I remember the first time I had to choose a pet food extruder; it felt like diving into a sea of options without a map.
To choose the right pet food extruder, consider factors like production capacity, technology type (single or twin-screw), energy efficiency, and specific functionalities tailored to your products. Evaluate your business goals and future expansion plans to ensure the extruder aligns with your needs.
Back then, I didn't even know where to start. But as I dug deeper, I realized it's all about understanding your unique needs. It's like picking the perfect car: you need to consider not just what you want today but where you see yourself in a few years. Do you need a robust single-screw for simplicity or a versatile twin-screw for more complex recipes? Each choice affects the quality and efficiency of your production, much like deciding between an SUV or a sports car for your lifestyle. As technology advances, keeping an eye on innovations can give you an edge, ensuring your investment stands the test of time. It might seem overwhelming, but once you break it down, choosing an extruder becomes a journey of aligning technology with your vision.
Gli estrusori monovite sono più efficienti dal punto di vista energetico rispetto ai bivite.Falso
Twin-screw extruders are generally more energy-efficient due to better mixing.
Evaluating future expansion plans is crucial when choosing an extruder.Vero
Considering expansion ensures the extruder meets long-term production needs.
What Are the Different Types of Pet Food Extruders?
Ever wondered what goes into making your pet's favorite kibble?
There are three main types of pet food extruders: single-screw, twin-screw, and co-rotating twin-screw extruders. Each offers unique benefits in processing efficiency, flexibility, and product consistency, tailored to specific manufacturing needs.
Estrusori a vite singola
Let me take you back to when I first started exploring the pet food industry. I quickly learned that single-screw extruders were the backbone of dry pet food production. These machines operate with a simplicity that's hard to beat—imagine a giant pasta maker, tirelessly mixing and cooking ingredients to create that perfect kibble texture.
One of the primary advantages of single-screw extruders1 is their reliability. They require fewer parts and are easy to maintain, which was a godsend when I was just starting out and needed every bit of efficiency. However, their straightforward design means they have some limitations in terms of versatility, especially when dealing with more complex recipes.
Caratteristica | Single-Screw Extruder |
---|---|
Complexity | Basso |
Costo | Affordable |
Versatilità | Limitato |
Estrusori a doppia vite
As I delved deeper into pet food manufacturing, I encountered twin-screw extruders. These machines were a game changer for me. With two intermeshing screws, they offer a level of control and flexibility that single-screw extruders simply can't match. Whether I was working with sticky ingredients or needed precise moisture control, these machines delivered.
Il twin-screw technology2 felt like stepping into the future. It allowed me to experiment with high-moisture recipes and produce consistent quality, batch after batch. This versatility is crucial for those unique dietary products that our furry friends sometimes need.
Caratteristica | Twin-Screw Extruder |
---|---|
Complexity | Moderate to High |
Costo | Più alto |
Versatilità | Alto |
Estrusori bivite co-rotanti
Then, there was the discovery of co-rotating twin-screw extruders—a true marvel in pet food technology. These machines boast screws that rotate in the same direction, which amps up the mixing efficiency and heat transfer capabilities. This was particularly beneficial when I aimed for complex product designs that required intricate temperature control and ingredient blending.
Co-rotating twin-screws provide enhanced processing capabilities3, making them suitable for high-capacity production environments. Whether it's crafting gourmet treats or meeting high-capacity demands, they've been invaluable.
Caratteristica | Vite doppia co-rotante |
---|---|
Complexity | Alto |
Costo | Premium |
Versatilità | Very High |
Each of these extruders has played a significant role in my journey through the pet food industry. From the humble beginnings with single-screw machines to the advanced capabilities of co-rotating twin-screws, I've found the perfect blend of technology to cater to our beloved pets' dietary needs.
Single-screw extruders are cost-effective for dry pet food.Vero
Single-screw extruders are known for their simplicity and affordability.
