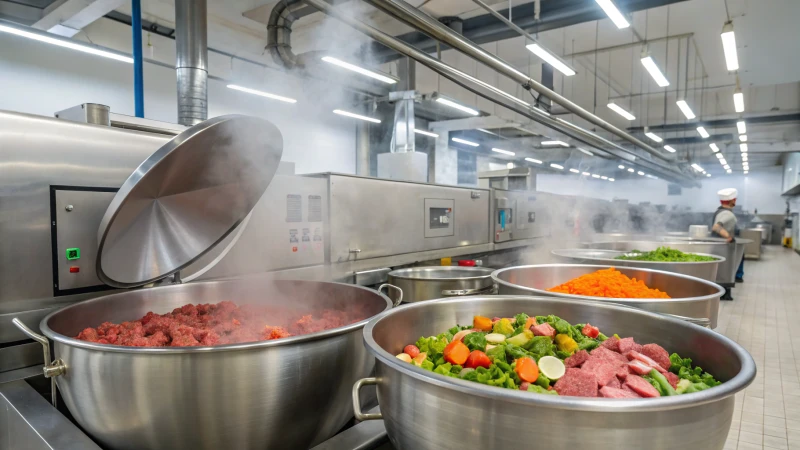
Wat zijn de grondstoffen voor de productie van dierenvoeding?
Zelf droog hondenvoer maken is een lonende manier om ervoor te zorgen dat uw huisdier een uitgebalanceerde voeding krijgt
Darin® Moist Treats Processing Line is a state-of-the-art system designed for high-efficiency production of soft, chewy, and jelly-based pet snacks. Engineered for pet food manufacturers, this fully automated line integrates advanced mixing, precision forming, rapid sterilization, and airtight packaging technologies. Customizable to produce meat paste strips, gel bites, or layered treats, it ensures compliance with global safety standards (AAFCO, FDA, EU). With a hygienic stainless-steel design and intelligent control interfaces, Darin® minimizes downtime, reduces labor costs, and scales output up to 2,000 kg/hour. Ideal for brands prioritizing quality, innovation, and rapid market adaptation.
Soft meat strips, collagen chews, vitamin-enriched jelly snacks, dental care bites.
Core Advantages:
Multi-Ingredient Compatibility: Seamlessly process meat, vegetables, grains, and functional additives.
Scalable Efficiency: Choose between compact (DR-SL5) or high-capacity (DR-SL20) models to match your production needs.
Energy-Saving Design: 30% lower energy consumption vs. conventional systems, with transparent power usage metrics.
Hygienic & Smart: CIP/SIP cleaning, IoT-enabled monitoring, and antimicrobial surfaces for contamination-free output.
Ideaal voor: Meat strips, collagen chews, veggie blends, functional jelly snacks, and grain-free formulations.
Model | Output | Installed Capacity |
---|---|---|
DR-SL5 | 500 kg/u | 37 kW |
DR-SL20 | 2000 kg/h | 75 kW |
The Darin® Moist Treats Processing Line seamlessly integrates 12 core components to automate the entire workflow from raw material preparation to sterile packaging. Designed for precision and hygiene, this system ensures consistent quality for soft, chewy, or gel-based pet snacks. The system includes:
① Control Cabinet
② Meat Grinder
③ Skip elevator A
④ Mixer
⑤ Skip elevator B
⑥ Vacuum Former
⑦ Steam Cooker
⑧ Auto Cutter
⑨ Conveyor
⑩ Gravy Cookers
⑪ Packing Machine
⑫ Autoclave
The Darin® Moist Treats Processing Line operates through a fully automated, step-by-step workflow designed to transform raw ingredients into high-quality moist pet snacks. Below is a detailed breakdown of the process:
Belangrijkste onderdelen:
Meat Grinder (②): Fresh meat or meat powder is ground into a uniform consistency.
Skip Elevators (③, ⑤): Transport raw materials (e.g., vegetables, flour, fat) to the mixer.
Proces:
Ingredients are pre-processed, weighed, and fed into the system. Dry and wet components are separated for precise mixing.
Belangrijkste onderdelen:
Mixer (④): Combines meat, vegetables, flour, and additives (e.g., vitamins, preservatives) into a homogeneous paste.
Control Cabinet (①): Adjusts mixing parameters (speed, temperature) via PLC automation.
Proces:
Recipes are programmed into the system to ensure consistency. The mixture is vacuum-treated to remove air bubbles.
Belangrijkste onderdelen:
Vacuum Former (⑥): Shapes the mixture into strips, bites, or layered textures.
Steam Cooker (⑦): Cooks products gently to retain moisture and nutrients.
Gravy Cookers (⑩): Adds liquid flavors or coatings (e.g., collagen, broth).
Proces:
Formed snacks are partially cooked to set their structure. Optional flavor infusions are applied here.
Belangrijkste onderdelen:
Auto Cutter (⑧): Slices cooked products into uniform sizes.
Conveyor (⑨): Transfers snacks to the next stage without manual handling.
Proces:
Products are cooled slightly before cutting to maintain shape integrity.
Belangrijkste onderdelen:
Autoclave (⑫): Uses high-pressure steam to sterilize snacks (eliminates pathogens).
Packing Machine (⑪): Seals products in airtight pouches or trays with gas flushing (extends shelf life).
Proces:
Sterilized snacks are cooled, inspected, and packaged under hygienic conditions. Labels and batch codes are auto-printed.
Smart Monitoring:
IoT sensors track temperature, humidity, and microbial levels in real time.
Uitvoercapaciteit:
DR-SL5 Model: 500 kg/hour (ideal for startups or niche brands).
DR-SL20 Model: 2000 kg/hour (suits large-scale manufacturers).
For a tailored solution, Neem contact met ons op to optimize your moist treats production! 🐾
Looking to create a unique pet food product? We provide full customization services, from concept to finished machine. Our engineering team uses CAD and 3D modeling to bring your ideas to life—fast and accurately. Let’s work together to build your next best-seller.
