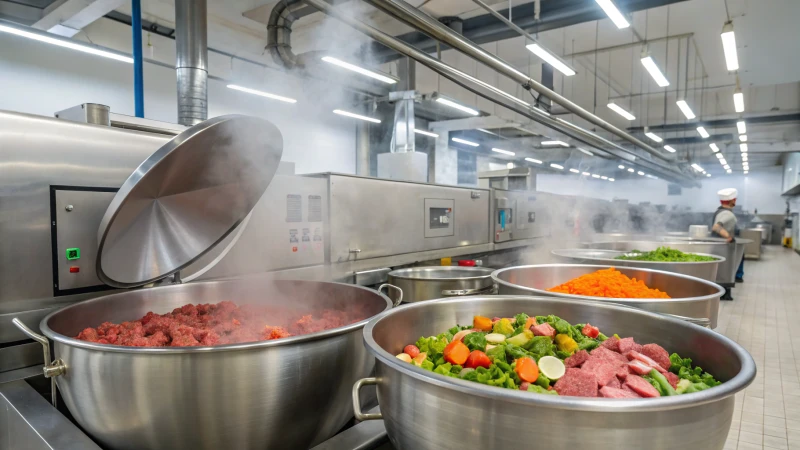
Wat zijn de grondstoffen voor de productie van dierenvoeding?
Zelf droog hondenvoer maken is een lonende manier om ervoor te zorgen dat uw huisdier een uitgebalanceerde voeding krijgt
Rawhide Twisting Line is an industrial-grade machine specifically designed for producing twisted rawhide ropes used in natural dog chews. These twisted ropes are the base material for a wide range of pet chew products, including knotted bones, braided sticks, rings, and twists.
This equipment is critical in the production line because uniform twisting ensures consistent shape, chew strength, and visual appeal—all key concerns for pet food brands and OEM buyers targeting global retail and export markets.
Used for Rawhide Twisting Production.
Model | Output | Installed Capacity |
---|---|---|
DR-RT3 | 3000pcs/h | 17kw |
Looking to create a unique pet food product? We provide full customization services, from concept to finished machine. Our engineering team uses CAD and 3D modeling to bring your ideas to life—fast and accurately. Let’s work together to build your next best-seller.
The Rawhide Twisting Line is an automated, multi-stage system engineered for the mass production of natural rawhide dog chews. Each module plays a critical role in transforming rawhide sheets into consistent, export-quality twisted ropes. The system includes:
① Control Cabinet
② Water Squeezer
③ Robot Arm A
④ Vibrating Cutter
⑤ Robot Arm B
⑥ Strip Cutter
⑦ Twisting Machine
⑧ Dryer
⑨ Final Cutter
Rawhide Twisting Line operates through a streamlined, modular process that transforms rawhide sheets into standardized chew ropes. This system ensures constante kwaliteit, low labor inputen compliance with international food-grade standards.
Feeding & Pre-treatment
Rawhide sheets are first moistened and softened. Robot Arm A feeds them into the line, ensuring hygienic handling.
Cutting Phase
De Vibrating Cutter slices the rawhide into even-width strips. The Strip Cutter then adjusts each strip to the required length.
Water Removal
Moisture is reduced via the Water Squeezer, optimizing flexibility and preventing over-wet twisting.
Twisting Operation
The strips are transferred by Robot Arm B into the Draaimachine, where precise torque creates consistent spiral ropes. Twist speed, direction, and density are adjustable.
Drying Process
De Droger uses controlled airflow and temperature to dehydrate the twisted rawhide, enhancing shelf life and firmness.
Final Cutting & Shaping
After drying, the Final Cutter trims the ropes into pre-set sizes or formats (straight sticks, knots, etc.), ready for packaging.
Choose Darin Rawhide Twisting Line for consistent quality, full automation, and export-grade compliance. Trusted by global pet food brands—upgrade your production today!
De motoren van Darin Machinery zijn afkomstig van WEG met 3 jaar wereldwijde garantie of Siemens.Geniet van een betrouwbaar wereldwijd after-sales service systeem.
Elektrische onderdelen zijn van ABB of Schneider, gemakkelijk te vervangen op de plaatselijke markt.
PLC- en aanraakschermen van Siemens, Duitsland, worden door Darin Machinery gebruikt om de bediening te vereenvoudigen en minder arbeid te vereisen.
Als er storingen optreden, geven de touchscreens van Darin Machinery relevante informatie weer, zodat problemen snel kunnen worden gediagnosticeerd en opgelost.
De bedieningskasten van Darin Machinery zijn uitgerust met een veilige spanning van 24 V, zodat de veiligheid van de operator zelfs bij een elektrische lekkage gewaarborgd is.
Darin Machinery heeft drie soorten beschermers: overstroom, overspanning en oververhitting om de veiligheid van de machine en de operator te garanderen.
Servo follows the cutting size more accurately, rolling cutting can cut products with strong toughness, such as cowhide products, and the cutter does not cut the conveyor belt.
The end of the conveyor belt has a small turning radius, which makes material transportation smoother.
Its components are arranged for quick disassembly, ensuring efficient upkeep and hygienic operation.
Alle deksellichamen, gaasbanden en onderdelen die in contact komen met materialen bij Darin Machinery zijn gemaakt van voedselveilig roestvrij staal 304, voor een superieure duurzaamheid en veiligheid.
Darin® Machinery is global leading manufacturer of pet food production lines, Darin® provide full-cycle, one-stop production equipment solutions for all types of pet food, pet treats & pet health products.
Alle machines zijn gecertificeerd met Europese CE-goedkeuring en ISO 9001-certificering.
■ Run in 99+ countries including USA, Germany, Japan, Italy, UAE, Australia etc.
■ Machineleverancier van General Mills, Kelloggs, Melinda, Bill Gates foundation & Wanpi.
■ 290+ Invention patents & utility model patents.
■ Government-certified high-tech enterprise.
■ Member of APPA (USA) & Deputy President Unit of SDPIA.
■ Professional food machinery manufacturer with 18 years of experience.
Ons uitgebreide productassortiment omvat productielijnen voor droogvoer, natvoer, halfvochtig voer en rauw voer, maar ook gewone traktaties voor huisdieren zoals koekjes, jerky, tandkluiven, runderhuidkluiven en trainingssnacks. Daarnaast bieden we verschillende productielijnen voor voedingsmachines, snacks, energierepen en ondersteunende apparatuur.
