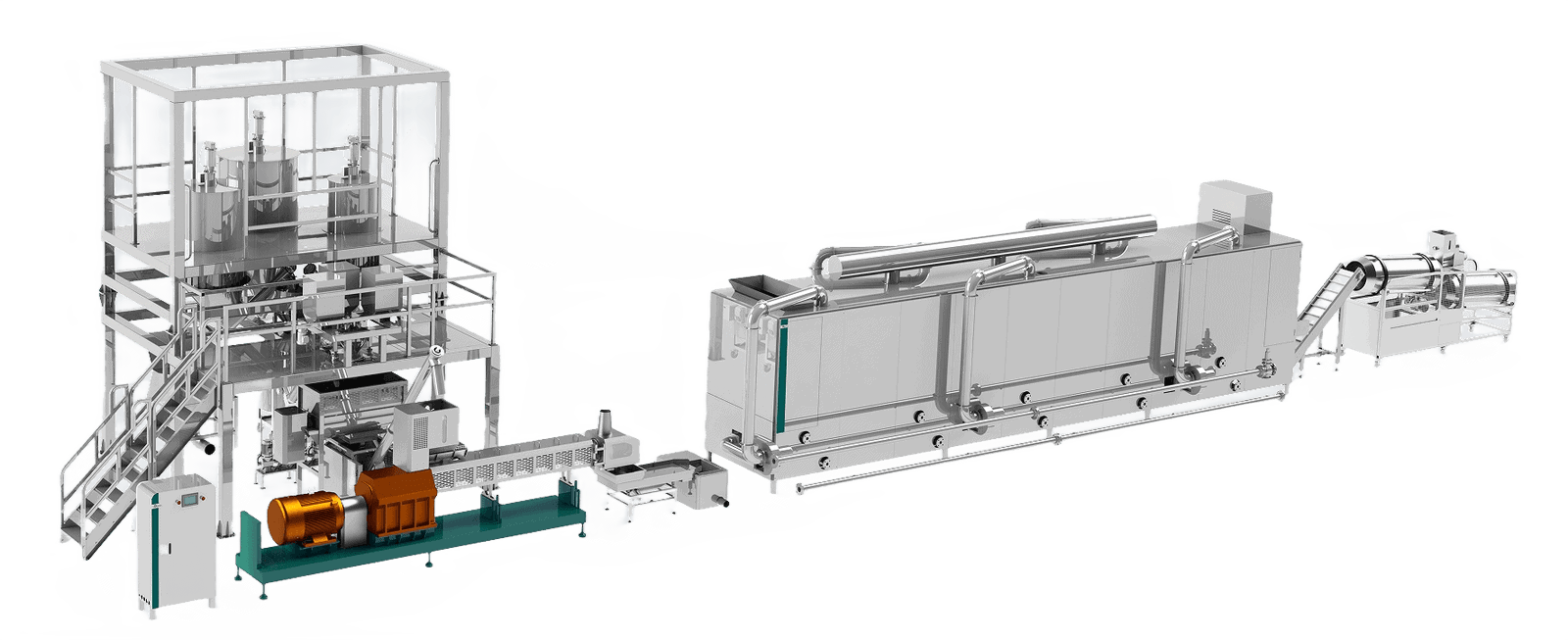
Ever wondered how your pet’s favorite kibble is made? It’s all thanks to some pretty impressive machinery.
A pet food extruder typically consists of a feeder, pre-conditioner, extruder barrel, screw, die, and cutter. Each component plays a vital role in processing ingredients into finished products. Understanding these elements helps optimize production and ensure consistent quality.
When I first delved into the world of pet food manufacturing, I was amazed by the complexity of the extrusion process. It's like the backbone of creating those perfect little kibbles my dog can't get enough of! Each component of the extruder plays a crucial role. For example, when I learned about the screw's job in pushing and mixing ingredients, it reminded me of my own kitchen mixer—only way more powerful and precise. Let's explore what makes each part so essential to crafting high-quality pet food.
The feeder is used to add raw materials into the extruder.真
The feeder introduces raw materials into the extrusion process.
The cutter shapes the extruded pet food into desired forms.真
The cutter slices the extruded material into specific shapes.
How Does the Feeder System Work in an Extruder?
Have you ever wondered what magic turns raw materials into your pet's favorite meal or the plastic items we use daily?
