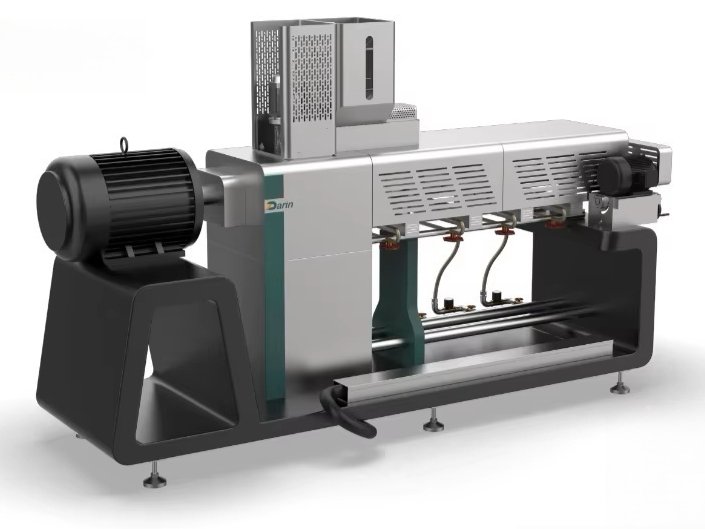
When selecting an air compressor for industrial use, misunderstanding the differences between single-screw and twin-screw compressors can lead to costly mistakes. An ill-suited compressor can cause excessive energy bills, frequent maintenance downtime, and even damage to critical production lines. Fortunately, understanding their structural, operational, and performance differences allows you to make the right investment, ensuring high efficiency and lower total ownership costs. This article will clearly explain these differences and guide you toward the right choice.
Single-screw compressors use one central rotor and two star-shaped gate rotors to compress air with minimal vibration and balanced operation, while twin-screw compressors use two intermeshing helical rotors (male and female) that deliver superior sealing, higher pressure capability, and better energy efficiency for continuous heavy-duty industrial applications.
Choosing the correct compressor is essential to optimize your production efficiency, save energy costs, and avoid unnecessary maintenance troubles. Let's continue reading to understand the detailed mechanisms, advantages, and application scenarios for each type of screw compressor.
Twin-screw compressors are generally more energy-efficient than single-screw compressors in heavy-load operations.Verdadeiro
Twin-screw compressors offer better sealing and reduced internal leakage, leading to superior energy efficiency under demanding industrial conditions.
How Single-Screw and Twin-Screw Compressors Work
Single-screw compressor working principle
A single-screw compressor operates with a single main rotor engaging with two gate rotors mounted perpendicularly. As the main rotor spins, air gets trapped between the threads of the screw and the lobes of the gate rotors. As rotation continues, the trapped volume reduces, thus compressing the air before it exits toward the system. The design inherently balances axial and radial loads, leading to smooth, low-vibration operation.
Caraterísticas principais | Single-Screw Compressor |
---|---|
Componentes Principais | One screw rotor, two gate rotors |
Compression Process | Trapped air compressed between rotor and gates |
Método de arrefecimento | Oil-injected or water-injected |
Vibration Levels | Very low |
Ideal Usage | Medium-load, medium-pressure applications |
Twin-screw compressor working principle
A twin-screw compressor employs two precisely machined rotors (a male rotor and a female rotor) that mesh closely. As these rotors turn together, air is trapped in the cavities between their lobes. The trapped air moves along the rotors as the volume between the lobes and the housing gradually decreases, causing compression. Twin-screw compressors require precise timing gears to synchronize the rotors but achieve extremely efficient compression.
Caraterísticas principais | Twin-Screw Compressor |
---|---|
Componentes Principais | Male rotor and female rotor |
Compression Process | Volume reduction between meshed lobes |
Método de arrefecimento | Mostly oil-injected; oil-free models also exist |
Vibration Levels | Moderate (well-managed with good mounting) |
Ideal Usage | Heavy-load, high-pressure industrial settings |
Performance Comparison: Single-Screw vs Twin-Screw Compressors
Efficiency and energy consumption
Single-screw compressors deliver good energy performance at moderate pressures but struggle with high efficiency under extremely heavy loads. Some internal leakage is inevitable due to the interaction between the screw and the gates.
Twin-screw compressors achieve exceptional energy efficiency, especially in oil-injected models. Thanks to superior sealing and minimal leakage, they perform consistently even under high-demand and full-load conditions.
