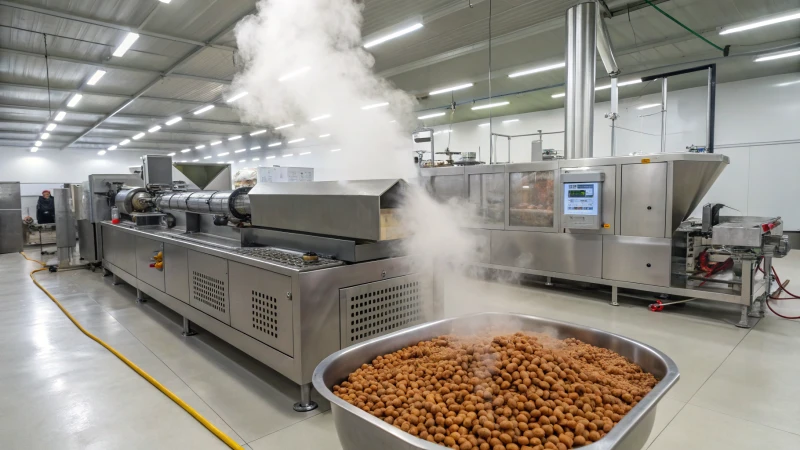
Pet owners demand high-quality, nutritious, and safe food for their beloved animals. However, achieving consistency, hygiene, and efficiency in pet food production is impossible without specialized machinery. Traditional manual production methods are inefficient, lack uniformity, and pose contamination risks. The solution? Pet food processing machines—advanced equipment designed to streamline production while maintaining optimal quality and safety.
A pet food processing machine is specialized equipment designed to automate and optimize the production of pet food. It includes processes such as mixing, extrusion, drying, cooling, and packaging, ensuring consistency, safety, and efficiency in manufacturing. These machines cater to dry kibble, wet food, and treats, meeting industry standards and pet dietary needs.
To fully understand how pet food processing machines work and how they can benefit your business, let’s explore their components, advantages, and selection criteria.
What Are Pet Food Processing Machines and Why Are They Important?
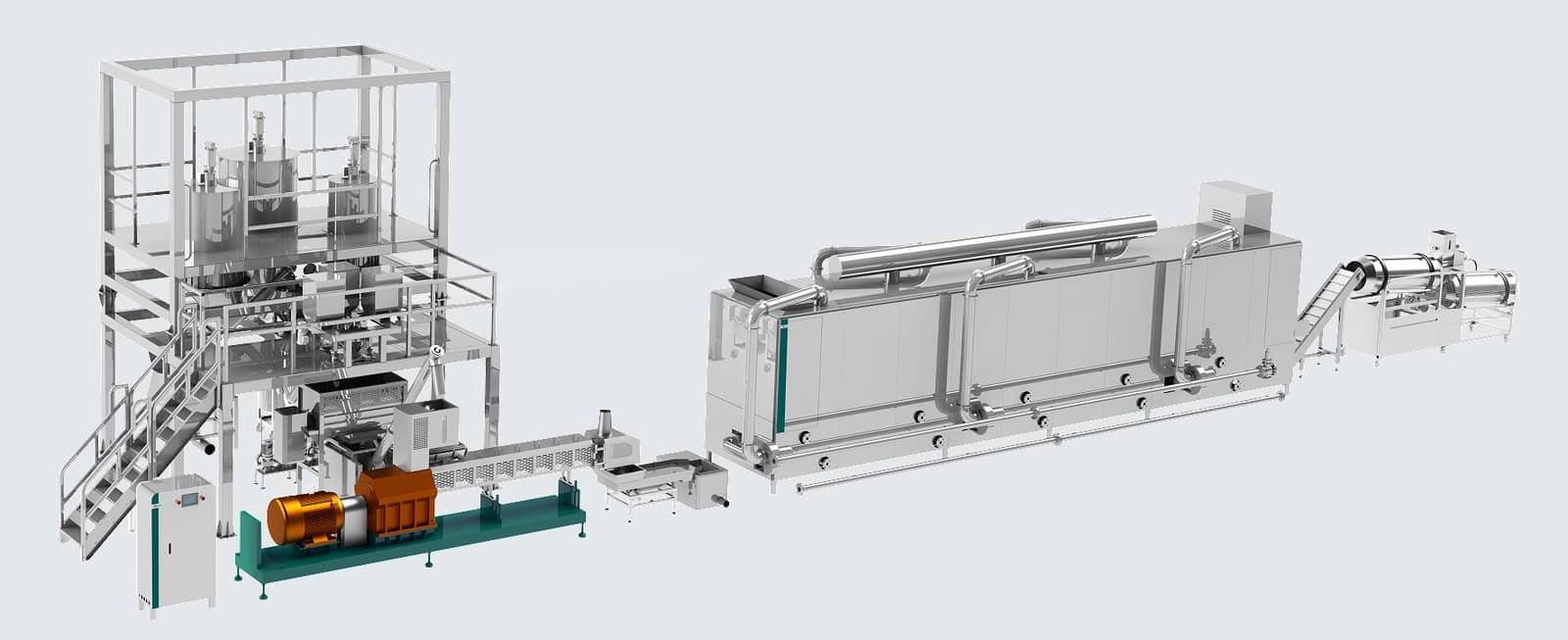
Pet owners want nutritious, safe, and tasty food for their furry friends. But creating pet food that meets these expectations — while also being cost-effective and scalable — requires advanced machinery. Pet food processing machines are the backbone of the industry, ensuring that every kibble, can, and treat is made with precision and care.
Pet food processing machines are specialized equipment designed to automate and optimize the production of pet food. They handle tasks like grinding, mixing, cooking, drying, coating, and packaging, ensuring products are consistent, nutritious, and safe for pets. These machines improve efficiency, enhance quality control, and help manufacturers meet strict regulatory standards.
Let’s break down what these machines do, why automation is crucial, and how they guarantee product quality and safety.
