Dog food production is a complex process that requires specialized machinery to ensure high-quality, nutritious, and safe products. Whether producing dry kibble, wet food, or raw diets, manufacturers rely on various machines to handle ingredient processing, mixing, extrusion, drying, packaging, and quality control. Using the right equipment is essential for efficiency, consistency, and meeting industry standards.
The primary machines used in dog food production include extruders, grinders, mixers, dryers, and packaging systems. These machines work together to process raw ingredients, form the desired dog food shape and texture, and ensure proper storage and distribution. Each type of dog food requires specific machinery and processing methods to maintain nutritional value and palatability.
To better understand how dog food is manufactured, let’s explore the key machines used in the production process.
What Are the Essential Machines for Making Dry Dog Food (Kibble)?
Manufacturing dry dog food (kibble) requires a carefully designed production process that ensures nutritional balance, texture, and shelf stability. Without the right equipment, manufacturers may face issues such as inconsistent kibble quality, inefficient production, or high waste. Investing in the right machines is crucial for producing high-quality pet food that meets industry standards and consumer expectations.
The essential machines for making dry dog food (kibble) include raw material processing equipment (grinders, mixers), an extruder for cooking and shaping, a dryer for moisture removal, a coating machine for adding fats and flavors, and a packaging system for final product distribution. Each machine plays a critical role in ensuring kibble consistency, safety, and nutritional value.
To better understand the process, let’s explore each essential machine in detail and how they contribute to high-quality kibble production.
1. Raw Material Processing Equipment
The first step in kibble production involves processing the raw ingredients, including meats, grains, and supplements.
1.1 Grinding Machine (Hammer Mill or Pulverizer)
- Breaks down raw materials like corn, wheat, and meat by-products into a fine powder.
- Ensures consistency in ingredient size for better mixing and extrusion.
- Reduces the risk of clogging in later stages.
1.2 Batch or Continuous Mixer
- Blends dry and wet ingredients uniformly.
- Ensures proper distribution of nutrients, flavors, and additives.
- Some advanced mixers have vacuum or heating functions for better homogenization.
Fitur | Hammer Mill | Pulverizer |
---|---|---|
Grinding Fineness | Medium | Very Fine |
Processing Speed | Fast | Sedang |
Suitable for | Grains, coarse material | Soft ingredients |
2. Extrusion System – The Heart of Kibble Production
Extrusion is the most critical step in making dry dog food. This process cooks the ingredients using heat and pressure, shapes them, and expands the final product.
2.1 Twin-Screw Extruder (Recommended)
- Uses two interlocking screws for better mixing, cooking, and forming.
- Higher efficiency and flexibility for producing different kibble sizes.
- Suitable for high-fat and high-moisture formulations.
2.2 Single-Screw Extruder (Basic Option)
- Uses one screw for processing and shaping kibble.
- More affordable but less versatile.
Fitur | Twin-Screw Extruder | Single-Screw Extruder |
---|---|---|
Processing Speed | Faster | Slower |
Kibble Consistency | Lebih tinggi | Sedang |
Nutrient Retention | Better | Lebih rendah |
Suitable for | Complex recipes | Basic formulations |
3. Drying and Cooling Systems
After extrusion, kibble contains moisture that must be reduced for storage stability.
3.1 Belt Dryer (Hot Air Circulation)
- Uses conveyor belts and hot air to dry kibble gradually.
- Ensures even moisture removal to prevent spoilage.
3.2 Rotary Drum Dryer
- Suitable for larger-scale production.
- Uses rotating motion for better heat distribution.
After drying, the kibble must be cooled before further processing.
3.3 Counterflow Cooler
- Ensures kibble reaches a stable temperature before packaging.
- Prevents condensation that could lead to mold growth.
Fitur | Belt Dryer | Rotary Drum Dryer |
---|---|---|
Drying Efficiency | Tinggi | Very High |
Space Requirement | Sedang | Large |
Konsumsi Energi | Sedang | Lebih tinggi |
4. Coating and Flavoring Machine
Once the kibble is dried, fats, vitamins, and flavor enhancers are applied.
4.1 Vacuum Coater (Recommended)
- Ensures deep penetration of liquid additives (oils, vitamins).
- Enhances palatability and nutrition.
4.2 Drum Coater
- Sprays fat and flavoring onto the surface of kibble.
- Suitable for budget-friendly production.
Fitur | Vacuum Coater | Drum Coater |
---|---|---|
Coating Efficiency | Tinggi | Sedang |
Nutrient Retention | Better | Lebih rendah |
Suitable for | Premium kibble | Standard kibble |
5. Packaging and Weighing Systems
Final packaging determines product shelf life, freshness, and marketability.
5.1 Automatic Weighing & Bagging Machine
- Accurately measures and fills bags to minimize waste.
- Ensures uniform weight distribution in each package.
5.2 Vertical Form Fill Seal (VFFS) Machine
- Creates bags, fills them, and seals automatically.
