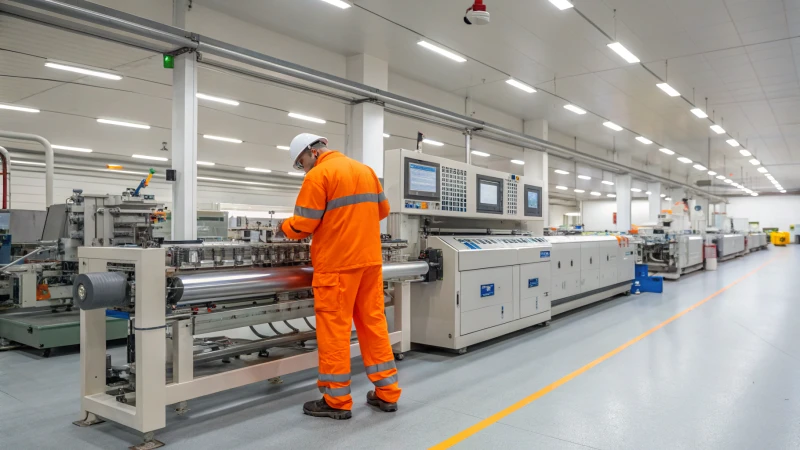
In the competitive world of pet food manufacturing, minimizing production downtime and maximizing efficiency are essential for maintaining profitability. However, many pet food manufacturers face the risk of unexpected equipment failures, which can lead to costly repairs, production delays, and even safety issues. One of the most effective strategies to avoid such disruptions is implementing a robust preventative maintenance program. Not only does preventative maintenance help reduce unexpected failures, but it also offers significant cost-saving benefits. This article will explore how a preventative maintenance strategy can save costs and improve the overall performance of pet food production operations.
Preventative maintenance (PM) saves costs in pet food production by reducing unplanned downtime, extending the lifespan of equipment, preventing major repairs, improving energy efficiency, and maintaining product quality. By proactively addressing potential issues, manufacturers can avoid expensive breakdowns, minimize waste, and optimize production processes.
The consequences of neglecting equipment maintenance are far-reaching—unexpected breakdowns can lead to costly repairs, delays, and even product recalls. Conversely, a proactive approach to maintenance can significantly reduce such risks, ensuring that the production line runs smoothly and efficiently. The following sections delve into how preventative maintenance plays a crucial role in reducing costs and improving operational efficiency.
Key Ways Preventative Maintenance Saves Costs in Pet Food Production
1. Reducing Unplanned Downtime
Unplanned downtime is one of the most significant and costly issues in pet food production. Machines breaking down unexpectedly can halt the entire production process, resulting in lost output, missed deadlines, and the potential for missed revenue. Preventative maintenance helps identify issues before they cause equipment failure, which can prevent these costly shutdowns.
How It Saves Costs:
- Scheduled downtime for maintenance is far more manageable and less costly than unexpected breakdowns.
- Predictive maintenance technologies, such as sensors and diagnostic tools, can provide early warnings of potential problems, reducing the likelihood of unscheduled downtime.
By preventing sudden equipment failures, manufacturers can maintain steady production schedules and minimize the financial impact of downtime.
2. Extending the Lifespan of Equipment
Regular maintenance is key to prolonging the life of production equipment. The longer machinery operates without failure, the more cost-effective it becomes. Equipment that is neglected or poorly maintained tends to wear out faster, leading to frequent repairs or even complete replacement.
How It Saves Costs:
- Reduced frequency of major repairs: Preventative maintenance helps avoid the wear and tear that typically leads to expensive overhauls.
- Extended equipment life: Regular servicing, lubrication, and part replacements prevent premature failure and extend the lifespan of machinery.
By increasing the life expectancy of equipment, manufacturers can avoid the high costs associated with frequent replacements or upgrades.
3. Preventing Major Repairs
One of the biggest advantages of preventative maintenance is its ability to identify small issues before they turn into major, expensive repairs. For instance, worn-out seals, bearings, or motors, if left unchecked, can lead to system-wide failures that require costly repairs and extended downtime.
How It Saves Costs:
- Early detection of small issues allows for repairs to be made before they escalate into larger, more expensive problems.