Pet food processing machines are essential for maintaining consistent product quality and safety.True
These machines control factors like temperature, pressure, and ingredient distribution, minimizing contamination risks and ensuring uniformity in every batch.
Definition and Functions of Pet Food Processing Machines
Pet food processing machines perform various functions to turn raw ingredients into finished products. Let’s explore the key stages:
- Ingredient Preparation: Grinders and mixers break down and blend raw materials like meat, vegetables, and grains.
- Extrusion & Cooking: Extruders cook the mixture at precise temperatures, shaping the food into forms like kibble or pellets.
- Drying & Cooling: Dryers remove excess moisture, while cooling systems prepare the food for coating.
- Coating & Flavoring: Coaters add essential nutrients, oils, and flavor enhancers to boost palatability.
- Packaging & Quality Control: Machines weigh, portion, and seal the food, with quality control systems checking for contaminants and defects.
Process Stage | Key Machines | 기능 |
---|---|---|
Ingredient Prep | Grinders, Mixers, Conveyors | Chop and blend raw materials |
Cooking & Shaping | Single/Twin-Screw Extruders | Cook under pressure, form shapes |
Drying & Cooling | Belt Dryers, Cooling Conveyors | Remove moisture, stabilize products |
Coating & Flavoring | Drum Coaters, Vacuum Coaters | Add nutrients, flavors, and enhancers |
패키징 | Weighing Systems, Bagging Machines | Portion, pack, and seal finished food |
The Role of Automation in Pet Food Manufacturing
Automation revolutionizes pet food production. Here’s how:
- Consistency & Precision: Automated systems control ingredient ratios, temperature, and cooking times, ensuring uniformity.
- Efficiency & Scalability: Machines operate continuously, drastically increasing output and lowering labor costs.
- Flexibility & Innovation: Automated lines adapt to changing recipes and product types, allowing rapid innovation.
- Data & Monitoring: Sensors collect real-time data, helping manufacturers fine-tune processes and detect issues early.
Automation in pet food manufacturing increases production efficiency and reduces human error.True
Automated systems streamline processes and maintain tight control over variables like temperature and mixing times, reducing the risk of mistakes.
How These Machines Ensure Product Quality and Safety
Safety and quality are paramount in pet food production. Processing machines are designed to minimize risks and preserve nutritional value:
- Sanitary Design: Machines use stainless steel and feature self-cleaning mechanisms to prevent bacterial contamination.
- Temperature & Pressure Control: Precise cooking conditions destroy pathogens while preserving nutrients.
- Quality Assurance Systems: Built-in sensors and X-ray detectors catch foreign materials or inconsistencies before packaging.
- Traceability & Documentation: Automated systems log data, helping manufacturers trace and resolve any issues.
Safety Measure | Machine Feature | 혜택 |
---|---|---|
Sanitation | Stainless steel surfaces, CIP systems | Reduces contamination risk |
Thermal Processing | Extruder temperature control | Kills harmful bacteria |
Contaminant Detection | Metal detectors, X-ray scanners | Identifies foreign objects |
Real-Time Monitoring | IoT-enabled sensors | Catches anomalies during production |
Batch Tracking & Logging | Automated data collection | Enables traceability and quick recalls |
The Power of Pet Food Processing Machines
Pet food processing machines are essential for creating the safe, nutritious, and high-quality products that pets deserve. They enhance efficiency, guarantee consistency, and safeguard food safety — all while giving manufacturers the flexibility to innovate and meet evolving consumer demands.
Investing in state-of-the-art processing equipment isn’t just about production volume; it’s about building trust with pet owners and delivering products that genuinely enhance pets' well-being.
Are you ready to elevate your pet food production line with advanced machinery? Contact us today — let’s shape the future of pet nutrition together! 🐾
What Are the Key Components of a Pet Food Processing Line?
Creating high-quality, nutritious pet food requires more than just the right ingredients — it demands a seamless production line equipped with specialized machinery. Each component plays a critical role in transforming raw materials into safe, consistent, and delicious products that pets love.
A pet food processing line consists of several key components: raw material handling systems, mixing and grinding units, extrusion and cooking technology, drying and cooling mechanisms, coating and flavoring processes, and packaging and sealing equipment. These elements work together to optimize efficiency, ensure product quality, and meet safety standards.
Let’s break down each component to understand how they contribute to the production process and why they are essential for successful pet food manufacturing.
A complete pet food processing line is essential for large-scale production, consistency, and safety.True
Each component in the production line performs a vital function, from ingredient preparation to final packaging, ensuring products meet quality and safety standards.
Raw Material Handling and Storage Systems
Proper handling and storage of raw ingredients lay the foundation for quality pet food.
- Key Machines: Silos, conveyors, hoppers, feeders
- Function: Store, transport, and deliver raw materials like meat, grains, and supplements to the processing line while maintaining freshness and preventing contamination.
Handling Equipment | 목적 | 혜택 |
---|---|---|
Silos | Store large quantities of grains | Preserve ingredient quality |
Conveyors | Transport materials to mixers | Reduce manual labor |
Feeders & Hoppers | Control ingredient flow | Ensure consistent batch sizes |
Mixing and Grinding Units
Blending and breaking down ingredients ensures even nutrient distribution and optimal texture.
- Key Machines: Grinders, paddle mixers, ribbon blenders
- Function: Grind raw materials to the desired size, mix ingredients uniformly, and prepare the blend for extrusion.
Mixing units ensure consistent nutrient distribution in pet food batches.True
Proper mixing prevents nutrient imbalances, ensuring pets receive the right vitamins and minerals in every bite.
Extrusion and Cooking Technology
Extrusion is the heart of pet food production, where raw ingredients are cooked, shaped, and sterilized.
- Key Machines: Single-screw extruders, twin-screw extruders
- Function: Cook the ingredient mixture under heat and pressure, shaping it into various forms like kibble or pellets, while destroying harmful bacteria.