- Ideal for large-scale production.
5.3 Metal Detector & Quality Control
- Ensures no metal contaminants are present.
- Meets safety regulations.
Fitur | Automatic Weighing | VFFS Machine |
---|---|---|
Kecepatan | Tinggi | Very High |
Accuracy | Precise | Sedang |
Suitable for | Mid-to-large production | Large-scale |
To set up a dry dog food manufacturing line, you need essential machines that handle each stage of production efficiently. From grinding and mixing raw ingredients to extrusion, drying, coating, and packaging, each machine plays a vital role in ensuring consistent kibble quality.
Essential Machines for Dry Dog Food Production:
- Grinding Machine (Hammer Mill/Pulverizer) – Prepares raw ingredients.
- Pengaduk – Blends ingredients uniformly.
- Extruder (Twin-Screw or Single-Screw) – Cooks and shapes kibble.
- Dryer & Cooler – Removes moisture and stabilizes kibble.
- Coater (Vacuum or Drum) – Adds essential nutrients and flavors.
- Packaging System (Weighing, Sealing, and Quality Control) – Ensures product shelf stability and safety.
Investing in high-quality machinery optimizes production efficiency, improves kibble consistency, and ensures compliance with pet food industry standards. By selecting the right equipment, manufacturers can produce premium kibble that meets market demands while maintaining cost efficiency.
Looking for Reliable Dog Food Processing Equipment?
We provide high-performance kibble production machines tailored to your manufacturing needs. Hubungi kami hari ini to discuss custom solutions for your pet food business! 🚀
What Machines Are Used for Wet and Canned Dog Food Production?
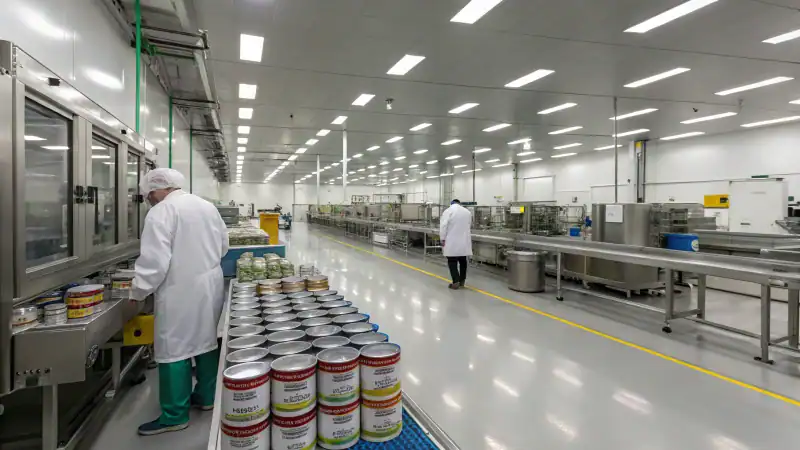
Producing wet and canned dog food requires specialized machinery to ensure consistent quality, safety, and efficiency. Without the right equipment, manufacturers face contamination risks, inconsistent textures, and inefficient processing. This can lead to product recalls, loss of customer trust, and compliance issues with food safety regulations. The right machines streamline production, reduce waste, and maintain the nutritional integrity of pet food.
Key Machines Used in Wet and Canned Dog Food Production
The primary machines used in wet and canned dog food production include mixing systems, cooking and sterilization units, filling and sealing equipment, and packaging machinery. These machines work together to ensure uniform mixing, proper cooking, airtight sealing, and compliance with food safety standards.
Manufacturers must invest in reliable, high-capacity equipment to maintain efficiency and product consistency. Understanding the role of each machine helps optimize the production line and ensures that pet food meets industry standards.
1. Raw Material Handling and Preparation Equipment
Ingredient Batching Systems
Batching systems measure and dispense precise quantities of raw ingredients, including meats, grains, vitamins, and minerals. Automated batching ensures accuracy and consistency in every batch of wet dog food.
Common Equipment:
- Ingredient silos and storage tanks – Store raw materials such as meat slurries, fats, and powders.
- Weighing and dosing systems – Ensure precise ingredient proportions.
- Meat grinders and choppers – Process raw meat into fine or coarse particles for uniform texture.
Grinding and Emulsifying Machines
These machines break down raw meat, vegetables, and grains into a smooth paste, forming the base for wet dog food.
Common Equipment:
- Meat grinders – Reduce raw meat into small, uniform pieces.
- Emulsifiers – Further refine the mixture for a consistent texture.
- Colloid mills – Homogenize fat, water, and protein components.
2. Cooking and Mixing Equipment
High-Temperature Cooking Systems
Wet dog food must be cooked to eliminate pathogens while retaining nutritional value.
Common Equipment:
- Steam cookers – Cook ingredients at controlled temperatures to prevent nutrient loss.
- Vacuum kettles – Cook at lower temperatures to preserve flavors.
- Extruders – Process meat, starches, and additives under pressure for uniform cooking.