The Darin® Moist Treats Processing Line delivers automated, hygienic, and flexible pet snack production. Featuring PLC and IoT-driven control, it ensures precision with reduced labor costs. CIP/SIP cleaning, antimicrobial surfaces, and FDA-compliant sterilization guarantee safety. Adaptable for grain-free, collagen-rich, or functional treats, it cuts energy use by 30% versus traditional lines. Choose scalable models—DR-SL5 (500kg/h) for startups or DR-SL20 (2000kg/h) for mass production—all meeting AAFCO, FDA, and EU standards. Elevate your brand with premium dental chews, hypoallergenic bites, or high-moisture snacks. [Contact us] to innovate smarter! 🐾
De motoren van Darin Machinery zijn afkomstig van WEG met 3 jaar wereldwijde garantie of Siemens.Geniet van een betrouwbaar wereldwijd after-sales service systeem.
Elektrische onderdelen zijn van ABB of Schneider, gemakkelijk te vervangen op de plaatselijke markt.
PLC- en aanraakschermen van Siemens, Duitsland, worden door Darin Machinery gebruikt om de bediening te vereenvoudigen en minder arbeid te vereisen.
Als er storingen optreden, geven de touchscreens van Darin Machinery relevante informatie weer, zodat problemen snel kunnen worden gediagnosticeerd en opgelost.
De bedieningskasten van Darin Machinery zijn uitgerust met een veilige spanning van 24 V, zodat de veiligheid van de operator zelfs bij een elektrische lekkage gewaarborgd is.
Darin Machinery heeft drie soorten beschermers: overstroom, overspanning en oververhitting om de veiligheid van de machine en de operator te garanderen.
Servo follows the cutting size more accurately, rolling cutting can cut products with strong toughness, such as cowhide products, and the cutter does not cut the conveyor belt.
The end of the conveyor belt has a small turning radius, which makes material transportation smoother.
Its components are arranged for quick disassembly, ensuring efficient upkeep and hygienic operation.
Alle deksellichamen, gaasbanden en onderdelen die in contact komen met materialen bij Darin Machinery zijn gemaakt van voedselveilig roestvrij staal 304, voor een superieure duurzaamheid en veiligheid.
Darin® Machinery is global leading manufacturer of pet food production lines, Darin® provide full-cycle, one-stop production equipment solutions for all types of pet food, pet treats & pet health products.
Alle machines zijn gecertificeerd met Europese CE-goedkeuring en ISO 9001-certificering.
■ Run in 99+ countries including USA, Germany, Japan, Italy, UAE, Australia etc.
■ Machineleverancier van General Mills, Kelloggs, Melinda, Bill Gates foundation & Wanpi.
■ 290+ Invention patents & utility model patents.
■ Government-certified high-tech enterprise.
■ Member of APPA (USA) & Deputy President Unit of SDPIA.
■ Professional food machinery manufacturer with 18 years of experience.
Ons uitgebreide productassortiment omvat productielijnen voor droogvoer, natvoer, halfvochtig voer en rauw voer, maar ook gewone traktaties voor huisdieren zoals koekjes, jerky, tandkluiven, runderhuidkluiven en trainingssnacks. Daarnaast bieden we verschillende productielijnen voor voedingsmachines, snacks, energierepen en ondersteunende apparatuur.
Darin Machinery’s equipment is operational in over 99 countries and regions, including the USA, Germany, Japan, Italy, Spain, the Netherlands, Australia, Canada, Holland, Saudi Arabia, Brazil, Mexico, Indonesia, Thailand, and more. Darin Machinery serves renowned clients worldwide, including General Mills, Kellogg’s, and the Bill & Melinda Gates Foundation, among top-tier pet food suppliers.
When purchasing the Moist Treats Processing Line, you might be interested in the following questions.
Core Technical Specifications of Darin® Moist Treats Processing Line
As a leading supplier of pet food machinery, Darin® Machinery designs its Verwerkingslijn voor vochtige lekkernijen to deliver precision, efficiency, and compliance. Below are the key technical specifications:
Model | Output | Installed Capacity |
---|---|---|
DR-SL5 | 500 kg/hour | 37 kW |
DR-SL20 | 2000 kg/hour | 75 kW |
Schaalbaarheid: Choose compact (DR-SL5) or high-throughput (DR-SL20) models to match your production needs.
Besturingssysteem:
PLC & IoT Integration: Centralized control cabinet for automated parameter adjustments (mixing speed, temperature, sterilization time).
Real-time bewaking: Sensors track humidity, microbial levels, and energy consumption.
Core Equipment:
Meat grinder (for fresh meat/powder), vacuum mixer, steam cooker, autoclave (sterilization), and gas-flush packaging machine.
Customizable vacuum former for shaping strips, bites, or layered textures.
Grondstoffen: Meat powder, fresh meat, vegetables, flour, fat, collagen, and functional additives (e.g., vitamins, preservatives).
Formula Flexibility: Supports grain-free, high-protein, hypoallergenic, and functional recipes.
Sanitation Design:
CIP/SIP Systems: Automated cleaning-in-place and sterilization-in-place.
Antimicrobial Surfaces: Stainless steel construction with FDA-compliant conveyor belts.
Sterilization: Autoclave achieves 121°C/250°F for pathogen elimination (FDA and EU compliant).
30% Lower Energy Consumption vs. traditional lines (e.g., DR-SL20 uses only 75 kW for 2000 kg/h output).
Heat Recovery Systems: Reuse excess steam energy during cooking and sterilization.
Meets AAFCO, FDAen EU pet food safety regulations.
Certifications: ISO 9001 (quality management), CE (EU machinery safety).
Product Types: Soft meat strips, dental chews, collagen-enriched snacks, jelly bites, and hypoallergenic formulas.
Packaging Formats: Aseptic pouches, trays, or bulk packaging with gas-flush preservation.
Why These Specs Matter?
Efficiëntie: High throughput with minimal downtime (automated workflows).
Veiligheid: Guaranteed pathogen-free output for global market access.
Adaptability: Rapid switch between recipes and shapes to meet trending demands.
For a detailed technical proposal, Contact Darin® Machinery Team – let’s tailor a solution for your production goals! 🏭
Raw Materials Compatible with the Darin® Moist Treats Processing Line
The Darin® Moist Treats Processing Line is engineered to handle a wide variety of raw materials, enabling versatile production of high-quality pet snacks. Below is a detailed breakdown of compatible ingredients and their applications:
Fresh Meat: Chicken, beef, pork, fish (ground by the meat grinder for uniform texture).
Meat Powder: Dehydrated poultry, liver, or seafood (ideal for concentrated protein formulas).
