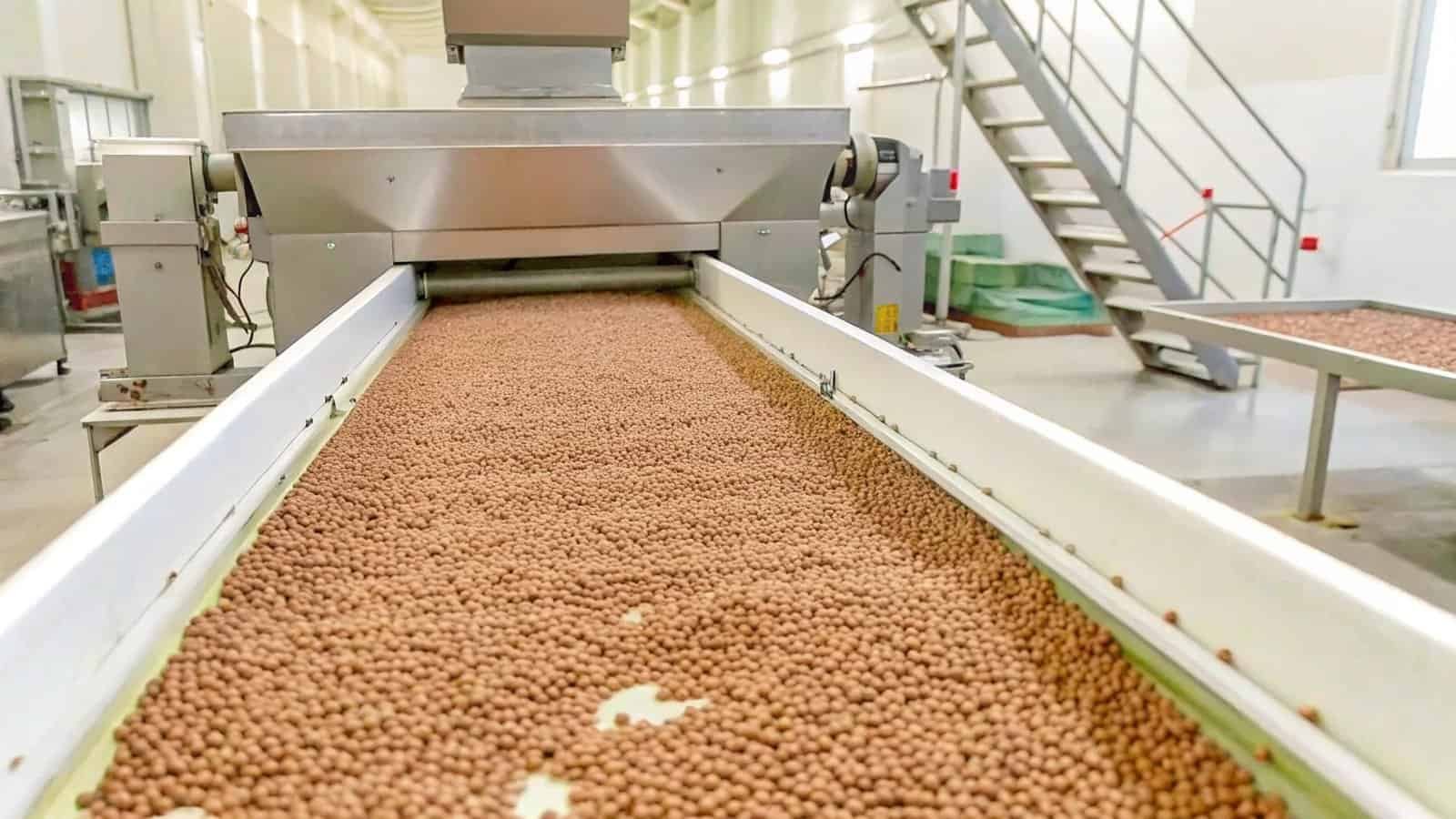
Fish farmers and feed manufacturers often struggle with choosing the right extruder for their operations. The type of extruder used directly impacts feed quality, fish growth, production efficiency, and costs. The two main types of extruders—dry and wet fish feed extruders—serve similar functions but differ in operation, cost, and final product quality. Understanding their differences is crucial to making the best choice for specific aquaculture needs.
A dry fish feed extruder operates without requiring steam or additional moisture, using friction-generated heat to cook the feed ingredients, making it energy-efficient and cost-effective. In contrast, a wet fish feed extruder requires steam pre-conditioning before extrusion, ensuring better gelatinization and digestibility, but involves higher operational costs and a more complex setup.
While both extruders produce high-quality floating and sinking fish feed, the choice depends on production scale, raw material processing, and feed nutritional requirements. Continue reading to understand the in-depth differences, advantages, and drawbacks of each type.
Wet fish feed extruders are more suitable for large-scale production than dry extruders.Igaz
Wet extruders require steam conditioning, making them ideal for high-capacity operations and ensuring superior feed quality.
