that every batch is just right. From ingredient sourcing6 to packaging, it's all about maintaining that perfect balance between safety and flavor.
Regulatory Compliance
Finally, adhering to regulations is much like following a trusted cookbook—ensuring everything is done correctly and safely. Organizations like the FDA provide guidelines for pet food manufacturing7, reassuring pet owners that their furry companions are getting only the best. This compliance not only ensures product safety but also builds trust with consumers like you and me.
Ingredient pre-treatment eliminates all pathogens.False
Pre-treatment reduces but may not eliminate all pathogens; sterilization completes this.
Sterilization extends shelf life without preservatives.True
High-temperature steam or pressure cooking kills microorganisms, extending shelf life.
Why is freeze-drying the best choice for premium pet foods?
Uncover the secret behind why freeze-drying is the go-to method for crafting top-tier pet foods, ensuring every bite is packed with nutrients and flavor.
Freeze-drying is ideal for high-end pet foods because it retains more nutrients, enhances flavor, and maintains the texture of raw ingredients. This process extends shelf life without preservatives, making it a premium choice.
Nutrient Retention
I remember the first time I considered switching my pet's food to freeze-dried options. I was amazed by how this method keeps all those essential nutrients locked in. Freeze-drying removes moisture at low temperatures, unlike conventional heat-based drying, ensuring vitamins and minerals stay intact. This approach has been a game-changer for my pet’s health, and I'm always learning more about nutrient retention here8.
Flavor and Palatability
When I first gave my pet freeze-dried food, the reaction was priceless. It's like they were tasting something truly fresh! This method enhances flavor by concentrating natural tastes, making pet food more palatable. The aroma and taste are so irresistible that even the pickiest eaters enjoy it. I've been fascinated by the science behind flavor enhancement ever since reading this9.
Structure and Texture
Maintaining that raw-like texture is crucial for our furry friends' instincts. It's not just about nutrition—it's about giving them an experience they love. Freeze-dried foods do just that, retaining a texture that appeals to pets' natural preferences.
Method | Texture Preservation |
---|---|
Freeze-Drying | Excellent |
Heat Drying | Poor |
Air Drying | Moderate |
Shelf Life and Preservation
I appreciate how freeze-dried foods resist spoilage without artificial preservatives. It means I can stock up without worrying about waste. The extended shelf life is a huge plus in my household, and it's fascinating to understand the preservation process in detail10.
Cost vs. Quality
While initially hesitant about the cost, I've realized the investment is worth it for my pet’s well-being. Freeze-drying might be pricier due to specialized equipment, but the quality of the product justifies every penny. It's comforting to know my pet enjoys nutritional value, storage ease, and overall health benefits.
Environmental Impact
I try to make eco-conscious choices whenever possible. Freeze-drying does consume energy, but it offers eco-friendly packaging options due to reduced weight and volume, lowering the carbon footprint during transport. It's enlightening to learn about these environmental impacts here11.
Overall, embracing freeze-drying for my pet's diet has been one of the best decisions I've made. The premium quality, long shelf life, and enhanced nutritional profile make it an unmatched choice in high-end pet food production.
Freeze-drying retains more nutrients than heat drying.True
Freeze-drying preserves nutrients by removing moisture at low temperatures.
Freeze-dried pet foods require artificial preservatives.False
Freeze-dried foods resist spoilage without artificial preservatives due to low moisture.
How Do Semi-Moist Production Lines Combine Dry and Wet Methods?
Ever wonder how semi-moist pet foods manage to be both soft and shelf-stable? It's like having your cake and eating it too!
Semi-moist production lines merge dry extrusion with controlled moisture infusion, achieving a soft texture and extended shelf life. This process balances the benefits of dry and wet methods for optimal pet food.
Understanding the Semi-Moist Process
Imagine opening a bag of pet food and finding it just the right texture—not too crunchy, not too soggy. That's the magic of semi-moist pet foods, which maintain a delightful softness with a moisture content of 15%-30%. This keeps them stable on the shelf, straddling the line between dry kibble and wet canned delights. It all kicks off with raw material pre-treatment12, where ingredients are carefully mixed to perfection.