Darin Machinery’s equipment is operational in over 99 countries and regions, including the USA, Germany, Japan, Italy, Spain, the Netherlands, Australia, Canada, Holland, Saudi Arabia, Brazil, Mexico, Indonesia, Thailand, and more. Darin Machinery serves renowned clients worldwide, including General Mills, Kellogg’s, and the Bill & Melinda Gates Foundation, among top-tier pet food suppliers.
When purchasing the Rawhide Twisting Line, you might be interested in the following questions.
De Dog Chews Rawhide Twists Processing Line typically has a production capacity that can vary depending on the configuration, automation level, and number of forming and drying stations. Here are standard ranges:
Standard Output:
100–200 kg/hour
High-Capacity Line:
300–500 kg/hour, especially with multi-layer drying systems and multiple forming machines.
In Pieces (approximate):
Since a rawhide twist chew typically weighs 10–25 grams:
100 kg/hour ≈ 4,000–10,000 pcs/hour
500 kg/hour ≈ 20,000–50,000 pcs/hour
Size & weight of the chew – Smaller twists increase the piece count per hour.
Forming machine configuration – Automatic vs. semi-auto.
Drying system capacity – Larger belt dryers or multi-layer options reduce bottlenecks.
Material feeding speed & consistency – Impacts continuous production efficiency.
Would you like me to recommend a specific configuration for your target capacity or market demand?
Ja, de Dog Chews Rawhide Twists Processing Line can be configured to handle a wide variety of shapes and sizes, but with the following important considerations:
The line can produce:
✅ Twists – Single, double, or triple braided styles
✅ Knots – Bone-shaped with tied ends
✅ Rolls & Sticks – Straight or compressed rolls
✅ Braids – 3-strand or 5-strand woven chews
✅ Flat Chips – If combined with a cutting/shaping module
Interchangeable Molds or Forming Heads
Different forming molds can be installed to switch between shapes.
Automatic or manual replacement depending on the line configuration.
Customizable Cutting Length
Adjustable blade settings to control the length of twists or rolls.
Optional Forming Attachments
Add-on systems for knotting, braidingof rolling can be included.
Some shapes (like tight knots or artistic braids) may require semi-automatic or manual assistance.
Programmable Controls
Advanced lines may feature PLC/HMI control systems where parameters for different shapes can be preset and switched easily.
Very complex novelty shapes (like hearts, animals) may require custom molding of manual intervention.
Shape changes might reduce throughput slightly, depending on complexity.
Different shapes may need adjusted drying times en humidity control during processing.
Would you like a recommendation for a multi-shape line optimized for flexibility, or a high-output line focused on one or two core shapes (like braided sticks or knotted bones)?
For optimal performance of the Dog Chews Rawhide Twists Processing Linede rawhide material must meet certain specifications to ensure smooth processing, proper forming, and consistent product quality.
Parameter | Specification Range | Opmerkingen |
---|---|---|
Vochtgehalte | 18% – 25% | Ideal for pliability without being too wet or brittle. Over-dried rawhide may crack; too wet may stick. |
Thickness | 2.0 – 5.0 mm | Varies depending on product type. Thicker hides are better for knotted or long-lasting chews. |
Width (Strips) | 10 – 50 mm (can be wider and cut) | Based on target product size. Braids may use narrower strips; rolls and bones use wider. |
Length | 150 – 600 mm | Can be customized; longer strips give more flexibility in forming complex shapes. |
Type | Beef hide, buffalo hide, or pigskin | Buffalo is tougher; pigskin is softer and more digestible. Choose based on market preference. |
Voorbereiding | Cleaned, dehaired, defatted, decontaminated | Preferably pre-treated and sterilized; some lines include soaking/softening stages. |
Uniformiteit: Rawhide should be consistently thick and smooth to prevent forming issues or jams in automated machines.
Pre-soaking: If using dry hides, pre-soaking in warm water (with optional mild food-grade softeners) is recommended before feeding.
Trimming: Edges should be trimmed to avoid ragged ends that could jam the rollers or forming molds.
Would you like a detailed guide for preparing rawhide for use in the production line, or sourcing recommendations for compliant rawhide suppliers?
Ja, high-quality Dog Chews Rawhide Twists Processing Lines—especially those intended for export or use in regulated markets—are typically designed and built to meet key food-grade certifications relevant for pet chew production. Here's what you should expect:
Certificering | Beschrijving | Relevance |
---|---|---|
CE (Conformité Européenne) | Ensures machinery meets EU health, safety, and environmental protection standards. | Mandatory for European Union imports. |
FDA (Amerikaanse Food and Drug Administration) | Materials in contact with food must be FDA-compliant (e.g., stainless steel, belts). | Applies if exporting to the U.S. |
GMP (goede productiepraktijken) | Guidelines for hygienic design, cleanability, and traceability. | Widely accepted in global pet food facilities. |
ISO 9001 / ISO 22000 | Quality and food safety management systems. | Optional but enhances trust and compliance. |
Food-Grade 304 or 316 Stainless Steel for all contact parts.
Hygienic Design: Rounded edges, smooth welds, and easy-to-clean surfaces.
Belt Materials: PU or Teflon belts that are FDA- and EU-compliant.
Sanitation Support: Wash-down compatible sections and removable components for cleaning.
Electrical Safety: CE-certified electrical systems with proper grounding and overload protection.
Certification coverage may vary by supplier or factory configuration. Some lines are CE-certified by default, but FDA and GMP compliance often require:
A declaration of conformity for material use.
Optional factory inspection reports or audit trails.
Would you like assistance with selecting a line that is pre-certified for FDA and CE, or do you need help preparing compliance documents for an export project?
Ja, de Dog Chews Rawhide Twists Processing Line can be modularly configured to integrate essential post-forming processes zoals drying, flavoring, and sterilization—either inline or as auxiliary systems.
✅ YES – Fully Integratable
Dryer Types:
Multi-layer Mesh Belt Dryer (most common)
Hot Air Circulation Oven
Microwave Dryer (optional, for faster sterilizing/drying)
Temperature Range:
Typically adjustable from 50°C to 90°C, depending on rawhide thickness and moisture.
Voordelen:
Continuous operation synchronized with forming.
Controlled humidity and airflow to prevent cracking or mold.
