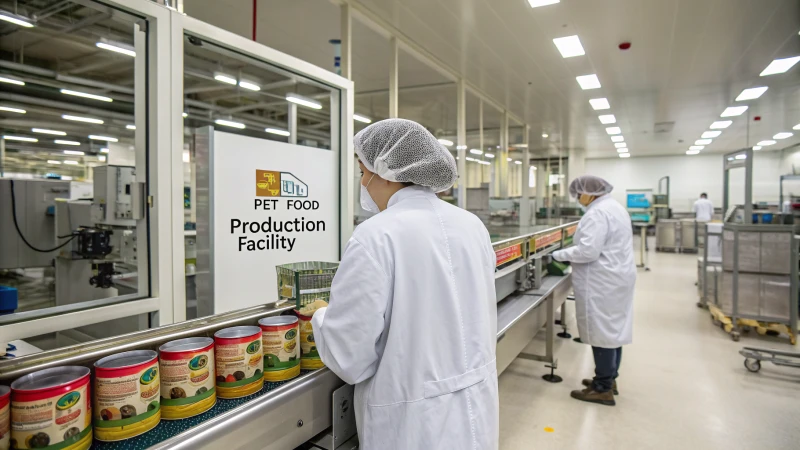
Wet pet food is a popular choice among pet owners due to its high moisture content, palatability, and nutritional benefits. However, producing wet pet food requires a specialized production line that ensures quality, efficiency, and safety. If not properly manufactured, wet pet food can suffer from contamination, inconsistent texture, or nutritional imbalances, leading to poor pet health and product recalls. To avoid these issues, manufacturers must understand how a wet pet food production line functions and the key stages involved in the process.
A wet pet food production line is a series of interconnected machines and processes designed to manufacture, cook, and package wet pet food efficiently. It includes raw material preparation, mixing, cooking, canning or pouching, sterilization, and quality control. The process ensures that pet food meets nutritional, safety, and regulatory standards while maintaining consistency in texture and flavor.
Understanding how a wet pet food production line works is essential for manufacturers looking to optimize production efficiency and product quality. Below, we break down the key stages of the production process and the critical factors to consider.
What Are the Key Components of a Wet Pet Food Production Line?
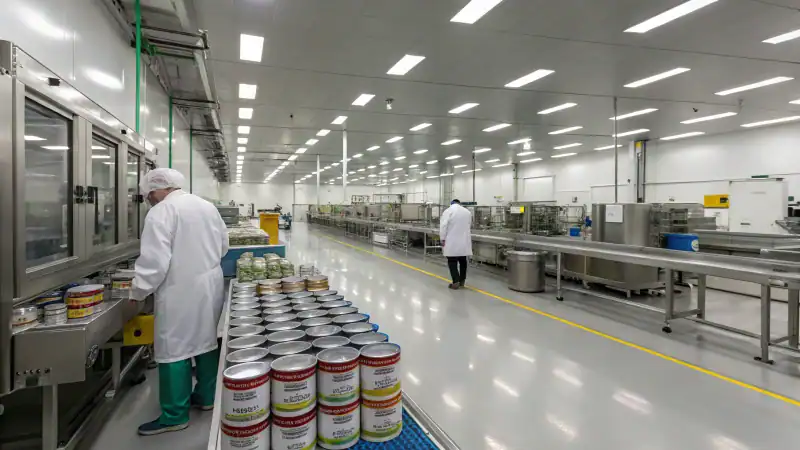
Understanding the Importance of a Wet Pet Food Production Line
The pet food industry has seen significant growth as pet owners demand higher-quality and nutritionally balanced meals for their pets. Wet pet food, known for its high moisture content and palatability, requires a sophisticated production line to ensure safety, consistency, and compliance with food industry standards. Without the right components, manufacturers risk contamination, inefficiencies, and inconsistent product quality, which can lead to financial loss and reputational damage.