In an extruder, the feeder system is crucial for consistently delivering raw materials into the machine. It ensures a steady flow, regulates the feed rate, and prevents blockages, facilitating smooth and efficient extrusion processes.
The Basics of Extruder Feeder Systems
I remember the first time I stood in front of a massive extruder, feeling like a tiny ant next to an engineering giant. The feeder system caught my eye immediately because it seemed like the heart of the operation, rhythmically pulsing raw materials into the machine. This part is designed to deliver materials at a consistent rate, a bit like a seasoned chef steadily adding spices to a simmering pot. It's essential for maintaining not just efficiency but also the quality of the end product. There are different types, such as volumetric feeders1, which are a bit like measuring cups delivering a fixed amount, and gravimetric feeders, which are more like precision scales ensuring exact weights.
Feeder Type | 説明 |
---|---|
Volumetric Feeder | Delivers a fixed volume per time unit. |
Gravimetric Feeder | Measures by weight for precise control. |
Components of a Feeder System
Let's dive into the nuts and bolts—or should I say screws and hoppers—of what makes these systems tick. Think of the hopper as a storage silo holding all your raw ingredients. Then there's the auger or screw, which does the heavy lifting, moving materials into the extruder just like those conveyor belts you see in old cartoons. The motor powers it all, ensuring that everything flows smoothly, without a hiccup.
Each component plays a crucial role in making sure everything works in harmony. It's kind of like an orchestra where each instrument must be perfectly in sync.
- Hopper: Holds and releases raw materials.
- Auger or Screw: Moves materials into the extruder.
- モーター: Powers the auger for consistent flow.
Challenges and Solutions
Running an extruder isn't always smooth sailing. I’ve learned that feeder systems can sometimes throw a tantrum—like inconsistent feed rates or even blockages. Regular maintenance is key, much like keeping your car engine purring with timely oil changes. Choosing the right type of feeder can also help dodge these issues. For instance, integrating sensors can be a game-changer, offering real-time feedback to prevent overfeeding or underfeeding.
Industry Applications
Extruder feeder systems have their fingerprints all over industries, from pet food production2 to plastics manufacturing. I’ve seen firsthand how in pet food processing, these feeders ensure that ingredients blend uniformly, making sure every kibble tastes just right for our furry friends. In plastics, they provide the exact mix of polymers and additives needed to produce high-quality products.
Industry | Role of Feeder System |
---|---|
Pet Food | Ensures uniform ingredient blending. |
Plastics | Provides precise polymer-additive mixture. |
The efficiency and accuracy of these systems are vital for product quality. They’re like unsung heroes in modern manufacturing, working tirelessly behind the scenes.
Volumetric feeders measure material by weight.偽
Volumetric feeders deliver a fixed volume, not by weight.
Hoppers release raw materials in feeder systems.真
Hoppers hold and release raw materials into the feeder system.
Why Are Pre-conditioners Essential in Pet Food Processing?
Imagine transforming a pile of raw ingredients into a delicious and nutritious meal for your furry friend. That's where pre-conditioners come into play, making magic happen in pet food production.
A pre-conditioner in pet food processing primarily hydrates and heats raw materials before extrusion. This step enhances ingredient blending, starch gelatinization, and protein denaturation, resulting in improved product texture and nutritional quality.
How Does a Pre-conditioner Work?
Have you ever tried baking a cake without mixing the batter properly? It’s almost always a disaster. I remember once forgetting to add water to the cake mix, and let’s just say it turned into a crunchy cookie instead. That’s precisely the kind of challenge a pre-conditioner helps avoid in pet food processing. By heating and adding moisture to the ingredients, it ensures everything blends perfectly. Steam and water swell and soften the particles, paving the way for that all-important gelatinization of starches3, which not only boosts digestibility but also enhances nutritional value.
The Benefits of Using Pre-conditioners
-
Improved Product Quality: Think of pre-conditioning as a chef meticulously preparing ingredients for a gourmet dish. This step guarantees even mixing, leading to consistent texture and flavor—something our pets appreciate as much as we do! Enhanced blending facilitates better protein denaturation4, refining the texture further.
-
エネルギー効率: By partially cooking the ingredients, pre-conditioners save on energy costs during extrusion. It's like preheating an oven; you get things cooking faster without using extra gas or electricity.
-
Increased Production Capacity: Imagine how much quicker you could bake cookies if you didn’t have to mix each batch individually. Pre-conditioning streamlines the extrusion process, allowing for quicker production speeds and increased throughput.
