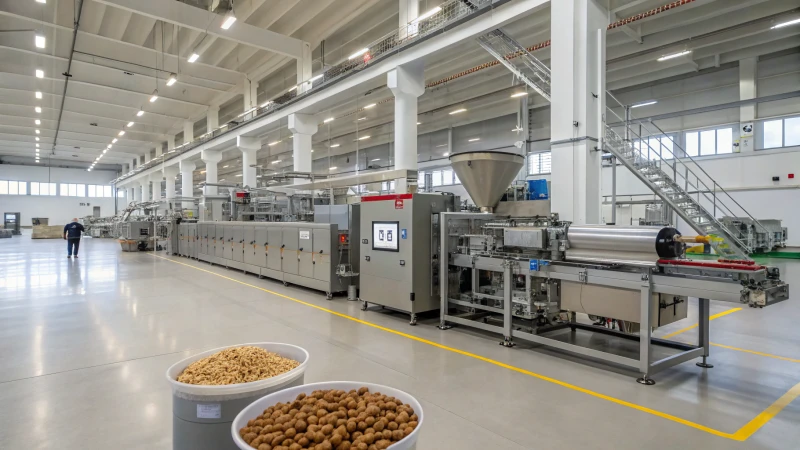
Pet owners want the best for their furry companions, and a crucial aspect of their well-being is the food they consume. However, many pet parents remain unaware of how pet food is processed and whether it maintains nutritional integrity. Poorly processed pet food can lead to health issues, including digestive problems, obesity, and nutrient deficiencies. Understanding the pet food manufacturing process helps consumers make informed choices, ensuring their pets receive safe and balanced meals.
Pet food is processed through a series of steps, including ingredient selection, grinding, mixing, cooking (extrusion or baking), drying, cooling, coating with fats or flavors, and packaging. Each step ensures the food meets nutritional standards, remains safe for consumption, and is appealing to pets. The process varies depending on whether the food is dry kibble, wet canned food, or freeze-dried raw food.
With so many pet food options available, understanding the production process helps pet owners select the right type of food for their pets. Let’s explore the details of pet food processing, the differences between various types, and what factors influence quality.
What Ingredients Are Used in Pet Food Processing?
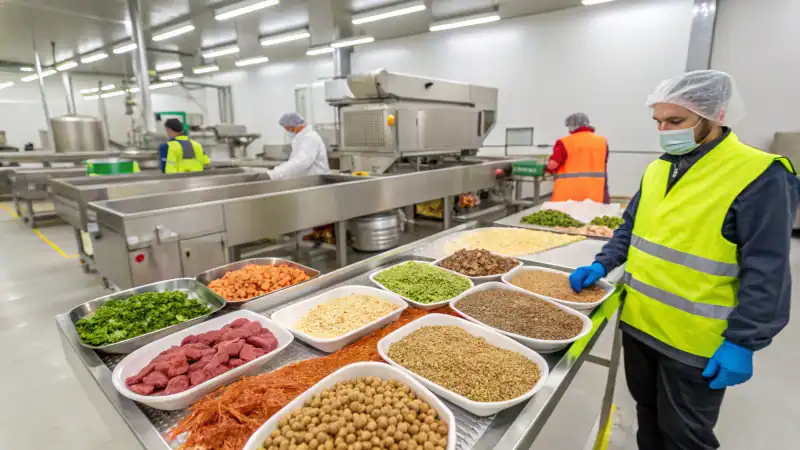
Pet food processing is a crucial industry that directly impacts the health and well-being of pets. Many pet owners are unaware of what goes into their pet’s food, leading to concerns about quality, safety, and nutrition. The wrong ingredients or poor processing methods can result in health issues like obesity, allergies, and digestive problems in pets. Understanding the ingredients used in pet food processing helps pet owners make informed decisions and ensures that manufacturers adhere to high-quality standards. This article explores the key ingredients used in pet food processing and their nutritional significance.
What Are the Main Ingredients Used in Pet Food Processing?
The primary ingredients used in pet food processing include proteins (meat, fish, and plant-based sources), carbohydrates (grains, legumes, and fiber sources), fats (animal and plant-based oils), vitamins, minerals, and functional additives (probiotics, prebiotics, antioxidants, and preservatives). These ingredients are carefully formulated to meet the nutritional needs of pets while ensuring taste, digestibility, and shelf stability.
Understanding the ingredients in pet food can help pet owners select the best options for their pets’ health. While high-quality proteins and essential nutrients are vital, some processed foods may contain fillers, artificial additives, or low-quality ingredients. Pet owners should focus on ingredient lists and choose products that prioritize natural, nutrient-rich components.
