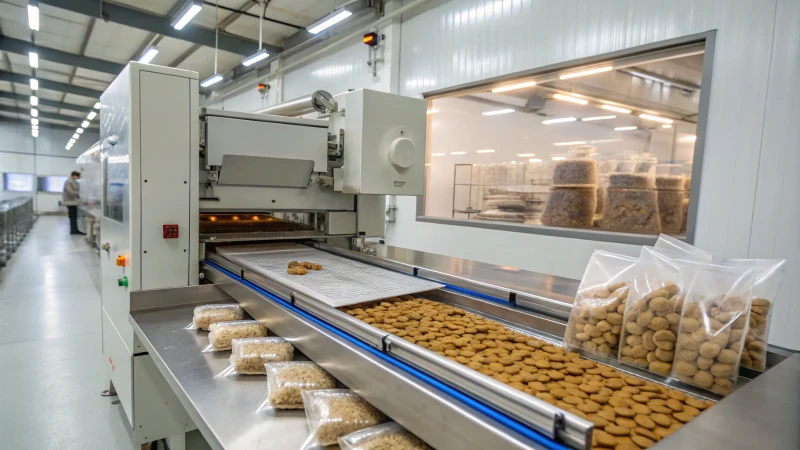
Want to lift your pet food business? Let's see how a bit of machinery magic might really change everything!
A pet treats molding machine is special equipment. It shapes and forms pet treats efficiently. This machine helps increase production capabilities. Products have consistent quality with it. Businesses meet rising consumer demand for premium items by investing in this machinery. They improve operational efficiency as well.
I remember when I started in the pet food industry. The thought of increasing production felt terrifying. Then, I found the pet treats molding machine. Everything changed after that. This amazing machine simplified my production line. It allowed me to create high-quality treats. My customers love these treats. In this blog post, I’ll share how buying a molding machine transforms operations. It's really important for success in today’s tough pet food market.
A pet treats molding machine improves production efficiency.True
This machine streamlines the shaping process, allowing for faster production rates and consistent quality, which is essential for meeting market demands.
Investing in a molding machine is unnecessary for pet food businesses.False
In reality, such machinery is crucial for maintaining competitiveness and meeting consumer expectations in the growing pet food market.
What Are the Key Features of a Pet Treats Molding Machine?
Have you ever wondered what makes a pet treats molding machine truly effective? Let me guide you through the important features that truly improve your production process!
Key features of a pet treats molding machine include precise shaping, fast operation, versatility, material compatibility, temperature control and levels of automation. These very features allow efficient production. They also maintain safety standards.

Understanding the Molding Process
The molding process is crucial in the production of pet treats. This involves shaping the raw mixture into specific forms, which can include biscuits, jerky, or dental chews.
A well-designed molding machine should provide:
- Precision: Accurate shaping of treats ensures consistency in size and weight.
- Speed: High production rates are essential for meeting market demands.
- Versatility: Ability to switch between different treat shapes and sizes with ease.
For more insights into production efficiency, check out manufacturing techniques1.
Key Features to Look For
When evaluating a pet treats molding machine, consider the following key features:
Feature | Importance |
---|---|
Material Compatibility | Machines should accommodate various ingredients such as meats, grains, and flavorings. |
Temperature Control | Proper temperature management affects texture and consistency of treats. |
Automation Levels | Automation enhances efficiency by reducing manual labor and minimizing human error. |
Sanitation Standards | Easy cleaning mechanisms are vital for food safety compliance. |
Understanding these features helps in selecting a machine that meets both operational and regulatory requirements.
Performance Metrics
To gauge a machine's performance, consider the following metrics:
- Output Capacity: Measured in kg/hour, indicating how much product can be molded per hour.
- Energy Efficiency: Important for long-term operational cost reduction.
- Downtime Rates: Frequency of breakdowns or maintenance needs affects overall productivity.
For more on optimizing machinery performance, explore industrial efficiency2.
Customization Options
Customization plays a significant role in tailoring machinery to specific production needs. Options might include:
- Mold Designs: Custom molds for unique pet treat shapes.
- Ingredient Feeders: Ability to integrate with existing systems for seamless operation.
- Control Systems: Advanced controls that allow for real-time adjustments during production.
For innovative solutions in customization, refer to custom machinery3.
Conclusion
While we won't delve into the conclusion, understanding these key features is essential when considering a pet treats molding machine. Each feature contributes significantly to operational efficiency and product quality.
Molding machines ensure consistent treat sizes and weights.True
Precision in molding machines allows for uniformity in pet treat production, which is crucial for quality control.