Hydraulic and Ribbon Blenders
Mixing is crucial to ensure that flavors, nutrients, and moisture levels remain uniform.
Common Equipment:
- Ribbon blenders – Mix dry and wet ingredients thoroughly.
- Vacuum mixers – Remove air bubbles and improve product consistency.
- Homogenizers – Ensure a smooth final texture.
3. Can Filling and Sealing Equipment
Filling Machines
Wet dog food must be filled into cans, pouches, or trays with precision to avoid contamination and weight inconsistencies.
Common Equipment:
- Piston fillers – Dispense consistent portions into cans or trays.
- Vacuum fillers – Remove excess air to maintain product integrity.
- Auger fillers – Used for semi-solid pastes.
Sealing and Closing Systems
Airtight sealing prevents spoilage and ensures a long shelf life.
Common Equipment:
- Can seamers – Seal metal cans using double seams.
- Heat sealers – Seal plastic pouches and trays.
- Induction sealers – Provide hermetic sealing for added protection.
4. Sterilization and Cooling Systems
Retort Processing (Autoclave Sterilization)
Canned wet dog food requires sterilization to prevent bacterial growth.
Common Equipment:
- Retort machines – High-pressure steam sterilization.
- Water spray autoclaves – Ensure uniform heat distribution.
Cooling Conveyors
After sterilization, the cans must be cooled gradually to prevent texture degradation.
Common Equipment:
- Water cooling tunnels – Cool products evenly.
- Air blast coolers – Rapid cooling to safe storage temperatures.
5. Labeling and Packaging Equipment
Labeling Systems
After sealing, labels are applied for branding and regulatory compliance.
Common Equipment:
- Automatic label applicators – Place labels precisely.
- Inkjet coders – Print batch numbers and expiration dates.
Final Packaging and Palletizing
Cans and pouches must be packed into boxes for transportation.
Common Equipment:
- Cartoning machines – Package cans into boxes.
- Robotic palletizers – Stack and wrap finished products.
Comparison of Wet Dog Food Processing Equipment
Machine Type | Fungsi | Key Benefit |
---|---|---|
Batching System | Measures ingredients accurately | Consistency in formulation |
Grinding Machine | Processes meat and grains into a paste | Uniform texture |
Cooking System | Cooks ingredients at precise temperatures | Retains nutrition and flavor |
Filling Machine | Dispenses food into cans/pouches | Ensures portion accuracy |
Sealing Machine | Creates airtight packaging | Extends shelf life |
Retort Machine | Sterilizes to prevent bacteria | Food safety compliance |
Cooling System | Lowers temperature before storage | Prevents spoilage |
Labeling Machine | Prints branding and regulatory info | Compliance and consumer appeal |
Choosing the Right Equipment for Wet Dog Food Production
Investing in high-quality machines ensures efficient, safe, and consistent wet dog food production. Manufacturers must select equipment based on production scale, ingredient requirements, and regulatory standards. Advanced automation reduces labor costs, minimizes contamination risks, and improves overall product quality.
For expert guidance on selecting the right machines for your pet food production line, contact us today!
What Equipment is Needed for Raw and Freeze-Dried Dog Food Production?
Producing high-quality raw and freeze-dried dog food requires specialized equipment to ensure efficiency, safety, and compliance with food industry regulations. The pet food industry is growing rapidly, and pet owners increasingly demand premium, high-nutrient, and minimally processed food for their pets. Without the right machinery, production can be inefficient, costly, and may fail to meet health and safety standards.
To produce high-quality raw and freeze-dried dog food, manufacturers need industrial meat processing equipment, freeze-drying systems, mixing and blending machines, quality control tools, and specialized packaging solutions. These machines ensure efficiency, consistency, and compliance with pet food safety standards.
Raw and freeze-dried pet food production involves several steps, including ingredient preparation, grinding, blending, freezing, drying, and packaging. Using the right machinery ensures that the final product retains its nutritional value, texture, and safety standards. Below, we explore the key equipment required for raw and freeze-dried dog food production.
1. Ingredient Preparation Equipment
Before processing begins, raw ingredients such as meats, vegetables, and supplements need to be prepared properly.
Meat Processing Equipment
Equipment | Fungsi |
---|---|
Meat Grinder | Breaks down raw meat and bones into a fine, uniform texture. Industrial grinders with bone-crushing capabilities are essential. |
Meat Slicer & Dicer | Cuts meat into smaller portions before grinding or blending. |
Bone Saw | Used for cutting large bones into manageable pieces. |
Blanching Machine | Used to pre-treat vegetables by briefly exposing them to hot water or steam to preserve color and nutrients. |
Mixing & Blending Machines
Equipment | Fungsi |
---|---|
Ribbon Blender | Ensures even mixing of ground meat, vegetables, vitamins, and minerals. |
Vacuum Mixer | Removes air during the mixing process to prevent oxidation and preserve freshness. |
Emulsifier | Helps in creating a smooth texture by breaking down fats and proteins uniformly. |
2. Freezing & Freeze-Drying Equipment
For freeze-dried pet food, a freezing and dehydration system is essential.