1. Protein Sources in Pet Food
Protein is the most important macronutrient in pet food, supporting muscle growth, energy, and overall health. Pet food manufacturers use various protein sources, including:
Animal-Based Protein
Protein Source | Előnyök | Common Uses |
---|---|---|
Chicken | High in lean protein, easily digestible | Used in dry and wet pet food |
Beef | Rich in amino acids and iron | Popular in premium pet food brands |
Lamb | Hypoallergenic, ideal for sensitive pets | Used in specialized pet food formulas |
Fish (Salmon, Tuna) | Omega-3 fatty acids for coat health | Included in premium and grain-free formulas |
Turkey | Low-fat protein source | Found in weight management pet foods |
Plant-Based Protein
Protein Source | Előnyök | Common Uses |
---|---|---|
Soy | High protein, alternative to animal protein | Used in vegetarian and hypoallergenic pet foods |
Pea Protein | Easily digestible and rich in amino acids | Common in grain-free pet foods |
Potato Protein | Low-allergen, good alternative for sensitive pets | Found in specialty pet food formulas |
2. Carbohydrates and Fiber Sources
Carbohydrates provide pets with energy and aid digestion. Some of the most commonly used carbohydrates in pet food include:
Carbohydrate Source | Előnyök | Common Uses |
---|---|---|
Rice | Easily digestible, low in allergens | Used in premium and sensitive-stomach pet foods |
Édesburgonya | High in fiber, vitamins, and antioxidants | Included in grain-free and holistic pet foods |
Barley | Provides sustained energy | Found in natural and whole-food-based pet diets |
Corn | Cost-effective energy source | Used in commercial pet foods (though sometimes controversial) |
Oats | Rich in soluble fiber, supports digestion | Common in limited-ingredient diets |
3. Fats and Oils in Pet Food
Fats are a crucial energy source and support skin, coat, and brain health. Essential fats include:
Fat/Oil Source | Előnyök | Common Uses |
---|---|---|
Chicken Fat | High in omega-6 fatty acids | Found in dry kibble and wet pet food |
Fish Oil | Rich in omega-3s, supports heart and skin health | Used in premium pet food |
Flaxseed Oil | Plant-based omega-3 source | Included in natural and grain-free pet foods |
Sunflower Oil | Supports skin and coat health | Found in holistic and specialty pet diets |
4. Essential Vitamins and Minerals
Pet food manufacturers add vitamins and minerals to ensure a balanced diet. Some key micronutrients include:
Tápláló | Funkció |
---|---|
A vitamin | Supports vision and immune health |
Vitamin D | Essential for bone health and calcium absorption |
E vitamin | Powerful antioxidant for cell health |
B vitaminok | Help with energy metabolism and nervous system function |
Calcium | Strengthens bones and teeth |
Iron | Prevents anemia and supports oxygen transport |
5. Functional Additives in Pet Food
Pet food processors also include functional ingredients that enhance health benefits and improve shelf stability.
Additive Type | Cél |
---|---|
Probiotikumok | Support gut health and digestion |
Prebiotics | Promote healthy gut bacteria growth |
Antioxidants | Prevent spoilage and support immune function |
Preservatives (Natural or Synthetic) | Extend shelf life |
Natural preservatives like tocopherols (Vitamin E) are safer than synthetic preservatives.Igaz
Natural preservatives are less likely to cause allergic reactions and are preferred in premium pet food formulations.
How Are These Ingredients Processed?
Pet food ingredients undergo various processing techniques to ensure safety and nutritional value. Common processing methods include:
- Extrudálás: Used for dry kibble production, where ingredients are cooked at high temperatures and shaped into pellets.
- Canning: Used for wet pet food, where ingredients are mixed, cooked, and sealed in airtight containers.
- Freeze-Drying: Retains maximum nutrients while removing moisture, ideal for high-quality pet foods.
- Dehydration: A slow-drying process used in natural pet foods to maintain ingredient integrity.
Következtetés
Understanding the ingredients used in pet food processing is crucial for ensuring pets receive the right nutrition. High-quality protein sources, balanced carbohydrates, essential fats, vitamins, and functional additives all play a role in pet health. Pet owners should carefully evaluate ingredient lists and opt for nutritious, well-processed pet foods to promote their pets’ long-term well-being.
How Is Dry Pet Food (Kibble) Processed?
Pet owners trust kibble as a convenient, affordable, and nutritionally complete food option for their pets. However, many are unaware of the complex processing methods involved in producing high-quality dry pet food. Improper processing can lead to nutrient loss, contamination, or poor digestibility, which may affect pet health. This article explores the entire kibble manufacturing process, from ingredient selection to packaging, ensuring you understand how your pet’s food is made.
What Is the Process for Making Dry Pet Food (Kibble)?
The production of dry pet food (kibble) involves ingredient selection, grinding and mixing, extrusion cooking, drying, coating with fats and palatants, cooling, and packaging. Each step ensures the food is safe, nutritionally balanced, and palatable for pets. Modern pet food manufacturers use strict quality control measures to meet regulatory standards and maintain consistency.