Co-rotating twin-screw extruders have limited versatility.Falso
Co-rotating twin-screw extruders are highly versatile, ideal for complex products.
How Does Extruder Technology Impact Pet Food Quality?
Ever wondered how the crunch in your pet's kibble gets just right? Extruder technology might be the secret behind it!
Extruder technology impacts pet food quality by enhancing nutritional profiles, improving texture, and ensuring food safety. It allows manufacturers to produce diverse, high-quality pet foods efficiently and consistently.
Understanding Extruder Technology
Picture this: I'm standing in a bustling factory, surrounded by the hum of machines and the scent of fresh ingredients. It's here that extruder technology comes to life, transforming raw materials into pet food that meets the highest standards. At its core, this technology involves pushing material through a die to create specific shapes and textures. This process isn't just about aesthetics—it's about precision in cooking and nutrition, ensuring that each piece is crafted to perfection.
Potenziamento nutrizionale
I remember when my own dog, Max, struggled with a sensitive stomach. It was extrusion that came to the rescue. This process breaks down complex nutrients into simpler, more digestible forms. For pets like Max, this means easier digestion and better nutrient absorption.
Nutriente | Impact of Extrusion |
---|---|
Proteine | Improved digestibility and absorption |
Carboidrati | Conversion to simpler sugars for better digestion |
Vitamine | Stability can be compromised; careful formulation is necessary |
Imagine proteins becoming more bioavailable, and carbohydrates transforming into simpler sugars that pets can easily digest.
Texture and Palatability
Think back to when you tried a new snack—if it didn't feel right on your tongue, it probably wasn't a hit. The same goes for our pets. Extruders allow us to create a variety of textures, from crunchy to soft. This versatility isn't just about taste; it's about crafting diets that cater to specific health needs, like dental chews that support oral health.
Safety and Consistency
Nothing is more reassuring than knowing the food we give our pets is safe. The high temperatures during extrusion destroy harmful pathogens, ensuring every bite is as safe as it is tasty. Consistency is key too—it's about delivering the same quality with every batch, building trust with pet owners everywhere.
If you're curious about how extrusion affects nutritional profiles4 or how texture5 plays a role in pet food, dive into some scientific studies. They offer a wealth of insights into crafting diets that are both nutritious and enjoyable for our furry friends.
Extruder technology improves pet food digestibility.Vero
Extrusion breaks down complex nutrients, enhancing their digestibility.
Extruder technology reduces pet food safety by spreading pathogens.Falso
High temperatures in extrusion destroy harmful pathogens, ensuring safety.
Why is Production Capacity Important When Choosing an Extruder?
Have you ever thought about how the right extruder can revolutionize your pet food production?
Production capacity is key when selecting an extruder because it determines the volume of product that can be processed within a specific timeframe. It influences efficiency, cost-effectiveness, and overall production quality.
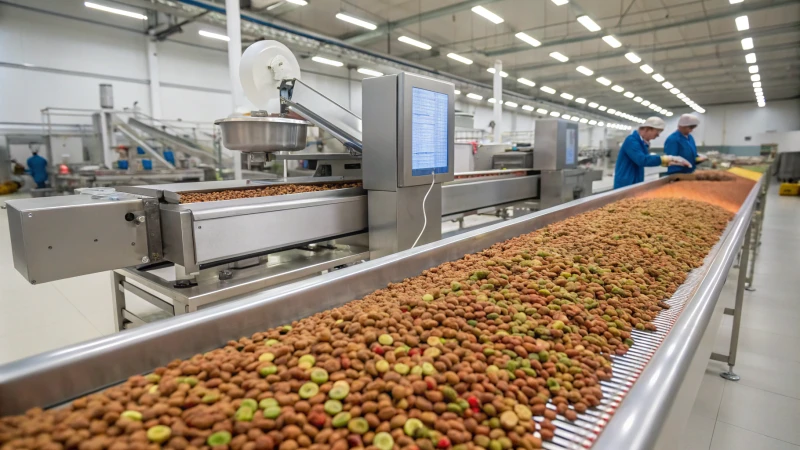
Understanding Production Capacity
When I first started exploring the world of extrusion, it struck me just how crucial production capacity was. Essentially, it's the maximum amount of output an extruder can churn out in a set period. For anyone in the pet food industry6, like myself, grasping and optimizing this capacity is absolutely vital to keeping up with market demand.