Freezing Equipment
Equipment | Fungsi |
---|---|
Blast Freezer | Rapidly freezes ingredients to maintain freshness and lock in nutrients. |
Plate Freezer | A space-efficient freezing method that quickly freezes large batches of food. |
Freeze-Drying Machines
Equipment | Fungsi |
---|---|
Vacuum Freeze Dryer | Slowly removes moisture from frozen food while preserving nutrients and texture. |
Lyophilization Chamber | Large-scale freeze-drying chamber for high-volume production. |
Vacuum Pump | Creates a low-pressure environment inside the freeze-drying chamber. |
3. Quality Control & Food Safety Equipment
Maintaining quality and safety is crucial in pet food production.
Equipment | Fungsi |
---|---|
Metal Detector | Ensures no metal contaminants are present in the final product. |
X-ray Machine | Detects foreign objects and ensures product safety. |
Moisture Analyzer | Ensures proper moisture content in freeze-dried food. |
Microbiological Testing Kits | Tests for bacteria, pathogens, and contaminants. |
4. Packaging & Labeling Equipment
Once the product is ready, efficient packaging is necessary to maintain shelf life and ensure easy distribution.
Packaging Machinery
Equipment | Fungsi |
---|---|
Vacuum Sealer | Removes air from packaging to prevent spoilage. |
Modified Atmosphere Packaging (MAP) System | Increases shelf life by replacing oxygen with nitrogen. |
Pouch Filling Machine | Automatically fills bags with product and seals them. |
Cartoning Machine | Places filled packages into boxes for shipping. |
Labeling & Date Coding
Equipment | Fungsi |
---|---|
Automated Labeling Machine | Applies product labels accurately and consistently. |
Inkjet Printer | Prints expiration dates and batch codes. |
5. Additional Equipment for Large-Scale Production
For manufacturers producing large batches of raw and freeze-dried dog food, additional automation and processing equipment can improve efficiency.
Equipment | Fungsi |
---|---|
Conveyor System | Automates the movement of raw materials and finished products. |
Industrial Dehydrator | Alternative to freeze-drying for making air-dried pet food. |
Cold Storage Units | Preserves raw ingredients before processing. |
Water Filtration System | Ensures clean, high-quality water for food production. |
Investing in the right equipment is crucial for producing safe, high-quality raw and freeze-dried dog food. The process requires a combination of grinding, blending, freezing, freeze-drying, and packaging technologies to maintain the food's nutritional integrity and safety. Manufacturers looking to enter this growing market should prioritize efficiency, automation, and food safety compliance to stay competitive.
Looking to Set Up a Pet Food Production Facility?
If you need guidance on selecting the right machinery or setting up a raw and freeze-dried pet food production line, contact us today for expert advice and customized solutions. 🚀
How Do Extruders Work in Dog Food Manufacturing?
Dog food manufacturing involves several complex processes to ensure high-quality, nutritionally balanced kibble. One of the most critical steps in this process is extrusion. Without an efficient extruder, dog food production would be inconsistent, affecting both texture and digestibility. Understanding how extruders work can help manufacturers optimize production and ensure pet food meets industry standards.
Extruders in dog food manufacturing function as high-pressure cooking machines that blend and shape ingredients into uniform kibbles. The process involves mixing, shearing, heating, and expanding the raw materials under precise conditions. The extrusion process enhances digestibility, improves nutrient retention, and ensures a consistent product shape and texture.
Dog food extrusion is a highly controlled process that requires a combination of mechanical, thermal, and chemical forces. It is essential for producing dry and semi-moist pet foods with long shelf life and optimal nutritional quality. Below, we explore the working principles of extruders, their types, key benefits, and how they impact dog food quality.
1. What Is Extrusion in Dog Food Manufacturing?
Extrusion is a high-temperature, high-pressure process used to produce dry dog food (kibble) and some semi-moist pet foods. It involves forcing a mixture of ingredients through a specialized machine called an extruder. This process ensures consistency, improves digestibility, and eliminates harmful pathogens.
1.1 Basic Working Principle of Extrusion
The extrusion process includes several key steps:
- Pencampuran Bahan: Dry and wet ingredients, such as grains, protein sources, vitamins, and minerals, are combined into a uniform mixture.
- Preconditioning: Steam and water are added to the mixture to preheat and hydrate the ingredients.
- Extrusion Cooking: The preconditioned mixture enters the extruder, where it is exposed to intense heat and pressure.
- Shearing and Expansion: Inside the extruder barrel, screws shear and press the mixture through a die, forming the kibble shape.
- Drying & Cooling: The extruded kibbles are dried to reduce moisture and then cooled before further processing.
- Coating & Packaging: A fat or flavor coating is applied to enhance palatability before final packaging.