Fator | Single-Screw Compressor | Twin-Screw Compressor |
---|---|---|
Eficiência energética | Moderado | Elevado |
Leakage Control | Bom | Excelente |
Load Handling | Moderado | Muito elevado |
Lifecycle Energy Costs | Higher over time | Lower over time |
Reliability and maintenance
Single-screw compressors benefit from symmetrical force distribution, reducing bearing wear. However, gate rotor wear can become a problem if not properly maintained.
Twin-screw compressors, with their simpler rotor-to-rotor engagement (without additional gate rotors), tend to have lower mechanical wear points but require precise maintenance of timing gears and bearings to ensure rotor alignment.
Aspeto | Single-Screw Compressor | Twin-Screw Compressor |
---|---|---|
Wear Components | Gate rotors | Bearings, timing gears |
Service Intervals | Moderado | Longer intervals |
Complexidade da manutenção | Moderado | Um pouco mais alto |
Typical Service Life | 10–15 years | 15–20+ years |
Practical Application Scenarios
When to choose a single-screw compressor
Single-screw compressors are ideal when you need medium air volume at medium pressure, and cost is a primary concern. Industries such as food processing, textile manufacturing, and electronics assembly often find single-screw compressors sufficient for their needs.
Typical examples include:
- A beverage bottling plant operating 16 hours per day
- An electronics workshop with moderate compressed air usage
- A textile dyeing facility with consistent but not extreme air demands
When to choose a twin-screw compressor
Twin-screw compressors are suited for large-scale, high-demand environments where uptime, efficiency, and maintenance cost control are critical. They are preferred in industries such as steel production, automotive manufacturing, and chemical processing plants.
Typical examples include:
- An automotive assembly line running 24/7
- A large petrochemical refinery needing stable air pressure for critical processes
- A mining operation requiring portable high-volume air delivery underground
Requisito | Melhor escolha | Motivo |
---|---|---|
Moderate load, budget-sensitive | Single-Screw Compressor | Lower initial cost and simple operation |
Continuous heavy load, energy-saving focus | Twin-Screw Compressor | Higher efficiency and reliability |
Case Study: Compressor System Upgrade at an Automotive Factory
An automotive manufacturing plant originally installed multiple single-screw compressors. As production demands increased, the compressors struggled with efficiency and uptime, leading to rising operational costs.
After an energy audit, the plant replaced the old units with high-efficiency twin-screw compressors equipped with variable speed drives (VSDs). Results included a 20% reduction in energy consumption, a 33% reduction in maintenance costs, and a significant increase in system reliability.
Parâmetro | Antes (parafuso único) | After (Twin-Screw + VSD) |
---|---|---|
Total Power Consumption | 950 kW | 750 kW |
Average Maintenance Cost | $180,000/year | $120,000/year |
System Uptime | 94% | 99.5% |
Retorno do investimento | — | 2.5 years |
This case demonstrates the importance of choosing the right type of compressor for scaling operations.
Conclusão
Understanding the key differences between single-screw and twin-screw compressors is critical for making an informed equipment investment. Single-screw compressors offer simplicity, low vibration, and suitability for mid-range industrial needs, whereas twin-screw compressors excel in energy efficiency, durability, and handling heavy-duty industrial requirements. Matching your compressor choice to your specific operational goals can significantly enhance productivity and profitability.
