I remember my first time navigating the maze of food processing machinery, and boy, was it a journey!
Single-screw extruders are typically used for simpler processes requiring lower shear, whereas twin-screw extruders offer greater flexibility and control for complex recipes due to their dual screw configuration, which allows for better mixing, kneading, and cooking.
It's like choosing between two vehicles for a road trip. The single-screw is your reliable sedan—perfect for straightforward journeys. But if you're planning an adventurous route with twists and turns, the twin-screw is your all-terrain SUV, ready for anything! When I was choosing machinery, considering factors like cost and energy consumption was crucial. It felt like selecting just the right tool from a vast toolbox. Dive into the details with me as I share insights that might just make your decision a little clearer.
Single-screw extruders are more energy-efficient than twin-screw extruders.Vals
Twin-screw extruders often consume more energy due to their complexity.
Twin-screw extruders provide better mixing than single-screw extruders.Echt
The dual screw configuration enhances mixing, kneading, and cooking.
How Do Single-Screw Extruders Work?
Ever wondered how your pet's favorite treats get their shape and texture? It all starts with the fascinating world of single-screw extruders.
Single-screw extruders work by feeding material into a rotating screw housed in a barrel. The screw's rotation pushes the material forward, melting it through friction and heat, and then forcing it through a die to shape it.
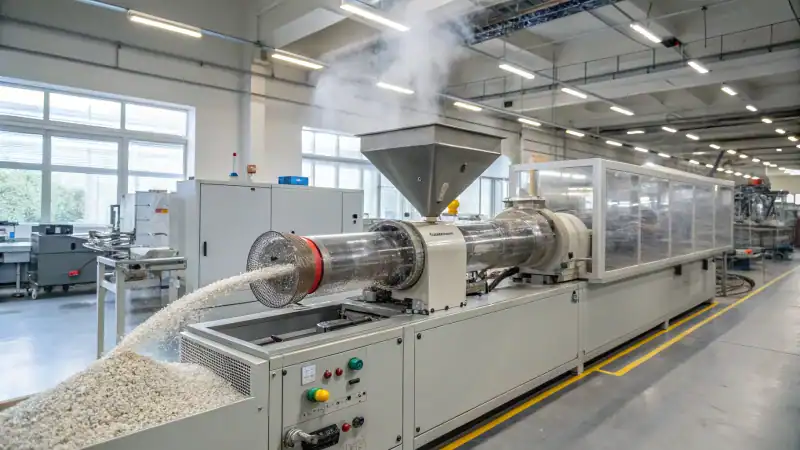
The Basics of Single-Screw Extrusion
Let me take you back to when I first stepped into the world of machinery. I was fascinated by these giant metal beasts that could turn raw, unappetizing materials into appetizing bites for our furry friends. At the heart of it all was the single-screw extruder, a straightforward yet ingenious device.
These machines operate by having a rotating screw inside a barrel. The principle is simple: as the screw turns, it nudges the material forward, generating enough heat through friction, assisted by external heaters, to melt it. I remember watching this process for the first time and being amazed at how effortlessly the extruder could transform and shape materials by pushing them through a die.
Components and Their Functions
Component | Functie |
---|---|
Hopper | Feeds raw material into the barrel |
Screw | Rotates to move and melt the material |
Barrel | Houses the screw and applies heat |
Heaters | Provide additional thermal energy to melt the material |
Die | Shapes the melted material as it exits the extruder |
The Extrusion Process
Watching the extrusion process unfold was like seeing magic happen. You start with raw ingredients in the hopper1, which are then gently coaxed along the barrel by the screw's rotation. It's here that the real transformation occurs—material heats up from friction and those trusty external heaters2, emerging as perfectly shaped treats.
Factors Affecting Extrusion
My journey taught me that several factors can impact the efficiency of an extruder:
- Screw design: Just like choosing the right tool for a task, the screw's geometry is crucial for optimal movement and melting.
- Temperature control: Keeping temperatures just right ensures quality every time.
- Material properties: Different materials, like unique pets, need specific settings to bring out their best.
For those eager to master these factors, diving into this expert discussion3 can provide invaluable insights.
Single-screw extruders use external heaters to melt material.Echt
External heaters provide additional thermal energy to melt the material.
The die in a single-screw extruder feeds raw material into the barrel.Vals
The hopper, not the die, feeds raw material into the barrel.
Why Choose Twin-Screw Extruders Over Single-Screw Models?
Remember the excitement of getting a new tool that makes everything easier? That's what twin-screw extruders feel like for manufacturers.
Twin-screw extruders excel in versatility, efficiency, and precise control over product quality. These machines enable thorough mixing, consistent output, and adaptability across various materials and applications, essential for modern manufacturing needs.
