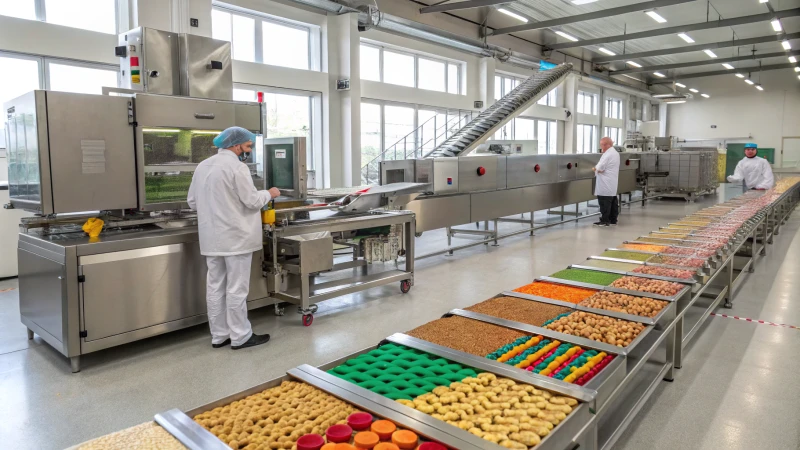
Have you ever wondered how your dog’s favorite kibble or cat’s moist meal is made? Manufacturing pet food is a precise, multifaceted process that blends science, technology, and quality control to ensure a safe, nutritious product for pets. The process involves multiple stages, from ingredient sourcing and formulation to cooking, testing, and packaging. Understanding how pet food is manufactured is key for any pet food business owner or consumer interested in the product's quality and production standards.
Pet food production is divided into two major categories: wet food and dry food, each with its own unique manufacturing process. The production of wet food typically involves a more delicate cooking process to preserve the moisture and nutrients, while dry food, commonly known as kibble, is baked or extruded to create a crispy texture. Both processes require specialized equipment, rigorous quality checks, and adherence to food safety regulations.
This article will guide you through the entire pet food manufacturing process, step by step, from ingredient sourcing to the final packaging, ensuring that you get a complete picture of how the food ends up in your pet’s bowl.
1. Ingredient Sourcing and Quality Control
The first step in the pet food manufacturing process begins with sourcing high-quality ingredients. The quality of ingredients plays a vital role in ensuring the final product is nutritious and safe for pets. Common ingredients in pet food include meat, poultry, fish, grains, vegetables, and added nutrients like vitamins and minerals.
Key Factors in Ingredient Sourcing:
- Protein Sources: Chicken, beef, turkey, lamb, and fish are common animal proteins used in pet food.
- Grains & Vegetables: Brown rice, sweet potatoes, peas, and carrots are added for carbohydrates and fiber.
- Vitamins & Minerals: Added for balanced nutrition.
- Preservatives: Natural preservatives like tocopherols (Vitamin E) and ascorbic acid (Vitamin C) are used to ensure shelf life.
Ingredient quality control ensures that all ingredients meet the necessary standards for pet consumption. Manufacturers often establish long-term relationships with reputable suppliers who meet stringent standards for sourcing and providing ingredients. Every ingredient batch is tested for contamination, microbial safety, and nutrient content to guarantee that only high-quality materials are used in the production process.
2. Formulation and Recipe Development
Once the ingredients are sourced, the next step is formulating the pet food recipe. This is the stage where nutritionists and veterinarians work to create a recipe that balances all the essential nutrients pets need, such as protein, fats, carbohydrates, vitamins, and minerals.
Key Aspects of Pet Food Formulation:
- Species-Specific Needs: Dogs, cats, and other pets have different nutritional requirements, so formulations are tailored to each species.
- Life Stage Considerations: Puppies and kittens, adult pets, and senior animals have different dietary needs.
- Health Conditions: Special formulations may be required for pets with allergies, sensitivities, or medical conditions like obesity, kidney disease, or digestive issues.
Scientific analysis and trial batches are created to fine-tune the recipe. Once a formula is finalized, it undergoes a trial period to ensure the pets like the taste and the food is safe for consumption.
3. Processing Methods: Wet vs Dry Food
There are two main types of pet food: wet food (often called canned food) and dry food (kibble). Each type requires a different manufacturing process due to their distinct textures and moisture content.
Wet Food Processing
Wet pet food contains about 70% moisture, making it soft and easy to eat for pets that might have dental issues or need extra hydration. The canning process involves heating ingredients to sterilize them, ensuring the food is safe and stable for long periods.
Dry Food Processing
Dry pet food, on the other hand, has less moisture (about 10%), which gives it a longer shelf life and a crunchy texture that helps maintain dental health. The manufacturing process for dry food typically involves extrusion, baking, or other cooking methods to create crunchy pieces.
4. The Extrusion Process for Dry Food
Extrusion is the most common method used to produce dry kibble pet food. It involves cooking and shaping the food under high heat and pressure. The process is fast, cost-effective, and can create various shapes and sizes of kibble, suitable for different pet breeds and sizes.