✅ YES – Optional Integration
Flavor Application Methods:
Spray Coating System: Sprays liquid flavor (chicken, beef, etc.) after partial or full drying.
Tumbler Marination Machine: For soaking or tumbling chews in flavoring solution before final drying.
Notes:
Gebruik food-safe pumps and tanks for flavor liquids.
Some users prefer flavoring after sterilization for strong aroma.
✅ YES – Optional and Recommended
Sterilization Options:
Microwave Sterilization Unit
UV Sterilization Tunnel
Steam Sterilization Cabinet (used offline for bulk batches)
Purpose:
Eliminate pathogens like Salmonella or E. coli.
Required by export regulations (e.g., EU, US).
Placement Options:
After drying (ideal).
Before packaging (if using final surface treatment).
Rawhide Forming
Pre-Drying / Full Drying
Flavor Spray or Tumble Marination
Final Drying
Sterilization
Cooling + Metal Detection
Verpakking
Would you like help designing a complete line layout based on your desired capacity and which of these modules you need? I can provide a recommended configuration.
De Dog Chews Rawhide Twists Processing Line is available in multiple automation levels, depending on your production goals, budget, labor conditions, and desired flexibility. Here's a breakdown of the common configurations:
✅ Ideal for medium to large-scale industrial production
Kenmerken:
Automatic rawhide strip feeding
Continuous forming (twisting, rolling, optional knotting)
Integrated conveyor transfer
Inline drying system (multi-layer or tunnel dryer)
Optional: automatic flavor spraying, sterilization, metal detection, and packing line
Voordelen:
Highest output (up to 300–500 kg/h)
Minimal manual labor (1–2 operators for monitoring only)
Consistent product quality and hygiene
Suitable for export-grade production with strict food safety compliance
Who It’s For:
Large pet chew factories, OEM exporters, high-volume contract manufacturers
⚙️ Flexible for small to medium producers or custom shape output
Kenmerken:
Manual feeding of rawhide strips
Semi-automatic forming machines (e.g., twist rollers or knotting assist machines)
Drying system may be batch oven or separate belt dryer
Optional: manual or batch flavoring and sterilization
Voordelen:
Lower investment cost
Easier shape switching and customization
Can be upgraded to full automation later
Who It’s For:
Startups, niche pet treat brands, custom shape producers
👷 For pilot production, R&D, or small workshops
Kenmerken:
Manual cutting and shaping
Small tabletop forming machines
Drying in hot-air ovens or trays
Hand-applied flavor or sterilization
Who It’s For:
Artisanal producers, test labs, low-volume special order facilities
Automatiseringsniveau | Output | Labor Need | Flexibiliteit | Investment |
---|---|---|---|---|
Fully Automatic | 300–500 kg/h | Very Low | Matig | Hoog |
Semi-Automatic | 100–200 kg/h | Medium | Hoog | Medium |
Manual-Assisted | <100 kg/h | Hoog | Zeer hoog | Laag |
Would you like me to recommend a configuration that matches your target output, space, and labor availability? I can also provide ROI analysis between semi-automatic vs. fully automatic options.
De number of operators required to run the Dog Chews Rawhide Twists Processing Line depends primarily on the automation level, but also on the plant layout, product variety, and whether auxiliary processes (like flavoring and packaging) are integrated.
Line Type | Operators Needed | Opmerkingen |
---|---|---|
Fully Automatic Line | 1–2 operators | One person monitors the control panel, material feed, and forming line. A second may supervise drying, packaging, or quality checks. Very low labor demand. |
Semi-Automatic Line | 3–5 operators | Operators handle rawhide feeding, forming, and transfer to/from dryer. Flexible for various shapes, but needs more manual coordination. |
Manual-Assisted Line | 5–8 operators | Most labor-intensive. Required for hand-feeding, knotting, drying tray loading/unloading, and manual flavoring. |
👨💼 1 Line Supervisor / HMI Operator
👷 1 Material Handler (rawhide feed + packing area support)
(Optional) 1 QC/Inspector during shift
Frequent shape changes or SKU switching
Manual packaging (vs. auto pouch or shrink wrap)
Batch flavoring or off-line sterilization
Manual knotting (if complex shapes not fully automated)
Would you like a labor estimate and layout plan based on a specific capacity goal (e.g., 200 kg/hour)? I can map out operator roles by station for a real-world setup.
De installation space en layout plan for the Dog Chews Rawhide Twists Processing Line depend on your target capaciteit, automation levelen optional modules (e.g., drying, flavoring, sterilization, packaging).
Below is a standard guideline for spatial planning and layout based on different production configurations:
Recommended Space:
Length: 25–35 meters
Width: 5–8 meters
Height: ≥3.5 meters (required for multi-layer dryers)
Layout Includes:
Rawhide strip feeder & pre-soaking area
Forming section (twist/roll/knot machines)
Conveyor transfer system
Multi-layer mesh belt dryer (15–20m long)
Optional modules: flavor sprayer, sterilizer
Cooling conveyor
Automatic packing station
✅ Ideal for large-scale factory floors or export-focused facilities
Recommended Space:
Length: 15–20 meters
Width: 4–6 meters
Height: ≥3.0 meters
Layout Includes:
Manual or assisted feeding area
Semi-automatic forming machines
Belt dryer or hot-air drying oven
Manual/automatic flavoring station
Manual transfer zone
Packaging and metal detection
✅ Flexible and scalable – often installed in modular halls or partitioned workshops
Recommended Space:
Length: 8–12 meters
Width: 3–5 meters
Height: ≥2.8 meters
Layout Includes:
Manual cutting/forming tables
Drying oven and tray stacking area
Small tumbler or manual flavor station
Manual packaging table
✅ Ideal for R&D labs, startup facilities, or custom order production
Rawhide pre-processing area (soaking, softening, trimming)
Water drainage or cleaning zones
Packaging material storage
QC & lab area (optional) for high-end export production
Would you like a custom AutoCAD or PDF layout drawing based on your facility dimensions or target capacity? I can also help optimize the flow line for labor efficiency and hygiene compliance.