Enhanced Mixing Capabilities
I remember the first time I watched a twin-screw extruder in action. It was like magic—ingredients blending seamlessly without a hitch. This is thanks to their enhanced mixing capabilities4. Industries like pet food manufacturing, where consistency is key, benefit greatly from this feature. The intermeshing screws ensure even distribution of ingredients, cutting down on segregation and making sure each batch is just right. Imagine baking a cake where every slice is perfect; that's the kind of reliability twin-screw extruders bring.
Greater Processing Flexibility
Then there's the flexibility. Have you ever tried switching recipes on a whim? It's a breeze with these machines. Twin-screw extruders handle anything from powders to liquids, adapting effortlessly to diverse production needs. This adaptability is crucial in the pet food industry, where different products require unique processing conditions. The ability to switch without downtime means manufacturers can keep up with demand without missing a beat.
Functie | Voordeel |
---|---|
Efficient Mixing | Ensures uniform product quality |
Veelzijdigheid | Adapts to various materials and recipes |
Schaalbaarheid | Supports both small and large-scale production |
Precise Control Over Product Quality
When I talk about control, I mean having the power to tweak every little detail to perfection. Twin-screw extruders offer precise control over temperature, pressure, and shear force during processing. For companies producing premium or specialty pet foods, this control is non-negotiable. Maintaining texture and nutritional value across batches isn't just important; it's imperative. Some advanced models even let you adjust parameters on the fly through integrated control systems5.
Increased Efficiency and Output
Efficiency is where these machines really shine. I once saw a production line transform overnight with the addition of a twin-screw extruder. By combining multiple functions—mixing, cooking, shaping—into one step, they cut down on equipment needs and labor costs. This streamlining speeds up production while keeping costs down, making it perfect for scaling operations quickly without sacrificing quality. If you're curious about how industrial efficiencies can be further optimized, diving into industrial efficiencies6 might be enlightening.
Twin-screw extruders improve ingredient distribution.Echt
Their intermeshing screws allow for better mixing, reducing segregation.
Twin-screw extruders are limited to small-scale production.Vals
They support both small and large-scale production due to scalability.
Which Extruder Type Offers Better Energy Efficiency?
Choosing the right extruder can feel like solving a puzzle, especially when energy efficiency is at stake. Join me as I unravel which type saves more energy in our manufacturing journeys.
Twin screw extruders generally offer better energy efficiency than single screw extruders. They provide more control over the process, reduce energy consumption, and enhance product quality, making them a preferable choice for many industries.
Types extruders begrijpen
Extruders are vital in various industries, from food processing to plastics. The most common types are single screw and twin screw extruders. Each has its own advantages and disadvantages7, impacting their energy efficiency.
When I first dove into the world of extrusion, I was amazed at how pivotal these machines are across various industries—from whipping up pet treats to molding durable plastic products. The two main contenders in this arena are single screw and twin screw extruders. Each brings its unique set of perks and quirks that influence their energy efficiency.
Single Screw vs. Twin Screw: A Comparison
Functie | Extruder met één schroef | Tweelingschroefextruder |
---|---|---|
Energie-efficiëntie | Matig | Hoog |
Procesbeheersing | Basis | Advanced |
Material Handling | Beperkt | Versatile |
I remember the first time I encountered a single screw extruder. Its simplicity was impressive and cost-effective for sure, but I soon realized it gulped down more energy than I liked. The lack of fine-tuned control often meant more waste—a frustrating fact when you're trying to keep an eye on both the budget and the environment.
Then came the twin screw extruder, a game-changer in my books. Offering greater control over material processing8, it not only slashed energy consumption but also elevated product quality. This fine balance meant less waste and more efficient use of resources.
Factors Influencing Energy Efficiency
Through trial and error, I’ve discovered several factors that play into the energy efficiency of extruders:
- Screw Design: The design geometry can make or break how effectively materials are processed, directly impacting energy use.
- Temperatuurregeling: Keeping temperatures in check is crucial—an area where many machines can fall short, leading to excessive energy use.
- Material Properties: The type of material being processed dictates how much energy is needed.
For me, twin screw extruders excelled in these areas by providing better control and adaptability. This flexibility allows manufacturers to tailor the extrusion process, improving overall efficiency9.
Real-World Applications
Let me paint you a picture: In industries like pet food processing, where every cent counts, opting for a twin screw extruder has been a smart move for many. With their advanced mixing capabilities and energy-saving features, these machines not only cut costs but also leave a smaller carbon footprint. It's not just about saving money—it's about making a difference.
Manufacturers focusing on sustainability and efficiency might find twin screw extruders an ideal choice for reducing energy consumption10 while maintaining top-notch product consistency. Their ability to handle diverse materials makes them suitable for evolving market demands in the pet food sector and beyond.