Collagen & Gelatin: Added for chewiness or to create jelly-like textures.
Animal Fats: Rendered poultry fat, fish oil (enhances flavor and energy density).
Groenten: Carrots, peas, spinach (finely chopped or pureed for nutrient retention).
Grains/Alternatives:
Traditional: Wheat flour, rice flour (binder for texture).
Graanvrij: Potato starch, tapioca, chickpea flour (supports hypoallergenic recipes).
Vezelbronnen: Pumpkin, sweet potato (for digestive health snacks).
Vitaminen en mineralen: Custom premixes (e.g., A, D3, taurine for nutritional balance).
Conserveringsmiddelen: Natural options like rosemary extract or citric acid.
Functional Powders: Probiotics, glucosamine, or omega-3 blends (targeted health benefits).
Broths & Gravies: Chicken/beef broth (injected via gravy cookers for palatability).
Hydration Agents: Water or bone broth (adjust moisture content in final products).
Natural Flavors: Liver powder, yeast extract (boost aroma without artificial additives).
Novel Proteins: Insect meal, venison (for limited-ingredient diets).
Plant Proteins: Soy isolate, pea protein (vegan or hypoallergenic formulations).
Fruit Purees: Apples, blueberries (added for antioxidants or natural sweetness).
Texture Adaptation:
Soft & Chewy: Blends meat/fat with binding agents (e.g., flour, gelatin).
Jelly/Gel-Based: Uses collagen or plant-derived gelling agents.
Vochtbeheersing: Adjustable steam cooking and vacuum mixing to retain 20-40% moisture.
Hybrid Formulas: Seamlessly combine animal and plant ingredients (e.g., meat + vegetable strips).
Preventie van besmetting:
Stainless steel contact surfaces and CIP/SIP systems ensure allergen separation.
Dedicated production zones for raw vs. cooked materials.
Naleving: Handles ingredients meeting AAFCO, FDA, and EU feed regulations.
Example Applications:
Tandkauwen: Meat strips with calcium additives.
Functional Bites: Collagen jelly with joint-support supplements.
Grain-Free Snacks: Pureed chicken + pea starch bites.
For tailored material compatibility testing or recipe development, Contact Darin® Team – we’ll optimize your formulation for seamless production! 🐾
Can the Darin® Moist Treats Processing Line Be Customized for Specific Factory Layouts or Unique Processes?
Absolutely. The Darin® Moist Treats Processing Line is designed with modularity and adaptability at its core, ensuring seamless integration into diverse factory environments and specialized production workflows. Below are the key customization capabilities we offer:
Modular Components:
Equipment (e.g., mixer, vacuum former, autoclave) can be rearranged or scaled to fit limited floor space, irregular shapes, or multi-level facilities.
Conveyor lengths and angles are adjustable to align with existing workflows.
Compact Models:
De DR-SL5 (500 kg/h) is ideal for small factories, while the DR-SL20 (2000 kg/h) can be configured for high-density layouts.
Add-On Modules:
Integrate specialized steps like flavor spraying, vriesdrogenof CBD infusion for functional treats.
Add in-line quality control systems (e.g., X-ray detection, moisture sensors).
Recipe-Specific Adjustments:
Modify mixing time, steam pressure, or sterilization parameters to suit unique formulations (e.g., high-collagen chews or vegan jelly snacks).
PLC/IoT Compatibility:
Sync with your factory’s ERP/MES systems for real-time data sharing.
Customize HMI interfaces to match operator preferences or multilingual needs.
Energy System Adaptations:
Adjust voltage (220V/380V), steam supply, or compressed air interfaces to align with local infrastructure.
Material-Specific Sanitation:
Install allergen-segregation zones or dedicate equipment lines for halal/kosher-certified production.
Upgrade to ATEX-certified components for dust-prone environments.
Regulatory Tailoring:
Modify documentation and validation protocols to meet regional standards (e.g., China’s GB/T, Japan’s JAS).
Pre-Installation Services:
3D factory layout simulations to optimize space and workflow efficiency.
Mockup trials for new recipes or packaging formats.
Post-Installation Optimization:
Remote IoT diagnostics and on-site training for unique processes.
A client in Europe required a hypoallergenic cat treat line with:
Compact layout (15m x 8m area).
Integration of a proprietary probiotic coating system.
Compliance with EU organic certification.
Oplossing:
Shortened conveyor paths and vertical stacking of the autoclave/packaging units.
Added a post-cooking probiotic spray module.
Upgraded CIP cycles and documentation for organic audits.
Why Choose Darin® for Customization?
Proven Expertise: 15+ years of tailoring lines for 200+ global clients.
Fast ROI: Minimize downtime with pre-engineered modular upgrades.
Future-Proof Design: Scalable architecture supports emerging trends (e.g., insect protein, sustainable packaging).
Neem contact met ons op to schedule a factory assessment and design a line that fits like a glove! 🛠️
Ja, de Verwerkingslijn voor vochtige lekkernijen complies with FDA-voorschriften (via mandatory facility and product registration), CE standards (if applicable for EU markets), and GMP requirements (through adherence to quality management protocols). Below are details:
FDA Compliance
The line meets FDA requirements through facility registration en product listing in FDA’s database. FDA does not issue certificates; compliance is confirmed via a registration number and official acknowledgment letter147.
A U.S. agent is required for registration15.
CE-certificering
If the line is exported to the EU, CE marking is required. This involves compliance with EU directives (e.g., machinery safety), testing by EU-notified bodies, and technical documentation268.
GMP Compliance
The line adheres to Goede productiepraktijken (GMP) for hygiene, traceability, and quality control. GMP certification is typically verified through third-party audits158.
For specific documentation or certification inquiries, please provide the target market and product category.
Ja, de Verwerkingslijn voor vochtige lekkernijen incorporates energy-saving modes and green technologies to enhance efficiency and reduce environmental impact. Here are the key features:
Energy-Efficient Heating Systems
The line utilizes optimized thermal management, such as precise temperature control and heat recovery mechanisms, to minimize energy consumption during heating or drying processes. For example, some systems employ closed-loop steam circulation to reuse waste heat, reducing overall energy demand79.
Green Material Compatibility
The equipment supports processing of biodegradable or plant-based ingredients, aligning with sustainable production trends. This includes compatibility with bio-based packaging materials and reduced reliance on synthetic additives3.