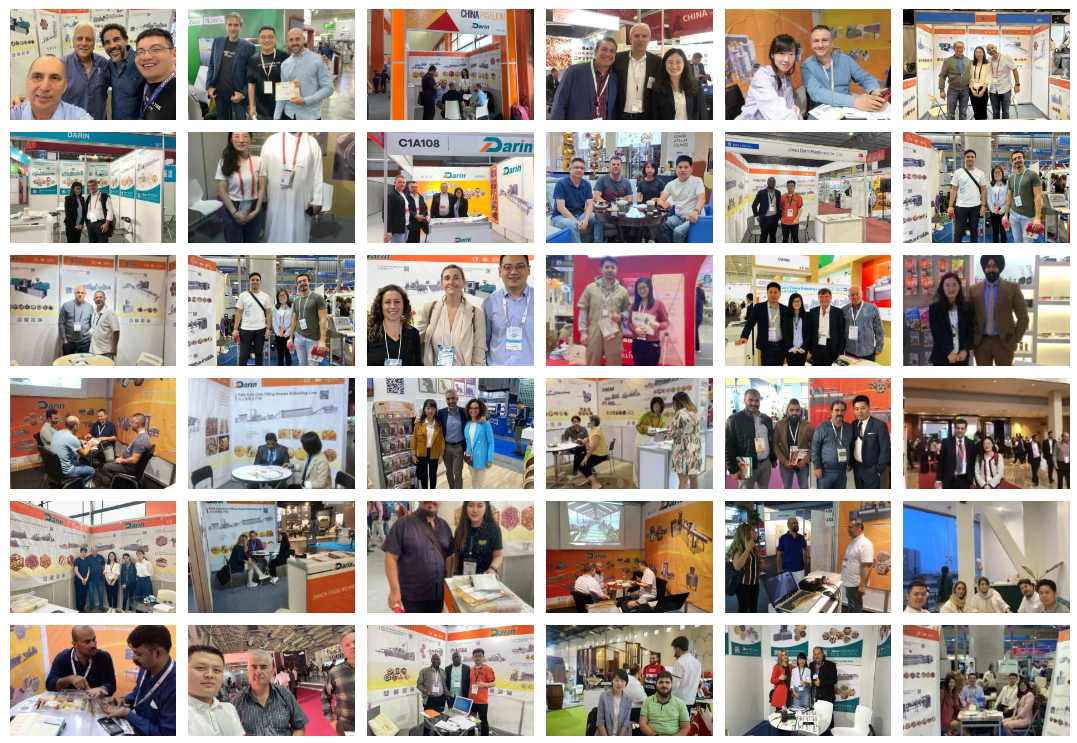
Contact Us for the Right Compressor Solution!
Whether you need a reliable single-screw compressor for medium-sized operations or a high-efficiency twin-screw compressor for heavy industrial applications, [Your Company Name] is ready to help. Contacte-nos hoje for expert consultation, customized recommendations, and the best compressor solutions tailored to your needs!
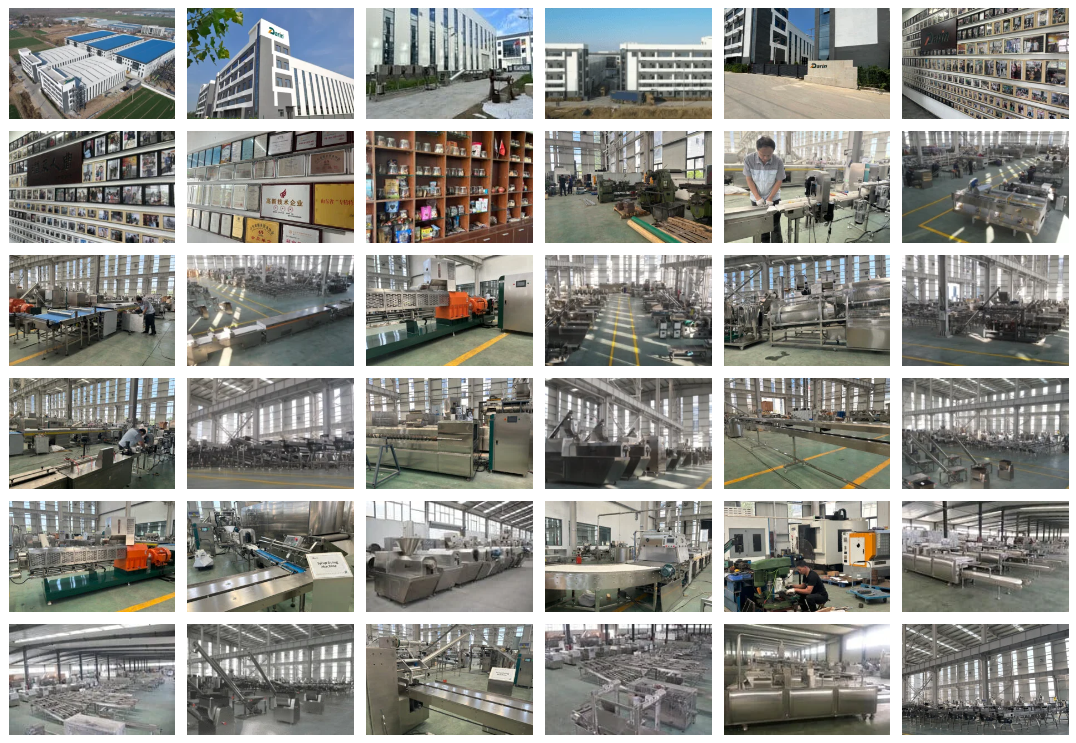