Extruder Type | Best For | Main Advantage |
---|---|---|
단일 스크류 압출기 | Simple, uniform products | Cost-effective, easy to maintain |
트윈 스크류 압출기 | Complex, multi-ingredient recipes | Versatile, high-capacity |
Drying and Cooling Mechanisms
Proper drying and cooling extend shelf life and stabilize the final product.
- Key Machines: Belt dryers, rotary dryers, cooling conveyors
- Function: Reduce moisture content to prevent spoilage, then cool the product to prepare it for coating or packaging.
Drying and cooling are essential for extending pet food shelf life.True
Reducing moisture content prevents microbial growth, while cooling stabilizes the food for safe storage.
Coating and Flavoring Processes
This step enhances taste and nutritional value.
- Key Machines: Drum coaters, vacuum coaters
- Function: Apply essential oils, vitamins, minerals, and flavor enhancers to boost product palatability and nutritional content.
Coating Machine | 목적 | 혜택 |
---|---|---|
Drum Coater | Evenly coat food with liquids or powders | Improves taste and appearance |
Vacuum Coater | Infuse ingredients into food’s core | Enhances nutritional absorption |
Packaging and Sealing Equipment
The final step is packaging products for distribution, ensuring freshness and safety.
- Key Machines: Weighing systems, bagging machines, sealers, metal detectors
- Function: Portion, bag, seal, and inspect products for contaminants, preparing them for shipping and retail.
Automated packaging systems help prevent contamination and ensure precise portioning.True
Automated packaging reduces human handling, lowering contamination risks, while precise weighing ensures accurate portion sizes.
Final Thoughts: The Power of an Integrated Production Line
Every component of a pet food processing line plays an indispensable role in creating products that pets love and owners trust. From handling raw materials to packaging the final product, these machines work in harmony to deliver consistent, safe, and high-quality pet food at scale.
If you’re a manufacturer looking to optimize your production line or explore new product innovations, having the right machinery is your first step to success.
Ready to build a top-tier pet food processing line? Contact us today to explore cutting-edge solutions tailored to your production needs! 🐾
How Does a Pet Food Extruder Work?
Producing high-quality, nutritious pet food is both a science and an art. If the extrusion process is not optimized, pet food can lose essential nutrients, suffer from poor texture, and be unappealing to pets — leading to product rejection and financial losses. However, mastering extrusion technology can enhance product digestibility, improve palatability, and ensure consistent kibble shapes and sizes, meeting both pets' needs and pet owners' expectations.
A pet food extruder works by mixing, cooking, and shaping raw ingredients under high pressure and temperature, producing kibble with enhanced digestibility and palatability. Single-screw extruders offer simplicity and lower costs, while twin-screw extruders provide better versatility, mixing, and control over texture and ingredient combinations.
Understanding the core principles of extrusion, the impact of different screw configurations, and the vital role of temperature and pressure will empower manufacturers to optimize their processes and deliver superior products to the market.
Single-Screw vs. Twin-Screw Extruders
The heart of any extruder is the screw mechanism that pushes ingredients through the barrel to cook and shape them. Let’s break down the differences between single and twin-screw extruders:
기능 | 단일 스크류 압출기 | 트윈 스크류 압출기 |
---|---|---|
Design | One rotating screw within a barrel | Two intermeshing rotating screws in the same barrel |
Mixing Capability | 보통 | Excellent, more homogeneous ingredient distribution |
다용도성 | Limited to simpler recipes | Highly versatile, suitable for complex formulas |
Shear Control | Lower, less control over shear forces | Higher, more precise shear control |
Output Consistency | Can vary, especially with ingredient changes | Consistent output, even with varied raw materials |
Maintenance & Cost | Easier and cheaper to maintain | Higher initial investment and more complex upkeep |
Twin-screw extruders provide better control over pet food texture and nutrient retention.True The dual-screw design allows for precise manipulation of shear forces, temperature, and mixing, optimizing product quality.
How Extrusion Improves Digestibility and Palatability
Extrusion not only shapes the kibble but also fundamentally alters ingredient structure to enhance nutrient bioavailability and flavor. The high-pressure, high-temperature process breaks down complex starches, gelatinizing them to improve digestibility.
압출의 효과 | Result |
---|---|
Starch Gelatinization | Increases digestibility and nutrient absorption |
Protein Denaturation | Makes proteins more accessible for digestion |
Fat Integration | Disperses fats evenly, boosting palatability |
Maillard Reaction | Creates appealing roasted flavors for pets |
Pet food extrusion reduces nutrient content and damages proteins.False Properly controlled extrusion can enhance nutrient bioavailability and preserve protein integrity, contributing to more nutritious, digestible food.
The Role of Temperature and Pressure in Shaping Kibble
Temperature and pressure are the critical control parameters during extrusion. They dictate cooking efficiency, kibble expansion, and the final product’s texture.
매개변수 | Effect on Product |
---|---|
Temperature (90–160°C) | Affects starch gelatinization, protein denaturation, and bacterial safety |
Pressure (20–100 bar) | Determines kibble density, expansion, and crunchiness |
Moisture (20–30%) | Influences cooking efficiency and product texture |
Screw Speed (200–600 rpm) | Controls residence time and shear force intensity |
Optimizing these variables allows manufacturers to fine-tune product characteristics — from soft, chewy treats to crispy, airy kibble.
Understanding the intricacies of pet food extrusion empowers manufacturers to create high-quality, appealing products that meet pets' nutritional needs. Whether opting for a single-screw extruder for straightforward formulations or investing in a twin-screw extruder for complex, premium offerings, mastering the relationship between pressure, temperature, and ingredient interactions is key to success.
If you're ready to elevate your pet food production, invest in cutting-edge extrusion technology, or need tailored advice on optimizing your processes — reach out to us today. We specialize in helping manufacturers deliver market-leading pet food that pets crave and owners trust.
Let’s craft the future of pet nutrition together! 🐾
What Types of Pet Food Can Be Produced?
