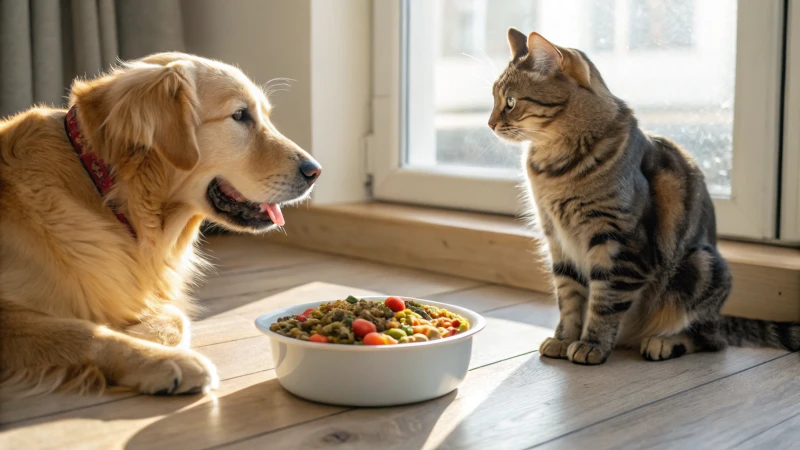
In the world of pet food manufacturing, having the right equipment is crucial to producing high-quality and nutritious meals for our feline companions. But have you ever wondered how cat food is made on a large scale? A cat food making machine is the backbone of this industry, enabling manufacturers to create a variety of cat food products efficiently. However, without proper knowledge of how these machines work, it may be challenging to select the right one or even understand their importance. This article will break down what a cat food making machine is and how it operates.
A common problem for pet food manufacturers is ensuring both the quality and consistency of the product while meeting demand. Traditional methods can be slow, inefficient, and costly. This is where a cat food making machine steps in to streamline the process, providing a solution for mass production. If you're in the pet food industry or simply curious about how cat food is made, this article will guide you through the details of these innovative machines and how they function.
A cat food making machine is an automated piece of equipment used to produce various forms of cat food, including dry kibble, wet food, and even treats. The machine works by mixing ingredients, extruding or molding them into the desired shape, and then cooking or drying the final product to ensure it meets nutritional standards. The process typically involves several stages, including ingredient mixing, extrusion, drying, and packaging, to ensure that the food is safe, nutritious, and appealing to cats.
Understanding how a cat food making machine functions is key to knowing how these devices contribute to high-quality pet food production. If you're looking to learn more about the specific components or working processes of these machines, keep reading as we delve into the details.
What Are the Key Components of a Cat Food Making Machine?
Making nutritious and appealing cat food requires specialized machinery, which is tailored to the specific needs of processing ingredients into safe and palatable food for your feline companions. A cat food making machine integrates various components that ensure a smooth, efficient, and hygienic process to produce high-quality food. Whether you're an experienced pet food manufacturer or just starting, understanding these key components can help you choose the right equipment for your needs.
The process of making cat food involves mixing, extruding, and cooking ingredients like meat, grains, vegetables, vitamins, and minerals. The cat food making machine typically has several critical parts that handle these operations efficiently. In this article, we will explore the primary components of a cat food making machine and how each part plays a role in producing the best cat food.
The key components of a cat food making machine include the extruder, mixer, dryer, cutter, and cooling system. These parts work together to process raw ingredients into high-quality cat food. The extruder is responsible for blending and cooking the ingredients under pressure, while the mixer ensures even distribution of all components. The cutter shapes the food into the desired form, and the dryer and cooling system ensure the food maintains its texture and shelf life.
To understand the full process of making cat food and how each part operates in harmony, it is essential to delve deeper into each component and its function. These machines are designed not only to produce tasty and nutritious food but also to ensure consistency, hygiene, and scalability in production.
Understanding how each of these parts works together can guide you in operating a cat food production line effectively and help you achieve optimal results, from formulation to packaging.
1. Extruder: The Heart of the Machine
The extruder is often referred to as the "heart" of the cat food making machine. It plays a central role in processing the ingredients by cooking, shaping, and sometimes even adding nutrients to the final product. The main tasks of the extruder include:
- Mixing and Cooking: The extruder mixes ingredients such as meat, grains, and additives. The raw ingredients are combined and then subjected to high pressure and heat. This cooking process helps eliminate bacteria and ensures the food is digestible.
- Formálás: After cooking, the mixture is forced through dies to form pellets or kibble. The size and shape of the dies can be adjusted, allowing manufacturers to create various types of cat food.
- Tápanyag visszatartás: The extrusion process is designed to preserve the nutritional value of the ingredients, especially essential vitamins and minerals, which are crucial for a cat's health.
2. Mixer: Ensuring Even Distribution of Ingredients
A proper mix is crucial for ensuring the consistency and quality of cat food. The mixer ensures that all ingredients, including meat, vegetables, grains, and additives like vitamins and minerals, are evenly distributed. Key features of the mixer include:
- Even Ingredient Blending: The mixer ensures all ingredients are uniformly distributed, preventing clumping and ensuring consistency in the final product.
- Adjustable Settings: The mixer speed and time can be controlled to suit the type of ingredients being processed and the desired consistency of the mix.
3. Cutter: Shaping the Food
Once the ingredients have been extruded and shaped, the cutter comes into play. It cuts the food into the desired size and shape, whether it's kibble, pellets, or any other form.
- Adjustable Cutting Sizes: Depending on the specific requirements of the cat food, the cutter can be adjusted to create different sizes and shapes. This allows manufacturers to create a wide range of products, from small kibble for kittens to larger pieces for adult cats.
- Uniformity: The cutter ensures that each piece of food is uniform in size, which helps with consistent cooking and drying, as well as creating an appealing product for the consumer.
4. Dryer: Reducing Moisture Content
The drying process is crucial for preserving the food and preventing spoilage. The dryer removes excess moisture from the extruded food, making it suitable for long-term storage. This step helps maintain the food's texture and ensures it is safe for consumption.
- Drying Process: The food is typically dried using hot air or steam to reduce its moisture content to a safe level (usually around 10-12%).
- Maintaining Nutritional Integrity: The dryer is designed to remove moisture efficiently without affecting the nutrients, ensuring the food remains nutritionally balanced for your cat.
5. Cooling System: Preserving Texture and Flavor
Once the food has been dried, it needs to be cooled to maintain its texture and prevent degradation. The cooling system helps bring down the temperature of the food, making it safe to package and store.
- Cooling Process: The cooling system reduces the temperature of the food gradually to preserve its shape and texture.
- Flavor Retention: Cooling ensures that the food retains its flavor, preventing it from becoming too dry or brittle.
6. Control Panel: Managing the Entire Process
The control panel serves as the brain of the operation, allowing operators to monitor and adjust the settings of the entire production line. This part of the machine enables manufacturers to:
- Set Parameters: Operators can adjust the temperature, pressure, speed, and other factors based on the type of cat food being produced.
