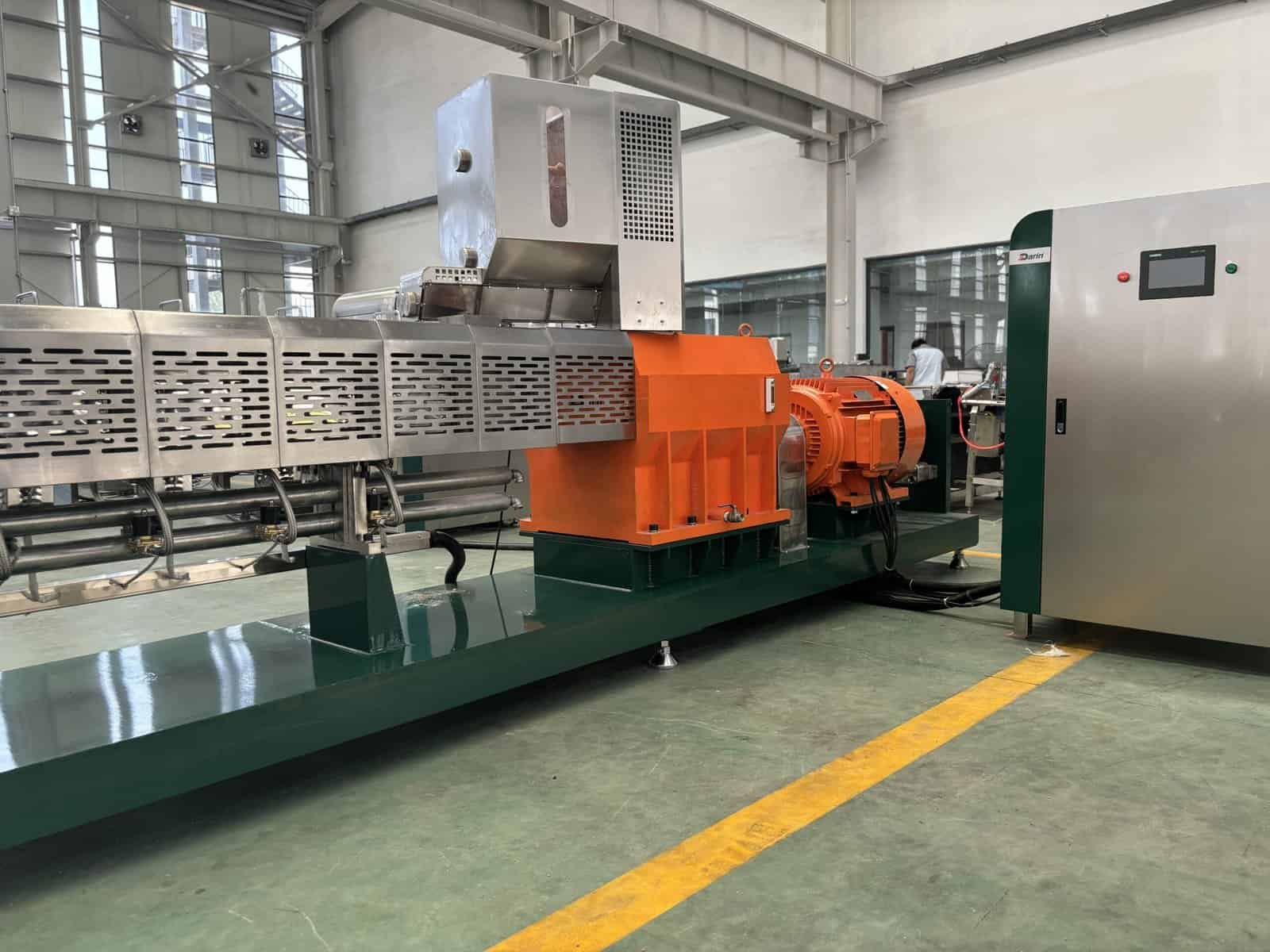
Двухшнековые пищевые экструдеры занимают центральное место в современных линиях по переработке пищевых продуктов, производя все: от кормов для домашних животных и закусок до текстурированного белка. Но за их высокой производительностью стоит вопрос, который часто имеет решающее значение для производителей: сколько энергии потребляют эти машины? Без четкого ответа производители рискуют недооценить эксплуатационные расходы, перегрузить системы электроснабжения или упустить ключевые возможности для повышения энергоэффективности. К счастью, понимание энергетического профиля двухшнековых экструдеров позволяет проводить обоснованное планирование, оптимизировать производство и экономить средства в долгосрочной перспективе.