De Dog Chews Rawhide Twists Processing Line requires utilities such as elektriciteit, water, and optionally compressed air, depending on the automation level and additional modules (dryers, sprayers, etc.). Below is a detailed breakdown:
Item | Stroomverbruik | Opmerkingen |
---|---|---|
Forming Machine | 2–5 kW | Depends on number of heads and automation level |
Belt Dryer (Electric Heating) | 40–80 kW | Large dryers are power-intensive; may use gas or steam to reduce electricity |
Hot Air Circulation Oven | 15–30 kW | For smaller or batch drying |
Flavor Sprayer / Tumbler | 1–2 kW | Optional |
Koeltransportband | 1–2 kW | Optional |
Metal Detector / Auto Packaging | 2–4 kW | Optional add-ons |
🔌 Total Power Load (fully automatic line):
~60–100 kW, depending on modules and heating method
🔌 Spanning: 380V, 50/60Hz, 3-phase (standard for industrial machinery)
Usage | Estimated Consumption | Opmerkingen |
---|---|---|
Rawhide soaking / softening | 300–600 liters/day | Depends on batch size and hide moisture |
Machine cleaning / sanitation | 200–400 liters/day | Required daily for hygiene |
Optional steam sterilizer | 200–500 liters/batch | If integrated |
💧 Water Quality: Clean potable water or filtered well water is acceptable for rawhide soaking and cleaning.
Uitrusting | Druk | Flow Rate |
---|---|---|
Pneumatic cutters / knotting units / sprayers | 0.6–0.8 MPa | 0.3–0.6 m³/min |
Air-powered packaging or ejectors | Optional | As needed |
🛠️ Compressor Recommendation:
5.5–11 kW air compressor (screw type) with air dryer + 0.6 m³ air tank
Gebruik gas or steam heating for dryers to reduce electrical load.
Recycle hot air in circulation systems to cut down energy use.
Gebruik solar pre-heating or heat recovery if aiming for a sustainable setup.
Would you like a tailored utility layout guide or a power load list to submit to your plant’s engineering team? I can also help match the dryer system to your local energy cost structure (electric vs. gas).
Ja, de Dog Chews Rawhide Twists Processing Line can absolutely be customized with branded molds or specific product designs to help you develop unique, market-differentiated pet chews under your own brand.
Type aanpassing | Beschrijving | Opmerkingen |
---|---|---|
Branded Molds (Logo Embossing) | Custom molds can be made to emboss your brand name, logoof pattern directly onto the chew during forming. | Requires precision CNC mold fabrication. MOQ usually applies. |
Custom Shapes (bones, stars, twists, etc.) | Molds and forming dies can be made for non-standard shapes—braids, knotted bones, candy cane twists, holiday themes. | Ideal for seasonal product lines or private label innovation. |
Size Customization | Length, width, and diameter of twists and rolls can be configured to match your brand’s sizing chart. | Useful for “small dog,” “puppy,” or “long-lasting” chew variants. |
Color/Flavor Coating Zones | Spray systems can be adjusted for multi-flavor of striped color designs with liquid coatings. | Adds visual appeal and branding flexibility. |
Packaging Compatibility | Final product dimensions can be tailored to fit specific pouch or tray sizes for retail-ready output. | Optional integration with auto-packaging lines. |
You provide drawings, samples, or 3D models.
The manufacturer produces custom CNC-engraved molds (twist heads, bone press molds, etc.).
Molds are installed on the forming machine and tested for fit and output.
Adjustments are made for feeding width, forming tension, and drying time to match shape.
Design + Engineering: 5–10 working days
Mold Production: 10–15 working days
Testing & Line Adjustment: 3–5 working days
Total Time: ~20–30 days depending on complexity
Would you like help designing a custom product line with your logo or unique shapes for private label? I can assist with the design process, mold compatibility check, and cost estimate.
A complete Dog Chews Rawhide Twists Processing Line is typically delivered as a modular system, with each unit handling a specific stage of the production process—from rawhide preparation to finished chews. Below is a detailed breakdown of the standard and optional components included in a full processing line package:
Component | Functie | Opmerkingen |
---|---|---|
1. Rawhide Strip Cutter | Cuts rawhide sheets into uniform strips. | Adjustable width (10–50 mm), manual or automatic feeding. |
2. Soaking/Softening Tank | Softens rawhide strips for pliability before forming. | Stainless steel tank; optional heating or agitation system. |
3. Twisting/Rolling Machine | Automatically twists or rolls strips into sticks. | Available in single or multi-head models; shape and length adjustable. |
4. Pressing Unit (Optional) | Compresses or embosses the chew (e.g., bones, logo). | Used for knotted bones or branded designs. |
5. Conveyor Transfer System | Moves product from forming to drying line. | Food-grade belts; fully automated. |
6. Drying System | Dries the chews to safe moisture levels. | Multi-layer mesh belt dryer or hot-air circulation oven. |
7. Cooling Conveyor | Cools the chews before flavoring or packaging. | Prevents condensation and spoilage. |
8. Electrical Control Cabinet (PLC + HMI) | Centralized control of line speed, temperature, timers, alarms. | Touch screen panel with preset programs. |
Component | Functie | Opmerkingen |
---|---|---|
9. Knotting Machine | Assists in forming knotted rawhide bones. | Semi-auto or manual assist. |
10. Braiding Machine | Forms 3-strand or 5-strand braided chews. | For premium chew designs. |
11. Flavoring System (Spray or Tumbler) | Applies chicken/beef flavors or digest coating. | Inline sprayer or batch tumbler with drum rotation. |
12. Sterilization Unit | Kills bacteria (E. coli, Salmonella) pre-packaging. | Microwave, UV, or steam-based options. |
13. Metal Detector | Detects metal contamination before final packaging. | Ensures safety compliance for export. |
14. Auto Packing Machine | Weighs, bags, seals, and codes final product. | Supports zipper pouches, pillow packs, or shrink wrap. |
Machines are delivered modularly assembled or partially disassembled with:
Full wiring diagrams
Layout drawings
User manual and maintenance instructions
Spare parts kit (belts, sensors, O-rings, lubricants)
Would you like a turnkey quotation including all modules for a specific output (e.g., 200 kg/h line with flavoring + auto-packing)? I can also propose a layout diagram tailored to your facility.
De Dog Chews Rawhide Twists Processing Line is built using high-grade, food-safe materials to meet hygiene standards for pet food production and ensure long-lasting, corrosion-resistant operation.