- Monitor Performance: The control panel displays real-time data, allowing manufacturers to track the performance of the machine and ensure optimal efficiency.
7. Packaging System: Sealing in Freshness
Once the cat food is processed, it's ready for packaging. The packaging system seals the food in bags or cans, ensuring that it remains fresh and safe for long periods. This system typically includes:
- Weighing and Filling: The packaging system weighs the food accurately before filling it into containers.
- Tömítés: The food is then sealed to maintain freshness and prevent contamination.
Example of a Production Flow:
Lépés | Leírás | Equipment Involved |
---|---|---|
Hozzávalók keverése | Raw ingredients are mixed for uniform consistency. | Keverő |
Extrusion & Cooking | Ingredients are cooked under pressure. | Extruder |
Shaping & Cutting | Food is shaped into pellets or kibble. | Cutter |
Szárítás | Excess moisture is removed. | Szárító |
Cooling | Food is cooled to preserve texture and flavor. | Cooling System |
Csomagolás | Food is weighed, filled, and sealed for storage. | Packaging System |
Következtetés
The cat food making machine is a complex system designed to handle the different steps involved in producing quality cat food. Each component – from the extruder to the packaging system – plays a crucial role in ensuring the food is nutritious, safe, and appealing to cats. Understanding how these components work together will help manufacturers optimize their production processes, reduce waste, and ensure the consistent quality of their products. If you're in the market for a cat food making machine, choosing the right equipment based on these key components is essential for meeting the demands of your customers and providing high-quality food for cats.
Contact us today to learn more about our cat food making machines and how we can help you streamline your production process!
How Does a Cat Food Making Machine Mix Ingredients?
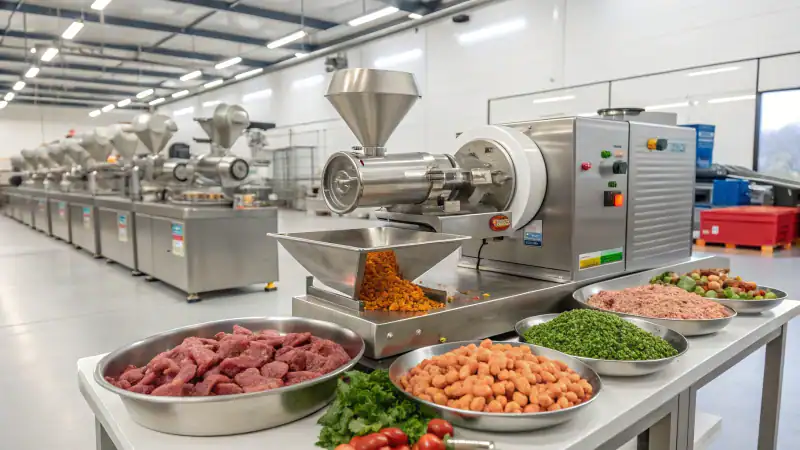
In the production of cat food, creating the perfect texture and consistency requires precision and efficiency. Without a properly functioning mixing process, ingredients can be unevenly distributed, affecting both the quality and nutritional value of the final product. Ensuring that wet, dry, and powdered ingredients blend harmoniously demands an advanced system that can handle various ingredients at scale. If you're a manufacturer or pet food supplier, understanding how a cat food making machine blends ingredients is key to improving product quality and increasing production efficiency. This article will delve into the science behind the mixing process and how it works in modern cat food production.
A cat food making machine blends ingredients using a combination of specialized equipment and precise mechanisms that include rotary mixers, paddle mixers, and screw conveyors. The goal is to evenly distribute ingredients, such as proteins, vitamins, grains, and fats, to create a balanced and nutritious cat food product. The blending process typically involves feeding ingredients into a mixing chamber, where powerful stirring or kneading action ensures uniform consistency. The machine's speed, timing, and configuration are adjusted to achieve the ideal consistency.
The effectiveness of the mixing process has a significant impact on both the texture and flavor of the final cat food product. If the blending is not properly done, the food might end up with lumps or an uneven nutrient distribution. Continue reading to explore the technical aspects of the process, types of machines used, and the critical role of ingredient consistency.
Types of Machines Used for Mixing Cat Food Ingredients
In the industrial production of pet food, a wide range of mixing equipment is used depending on the size, type, and formulation of the food. Let's break down some of the most common types of mixing machines that are designed to efficiently blend the ingredients.
1. Szalagkeverők
Ribbon mixers are one of the most common types of machines used for dry ingredient mixing. These machines consist of a large cylindrical container with two intertwined ribbon-shaped blades. The ribbons rotate in opposite directions, creating a swirling motion that efficiently mixes the dry ingredients. Ribbon mixers are especially effective for bulk dry ingredients, like powders, grains, and vitamins, ensuring that they are uniformly distributed.
Advantages:
- High efficiency in mixing dry ingredients.
- Prevents segregation of powders or ingredients with different densities.
- Suitable for large-scale production.
2. Lapátos keverők
Paddle mixers are designed with flat paddles that rotate within a cylindrical drum. This mixing action is gentler compared to ribbon mixers, making it suitable for both dry and wet ingredients. Paddle mixers are commonly used in recipes that include both liquid and dry components, such as when fats, oils, or broths are added to dry kibble mixes. The gentle mixing prevents ingredient degradation and ensures an even distribution.
Advantages:
- Great for wet and dry ingredients.
- More delicate on ingredients to preserve their integrity.
- Versatile in different formulations.
3. Screw Conveyors
Screw conveyors are used to transport ingredients to the mixing chamber and ensure they are fed in a consistent manner. This component is essential for continuous feeding during the mixing process, ensuring that all ingredients are added at the right time and in the right quantity.
Advantages:
- Provides continuous ingredient feeding.
- Helps to prevent ingredient wastage.
- Allows for precise control over the ratio of ingredients.
4. Vertical and Horizontal Mixers
Vertical mixers employ a vertical axis to mix the ingredients, while horizontal mixers mix ingredients along a horizontal plane. Both are used depending on the product requirements and scale of production. Vertical mixers tend to work best for smaller batches, whereas horizontal mixers can handle large-scale mixing of both dry and wet ingredients in the same chamber.
Advantages:
- Horizontal mixers are excellent for large volumes.
- Vertical mixers offer more compact design.
- Both are effective in ensuring a thorough mixture.
How the Mixing Process Works in Cat Food Production
The blending of ingredients in a cat food making machine is a carefully controlled process, designed to ensure that the nutrients and flavors are evenly distributed throughout the product. Let’s break down the general steps involved in the mixing process.
1. lépés: Hozzávalók előkészítése
Before mixing begins, the ingredients are pre-processed and prepared. This may involve grinding meats, cereals, or grains into the desired texture, and adding necessary supplements such as vitamins and minerals. The quality of the ingredients is essential, as any inconsistencies at this stage can lead to improper mixing.