1. How Do Dry and Wet Fish Feed Extruders Work?
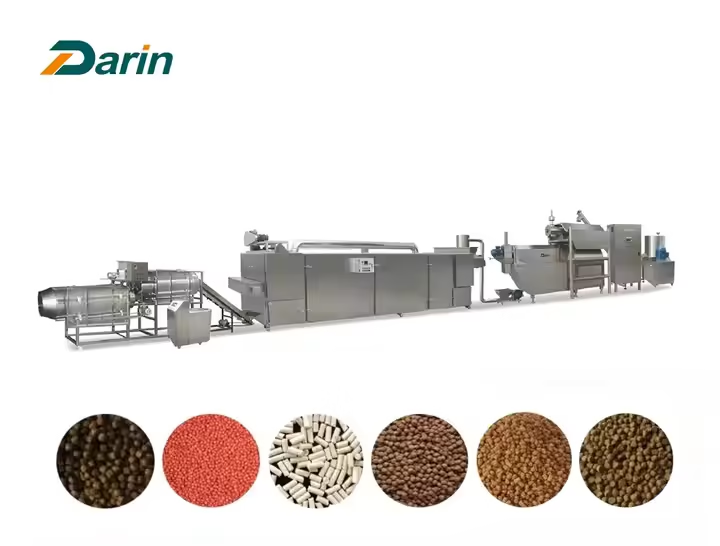
Dry Fish Feed Extruder Working Principle
A dry fish feed extruder primarily relies on mechanical energy and frictional heat to cook and shape feed ingredients. The process involves:
- Összetevőkeverés: Raw materials are ground and blended for uniform consistency.
- Screw Compression: The mixture is pushed through a high-pressure screw system.
- Heat Generation: Frictional heat from the screw mechanism causes gelatinization.
- Extrusion & Cutting: The feed is shaped and cut into pellets before cooling.
Wet Fish Feed Extruder Working Principle
A wet fish feed extruder uses steam pre-conditioning to improve the cooking process. The key steps include:
- Pre-conditioning: Steam is added to the raw ingredients, softening and partially cooking them.
- Extrudálási folyamat: The mixture passes through a screw system similar to the dry extruder.
- Enhanced Cooking: The additional heat and moisture ensure better gelatinization.
- Pellet Formation & Drying: The extruded feed is cut, dried, and cooled before packaging.
Jellemző | Dry Extruder | Wet Extruder |
---|---|---|
Steam Requirement | No | Yes |
Energiafogyasztás | Alsó | Magasabb |
Processing Temperature | Magasabb | Alsó |
Feed Digestibility | Good | Kiváló |
Pellet Durability | Mérsékelt | Magas |
Initial Investment Cost | Alsó | Magasabb |
Best for | Small/Medium Farms | Large-Scale Production |
2. Advantages and Disadvantages of Dry vs. Wet Fish Feed Extruders
Dry Fish Feed Extruder: Pros & Cons
✅ Előnyök
- Lower initial cost and operational expenses.
- Simple installation and maintenance.
- Suitable for small-scale and medium-scale fish farming.
- No need for steam boilers or complex heating systems.
- Produces stable and durable floating fish feed.
❌ Disadvantages
- Lower starch gelatinization and digestibility compared to wet extruders.
- Pellets may be less uniform in size and texture.
- Limited capacity for large-scale production.
Wet Fish Feed Extruder: Pros & Cons
✅ Előnyök
- Produces highly digestible and nutritious fish feed.
- Ensures better gelatinization and enhances feed quality.
- Ideal for large-scale and commercial feed production.
- Reduces feed waste and improves fish growth efficiency.
❌ Disadvantages
- High equipment and operational costs.
- Requires a steam boiler, increasing complexity.
- Not cost-effective for small-scale farms.
3. Production Cost Analysis: Dry vs. Wet Extruder
Cost is a significant factor in selecting the right extruder. Below is a comparative analysis of production costs between the two extruder types:
Cost Factor | Dry Extruder ($/ton) | Wet Extruder ($/ton) |
---|---|---|
Initial Investment | $5,000 - $30,000 | $20,000 - $100,000 |
Energiafogyasztás | Alsó | Magasabb |
Steam Boiler Cost | Not Required | $10,000 - $50,000 |
Maintenance Cost | Alacsony | Magas |
Feed Quality | Good | Kiváló |
Ideal Production Scale | Small to Medium | Large-scale |
Dry fish feed extruders require a steam boiler.Hamis
Dry extruders do not require steam boilers, unlike wet extruders, which use steam pre-conditioning.
4. Which Extruder Should You Choose?
Choose a Dry Fish Feed Extruder If:
✔️ You have a small or medium-sized fish farm.
✔️ You want a cost-effective és easy-to-maintain machine.
✔️ You don’t have access to steam boilers.
✔️ You need floating pellets but can compromise slightly on quality.
Choose a Wet Fish Feed Extruder If:
✔️ You operate a large-scale fish feed production business.
✔️ You want highly digestible, uniform, and premium-quality pellets.
✔️ You already have or can invest in a steam boiler.
✔️ You want the best fish growth performance and minimal feed waste.
5. Conclusion: Making the Best Choice for Your Fish Farming Business
Both dry and wet fish feed extruders have their unique advantages and limitations. A dry extruder is best for small-scale and cost-conscious farmers, while a wet extruder is ideal for large-scale commercial production due to its superior feed quality és nutritional benefits.
Before making a decision, consider your budget, production scale, feed quality requirements, and operational efficiency. If you are unsure which extruder suits your needs, consulting with a fish feed production expert can help optimize your investment.
👉 Need help choosing the right extruder? Contact us today for expert guidance and high-quality fish feed equipment!