ベネフィット | 説明 |
---|---|
Improved Quality | Even mixing and enhanced texture and flavor |
エネルギー効率 | Reduces energy needs by partial cooking |
Increased Capacity | Faster production speeds, higher throughput |
Integration into Production Lines
Pre-conditioners are like versatile kitchen gadgets that fit right into various stages of pet food production lines, often pairing with other machinery like extruders and dryers. This adaptability allows them to handle everything from dry kibble to semi-moist treats with ease.
Understanding how pre-conditioners fit into the bigger picture helps manufacturers optimize their processes to churn out high-quality pet food efficiently. For those looking to dive deeper into the world of food technology, exploring innovative machinery solutions5 is a great next step.
Pre-conditioners improve pet food texture.真
Pre-conditioners enhance blending and protein denaturation, improving texture.
Pre-conditioners decrease production capacity.偽
They increase capacity by streamlining processes for faster production.
Why is the extruder barrel critical in the production line?
Imagine trying to bake a cake without the right-sized oven. That's how crucial an extruder barrel is on a production line.
The extruder barrel is essential in the production line as it ensures consistent material flow, optimal temperature control, and high-quality output. It plays a critical role in mixing, melting, and transporting materials.
The Functionality of the Extruder Barrel
Let me take you back to when I first stepped into the world of manufacturing. I remember staring at this giant, intimidating machine that looked like it belonged in a sci-fi movie rather than a production floor. That was my first introduction to an extruder barrel. And over the years, I've learned just how much it does behind the scenes. At its core, the extruder barrel houses the screw mechanism that mixes and moves materials smoothly along the production line. Just think of it as the heartbeat of the process, controlling how materials get heated, melted, and mixed before they transform into their final forms. This is especially crucial in processes like plastic extrusion6, where uniformity is key.
Importance in Temperature Control
Temperature control might seem like a geeky detail, but trust me, it's everything in extrusion processes. Picture trying to make your favorite soup without letting it simmer just right—too hot and it burns, too cold and it's undercooked. The extruder barrel must maintain that sweet spot of precise temperatures to keep material viscosity just right and prevent any breakdowns. Some barrels even come with multiple heating zones—like having different stove burners—so you can fine-tune temperatures across the board for exact temperature regulation7. It's these nuances that help us churn out high-quality products while keeping waste at bay.
Material Consistency and Quality
I remember a time when a miscalculation in our extruder settings led to a batch of pet snacks that were less than stellar. That was a wake-up call about how much the barrel's design impacts consistency. A well-designed barrel ensures we get uniform pressure and shear rates, which are vital for nailing down the perfect material properties. In industries like pet food manufacturing, where consistency is non-negotiable, having an efficient barrel can spell the difference between a hit product and a costly mistake.
特徴 | メリット |
---|---|
Multi-zone Heating | Precise temperature control for varied materials |
Uniform Pressure | Consistent material flow and product quality |
Durable Materials | Increased lifespan and reduced maintenance costs |
Challenges and Considerations
Of course, keeping an extruder barrel in tip-top shape isn't always smooth sailing. There are days when wear and tear feel like they're conspiring against us or when setting the wrong temperature throws everything off balance. But through trial and error—and a fair share of troubleshooting—I've learned how crucial it is to stay ahead of common extruder problems8. Being proactive in maintenance is key to ensuring everything runs like clockwork.
Technological Innovations in Barrel Design
In recent years, I've seen some jaw-dropping innovations in extrusion technology that make me geek out a little (or a lot). Imagine self-cleaning barrels that cut down on downtime or materials that last longer than ever, reducing maintenance needs. Companies diving into these tech-forward solutions often witness leaps in production efficiency and quality.
These advancements prove that the extruder barrel isn't just another cog in the machine; it's a strategic investment for anyone serious about pushing boundaries in efficiency and product quality.
The extruder barrel ensures uniform material heating.真
The barrel is designed to uniformly heat materials, crucial for quality.
Extruder barrels have no impact on product consistency.偽
Barrel design affects pressure and shear, impacting material consistency.
How Does the Screw Influence Pet Food Quality?
Imagine cooking your pet's dinner and realizing that a tiny component could make all the difference.
The screw in pet food extrusion machines controls the mixing, cooking, and forming of ingredients. Its design influences the texture, flavor distribution, and nutritional quality of pet food products.