Efficienza ed economicità
Imagine being able to process larger batches without the hassle of constant stops and starts. That's what a higher production capacity brings to the table. It's not just about speed; it's about slashing downtime, which in turn cuts down per-unit production costs. For those of us facing hefty production demands7, machines with high capacities are game-changers, helping us meet orders swiftly.
Factor | Impact on Production |
---|---|
Alta capacità di produzione | Increases throughput |
Low Production Capacity | Limits batch size |
Impact on Output Quality
One thing I've learned is that production capacity isn't just about quantity—it's about quality too. A consistent capacity means each batch is uniform, which is essential for maintaining those high pet food quality8 standards we all strive for. Aligning capacity with our quality control measures ensures every product meets our expectations.
Aligning with Market Demand
Selecting an extruder with the right capacity isn't just smart—it's strategic. It allows us to pivot according to market demands without losing efficiency, keeping us agile and competitive. By syncing production capacity with market trends9, we can stay ahead of the curve, offering timely, tailored solutions that keep our clients happy and coming back for more.
High production capacity reduces per-unit costs.Vero
Larger batches lower downtime, thus reducing costs per unit.
Low production capacity increases product uniformity.Falso
Consistent high capacity ensures uniform quality across batches.
Why Does Energy Efficiency Matter in Extruder Selection?
When I first dove into the world of extrusion, I realized that energy efficiency wasn't just a buzzword—it's a game-changer.
Energy efficiency in extruder selection reduces operational costs, enhances productivity, and minimizes environmental impact. By choosing energy-efficient extruders, manufacturers can achieve sustainable production and comply with environmental regulations.
Understanding Energy Efficiency in Extrusion
Energy efficiency is like a secret weapon in the extrusion process. It’s the art of maximizing output while minimizing input—the very essence of doing more with less. Imagine you're driving a car that gets more miles per gallon; it’s similar but for manufacturing. The goal is to maintain product quality and output without the excess energy consumption that can weigh you down, especially as energy prices climb.
Benefits of Energy-Efficient Extruders
Thinking back to the time when I first upgraded my machinery, I remember the noticeable difference in our operating expenses.
Cost Savings: At first, it seemed like a steep investment, but over time, the reduced energy bills proved to be a game-changer. The savings began to add up, just like those small amounts of change you toss into a jar that eventually turn into something substantial.
Factor | Impatto |
---|---|
Energy Costs | Decrease |
Manutenzione | Potentially Reduced |
Production Output | Potentially Increased |
Environmental Impact: Let’s face it—we all want to do our part for the planet. By using less energy, our carbon footprint shrinks, and we meet sustainability targets with ease.
Operational Efficiency: I found that these machines not only consume less energy but also require less upkeep. The advanced technology and materials mean fewer breakdowns and longer lifespans, which is always a relief.
Factors to Consider When Selecting an Extruder
- Power Consumption: I always check how much juice a machine uses compared to what it outputs. It’s eye-opening how two similar machines can have such different efficiencies.
- Technology Integration: Look for features like variable frequency drives (VFDs) that adapt motor speed to match the workload. It’s like having cruise control for your extruder.
- Material Compatibility: Ensure your extruder can handle your specific materials without gulping down extra energy.
- Esigenze di produzione: I learned the hard way that a larger machine isn’t always better. If it's not fully utilized, you're essentially wasting energy.
- Manufacturing Standards: Trustworthy manufacturers often come with innovative designs that can enhance performance10.