The kibble production process transforms raw ingredients into a shelf-stable, nutritious product that meets pets' dietary needs. Understanding these steps helps pet owners make informed choices and ensures manufacturers adhere to the highest quality standards.
1. Ingredient Selection and Preparation
The first step in kibble manufacturing is choosing high-quality ingredients, which typically include:
- Protein sources (meat, fish, eggs, plant-based proteins like peas and lentils)
- Carbohydrates (corn, rice, wheat, barley, potatoes)
- Fats and oils (chicken fat, fish oil, vegetable oils)
- Vitamins and minerals (calcium, phosphorus, zinc, vitamin A, D, E)
- Functional additives (probiotics, prebiotics, fiber sources, antioxidants)
Once selected, the raw materials undergo csiszolás to create a uniform texture. Proteins, grains, and other ingredients are reduced to a fine meal, ensuring consistency in the final kibble product.
Common Ingredients Used in Kibble Production
Ingredient Type | Examples | Cél |
---|---|---|
Protein | Chicken, beef, lamb, fish, soy | Muscle development, energy |
Carbohydrates | Rice, corn, sweet potatoes | Provides energy, aids digestion |
Zsírok | Chicken fat, fish oil, flaxseed oil | Supports skin, coat, and brain function |
Fiber | Beet pulp, cellulose, pumpkin | Promotes digestion and gut health |
Vitamins & Minerals | Calcium, phosphorus, vitamin E | Supports overall health and immunity |
2. Mixing and Blending
After grinding, all ingredients are precisely weighed and blended in large industrial mixers. This step ensures an even distribution of nutrients throughout the batch. Water or steam may be added to help form a consistent dough.
Mixing is one of the most critical steps in kibble processing.Igaz
Proper blending ensures each piece of kibble contains the correct balance of nutrients, improving pet health and food consistency.
3. Extrusion Cooking – The Key to Kibble Formation
Extrusion is the most important step in kibble processing. This high-temperature, high-pressure cooking method ensures food safety, improves digestibility, and shapes the final kibble.
How Does Extrusion Work?
- The dough is fed into an extruder, a machine that uses steam, pressure, and mechanical shear to cook the ingredients.
- The mixture is heated to 100–200°C (212–392°F), cooking the starches, proteins, and fats while eliminating bacteria and pathogens.
- The cooked dough is pushed through die plates, which determine the kibble’s shape and size.
- As the hot mixture exits, it expands, creating the familiar light, porous texture of kibble.
Extruder Components and Functions
Extruder Part | Funkció |
---|---|
Hopper | Feeds the ingredient mixture into the machine |
Csigafolyosó | Moves and compresses ingredients |
Heating Chamber | Cooks the mixture at high pressure and temperature |
Die Plate | Shapes the kibble into specific sizes and forms |
Cutter Blade | Slices the extruded product into bite-sized pieces |
4. Drying and Moisture Control
Once shaped, the kibble contains too much moisture (20–25%), making it prone to spoilage. The drying process reduces moisture to under 10%, ensuring a longer shelf life.
- Kibble is passed through large dryers or ovens, where hot air removes excess moisture.
- Proper drying prevents mold growth, maintains texture, and ensures crunchiness.
5. Coating with Fats and Palatants
To enhance taste and nutritional value, kibble undergoes fat and flavor coating after drying.
- Animal fats, fish oils, or vegetable oils are sprayed onto the kibble for improved palatability and energy content.
- Palatants (flavor enhancers made from meat digest or yeast extracts) make the kibble more appealing to pets.
This step ensures kibble is tasty, nutritious, and attractive to pets while delivering essential fatty acids for skin and coat health.
6. Cooling and Packaging
After coating, kibble is cooled to prevent condensation inside packaging. It then undergoes quality control checks before being packed into bags.
Quality Control in Kibble Packaging
Control Measure | Cél |
---|---|
Moisture Testing | Ensures correct water content |
Nutrient Analysis | Confirms protein, fat, and vitamin levels |
Microbial Testing | Checks for bacteria and mold |
Texture & Palatability Tests | Ensures kibble consistency and taste |
Packaging is designed to preserve freshness, prevent spoilage, and maintain crunchiness. Some pet food brands use resealable bags or nitrogen flushing to extend shelf life.
7. Quality Assurance and Regulatory Compliance
Before reaching pet stores, kibble must comply with strict industry regulations. Food safety organizations such as:
- AAFCO (Association of American Feed Control Officials) – USA
- FEDIAF (European Pet Food Industry Federation) – Europe
- FDA (Food and Drug Administration) – USA
ensure pet food meets nutritional standards, safety, and labeling requirements.
AAFCO-approved pet foods guarantee complete and balanced nutrition.Igaz
AAFCO establishes nutritional standards to ensure pet foods meet essential dietary requirements.
Következtetés
The kibble manufacturing process is a highly controlled and scientifically advanced method that transforms raw ingredients into a safe, nutritious, and long-lasting pet food product. By selecting high-quality ingredients, using advanced extrusion technology, and following strict safety protocols, manufacturers ensure kibble provides complete and balanced nutrition for pets.