Automation reduces manual labor in pet treat production.True
Incorporating automation in molding machines enhances efficiency and minimizes human error during the production process.
How Can Molding Machines Supercharge Your Production Efficiency?
Have you ever thought about how those sleek, efficient molding machines change your production line? Let's explore the interesting world of molding machines. These machines transform your operations.
Molding machines increase production efficiency through automation of processes. They adjust production settings for the best results. High-quality outputs result from this automation. These innovations decrease cycle times. There is also less material waste. Product quality is really improved.
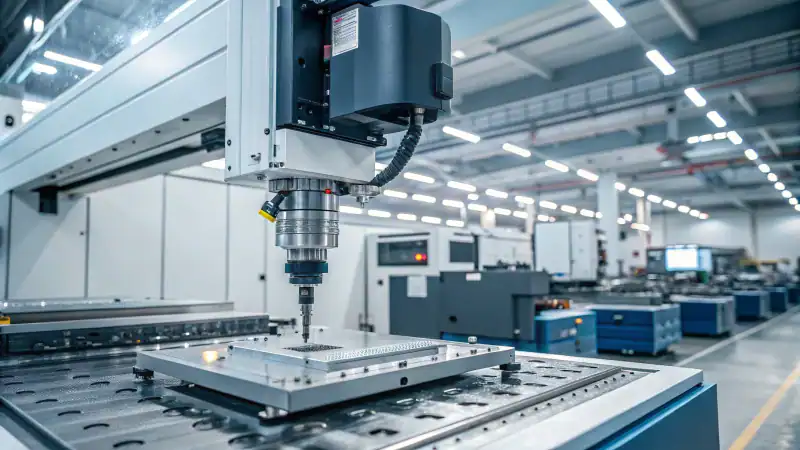
Understanding the Role of Molding Machines in Production
Molding machines are not just equipment; they are the backbone of modern manufacturing. I remember visiting a large pet food factory where I saw these machines work wonders. The transformation from raw materials to perfect products was really amazing.
Molding machines are crucial in the manufacturing sector, especially for producing high-quality parts and products efficiently. Their ability to automate processes significantly enhances productivity.
For instance, with advanced mold design, manufacturers can produce complex shapes with high precision, reducing the need for extensive post-processing. This not only saves time but also minimizes material waste.
- Efficiency through Automation: New molding machines use automation to run more smoothly. Imagine a system that loads materials, runs itself and unloads products - all easily! Automation reduces cycle times and labor costs. Teams can focus on more valuable tasks.
Benefits of Process Optimization
Process optimization is another key area where molding machines shine. By implementing sophisticated control systems, manufacturers can monitor and adjust parameters in real-time, ensuring optimal conditions throughout production.
Parameter | Impact on Production |
---|---|
Temperature Control | Reduces defects and improves quality |
Pressure Management | Ensures consistent part density |
Cycle Time Optimization | Increases throughput |
Molding machines really help with optimizing production processes. They have advanced controls for monitoring and adjusting in real-time - like a watchful guardian over production! I remember when temperature changes caused product issues. Now, keeping perfect conditions is second nature.
These adjustments lead to a more predictable production process, enhancing the overall efficiency of operations. For example, when temperature control is optimized, it can lead to fewer defects in the final product and reduce the need for rework, ultimately saving time and resources.
Enhancing Quality and Reducing Waste
Quality matters in manufacturing. Molding machines raise this to new levels. Good molds improve material flow and distribution. I once talked to a client who loved a new molding system. Precise molding cut material waste significantly. This saved money, which everyone values!
Furthermore, by reducing material waste through precise molding techniques, companies can save significantly on raw materials costs. This is particularly relevant in industries like pet food production, where ingredient quality directly influences product success.
- Real-World Example: A big pet food maker I worked with saw an amazing 30% drop in raw material use while increasing output by 20% with new molding tech. Success like this shows the huge impact of effective mold design.
Conclusion without Finalizing
In summary, molding machines enhance production efficiency through automation, process optimization, and quality assurance. Using them lets manufacturers improve operations and meet market demands well. If you’re curious about optimizing your manufacturing with molding tech, check this comprehensive guide4. Let’s continue pushing the boundaries together!
Molding machines automate production processes effectively.True
Automation in molding machines reduces manual labor, streamlining operations and increasing production speed, thus enhancing overall efficiency.
Molding machines do not improve product quality.False
Contrary to this claim, molding machines enhance product quality by ensuring precise material flow and reducing defects during production.
What Are the Cost Implications of Investing in Molding Machines?