Here’s a breakdown of the key materials used throughout the line:
Component Area | Materiaal | Specificatie | Opmerkingen |
---|---|---|---|
Contact Parts (rollers, forming units, hoppers, chutes) | Stainless Steel 304 | Food-grade, corrosion-resistant | Standard for food machinery; safe for rawhide contact |
Optional Upgrades (for harsh environments or sanitization) | Stainless Steel 316 | Higher corrosion resistance | Recommended if using strong cleaners or operating in humid areas |
Machine Frame & Structural Supports | Stainless Steel 304 of Carbon Steel + Powder Coating | — | Some cost-effective models may use coated carbon steel on non-contact parts |
Belts (Conveyor & Dryer) | Food-grade PU, Teflon (PTFE) meshof SUS 304 mesh | Heat-resistant, FDA-compliant | Choice depends on drying method and heat level |
Electric Cabinet Housing | Stainless Steel 304 or Powder-Coated Steel | IP54–IP65 enclosure | Protects from dust, humidity, and cleaning sprays |
Bearings & Shafts | Chrome steel or SUS 304 | Sealed type | Food-safe, greaseable design |
Spray Nozzles / Flavoring Units | SUS 316 or FDA-grade plastic | Non-corrosive | Especially if flavoring includes acids or oils |
FDA & EU Compliance (material contact safety)
CE-certificering (electrical and structural safety)
GMP/HACCP Compatibility (hygienic construction)
Welds are smooth and polished to prevent bacterial buildup.
Surfaces are designed with rounded edges and minimal dead corners voor eenvoudige reiniging.
Many parts are removable or flip-open for washdown and maintenance.
Would you like to specify SUS 316 upgrades for enhanced corrosion protection, or get a material traceability sheet for certification purposes (especially for FDA or EU audits)?
Ja, on-site installation and operator training are typically included (or available as an add-on service) when purchasing a Dog Chews Rawhide Twists Processing Line, especially from reputable manufacturers or turnkey solution providers.
Here’s how the service is usually structured:
✅ Included in most mid-to-large-scale orders (especially full lines)
What’s Included:
Machine unloading guidance & positioning
Electrical and utility connection assistance
Full mechanical assembly check
Calibration and test running with actual rawhide
Parameter setup for forming, drying, and transferring
Technician Support:
1–2 engineers dispatched for 5–10 working days, depending on line complexity.
Local hotel + food + translator (usually arranged by the buyer).
Round-trip airfare often included or quoted separately.
✅ Always included
Training Covers:
Machine operation & control panel handling (PLC/HMI)
Product changeovers (e.g., switching sizes/shapes)
Daily cleaning and sanitation protocols
Preventive maintenance routines
Troubleshooting common issues
Training Format:
Conducted on-site during and after commissioning
Hands-on sessions with your own team
Optional: Remote refresher training via video after initial install
Video installation guides and manuals
Online training modules for additional staff
Live video troubleshooting with factory engineers
🔧 Installation & Training: Often included in total line price
✈️ Engineer Travel: May be billed separately or pre-included
🏨 Local Accommodation: Usually buyer's responsibility unless negotiated
Would you like a sample installation schedule and a training checklist for operator onboarding? I can also provide a bilingual SOP (Standard Operating Procedure) format tailored to your plant.
De standard lead time for the production and delivery van een Dog Chews Rawhide Twists Processing Line typically ranges between:
Line Type / Size | Production Time | Delivery Time (by sea) | Total Lead Time |
---|---|---|---|
Standard Semi-Automatic Line | 25–30 working days | 15–30 days (port-to-port) | 40–60 days |
Fully Automatic Line (customized) | 35–45 working days | 20–35 days (depending on location) | 55–75 days |
With Custom Molds or Add-ons | +10–15 days extra | — | Varies by complexity |
Aanpassing (branded molds, special shapes, additional modules like flavoring, packing)
Order Queue (busy seasons like Q1 or just before pet expos can cause delays)
Packaging method (container vs. LCL)
Destination country (port distance, customs efficiency)
Day 1–5: Contract signed, deposit received
Day 6–35: Production of standard components and modules
Day 36–45: Assembly + factory test run (FAT)
Day 46–50: Final payment, packing, and shipping arrangement
Day 51–75: Ocean shipping + customs clearance + on-site installation
Priority Production Slot (available at extra cost)
Air Shipment for Urgent Components (costly but faster)
Local agent or warehouse support (if offered by the supplier in your region)
Would you like a sample production & shipping schedule tailored to your port of destination (e.g., Hamburg, Rotterdam, Los Angeles, etc.)? I can also recommend how to align delivery with site preparation and utility readiness.
De Dog Chews Rawhide Twists Processing Line is carefully packed and shipped to ensure safe arrival, smooth unloading, and easy installation at your site. Here’s a detailed explanation of the standard packaging and shipping methods:
Component Type | Packing Style | Kenmerken |
---|---|---|
Forming, cutting, pressing units | Fumigation-free wooden cases | Shock-proof, moisture-resistant, ISPM 15 compliant for export |
Drying system (belt dryer or oven) | Plastic film wrap + steel frame / wooden pallet | For large components that exceed crate size |
Electrical cabinets & sensitive parts | Wooden crates + anti-static/anti-humidity packaging | Protected against vibration, dust, and moisture |
Small tools, manuals, spare parts | Toolbox or carton | Placed inside crate or shipped with main machinery |
✅ All cases are labelled with part names, handling instructions, and weight specs for efficient unloading and installation.
Line Type | Container Requirement | Opmerkingen |
---|---|---|
Semi-Automatic Line (100–200 kg/h) | 1×20ft or 1×40ft container | Depending on dryer size and added modules |
Fully Automatic Line (300–500 kg/h) | 1×40ft HQ container (sometimes 2×40ft HQ for complex setups) | Dryer and forming units loaded separately |
Additional Modules (auto packer, sterilizer) | May require additional LCL or full container | Loaded based on volume and shipping cost efficiency |
🔧 All equipment is arranged for easy unpacking and floor layout assembly at destination.
🌊 By Sea (FCL or LCL) – Most common and cost-effective
✈️ By Air (for urgent small modules or replacement parts)
🚛 Inland transport (to bonded warehouse or consolidation hub, if needed)
📷 Pre-shipping photo or video report (to verify packing and completeness)
🧾 Full packing list + bill of lading + HS codes for smooth customs clearance
🏷️ Barcode or QR labeling on crates for warehouse management
Would you like a container load plan, packing list sample, or recommendations for freight forwarding partners to your destination port? I can also estimate freight cost based on your incoterm (FOB/CIF/DDP).