Looking for High-Quality Pet Food Processing Solutions? Contact Us!
If you are a pet food manufacturer looking for top-tier ingredients, state-of-the-art extrusion technology, or regulatory compliance guidance, we can help. Contact us today for customized solutions that meet the highest industry standards!
How Is Wet Pet Food (Canned Food) Processed?
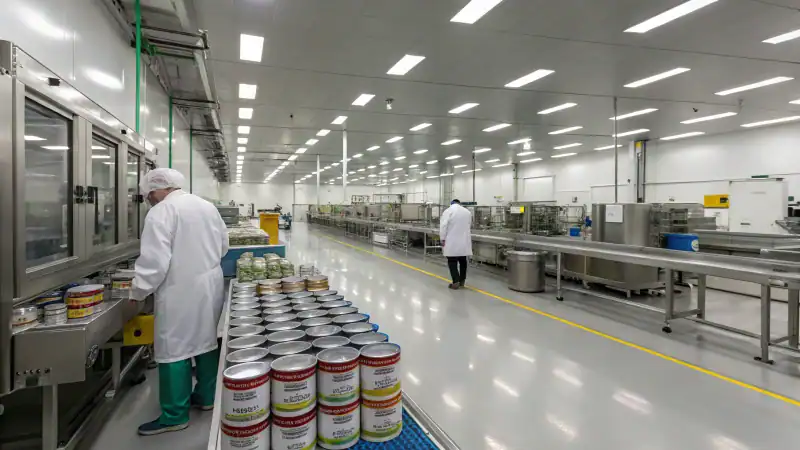
Wet pet food, commonly known as canned pet food, is a staple for many pet owners due to its high moisture content and palatability. However, few consumers understand how it is processed and manufactured. The process involves precise formulation, cooking, sterilization, and packaging, ensuring that the final product is both nutritious and safe. Understanding how wet pet food is made can help pet owners make informed decisions about their pets’ diets.
Wet pet food is processed through a multi-step manufacturing system that includes raw material selection, grinding, blending with essential nutrients, pre-cooking, filling, sealing, retorting (sterilization), and cooling. These steps ensure the product is safe, nutritious, and shelf-stable for extended periods.
Manufacturers adhere to stringent quality controls to ensure the safety and nutritional integrity of wet pet food. Each stage of the process is designed to preserve key nutrients while preventing contamination. Since wet pet food has a high moisture content, proper sterilization is crucial to prevent spoilage and bacterial growth. Keep reading to learn more about each step in detail.
1. Ingredient Selection and Sourcing
The first step in wet pet food production is selecting raw ingredients, which typically include:
- Protein sources: Meat (chicken, beef, fish, lamb) and meat by-products
- Carbohydrates: Rice, potatoes, peas, or other fiber sources
- Zsírok és olajok: Chicken fat, fish oil, or vegetable oils for energy and essential fatty acids
- Vitamins and minerals: Essential nutrients to meet pet dietary requirements
- Gelling agents: Such as guar gum or carrageenan, which help achieve the desired texture
Minőségellenőrzés:
Before processing, raw materials undergo quality checks for freshness, contamination, and nutritional adequacy. Any substandard ingredients are rejected to maintain food safety.
2. Grinding and Blending
Once the ingredients pass quality control, they are ground to the required consistency. This ensures uniformity in texture and proper mixing. The ground ingredients are then blended in large industrial mixers, where the necessary nutrients, water, and fats are added.
- Meat is ground into fine particles for uniform cooking.
- Carbohydrates and other ingredients are blended in precise proportions.
- Water is added to create a thick slurry that facilitates even cooking.
3. Pre-Cooking and Homogenization
Pre-cooking is essential to break down proteins and carbohydrates before canning. This step enhances digestibility and improves the food’s texture.
- The mixture is heated to a precise temperature, typically around 80–90°C (176–194°F).
- Homogenization ensures even distribution of nutrients and ingredients.
- This step also activates natural gelling agents, giving wet food its characteristic texture.
4. Filling and Sealing
Once pre-cooked, the wet pet food is transferred to high-speed can-filling machines. The food is filled into sterilized cans, trays, or pouches, ensuring precise portioning.
- Automatic fillers dispense the correct amount into each container.
- Lids are sealed using vacuum-sealing technology to prevent oxidation and bacterial growth.
- Minimal air is left inside the can to enhance shelf stability.
5. Retorting (High-Temperature Sterilization)
Retorting is a crucial step in ensuring food safety. It involves sterilizing the sealed cans in a high-pressure, high-temperature steam chamber.
Paraméter | Typical Range |
---|---|
Hőmérséklet | 115–130°C (239–266°F) |
Pressure | 10–20 PSI |
Duration | 30–90 minutes |
This process eliminates harmful bacteria such as Salmonella and Listeria, ensuring the food remains safe for extended storage.