At first, I thought about investing in molding machines. I soon saw it involved more than just numbers. This journey has many financial details. These details really affect your business's production abilities. They also influence its future. Let's explore what these costs truly mean.
Investing in molding machines involves various costs. Initial purchase prices vary from $10,000 to more than $100,000. Ongoing expenses include maintenance and labor. Profitability depends on market demand and technology. This is very important.
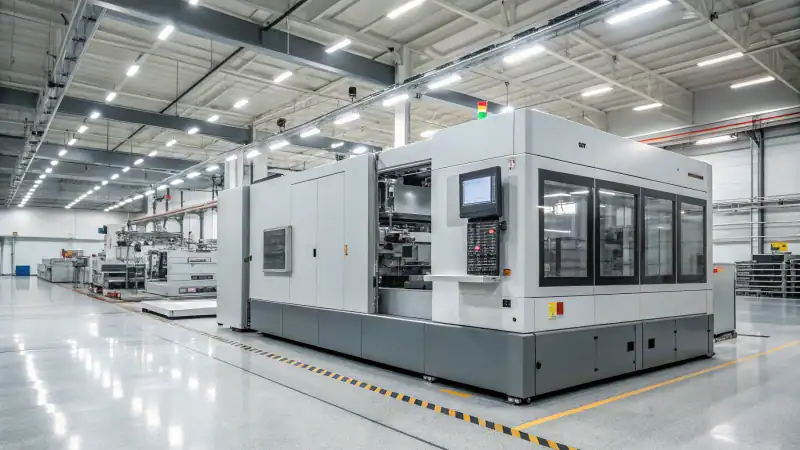
Understanding Initial Investment Costs
Buying molding machines feels like stepping into the unknown. My first purchase excited and worried me. The financial commitment felt big. Initial costs often trip businesses because they differ by machine type, capacity, and technology.
For example, basic injection molding machines start around $10,000, while high-capacity models might exceed $100,000! Don’t forget extra features—automation adds costs fast. It’s crucial to evaluate your specific needs against these price ranges to ensure you make an informed investment decision.
Ongoing Operational Costs
But there's more after buying! I learned this lesson the hard way. Continual operational costs shape molding machines' overall expenses. Here’s a simple breakdown:
- Electricity and Maintenance: Like my old car needs oil changes, these machines need maintenance too. Frequent use demands regular checks. Costs range from a few hundred to several thousand dollars yearly.
- Labor Costs: Skilled operators drive your production line. Finding good talent increases total expenses. Keep skilled workers.
- Material Costs: Material choice sways production costs. High-quality or specialized materials mean higher expenses but also boost product value.
Potential Profitability
Profit potential excites many in this field. Watching production efficiency soar with the right machine thrilled me. Profit is really possible! Careful profit margin analysis shows expected earnings compared to your investment.
Factor | Initial Cost Estimate | Ongoing Cost Estimate | Expected ROI |
---|---|---|---|
Basic Injection Machine | $10,000 - $50,000 | $5,000/year | 20% - 40% |
High-Capacity Machine | $50,000 - $150,000 | $10,000/year | 30% - 50% |
Influencing Factors
Several factors influence both initial and ongoing costs. These insights could save a headache:
- Market Demand: Changing demand for molded products sometimes supports investing in smarter machinery. I’ve seen it happen.
- Technological Advances: Staying updated with new technology is vital. Upgrading machinery felt scary; yet it led to better efficiency later.
- Geographic Location: Location impacts costs due to local labor rates and material access. Research local market conditions; that information is very important.
Evaluate these factors carefully. Use my experiences in decision-making. Understanding cost implications of molding machine investments enables informed choices aligning with your business goals.
Basic injection molding machines start around $10,000.True
The initial cost of basic injection molding machines typically begins at approximately $10,000, highlighting the financial commitment involved in this investment.
High-capacity molding machines exceed $150,000 in cost.False
High-capacity molding machines can often exceed $150,000, indicating significant investment for advanced production capabilities.
How Can Molding Machines Meet Consumer Demand for Customization?
Do you dream of having a product that truly fits your needs? Let us discover how modern molding machines transform this dream into reality. These machines use new technology for production. They change how products match our expectations.
Molding machines satisfy consumer demand for customization. They integrate advanced technologies like IoT and AI. Diverse material capabilities help them, too. These machines enable tailored products. Production happens efficiently and at scale.