De standard warranty period for the Dog Chews Rawhide Twists Processing Line is typically:
✅ 12 maanden from:
The date of shipmentof
The date of successful commissioning (if on-site installation is included), whichever comes first.
🛡️ Extended warranty options (up to 24 or 36 months) are often available upon request or with service agreements.
Coverage Area | Inbegrepen | Opmerkingen |
---|---|---|
Core mechanical parts (rollers, shafts, molds, gears) | ✅ Yes | Covers breakage, material defects, abnormal wear |
Electrical components (motors, PLCs, inverters, sensors) | ✅ Yes | Includes branded parts like Siemens, Omron, Delta, etc. |
Control system (PLC/HMI) | ✅ Yes | Software bugs, panel malfunctions included |
Welding & structure | ✅ Yes | Frame deformation, weld cracks covered |
Labor for part replacement | ✅ Yes (if done remotely or by factory technician) | On-site labor included if installation service is purchased |
Shipping cost of spare parts | ❌ Not usually included | Buyer pays freight; parts themselves are free if under warranty |
Consumables (belts, Teflon mesh, gaskets, cutting blades)
Damage due to:
Improper operation or maintenance
Unauthorized modifications
Force majeure (flood, fire, voltage surge)
Downtime losses (though remote troubleshooting is offered)
Lifetime technical support
Spare parts available at factory price
Remote diagnostics via video or online chat
Optional: Annual maintenance packages
Would you like a warranty certificate template, or assistance drafting a service-level agreement (SLA) for extended support coverage? I can also provide examples of typical spare parts kits shipped with the machine.
Yes, most professional manufacturers of the Dog Chews Rawhide Twists Processing Line do support product samples or trial batch testing before you place a final order. This is an excellent way to confirm product quality, machine performance, and shape compatibility.
Option | Beschrijving | Opmerkingen |
---|---|---|
Free Product Samples | The factory can send pre-produced dog chews (e.g., twists, rolls, bones) made on their existing line. | Good for checking quality, size, texture, and market fit. |
Trial Batch with Your Rawhide / Design | You can ship your rawhide material or design sketches, and the factory will run a small trial to produce samples. | Helps validate shape compatibility and drying behavior. |
On-site Trial Run (Factory Visit) | You visit the factory and witness a live demo or a test run using your product specs. | Ideal for confirming forming precision and process stability. |
Online Video Demo with Custom Sample | The factory runs your custom shape or rawhide type and sends you a video + output samples. | Faster and lower cost than physical visit. Often free. |
Test twist tightness, roll diameter, or braid firmness
Check drying time en final moisture level
Run samples with or without flavor coating
Validate custom molds or embossing
Sample chews usually shipped by DHL, FedEx, or EMS
Custom mold trial costs may be refunded upon final order
Confirms product performance before investment
Helps finalize machine configuration (e.g., number of twist heads, dryer size)
Builds trust between buyer and manufacturer
Would you like me to help arrange a custom product sample trial, provide a material submission checklist, or draft a sample trial agreement to protect your design?
Yes, a reputable supplier of the Dog Chews Rawhide Twists Processing Line will provide complete documentation as part of the delivery package. These documents are essential for installation, operation, maintenance, compliance, and troubleshooting.
Document Type | Inbegrepen | Doel |
---|---|---|
✅ User Manual / Operation Manual | Ja | Step-by-step instructions for operating each module (forming, drying, etc.) |
✅ Electrical Schematics / Wiring Diagrams | Ja | Detailed layout of all electrical components, control panels, motor drives, PLCs, and sensor wiring |
✅ P&ID (Piping & Instrumentation Diagram) | Yes (if applicable) | Provided if the line includes pneumatic, steam, water, or flavoring spray systems |
✅ Installation Layout Drawings | Ja | Shows recommended spacing, utility access, and flow line configuration |
✅ Spare Parts List | Ja | Full list of included and optional spare parts with part numbers |
✅ Maintenance Schedule & Checklist | Ja | Covers lubrication, belt tension, cleaning, wear part replacement timelines |
✅ Material Certificates (e.g., SUS 304/316) | Yes (upon request) | For compliance with FDA, CE, or GMP requirements |
✅ PLC/HMI Program Backup | Ja | Preloaded on USB or sent via secure download for recovery |
✅ Certificate of Conformity (CE/FDA/GMP) | Yes (based on configuration) | Required for export or customs clearance |
Printed hard copies + USB flash drive (standard)
Digital PDF or DWG files can be emailed for advance planning
Bilingual versions (e.g., English + Chinese) available
Training SOPs (Standard Operating Procedures)
IQ/OQ validation documents (if used in regulated facilities)
Factory Acceptance Test (FAT) report
Wiring color code legend and control cabinet layout
Would you like a sample document index or a preview of a user manual or electrical schematic from a real order? I can also help draft a technical document checklist to include in your purchase contract.
De standard response time for technische ondersteuning after installing the Dog Chews Rawhide Twists Processing Line is typically very fast, especially if the supplier offers dedicated after-sales service. Here's how it usually breaks down:
Support Type | Reactietijd | Availability |
---|---|---|
Remote Support (online/phone/video) | ✅ Within 12–24 hours (often within 2–6 hours for urgent issues) | 7 days a week, especially during first 3–6 months post-installation |
Email Technical Inquiries | ✅ Within 24 hours | For non-urgent questions, documentation requests |
Spare Part Support | ✅ Quotation within 1–2 working days | Express shipping offered for urgent components |
On-Site Engineer Dispatch | 🚀 Within 3–7 days (international) | Travel time varies based on visa, flight availability, and location |
📞 24/7 phone hotline
💬 Live chat / WhatsApp / WeChat / Skype
🎥 Video troubleshooting via Zoom or Teams
📧 Email ticketing system
🛠️ Local agent support (in selected countries)
PLC or HMI parameter reset
Error code diagnostics
Mechanical jam guidance (e.g., rawhide feeding issues)
Remote program updates or backup restore
Preventive maintenance walkthrough
Free support during warranty period
Priority response within 6–12 hours for registered users
Annual service package with scheduled video inspections
Would you like a sample after-sales support policy, a spare part request form, or a service response agreement template to include in your purchase contract?