Water Conservation Technologies
Advanced water recycling systems are integrated to reduce freshwater usage. For instance, wastewater from cleaning or cooling processes is filtered and reused, lowering both water consumption and discharge410.
Low-Emission Design
The line adheres to environmental regulations by incorporating technologies like vapor condensation and exhaust gas treatment systems to minimize volatile organic compound (VOC) emissions and carbon footprint17.
Smart Automation
Automated controls and IoT-enabled sensors optimize resource allocation (e.g., adjusting energy use based on real-time production demands), further enhancing energy efficiency8.
For specific configurations or certifications related to green technologies, additional details can be provided based on the target market and operational requirements.
To ensure optimal performance and seamless integration of the Darin® Moist Treats Processing Line, your facility must meet the following infrastructure specifications. These requirements are designed to support hygiene, efficiency, and safety while aligning with global production standards:
Spanning:
DR-SL5: 380V, 3-phase, 50/60Hz (37 kW installed capacity).
DR-SL20: 380V, 3-phase, 50/60Hz (75 kW installed capacity).
Backup Systems:
Uninterruptible Power Supply (UPS) recommended for critical components (e.g., PLC control cabinet).
Water Quality:
Potable water supply (pH 6.5–7.5, <50 ppm hardness) for cleaning and steam generation.
Optional: RO filtration system for CIP/SIP cleaning.
Steam Capacity:
200–300 kg/hour of dry saturated steam (6–8 bar pressure) for cooking and sterilization.
Production Area:
Model | Minimum Floor Space | Layout Type |
---|---|---|
DR-SL5 | 10m (L) × 5m (W) × 3m (H) | Linear or U-shaped |
DR-SL20 | 25m (L) × 8m (W) × 4m (H) | Linear with parallel zones |
Floor Load: ≥500 kg/m² (reinforced concrete recommended).
Clearance: 1m around equipment for maintenance access.
Airflow:
10–15 air changes/hour in production areas to control humidity and odors.
Exhaust systems for steam and heat discharge (e.g., above autoclave and steam cookers).
Temperatuurregeling:
Maintain 18–25°C in processing zones to prevent ingredient degradation.
Compressed Air:
Oil-free, dry air supply (6–8 bar, 0.5 m³/min) for pneumatic controls and packaging.
Gas Flushing (Optional):
Nitrogen/CO₂ supply for modified atmosphere packaging (MAP).
Drainage System:
Sloped floors with stainless steel drains (DN50 minimum) for CIP wastewater.
Grease traps for fat/oil separation in effluent.
Waste Handling:
Dedicated zones for recyclable packaging waste and organic byproducts.
Electrical Safety:
Grounding systems and circuit breakers compliant with IEC/EN 60204-1.
Fire Protection:
Class B/C fire extinguishers near heat-generating equipment (e.g., steam cookers).
Certificeringen:
Facility must meet local food safety regulations (e.g., HACCP, ISO 22000).
Cold Storage: For raw material preservation (0–4°C).
Dust Control: Centralized vacuum systems for powder handling areas.
IoT Integration: Pre-wired data ports for real-time monitoring dashboards.
Pre-Installation:
3D layout simulations to optimize space and workflow.
Utility audits to verify compatibility (e.g., voltage stability, steam capacity).
Post-Installation:
Staff training for equipment operation and maintenance.
Annual calibration and compliance checks.
Why These Requirements Matter?
Maximize Uptime: Proper power, steam, and airflow prevent operational bottlenecks.
Ensure Hygiene: Compliant drainage and ventilation reduce contamination risks.
Future-Proofing: Modular design allows phased upgrades (e.g., adding IoT sensors).
Contact Darin® Engineers for a facility assessment and customized installation plan! 🏭
The delivery lead time for the Darin® Moist Treats Processing Line depends on model selection, customization requirements, and logistics planning. Below is a detailed breakdown of timelines and key considerations:
Model | Standard Configuration | Customized Configuration |
---|---|---|
DR-SL5 | 60–75 days | 90–120 days |
DR-SL20 | 90–120 days | 120–150 days |
Standard Configuration: Pre-engineered setups with default specifications (no major customization).
Customized Configuration: Includes layout adjustments, specialized modules (e.g., freeze-drying), or compliance upgrades.
Order Confirmation & Design Finalization:
Standaard: 1–2 weeks (approval of technical drawings and contracts).
Customized: 3–4 weeks (includes 3D simulations and mockup trials).
Manufacturing & Assembly:
*DR-SL5*: 30–40 days (compact design, fewer components).
*DR-SL20*: 60–75 days (complex assembly for high-capacity systems).
Testing & Quality Assurance:
10–15 days for factory acceptance testing (FAT) to ensure compliance with specifications.
Packaging & Shipping:
15–25 days for sea freight (varies by destination port).
Expedited: 5–7 days for air freight (additional cost applies).
Installation & Commissioning:
2–3 weeks for on-site setup, including staff training and trial runs.
Customization Complexity:
Adding non-standard modules (e.g., probiotic spray systems) may extend timelines by 4–8 weeks.
Material Availability:
Specialty components (e.g., ATEX-certified parts) may require longer procurement.
Logistics:
Port congestion, customs clearance, or regional holidays can delay delivery.
Priority Production Slots: Reduce manufacturing time by 20% (additional 15–20% cost premium).
Partial Shipments: Critical components (e.g., control cabinets) can be air-freighted ahead of full shipment.
Pre-Installation:
Darin® provides a detailed installation checklist 30 days prior to shipment.
On-Site Assistance:
Engineers dispatched for commissioning (included in standard service packages).
Why Choose Darin®?
Transparent Scheduling: Real-time progress updates via IoT-tracked production stages.
Global Logistics Network: Partnerships with DHL, Maersk, and FedEx ensure reliable delivery.
Risk Mitigation: Contingency plans for supply chain disruptions (e.g., backup component suppliers).
Neem contact met ons op to lock in your production slot and receive a guaranteed delivery timeline! 🚚
Yes, Darin® Machinery offers comprehensive on-site installation support to ensure seamless commissioning and optimal performance of your Moist Treats Processing Line. Our service package includes the following:
Engineer Dispatch:
Certified engineers will travel to your facility to supervise equipment assembly, alignment, and integration with existing utilities (power, steam, compressed air).