Типичный промышленный двухшнековый пищевой экструдер потребляет от 30 до 500 киловатт (кВт) электроэнергии в зависимости от его размера, мощности, применения, конструкции шнека и формулы материала. Большинство систем среднего масштаба работают при 75–150 кВт во время работы. Потребление энергии зависит от мощности двигателя, нагревательных элементов цилиндра, систем охлаждения, подающих устройств и оборудования, расположенного ниже по потоку.
Если вы оцениваете производственные затраты или планируете электроснабжение вашего завода, читайте дальше. Мы разберем реальные диапазоны потребления, факторы, влияющие на потребление энергии, и как оптимизировать использование энергии.
\
Двухшнековые экструдеры потребляют значительно больше энергии, чем одношнековые.Правда
Благодаря конфигурации с двумя приводами, конструкции с распределением крутящего момента и, как правило, более высокой производительности двухшнековые экструдеры потребляют больше электроэнергии, чем одношнековые аналоги.
🔧 Факторы, влияющие на потребление энергии в двухшнековых экструдерах
1. Установленная мощность двигателя
Большая часть энергии в двухшнековом экструдере потребляется приводным двигателем. В зависимости от размера приложения:
Размер экструдера | Установленная мощность двигателя (кВт) | Пропускная способность (кг/ч) | Типичное применение |
---|---|---|---|
Лабораторные масштабы | 3–11 кВт | <50 | НИОКР, университеты |
Мелкомасштабные | 15–45 кВт | 100–500 | Закуски, сухие завтраки |
Средний масштаб | 55–132 кВт | 500–1500 | Корм для домашних животных, воздушные закуски |
Крупномасштабные | 160–500+ кВт | 2000–10000+ | Высокообъемный белок, корм для водных животных |
- КПД двигателя (часто выше 90% в современных системах) также влияет на фактическое потребление энергии.
- Коэффициент нагрузки (процент использования двигателя во время фактической работы) имеет значение: многие экструдеры работают с мощностью двигателя от 60 до 90%.
2. Нагревательные элементы и зоны ствола
Экструдеры используют электрические нагреватели для контроля температуры процесса:
- Каждая зона ствола (обычно 5–12 зон) использует отдельные электрические нагревательные элементы.
- Средняя энергия на зону: 3–10 кВт в зависимости от длины зоны и целевой температуры.
- Для 7-зонного экструдера общая потребность в тепле может составлять от 20 до 70 кВт.
Количество зон ствола | Общая мощность нагрева (кВт) |
---|---|
5 зон | 15–40 кВт |
7 зон | 20–70 кВт |
10+ зон | 40–100+ кВт |
Совет: Системы предварительной подготовки (например, паровые кондиционеры) могут снизить потребность в нагреве внутри бочки, но увеличить потребление энергии пара.
3. Система кормления и вспомогательное оборудование
- Гравиметрические или объемные дозаторы: Обычно потребляют 0,5–2,0 кВт на единицу.
- Системы резки, конвейеры и сушилки ниже по течению также потребляют электроэнергию.
- Полная экструзионная линия общая мощность = мощность экструдера + последующее оборудование (может удвоить общую энергию системы).
4. Характеристики материала и рецептура
- Высокожирные или высоковлажные исходные материалы как правило, для обработки требуется меньше энергии.
- Плотные крахмалы и белковые смеси (например, соевый TVP или корм для собак) требуют более высокого крутящего момента и более длительного времени обработки.
Тип ввода | Относительный спрос на энергию |
---|---|
Кукурузная крупа, рис | Низкий |
Изолят соевого белка | Средний |
Смеси пшеничного глютена | Высокий |
Побочные продукты, богатые клетчаткой | Очень высокий |
\
Влажность исходного материала не влияет на потребление энергии.Ложный
Содержание влаги существенно влияет на потребление энергии — более высокая влажность снижает требования к трению и крутящему моменту, уменьшая общее потребление энергии.