Steps in the Extrusion Process:
- Mixing: Ingredients are blended in large mixers to create a uniform dough.
- Cooking: The dough is heated in an extruder, where it is subjected to high temperature and pressure. This step ensures the food is cooked thoroughly and makes it easy to digest.
- Shaping: The food is forced through a die (mold) to form the kibble shapes. Different shapes and sizes can be created depending on the die used.
- Drying: The shaped kibble is dried to remove excess moisture, ensuring it stays crispy and shelf-stable.
- Coating: A coating of fats, oils, and sometimes flavorings is added to the kibble to enhance taste and appeal.
The extrusion process is efficient and produces a consistent, high-quality product. It also allows manufacturers to add functional ingredients like joint supplements, probiotics, or flavor enhancers during the coating stage.
5. The Canning and Cooking Process for Wet Food
Wet pet food undergoes a more involved cooking process that preserves the moisture while maintaining the nutritional integrity of the ingredients. The food is packed into cans or pouches before being cooked.
Steps in Wet Food Processing:
- Preparation: Ingredients (meat, vegetables, broth) are prepared and mixed.
- Filling: The prepared mixture is packed into cans or pouches.
- Sealing: The cans or pouches are sealed to create a vacuum, ensuring no air enters and the product remains sterile.
- Sterilizing: The sealed cans are placed in a pressure cooker (retort) and heated to high temperatures for several hours. This step kills any harmful bacteria and extends shelf life.
- Cooling: After sterilization, the cans are cooled down quickly to stop the cooking process.
- Labeling: The finished cans or pouches are labeled and ready for distribution.
The canning process ensures that wet food retains its moisture and flavors while providing a shelf-stable product that can last for months without refrigeration.
6. Nutritional Testing and Quality Control
Before pet food can be sold to consumers, it must undergo rigorous nutritional testing to ensure it meets the standards set by regulatory bodies like the AAFCO (Association of American Feed Control Officials). Pet food manufacturers must conduct tests to verify that the food contains the right balance of nutrients, is free from contaminants, and is safe for pets to consume.
Types of Quality Control Measures:
- Nutritional Testing: To confirm that the pet food provides adequate protein, fats, vitamins, and minerals.
- Microbial Testing: Ensuring the food is free from harmful bacteria like Salmonella or E. coli.
- Sensory Evaluation: Taste tests and appearance checks to ensure consistency in the final product.
Each batch of pet food is tested before it reaches the market to ensure it meets both nutritional standards and safety requirements.
7. Packaging and Labeling
Once the food is produced and tested, it is packaged and labeled. Packaging serves two main purposes: protection and marketing. The packaging must keep the food safe from contamination, while the labels must provide essential information such as nutritional content, ingredients, expiration date, and storage instructions.
Types of Packaging:
- Plastic Bags: Common for dry food and kibble.
- Cans: Popular for wet food.
- Pouches: Used for both wet and dry food, often for convenience.
- Eco-Friendly Packaging: Increasingly popular as consumers demand more sustainable options.
Labels must comply with regulatory requirements and often include detailed information on the ingredients, nutritional value, feeding guidelines, and manufacturing details.
8. Pet Food Safety Regulations and Compliance
Pet food manufacturing is regulated by agencies such as the FDA (Food and Drug Administration) and AAFCO, ensuring that all products are safe and meet
minimum nutritional standards. Manufacturers must adhere to Good Manufacturing Practices (GMP) and regular audits to maintain their compliance with health and safety regulations.
9. How Technology is Revolutionizing Pet Food Manufacturing
Advances in technology have had a major impact on the pet food manufacturing process, from ingredient sourcing and recipe formulation to packaging and distribution. AI and data analytics are being used to track quality, predict demand, and optimize production schedules. Automation in production lines has increased efficiency, reduced human error, and minimized operational costs.
Conclusion: The Journey from Ingredients to Pet’s Bowl
Manufacturing pet food is a complex, multi-step process that blends science, engineering, and strict quality control standards. From sourcing high-quality ingredients and formulating nutritionally balanced recipes to cooking, testing, and packaging, every step must be carefully managed to ensure the safety and nutrition of the final product. With advances in technology and stringent regulations, the pet food industry continues to evolve, providing safe and nutritious options for pets worldwide.
Call to Action
Ready to start your pet food journey? Whether you're a pet food manufacturer looking for guidance or a pet owner curious about what's in your pet’s food, reach out to us today for expert insights and resources.
External Footnotes & Recommended Explanation Text
- Learn about pet food regulations and safety compliance
- Explore innovations in pet food packaging solutions
- Find out more about extrusion processes in pet food manufacturing
- Read about advances in pet food nutrition
- Discover how AI is revolutionizing pet food production
- Understand the basics of pet food labeling and packaging regulations
- Check out the latest trends in sustainable pet food packaging
- Learn about pet food testing standards
- Explore how extrusion helps in pet food quality control
- Know more about raw materials used in pet food production