Wet pet food remains sterile and safe due to high-temperature retort processing.Igaz
Retort sterilization at temperatures above 115°C effectively eliminates pathogens and extends shelf life.
6. Cooling and Labeling
After sterilization, the cans are rapidly cooled using cold water sprays or air cooling. This prevents overcooking and ensures proper sealing integrity.
Once cooled, the cans undergo labeling and packaging:
- Labels are applied with product information, ingredients, and expiry dates.
- Batch codes are printed for traceability and quality control.
- Final inspection is conducted to remove any defective cans.
7. Storage and Distribution
The final step is storing the finished product in climate-controlled warehouses before distribution. Cans are tested periodically to ensure they meet safety standards.
Quality Control Checks | Cél |
---|---|
Microbial Testing | Ensures food is free of bacteria and mold |
Texture and Consistency Analysis | Ensures uniform texture across batches |
Shelf-Life Testing | Determines how long the food remains safe |
Benefits of Retort-Processed Wet Pet Food
- Long Shelf Life: Retorted food can last 2–5 years without preservatives.
- Nutrient Preservation: Heat processing locks in essential nutrients.
- High Moisture Content: Aids in hydration, especially for cats and senior pets.
- Improved Palatability: Wet food is more flavorful than dry kibble.
Common Myths About Wet Pet Food Processing
Myth | Truth |
---|---|
"Canned pet food contains harmful preservatives." | False. Retort processing eliminates the need for chemical preservatives. |
"The cooking process destroys all nutrients." | False. While some heat-sensitive vitamins degrade, manufacturers compensate by adding extra nutrients. |
"Wet food is less safe than dry kibble." | False. Properly canned food is sterilized and free of bacteria. |
Final Thoughts
Wet pet food undergoes a rigorous manufacturing process to ensure safety, quality, and nutrition. From ingredient selection to sterilization and packaging, every step is carefully controlled to provide pets with high-quality meals. If you’re considering wet food for your pet, knowing how it's processed can help you make a confident, informed choice.
Looking for High-Quality Wet Pet Food? Contact Us!
At Darin Machinery, we specialize in premium wet pet food production, using only the highest-quality ingredients and state-of-the-art processing. Contact us today to learn more about our products and how we can meet your pet’s dietary needs!
What Is Freeze-Dried and Raw Pet Food Processing?

Pet owners are increasingly concerned about providing the best nutrition for their pets, leading to a surge in interest in raw and freeze-dried pet foods. However, many are unaware of how these products are made and whether they are truly safe and nutritious. Improper handling of raw pet food can lead to bacterial contamination, while inefficient freeze-drying can strip essential nutrients. Understanding the manufacturing process of both freeze-dried and raw pet food can help pet owners make informed decisions and ensure they are providing the best for their furry companions.
Freeze-dried and raw pet food processing involves selecting high-quality raw ingredients, freezing them at ultra-low temperatures, and either drying them through sublimation (freeze-drying) or keeping them in their raw state while implementing strict pathogen control measures. These processes retain most nutrients while ensuring safety and extended shelf life.
Many pet owners choose freeze-dried or raw diets because they mimic a pet’s natural ancestral diet. But are these foods truly better than conventional kibble or wet food? To fully understand the benefits and risks, we need to delve deeper into the science behind their production.
Freeze-dried pet food retains 98% of its nutrients compared to fresh raw food.Igaz
Freeze-drying removes moisture while preserving the majority of vitamins, minerals, and proteins, making it a highly nutritious alternative.
The Process of Freeze-Dried Pet Food
Step 1: Ingredient Selection
Manufacturers start with high-quality meats, organ meats, bones, and sometimes vegetables or fruits. These ingredients are crucial for maintaining the appropriate balance of protein, fat, and essential nutrients.
Step 2: Freezing at Ultra-Low Temperatures
The selected ingredients are flash-frozen at temperatures as low as -40°F (-40°C). This rapid freezing process prevents ice crystal formation, which can damage cellular structures and reduce the quality of the final product.
Step 3: Sublimation (Freeze-Drying)
Freeze-drying is a complex process where the frozen raw materials are placed in a vacuum chamber. Through sublimation, water transitions directly from ice to vapor without passing through the liquid stage. This method retains the food’s structure, color, and nutritional integrity.
Step 4: Pathogen Control Measures
Unlike traditional raw food, freeze-dried pet food undergoes a "kill step," such as High Pressure Processing (HPP) or irradiation, to eliminate harmful bacteria like Salmonella and Listeria.
Step 5: Packaging and Storage
The final product is sealed in airtight packaging to prevent moisture reabsorption. Proper storage ensures a long shelf life—often up to 25 years if kept in optimal conditions.