1.2 Extrusion Temperature & Pressure Control
Parameter | Value Range | Tujuan |
---|---|---|
Suhu | 90°C – 160°C | Kills bacteria, gelatinizes starches |
Pressure | 30 – 50 bar | Ensures uniform kibble texture |
Kadar air | 18% – 30% (before drying) | Facilitates expansion and cooking |
2. Types of Extruders Used in Dog Food Manufacturing
There are two main types of extruders used in pet food production: single-screw and twin-screw extruders. Each type has distinct advantages depending on the type of dog food being produced.
2.1 Single-Screw Extruders
Single-screw extruders are widely used in dry dog food manufacturing due to their simplicity and cost-effectiveness.
Advantages of Single-Screw Extruders
- Cost-efficient and energy-saving
- Suitable for standard dry kibble production
- Easier maintenance with fewer moving parts
Disadvantages
- Less flexibility in ingredient formulation
- Limited ability to handle high-fat content ingredients
2.2 Twin-Screw Extruders
Twin-screw extruders offer greater versatility and are used for specialized formulations, including grain-free or high-meat-content kibbles.
Advantages of Twin-Screw Extruders
- Can handle a wider range of raw materials
- Better control over texture and density
- Improved cooking efficiency
Disadvantages
- Higher operational and maintenance costs
- More complex machine design requiring skilled operation
Fitur | Single-Screw Extruder | Twin-Screw Extruder |
---|---|---|
Biaya | Lebih rendah | Lebih tinggi |
Ingredient Flexibility | Terbatas | Tinggi |
Processing Speed | Sedang | Tinggi |
3. Key Benefits of Extrusion in Dog Food Manufacturing
Extrusion provides multiple benefits that improve the quality and safety of dog food.
3.1 Nutritional Advantages
- Improved Digestibility: Cooking at high temperatures gelatinizes starches, making them easier for dogs to digest.
- Nutrient Retention: Controlled temperature prevents excessive nutrient loss.
- Fat Coating Enhancement: Allows for post-extrusion application of fats and flavors, enhancing palatability.
3.2 Food Safety Benefits
- Pathogen Elimination: The high temperature kills harmful bacteria like Salmonella and E. coli.
- Moisture Control: Reducing moisture prevents mold growth and extends shelf life.
3.3 Efficiency and Scalability
- High Production Speed: Continuous processing increases efficiency.
- Customizable Shapes and Sizes: Dies can be changed to produce different kibble shapes.
Manfaat | Impact on Dog Food Quality |
---|---|
Pathogen Reduction | Eliminates bacteria and mold |
Digestibility | Improves nutrient absorption |
Shape Consistency | Ensures uniform kibble sizes |
4. Challenges and Solutions in Extrusion
Despite its benefits, extrusion has some challenges that manufacturers must address.
4.1 Common Challenges
- Ingredient Sensitivity: Some vitamins degrade under high temperatures.
- Extruder Wear and Tear: High-pressure operation leads to mechanical wear.
- Fat Absorption Issues: Over-processing can reduce fat coating efficiency.
4.2 Solutions
- Use of Co-Extrusion: Allows vitamins to be added post-extrusion.
- Regular Maintenance: Prevents extruder breakdowns.
- Controlled Processing Conditions: Optimizes fat absorption without over-processing.
Challenge | Solution |
---|---|
Vitamin Degradation | Post-extrusion coating process |
Wear and Tear | Routine maintenance schedule |
Fat Absorption | Optimal drying and cooling process |
Kesimpulan
Extruders are the backbone of dog food manufacturing, ensuring efficient, safe, and high-quality kibble production. By understanding how extruders work and optimizing processing parameters, pet food manufacturers can improve digestibility, enhance nutrition, and produce a consistent product. Choosing the right extruder—whether single or twin-screw—depends on the formulation and production needs.
For pet food manufacturers looking to enhance production efficiency and product quality, investing in advanced extrusion technology is essential. If you're interested in upgrading your extrusion system or need expert guidance, contact us today for professional solutions!
What Role Do Drying and Cooling Systems Play in Dog Food Production?
In the pet food industry, the quality, safety, and shelf life of dog food are heavily influenced by drying and cooling processes. If these steps are not properly executed, dog food can suffer from mold growth, reduced nutritional value, and textural inconsistencies. Inefficient drying can lead to excess moisture, causing bacterial contamination, while improper cooling may result in condensation and spoilage. To ensure product safety, extended shelf life, and optimal nutrient retention, manufacturers rely on advanced drying and cooling technologies.
Drying and cooling systems play a crucial role in dog food production by removing moisture, stabilizing the product, preventing microbial growth, and enhancing texture and shelf life. These systems ensure consistent product quality, efficient energy use, and compliance with industry safety standards.
To fully appreciate their impact, we need to explore the fundamental mechanisms behind these systems and how they contribute to high-quality pet food production.
Understanding the Drying Process in Dog Food Production
The drying phase is one of the most essential stages in dog food manufacturing. It primarily applies to kibble, where moisture reduction is vital for product stability. The primary objectives of drying include:
- Moisture Reduction: Reducing moisture content to an optimal level (usually below 10%) to prevent bacterial and fungal growth.