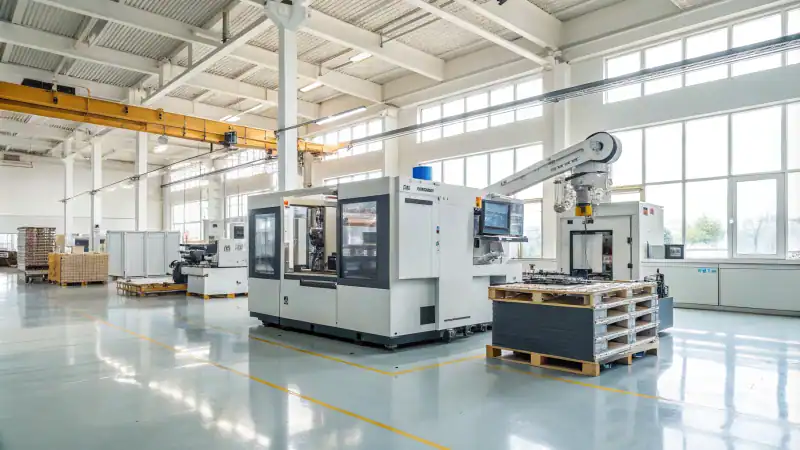
The Evolution of Molding Technology
Molding machines are no longer just machines for mass production. They have become the heart of customization in today's factories. I remember my first time in this industry. The machines could not only create standard products but also adjust to fit specific customer desires. It’s similar to watching a skilled chef make a dish just for your taste, right in front of you.
Molding technology has come a really long way. It's amazing to see the progress! At first, customization was a luxury. Today, with 3D printing and modular systems, manufacturers adapt production for unique designs quickly. I've seen companies use additive manufacturing5 to create detailed, personalized designs. This seemed impossible a few years ago.
Customization at Scale
Picture adjusting a product's design in real-time because someone asked for a small change! Modern molding machines have smart technologies making this happen. They use IoT and AI to check production data instantly, so they can meet individual choices fast. I remember seeing smart sensors6. They check materials during production, making sure every piece matches what the customer needs.
Diverse Material Capabilities
Many people care about sustainability today. Molding machines handle this change well. They now work with many materials, like biodegradable plastics and recycled composites. This supports customization and sustainability. It feels good to be in an industry that cares for the planet!
A comparison of common molding materials is illustrated below:
Material Type | Customization Potential | Sustainability Level |
---|---|---|
Traditional Plastics | Moderate | Low |
Biodegradable Plastics | High | High |
Recycled Materials | High | Moderate |
Natural Composites | Very High | High |
Consumer Insights and Feedback Loops
Knowing what consumers want is very important. Molding machines now have feedback loops for gathering insights directly from consumers. This allows fast changes in products to keep up with preferences. By using data analysis and surveys, companies understand customer needs. Curious about consumer influence on manufacturing? See consumer-driven manufacturing7.
Future Trends in Customization
The future of molding machines seems limitless. Machine learning algorithms are coming soon. They may even predict consumer trends, helping manufacturers stay ahead with personalized products. It’s an exciting time in our field! Customization might become the rule, not the exception.
By adopting new technology and market changes, molding machines may meet today's consumer needs and predict future desires for personalization. It’s an exciting journey and I am happy to be part of it.
Molding machines can produce customized products at scale.True
Advancements in technology allow molding machines to efficiently create tailored products while maintaining high production speeds, meeting consumer demand effectively.
3D printing is no longer relevant in modern molding technology.False
Contrary to this claim, 3D printing remains a crucial innovation in molding technology, enhancing customization capabilities significantly.
How Can I Ensure My Pet Treats Molding Machines Stay in Top Shape?
Have you ever thought about ways to keep pet treat molding machines working well? Understanding their maintenance needs is very important. It really helps achieve efficiency and high-quality production. Let’s explore this together!
Daily visual inspections help pet treats molding machines stay in good condition. Regular cleaning removes dirt and keeps parts working smoothly. Lubrication reduces friction between moving parts. Scheduled checks identify wear and check how well the machines function. These steps help the machines work their best for a long time.