⚡ Примеры потребления энергии
✅ Пример из практики: Линия по производству кормов для домашних животных (Darin Machinery DSE-65)
- Тип экструдера: Двухшнековый, диаметр шнека 65 мм
- Двигатель: Главный привод 75 кВт
- Зоны нагрева: 6 × 5 кВт = 30 кВт
- Устройство подачи и резка: 3 кВт комбинированная
- Общая потребляемая мощность при нагрузке 85%: ≈ 90–95 кВт
- Пропускная способность: 500–800 кг/ч
- Удельное потребление энергии (УПЭ): \~0,12–0,18 кВтч/кг
✅ Пример: Линия TVP (текстурированный растительный белок)
- Экструдер: Двухшнековый, 100 мм
- Главный двигатель: 160 кВт
- Нагрев ствола: 8 зон × 7 кВт = 56 кВт
- Охлаждение + Подача: 4 кВт
- Общая эксплуатационная нагрузка: 180–200 кВт
- Выход: \~1500 кг/ч
- СЕКРЕТ: \~0,13 кВтч/кг
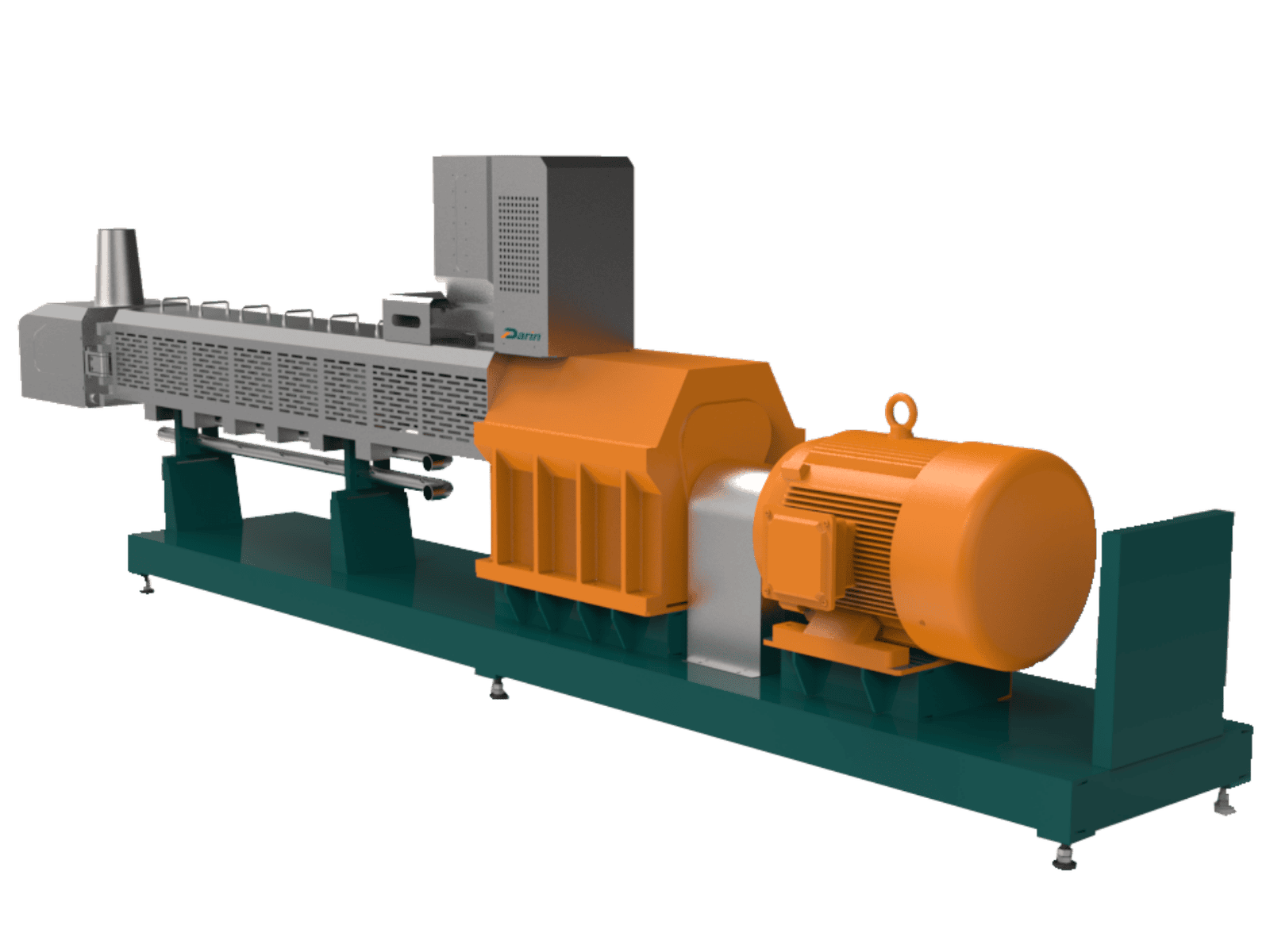
📈 Как оценить энергопотребление вашего двухшнекового экструдера?