- Nutrient Preservation: Protecting sensitive vitamins and proteins from heat degradation.
- Texture Enhancement: Achieving the right crunchiness and firmness for palatability.
- Extended Shelf Life: Ensuring longer storage without spoilage.
Types of Drying Systems Used in Dog Food Manufacturing
Several drying methods are commonly employed in commercial dog food production:
Metode Pengeringan | Process Description | Keuntungan | Disadvantages |
---|---|---|---|
Convection Drying | Hot air circulates through the kibble to remove moisture. | Uniform drying, energy-efficient | Potential for nutrient loss due to high temperatures |
Vacuum Drying | Kibble is dried under low pressure, lowering the boiling point of water. | Retains more nutrients, prevents oxidation | Expensive and complex machinery |
Freeze Drying | Food is frozen and then dehydrated under vacuum. | Retains nutrients and flavor, lightweight product | High production costs |
Infrared Drying | Uses infrared radiation to penetrate kibble and evaporate moisture. | Fast drying, energy-efficient | Requires precise control to avoid over-drying |
Critical Parameters in the Drying Process
Proper control over drying parameters ensures food safety and consistency:
- Temperature Control: Prevents over-drying, which can cause brittleness.
- Humidity Levels: Ensures even moisture removal to prevent mold growth.
- Airflow Management: Maintains uniform drying and prevents uneven texture.
- Dwell Time: Determines how long the kibble stays in the dryer for optimal moisture reduction.
The Importance of Cooling Systems in Dog Food Manufacturing
After drying, the kibble or pet food must be cooled properly to prevent condensation, which can lead to mold growth. The cooling stage ensures:
- Prevention of Moisture Reabsorption: If kibble is not cooled before packaging, it can absorb moisture from the surrounding air, reducing shelf stability.
- Texture and Structural Integrity: Helps maintain crunchiness by stabilizing fats and proteins.
- Improved Handling and Packaging Efficiency: Reduces heat-related packaging issues.
Common Cooling Methods Used in Dog Food Production
There are several cooling systems used in the industry, each with specific benefits:
Cooling System | Process Description | Manfaat | Limitations |
---|---|---|---|
Forced Air Cooling | Kibble is cooled using controlled air circulation. | Quick cooling, prevents condensation | Requires precise airflow control |
Fluidized Bed Cooling | Uses a stream of air to keep kibble suspended while cooling. | Uniform cooling, enhances crispiness | High energy consumption |
Evaporative Cooling | Water mist and air help in rapid cooling. | Energy-efficient, gentle on food | Not suitable for all types of kibble |
Optimizing Cooling Parameters
The effectiveness of cooling depends on various parameters:
- Airflow Velocity: Ensures rapid and even cooling.
- Temperature Control: Maintains the ideal final temperature before packaging.
- Time Duration: Prevents over-cooling, which may affect the texture.
The Impact of Drying and Cooling on Product Quality and Safety
1. Shelf Life and Microbial Safety
- Proper drying reduces the water activity (Aw) in dog food, limiting the growth of bacteria and fungi.
- Effective cooling prevents condensation, which can create a breeding ground for microbes.
2. Nutritional Integrity
- Excessive heat during drying can degrade vitamins such as B-complex dan Vitamin C.
- Optimized drying and cooling preserve essential nutrients, ensuring a balanced diet for dogs.
3. Energy Efficiency and Cost Savings
- Advanced drying systems utilize heat recovery dan automated controls to optimize energy use.
- Efficient cooling reduces processing times and improves production throughput.
4. Regulatory Compliance
Manufacturers must adhere to strict FDA and AAFCO guidelines for pet food production. Drying and cooling systems help in:
- Meeting moisture content regulations to ensure safety.
- Preventing contamination risks related to improper cooling.
Future Trends in Drying and Cooling Technologies for Dog Food
As pet food production evolves, manufacturers are adopting innovative drying and cooling solutions to improve efficiency and sustainability.
Emerging Technology | Deskripsi | Industry Benefit |
---|---|---|
Solar-Assisted Drying | Uses solar energy to supplement conventional dryers. | Reduces energy costs and carbon footprint. |
AI-Optimized Drying Systems | Machine learning algorithms adjust drying parameters in real-time. | Enhances precision, minimizes nutrient loss. |
Cryogenic Cooling | Uses liquid nitrogen or CO₂ to rapidly cool kibble. | Improves efficiency and prevents lipid oxidation. |
Kesimpulan
Drying and cooling systems play a critical role in ensuring the quality, safety, and shelf life of dog food. By optimizing these processes, manufacturers can maintain the nutritional integrity, palatability, and microbial stability of pet food products. As technology advances, adopting energy-efficient and AI-driven drying and cooling systems will further enhance production capabilities while ensuring pet health and food safety.