Duur: 2–3 weeks (varies by line complexity).
Key Tasks:
Equipment calibration (e.g., mixer speed, sterilization temperature).
Safety checks and compliance validation (e.g., electrical grounding, CIP/SIP cycles).
Hands-On Training:
Operators: Training on PLC control interfaces, recipe adjustments, and emergency protocols.
Maintenance Teams: Guidance on routine upkeep (e.g., conveyor belt cleaning, grinder blade replacement).
Documentatie:
Multilingual manuals (English, Spanish, Mandarin, etc.) and video tutorials for future reference.
Proefproducties:
Engineers oversee initial batches to troubleshoot and optimize parameters (e.g., moisture retention, cutting precision).
Remote Assistance:
IoT-enabled diagnostics for real-time troubleshooting.
24/7 technical hotline for urgent issues.
Preventive Maintenance Plans:
Annual on-site inspections (optional add-on).
Spare parts inventory recommendations.
Service Regions:
Supported in over 50 countries via Darin®’s network of regional partners.
Visa and logistics coordination for engineer deployments.
Cost Structure:
Standard Package: Installation and basic training included in equipment pricing.
Premium Package: Extended support (e.g., 6-month remote monitoring) available at additional cost.
A pet food manufacturer in São Paulo required:
Integration of the DR-SL20 line into a retrofitted factory space.
Portuguese-language training for operators.
Oplossing:
Darin® engineers redesigned conveyor layouts to fit the facility’s constraints.
Conducted bilingual training sessions and left localized operation manuals.
Post-installation remote support resolved humidity-related packaging issues within 48 hours.
Training Programs for Operating and Maintaining the Darin® Moist Treats Processing Line
Darin® Machinery provides comprehensive, hands-on training programs tailored to ensure seamless operation and longevity of your Moist Treats Processing Line. Our training covers both theoretical knowledge and practical skills, empowering your team to maximize productivity, safety, and compliance. Below are the key components of our training offerings:
Target Audience: Production line operators, quality control staff.
Key Topics:
System Overview:
Introduction to line components (e.g., vacuum former, autoclave, PLC control cabinet).
Understanding workflow stages (mixing, forming, sterilization, packaging).
Daily Operations:
Startup/shutdown procedures and safety interlocks.
Adjusting parameters (e.g., mixing speed, cooking temperature, cutting precision).
Loading raw materials and troubleshooting jams or blockages.
Recipe Management:
Programing and switching between formulations (e.g., grain-free vs. high-protein).
Calibrating moisture levels for different textures (soft, chewy, or jelly-based).
Kwaliteitsborging:
Monitoring IoT dashboards for real-time data (humidity, microbial counts).
Conducting in-line checks (weight consistency, packaging integrity).
Training Format:
On-site demonstrations by Darin® engineers.
Simulated production runs with feedback.
Multilingual operation manuals and quick-reference guides.
Target Audience: Maintenance technicians, engineers.
Key Topics:
Preventief onderhoud:
Daily/Weekly tasks: Cleaning CIP/SIP systems, lubricating conveyors, inspecting belts.
Monthly checks: Replacing grinder blades, calibrating sensors, testing sterilization cycles.
Troubleshooting Common Issues:
Resolving conveyor misalignment, vacuum leaks, or PLC errors.
Diagnosing temperature fluctuations in steam cookers or autoclaves.
Spare Parts Management:
Identifying critical spare parts (e.g., sealing jaws, cutter blades).
Safe replacement procedures to minimize downtime.
Veiligheidsprotocollen:
Lockout-tagout (LOTO) procedures during repairs.
Handling food-grade lubricants and sanitizers.
Training Format:
Hands-on workshops with equipment disassembly/reassembly.
Video tutorials for complex procedures (e.g., autoclave maintenance).
Customized maintenance schedules based on usage intensity.
Target Audience: Senior engineers, production managers.
Key Topics:
Deep Dive into Automation:
PLC programming basics (modifying logic for custom workflows).
Integrating IoT data with factory ERP/MES systems.
Energy Optimization:
Adjusting steam and power usage to reduce costs.
Interpreting energy consumption reports from smart meters.
Nalevingscontroles:
Preparing documentation for AAFCO, FDA, or EU inspections.
Validating sterilization efficacy logs and sanitation records.
Training Format:
Remote sessions with Darin® automation experts.
Case studies on optimizing high-volume production (e.g., DR-SL20 models).
Target Audience: All staff interacting with the line.
Key Topics:
Normen voor voedselveiligheid:
HACCP principles for critical control points (e.g., sterilization, packaging).
Allergen management and cross-contamination prevention.
Emergency Protocols:
Responding to equipment malfunctions (e.g., overheating, pressure leaks).
Fire safety and evacuation procedures near heat-generating units.
Certificering:
Participants receive a Darin®-approved certificate upon passing written/practical exams.
Remote Assistance:
24/7 access to Darin®’s technical hotline for urgent queries.
IoT-enabled remote diagnostics for real-time troubleshooting.
Refresher Courses:
Annual on-site updates for new features or regulatory changes.
Access to an online portal with training videos, FAQs, and software updates.
Customized Learning Paths: Tailored to your team’s expertise and production goals.
Multilingual Support: Materials and trainers available in English, Mandarin, Spanish, and more.
Certified Expertise: Trainers with 10+ years of industry experience.
Neem contact met ons op to design a training plan that ensures your team masters the Moist Treats Processing Line with confidence! 🎓
De acceptance testing criteria and procedures for the Verwerkingslijn voor vochtige lekkernijen ensure the equipment meets contractual specifications, safety standards, and operational efficiency. Below are the details:
Performance Standards
Capaciteit: Verify production output matches the agreed capacity (e.g., XX kg/hour).
Energie-efficiëntie: Confirm energy consumption aligns with technical specifications.
Stability: Run continuous operation for 24-48 hours to check for downtime or malfunctions.
Quality Compliance
Product Quality: Ensure processed treats meet parameters (e.g., moisture content, texture, sterilization).
Hygiene & Safety: Validate compliance with GMP en FDA hygiene standards (e.g., no cross-contamination).
Safety & Certification
CE Compliance (if applicable): Check safety interlocks, emergency stops, and electrical/mechanical safety.