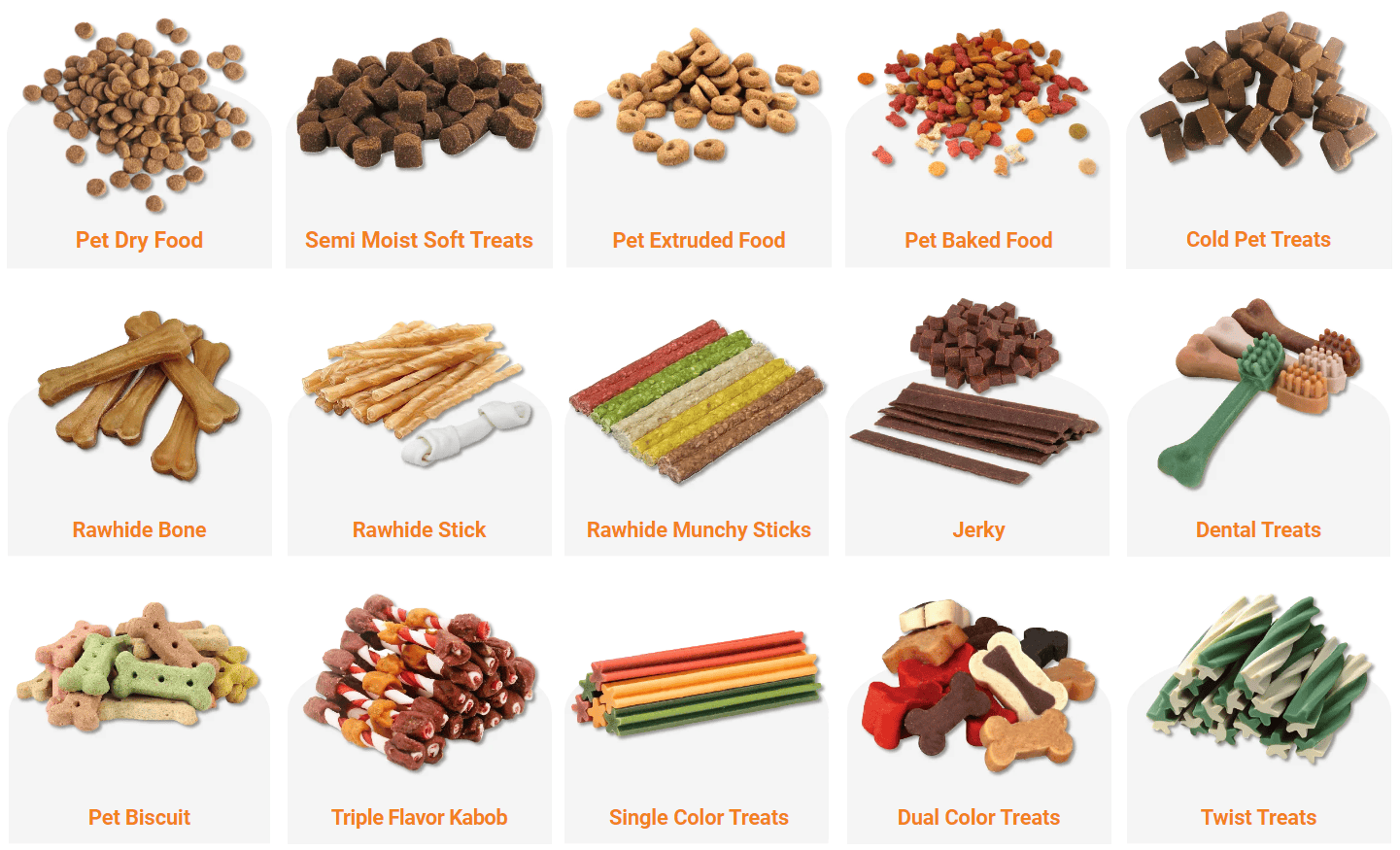
Choosing the right type of pet food is crucial for ensuring pets get the nutrition they need. Whether you're a pet owner, retailer, or manufacturer, understanding the different types of pet food available is key to making informed decisions. But with so many options, where do you start? Let’s dive in and explore the diverse world of pet food production.
There are four primary types of pet food that can be produced: dry pet food (kibble), wet pet food (canned and pouch), semi-moist pet food, and treats or specialty pet products. Each type has unique characteristics, benefits, and production requirements, catering to various pet dietary needs and consumer preferences.
Curious about what makes each type special and how they are produced? Let’s break it all down so you can choose or create the perfect food for your furry friends.
Dry Pet Food (Kibble)
Dry pet food is one of the most popular options due to its convenience, long shelf life, and affordability. It’s typically made by combining ingredients like meat, grains, and vegetables into a dough, which is then cooked and extruded into small, bite-sized pieces.
혜택 | Challenges |
---|---|
Easy to store and measure | Can be less palatable for some pets |
Promotes dental health | Lower moisture content |
Cost-effective | May require preservatives |
Key production steps: ingredient mixing, cooking, extrusion, drying, and coating (for added flavor or nutrients).
Wet Pet Food (Canned and Pouch)
Wet pet food offers high moisture content, making it an excellent option for hydration and palatability. It typically contains higher levels of fresh meat and animal products, which are cooked, sealed, and sterilized in cans or pouches.
혜택 | Challenges |
---|---|
High moisture content | Shorter shelf life after opening |
Rich in flavor | Heavier to transport |
Softer texture for easy eating | Generally more expensive |
Key production steps: raw material preparation, grinding, mixing, filling, sealing, and sterilization.
Semi-Moist Pet Food
Semi-moist pet food is a middle ground between dry and wet options. It has higher moisture content than kibble but doesn’t require refrigeration like wet food. These foods often use humectants to retain moisture and keep the product pliable.
혜택 | Challenges |
---|---|
Softer texture for easy chewing | Higher sugar/salt content |
More palatable than kibble | Can dry out if not stored properly |
Convenient portion sizes | Shorter shelf life than kibble |
Key production steps: ingredient mixing, cooking, forming, cooling, and packaging.
