Ever wondered how your pet's favorite kibble is made?
The extrusion process in pet food production involves blending raw ingredients, cooking them under high pressure and temperature, and then shaping them into pellets or kibbles. This method enhances digestibility and nutritional value while ensuring shelf stability.
I remember the first time I walked through a bustling pet food manufacturing plant, the air thick with the warm, savory aroma of cooking kibble. It was mesmerizing to see raw ingredients transformed into perfectly shaped nuggets that our furry friends love. Each step in this process is carefully calibrated to ensure not just flavor, but also the nutritional integrity that keeps pets healthy and happy. Let me take you through each stage and show you how it all comes together to meet different dietary needs and consumer demands.
A extrusão melhora a digestibilidade dos alimentos para animais de estimação.Verdadeiro
The cooking process in extrusion breaks down starches, improving digestibility.
A extrusão diminui o valor nutricional dos alimentos para animais de companhia.Falso
Extrusion preserves and sometimes enhances nutrients through controlled cooking.
What Are the Main Steps in the Extrusion Process?
Extrusion might seem complex, but breaking it down reveals a fascinating process shaping materials in everyday products.
The extrusion process involves five main steps: feeding, melting, mixing, forming, and cooling. Each step is crucial for transforming raw materials into a continuous profile with specific dimensions and properties.
When I first stepped into the world of extrusion, I was both fascinated and a bit overwhelmed by the intricacies involved. It reminded me of watching my grandmother make pasta from scratch—feeding the dough through a roller, adjusting the thickness, and finally cutting it into perfect strands. The extrusion process is similar, but on a much larger and more industrial scale.
Step 1: Feeding
Imagine standing in front of a massive machine, with bags of material ready to be transformed. The feeding stage is where it all begins. I recall the thrill of seeing those raw materials, usually in pellet form, being poured into the extruder's hopper. It’s essential to ensure that these materials are fed at a consistent rate to maintain a smooth flow throughout the process. This stage ensures a consistent supply of material to the extrusion machine1, enabling uniform output.
Step 2: Melting
As the pellets move forward, they encounter heat that slowly melts them down. I liken this to melting chocolate—careful attention is needed to avoid burning while ensuring everything melts uniformly. The heat from the extruder’s barrel, combined with friction from the screw inside, ensures a perfectly melted mixture.
Step 3: Mixing
This step is where creativity meets engineering. It reminds me of mixing ingredients for a cake—you want everything evenly distributed for the best results. Whether adding colorants or specific additives, achieving a homogeneous blend is crucial for consistency in the final product. Proper mistura2 is essential for maintaining consistency.
Step 4: Forming
The forming stage is where the magic happens. The molten mixture passes through a die, shaping it into a desired form. It’s like using cookie cutters on dough—the die determines the final shape and size. From tubes to intricate profiles, this step defines the product's dimensions.
Estágio | Objetivo |
---|---|
Alimentação | Supply raw material |
Derretimento | Homogenize through heat |
Mistura | Blend materials and additives |
Formação | Shape material into final product |
Step 5: Cooling
Finally, much like letting freshly baked bread cool before slicing, the product needs to set properly. The cooling stage ensures that the formed shape solidifies and retains its intended properties. Depending on the product, cooling can involve air or water baths, preparing it for any additional processing like cutting or revestimento3.
Reflecting on these steps, I find a certain satisfaction in understanding how each one contributes to creating products we often take for granted. Just like in cooking or baking, each stage of extrusion has its own charm and significance.
Feeding involves melting raw material in the hopper.Falso
Feeding involves supplying raw material, not melting it.
Cooling solidifies the formed product after extrusion.Verdadeiro
Cooling helps retain shape and solidify the material.
How Does Extrusion Improve Nutritional Value in Pet Food?
Ever wondered why your pet's kibble is more than just crunchy bites? Let me take you behind the scenes to explore how extrusion enhances pet food nutrition.
Extrusion improves pet food nutritional value by enhancing digestibility, preserving vitamins, and reducing anti-nutritional factors. The process uses heat and pressure, leading to better nutrient absorption in pets.