- Lower repair costs: Addressing minor issues early can significantly reduce the expense of major repairs that might require replacement parts or extensive labor.
A well-implemented PM program can help catch problems while they’re still manageable, preventing them from spiraling into large-scale repair needs.
4. Improving Energy Efficiency
Pet food production machinery often runs for extended periods, consuming significant amounts of energy. Regular maintenance can optimize the energy efficiency of machinery, ensuring that it operates within optimal performance levels.
How It Saves Costs:
- Lubrication and cleaning reduce friction, improving the overall efficiency of machines, such as mixers, extruders, and conveyors.
- Calibration of machines can ensure that they are running at the most efficient speeds, reducing unnecessary energy consumption.
- Proper alignment and maintenance of motors and pumps ensures that equipment doesn’t overconsume power, reducing electricity costs.
By improving energy efficiency, manufacturers can significantly lower utility bills, contributing to long-term savings.
5. Maintaining Product Quality and Consistency
Inconsistent or faulty production equipment can lead to defects in the final pet food product, such as incorrect ingredient blending or improper cooking. This can result in costly product recalls, customer dissatisfaction, and potential regulatory issues.
How It Saves Costs:
- Regular calibration and inspection ensure that machines like mixers and extruders are working correctly, producing consistent product quality.
- Preventing contamination: Proper cleaning and sanitation as part of preventative maintenance help prevent the buildup of residues, ensuring that raw materials are processed correctly and safely.
By preventing product defects and ensuring consistent quality, manufacturers can avoid the financial costs associated with recalls and reputational damage.
6. Reducing Waste and Overproduction
Inefficient machines or improperly calibrated equipment can lead to waste in the production process. For instance, overmixing ingredients or undercooking pet food products can lead to defective batches that need to be discarded.
How It Saves Costs:
- Better ingredient control: Regular maintenance ensures that mixers, extruders, and other machinery are calibrated to work with the right quantities of ingredients, minimizing waste.
- Improved consistency: Properly functioning machines ensure that each batch is produced to the correct specifications, avoiding overproduction or underproduction.
Reducing waste and overproduction allows manufacturers to make the most of their raw materials, ensuring maximum profitability.
7. Avoiding Regulatory Fines and Penalties
In the pet food industry, manufacturers must adhere to strict safety and quality standards set by regulatory bodies. Equipment failures that result in safety violations, contamination, or production errors can lead to costly fines or legal action.
How It Saves Costs:
- Regular checks for compliance: Preventative maintenance ensures that equipment meets the necessary standards, reducing the risk of non-compliance.
- Improved safety: Regular safety checks, including temperature control and sanitation, help maintain a safe production environment and prevent penalties related to food safety violations.
By ensuring equipment meets regulatory requirements, manufacturers can avoid the costs associated with fines, recalls, or legal battles.
Preventative Maintenance: A Cost-Effective Strategy
The Cost Comparison: Preventative Maintenance vs. Reactive Maintenance
Maintenance Type | Average Costs | Impact on Operations |
---|---|---|
Preventative Maintenance | Low to Moderate | Reduced downtime, fewer repairs, longer equipment lifespan |
Reactive Maintenance | Magas | Expensive repairs, increased downtime, potential production delays, and reduced product quality |
The table above highlights how preventative maintenance (PM) provides a far more cost-effective approach compared to reactive maintenance. While PM requires a smaller, ongoing investment in terms of labor and materials, the costs of reactive maintenance—such as emergency repairs and unplanned downtime—can be significantly higher. Furthermore, reactive maintenance often results in lost revenue due to production delays, which PM can prevent.
Következtetés
Preventative maintenance is a powerful tool for pet food manufacturers looking to reduce operational costs and enhance production efficiency. By focusing on regular inspections, early issue detection, energy optimization, and consistent product quality, manufacturers can not only avoid costly repairs but also extend the lifespan of equipment, reduce waste, and improve overall profitability. Investing in preventative maintenance is an investment in the long-term success and sustainability of your business.
CTA: Lépjen kapcsolatba velünk
To learn more about how preventative maintenance can benefit your pet food production operations or to schedule a consultation for implementing a tailored maintenance program, get in touch with us today. Our team of experts is ready to help you maximize the performance of your machinery and minimize your operational costs.