Documentation: Review CE/FDA/GMP certificates, technical manuals, and risk assessments.
Automation & Controls
Test PLC systems, sensors, and IoT integration for accuracy and reliability.
Step 1: Pre-Testing Preparation
Confirm installation completion and calibration of all components.
Review equipment documentation (e.g., manuals, compliance certificates).
Step 2: Functional Testing
Run the line with raw materials to test:
Ingredient feeding, mixing, cooking/cooling, and packaging functions.
Automated controls and emergency shutdown systems.
Step 3: Performance Validation
Measure actual output against guaranteed capacity.
Record energy/water consumption and compare to specifications.
Step 4: Quality Sampling
Collect product samples for lab testing (e.g., microbial analysis, moisture content).
Step 5: Safety Checks
Verify safety guards, alarms, and compliance with CE Machinery Directive (e.g., EN ISO 12100).
Step 6: Final Review
Sign an Acceptance Certificate upon successful testing.
Address any deviations with corrective actions or penalties (per contract terms).
Provide a detailed test report and troubleshooting guidelines.
Offer operator training refreshers if needed.
For customized requirements (e.g., third-party audits), discuss specifics during contract finalization.
Ja, Darin® Machines provides critical spare parts for the Verwerkingslijn voor vochtige lekkernijen during commissioning to ensure smooth operation and minimize downtime.
Included Spare Parts
Common Wear Items: Seals, gaskets, filters, and belts.
High-Risk Components: Sensors, nozzles, or heating elements prone to early failure.
Scope of Support
Spare parts are provided free of charge if failures occur due to manufacturing defects or installation errors.
Consumables (e.g., lubricants) may require separate purchase.
Process for Replacement
On-site technicians will diagnose issues and replace parts immediately during commissioning.
A spare parts list is provided upfront for transparency.
Post-acceptance, spare parts can be ordered via Darin®’s global logistics network (lead time: 5-15 business days).
Recommend purchasing a preventive maintenance kit for long-term reliability.
For specific part availability or extended warranties, discuss during contract finalization.
The responsibility for logistics and insurance of the Verwerkingslijn voor vochtige lekkernijen depends on the agreed trade terms (e.g., EXW, FOB, CIF). Here’s the standard breakdown:
Supplier Responsibility (If CIF/DAP Terms)
Logistiek: Darin® Machinery arranges transportation to the designated port or site.
Insurance: Full coverage for the Moist Treats Processing Line during transit (e.g., All Risks or Institute Cargo Clauses A).
Buyer Responsibility (If EXW/FOB Terms)
Logistiek: Buyer manages shipping and customs clearance.
Insurance: Buyer secures insurance for the equipment during transit.
Hybrid Agreements
For turnkey projects, Darin® may handle door-to-door logistics and insurance as part of the contract.
Key Steps:
Confirm trade terms in the contract (e.g., INCOTERMS® 2020).
Review insurance certificates and delivery timelines before shipment.
For specific arrangements, clarify requirements during contract negotiation.
Additional costs for modifications to the Moist Treats Processing Line requested before delivery are managed through a structured process to ensure transparency and mutual agreement. Here’s how Darin® Machinery handles such changes:
Formal Submission
The buyer submits a written change order detailing the modification requirements (e.g., design adjustments, added features).
Technical & Cost Evaluation
Darin® evaluates feasibility, impacts on production timelines, and calculates costs (e.g., materials, labor, redesign).
Approval & Agreement
A revised quote and updated delivery schedule are provided. Work proceeds only after the buyer approves the changes in writing.
Buyer Responsibility
Covers all costs from modifications initiated by the buyer (e.g., upgraded components, custom layouts).
Supplier Responsibility
No charges if modifications are due to Darin®’s errors (e.g., design flaws, non-compliance with specifications).
Upfront Deposit
Typically additional cost is required before modification work begins.
Final Payment
Remaining balance is paid upon completion of modifications, before shipment.
Modifications may extend the original lead time. A revised schedule is shared with the buyer for approval.
Change Order Clause
Original contracts include terms for handling modifications, ensuring legal clarity on cost and liability.
Documentatie
All changes are recorded in a supplementary agreement signed by both parties.
Recommendation:
Discuss potential modifications early in the project to minimize delays and costs. For urgent requests, expedited services may be available at a premium.
Ja, Darin® Machines provides complete technical documentation for the Verwerkingslijn voor vochtige lekkernijen upon delivery. The documentation includes:
Operation Manuals
Step-by-step guides for setup, operation, safety protocols, and troubleshooting.
Maintenance Manuals
Scheduled maintenance procedures, lubrication charts, and component lifespan details.
Electrical & Pneumatic Diagrams
Circuit diagrams, PLC wiring schematics, and pneumatic system layouts.
Spare Parts Catalog
List of replaceable parts with codes, specifications, and ordering instructions.
CE Declaration of Conformity (if applicable), FDA/GMP compliance reports, and risk assessment documents.
Digital Formats
PDF or cloud-based access for easy reference and updates.
Language Options
Documentation available in English, Chinese, or other requested languages.
Revision Updates
Free updates for critical system upgrades or safety revisions.
For tailored configurations, customized diagrams and operational guidelines are included.
Opmerking:
Documentation is reviewed during commissioning to ensure alignment with the installed system.
Contact our support team for urgent requests or missing files.
Darin® Moist Treats Processing Line Warranty Terms and Coverage
Darin® Machinery provides comprehensive and transparent warranty services for all Moist Treats Processing Lines to ensure investment security and long-term operational stability. Below are the detailed warranty policies:
Full System Warranty: 12 maanden (calculated from the date of equipment acceptance and signed delivery documentation).
Extended Coverage for Critical Components:
PLC control systems, servo motors, and sterilization equipment (autoclaves): Additional 6 months (total 18 months).
The following components are eligible for free repair or replacement if failures result from material defects or manufacturing issues during the warranty period:
Component Category | Covered Components Examples |
---|---|
Core Mechanical Parts | Vacuum former, meat grinder, mixer, conveyor drive motors, steam cooker heat exchangers |
Besturingssystemen | PLC control cabinet, touchscreen HMI, IoT sensors, electrical junction boxes |
Sterilization & Packaging | Autoclave (⑫), gas-flush packaging machine (⑪), vacuum sealing modules |
Structural Components | Food-grade stainless steel frames, protective covers, fastening bolts |
The following scenarios require customer responsibility for repair or replacement costs:
Normal Wear and Tear:
Meat grinder blades, cutter blades, sealing strips, conveyor belts.