Nutritional Value of Freeze-Dried Pet Food
Tápláló | Megtartási arány (%) |
---|---|
Protein | 98% |
Vitaminok | 95-98% |
Ásványi anyagok | 97-99% |
Moisture | <5% |
Advantages of Freeze-Dried Pet Food
- Long shelf life (up to 25 years)
- Lightweight and convenient for travel
- Minimal processing, high nutrient retention
- Reduces bacterial risks compared to raw food
- Rehydrates easily for a fresher taste
The Process of Raw Pet Food Manufacturing
Unlike freeze-dried food, raw pet food is stored and consumed in its natural state. The production process is more straightforward but requires strict quality control to prevent contamination.
Step 1: Ingredient Selection
Raw pet food includes raw meat, bones, organs, and sometimes vegetables or supplements. High-quality sources such as free-range chicken, grass-fed beef, or wild-caught fish are preferred.
Step 2: Grinding and Mixing
Many raw diets are ground to ensure a balanced distribution of nutrients and ease of digestion. The mixture often includes finely ground bones for calcium.
Step 3: Pathogen Control and Safety Measures
Since raw food is not cooked, stringent safety measures are required. Common pathogen reduction techniques include:
- High Pressure Processing (HPP): Uses high-pressure water to eliminate bacteria.
- Irradiation: Exposes food to ionizing radiation to kill harmful microorganisms.
- Fermentation and probiotics: Some raw food brands introduce beneficial bacteria to outcompete harmful pathogens.
Step 4: Flash Freezing and Storage
To maintain freshness, raw pet food is rapidly frozen at -20°F (-29°C) or lower. Consumers must store it in a freezer and thaw it before feeding.
Risks and Benefits of Raw Pet Food
Tényező | Raw Food | Freeze-Dried Food |
---|---|---|
Tápanyag visszatartás | Magas | Very High |
Szavatossági idő | Short (1-2 months) | Long (up to 25 years) |
Bacterial Risk | Magasabb | Alsó |
Convenience | Requires freezer storage | No freezer needed |
Palatability | Kiváló | Excellent after rehydration |
Benefits of Raw Pet Food
- Closest to a natural diet
- Minimal processing preserves nutrients
- May improve digestion and coat health
Risks of Raw Pet Food
- Bacterial contamination risk
- Requires strict freezer storage
- Short shelf life
Raw pet food contains more bacteria than freeze-dried food.Igaz
Since raw pet food is not processed with a 'kill step' like freeze-drying or cooking, it has a higher risk of bacterial contamination.
Which Is Better: Freeze-Dried or Raw Pet Food?
The choice between freeze-dried and raw pet food depends on several factors:
- Safety Concerns: Freeze-dried food undergoes bacterial elimination processes, making it safer for households with children or immunocompromised individuals.
- Convenience: Freeze-dried pet food requires no refrigeration and is easy to store, making it ideal for busy pet owners.
- Költségek: Freeze-dried food tends to be more expensive due to the freeze-drying process.
- Pet Preference: Some pets prefer the texture and moisture content of raw food.
Both freeze-dried and raw pet foods offer numerous health benefits, mimicking a pet’s natural diet more closely than traditional kibble. However, safety and convenience factors make freeze-dried food a more practical choice for many pet owners. Regardless of the option chosen, ensuring a balanced diet and proper handling procedures is crucial to your pet’s health.
How Do Manufacturers Ensure Pet Food Safety and Quality?

Pet food recalls due to contamination or poor-quality ingredients can have devastating consequences for pets and their owners. Contaminants such as Salmonella, E. coli, and aflatoxins pose serious health risks, while nutrient imbalances can lead to long-term health issues. To address these concerns, manufacturers implement rigorous safety and quality control measures throughout the pet food production process. By adhering to strict industry regulations, using advanced testing methods, and employing cutting-edge technology, manufacturers ensure that pet food is safe, nutritious, and consistent in quality.
Pet food manufacturers ensure safety and quality through stringent ingredient sourcing, advanced food processing technologies, microbial testing, nutritional analysis, and compliance with regulatory standards. These measures help prevent contamination, maintain nutritional balance, and guarantee product consistency.
Ensuring pet food safety and quality requires multiple layers of testing and verification at every stage of production. From raw material selection to final packaging, manufacturers use a combination of scientific analysis, automation, and regulatory oversight to deliver safe and nutritious pet food products.
Pet food manufacturing involves more safety tests than human food production.Igaz
Because pets often consume the same food daily, manufacturers must ensure that every batch meets consistent safety and nutritional standards.
Key Steps in Ensuring Pet Food Safety and Quality
1. Strict Ingredient Sourcing and Supplier Verification
Pet food safety starts with high-quality ingredients. Manufacturers work with trusted suppliers who must meet strict quality standards and undergo routine audits.
- Supplier Audits: Regular inspections of ingredient suppliers ensure compliance with safety standards.
- Ingredient Traceability: Every ingredient is tracked from its source to the final product.
- Raw Material Testing: Incoming ingredients are tested for pathogens, toxins, and nutritional composition before use.
