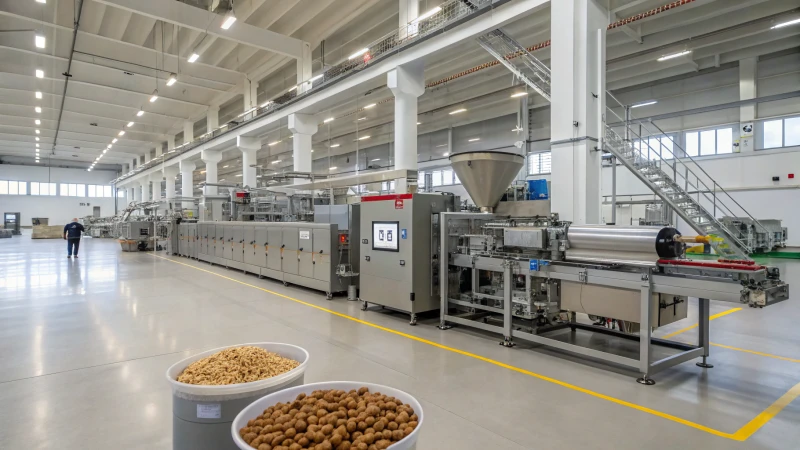
The production of pet food is a rapidly growing industry that demands high-quality, efficient, and innovative machinery to ensure that the final products are safe, nutritious, and appealing to pets. However, manufacturers often face challenges in selecting the right machinery for various pet food production processes. With the increasing consumer demand for premium, organic, and specialized pet foods, understanding the types of machinery used in pet food production can help businesses stay competitive. This article will guide you through the different types of pet food production machinery and how they contribute to the manufacturing process.
Pet food production involves various stages, each requiring specialized machinery. These include mixing, extruding, drying, coating, and packaging processes. By understanding the types of machinery involved, pet food manufacturers can optimize production efficiency, improve product quality, and ensure the safety and nutrition of the pet food.
This article explores the key types of pet food production machinery and their specific roles in the manufacturing process. Understanding these will help you make better decisions when setting up or upgrading your production line.
Types of Pet Food Production Machinery
The process of making pet food involves several distinct steps, and each step requires different machinery. Here, we’ll break down the types of machinery used in pet food production and how each type serves its specific purpose.
1. Mixer and Ingredient Handling Equipment
Mixing machinery is essential in the initial stages of pet food production. It ensures that the raw ingredients are combined thoroughly before any further processing. Ingredients often include meat, vegetables, cereals, vitamins, and minerals, which need to be uniformly blended to provide consistent nutrition across batches.
Types of Mixing Equipment:
- Ribbon Mixers: These are ideal for mixing dry ingredients, creating a homogeneous blend.
- Paddle Mixers: They are used for both wet and dry mixing, offering a more intensive mix, especially when dealing with sticky ingredients.
- Vertical Mixers: These provide efficient mixing for small to medium-sized batches, particularly for pet foods with a higher liquid content.
In addition to mixing, ingredient handling equipment such as sifters, grindersdan conveyors are used to process raw materials before they are mixed.
2. Extruders
Extrusion is one of the most crucial stages in pet food production, where ingredients are subjected to high pressure and temperature, shaping the pet food and cooking it simultaneously. Extruders are versatile machines used to produce dry, semi-moist, and wet pet foods.
There are two main types of extruders:
- Ekstruder Sekrup Tunggal: These are most commonly used in the production of dry pet food. They are efficient and can handle a wide range of ingredients.
- Ekstruder Sekrup Ganda: These are used for higher precision and flexibility in producing pet foods that require more complex shapes and textures, such as snacks or treats.
Extrusion machines are capable of producing kibble, snacks, and special-shaped treats. They can also be adjusted to achieve the desired texture and quality for different types of pet food, such as crunchy or chewy formulations.
3. Dryers
After the extrusion process, pet food must be dried to ensure it reaches the correct moisture content, which helps increase shelf life and prevent bacterial growth. Drying also improves the texture and makes the pet food more palatable.
The most commonly used types of dryers in pet food production are:
- Hot Air Dryers: These are used to reduce moisture content and enhance the crispiness of the product.
- Tunnel Dryers: These are large-scale dryers where pet food moves through a series of hot air chambers to ensure even drying.
- Fluidized Bed Dryers: These work by suspending the pet food in hot air, providing even and efficient drying.
Dryers are crucial for achieving the desired texture and consistency while ensuring food safety standards are met.
4. Coating Machines
Coating machines are used to apply a layer of flavor, oil, or other nutrients to the pet food after it has been extruded and dried. This process adds flavor, improves the appearance, and enhances the nutritional value of the food.
Types of Coating Machines:
- Spray Coating Machines: These are used for evenly spraying fat, flavors, or vitamins onto the surface of the pet food.
- Drum Coaters: These are typically used for coating dry food with oils or flavors. The pet food is tumbled in a drum while the coating is applied.
- Batch Coating Systems: These systems allow for batch processing, where food is coated with specific ingredients in a controlled environment.
Coating machines are essential for the flavor enhancement and nutritional enrichment of pet food products, making them more appealing to both pets and their owners.
5. Cooling Equipment
Cooling equipment is used to lower the temperature of pet food after it has been processed through the extruder or oven. This helps solidify the food and preserve its structure.
Cooling Equipment Types:
- Air Coolers: These are often used in conjunction with extrusion machines and provide continuous air circulation to cool down the food.
- Water-Cooled Systems: These systems are more efficient for larger production volumes and help to quickly reduce the temperature of the food.
- Cooling Conveyors: These convey systems move the pet food through cooling zones, offering controlled temperature reduction.
Efficient cooling prevents moisture from affecting the product’s texture and shelf life.
6. Packaging Machinery
Once the pet food is fully processed and cooled, it is ready for packaging. The packaging machinery ensures that the food is safely sealed in bags, pouches, or cans, ready for shipping.
Types of Packaging Machines:
- Vertical Form Fill Seal Machines: These are used for packaging dry and wet pet foods in bags.
- Canning Machines: These machines are used for sealing wet food in cans or tins.
- Pouch Packaging Machines: These are ideal for packing soft or wet food in sealed pouches.
Packaging machinery plays an essential role in maintaining the freshness and safety of the product while providing attractive packaging to consumers.
7. Quality Control and Inspection Equipment
To maintain product quality and safety, quality control equipment is used at every stage of pet food production. These machines include metal detectors, X-ray machinesdan weight checkers to ensure that the products are free from contaminants and meet regulatory standards.
8. Automation and Control Systems
The integration of automation and control systems in pet food production is becoming increasingly important. These systems monitor and control various production parameters such as temperature, moisture, and speed, ensuring consistent product quality while reducing human error.
Automation tools include:
- PLC (Programmable Logic Controllers): Used to automate machine functions and processes.
- SCADA Systems (Supervisory Control and Data Acquisition): These systems provide centralized control over production lines, improving efficiency and traceability.
Kesimpulan
The production of pet food involves several complex processes, each requiring specific machinery to ensure efficiency, consistency, and quality. From mixing and extruding to coating and packaging, understanding the types of pet food production machinery is essential for manufacturers to make informed decisions and streamline their operations.
By selecting the right machinery, manufacturers can improve production efficiency, meet consumer demand for high-quality pet food, and ensure that pets receive safe, nutritious meals.
If you're looking to upgrade your pet food production line or need help with selecting the right machinery, feel free to contact us for expert advice tailored to your business needs.