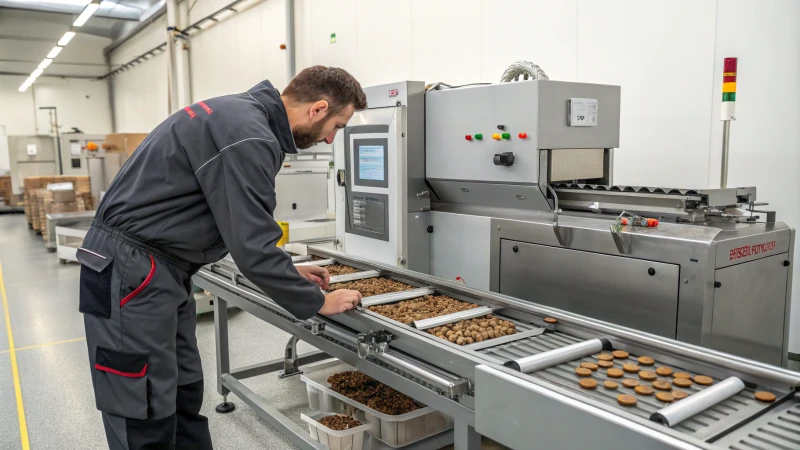
Importance of Regular Maintenance
Regular maintenance of our molding machines is very important in the pet food industry. These machines need care to avoid sudden, costly breakdowns. This care is crucial for keeping our operation running. Early in my career, machines would often stop without warning. This caused panic and stress. At that time, I learned the importance of keeping everything checked. It ensures a steady flow of pet treats.
Some of the key benefits of regular maintenance include:
- Reduced Downtime: Scheduled maintenance helps find and fix potential issues before they become major problems. This approach has really saved me from many unexpected halts in production.
- Quality Assurance: Regular checks ensure that my machinery operates within the correct limits. Every batch of treats meets the quality we promise.
- Cost Savings: Preventative maintenance reduces repair costs. It is truly a financial game changer.
Daily Maintenance Tasks
A daily routine really keeps my molding machines in top condition. Here’s a quick look at daily tasks:
Task | Description |
---|---|
Visual Inspection | Check for any visible signs of wear or damage. |
Cleanliness Check | Ensure the machine is clean and free from debris. |
Lubrication | Lubricate moving parts to reduce friction. |
Functional Tests | Run test cycles to verify machine operation. |
Every day, these simple tasks stop bigger problems from appearing later.
Weekly and Monthly Maintenance
Weekly and monthly routines are important for complete care. Here are tasks I follow:
Weekly Tasks
- Tighten Bolts and Screws: Checking and tightening any loose parts stops misalignment. This prevents the machine from facing bigger problems.
- Inspect Electrical Components: I look at wiring and connections for any wear or corrosion signs. Prevention is really valuable!
Monthly Tasks
- Replace Filters: Changing air and oil filters maintains top machine performance.
- Calibrate Machines: Calibration checks are crucial for accurate molding, which ensures quality.
By following these schedules, I’ve avoided common problems due to neglected maintenance.
Common Issues and Troubleshooting
Even with careful maintenance, issues still arise. Here are some common problems with pet treats molding machines and solutions that have worked for me:
Issue | Possible Cause | Solution |
---|---|---|
Inconsistent Molding | Misalignment or worn molds | Adjust or replace molds |
Overheating | Lack of lubrication | Increase lubrication frequency |
Unusual Noises | Loose parts or debris | Conduct a thorough inspection |
Having a troubleshooting guide helps me fix minor issues quickly. This reduces disruptions in production.
Conclusion on Maintenance Practices
These maintenance practices help me keep the pet treats molding machines running smoothly. They also maintain high-quality production standards. For more insights on specific maintenance schedules suited to your machinery, explore resources like maintenance best practices8 and troubleshooting guides9. Let's keep those tails wagging with top-notch treats!
Regular maintenance extends the lifespan of molding machines.True
Consistent upkeep helps prevent breakdowns, ensuring machinery lasts longer and operates efficiently.
Daily inspections are unnecessary for molding machine maintenance.False
Regular visual checks are essential to identify wear and prevent major issues in production.
Conclusion
Pet treats molding machines boost production efficiency, ensure product quality, and meet customization demands while requiring regular maintenance for optimal operation.
Exploring this link can provide you with comprehensive insights into advanced machinery options tailored for pet treat manufacturing. ↩
This link will help you understand how energy efficiency impacts the overall cost of operating a molding machine for pet treats. ↩
Learn more about how custom machinery can enhance your production line's flexibility and efficiency with this link. ↩
This link provides insights into advanced molding technologies that boost efficiency in manufacturing processes. ↩
Explore how modern molding technology adapts to consumer preferences for tailored products, enhancing your understanding of industry practices. ↩
Learn about the impact of consumer feedback on molding processes and how it drives innovation in product design. ↩
Gain insights into future trends in molding technology and how they will shape consumer product customization. ↩
This link provides expert insights into effective maintenance practices that can enhance the performance and lifespan of your equipment. ↩
Explore this resource for troubleshooting tips to quickly address common issues with molding machines in pet food production. ↩