2. Advanced Food Processing Technologies
Modern pet food manufacturing employs advanced technologies to ensure food safety and enhance shelf life.
Processing Method | Cél | Commonly Used For |
---|---|---|
High-Pressure Processing (HPP) | Eliminates bacteria without heat | Raw and freeze-dried pet food |
Extrusion Cooking | Kills pathogens, improves digestibility | Száraz kutyaköles |
Freeze-Drying | Preserves nutrients while removing moisture | Freeze-dried raw food |
Pasteurization | Destroys harmful bacteria | Wet/canned food |
3. Microbial Testing and Contaminant Screening
To prevent bacterial contamination, manufacturers conduct thorough testing throughout production.
- Pathogen Testing: Checks for Salmonella, Listeria, and E. coli at multiple stages.
- Mycotoxin Screening: Detects toxic molds in grains and proteins.
- Heavy Metal Analysis: Ensures pet food does not contain dangerous levels of lead, mercury, or arsenic.
Pet food contamination mostly comes from poor-quality raw ingredients.Igaz
Low-quality ingredients increase the risk of bacterial contamination, toxins, and inconsistent nutrient levels.
4. Nutritional Analysis and Quality Control
Ensuring that pet food meets precise nutritional requirements is critical to pet health.
- Guaranteed Nutrient Profiles: Manufacturers analyze protein, fat, vitamins, and minerals to meet pet dietary needs.
- Batch Consistency Testing: Every production batch is tested to ensure uniformity.
- Palatability Studies: Testing ensures the food is appealing to pets.
5. Compliance with Industry Regulations and Certifications
Pet food manufacturers must adhere to strict government and industry standards.
Szabályozó Testület | Régió | Role in Pet Food Safety |
---|---|---|
FDA (Food and Drug Administration) | USA | Oversees pet food safety, ingredient approvals |
AAFCO (Association of American Feed Control Officials) | USA | Sets nutritional guidelines for pet food |
FEDIAF (European Pet Food Industry Federation) | Európa | Ensures compliance with European pet food standards |
ISO 22000 Certification | Global | Food safety management certification |
Manufacturers that comply with these regulations demonstrate a commitment to safety and quality.
6. Packaging and Shelf-Life Stability Testing
Proper packaging ensures product freshness and prevents contamination.
- Airtight, Moisture-Proof Packaging: Protects against mold and spoilage.
- Oxygen Absorbers & Preservatives: Prevent oxidation and nutrient degradation.
- Accelerated Shelf-Life Testing: Simulates long-term storage conditions to ensure product integrity.
7. Recall Readiness and Continuous Improvement
Even with the best quality control, unforeseen issues can arise. Manufacturers implement recall protocols to respond quickly if a problem is detected.
- Recall Protocols: Plans in place for rapid response in case of contamination.
- Customer Feedback Systems: Monitors complaints to identify potential issues.
- Continuous Research & Development: Ongoing improvements based on new safety technologies.
Most pet food recalls are due to bacterial contamination.Igaz
Salmonella, Listeria, and E. coli are common causes of recalls, highlighting the importance of strict microbial testing.
The Future of Pet Food Safety and Quality Assurance
Advancements in food safety technology are continually improving pet food production. Some emerging innovations include:
- AI-Powered Quality Control: Machine learning algorithms detect inconsistencies in production.
- Blockchain Traceability: Enables real-time tracking of ingredients and manufacturing steps.
- DNA-Based Pathogen Detection: Faster and more accurate identification of harmful bacteria.
- Sustainable and Ethical Sourcing: Ensures ingredients are responsibly harvested and safe.
A Commitment to Pet Health
Pet food manufacturers invest heavily in safety and quality assurance to ensure that pets receive nutritionally balanced and contamination-free food. By following strict sourcing, processing, and testing protocols, they safeguard pet health while complying with regulatory standards.
How to Choose the Best Processed Pet Food for Your Pet?

When it comes to feeding your pet, choosing the right processed pet food is crucial for their health and longevity. Many pet owners struggle with selecting the best option due to the overwhelming number of brands, formulas, and ingredient lists available on the market. A poor diet can lead to obesity, digestive issues, allergies, and long-term health conditions such as diabetes and kidney disease. To ensure your pet gets optimal nutrition, you must evaluate the food based on its ingredients, nutritional value, safety, and suitability for your pet’s specific needs.
What Is the Best Processed Pet Food for Your Pet?
The best processed pet food is one that meets AAFCO (Association of American Feed Control Officials) or FEDIAF (European Pet Food Industry Federation) standards, contains high-quality protein sources, essential vitamins, and minerals, and is free from harmful preservatives, artificial flavors, and fillers. It should also be tailored to your pet's life stage, breed, size, and specific dietary needs. Consulting your veterinarian and carefully reading the ingredient label can help ensure you make the best choice.
Pet owners often assume that all pet foods are created equal, but quality can vary significantly. Keep reading to discover what to look for when choosing processed pet food and how to make the best choice for your furry friend.