Step 2: Feeding Ingredients into the Mixing Chamber
Once the ingredients are ready, they are fed into the mixing chamber via conveyors or hoppers. The feeder system is designed to ensure that the ingredients enter the chamber in precise quantities, preventing overloading and underfeeding.
Step 3: Mixing and Blending
The actual mixing process begins when the ingredients are placed in the mixer. Depending on the machine type, the ingredients are subjected to intense mechanical action. For instance, in a ribbon or paddle mixer, the rotating paddles or ribbons work to evenly distribute the ingredients by creating constant movement in the chamber. This ensures uniform mixing without clumping or separation.
The time and speed of mixing are crucial at this stage. The operator can adjust the mixer settings to achieve the desired texture or consistency. If the ingredients are being mixed with wet components like meat broth or oils, the mixing time may be slightly longer to ensure proper hydration.
Step 4: Homogenization
Once the ingredients are adequately mixed, they move into the homogenization phase. This phase ensures that the different ingredients are thoroughly combined and no ingredient remains separate or unevenly distributed. For example, in a dry kibble mix, the fats and oils need to be uniformly distributed, as this will affect both the nutritional value and texture of the final product.
Step 5: Final Inspection and Adjustment
Once the ingredients have been mixed, the blend is inspected to ensure consistency. If necessary, adjustments can be made at this stage by adding more ingredients, whether it be more moisture or additional dry components. This final check ensures that the mixture is ready for extrusion, cooking, or any other subsequent processes.
Importance of Proper Mixing in Cat Food Production
Proper mixing is critical to achieving a consistent and high-quality cat food product. If the ingredients are not evenly mixed, the final product may contain "hot spots" where certain nutrients or flavors are concentrated, while others are lacking. This can lead to poor nutritional value and flavor, affecting pet health and customer satisfaction. Additionally, improper mixing can result in issues like uneven cooking during the extrusion or baking process, leading to inconsistent textures and potential issues with digestibility.
To avoid these issues, modern cat food making machines are equipped with advanced sensors and monitoring systems that ensure the mixing process is precise. Automation and computer controls also play a significant role in ensuring consistency, reducing the margin for human error.
Key Considerations for Selecting a Cat Food Making Machine
When selecting a machine for mixing ingredients in cat food production, several factors must be considered to ensure optimal performance.
1. Ingredient Types
Machines should be chosen based on the types of ingredients being processed. For example, a paddle mixer may be required for wet mixes, while a ribbon mixer may be more appropriate for dry ingredients.
2. Production Volume
Different machines are designed for various production scales. Smaller-scale manufacturers may benefit from a more compact and cost-effective solution, while large-scale manufacturers may need high-capacity mixers with continuous feeding systems.
3. Testreszabás
Some machines offer adjustable mixing speeds, times, and configurations to suit different formulations. Customizability is essential for producers who need flexibility in their production process.
4. Maintenance and Durability
Investing in machines that are easy to maintain and have durable parts is key for reducing downtime and ensuring long-term reliability.
Következtetés
Mixing is one of the most important steps in cat food production, as it ensures that all ingredients are evenly distributed, resulting in a consistent, high-quality product. Whether using a ribbon mixer, paddle mixer, or screw conveyor, the goal is always the same: to create a nutritious and appealing cat food product that meets industry standards. By understanding how the process works and selecting the right equipment for the job, manufacturers can enhance their production efficiency and improve the overall quality of their products.
Are you interested in upgrading your cat food production process? Contact us today to learn more about the best cat food making machines and how we can help optimize your production line.
What Is the Extrusion Process in Cat Food Manufacturing?
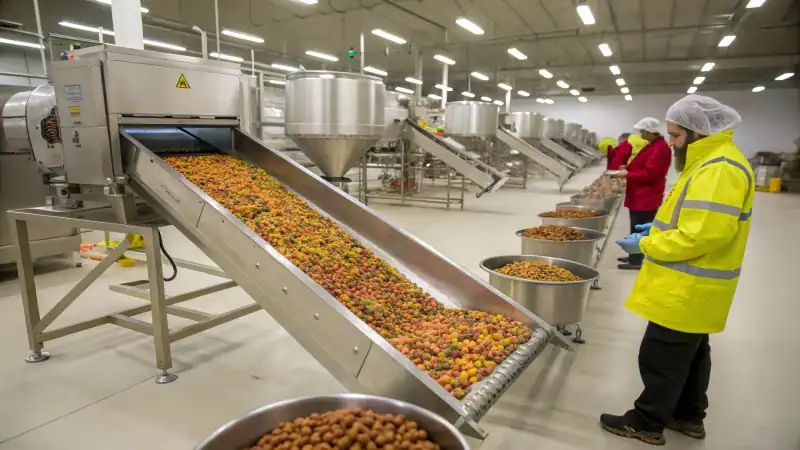
In the world of pet food manufacturing, particularly for cat food, the extrusion process plays a crucial role in producing high-quality, nutritious, and palatable products. However, despite its significance, many people are unaware of the intricate details involved in this process. If you’re a pet food manufacturer, understanding the extrusion process is vital for ensuring the final product’s quality, consistency, and appeal to your feline customers.
The extrusion process in cat food manufacturing involves shaping and cooking raw ingredients under high pressure and temperature. Extrusion allows manufacturers to control the texture, shape, and nutritional content of cat food, making it more digestible, tasty, and easy to handle. It’s the most commonly used method for making dry pet food, including kibble. The process significantly impacts the nutritional profile of the food, such as digestibility and vitamin preservation, ensuring that cats get the nutrients they need in every meal.
Understanding this process is not only essential for manufacturers but also for pet owners who care about what goes into their cat’s food. Keep reading as we explore how extrusion is used to create the perfect cat food, its benefits, and why it’s preferred over other methods.
What Exactly Is the Extrusion Process in Cat Food Manufacturing?
The extrusion process in cat food manufacturing involves mixing, cooking, and shaping ingredients under controlled pressure and temperature. It begins with grinding raw ingredients into a uniform mixture, which is then fed into an extruder—a machine that uses heat and pressure to cook and mold the mixture into desired shapes. After extrusion, the food is dried, cooled, and packaged for distribution. This method enhances the texture, flavor, and digestibility of the food, ensuring it meets the nutritional needs of cats. The precise control over these factors is one reason extrusion is widely used in pet food production.
As manufacturers seek ways to optimize production efficiency while maintaining food quality, extrusion has become a standard, reliable technique. But why is extrusion so beneficial in cat food production? Let's dive into the core advantages of this method.
Benefits of the Extrusion Process in Cat Food Manufacturing
The extrusion process offers several notable advantages for both manufacturers and consumers:
-
Enhanced Nutritional Retention: The high-temperature cooking in an extruder helps preserve important nutrients, such as proteins and fats, while reducing the loss of vitamins and minerals.
-
Javított emészthetőség: By breaking down ingredients under high pressure, the process enhances digestibility, ensuring cats get the most out of their food.