Merging Dry and Wet Techniques
In my journey through the world of pet food production, I've seen how semi-moist lines use a soft extrusion process to work their magic. The beginning stages mimic dry pet food production with high-temperature extrusion. But here's the twist—post-extrusion, moisture-infusing agents are introduced, giving that soft texture akin to wet food.
I remember watching as moisture and flavoring agents were blended in, a pivotal step that shapes the taste profile13. It's fascinating to see how this enhances palatability, ensuring our furry friends keep coming back for more.
Quality Control and Packaging
Maintaining the quality of semi-moist foods is no small feat. I learned that during the cooling phase, moisture levels are closely monitored to prevent spoilage and stabilize the product.
Process Stage | Key Actions | Desired Outcome |
---|---|---|
Raw Material Pre-treatment | Selection & Mixing | Consistent Quality |
Soft Extrusion | High-Temp Processing | Structure Formation |
Moisture Infusion | Blending & Flavoring | Palatable Texture |
Cooling & Packaging | Moisture Control | Shelf Stability |
Packaging wraps up the process, using advanced materials to ensure freshness without refrigeration. It's all about offering convenient pet food options that boast nutritional benefits14 alongside easy storage.
These methods showcase how semi-moist production lines creatively merge the best aspects of both dry and wet pet food techniques. It's truly an innovative approach that keeps pet owners and their companions happy.
Semi-moist pet food has 15%-30% moisture content.True
Semi-moist pet foods are crafted to maintain a moisture content between 15%-30%.
Moisture agents are added before extrusion in semi-moist foods.False
Moisture and flavoring agents are blended into the product post-extrusion.
Why Are Specialty Production Lines Crucial for Niche Markets?
Have you ever wondered why some brands seem to know exactly what you want, even before you do?
Specialty production lines are crucial for niche markets because they enable manufacturers to tailor products to specific consumer preferences and requirements. This customization fosters brand loyalty, increases market competitiveness, and meets regulatory standards unique to niche products.
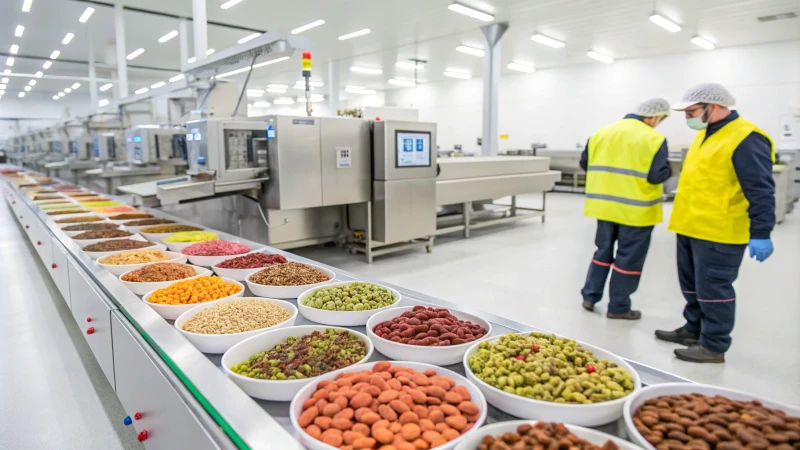
Customization for Unique Consumer Preferences
You know, sometimes I find myself craving a particular kind of treat that isn’t just your everyday option. It’s like when I discovered grain-free snacks for my pet—something regular production lines just couldn’t accommodate. Specialty production lines step in here, allowing manufacturers to tweak ingredients, sizes, and even packaging to meet those unique needs, much like finding that perfect snack that hits the spot. Imagine the pet food industry where consumers are now looking for grain-free or organic options; these lines cater precisely to those demands, meeting precise consumer needs15.