Используйте это формула оценки энергии:
Всего кВтч в час = Мощность двигателя (кВт) × Коэффициент нагрузки + Мощность нагрева (кВт) + Питатель + Вспомогательное оборудование (кВт)
Затем вычислите Удельная энергия (УЭ):
SEC (кВт·ч/кг) = Общее количество кВт·ч в час ÷ Выработка в кг/ч
Компонент | Ввод формулы | Пример (линия средней шкалы) |
---|---|---|
Мощность двигателя | 110 кВт | 110 |
Коэффициент нагрузки (70%) | 0.7 | 77 |
Мощность нагрева | 40 кВт | 40 |
Вспомогательное оборудование (податчик/резчик) | 3 кВт | 3 |
Всего кВтч в час | — | 120 кВтч |
Выход | — | 1000 кг/ч |
СЕЦ | — | 0,12 кВтч/кг |
🔋 Стратегии энергосбережения для двухшнековых экструдеров
- Используйте приводы VFD (Частотно-регулируемые приводы): оптимизируют обороты двигателя и снижают нагрузку на холостом ходу.
- Улучшить изоляцию: Предотвращает потери тепла вокруг зон ствола.
- Переключиться на индукционный нагрев: Более эффективно и отзывчиво, чем резистивный нагрев.
- Используйте прекондиционеры: Снижение тепловой нагрузки на ствол и требуемого крутящего момента двигателя.
- Текущее обслуживание: Предотвращает износ шнека и скачки трения в цилиндре.
- Выберите правильную конструкцию винта: Минимизируйте крутящий момент и нарастание давления.
- Мониторинг нагрузки и автоматизация: Выявляйте и адаптируйтесь к моделям спроса в реальном времени.
\
Стоимость энергии является незначительным фактором в окупаемости инвестиций в экструзионную линию.Ложный
Затраты на электроэнергию часто являются второй по величине статьей эксплуатационных расходов после сырья при экструзионных операциях, особенно при крупномасштабном круглосуточном производстве.
📊 Сравнение: энергопотребление одношнекового и двухшнекового экструдера
Параметр | Одновинтовой | Двухвинтовой |
---|---|---|
Мощность двигателя (типичная) | 15–55 кВт | 30–500+ кВт |
Энергия на кг продукции | 0,08–0,12 кВтч/кг | 0,12–0,25 кВтч/кг |
Гибкость и контроль рецептов | Ограниченный | Высокий |
Диапазон пропускной способности | Узкий | Широкий |
Подходит для сложных рецептов? | Нет | Да |
✅ Заключительные мысли
Двухшнековые экструдеры — мощные, гибкие и незаменимые в современной пищевой промышленности, но их энергопотребление необходимо понимать и контролировать. Выбирая правильную производительность, оптимизируя конфигурацию и применяя меры по энергосбережению, производители могут сбалансировать производительность с устойчивостью и экономической эффективностью.
📩 Свяжитесь с нами для индивидуального анализа энергопотребления
Darin Machinery специализируется на разработке энергоэффективных двухшнековых экструдеров для кормов для домашних животных, закусок, TVP и т. д. Свяжитесь с нашей технической командой, чтобы оценить ваше конкретное применение и получить индивидуальный профиль мощности, который соответствует вашим целям по выходу и при этом минимизирует потери энергии.
👉 Электронная почта: darin4@darin.cn
👉 Веб-сайт: https://petreatsmachine.com/
👉 Запросите расценки или консультацию сегодня!