-
Consistency in Quality: Extrusion ensures uniformity in the texture, shape, and size of the kibble, improving the overall quality control of the product.
-
Testreszabás: Manufacturers can adjust the extrusion parameters—such as temperature, pressure, and extrusion speed—to achieve specific characteristics like size, shape, and texture, meeting the preferences of different cat breeds and owners.
-
Polcstabilitás: The drying process following extrusion ensures that the final product has a long shelf life without the need for refrigeration, making it convenient for storage and distribution.
The Step-by-Step Extrusion Process in Cat Food Manufacturing
1. Ingredient Preparation
The first step is sourcing and preparing the ingredients, which typically include meat, grains, vegetables, and supplements. These ingredients are ground into a fine powder or meal to ensure uniformity when mixed.
2. Keverés
The dry ingredients are mixed with wet ingredients (like water or fat) to form a dough-like consistency. This mixture may also include flavorings and nutrients specific to a cat’s dietary needs. The mixture is thoroughly blended to ensure even distribution of all ingredients.
3. Extrudálás
The mixture is then fed into the extruder, which is a large industrial machine consisting of a screw conveyor that moves the mixture through a barrel. The extruder applies heat (up to 160–180°C), pressure (up to 500 psi), and mechanical shear forces to cook and shape the food. During this stage, starches gelatinize, proteins denature, and fats emulsify.
4. Formálás
After being cooked, the mixture exits the extruder through a die, forming the desired shape—most commonly small kibbles, though some manufacturers produce larger chunks or other forms. The die can be customized to create shapes like fish, hearts, or other fun, attractive designs.
5. Szárítás
The freshly extruded food is still moist, so it’s passed through a dryer to remove excess water content. The drying process prevents spoilage and extends shelf life. The temperature and airflow in the drying chamber are carefully controlled to maintain the food's integrity.
6. Cooling
Once the food is dried, it is cooled rapidly to room temperature. This helps maintain the kibble’s shape and ensures it remains crisp and crunchy.
7. Bevonat
A layer of fat or flavoring may be sprayed onto the kibble for added taste and aroma. This coating can also help improve the food’s palatability, making it more attractive to cats.
8. Csomagolás
Finally, the finished cat food is packaged in airtight bags or containers to maintain freshness and prevent contamination.
The Role of Temperature and Pressure in Extrusion
The temperature and pressure settings during extrusion are critical for determining the final product’s quality. By carefully controlling these factors, manufacturers can manipulate the density, digestibility, and texture of the food. For example, higher temperatures can lead to better protein and fat denaturation, which aids in digestibility but may reduce nutrient levels if overdone. Conversely, too low of a temperature might fail to adequately cook the ingredients, resulting in a less palatable and less digestible product.
The moisture content also plays an essential role in how well the ingredients bond and retain their nutritional value during the extrusion process. Too much moisture could lead to soggy food, while too little may prevent the kibble from forming correctly.
Tables and Charts: Understanding the Impact of Extrusion on Cat Food
Here’s a simple table to visualize how extrusion parameters affect the final product:
Paraméter | Impact on Cat Food |
---|---|
Temperature (160–180°C) | Improves digestibility and protein structure, but excessive heat can degrade vitamins. |
Pressure (up to 500 psi) | Ensures uniform cooking, affects texture and density. |
Moisture (10-12%) | Critical for forming kibble and maintaining shelf stability. |
Extrusion Speed | Controls the texture and crunchiness of the final product. |
Another key aspect of extrusion is its influence on nutrient preservation. Below is a chart comparing the retention of nutrients in extruded cat food versus other cooking methods:
Tápláló | Extrusion Retention (%) | Baking Retention (%) | Boiling Retention (%) |
---|---|---|---|
Protein | 85-90% | 70-80% | 60-70% |
Fat | 80-85% | 60-70% | 50-60% |
Vitamins (C, E, B) | 70-85% | 50-65% | 40-50% |
As illustrated, extrusion maintains a higher percentage of key nutrients compared to other traditional cooking methods, ensuring a higher-quality cat food product.
The Future of Extrusion in Cat Food Manufacturing
As consumer demand for specialized and high-quality pet foods grows, the extrusion process continues to evolve. Manufacturers are experimenting with new ingredients, improving equipment design, and optimizing energy usage to create more sustainable and nutritious pet foods. Some modern extruders even incorporate technologies like cold extrusion, which uses lower temperatures to preserve sensitive nutrients like probiotics and enzymes.
Moreover, the growing trend of plant-based diets for cats has led to innovations in extrusion that accommodate alternative protein sources, like peas, lentils, and other legumes. As these trends evolve, the extrusion process will continue to adapt to meet both the nutritional needs of cats and the expectations of conscientious pet owners.
Következtetés
The extrusion process is a fundamental part of modern cat food manufacturing. By ensuring high-quality, nutritious, and palatable food for felines, it serves as an essential tool for manufacturers aiming to meet the demands of discerning pet owners. Understanding how extrusion works, its benefits, and its impact on the final product can help you make informed decisions about the cat food you choose for your feline companions.
Call to Action
Interested in learning more about the extrusion process and how it can improve your cat food products? Contact us today to get expert advice and insights tailored to your needs! We are here to help you produce the best possible food for your furry friends.
How Is Cat Food Dried or Cooked During Production?
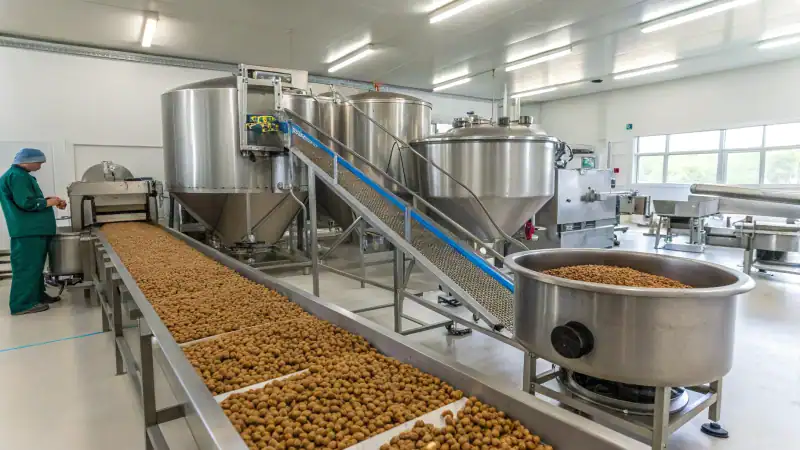
When it comes to producing high-quality cat food, the methods used for drying or cooking play a crucial role in ensuring both safety and nutritional value. Improper cooking or drying processes can lead to nutrient loss, contamination, and even spoilage. Therefore, understanding how these processes work is essential for pet owners concerned about what goes into their cats' meals. In this article, we’ll dive into the different cooking and drying techniques used during cat food production, why they matter, and how they affect the final product.