The Role of Screw Design in Pet Food Processing
I remember the first time I saw the inside of a pet food extrusion machine—it was like peering into the heart of what makes our furry friends' meals so special. The screw design is pivotal here, as it intricately mixes, cooks, and forms ingredients into those perfect kibble pieces. Different screw configurations can really make a difference in the final product, affecting everything from its nutritional profile to its texture.
-
Single Screw: These are great for simpler formulations. Think of them like a trusty old blender—reliable and straightforward, perfect for basic recipes.
-
Twin Screw: Now, these are the heavy lifters. They allow for more complex formulations, providing better mixing and cooking control, which can really enhance nutrient retention9.
Screw Type | メリット | アプリケーション |
---|---|---|
Single Screw | Cost-effective, straightforward | Basic dry foods |
Twin Screw | Enhanced mixing, nutrient retention | Premium or complex formulations |
Influence on Ingredient Mixing and Cooking
The way screws affect mixing and cooking is fascinating. I liken it to how you would adjust your stove's flame to get that perfect simmer. The speed and pressure created by the screw can change the temperature, which in turn affects how proteins and starches gelatinize—crucial for digestibility and palatability.
Customizing screw elements is like adding a pinch of salt to your dish—subtle adjustments can lead to significant differences in moisture retention and flavor distribution10.
Nutritional and Sensory Quality Impacts
Have you ever thought about how a pet food’s smell or texture can make or break its appeal to our pets? The design of the screw ensures consistent kibble size and shape, which is essential for consumer satisfaction11. It's like making sure every cookie in the batch comes out just right. Moreover, it helps incorporate fats and oils that enhance flavor without compromising nutritional value.
Screw configurations are also key in maintaining the integrity of sensitive ingredients like vitamins and minerals—these are the nutrients that keep our pets healthy and happy.
Innovations in Screw Technology
I'm always amazed at how innovation continues to drive our industry forward. Emerging technologies in screw design focus on optimizing processing conditions to improve efficiency12 while minimizing nutrient loss. Innovations such as self-cleaning screws not only reduce downtime but also increase throughput.
By integrating sensors and advanced materials, modern screw designs offer real-time data on the extrusion process. This helps manufacturers make precise adjustments, ensuring that every batch of pet food meets our high standards of quality.
Twin screws enhance nutrient retention in pet food.真
Twin screws provide better mixing and cooking control, enhancing nutrient retention.
Single screws are used for complex pet food formulations.偽
Single screws are generally used for simpler formulations, not complex ones.
How Does the Die Shape Pet Food?
Ever pondered how your furry friend's food gets those perfect shapes? It's all thanks to a nifty tool called the die.
In pet food production, the die is used to shape the extruded mixture into specific forms like kibbles or biscuits. It ensures uniform size and texture, enhancing both the product's appeal and its functionality.
The Role of Dies in Pet Food Manufacturing
I remember my first visit to a pet food manufacturing plant, feeling a bit like Charlie in Willy Wonka's factory. As I watched the machinery work its magic, I was fascinated by the die13's role. It’s this unassuming component that takes the pet food mix and transforms it into uniform, appealing shapes. The die’s role isn't just about aesthetics; it’s also crucial for getting the texture just right.
Types of Dies and Their Applications
Different shapes call for different dies. There’s a unique satisfaction in knowing that flat dies make those familiar kibble shapes, while ring dies create more intricate designs. It's like having a set of cookie cutters specifically for pet food! Here's a quick overview:
Die Type | 申し込み |
---|---|
Flat Die | Kibble |
Ring Die | Complex Shapes |
Pellet Die | Small Pellets |
Influence on Nutritional Quality
There's something almost magical about how the design of a die can influence cooking times and nutritional retention. It’s not just about making food look pretty—it’s about ensuring our pets get the best nutrients possible. The cooking process14 inside the extruder is finalized as the mix passes through the die, impacting everything from nutrient retention to how appealing the final product is to our pets.
Customization for Brand Differentiation
Every time I see a uniquely shaped kibble, I can't help but think about the custom dies behind them. These dies are key for brands wanting to stand out in a crowded market. They allow for creative designs that aren't just eye-catching but also functional, meeting specific brand goals and consumer preferences.
The die’s contribution goes beyond mere shape; it’s essential for achieving texture, consistency, and nutritional excellence in pet food production. For more on how pet food dies can be customized for branding, check out this informative guide15.