Spare parts for the Dog Chews Rawhide Twists Processing Line are typically available for fast shipment, and in some cases, locally stocked depending on the supplier's global presence or partner network.
Here’s a breakdown of what you can expect:
Type of Spare Part | Stock Status | Opmerkingen |
---|---|---|
Standard Wear Parts (belts, blades, gaskets, sensors) | ✅ In stock at factory | Ready for fast air shipment (DHL/UPS/FedEx) within 1–3 days |
Critical Electrical Components (PLC, HMI, inverter, motor) | ✅ Factory stocked or third-party fast source | Branded parts (e.g., Siemens, Delta, Omron) sourced quickly if not on hand |
Custom Molds or Forming Heads | ⚠️ Made-to-order | Production time 7–15 working days depending on complexity |
Large Modules or Non-consumables | ⚠️ Usually made-to-order | Shipped by sea or air depending on urgency |
✈️ Express Air: 3–7 days worldwide (DHL, UPS, FedEx)
🚢 Sea Freight: For bulky items (dryers, cabinets) – 20–40 days
🛒 Local Agent/Warehouse Support: Available in select regions (ask supplier)
Most suppliers include a starter kit of high-wear parts, which often contains:
Conveyor belt spares
Forming machine rubber rollers or seals
Teflon mesh (for dryer)
Cutting blades
Limit switches / sensors
Grease / oil
Request a recommended spare parts list for 6–12 months of operation.
Keep critical parts on-site to avoid downtime, especially for exports or remote locations.
Would you like help creating a spare parts inventory checklist or a preloaded maintenance toolkit tailored to your production capacity? I can also help negotiate free spare parts bundles as part of your machine order.
Ja, remote troubleshooting and software support are definitely available for the Dog Chews Rawhide Twists Processing Line, especially if the line is equipped with a modern PLC + HMI control system (which is standard for mid-to-high-end models).
Functie | Availability | Beschrijving |
---|---|---|
Real-time video support | ✅ Yes | Via WhatsApp, Zoom, WeChat, or Teams—used to guide your operator through diagnosis and quick fixes. |
Error code analysis | ✅ Yes | If the HMI shows faults (e.g., motor overload, temperature alarms), technicians can advise based on your screenshots or videos. |
Live programming assistance | ✅ Yes | For adjusting parameters (speed, temperature, timing) or restoring factory settings via HMI. |
Step-by-step PDF/Video guides | ✅ Yes | Sent for common troubleshooting tasks like belt alignment, sensor adjustment, or mold replacement. |
Functie | Beschrijving |
---|---|
Remote program update | PLC logic or HMI interface can be updated via USB, SD card, or remote link (TeamViewer or VNC). |
Backup & recovery files | Provided at installation or upon request to restore original factory settings. |
Custom parameter reprogramming | If you switch product types (e.g., twist → knot), software can be updated remotely. |
🖥️ Common PLC brands supported: Siemens, Delta, Mitsubishi
📱 HMI brands: Weinview, Siemens, Kinco
Internet connection at the control panel (or nearby laptop/tablet)
Photos/videos of machine panel and fault condition
Serial number or machine ID for reference
Reduces downtime significantly
Avoids travel cost for minor issues
Ensures long-term usability and flexible production switching
Would you like a checklist of recommended remote diagnostic tools to keep at your site, or a sample support request form template for structured communication with the technical team?
De recommended maintenance schedule for the Dog Chews Rawhide Twists Processing Line is designed to ensure optimale prestatie, long service lifeen constante productkwaliteit. Below is a detailed daily, weekly, monthly, and quarterly maintenance checklist tailored for production environments.
Component | Taak | Opmerkingen |
---|---|---|
Forming Units | Wipe down rollers and molds with food-safe cloth | Prevents rawhide buildup and jamming |
Transportbanden | Inspect for debris, damage, or misalignment | Clean with warm water or approved cleaner |
Dryer (Mesh Belt or Oven) | Remove visible residue; check exhaust vents | Clean mesh or trays daily after use |
Control Panel (HMI/PLC) | Wipe screen, inspect for alarms | Log any fault messages for review |
Lubrication Points (Light-use) | Check moving parts (guide rails, chains) | Apply food-grade grease if needed |
Component | Taak | Opmerkingen |
---|---|---|
Twisting/Pressing Mechanism | Inspect bearings, seals, alignment | Adjust or tighten loose fittings |
Sensors & Limit Switches | Test functionality | Clean photoeyes or proximity sensors |
Dryer Fans & Heating Elements | Clean vents, inspect for overheating signs | Tighten any loose terminal connections |
Compressed Air System (if used) | Drain air tank moisture; check pressure | Inspect filters and hoses for leaks |
Component | Taak | Opmerkingen |
---|---|---|
Gearboxes & Motors | Inspect oil/grease level; listen for noise | Re-lubricate per manufacturer spec |
Electrical Cabinet | Dust removal, tighten terminals | Use anti-static cloth; check for heat damage |
Flavored Spray Unit / Tumbler (if any) | Deep clean tanks and nozzles | Prevent clogging and flavor contamination |
Metal Detector / Auto Packer (if equipped) | Verify calibration with test samples | Replace worn seals or belts |
Component | Taak | Opmerkingen |
---|---|---|
Full Line Mechanical Inspection | Check for abnormal wear or fatigue | Replace worn parts proactively |
PLC / HMI System | Backup control program to USB/PC | Check for firmware updates |
Safety Devices | Test emergency stop buttons, covers | Verify interlock function |
Performance Test | Run product output & weight accuracy test | Validate line efficiency and waste % |
Belts (conveyor, mesh)
Twisting molds or heads
Teflon sheets
Photoelectric sensors
Gearbox oil and food-grade grease
Touch screen protective film
Digital caliper & belt tension gauge
Infrared thermometer
Air blower for control cabinets
Portable grease gun
pH-neutral cleaning agents
Would you like this maintenance schedule formatted as a printable log sheet or SOP (Standard Operating Procedure) for your team? I can also help you prepare a preventive maintenance calendar with reminders.
Ja, video tutorials and detailed service manuals are typically provided by professional manufacturers of the Dog Chews Rawhide Twists Processing Line to ensure that your operators and maintenance team can confidently operate, maintain, and troubleshoot the line.