Looking to optimize your pet food manufacturing process? Contact us today to explore the latest drying and cooling solutions for your production needs!
What Are the Key Packaging Machines Used in Dog Food Factories?
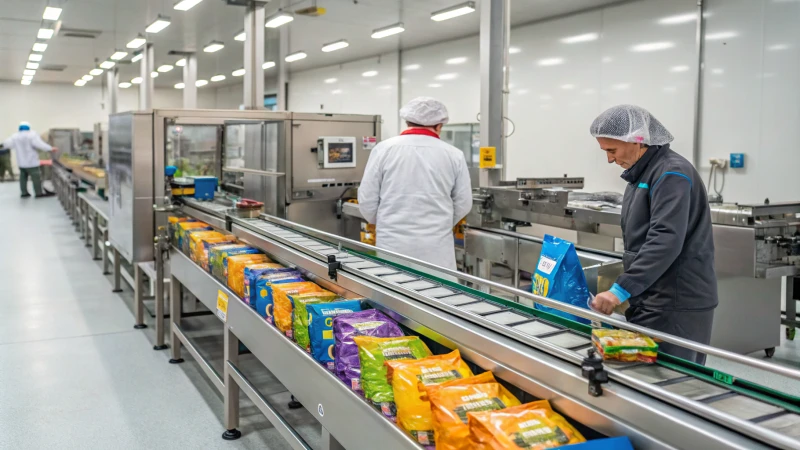
The pet food industry, particularly dog food manufacturing, relies on advanced packaging solutions to ensure product quality, extended shelf life, and market competitiveness. Inefficient packaging can lead to product contamination, spoilage, and reduced consumer trust. Therefore, modern dog food factories utilize various packaging machines designed for efficiency, precision, and hygiene.
The key packaging machines used in dog food factories include vertical form-fill-seal (VFFS) machines, multihead weighers, vacuum sealers, can seamers, robotic palletizers, and labeling machines. These machines help in automating the packaging process, ensuring accurate portioning, sealing, and branding of dog food products.
Dog food packaging varies from dry kibble to wet canned food, each requiring different machinery. The right choice of packaging equipment ensures safety, efficiency, and compliance with industry standards.
1. Vertical Form-Fill-Seal (VFFS) Machines
VFFS machines are essential for packaging dry dog food in flexible bags. These machines:
- Form bags from a roll of film
- Accurately fill them with dog food
- Seal them securely to maintain freshness
- Offer customization for different bag sizes and styles (pillow bags, gusseted bags, quad-seal bags)
Fitur | Deskripsi |
---|---|
Kecepatan | Up to 100 bags per minute |
Material | Works with plastic films, laminates, or paper-based materials |
Fleksibilitas | Supports resealable zippers, tear notches, and different bag shapes |
2. Multihead Weighers
Multihead weighers ensure precise portioning of dog food, reducing waste and maximizing efficiency. These weighers:
- Use multiple weighing heads to distribute kibble into packaging
- Work in conjunction with VFFS or other filling machines
- Maintain accuracy within fractions of a gram
3. Vacuum Sealers
Vacuum sealing is crucial for extending shelf life and preserving the freshness of dog food. These machines:
- Remove excess air from packages
- Prevent oxidation and bacterial growth
- Maintain product integrity during transportation and storage
Type | Fungsi |
---|---|
Chamber Vacuum Sealer | Best for bulk packaging of dog food |
External Vacuum Sealer | Used for pre-formed pouches with smaller volumes |
4. Can Seamers
For wet dog food, can seamers play a crucial role. These machines:
- Hermetically seal metal cans with dog food
- Prevent contamination and leakage
- Support high-speed production lines
Fitur | Deskripsi |
---|---|
Sealing Type | Double or triple seam for airtight sealing |
Kapasitas | Handles up to 600 cans per minute |
Compatibility | Works with various can sizes |
5. Robotic Palletizers
Robotic palletizers automate the stacking of packaged dog food onto pallets for shipping. These machines:
- Improve efficiency in warehouse operations
- Reduce labor costs and manual errors
- Handle heavy loads with precision
6. Labeling and Coding Machines
Proper labeling is essential for regulatory compliance and branding. Labeling machines:
- Apply stickers or print labels directly onto packaging
- Include batch codes, expiration dates, and barcodes
- Use thermal transfer or inkjet technology for durability
Modern dog food factories rely on a range of packaging machines to maintain efficiency, accuracy, and product integrity. Choosing the right packaging equipment ensures compliance with safety standards, extends shelf life, and enhances brand appeal.
Hubungi Kami
Looking for high-quality dog food packaging machines? Contact us today for expert guidance and customized solutions.
How Do Quality Control Machines Ensure Dog Food Safety?