Drying or cooking is essential for producing cat food, as it helps preserve the product while maintaining nutritional content. Cat food is typically cooked using extrusion, steam cooking, or air-drying processes to ensure both safety and quality. These techniques prevent spoilage, reduce bacterial contamination, and help preserve essential nutrients while making the food shelf-stable.
The production process involves various technical steps that aim to make the food palatable, nutritious, and safe. There are different techniques, depending on the type of food being produced (wet, dry, or semi-moist), and the specific nutritional profile the food aims to meet. Let’s explore how this is achieved in more detail.
The Different Techniques for Drying and Cooking Cat Food
1. Extrusion Cooking
Extrusion is one of the most common methods used in dry cat food production. It involves the use of a machine called an extruder, which forces raw ingredients like meat, vegetables, grains, and vitamins through a heated barrel under pressure. The extruder's screw mechanism pushes the mixture through a die, where the food is shaped into kibble and then rapidly cooked by steam and heat. This process ensures that the food is cooked at high temperatures (often between 180°C and 200°C) to kill harmful pathogens and create a crunchy texture.
Advantages of Extrusion:
- Preserves nutrients: The high temperature and pressure help to preserve essential vitamins and minerals, although some heat-sensitive nutrients can be lost in the process.
- Consistency: The extrusion process creates uniform kibble shapes, which help with portion control and make the food more appealing to cats.
- Shelf-stable: Since the food is rapidly cooked and dried, it can be stored for longer periods without refrigeration.
However, while extrusion maintains most of the nutrients, some vitamins (like vitamin C) may degrade due to the heat. Manufacturers often add extra nutrients to compensate for any loss during the cooking process.
2. Steam Cooking
For wet or canned cat foods, steam cooking is the predominant method. Unlike extrusion, which is used for dry food, steam cooking involves cooking the raw ingredients in large pressure cookers or steamers. The food is usually pre-cooked or partially cooked before being mixed with other ingredients like broth, fats, and additives. The mixture is then sealed in cans or pouches and cooked further under high pressure and temperature to kill bacteria and preserve the food.
Advantages of Steam Cooking:
- Moisture retention: Steam cooking helps preserve the moisture content of the food, making it more appealing to cats who prefer wet food.
- Flavor retention: The slow cooking process helps retain the natural flavors of the ingredients.
- Nutrient preservation: Since the food is not exposed to extremely high temperatures for long periods, steam cooking tends to preserve more nutrients compared to dry food processing.
3. Air-Drying (Dehydration)
Air-drying, or dehydration, is typically used for making raw, freeze-dried, or semi-moist cat food. This method removes moisture from the food slowly at low temperatures, often in specialized dehydrators or freeze-drying machines. The process involves freezing the food, then subjecting it to low heat or air circulation to remove water without cooking the ingredients.
Advantages of Air-Drying:
- Nutrient preservation: Air-drying preserves more of the natural nutrients since the food is not exposed to high heat.
- Raw food appeal: Dehydrated cat food retains much of the taste and nutritional profile of raw ingredients, making it a popular choice among raw food enthusiasts.
- Convenience: Air-dried food is often easier to store and transport, with a longer shelf life compared to fresh raw food.
However, air-dried food can be more expensive and may require rehydration before serving.
How Does the Cooking or Drying Method Affect the Nutritional Profile of Cat Food?
The method used for drying or cooking can significantly impact the final product’s nutrient composition. Some key points to consider:
- Protein levels: High-heat processes like extrusion can alter the structure of proteins, reducing their digestibility. However, manufacturers compensate by adding more easily digestible proteins after cooking.
- Fat content: Heat-sensitive fats can break down during high-temperature cooking, potentially reducing their health benefits for cats. Steam cooking, with its gentler temperatures, often preserves fats better.
- Vitamins and minerals: Some vitamins (such as B vitamins) are more sensitive to heat, so their levels may decrease during extrusion or steam cooking. Manufacturers may add these nutrients back in after cooking to ensure the food remains balanced.
Nutrient Preservation in Different Processes:
Tápláló | Extrusion Cooking | Steam Cooking | Air-Drying |
---|---|---|---|
Protein | Moderately preserved | Well-preserved | Well-preserved |
Zsírok | Some loss | Well-preserved | Well-preserved |
Vitamins (B, C) | Mérsékelt veszteség | Mild loss | Minimal loss |
Ásványi anyagok | Well-preserved | Well-preserved | Well-preserved |
Why Does Drying and Cooking Matter for Your Cat’s Health?
Choosing the right cooking or drying method matters not only for taste but also for the health of your cat. The food’s texture, nutrient content, and digestibility all depend on how the ingredients are treated during the production process. Cats, being obligate carnivores, require high-quality protein, balanced fats, and specific vitamins and minerals to thrive. Poorly processed food can lead to deficiencies or imbalances that affect your cat’s health, from skin problems to digestive issues.
Következtetés
Understanding how cat food is dried or cooked during production is key to ensuring that your cat gets the best nutrition from their meals. Whether through extrusion, steam cooking, or air-drying, each method has its advantages and challenges, but they all aim to provide safe, nutritious, and appetizing food for your feline friend.
How Does the Cat Food Making Machine Package the Final Product?
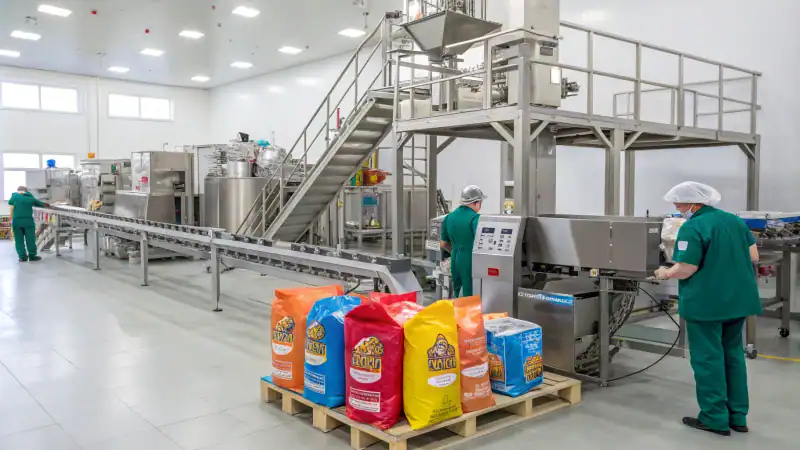
When producing cat food, many manufacturers rely on automated systems to not only create the kibble but also package the final product efficiently and consistently. The final packaging step is crucial, ensuring that the food reaches consumers in a way that preserves its freshness and nutritional integrity. A streamlined, reliable packaging system reduces labor costs, increases productivity, and guarantees the safety and quality of the product. But how exactly does the cat food making machine package the final product?
The cat food making machine typically utilizes integrated systems to package the final product. These systems consist of automated conveyors, bagging machines, and sealing units that prepare the kibble for transport to the consumer. The machines work together in harmony to weigh, fill, seal, and label each package with speed and accuracy.