All processed pet foods contain artificial preservatives.Hamis
Many high-quality pet foods use natural preservatives such as tocopherols (Vitamin E) and ascorbic acid (Vitamin C).
Key Factors to Consider When Choosing Processed Pet Food
1. Understanding Pet Food Labels
One of the most critical steps in selecting the best food for your pet is reading and understanding the food label. Here’s what to look for:
- Ingredient List: The first few ingredients should include a high-quality protein source such as chicken, beef, fish, or lamb.
- Guaranteed Analysis: Indicates the levels of crude protein, fat, fiber, and moisture in the food.
- AAFCO or FEDIAF Statement: Ensures the food meets established nutritional guidelines.
- No Harmful Additives: Avoid artificial colors, preservatives (BHA, BHT, ethoxyquin), and unnecessary fillers (corn, wheat, soy).
Label Term | Meaning |
---|---|
"Complete and Balanced" | Meets minimum nutritional requirements set by AAFCO/FEDIAF |
"Natural" | Contains no synthetic ingredients (except essential vitamins and minerals) |
"Grain-Free" | No wheat, corn, or soy; alternative carb sources used |
"High-Protein" | More protein content, often from animal sources |
"Limited Ingredient" | Fewer ingredients, designed for pets with food sensitivities |
2. Choosing Between Dry, Wet, or Freeze-Dried Food
The type of pet food you choose depends on your pet’s preferences, health needs, and lifestyle.
- Száraz kutyakaják: Convenient, cost-effective, and promotes dental health.
- Wet/Canned Food: Higher moisture content, beneficial for hydration and palatability.
- Freeze-Dried/Dehydrated Food: Retains nutrients, has a long shelf life, and often has minimal processing.
Food Type | Pros | Cons |
---|---|---|
Dry Kibble | Affordable, long shelf life, supports dental health | Can be lower in moisture and may contain more preservatives |
Wet/Canned | Higher in moisture, often more palatable | More expensive, requires refrigeration |
Freeze-Dried | Nutrient-rich, minimally processed | Expensive, requires rehydration |
3. Identifying High-Quality Ingredients
When evaluating pet food, ensure it contains essential nutrients:
- Protein: Look for named animal sources such as “chicken meal” instead of generic terms like “meat meal.”
- Healthy Fats: Omega-3 and omega-6 fatty acids (from fish oil or flaxseed) support skin and coat health.
- Fiber and Carbohydrates: Ingredients such as sweet potatoes, peas, and brown rice provide digestible energy.
- Vitamins and Minerals: Taurine (for cats), calcium, and antioxidants are crucial for overall health.
Grain-free diets are always better for pets.Hamis
Grain-free diets are beneficial for pets with grain allergies, but whole grains can provide valuable nutrients and fiber for many pets.
4. Special Dietary Considerations
Different pets have different nutritional requirements. Consider these factors when selecting food:
- Age: Puppies and kittens need higher protein and fat levels compared to senior pets.
- Breed & Size: Large breeds may require joint-supporting ingredients like glucosamine.
- Health Conditions: Pets with allergies, obesity, or kidney disease need specialized diets.
Example: Choosing the Right Food for a Senior Dog | Tényező | Recommended Nutrients |
---|---|---|
Joint Health | Glucosamine, chondroitin | |
Weight Management | Lower fat, higher fiber | |
Heart Health | Omega-3 fatty acids, taurine | |
Digestive Support | Probiotics, easily digestible proteins |
5. Avoiding Harmful Ingredients
Some ingredients in pet food can be harmful over time. Avoid:
- Artificial Preservatives: BHA, BHT, ethoxyquin
- Artificial Colors & Flavors: Red 40, Blue 2, Yellow 5
- Excessive Fillers: Corn, wheat, soy
- Meat By-Products: Low-quality protein sources with less nutritional value
Meat by-products are always bad for pets.Hamis
High-quality by-products, such as organ meats, can provide essential nutrients, but low-quality by-products should be avoided.
Final Thoughts: Making the Right Choice
Choosing the best processed pet food requires careful evaluation of ingredients, quality, and suitability for your pet’s needs. Always:
- Read labels carefully and prioritize real, high-quality protein sources.
- Choose food appropriate for your pet’s age, size, and health condition.
- Avoid artificial additives and excessive fillers.
- Consult your veterinarian for personalized recommendations.
Your pet’s health depends on the nutrition you provide. Investing in high-quality processed pet food can lead to a longer, healthier, and happier life for your furry friend.
Következtetés
Pet food processing involves multiple steps to ensure safety, nutritional adequacy, and palatability. Understanding these processes empowers pet owners to make informed choices about their pet’s diet, prioritizing health and longevity.
Kapcsolatfelvétel
If you want high-quality pet food Machine that meets rigorous safety standards, contact us today to learn more about our manufacturing processes and premium ingredients.