Human Error:
Damage caused by improper operation (e.g., overloading, using corrosive cleaning agents).
External Factors:
Natural disasters, unstable voltage, unauthorized third-party modifications.
Free Support:
Fault diagnosis and remote technical guidance.
Logistics and labor costs for replacing defective parts during the warranty period (covered by Darin®).
Reactietijd:
Within 48 hours for critical failures (e.g., PLC system shutdown).
5–10 business days for spare parts delivery (subject to inventory availability).
Customers may purchase extended coverage:
Extended Warranty Plan:
Full system coverage up to 24 months: Pay 4–6% of the equipment’s total cost (varies by model).
Comprehensive Coverage Package:
Includes periodic replacement of consumables (e.g., blades, seals) and priority engineer dispatch.
Why Choose Darin® Warranty Services?
✅ Global Support Network: Certified engineers.
✅ Transparent Terms: No hidden clauses, clearly defined responsibilities.
✅ Rapid Response: Priority handling for critical failures to minimize downtime.
Neem contact met ons op for full warranty terms or upgrade plans! 🔧
Darin®’s warranty policy underscores our commitment to being your long-term trusted partner, ensuring seamless production and business growth.
Ja, Darin® Machines offers 24/7 remote technical support for the Verwerkingslijn voor vochtige lekkernijen to address urgent breakdowns or operational issues. Here’s how it works:
24/7 Availability:
Immediate assistance via phone, email, or dedicated online platforms, regardless of time zone.
Languages:
Support provided in English, Chinese, and other major languages.
IoT-Enabled Systems:
For lines equipped with IoT sensors, engineers can perform real-time diagnostics to identify issues (e.g., motor failures, temperature deviations).
Guided Troubleshooting:
Step-by-step instructions to resolve minor issues without on-site visits.
If remote resolution is impossible, Darin® dispatches local technicians within 24-72 hours (depending on location).
Free remote support during the standard warranty period (typically 12-24 months).
Extended Support Contracts:
Annual plans for priority access to 24/7 support and discounted on-site services.
Opmerking:
Ensure the line’s control system has internet connectivity for remote access.
For critical production environments, recommend pairing with a preventive maintenance plan to minimize downtime.
Ja, Darin® Machines offers preventive maintenance contracts tailored for the Verwerkingslijn voor vochtige lekkernijen to maximize uptime, extend equipment lifespan, and reduce unexpected breakdowns. Below are the key details:
Basic Plan
Included Services:
Annual/bi-annual inspections.
Lubrication, calibration, and wear-part replacements (e.g., seals, belts).
Remote diagnostics and priority technical support.
Advanced Plan
Included Services:
Quarterly on-site visits by certified technicians.
Full system performance audits.
Free emergency spare parts (up to a value limit).
Software/firmware updates.
Fixed Annual Fee:
Based on equipment complexity, usage intensity, and service tier (Basic/Advanced).
Pay-Per-Visit:
Flexible billing for facilities with seasonal production cycles.
Reduced Downtime:
Scheduled maintenance minimizes unplanned stoppages.
Cost Savings:
Discounts on spare parts (10-20%) and labor rates for contract holders.
Extended Warranty:
Optional extension of warranty coverage when signing multi-year contracts.
Assessment Phase:
Darin® conducts a free initial inspection to tailor the contract to your line’s needs.
Flexible Terms:
Contracts can be adjusted annually based on performance feedback.
Local technicians are available in major regions for rapid on-site response.
Opmerking:
Contracts include detailed service reports and actionable recommendations post-inspection.
Ja, Darin® Machines maintains a global spare parts inventory for the Verwerkingslijn voor vochtige lekkernijen to ensure rapid availability. Here are the details:
Common Parts:
High-wear components (e.g., seals, belts, sensors) and standard mechanical/electrical parts are stocked in regional warehouses (e.g., EU, North America, Asia).
Customized Parts:
Specialized components (e.g., custom-sized molds, proprietary heating elements) may require production lead time but are prioritized for existing clients.
Standard Parts:
5-15 business days after order confirmation, depending on location.
Expedited Shipping:
Emergency orders can be shipped via air freight in 3-7 business days (additional costs apply).
Custom Parts:
Lead time ranges from 4-8 weeks (manufactured upon request).
Online Portal:
Clients can check real-time inventory and place orders through Darin®’s dedicated spare parts portal.
Preventive Maintenance Kits:
Pre-packaged kits for annual maintenance reduce downtime and ensure parts availability.
Technical Assistance:
Contact our team for help identifying part numbers or compatibility.
Local Agents:
Regional service centers provide on-site support and spare parts delivery in critical cases.
Opmerking:
For urgent needs, notify our team immediately to activate priority logistics.
Yes! The Darin® Moist Treats Processing Line is designed with future-proof modularity, allowing seamless integration of new technologies to keep your production ahead of industry trends. Here’s how we ensure your line evolves with innovation:
Plug-and-Play Compatibility:
Critical components (e.g., PLC control systems, conveyors, sterilization units) are standardized for easy replacement or expansion.
Open interfaces support third-party IoT sensors, AI-driven quality control systems, or energy-efficient modules.
Scalable Design:
Add new modules (e.g., freeze-drying, 3D shaping, or CBD infusion) without disrupting existing workflows.
Technology Type | Examples of Upgradable Modules | Voordelen |
---|---|---|
Automation & AI | AI vision inspection systems, robotic sorting arms, predictive maintenance sensors. | Reduced waste, enhanced precision. |
Energie-efficiëntie | Heat recovery systems, solar-powered compressors, low-energy sterilization units. | Lower carbon footprint, cost savings. |
Hygiëne en veiligheid | UV-C pathogen disinfection tunnels, allergen-detection scanners, real-time microbial monitors. | Compliance with stricter regulations. |
Productinnovatie | Multi-layer extrusion heads, collagen-coating sprayers, or plant-based protein injectors. | Expand into new markets (e.g., vegan). |
Needs Assessment:
Darin® engineers evaluate your goals (e.g., higher speed, new product formats) and propose compatible upgrades.