After the kibble is produced in the extruder, it must go through a series of steps before it’s ready for sale. The extrusion process is often followed by drying, cooling, and seasoning. Once the food is ready, the packaging machines take over to ensure the final product is sealed, safe, and appealing to customers. In this article, we’ll explore the intricate process of how a cat food making machine packages the final product, the technology behind it, and how it ensures the food reaches homes in perfect condition.
The process of packaging pet food involves a mix of precision, efficiency, and automation. From filling to sealing and labeling, modern cat food packaging systems are designed to keep up with high demand while ensuring the kibble is preserved. Whether you are a manufacturer or simply curious about how this works, understanding the entire process can provide insights into the complexity and precision involved in making cat food.
The Packaging Process in Detail
1. Weighing and Portioning
The packaging of cat food begins once the kibble is cooled and ready for the next stage. Automated weighing systems ensure that each bag or pouch gets the correct portion of food. This process is extremely important to prevent overfilling or underfilling, which can affect product consistency and customer satisfaction. Weighing machines use highly sensitive sensors to detect the exact weight of the kibble being packed into each bag, ensuring accurate portions with minimal wastage.
2. Filling the Packaging Bags
Once the kibble is weighed, it moves on to the filling process. Cat food packaging machines are designed to handle a variety of bag types, from standard plastic bags to vacuum-sealed pouches. The bags are typically placed on a conveyor belt where they are opened and filled by automated machines. These machines use precise mechanisms to ensure that each bag receives the right amount of food, preventing both spills and incomplete packages.
For companies that produce different bag sizes (for instance, 1kg, 5kg, and 10kg), the packaging machines are often adjustable, allowing for quick size changes. Some systems also use multiple filling stations to handle larger volumes, ensuring the process can handle bulk production efficiently.
3. Sealing the Bags
After the bags are filled, they are sealed to keep the food fresh and prevent contamination. Sealing is an essential step in the packaging process as it helps maintain the nutritional value of the food and protects it from external elements such as moisture and air. The most common sealing methods for cat food packaging include heat sealing, where the bag edges are melted together, and vacuum sealing, which removes air from the bag to extend the food's shelf life.
In both cases, the machines ensure that the seal is robust and air-tight, preventing leaks or spoilage. For vacuum-sealed bags, the packaging machine will often have additional steps to remove any air and create a tight, compact package.
4. Labeling and Printing
Once the bags are sealed, they need to be labeled. The labels are typically printed with product information, including the ingredients, nutritional value, weight, and expiration date. Many cat food manufacturers also add branding elements and graphics that appeal to consumers.
Labeling is usually done using high-speed automated printers that print directly onto the bags or labels, ensuring each package is properly identified and adheres to industry regulations. Some machines are also equipped with barcode scanners to ensure the right product is being labeled and shipped.
5. Packaging and Final Quality Control
After labeling, the bags are often placed into larger boxes or cartons for easy handling and transportation. Automated systems use conveyors and robotic arms to group the individual bags into cartons, which are then sealed and sent to the warehouse for distribution.
At this stage, a final quality control check is conducted to ensure that all bags are sealed correctly, labeled properly, and free of defects. Any bags that fail the inspection process are typically removed from the production line and discarded.
Technology Used in Cat Food Packaging Machines
Cat food packaging systems have advanced significantly in recent years, integrating various cutting-edge technologies to improve efficiency, accuracy, and speed. Below are some of the key technologies commonly used in modern cat food packaging machines:
-
Servo Motors and Automation: These motors help control the speed and precision of the machines. They are capable of performing high-speed operations without sacrificing accuracy, making them ideal for high-volume production.
-
Vision Systems: Vision systems are used for quality control and verification, such as ensuring proper filling, checking bag seals, and verifying labels. These systems use cameras and sensors to detect any inconsistencies in the production process.
-
Vacuum Sealing Technology: This technology removes air from the bags, extending the shelf life of the product by preventing oxidation and moisture buildup. It's especially important for dry foods like kibble, which can lose freshness over time.
-
Robotic Arms: Automated robotic arms are used for tasks such as sorting, packing, and placing sealed bags into larger cartons. This automation reduces human labor and increases speed while ensuring precision.
-
Multi-Lane Filling Systems: These systems allow for faster production by filling multiple bags simultaneously. They are especially useful for high-demand products and can easily be adjusted for different bag sizes.
Advantages of Automated Cat Food Packaging
The use of automated cat food packaging systems brings several advantages to manufacturers and consumers alike:
-
Increased Production Efficiency: Automation allows for higher production rates and faster turnaround times. This is particularly beneficial in industries like pet food, where demand is constant.
-
Improved Consistency and Accuracy: Automation ensures each package is consistently filled, sealed, and labeled with the exact same specifications, improving product quality and reducing waste.
-
Cost-Effectiveness: While the initial investment in automated packaging machines can be significant, they quickly pay off by reducing labor costs, improving efficiency, and lowering the chances of human error.
-
Better Hygiene and Safety: Automated systems are designed to operate in clean, controlled environments, which reduces the risk of contamination. The ability to seal packages tightly also helps maintain the food’s safety and freshness.
-
Testreszabás: Many modern machines allow for quick changes to the production line, such as switching between different bag sizes or adjusting the fill level. This flexibility makes it easier to cater to various consumer preferences and market demands.
Final Thoughts
The packaging process in cat food production is crucial for delivering a product that is both fresh and safe for pets. The integration of advanced technology has made the entire process faster, more efficient, and more reliable. Whether it's through precision weighing, automated sealing, or smart labeling, cat food making machines ensure that every bag of kibble reaches pet owners in optimal condition.
Want to learn more about how automated packaging systems can benefit your pet food production line? Contact us for tailored solutions that fit your needs.
What Are the Benefits of Using a Cat Food Making Machine?
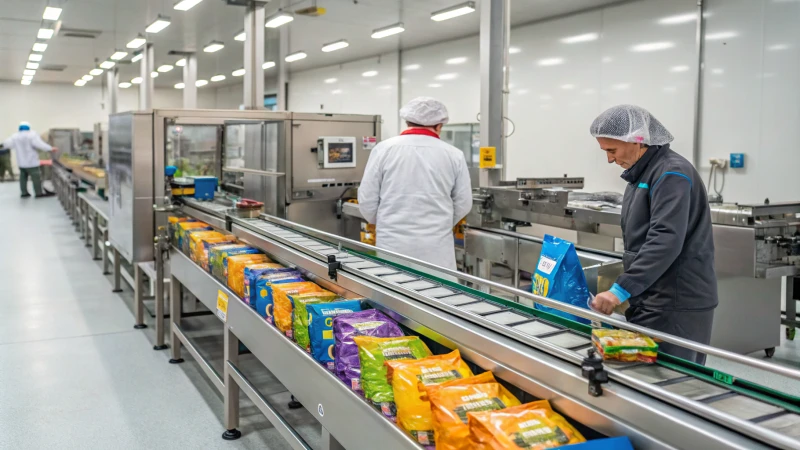
In recent years, the pet food industry has seen tremendous growth, particularly within the cat food sector. With an increasing number of pet owners seeking premium, nutritious food for their cats, manufacturers are looking for ways to meet the demand efficiently. This is where the cat food making machine comes in. The shift toward automation and more efficient production lines has revolutionized the industry. However, many pet food manufacturers and entrepreneurs are still wondering: what are the actual benefits of investing in a cat food making machine? In this article, we'll delve into the key advantages and how it can benefit your business.