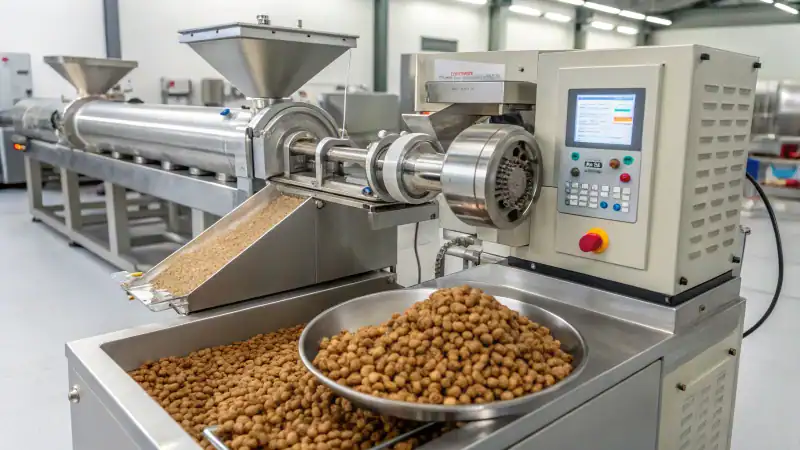
Compreender o processo de extrusão
I remember the first time I saw the extrusion process in action; it was like watching magic unfold. Ingredients get mixed and mashed, then forced through a die under intense heat and pressure. This transforms them into perfectly shaped kibbles or treats. What's fascinating is that this cooking method4 makes the nutrients more bioavailable, meaning our furry friends can absorb and utilize them better. It's like giving them a nutritional boost with every bite.
Enhancing Digestibility
One of the standout benefits of extrusion is how it improves digestibility. Think of it like breaking down complex carbs and proteins into simpler, more manageable pieces. I’ve seen how this makes it easier for pets to digest their food, ensuring they get all the goodness packed inside each kibble. Seeing pets thrive because they’re absorbing maximum nutrients is truly rewarding.
Nutrient Impact | Benefits for Pets |
---|---|
Hidratos de carbono | Digestão mais fácil |
Proteínas | Enhanced absorption |
Preserving Essential Vitamins
It always amazes me how extrusion preserves essential vitamins like A and E despite the high temperatures involved. The secret lies in the quick cooking time, which locks in these vital nutrients, keeping our pets healthy and full of energy. Ensuring they get their vitamins is like adding a little sunshine to their diet every day.
Reducing Anti-nutritional Factors
Ever worried about those pesky anti-nutritional factors lurking in raw ingredients? The extrusion process works wonders by deactivating these compounds. This not only makes the food safer but also ensures our pets can digest it smoothly, avoiding any tummy troubles.
Analyzing Nutrient Retention through Extrusion
I’ve pored over studies showing that extruded pet foods hold on to more nutrients than other methods. It’s like a science of its own! By tweaking the extrusion parameters, manufacturers can fine-tune their processes to keep as many nutrients as possible. It’s all about ensuring every meal packs a punch.
The table below illustrates nutrient retention:
Nutriente | Retention Rate Post-Extrusion |
---|---|
Proteína | 85-90% |
Vitaminas | 75-80% |
Exploring Extrusion Innovations
With continuous research and innovation, extrusion technology keeps pushing boundaries. Adjusting temperature and pressure settings can further enhance nutrient retention, making each bite even more beneficial for pets. These advancements are exciting because they mean we’re constantly finding better ways to nourish our furry companions.
By understanding how extrusion impacts nutritional content, I can make informed decisions about ingredient selection and processing techniques, ensuring pets receive high-quality nutrition from their meals.
A extrusão melhora a digestibilidade dos alimentos para animais de companhia.Verdadeiro
The high heat in extrusion breaks down complex carbohydrates and proteins.
Extrusion decreases vitamin retention in pet food.Falso
Despite high temperatures, quick cooking retains essential vitamins like A and E.
What Equipment is Essential for Pet Food Extrusion?
Imagine stepping into the world of pet food manufacturing, where every kibble is a masterpiece of nutrition and taste.
Essential equipment for pet food extrusion includes an extruder, pre-conditioner, grinder, mixer, and dryer. Each plays a critical role in shaping, cooking, and ensuring the quality and consistency of pet food products.