Future Trends in Energy-Efficient Extrusion
The future is bright with innovations like IoT integration for real-time monitoring and adaptive control systems that tweak processes on the fly to save energy.
With environmental regulations tightening, choosing energy-efficient equipment from the get-go isn't just smart—it's essential.
Conclusione
Initially, the cost of energy-efficient extruders might make you hesitate. However, if my experience is anything to go by, the long-term benefits—cutting down on operating costs and reducing environmental impact—far outweigh the initial price tag. They're perfect for anyone looking to improve their sostenibilità11 efforts.
Energy-efficient extruders reduce operational costs.Vero
Lower energy use decreases costs, offsetting initial investment over time.
Energy-efficient extruders increase maintenance needs.Falso
They often require less maintenance due to advanced technology and materials.
How Can Advanced Features Enhance Production Processes?
Ever wondered how advanced features in machinery can turbocharge your production line and make your life a whole lot easier?
Advanced features in production machinery can significantly enhance manufacturing processes by improving efficiency, flexibility, and product quality. They enable manufacturers to adapt quickly to market demands and reduce operational costs.
Increased Efficiency through Automation
Let me share a story. Imagine you're running a bustling production line where every second counts. This was me a few years ago, juggling multiple tasks, trying to keep everything on track. Then automation came into the picture, and it felt like I had an extra pair of hands—or several! Advanced automation technologies12 took over the repetitive tasks, allowing my team and me to focus on more strategic work. Robotic arms became our unsung heroes, tirelessly working through the day and night, ensuring consistency and precision without breaking a sweat.
Enhanced Flexibility with Modular Systems
There was this one time when a sudden shift in market demand hit us like a storm. We needed to switch gears fast—really fast. Thanks to modular systems, we could reconfigure our production lines with ease. This ability to adapt was like having a superpower, especially in the ever-changing pet food industry. The flexibility we gained allowed us to meet consumer expectations for diverse product offerings without missing a beat.
Caratteristica | Benefici |
---|---|
Automazione | Increases speed and accuracy |
Modular Systems | Boosts adaptability and versatility |
Improved Quality Control with Real-Time Monitoring
Quality control used to feel like walking a tightrope. One slip, and the consequences could be severe. But real-time monitoring technologies changed that narrative for us. Now, we're able to track every step of our production process closely, spotting defects as they occur. This capability is vital, especially when dealing with high-quality standards demanded in industries like pet food. By integrating sensors and data analytics, we've reduced waste and maintained consistent quality, giving us peace of mind.
Cost Reduction via Predictive Maintenance
I remember the days of unexpected machinery breakdowns—those were tough times. However, embracing predictive maintenance turned things around. By leveraging data analytics to foresee equipment failures before they happened, we minimized unexpected downtimes and saved significantly on repair costs. Implementing predictive maintenance13 strategies not only extended our machinery's lifespan but also kept our production running smoothly.
Rapid Responsiveness to Market Demands
In today's fast-paced world, being responsive to market changes can make or break a business. With advanced features like real-time data analytics at our disposal, we found ourselves better equipped to adjust our production schedules and strategies swiftly. This capability allowed us to meet consumer demands more effectively, positioning us as a reliable player in the competitive landscape.
By embracing these advanced features, I've seen firsthand how manufacturers can thrive amidst challenges, ensuring efficiency, adaptability, and quality in their production processes. It's not just about keeping up; it's about setting the pace.
Automation always reduces error margins in production.Falso
While automation reduces errors, it can introduce new issues if not managed properly.
Modular systems boost adaptability in manufacturing.Vero
Modular systems allow reconfiguration for different products, enhancing flexibility.
What Should You Consider for Future Expansion Plans?
Thinking about expanding your business is thrilling yet daunting. But what should you really focus on to make it a success?
For successful expansion plans, consider market potential, financial stability, operational capacity, and strategic partnerships. These elements help ensure sustainable growth and effective risk management.