Dies shape and finalize pet food texture.真
Dies determine the final shape and texture of pet food by extrusion.
Ring dies are used for kibble production.偽
Flat dies, not ring dies, are typically used for kibble production.
How do cutters ensure product consistency?
Have you ever wondered how pet food manufacturers achieve that perfect uniformity in every bite?
Product consistency with cutters is achieved through precise control mechanisms, high-quality blades, and advanced automation technologies. These elements work together to ensure uniform size and shape, critical for maintaining quality standards.
Understanding Cutter Technology
I remember walking through one of my factories for the first time, feeling both excitement and a tad overwhelmed. The hum of machinery was like music, each cutter working in perfect harmony to create uniform pet treats. But how do these cutters manage such precision?
Cutters are the unsung heroes in ensuring each piece of pet food or treat matches the next. They achieve this through cutting-edge technology:
- Precision Blades: High-quality blades are essential. They make clean cuts, reducing waste and ensuring each piece is just right. I always emphasize regular maintenance and sharpening because I’ve seen firsthand how dull blades can lead to inconsistencies.
- Automation Systems: Our modern cutters are equipped with sophisticated automation systems. They adjust cutting parameters on the fly, minimizing human error and ensuring a steady, consistent output.
Factors Influencing Consistency
There are several factors at play when it comes to maintaining consistency with a cutter, and I've learned this through years of experience:
ファクター | Impact on Consistency |
---|---|
Blade Sharpness | Dull blades lead to uneven cuts |
Material Type | Different materials require specific cutting settings |
Machine Calibration | Incorrect settings can cause size variations |
Understanding these factors16 is key to optimizing our processes and keeping that consistency our customers expect.
ベストプラクティスの実践
Achieving optimal results is no accident. It’s about implementing best practices, something I stress to my team regularly:
- Regular Calibration: Keeping our cutters calibrated means they’re always aligned with the specs we promise.
- Quality Monitoring: Continuous quality checks allow us to catch inconsistencies before they become a problem.
- トレーニング: Well-trained operators make all the difference. It’s why I invest in regular training sessions to reduce errors and improve output consistency.
By focusing on these areas, businesses like mine can enhance production efficiency and uphold high standards. Learn more about the importance of training17 in achieving product consistency.
Future Innovations in Cutting Technology
Looking ahead, I’m excited about the new technologies on the horizon. With AI and machine learning making their way into cutter systems, predictive maintenance and even greater precision are within reach.
Staying informed about these innovations is crucial for any business aiming to stay competitive in manufacturing. As technology evolves, so will our methods to achieve unmatched product consistency.
Precision blades reduce waste in product cutting.真
Sharp blades ensure clean cuts, minimizing material waste.
Automation systems increase human error in cutting processes.偽
Automation reduces human error by adjusting parameters in real-time.
結論
A pet food extruder consists of key components like feeders, pre-conditioners, barrels, screws, dies, and cutters that work together to produce high-quality pet food efficiently.
-
Learn how volumetric feeders ensure a consistent material flow in extrusion processes. ↩
-
Discover how feeder systems enhance ingredient mixing and consistency in pet food manufacturing. ↩
-
This link provides insight into how starch gelatinization enhances digestibility and nutritional value. ↩
-
Learn how denaturation processes improve texture and contribute to product quality. ↩
-
Explore cutting-edge machinery that enhances efficiency and product quality in food processing. ↩
-
Learn how the extruder barrel functions in plastic extrusion processes to enhance understanding of its role. ↩
-
Discover how advanced temperature control mechanisms improve extrusion efficiency and product quality. ↩
-
Explore typical issues faced with extruders and effective solutions to maintain optimal performance. ↩
-
Explore the advantages of twin screw extrusion in maintaining nutritional quality. ↩
-
Discover how screw design can enhance flavor distribution in pet food products. ↩
-
Find out why consistent kibble size is important for consumer acceptance. ↩
-
Investigate recent innovations that improve extrusion efficiency and product quality. ↩
-
Understanding the die's function in extrusion reveals its impact on product shape and texture. ↩
-
Learn how extrusion affects nutrient retention and cooking quality in pet food. ↩
-
Discover how custom dies can enhance brand identity through unique product shapes. ↩
-
Explore the various factors that can affect product consistency and how addressing them can improve quality control processes. ↩
-
Learn why operator training is crucial for maintaining high product standards and minimizing errors in production. ↩