The production of high-quality cat food is essential in today’s competitive pet food market. Traditional manual methods can be labor-intensive, inefficient, and inconsistent in product quality. To solve this, cat food making machines offer automation, consistent quality, and greater efficiency. By implementing such machines, manufacturers can scale their production, reduce labor costs, and ensure a higher standard of product quality. These machines help streamline the entire process, from mixing ingredients to shaping and packaging, allowing for better control over the final product and minimizing errors.
When it comes to manufacturing, speed, consistency, and quality control are key. This article will explore how cat food making machines can improve these aspects, helping manufacturers scale and enhance their operations. Read on to find out how you can benefit from this investment and why it might be the next step for your business.
Using a cat food making machine offers several significant advantages. These include improved production efficiency, cost reduction, consistent product quality, and the ability to meet rising consumer demands. Machines automate the labor-intensive process of mixing, cooking, shaping, and packaging, which not only speeds up production but also reduces human error, ensuring a higher quality end product. Furthermore, these machines help manufacturers produce a variety of flavors and formulations, thus offering more options to consumers while maintaining high standards of nutrition and safety.
One of the main pain points that cat food manufacturers face is the inconsistency in the production process when using traditional methods. Manual labor often leads to variations in ingredient proportions, inconsistent cooking times, and a lack of uniformity in the final product. This inconsistency can affect the nutritional content and taste, which directly impacts the brand’s reputation. By utilizing a cat food making machine, manufacturers can standardize the process, ensuring that each batch of food is consistent and meets the nutritional requirements. Automated machines allow for precise control over the mixing, cooking, and shaping of ingredients, reducing human error and increasing overall product quality.
Key Benefits of Using a Cat Food Making Machine
1. Improved Production Efficiency
One of the most significant benefits of using a cat food making machine is the increase in production efficiency. Traditional methods of food production often involve manual labor and a lengthy cooking process. Machines, on the other hand, automate these tasks, allowing for faster production rates. A well-optimized production line can produce large quantities of food in a shorter amount of time, helping manufacturers meet the growing demand for high-quality pet food.
Table 1: Production Efficiency Comparison
Method | Manual Production | Automated Production |
---|---|---|
Production Speed | Alacsony | Magas |
Consistency | Alacsony | Magas |
Labor Requirements | Magas | Alacsony |
Energy Usage | Változó | Efficient |
2. Költségcsökkentés
Automating the production process with a cat food making machine leads to significant cost savings. Although the initial investment in the equipment can be high, the long-term benefits far outweigh the costs. Automated systems reduce labor costs and minimize the risk of human error, which can lead to wasted ingredients, inefficiencies, and product recalls. Over time, the increased production rate and reduced operational costs will help offset the initial investment.
3. Következetes termékminőség
In the pet food industry, consistency is key. Consumers expect that the food they purchase will meet the same high-quality standards every time they buy it. A cat food making machine ensures uniformity by automatically regulating the cooking times, ingredient proportions, and mixing speeds. This precision results in consistently high-quality products, which helps build trust and loyalty with consumers. Whether it's the texture, taste, or nutritional value, a machine-controlled process guarantees that the final product meets expectations.
Chart 1: Comparison of Consistency in Product Quality
Data Points:
- Manual Process: Variability in texture, taste, and ingredient ratios
- Automated Process: Precise consistency in each batch
4. Increased Customization and Flexibility
With the flexibility that cat food making machines offer, manufacturers can produce a wide variety of formulations, flavors, and textures to meet different customer needs. Whether it's dry kibble, wet food, or specialized diets for cats with allergies or health concerns, these machines allow for easy switching between recipes. This capability is particularly valuable for companies that want to target niche markets or differentiate themselves from competitors.
5. Higher Hygiene and Safety Standards
Automated machines are designed with hygiene and safety in mind. The closed-system nature of these machines reduces the chances of contamination and maintains cleaner production environments. With food safety being of paramount importance in the pet food industry, these machines help ensure that the food is safe for consumption. In addition, regular cleaning cycles in these machines contribute to maintaining the highest standards of hygiene throughout the production process.
Real-Life Case Study: The Impact of Cat Food Making Machines
Company X, a well-established pet food manufacturer, recently switched from manual production methods to using an automated cat food making machine. Prior to the switch, the company faced challenges with slow production times, inconsistent product quality, and rising labor costs. After integrating the machine, Company X saw a 50% increase in production speed, a 30% reduction in labor costs, and a significant improvement in product consistency. Customer satisfaction also increased, as the quality of the food became more predictable. This transition not only allowed them to meet growing consumer demands but also boosted their profitability.
The Future of Cat Food Manufacturing
The rise of automation and technological innovation in the pet food industry is shaping the future of manufacturing. As demand for premium and specialized cat food grows, companies will need to invest in advanced machinery to remain competitive. By adopting cat food making machines, businesses can improve their production processes, meet customer demands for high-quality products, and increase their operational efficiency.
ClaimReview:
Automated cat food making machines are more efficient than manual production.Igaz
Automated systems increase production rates, reduce labor costs, and improve product consistency compared to manual methods.
Következtetés
In conclusion, the benefits of using a cat food making machine are clear. From increased production efficiency to cost savings és a termék konzisztenciája, these machines enable manufacturers to meet the growing demand for high-quality pet food. Whether you are looking to scale your business, improve the quality of your products, or reduce operational costs, investing in this technology can be a game changer for your pet food production line.
Kapcsolatfelvétel
If you're considering upgrading your production line or need more information about cat food making machines, feel free to contact us. We provide comprehensive solutions that can help you optimize your operations and improve the quality of your products. Get in touch today to discuss how we can assist you!
How to Select the Right Cat Food Making Machine for Your Business?