Tutorial Type | Inbegrepen | Content Covered |
---|---|---|
✅ Operation Walkthrough | Ja | Step-by-step video of how to start, run, and stop the full line (including twist forming, drying, transferring, etc.) |
✅ Cleaning & Sanitation Guide | Ja | Proper cleaning of forming heads, conveyors, dryer mesh, and flavoring systems |
✅ Maintenance Procedures | Ja | Lubrication points, sensor checks, belt alignment, and safety testing |
✅ Troubleshooting & Reset Demo | Ja | How to handle error codes, sensor misfires, motor resets, or HMI parameter changes |
✅ Mold Change & Product Switching | Ja | How to replace twist rollers or configure the machine for different chew shapes/sizes |
🔧 Format: MP4 video files via USB, download link, or private YouTube link (bilingual versions often available: English + Chinese)
Manual Type | Inbegrepen | Format |
---|---|---|
✅ User Operation Manual | Ja | Printed + PDF; with diagrams, safety info, settings |
✅ Maintenance Manual | Ja | Includes lubrication charts, wear part diagrams, replacement schedules |
✅ Troubleshooting Guide | Ja | Fault codes, HMI error messages, common issues and fixes |
✅ Electrical & Pneumatic Diagrams | Ja | Essential for in-house technicians to handle control panel and wiring |
Laminated SOPs (Standard Operating Procedures) for quick reference at each station
QR code labels on machines linking directly to related tutorial videos
Remote live training sessions via Zoom/Teams with factory engineers
Would you like a sample video tutorial list, bilingual SOP template, or help creating a training checklist for your team to standardize operator certification?
Ja, de Dog Chews Rawhide Twists Processing Line is typically designed with a modular and upgradeable architecture, allowing you to scale or enhance your line in the future as your production needs grow.
Upgrade Option | Beschrijving | Voordeel |
---|---|---|
Additional Cutting Units | Add precision length cutters or multi-blade systems | Enables faster shaping or diversified chew lengths |
Advanced Forming Modules | Add new rollers, braiding heads, or knotting attachments | Expand your product portfolio (e.g., knotted bones, braids, candy canes) |
Automated Feeding System | Upgrade to auto rawhide strip feeder | Increases line speed and reduces manual labor |
Automatic Flavoring Unit | Integrate inline liquid spray or tumbler marination system | Improves consistency and production hygiene |
Sterilization Module | Add UV, microwave, or steam sterilization section | Meets export or food safety regulations (e.g., FDA/CE) |
Smart HMI/PLC Upgrade | Install advanced touch screens with recipe memory & remote diagnostics | Improves operator usability and remote support capability |
Inline Metal Detector + Auto Packer | Add end-of-line safety and packaging system | Speeds up final packing and meets retail/export standards |
✅ Modular Conveyor Sections: Allow spacing and insertion of new machines
✅ PLC/HMI Expandability: Designed with additional I/O ports for future integration
✅ Stainless Steel Frame Standardization: Matching height and connection points across modules
✅ Pre-wired Expansion Ports: Optional (if requested at purchase)
Ask for future-proof electrical cabinet design
Leave space in your layout for expansion zones
Select HMI software that supports multi-recipe storage
Choose standardized machine widths for easier line syncing
Would you like a custom upgrade roadmap based on your current setup and 12–24 month expansion plans? I can also provide a phased investment layout to help you plan capacity growth while managing capital efficiently.
Ja, long-term service support is available, and extended warranties can be purchased for the Dog Chews Rawhide Twists Processing Line, especially when working with a reputable manufacturer or OEM supplier.
Support Type | Availability | Details |
---|---|---|
Lifetime Technical Support | ✅ Yes | Free consultation via email, phone, or video chat for the full service life of the equipment |
Spare Parts Supply Guarantee | ✅ Yes | 10+ years availability of standard and critical spare parts at factory price |
Remote Software Support | ✅ Yes | Ongoing support for PLC/HMI updates, parameter reprogramming, and troubleshooting |
Annual Maintenance Visits (optional) | ✅ Available by contract | Factory engineers visit your plant to inspect, calibrate, and upgrade the line |
Warranty Plan | Duur | Coverage |
---|---|---|
Standard Warranty | 12 maanden | Covers mechanical, electrical, and control system components |
Extended Warranty | +12 to +24 months | Can be purchased at time of order or before original warranty expires |
Premium Support Package | Custom (1–3 years) | Includes priority remote support, discounted spare parts, annual inspection, and training refreshers |
What It Covers:
PLCs, motors, sensors, gearboxes, inverters
Welding structure (cracks/deformation)
Free replacement of defective parts (buyer covers freight after year 1)
Remote troubleshooting and technical files
Extended Warranty Contract
Service & Support Policy
Maintenance Log Templates (for warranty validity)
Extended warranty pricing depends on line complexity and module count.
Some suppliers bundle extended service into full turnkey projects or multi-line installations.
Would you like a sample extended warranty contract or help creating a long-term maintenance & support agreement with clear KPIs (response time, part delivery time, support availability)?
Explore trends, tips, and innovations in Rawhide Twisting Line. Enhance efficiency and quality with expert insights.
Zelf droog hondenvoer maken is een lonende manier om ervoor te zorgen dat uw huisdier een uitgebalanceerde voeding krijgt
Zelf droog hondenvoer maken is een lonende manier om ervoor te zorgen dat uw huisdier een uitgebalanceerde voeding krijgt
Zelf droog hondenvoer maken is een lonende manier om ervoor te zorgen dat uw huisdier een uitgebalanceerde voeding krijgt
Zelf droog hondenvoer maken is een lonende manier om ervoor te zorgen dat uw huisdier een uitgebalanceerde voeding krijgt
Zelf droog hondenvoer maken is een lonende manier om ervoor te zorgen dat uw huisdier een uitgebalanceerde voeding krijgt
Zelf droog hondenvoer maken is een lonende manier om ervoor te zorgen dat uw huisdier een uitgebalanceerde voeding krijgt
laten we bespreken hoe we u kunnen helpen uw doelstellingen te bereiken en uw bedrijf te laten groeien!
Vertel ons zo specifiek mogelijk over uw behoeften.
Wij werken aan de beste oplossing & offerte op basis van uw vereisten.
Wij beginnen met de productie nadat wij uw goedkeuring en aanbetaling hebben ontvangen, en wij zorgen voor de verzending.
- Maak u geen zorgen, wij haten spam ook!
- Bel alleen als meerdere e-mails onbeantwoord blijven!