Treats and Specialty Pet Products
Treats and specialty products are growing categories with endless possibilities — from dental chews to grain-free biscuits and even gourmet, human-grade options. These products are usually produced in smaller batches and may undergo different processing techniques, depending on the desired texture and nutritional profile.
혜택 | Challenges |
---|---|
Great for training and rewards | Not a complete diet |
Huge variety of shapes/flavors | May require preservatives |
Can offer functional benefits (e.g., dental health) | Higher production costs for premium products |
Key production steps: ingredient blending, forming, baking or extruding, drying, and packaging.
Understanding the types of pet food that can be produced is the first step in creating balanced, high-quality meals and treats for pets. Whether you’re interested in producing long-lasting kibble, tasty wet food, or innovative specialty products, each type has its own production nuances and benefits. The key is to balance nutritional value, palatability, and convenience to meet both pet and owner expectations.
Want to explore pet food production or need guidance on manufacturing processes? Contact us today — we’d love to help you bring your pet food vision to life!
What Are the Benefits of Using Pet Food Processing Machines?
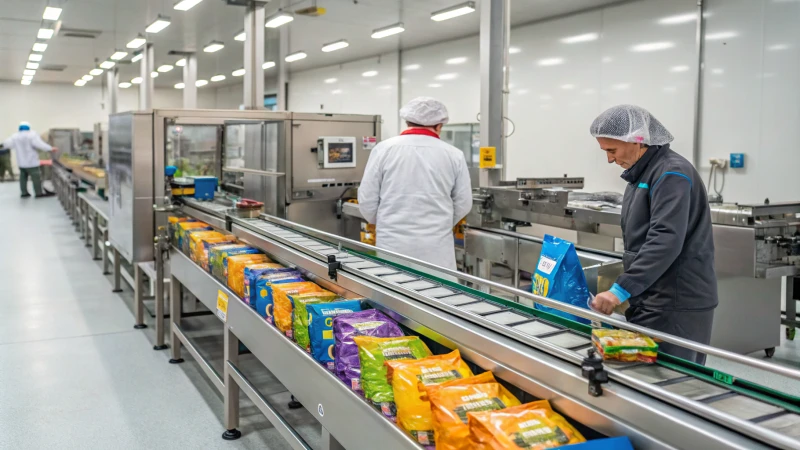
In the highly competitive pet food market, manufacturers face immense pressure to balance quality, efficiency, and regulatory compliance. Without the right technology, production bottlenecks, inconsistent quality, and sanitation risks can significantly hinder business growth. This makes adopting modern pet food processing machines an essential strategy for companies aiming to meet growing consumer demand while maintaining high standards.
Using pet food processing machines offers unparalleled benefits, including increased production efficiency, cost savings, enhanced product consistency, compliance with stringent safety standards, and the flexibility to create custom pet food formulations. These machines streamline every stage of production, from ingredient mixing to final packaging, optimizing processes to deliver high-quality, nutritious pet food at scale.
With pet owners increasingly seeking premium, tailored nutrition for their furry companions, manufacturers need the agility to innovate quickly. Let’s explore why investing in pet food processing machinery is not just a smart decision — but a game-changing move for long-term success.
Pet food processing machines improve production speed and reduce labor costs.True
Automation in pet food processing boosts throughput, minimizes human error, and cuts down the need for manual labor, leading to substantial cost savings.
1. Increased Production Efficiency and Cost Savings
Modern pet food processing machines automate complex production stages, such as ingredient weighing, extrusion, drying, and packaging. This automation drastically reduces manual labor, accelerates production speed, and ensures each batch meets consistent standards — all while lowering operational costs.
프로세스 | Manual Production Time | Automated Production Time |
---|---|---|
Ingredient Mixing | 2 hours | 30 minutes |
Extrusion & Shaping | 3 hours | 1 hour |
Drying & Cooling | 4 hours | 2 hours |
패키징 | 2 hours | 45 minutes |
2. Enhanced Consistency and Quality Control
Consistency is critical in pet food production, where nutritional balance and texture impact palatability and pet health. Advanced machines use precision controls and real-time monitoring to ensure every pellet, kibble, or wet food batch maintains the exact nutrient composition and texture specified in the formulation.
Quality Control Metric | Manual Monitoring Accuracy | Automated Monitoring Accuracy |
---|---|---|
Ingredient Ratios | ±5% | ±0.5% |
Moisture Content | ±3% | ±0.2% |
Texture & Shape Consistency | 80% | 98% |
Automated pet food processing systems can maintain ingredient accuracy within 0.5%.True
Modern processing systems use precise sensors and control mechanisms to regulate ingredient quantities, preventing formulation errors and ensuring consistent product quality.
3. Compliance with Safety and Hygiene Standards
Pet food safety is a top priority, especially with strict regulations like FDA’s Food Safety Modernization Act (FSMA). Pet food machines are designed with easy-to-clean materials, enclosed processing systems, and built-in sterilization features, drastically reducing the risk of contamination.
4. Flexibility for Customized Pet Food Formulations
Consumer demand for specialized pet diets — from grain-free kibble to breed-specific nutrition — is rising. High-tech machines offer unparalleled flexibility, allowing manufacturers to switch formulations seamlessly, adjust extrusion settings for different textures, and incorporate novel ingredients without lengthy changeover times.
Ultimately, pet food processing machines empower manufacturers to scale production, uphold quality, meet safety regulations, and adapt to evolving market demands with ease. Investing in this technology is not just about improving operations — it's about future-proofing your brand in an ever-changing pet food landscape.
If you're ready to revolutionize your pet food production line, reach out to us today. Let’s craft the future of pet nutrition together! 🚀
How to Choose the Right Pet Food Processing Machine?