Enhancing Brand Loyalty and Market Position
I remember when I stumbled upon a brand that really understood what I was looking for—it was like they read my mind. Offering products that align perfectly with niche demands can significantly boost brand loyalty. When businesses cater to these unique needs, they don’t just sell a product; they build trust. This trust turns into long-term engagement and positions the brand as a specialist in the field. Picture the feeling of seeing your favorite brand in a crowded aisle and knowing they’ve got your back, leading to increased customer trust16.
Compliance with Regulatory Standards
Navigating through regulations can feel like trying to solve a complex puzzle. Many niche markets come with their own sets of rules, like organic food or eco-friendly products. Specialty production lines are designed to tackle these challenges head-on, ensuring compliance without skimping on quality. It’s like having a reliable guide who knows all the shortcuts to keep you on track and out of trouble, ensuring regulatory compliance17.
Table: Benefits of Specialty Production Lines for Niche Markets
Benefit | Description |
---|---|
Customization | Allows for tailored products that meet specific consumer preferences. |
Brand Loyalty | Fosters trust and long-term engagement by addressing niche market needs. |
Regulatory Compliance | Ensures products meet niche-specific standards and regulations. |
Competitive Advantage | Differentiates brand offerings in a crowded market. |
Technological Innovations in Production
Technology often feels like that magic wand we all wish we had—a tool that makes things possible with just a wave. In production, technological advancements have empowered specialty lines with automation and precision engineering, making it easier to adapt quickly to market changes while reducing waste. It’s like upgrading from a bike to a rocket ship in terms of speed and efficiency, facilitated by technological advancements18.
Case Study: Pet Food Industry
Let me take you through a journey in the pet food industry, where specialty production lines have transformed the way manufacturers operate. From grain-free kibble to freeze-dried raw meals, these lines allow producers to offer a diverse array of products that keep pace with health-focused consumer trends. It’s like having an endless buffet of options that cater precisely to what your pet needs, driving innovation and setting new industry standards—illustrating how niche specialization can drive industry innovation19.
Specialty lines enhance brand loyalty by meeting niche needs.True
Catering to niche demands builds trust and long-term customer engagement.
Standard production lines meet all niche market requirements.False
Standard lines lack customization needed for specific consumer preferences.
Conclusion
Pet food production lines vary by process: dry, wet, semi-moist, freeze-dried, and specialty lines cater to diverse nutritional needs and consumer preferences in the pet food industry.
Learn how extrusion transforms raw ingredients into nutritious kibble with precise shapes and textures. ↩
Discover innovations that ensure optimal cooking conditions for consistent pet food quality. ↩
Explore how continuous baking systems enhance production efficiency by reducing manual intervention and operational downtime. ↩
Discover how sensor technologies improve product consistency by allowing real-time monitoring and adjustments during baking. ↩
Learn about energy management systems that optimize resource use in food production, lowering costs and increasing efficiency. ↩
Explore how sourcing high-quality ingredients impacts the safety and nutritional value of pet food. ↩
Understand how FDA regulations ensure the safety and quality of pet foods in the market. ↩
Discover how freeze-drying better preserves nutrients compared to other drying methods. ↩
Understand why pets find freeze-dried foods more flavorful and aromatic. ↩
Learn about the natural preservation advantages of freeze-drying. ↩
Explore how freeze-drying affects the environment compared to other processing methods. ↩
Discover how initial ingredient handling impacts the final product quality in pet food manufacturing. ↩
Learn why flavoring is crucial for enhancing the palatability of pet foods. ↩
Explore how semi-moist foods provide balanced nutrition for pets. ↩
Explores the importance of customization in meeting specific consumer preferences within niche markets. ↩
Discusses how addressing niche market needs can build trust and long-term customer relationships. ↩
Provides insights into compliance with regulatory standards crucial for niche markets like organic food. ↩
Examines innovations that enhance efficiency and adaptability in specialized manufacturing. ↩
Analyzes how specialty production lines drive innovation in response to niche consumer trends. ↩