Key Equipment for Pet Food Extrusion
Extrusoras
Extruders are like the heartbeats of any pet food production line. I remember the first time I saw an extruder in action—it was mesmerizing to watch raw ingredients transform into perfectly shaped kibbles. They work by forcing ingredients through a die to form specific shapes. There are several types, including single-screw and twin-screw extruders. Extrusoras de parafuso único5 are often preferred for their cost-effectiveness and ease of use.
Tipo | Caraterísticas | Vantagens |
---|---|---|
Single-screw | Simple design | Cost-effective, easy to operate |
Twin-screw | Complex but versatile | Greater control over product texture |
Pré-condicionadores
Pre-conditioners remind me of those chefs who prepare ingredients with such care and precision that you know the final dish will be exquisite. They help in hydrating and partially cooking the ingredients before they enter the extruder, ensuring a uniform product texture and enhancing qualidade nutricional6.
- Functionality:
- Mixes steam, water, and other liquids with dry ingredients.
- Prepares the mixture for efficient extrusion.
Grinders and Mixers
Grinders break down raw materials into smaller particles, essential for consistent extrusion. The first time I saw a mixer at work, I was struck by how it moved with purpose, ensuring every particle found its perfect match in the blend.
- Grinders: Assegurar particle size reduction7 for better processing.
- Mixers: Achieve homogenous blends crucial for product uniformity.
Sistemas de Secagem
Post-extrusion, drying systems take me back to my grandma's kitchen, where the aroma of baked goods filled the air. They remove excess moisture to enhance shelf life and prevent spoilage.
- Types:
- Batch Dryers: Suitable for smaller production.
- Continuous Dryers: Ideal for large-scale operations where efficiency is key.
Sistemas de controlo
Modern extrusion lines are equipped with advanced control systems that allow operators to monitor temperatures, pressures, and moisture levels throughout the process. This meticulous monitoring ensures qualidade consistente8 across batches.
Understanding each piece of equipment's role can significantly impact production efficiency and product quality. New technologies in processos de extrusão9 continue to evolve, offering more options and customization for manufacturers. Evaluating these components can help you design a more effective production line suited to your company's specific needs.
As extrusoras de parafuso único são mais versáteis do que as extrusoras de parafuso duplo.Falso
Twin-screw extruders offer greater versatility and control over texture.
Pre-conditioners enhance nutritional quality of pet food.Verdadeiro
Pre-conditioners hydrate and cook ingredients, improving nutritional quality.
How Does Extrusion Affect Pet Food Texture and Palatability?
Ever wondered how the pet food in your pantry gets its delightful crunch? Let's dive into the extrusion process that makes pet food irresistible to our furry friends.
Extrusion affects pet food by cooking ingredients under high heat and pressure, altering the texture and enhancing palatability. This process allows manufacturers to create various shapes and textures, improving taste appeal for pets.
A ciência por detrás da extrusão
Let's imagine standing beside a gigantic pasta maker, only this one crafts gourmet delights for our pets. This is essentially what extrusion is: ingredients are mixed, heated, and pushed through a die to form those perfect kibbles. I remember the first time I saw this process in action—it was like witnessing a culinary symphony where every note is crucial to the final piece. The magic happens when starches gelatinize, proteins denature, and pesky anti-nutritional factors are whisked away, creating not just food but a sensory experience for pets.
Texture Transformation
Have you ever marveled at how some kibbles are delightfully crunchy while others melt in your pet's mouth? This is where the artistry of extrusion comes into play. It's all about balance—temperature, moisture, screw speed—they all dance together to define texture.
Parâmetro | Impacto na textura |
---|---|
Temperatura | Influences porosity and crunchiness |
Humidade | Affects softness or hardness |
Velocidade do parafuso | Controls expansion and density |
I recall a project where we tweaked these elements to get just the right bite for a client's new line of gourmet kibble. Seeing the pets' approval made every tweak worth it.
Enhancing Palatability
Think of that mouth-watering aroma that wafts through your kitchen during a Sunday roast—that's the Maillard reaction at work. In pet food extrusion, it's the secret sauce that amps up flavors, making meals irresistible. Additionally, fat and flavor coatings can be applied post-extrusion to further increase appeal—it's like adding a dash of spice to grandma's famous stew—it's those small extras that make a world of difference.