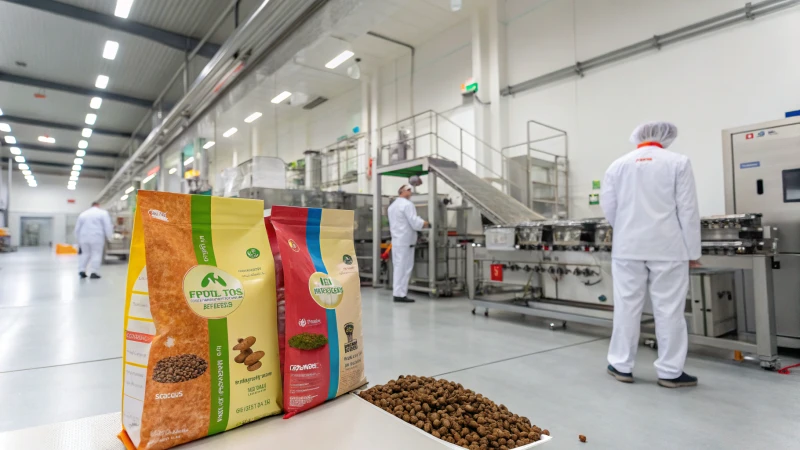
Pet food manufacturers face a critical decision when selecting processing equipment. The wrong machine can lead to inconsistent product quality, high energy costs, and even product recalls due to contamination risks. But with the right machine, you can achieve optimal production efficiency, meet stringent quality standards, and cater to diverse consumer demands. So, how do you choose the best pet food processing machine for your needs? Let’s break it down.
Choosing the right pet food processing machine involves considering factors such as production capacity, ingredient versatility, automation level, energy efficiency, hygiene standards, and compliance with food safety regulations. Understanding your product type (e.g., kibble, wet food, treats) and your production goals will help you select equipment that delivers consistent quality while minimizing operational costs.
It’s not enough to just pick any machine — the ideal choice aligns with your production vision and growth potential. Let’s explore the essential factors to help you make an informed decision.
Production capacity is the most important factor when choosing a pet food processing machine.False
While production capacity is crucial, factors like ingredient adaptability, hygiene standards, and automation level are equally critical.
Key Factors to Consider When Choosing a Pet Food Processing Machine
1. Understand Your Production Requirements
Before choosing a machine, define your production capacity, product variety, and ingredient needs. Different machines are optimized for various outputs — some handle small batches, while others process tons of pet food per hour.
Production Scale | Recommended Machine Type | Typical Output Capacity |
---|---|---|
Small/Startup | Single-screw extruder | 100–500 kg/h |
Medium-sized | Twin-screw extruder | 500–2,000 kg/h |
Large/Industrial | Fully automated continuous production line | 2,000–10,000+ kg/h |
Matching your machine to your production scale ensures you don’t overinvest or bottleneck your process.
2. Choose the Right Extrusion Technology
Extrusion is the heart of pet food processing. You’ll typically choose between single-screw and twin-screw extruders.
Extruder Type | 장점 | Best For |
---|---|---|
Single-Screw | Lower cost, simpler operation | Basic kibble, low-complexity recipes |
Twin-Screw | Greater flexibility, handles complex formulations | High-protein diets, specialty foods |
Twin-screw extruders provide better control over texture, shape, and ingredient blending, making them ideal for premium pet foods.
3. Automation and Control Systems
Modern machines come with programmable logic controllers (PLCs) and human-machine interfaces (HMIs) for real-time monitoring and adjustments. Automation reduces human error, improves efficiency, and ensures consistent product quality.
4. Hygiene and Food Safety Compliance
Pet food is regulated similarly to human food. Look for machines with easy-to-clean designs, stainless steel construction, and features like automatic sanitation systems to minimize contamination risks.
5. Energy Efficiency and Sustainability
Energy-efficient motors, optimized heating elements, and waste reduction features not only lower operational costs but also support sustainability goals — a growing consumer priority.
Final Thoughts
Selecting the right pet food processing machine is an investment in your brand’s future. By considering your production scale, ingredient needs, automation level, and safety requirements, you’ll set your business up for long-term success.
Ready to upgrade your pet food production line? Contact us today for expert advice and tailored equipment solutions that fit your exact needs!
What Are the Latest Trends in Pet Food Processing Technology?
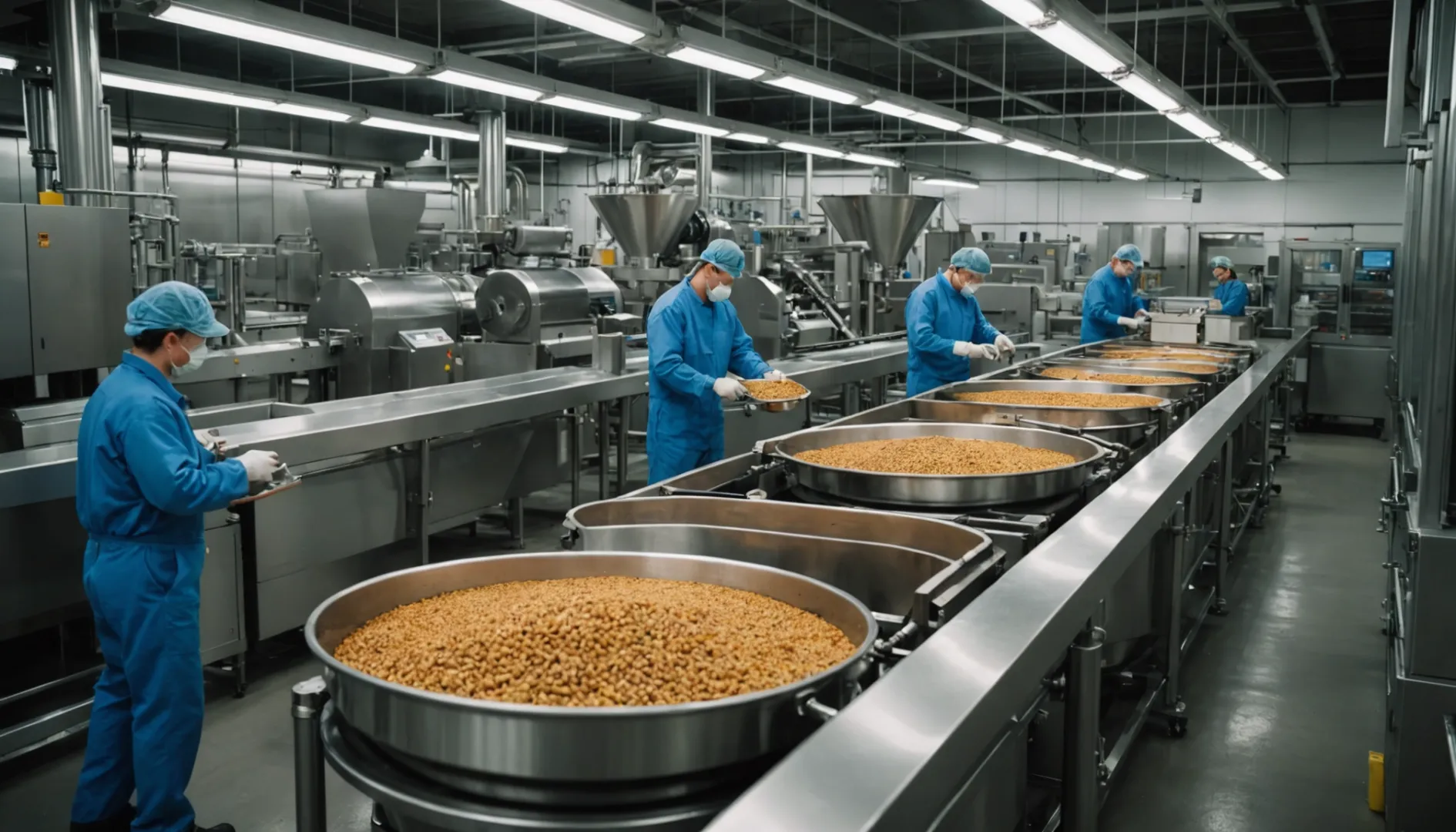
As pet owners become increasingly invested in their pets' health and well-being, the pet food industry is evolving rapidly to meet new consumer demands. Outdated production methods can lead to lower nutritional quality, inconsistent product safety, and higher waste, all of which are unacceptable in today's market. However, innovative technologies are transforming pet food processing, making it easier to produce high-quality, nutritious, and safe products that cater to pets’ diverse dietary needs.