Twin screw extruders offer superior energy efficiency.Echt
Twin screw extruders provide advanced process control, reducing energy use.
Single screw extruders have better material handling capabilities.Vals
Single screw extruders are limited in material handling compared to twin screws.
How Do Extruder Types Impact Product Quality?
Have you ever wondered how the type of extruder you choose can make or break your product quality?
Extruder types significantly impact product quality by determining texture, shape, and nutritional retention. Different designs and settings allow manufacturers to optimize these factors for specific product needs.
Types of Extruders and Their Functions
Choosing the right extruder is like picking the perfect tool for a craft project—it makes all the difference! I remember when I first delved into the world of extrusion. Single-screw extruders seemed like trusty old friends: reliable for simple tasks but not the best fit for complex recipes. In contrast, twin-screw extruders were like those multitasking gadgets everyone raves about; they offer flexibility and control, ideal for producing a wide range of textures. Then there are planetary roller extruders, which are like having a master chef in your kitchen—they offer precise control, especially for textures that need to be just right.
- Extruders met één schroef: Great for straightforward jobs, providing uniform products but limited in complexity.
- Extruders met twee schroeven: Offer versatility and better mixing for intricate recipes.
- Planetary Roller Extruders: Provide exact control, perfect for specialized textures or nutritional needs.
Effect on Product Texture and Shape
I’ve learned firsthand that the magic of extrusion lies in its ability to transform ingredients into textures and shapes that please both pets and their owners. By adjusting shear and temperature11, each extruder type plays a unique role in the end product. For instance, twin-screw extruders can mimic a magician’s wand, creating various textures just by tweaking screw speed and configuration.
Type extruder | Texture Control |
---|---|
Enkele schroef | Beperkt |
Dubbele schroef | Hoog |
Planetary Roller | Zeer hoog |
Voedingsretentie
When it comes to pet food, nutrition isn't just important—it’s everything. I’ve seen how different extruder designs can affect nutrient retention, sometimes making or breaking a product’s success in the market. Twin-screw extruders are like precision instruments, fine-tuning the heat to avoid nutrient loss while ensuring proper gelatinization. Planetary roller extruders excel at keeping moisture intact, which is crucial for semi-moist products.
- Heat Sensitivity: Twin-screw designs12 offer exact temperature control for heat-sensitive products.
- Moisture Retention: Planetary roller extruders keep moisture levels ideal, essential for certain treats.
Customization Opportunities
One of the exciting parts of working with extrusion technology is the endless customization possibilities. By changing die shapes and sizes, it's like having a blank canvas where you can create any product form imaginable. Twin-screw systems even let you add various ingredients, from supplements to flavor enhancers, truly tailoring products to specific needs.
Understanding how different extruder types influence product quality can seem overwhelming at first, but once you get the hang of it, it feels like unlocking a secret ingredient to success in pet food production. Explore more about extruder configurations13 to find the perfect fit for your production line.
Single-screw extruders offer high texture control.Vals
Single-screw extruders provide limited texture control, not high.
Planetary roller extruders maintain moisture levels well.Echt
They excel in maintaining moisture, crucial for semi-moist products.
What Factors Should Guide Your Extruder Choice?
Choosing the perfect extruder is like finding a trusted partner for your production line. It's all about knowing what truly matters to your business.
Key factors influencing extruder choice include material compatibility, production capacity, energy efficiency, operational costs, and technology integration. Evaluating these aspects helps optimize production and maintain high product standards.
Materiaal compatibiliteit
Let me tell you, getting the right extruder for your materials is crucial. I remember when I first started in the industry; I underestimated how different materials demanded different screw designs. It's not just about fitting the material into the machine but ensuring the machine handles it without a hitch. Consider whether the extruder can work with your planned materials without risking damage or sacrificing quality.
Productiecapaciteit
Back when I was new to this, I once chose an extruder that couldn't keep up with our production goals. It was a rookie mistake! You want to match the machine's throughput rate to your actual needs. If there's a mismatch, you'll either be underutilizing your machine or pushing it too hard, and neither is ideal for maintaining efficiency or extending the machine's life.
Energie-efficiëntie
Energy costs can sneak up on you, especially in large-scale operations. I've learned the hard way that choosing an energy-efficient extruder pays off in more ways than one. Look for machines with energy-saving features—these can really help cut down on costs and even lessen environmental impact.
Operational Costs
It's tempting to focus on the upfront price tag of an extruder, but believe me, long-term costs are where the real money goes. Maintenance, downtime, and parts replacement should be on your radar. I've found that comparing these costs across models helps ensure you're getting a good deal over the machine's lifespan.
Technology Integration
If you're like me and love seeing technology make life easier, then you'll appreciate modern extruders. Automated controls and real-time monitoring systems can turn a stressful operation into a smooth-running process. These tech features aren't just for show—they help maintain consistent quality and ease management tasks.