Tailoring Products for Pets
Every pet has its quirks—whether it's the finicky feline who turns up her nose at anything less than gourmet or the loyal dog who'll munch on anything as long as it's crunchy. Through extrusion, I help manufacturers tailor products to meet these diverse tastes by adjusting parameters such as temperatura10, moisture11e screw speed12. By doing so, we can create unique textures and flavors that cater to specific pet preferences, helping brands carve out a niche in the bustling pet food market. It’s like crafting a bespoke meal plan for each pet, ensuring they savor every bite.
Extrusion increases the porosity of pet food kibble.Verdadeiro
Higher extrusion temperatures can lead to a more porous structure.
The Maillard reaction reduces pet food palatability.Falso
The Maillard reaction enhances flavors, increasing palatability.
What Are the Safety and Quality Standards in Pet Food Extrusion?
Navigating the maze of pet food safety and quality standards can feel daunting, but it's crucial for the health of our furry friends and the success of our businesses.
Safety and quality standards in pet food extrusion include adherence to AAFCO guidelines, BPFse HACCP plans. These ensure the production of nutritionally adequate and safe pet food products.
Compreender os principais regulamentos
When I first stepped into the world of pet food extrusion, I was struck by the complexity of it all. It's not just about mixing ingredients and hoping for the best; it's a science. Following AAFCO diretrizes13 was my first big lesson. These guidelines are like a roadmap, helping ensure every batch of food is safe and nutritious. From defining ingredients to labeling and nutritional profiles, they guide me in crafting quality products that pets love.
Implementing Good Manufacturing Practices (BPFs14) was another turning point for me. Imagine running a kitchen where cleanliness is king—equipment hygiene, employee practices, everything counts. These practices prevent contamination and ensure that every product leaving my facility is up to standard.
HACCP: Análise de Perigos e Pontos Críticos de Controlo
O HACCP plan15 felt daunting at first, but breaking it down made all the difference. By identifying potential hazards and establishing control points, I could manage risks more effectively.
Chave HACCP Passos | Descrição |
---|---|
Conduct hazard analysis | Identify potential hazards in ingredients and production. |
Determine critical control points | Pinpoint where hazards can be controlled or eliminated. |
Establish critical limits | Define acceptable thresholds for each control point. |
Controlar os procedimentos | Regular checks to ensure control points are within limits. |
Importance of ISO Certificações
Achieving ISO certifications, like ISO 9001, was a badge of honor for me. It signals to everyone—customers and regulators alike—that quality management is a top priority. Plus, when exporting to other countries, CE certifications on machinery assure compliance with European standards, a must for international trade.
The Role of Testing and Quality Control
Testing raw materials and finished products became second nature to me. It's not just about meeting regulations; it's about peace of mind knowing each batch is safe and nutritious.
- Teste de ingredientes: I assess raw materials to weed out contaminants.
- Product Testing: Evaluating the nutritional content and safety of final products reassures both me and my customers.
- Controlo de processos: By keeping a close eye on extrusion conditions, I maintain consistency in quality.
Maintaining these stringent quality controls has helped me build trust not just with consumers but also with regulatory bodies.
Inovações em Tecnologia de Extrusão
Technological advancements have been a game-changer. With modern extruders featuring advanced sensors, I can monitor production in real-time, ensuring both safety and efficiency. Staying ahead with these innovations not only enhances product quality but also keeps me compliant with normas regulamentares16, ensuring my products are safe while remaining competitive in the market.
AAFCO guidelines ensure pet food is safe for pets.Verdadeiro
AAFCO guidelines define nutritional and safety standards for pet food.
ISO 9001 certification is irrelevant to pet food quality.Falso
ISO 9001 ensures quality management systems, crucial for pet food quality.
How is the Extrusion Process Evolving with Industry Trends?
Remember the first time you saw how pasta is made? That mesmerizing mix of science and art is what extrusion is all about.
The extrusion process is evolving through integration of digital technologies and sustainable practices. Key trends include automation, real-time monitoring, energy efficiency, and use of biodegradable materials. These innovations enhance productivity and align with environmental goals.