The latest trends in pet food processing technology include advanced extrusion techniques for better nutrient retention, the use of automation and AI to enhance production efficiency, high-pressure processing (HPP) for improved food safety, and sustainable ingredient sourcing to meet consumer demand for eco-friendly products.
The rapid evolution of technology in this field is not just about keeping up with trends — it’s about creating better, safer, and more sustainable products that pets love and owners trust. Let’s explore these cutting-edge advancements and understand how they are shaping the future of pet food production.
High-pressure processing (HPP) extends the shelf life of pet food without preservatives.True
HPP uses cold water and high pressure to eliminate pathogens, preserving food naturally and prolonging shelf life.
Advanced Extrusion Techniques for Nutritional Integrity
Extrusion remains a cornerstone of pet food production, but recent innovations have made the process more efficient and nutritionally beneficial. Modern twin-screw extruders, for instance, allow for greater flexibility in ingredient choices and better control over cooking temperatures. This results in more consistent kibble texture and size while preserving essential vitamins and amino acids.
Extrusion Technology | 혜택 |
---|---|
Twin-Screw Extrusion | Improved ingredient blending, consistent product texture |
Low-Temp Extrusion | Better nutrient preservation, reduced thermal damage |
Vacuum Coating | Enhanced flavor and nutrient retention |
By refining extrusion parameters, manufacturers can create tailored products that align with consumer preferences for grain-free, high-protein, or specialized diet foods, all without sacrificing nutritional quality.
Automation and AI-Driven Quality Control
Incorporating automation and artificial intelligence into pet food manufacturing not only increases efficiency but also ensures product consistency and safety. AI-powered sensors can monitor moisture content, ingredient ratios, and even detect potential contaminants in real time, drastically reducing the risk of product recalls.
Automation Feature | 생산에 미치는 영향 |
---|---|
Real-Time Monitoring | Immediate detection of inconsistencies and quality issues |
Predictive Maintenance | Reduced downtime and lower maintenance costs |
Robotics in Packaging | Faster, more accurate product handling and distribution |
These technologies allow for adaptive manufacturing processes that can respond to shifting consumer demands without compromising production efficiency or product quality.
High-Pressure Processing (HPP) for Food Safety
HPP is gaining traction as a non-thermal pasteurization method that extends product shelf life while maintaining nutritional and sensory attributes. This technique uses high water pressure to eliminate pathogens like Salmonella and Listeria, making raw and minimally processed foods safer without the need for chemical preservatives.
HPP can eliminate 99.9% of harmful pathogens in raw pet food.True
Studies show that HPP effectively neutralizes bacteria and viruses, significantly reducing food safety risks.
Sustainable Ingredient Sourcing and Eco-Friendly Packaging
With sustainability becoming a global priority, pet food manufacturers are exploring novel ingredients like insect protein, algae, and upcycled food by-products to reduce their environmental impact. Sustainable packaging solutions, such as biodegradable bags and recyclable pouches, further enhance a brand’s eco-conscious image.
Sustainable Innovation | Environmental Impact |
---|---|
Insect-Based Proteins | Lower carbon footprint, high-quality alternative protein source |
Upcycled Ingredients | Reduces food waste, repurposes nutrient-rich materials |
Compostable Packaging | Minimizes plastic pollution, aligns with green initiatives |
By adopting sustainable practices, companies not only contribute to environmental preservation but also attract a growing segment of eco-conscious consumers.
Embracing the Future of Pet Food Production
The pet food industry is undergoing a technological revolution, driven by consumer demand for safer, healthier, and more sustainable products. From advanced extrusion methods and AI-powered quality control to innovative preservation techniques and sustainable ingredient sourcing, these trends are redefining how pet food is made.