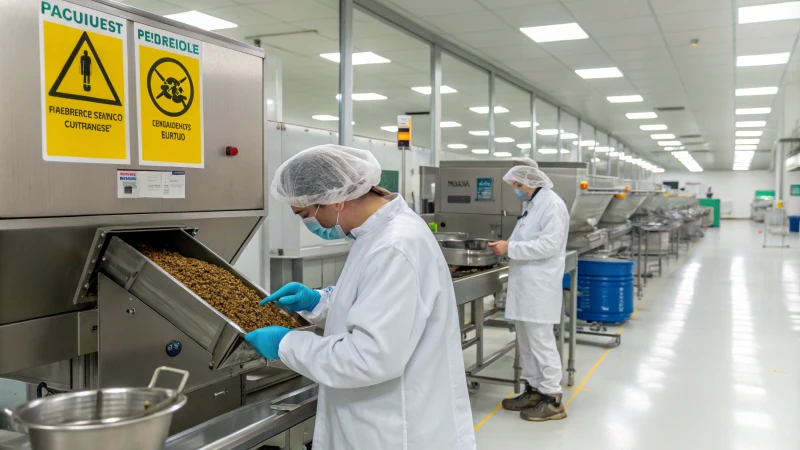
Dog food safety is a critical concern for manufacturers and consumers alike. Contaminated or substandard pet food can lead to serious health risks for pets, resulting in recalls, legal issues, and damage to a brand’s reputation. To mitigate these risks, modern dog food factories rely on advanced quality control machines that detect contaminants, ensure proper composition, and verify packaging integrity.
Quality control machines ensure dog food safety by detecting foreign contaminants, verifying ingredient composition, maintaining weight accuracy, and ensuring proper packaging integrity. Technologies like X-ray inspection, metal detection, near-infrared (NIR) spectroscopy, and seal testers help maintain compliance with industry regulations and prevent contamination.
Given the stringent safety requirements in the pet food industry, quality control machines play a crucial role in safeguarding dog food products from contamination, spoilage, and improper labeling.
1. Metal Detectors: Preventing Hazardous Contaminants
Metal detectors are essential in dog food production, as they help remove metal contaminants that could harm pets or damage manufacturing equipment. These machines:
- Detect ferrous, non-ferrous, and stainless steel contaminants
- Operate with high sensitivity to ensure food safety
- Work at different stages of production (raw material, in-process, and final packaging)
Metal Detector Type | Fitur |
---|---|
Conveyor Metal Detector | Scans food passing through on a conveyor belt |
Gravity-Fed Metal Detector | Ideal for detecting contaminants in bulk dry dog food |
Pipeline Metal Detector | Used for inspecting wet or semi-liquid dog food |
2. X-ray Inspection Systems: Detecting Non-Metal Contaminants
X-ray inspection is a more advanced technology that can identify foreign objects beyond metal contamination, such as:
- Glass shards
- Hard plastics
- Bone fragments
- Dense rubber materials
These machines ensure dog food is free from harmful materials while maintaining the integrity of sealed packages.
Fitur | Deskripsi |
---|---|
Detection Capability | Identifies foreign objects inside sealed packages |
Kompatibilitas Material | Works with metalized film packaging and glass containers |
Precision | Detects small particles as tiny as 0.3mm |
3. Near-Infrared (NIR) Spectroscopy: Ensuring Nutrient Consistency
NIR spectroscopy ensures that dog food contains the right balance of nutrients, proteins, and fats. This technology:
- Analyzes the chemical composition of dog food in real-time
- Detects deviations in ingredient ratios
- Helps maintain consistency in different production batches
Nutrient Parameter | Measured By NIR |
---|---|
Protein Content | ✓ |
Fat Percentage | ✓ |
Moisture Levels | ✓ |
Fiber Content | ✓ |
4. Checkweighers: Ensuring Accurate Weight and Portioning
Checkweighers play a vital role in maintaining compliance with weight regulations and ensuring accurate portioning of dog food. These machines:
- Weigh products at high speeds
- Remove underweight or overweight packages from the production line
- Prevents financial losses from incorrect weight distribution
5. Seal Integrity Testers: Preventing Leaks and Contamination
Seal testers ensure the integrity of dog food packaging, preventing leaks that could lead to contamination or spoilage. These testers:
- Detect weak or broken seals in pouches, bags, and cans
- Use vacuum or pressure tests to verify packaging durability
- Help extend shelf life and maintain freshness
Test Method | Fungsi |
---|---|
Vacuum Decay Test | Checks for air leaks in sealed packages |
Pressure Decay Test | Ensures packaging is airtight and secure |
Quality control machines are essential in dog food manufacturing, ensuring safety by detecting contaminants, verifying nutritional composition, maintaining weight accuracy, and ensuring packaging integrity. Investing in advanced inspection technologies not only safeguards pet health but also strengthens brand reputation and regulatory compliance.
Kesimpulan
Understanding the machinery used in dog food production helps ensure high-quality, nutritious products for pets. Investing in the right equipment improves efficiency, safety, and product consistency.
Ajakan untuk Bertindak
If you are looking for reliable dog food manufacturing equipment, contact us today to learn more about high-performance machinery tailored to your production needs.