Technical Integration:
Retrofitting is done during planned downtime to minimize disruption.
Existing PLC/IoT systems are reprogrammed for seamless control.
Testing & Training:
Factory Acceptance Testing (FAT) ensures upgraded modules meet specifications.
Staff receive targeted training for new workflows.
A U.S. client upgraded their DR-SL20 line with:
AI-kwaliteitscontrole: Added cameras to detect undercooked batches, reducing waste by 12%.
Heat Recovery Module: Reused steam energy, cutting energy costs by 18%.
Result: Achieved USDA Organic certification and expanded into premium markets.
Guaranteed Compatibility: Upgrades align with original design standards (no "legacy system" issues).
Kostenefficiëntie: Reuse existing infrastructure (e.g., power, steam lines) to minimize investment.
Global Support: Access Darin®’s R&D team for cutting-edge solutions tailored to pet food trends.
Future-Ready, Always Ahead
Whether adopting AI, sustainable tech, or novel product formats, Darin® ensures your Moist Treats line stays competitive. Neem contact met ons op to explore upgrade paths and future-proof your production today! 🚀
To report quality issues with the Verwerkingslijn voor vochtige lekkernijen and initiate resolution, follow the structured process below. Darin® Machinery prioritizes swift and transparent problem-solving to minimize operational disruptions.
24/7 Hotline: Call the dedicated support number provided in your documentation.
Online Portal: Submit a ticket via Darin®’s customer service platform (include photos/videos of the issue).
Email: Send details to E-mail with the subject line “Quality Issue – [Your Order Number]”.
Local Agent: Contact your regional service representative for on-site assistance.
Equipment model and serial number.
Detailed description of the issue (e.g., abnormal noise, production defects).
Timestamped logs or error codes from the control system.
Photos/videos demonstrating the problem.
Remote Diagnosis: Darin® engineers analyze submitted data to identify root causes (e.g., mechanical failure, software glitch).
On-Site Inspection (if needed): A technician is dispatched within 24-72 hours for critical cases.
Minor Issues:
Remote guidance for adjustments or part replacements (e.g., recalibrating sensors).
Express shipment of spare parts (if required).
Major Issues:
On-site repairs or component replacements by certified technicians.
If irreparable, negotiate replacements or refunds per warranty terms.
Warranty Coverage:
Free repairs/replacements for defects covered under warranty.
Reimbursement for downtime costs if stipulated in the contract.
Post-Warranty:
Solutions provided at discounted labor rates (if under a maintenance contract).
Root cause analysis report shared with the client.
Updated maintenance recommendations or design upgrades to prevent recurrence.
Acknowledgment: Within 2 hours of report submission.
Temporary Fix: Within 24 hours (for urgent issues).
Full Resolution: 3-10 business days, depending on part availability and complexity.
A Quality Issue Resolution Report is provided post-resolution, including:
Problem description and root cause.
Actions taken and replaced components.
Preventive recommendations.
Ja, Darin® Machines offers periodic performance audits for the Verwerkingslijn voor vochtige lekkernijen to ensure optimal operation, compliance, and long-term efficiency. Here’s how the audit process works:
Equipment Health Check:
Evaluate mechanical, electrical, and automation systems (e.g., motor efficiency, sensor accuracy, PLC performance).
Assess wear and tear on critical components (e.g., seals, belts, heating elements).
Process Optimization:
Analyze production output, energy/water consumption, and waste levels against benchmarks.
Identify bottlenecks or inefficiencies in the workflow.
Compliance Verification:
Confirm adherence to GMP, FDA, or CE standards (e.g., hygiene protocols, safety interlocks).
Standard Plans:
Annual Audit: Recommended for standard operations.
Semi-Annual Audit: Advised for high-intensity production environments.
Custom Schedules:
Tailored to match seasonal production cycles or specific regulatory requirements.
Review historical performance data and maintenance records.
Define audit goals (e.g., energy reduction, capacity improvement).
Darin® engineers conduct:
Functional Testing: Run the line under normal and peak loads.
Data Collection: Measure parameters (e.g., temperature stability, cycle times).
Safety Checks: Validate emergency stops and hazard controls.
Provide a Detailed Audit Report including:
Performance gaps and root causes.
Actionable recommendations (e.g., part replacements, software upgrades).
Cost-benefit analysis for proposed improvements.
Assist with executing upgrades or retrofits (optional).
Re-audit post-adjustments to verify results.
Preventive Maintenance Alignment:
Integrate audit findings with your maintenance schedule to avoid unplanned downtime.
Cost Savings:
Optimize energy/water usage and reduce material waste.
Compliance Assurance:
Mitigate risks of regulatory non-compliance or recalls.
Standalone Audit:
Fixed fee based on line complexity and audit depth.
Maintenance Contract Bundles:
Discounted audits when combined with annual preventive maintenance plans.
Explore trends, tips, and innovations in Braid Dog Chews Processing Line. Enhance efficiency and quality with expert insights.
Zelf droog hondenvoer maken is een lonende manier om ervoor te zorgen dat uw huisdier een uitgebalanceerde voeding krijgt
Zelf droog hondenvoer maken is een lonende manier om ervoor te zorgen dat uw huisdier een uitgebalanceerde voeding krijgt
Zelf droog hondenvoer maken is een lonende manier om ervoor te zorgen dat uw huisdier een uitgebalanceerde voeding krijgt
Zelf droog hondenvoer maken is een lonende manier om ervoor te zorgen dat uw huisdier een uitgebalanceerde voeding krijgt
Zelf droog hondenvoer maken is een lonende manier om ervoor te zorgen dat uw huisdier een uitgebalanceerde voeding krijgt
Zelf droog hondenvoer maken is een lonende manier om ervoor te zorgen dat uw huisdier een uitgebalanceerde voeding krijgt
laten we bespreken hoe we u kunnen helpen uw doelstellingen te bereiken en uw bedrijf te laten groeien!
Vertel ons zo specifiek mogelijk over uw behoeften.
Wij werken aan de beste oplossing & offerte op basis van uw vereisten.
Wij beginnen met de productie nadat wij uw goedkeuring en aanbetaling hebben ontvangen, en wij zorgen voor de verzending.
- Maak u geen zorgen, wij haten spam ook!
- Bel alleen als meerdere e-mails onbeantwoord blijven!