Market Potential Analysis
Diving into new markets feels like an adventure, doesn't it? I remember when I first looked at expanding my reach. Understanding the market potential14 was key. I had to dig deep into who my new customers might be, what they wanted, and who else was trying to win their business. That kind of homework helped me spot where I could really make a difference.
Financial Stability and Resources
You know, back when I was plotting my first big expansion, I realized something crucial—financial health was everything. Just like a well-oiled machine needs fuel, so does a growing business need a steady flow of resources. I took a long, hard look at my cash flow and margins and crafted a budget that made sure every penny would count toward growth.
Operational Capacity and Scalability
I had this moment when I looked at my bustling operation and thought, "Can we handle more?" It was time for an honest assessment. Was my infrastructure ready for more demand, or did it need an upgrade? It was like planning a road trip and making sure your car was ready to go the distance.
Operational Assessment Checklist
Factor | Current Status | Required Action |
---|---|---|
Infrastructure | Adeguato | Minor upgrades needed |
Human Resources | Understaffed | Hire additional staff |
Supply Chain | Efficiente | Maintain current systems |
Strategic Partnerships
There’s something special about teaming up with the right partners. When I first reached out to industry leaders for collaborations, it opened doors I hadn't even imagined. These partnerships were like adding rocket fuel to my growth plans, providing expertise and resources I wouldn't have had on my own.
Legal and Regulatory Compliance
Navigating the legal landscape can feel like learning a new language. Each new market had its own set of rules, and it was crucial to get them right from the start. This saved me from potential headaches down the line.
Risk Management and Contingency Planning
I can still recall the late nights spent mapping out what-if scenarios. A solid risk management strategy was my safety net—helping me anticipate bumps in the road before they became real issues.
Risk Management Framework
Risk Type | Probability | Impact Level | Mitigation Strategy |
---|---|---|---|
Market Volatility | Alto | Significant | Diversify market presence |
Financial Uncertainty | Medium | Moderato | Secure additional funding |
Operational Disruption | Basso | Alto | Develop backup systems |
By taking these steps, I laid down a path for expansion that felt both thrilling and secure. And sometimes, getting an outsider's perspective by engaging external advisors15 offered insights that were truly invaluable for our growth journey.
Market potential analysis reveals growth opportunities.Vero
Analyzing market potential helps identify high growth areas for expansion.
Financial stability is unnecessary for business expansion.Falso
Financial stability ensures resources are available for successful expansion.
Conclusione
Choosing a pet food extruder involves evaluating production capacity, technology type, energy efficiency, and future expansion plans to align with business goals and product needs.
-
Discover why single-screw extruders are a popular choice for pet food manufacturers, focusing on their cost-effectiveness and simplicity. ↩
-
Learn how twin-screw extruders enhance flexibility and precision in pet food production processes. ↩
-
Explore the advantages of co-rotating twin-screw extruders in achieving high efficiency and precise control. ↩
-
Exploring this will offer detailed insights into nutrient retention and enhancement during extrusion. ↩
-
Learning about texture's role can help you appreciate its importance in formulating appealing pet foods. ↩
-
Explore how production capacity impacts efficiency and cost in the pet food industry. ↩
-
Learn why matching extruder capacity to production demand is vital for manufacturers. ↩
-
Understand how production capacity can affect product uniformity and quality. ↩
-
Discover strategies for aligning production capabilities with market changes. ↩
-
Learn about advanced features that boost extruder efficiency and productivity. ↩
-
Discover strategies manufacturers use to enhance sustainability through energy-efficient technologies. ↩
-
Explore how automation can streamline production processes, increase efficiency, and reduce errors, making it essential for modern manufacturing. ↩
-
Discover how predictive maintenance can help prevent unexpected equipment failures, reduce costs, and improve overall production efficiency. ↩
-
Learn how to assess market potential to identify new growth opportunities effectively. ↩
-
Understand how external advisors can contribute valuable expertise to your expansion plans. ↩