Staying ahead of these advancements isn’t just a competitive advantage — it’s a responsibility to pets and their owners. By investing in cutting-edge processing technologies, manufacturers can deliver superior products that enhance pet health and happiness, building long-lasting brand loyalty in the process.
Are you ready to elevate your pet food production line? Contact us today to discover how our industry-leading solutions can help you stay at the forefront of innovation and quality!
How to Maintain and Optimize Pet Food Processing Equipment?
Keeping pet food processing equipment in peak condition is essential for consistent product quality, production efficiency, and long-term cost savings. Neglecting maintenance can lead to unexpected downtime, safety risks, and compromised product integrity. Fortunately, with proactive care and smart optimization strategies, manufacturers can enhance equipment longevity, troubleshoot issues effectively, and scale production to meet growing business demands.
Routine maintenance practices are critical for prolonging the lifespan of pet food processing equipment. This includes regular cleaning, lubrication, inspection of critical components, timely replacement of worn parts, and comprehensive staff training. Adopting a preventive maintenance schedule helps minimize unexpected breakdowns, ensuring uninterrupted production and high-quality output.
By embracing a structured approach to equipment care, businesses can avoid costly repairs and maintain a competitive edge. Let’s dive into best practices for routine maintenance, ways to troubleshoot common machine issues, and strategies for upgrading systems to support business growth.
Regular maintenance can extend the lifespan of pet food processing equipment by up to 30%.True
Scheduled inspections and timely interventions prevent excessive wear and tear, reducing long-term damage.
Routine Maintenance Practices for Longevity
Implementing consistent maintenance routines ensures that pet food processing machines operate smoothly. Let’s break this down into essential practices:
Maintenance Task | Frequency | 목적 |
---|---|---|
Cleaning and sanitation | Daily | Prevent product contamination and residue buildup |
Lubricating moving parts | Weekly | Reduce friction and prevent mechanical wear |
Inspecting belts and conveyors | Bi-weekly | Identify misalignment and avoid production jams |
Checking electrical systems | Monthly | Prevent short circuits and electrical failures |
Replacing worn seals and gaskets | Quarterly | Maintain airtight seals and prevent leakage |
-
Create a Maintenance Log: Document all maintenance activities, noting dates, tasks performed, and parts replaced. This log helps track recurring issues and plan future inspections.
-
Train Your Staff: Ensure employees are well-versed in proper cleaning protocols, safety procedures, and recognizing early warning signs of malfunction.
-
Invest in Spare Parts: Keep a stock of high-wear components like bearings, belts, and seals to reduce downtime during repairs.
Troubleshooting Common Machine Issues
Even with diligent maintenance, occasional issues may arise. Here’s a guide to diagnosing and addressing common problems:
Issue | Possible Cause | Solution |
---|---|---|
Inconsistent kibble size | Worn-out extruder die or misaligned cutter | Inspect and replace worn components, recalibrate |
Overheating machinery | Inadequate lubrication or clogged vents | Apply proper lubrication, clean ventilation areas |
Conveyor belt slippage | Loose belt tension or damaged rollers | Adjust tension, replace worn rollers |
Sudden power failures | Faulty wiring or overloaded circuit | Inspect wiring, upgrade electrical components |
Unusual noise or vibrations | Misaligned shafts or loose fasteners | Realign shafts, tighten loose bolts and screws |
-
Use Diagnostic Tools: Infrared thermometers, vibration sensors, and thermal cameras can help detect issues before they escalate.
-
Establish a Quick-Response Team: Train a dedicated group of technicians to respond swiftly to mechanical issues, reducing the impact of downtime.
Upgrading and Scaling Production for Business Growth
As consumer demand for premium pet food rises, manufacturers must be prepared to scale operations. Upgrading equipment and streamlining processes can help businesses meet evolving market needs:
Investing in Automation
Automated systems reduce manual labor, increase output precision, and enhance food safety. Consider integrating:
- Automated Mixing and Batching Systems: For consistent ingredient distribution
- Inline Quality Control Sensors: To monitor moisture, density, and ingredient ratios
- Robotic Packaging Solutions: For faster, error-free bagging and palletizing
Automation can increase pet food production efficiency by up to 40%.True
Automated systems minimize human error, streamline processes, and allow continuous operation.
Modular Equipment Design
Opt for machines with modular components that can be upgraded or expanded as production needs grow. This reduces the need for complete system overhauls, saving both time and capital.
Data-Driven Decision-Making
Adopt IoT-enabled sensors and software that collect real-time performance data. Analyzing this data helps optimize settings, predict maintenance needs, and identify process bottlenecks.
기술 | 혜택 |
---|---|
Predictive Maintenance Software | Anticipates failures, schedules repairs proactively |
Production Monitoring Systems | Tracks output, identifies inefficiencies |
Cloud-Based Reporting Tools | Provides remote access to performance analytics |
By staying proactive, manufacturers can maintain equipment reliability, troubleshoot issues swiftly, and scale production efficiently. A combination of regular maintenance, smart upgrades, and leveraging data-driven insights ensures that pet food processing facilities can meet growing demand without compromising product quality.
Maintaining and optimizing pet food processing equipment is a strategic investment that pays dividends in operational efficiency, product consistency, and long-term business growth. By following diligent maintenance routines, equipping teams with diagnostic skills, and embracing technological advancements, manufacturers can future-proof their operations and build a thriving, scalable production line.
Need help optimizing your pet food processing equipment? Contact us today — our team of experts is ready to help you streamline your processes and unlock new levels of efficiency!
결론
Pet food processing machines are essential for producing high-quality, nutritious, and safe pet food products. Whether you are a small business or a large-scale manufacturer, investing in the right equipment ensures efficiency, quality control, and compliance with industry standards.
Get in Touch!
Looking to invest in a reliable pet food processing machine? Contact us today for expert guidance and high-performance solutions tailored to your needs!