5. Часто задаваемые вопросы
В1: Сколько энергии обычно потребляет двухшнековый экструдер для пищевых продуктов?
A1: Двухшнековый пищевой экструдер обычно потребляет от 30 кВт·ч – 200 кВт·ч, в зависимости от его мощности, пропускной способности материала и мощности двигателя. Небольшие экструдеры для лабораторного или научно-исследовательского использования могут потреблять всего 5–20 кВт·ч, в то время как крупные промышленные модели, обрабатывающие несколько тонн в час, могут превышать 150 кВт·ч. Такие факторы, как диаметр шнека, соотношение длины к диаметру (L/D) и параметры процесса, также влияют на потребление.
В2: Какие факторы влияют на энергопотребление двухшнековых пищевых экструдеров?
A2: Ключевые факторы включают в себя:
- Размер и эффективность двигателя (более крупные двигатели потребляют больше мощности),
- Скорость вращения шнека и выходной крутящий момент,
- Тип материала и влажность,
- Конфигурация и сопротивление матрицы,
- Параметры температуры и давления процесса,
- Время работы и производственная загрузка.
Оптимизация в каждой области может значительно сократить потребление энергии.
В3: Как рассчитать эксплуатационные расходы двухшнекового пищевого экструдера?
A3: Чтобы рассчитать эксплуатационные расходы:
- Определить потребление кВт/ч в час (из технических характеристик или измерителя мощности),
- Умножить на количество часов, отработанных в день, затем
- Умножьте на местный тариф на электроэнергию за кВт·ч..
Пример: если ваш экструдер потребляет 100 кВт⋅ч и работает 8 часов в день по цене $0.10/кВт⋅ч, то ежедневные затраты = $80.
В4: Является ли двухшнековый экструдер более энергоэффективным, чем одношнековый?
A4: Двухшнековые экструдеры часто потребляют больше энергии, но предлагают более высокая производительность, лучший контроль и равномерное смешивание, что приводит к более высокая общая эффективность на килограмм продукции. Они особенно эффективны в условиях высокой влажности, сложной рецептуры или многофункциональных установок обработки.
В5: Как можно оптимизировать потребление энергии при двухшнековой экструзии?
A5: Для оптимизации:
- Используйте энергоэффективные двигатели (IE3 или IE4),
- Поддерживайте правильную конфигурацию шнеков для вашего рецепта,
- Уменьшение ненужного крутящего момента и давления за счет улучшенной конструкции штампа,
- Внедрение управления ПЛК для точной регулировки температуры и двигателя,
- Регулярно проводите техническое обслуживание компонентов, чтобы избежать механических потерь..
Системы мониторинга энергопотребления также могут помочь точно настроить потребление энергии на основе данных в режиме реального времени.
6. Ссылки
- Двухшнековые экструдеры – Обзор потребления энергии – https://www.sciencedirect.com/topics/engineering/twin-screw-extruder - ScienceDirect
- Оптимизация энергии экструзии – https://www.extru-techinc.com/articles/energy-optimization - Extru-Tech
- Сравнительное исследование одношнековых и двухшнековых экструдеров – https://www.researchgate.net/publication/347548901 - ResearchGate
- Руководство по эффективной экструзии – https://www.thermofisher.com/blog/materials/5-ways-to-reduce-energy-use-in-extrusion/ – Термо Фишер
- Практическое руководство по двухшнековой экструзии – https://www.polymerextrusionguide.com – Руководство по экструзии полимеров
- Что влияет на потребление энергии экструдером – https://www.ptonline.com/articles/tips-and-techniques-energy-management-for-extruders – Технология пластмасс
- Пищевая экструзия и использование энергии – https://www.springer.com/gp/book/9783030419616 – Спрингер
- Энергетические показатели двухшнекового и одношнекового двигателей – https://www.azom.com/article.aspx?ArticleID=19708 – АЗоМ
- Конструкция и работа двухшнековых экструдеров – https://onlinelibrary.wiley.com/doi/book/10.1002/9781119609020 – Уайли
- Как экономить энергию в процессах экструзии – https://www.processingmagazine.com/process-equipment/energy-efficiency/article/15583746 – Журнал обработки