Digital Transformation in Extrusion
When I first started exploring the world of extrusion, it felt like peering into a parallel universe where technology meets creativity. With digital transformation, this world is even more fascinating. Imagine walking into a factory floor where machines hum with precision, adjusting their operations in real-time as if they were alive. That's what automation and real-time monitoring bring to the table.
Automation and Real-Time Monitoring
I remember a time when unexpected breakdowns were a nightmare. Now, with predictive maintenance, those worries are nearly a thing of the past. Automation not only boosts precision but also keeps things running smoothly, almost like having a trusted ally who’s got your back day and night.
Tecnologia | Impacto na extrusão |
---|---|
Automatização | Enhances precision and reduces errors |
Monitorização em tempo real | Offers predictive maintenance insights |
Sustainability in Extrusion
Sustainability isn't just a buzzword; it's a personal mission. Picture this: energy-efficient machines that whisper instead of roar, and materials that naturally decompose without leaving a trace. That's the future we're striving for.
Energy Efficiency and Biodegradable Materials
Reducing power consumption isn't just good for the planet; it's a game-changer for the bottom line too. The adoption of biodegradable materials makes me feel like I'm contributing to something much larger—a collective effort to protect our environment. This shift aligns perfectly with the growing demand from eco-conscious consumers.
- Eficiência energética: Adoption of energy-saving technologies results in reduced operational costs and minimized environmental impact.
- Materiais biodegradáveis: Utilizing materials that decompose naturally supports sustainability and attracts eco-conscious consumers.
Industry-Specific Innovations
Each industry puts its unique spin on extrusion technology, much like chefs experimenting with recipes. Take pet food, for instance—extrusion shapes everything from texture to taste, creating products our furry friends love. Meanwhile, in the aluminum sector, extrusion enhances material properties, proving its versatility.
In my journey through the pet food industry, I’ve seen firsthand how técnicas avançadas de extrusão17 can revolutionize production. These innovations help meet the rising demand for premium pet foods while keeping manufacturers ahead of the competition.
Overall, the evolution of the processo de extrusão18 is a testament to our dedication to technological advancement and sustainable practices. Embracing these trends not only improves efficiency but also fulfills regulatory standards and satisfies the ever-growing consumer demand for eco-friendly products.
Automation reduces errors in the extrusion process.Verdadeiro
Automation enhances precision, minimizing human errors during extrusion.
Biodegradable materials increase the carbon footprint in extrusion.Falso
Biodegradable materials reduce the environmental impact of extrusion.
Conclusão
The extrusion process in pet food production involves blending, cooking, and shaping ingredients under high pressure, enhancing digestibility and nutritional value while ensuring product stability.
Understanding extrusion machines helps optimize their use and maintenance. ↩
Learn about mixing techniques to ensure uniformity and quality. ↩
Explore coating methods to enhance product properties post-extrusion. ↩
Learn how extrusion shapes pet food while retaining nutrients for better health outcomes. ↩
Learn how single-screw extruders offer cost-efficiency and simplicity in operation for pet food production. ↩
Discover how pre-conditioners enhance the nutritional profile of pet foods by optimizing ingredient preparation. ↩
Understand the importance of grinding materials to achieve optimal texture and consistency in pet foods. ↩
Explore how advanced control systems ensure consistent quality in pet food manufacturing. ↩
Stay updated on the latest technological advancements in pet food extrusion for enhanced production capabilities. ↩
Understanding how extrusion alters physical properties helps manufacturers adjust processes to achieve desired pet food textures. ↩
Explores how temperature variations during extrusion change pet food's structure, helping manufacturers control texture outcomes. ↩
Explains how the Maillard reaction enhances flavor profiles in extruded pet foods, boosting palatability. ↩
Understanding AAFCO guidelines ensures compliance with nutritional and labeling standards critical for pet food safety. ↩
GMPs help maintain high hygiene standards, preventing contamination during pet food production. ↩
HACCP plans identify and control potential hazards in the production process, ensuring product safety. ↩
Staying updated with regulatory standards helps manufacturers comply with safety requirements efficiently. ↩
Learn about innovative extrusion methods tailored for producing diverse pet food products efficiently. ↩
Explore how digital tools like automation and real-time monitoring are transforming the extrusion industry. ↩