Factor | Consideration |
---|---|
Material | Compatibility with materials |
Capaciteit | Throughput rate |
Energie | Efficiency features |
Costs | Long-term operational costs |
Technologie | Integration capabilities |
Every factor here is a piece of the puzzle in finding the right extruder for your needs. By keeping these aspects in mind, you're well on your way to enhancing your production process. Explore more about extruder selection14 to make informed decisions tailored to your industry.
Energy-efficient extruders reduce operational costs.Echt
Energy-efficient designs lower electricity usage, saving money over time.
All extruders can handle any material without damage.Vals
Different materials need specific extruder designs to prevent damage.
Are There Cost Differences Between Single and Twin-Screw Extruders?
Ever faced the dilemma of choosing between single and twin-screw extruders? It's a decision that hinges on your budget and production goals.
Yes, there are significant cost differences between single and twin-screw extruders. Single-screw extruders are generally cheaper upfront but may have higher operational costs depending on the application and material being processed.
Initial Investment and Operational Costs
I remember when I first stood in front of the daunting choice between single and twin-screw extruders, feeling like I was about to buy my first car. The single-screw models, much like an entry-level sedan, were simpler and more budget-friendly to start with. Their straightforward design made them less costly to produce and therefore less expensive for folks like me to purchase.
But as I dug deeper, I realized that the initial price tag was just the tip of the iceberg. Twin-screw extruders, although they reminded me of a sleek sports car with all the bells and whistles, required a heftier upfront investment due to their complexity. Here's a quick comparison:
Functie | Single-Screw Extruder | Twin-Screw Extruder |
---|---|---|
Initiële kosten | Onder | Hoger |
Operationele efficiëntie | Matig | Hoog |
Veelzijdigheid | Beperkt | Uitgebreid |
Operationele efficiëntie
The decision wasn't just about how much I'd spend on day one. It was about how these machines would perform over time. Twin-screw extruders could handle a wider range of materials with precision, like a versatile chef who can whip up any dish with ease. They promised better control over process parameters, which meant potential savings in the long run, especially in high-stakes industries where precision is key.
Versatility in Applications
As someone deeply involved in food processing and plastic production, I found the versatility of twin-screw extruders particularly appealing. They could tackle complex formulations and variable feed rates, making them ideal for demanding applications in sectors like food processing15 en plastic production16.
Onderhoud en levensduur
Maintenance was another aspect where these machines diverged. Single-screw extruders were like a trusty old truck—fewer parts meant easier fixes but also faster wear if not handled properly. Meanwhile, twin-screw extruders were akin to those high-performance cars that needed a little more TLC but promised durability that could justify their upkeep costs.
In the end, it all boiled down to balancing my budget with performance needs. By weighing these factors, I could ensure that my choice would align with my production requirements and offer long-term cost efficiency. It's a bit like choosing between the reliable old sedan and the flashy new sports car—each has its own set of benefits depending on what you're looking for.
Single-screw extruders are less versatile than twin-screw extruders.Echt
Single-screw extruders have limited versatility compared to the extensive applications of twin-screw extruders.
Twin-screw extruders always have lower operational costs.Vals
While efficient, twin-screw extruders can incur higher operational costs depending on maintenance and material handling.
Conclusie
Single-screw extruders are simpler and cost-effective for basic processes, while twin-screw extruders offer advanced mixing, flexibility, and efficiency for complex applications in food processing.
-
Learn about the hopper's role in feeding materials into the extruder for efficient processing. ↩
-
Explore different types of heaters that enhance the melting process in extrusion. ↩
-
Gain tips on optimizing extruder performance to improve efficiency and product quality. ↩
-
Discover how twin-screw extruders achieve superior mixing for uniform product consistency. ↩
-
Understand the role of integrated control systems in maintaining product quality. ↩
-
Explore how twin-screw extruders enhance operational efficiency in manufacturing. ↩
-
Understanding the pros and cons aids in choosing the right extruder for specific needs. ↩
-
Explores how twin screw technology improves efficiency in material processing. ↩
-
Learn strategies to optimize energy use in extrusion processes. ↩
-
Highlights the importance of energy savings for cost reduction and environmental impact. ↩
-
Discover how shear and temperature influence texture during extrusion, providing insights into achieving desired product characteristics. ↩
-
Learn why twin-screw extruders are ideal for maintaining precise temperature control during processing. ↩
-
Gain knowledge on various extruder configurations to optimize your pet food production process. ↩
-
Find comprehensive guides that help navigate the complexities of selecting the right extruder for your production needs. ↩
-
Explore how twin-screw extruders optimize food processing with superior control and versatility. ↩
-
Learn about the advantages of twin-screw extruders in handling diverse plastic materials. ↩