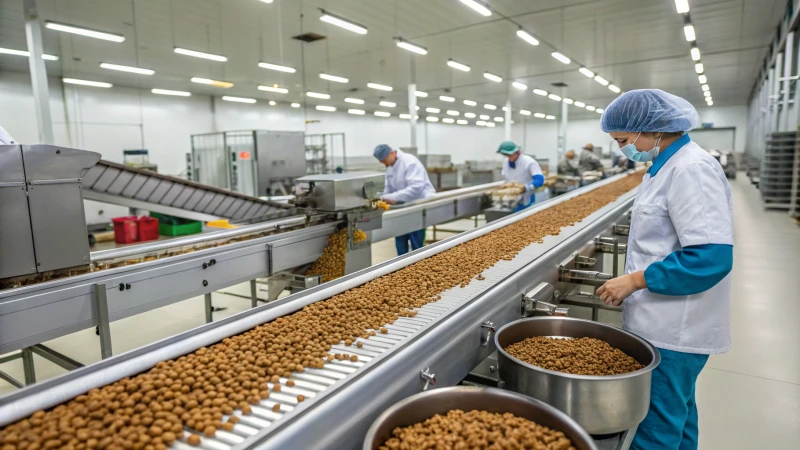
Selecting the right cat food making machine for your business can be overwhelming due to the multitude of options available in the market. Whether you're starting a new production line or upgrading an existing one, the wrong choice can lead to production delays, inefficiencies, and wasted resources. With the increased demand for premium pet food products, ensuring you have the right machinery is critical for staying competitive. This article will guide you step-by-step in choosing the ideal cat food production machine that aligns with your business goals, budget, and operational needs.
Choosing the right cat food making machine is a crucial step in optimizing production, maintaining product quality, and meeting industry standards. Consider factors like production capacity, automation levels, and machine versatility to ensure you choose a machine that fits your business requirements, scalability, and quality standards.
Before diving into the specific features of cat food production machines, it's essential to understand your business needs. The type of cat food you intend to produce, whether dry kibble, wet food, or semi-moist treats, will influence the type of machinery you select. A high-quality machine can streamline operations, reduce waste, and increase output, but the wrong choice could lead to production inefficiencies, quality issues, and increased operational costs.
Key Considerations When Choosing a Cat Food Making Machine
1. Termelési kapacitás
One of the most critical factors in selecting the right cat food making machine is ensuring it can meet the production capacity your business requires. Consider the following:
- Small-scale production: If you're a startup or focusing on a niche market, a smaller machine with a lower production capacity may suffice.
- High-volume production: Established businesses aiming for large-scale production need a machine with high throughput to keep up with demand.
Machines are usually rated by their output per hour, so make sure the chosen machine aligns with your production volume requirements to avoid bottlenecks.
2. Type of Cat Food
Different cat food types require different production processes:
- Dry Cat Food: This is the most common and includes kibble and pellets. A dry food extruder is used for processing, which involves cooking ingredients at high temperatures and pressures.
- Wet Cat Food: Wet food production requires specialized machines for grinding, mixing, and filling. These machines often include cooking units and may also have packaging features.
- Semi-Moist Treats: These require a combination of ingredients to be processed and shaped, often using an extruder with specific settings for moisture control.
Ensure the machine you choose is designed for the type of cat food you plan to produce.
3. Automatizálási és vezérlőrendszerek
In today’s competitive market, automation can significantly improve the efficiency of production. Automated systems minimize human error, reduce labor costs, and increase consistency across production batches. Here are some automation features to consider:
- Fully automated systems: These include automatic ingredient feeders, automatic mixing, and extruding processes, reducing human involvement and increasing speed.
- Semi-automated systems: These may require some manual operation but are still efficient for medium-scale production.
- Manual control systems: While less expensive, these require more human intervention and can lead to inconsistent results.
4. Energy Efficiency and Operating Costs
Manufacturing cat food can be energy-intensive, particularly for large-scale operations. It's essential to evaluate the energy efficiency of the machine to minimize operational costs in the long term. Look for machines with energy-saving features such as optimized heating systems and variable-speed motors to ensure that you can control electricity consumption.
Additionally, understand the maintenance costs associated with the machine. Regular maintenance schedules and spare parts availability can affect long-term expenses.
5. Quality Control Features
The quality of cat food must meet stringent health and safety standards, so your production machine should support quality control throughout the process. Some features to look for include:
- Temperature and pressure monitoring: These ensure that the ingredients are cooked properly.
- Moisture control: Essential for ensuring the correct texture of dry or semi-moist food.
- Uniform mixing capabilities: To ensure that ingredients are evenly blended, which directly impacts the nutritional consistency of the food.
Integrating systems like automated inspection and testing can also help ensure that the final product adheres to your quality standards.
6. Ease of Cleaning and Maintenance
The hygiene of your production line is paramount, as pet food is consumed by animals, and any contamination can have serious consequences. Machines should be easy to clean, with components that can be disassembled and sanitized quickly. This is particularly important in wet food production, where residues can lead to mold and bacterial growth.
Make sure the machine is designed for quick disassembly and has smooth surfaces that are easy to wipe down. Regular cleaning and maintenance schedules will also ensure the longevity of the machine.
7. Space and Layout
Finally, the size and layout of the production facility are crucial. Some machines are large and require substantial floor space, while others are more compact. When choosing a cat food making machine, ensure that it fits within the space you have available. Additionally, consider whether the machine can be easily integrated into your existing production line or if it will require significant adjustments to the facility.
8. Price and Return on Investment
The initial price of the machine is an obvious consideration, but it’s equally important to evaluate the long-term ROI. This involves:
- Lower operational costs from energy efficiency, minimal waste, and reduced labor costs.
- Increased production speed which leads to higher output.
- Improved product quality that enhances customer satisfaction and brand reputation.
Look for machines that balance affordability with performance to maximize your investment.
Key Features of Cat Food Making Machines
Jellemző | Előnyök | Fontosság |
---|---|---|
Extruder Technology | Efficient processing of dry food | Essential for producing consistent kibble shapes and textures |
Automated Feeders | Reduces labor, minimizes error | Speeds up the production process while maintaining consistency |
Energiahatékonyság | Lowers electricity costs | Saves operational costs over the long term |
Quality Control Systems | Monitors ingredient quality during production | Ensures the final product meets nutritional standards |
Sokoldalúság | Capable of producing multiple food types | Helps businesses diversify their product range |
Selecting the right cat food making machine for your business is not a one-size-fits-all decision. It requires careful consideration of your production needs, the type of food you plan to produce, and the long-term costs associated with the machinery. By focusing on production capacity, automation, energy efficiency, and quality control, you can make an informed choice that supports your business growth and ensures high-quality, safe products for your customers.
Choosing the right cat food making machine is crucial for optimizing production efficiency and maintaining product quality.Igaz
The right machine ensures higher throughput, reduces production downtime, and minimizes waste, directly contributing to cost savings and product quality.
Következtetés
A cat food making machine is a highly specialized and efficient tool that streamlines the production of cat food. It ensures that the food meets quality standards and is produced in large quantities, making it easier for manufacturers to cater to a growing demand for nutritious, safe, and tasty meals for cats. Understanding the intricacies of these machines can help you make informed decisions whether you are a pet food producer or just a curious pet lover.
Call to Action
If you're ready to invest in a cat food making machine for your business or need more information about the best machines for your needs, feel free to contact us for personalized guidance and recommendations. Our expert team is here to help you select the perfect machine that will scale with your business.