Key Components of a Wet Pet Food Production Line
A wet pet food production line consists of several key components, including raw material handling, grinding and mixing equipment, cooking and sterilization units, filling and packaging systems, quality control mechanisms, and storage solutions. Each component plays a crucial role in ensuring efficiency, hygiene, and compliance with industry standards.
A well-optimized wet pet food production line not only guarantees product safety but also enhances production efficiency, minimizes waste, and ensures cost-effective operations. Let’s explore each of these critical components in detail.
1. Raw Material Handling and Preparation
Importance of Raw Material Handling
The foundation of any wet pet food production line is the selection and handling of raw materials. This includes:
- Meat and Protein Sources: Chicken, beef, fish, lamb, or organ meats.
- Vegetables and Grains: Carrots, peas, potatoes, and rice for nutritional balance.
- Vitamins and Supplements: Essential nutrients added to meet dietary requirements.
Key Equipment for Raw Material Handling
Equipment Name | Fonction |
---|---|
Receiving Bins | Collect raw ingredients upon arrival. |
Cold Storage Units | Maintain the freshness of perishable ingredients. |
Weighing and Dosing Systems | Ensure precise ingredient proportions. |
Grinding Machines | Reduce meat and vegetables into a uniform consistency. |
Proper handling prevents contamination and ensures the right balance of ingredients for nutritional adequacy.
2. Grinding and Mixing Systems
The Role of Grinding in Wet Pet Food Processing
Grinding is essential for breaking down meat and other ingredients into smaller, digestible pieces. The finer the grind, the smoother and more homogenous the final product.
Types of Mixing Equipment
Mixer Type | Fonction |
---|---|
Batch Mixers | Process ingredients in controlled quantities. |
Continuous Mixers | Maintain a steady, uninterrupted mixing process. |
Vacuum Mixers | Remove air bubbles to enhance texture and consistency. |
Efficient grinding and mixing ensure that the wet pet food maintains a uniform composition and palatability.
3. Cooking and Sterilization Systems
Importance of Cooking in Wet Pet Food
Cooking helps to sterilize the ingredients, improve digestibility, and enhance flavor.
Cooking and Sterilization Equipment
Equipment Name | Fonction |
---|---|
Steam Cookers | Heat ingredients to safe temperatures. |
Extrudeuses | Shape and pre-cook wet pet food for uniformity. |
Retort Sterilization Chambers | Kill bacteria and extend shelf life. |
Without proper cooking and sterilization, pet food may harbor harmful bacteria like Salmonella or Listeria.
4. Filling and Packaging Systems
Efficient and Hygienic Filling Solutions
Once the wet pet food is cooked and sterilized, it must be filled into cans, pouches, or trays.
Filling Method | Avantages |
---|---|
Vacuum Fillers | Prevents air pockets, maintains consistency. |
Piston Fillers | Ensures precise portioning and viscosity control. |
Packaging Types and Sealing
Type d'emballage | Avantages |
---|---|
Cans (Metal Tins) | Durable, long shelf life, widely used. |
Pouches | Lightweight, cost-effective, convenient. |
Plastic Trays | Ideal for single-serve portions. |
A well-designed packaging system enhances product shelf stability and appeal.
5. Quality Control and Compliance Checks
Ensuring Product Safety and Consistency
Every wet pet food batch must undergo rigorous quality control to meet industry standards.
Quality Control Step | Objectif |
---|---|
Metal Detection | Detects foreign objects. |
Viscosity Testing | Ensures proper consistency. |
Microbiological Testing | Checks for bacteria and contaminants. |
Label Inspection | Verifies correct ingredient declarations. |
Adhering to strict quality checks prevents recalls and ensures compliance with pet food safety regulations.
6. Storage and Distribution
Importance of Proper Storage
Proper storage conditions preserve product quality and prevent spoilage.
Storage Type | Fonction |
---|---|
Refrigerated Storage | Keeps perishable raw materials fresh. |
Finished Product Warehouses | Stores packaged goods before distribution. |
Automated Retrieval Systems | Enhances efficiency in inventory management. |
An efficient distribution network ensures that the wet pet food reaches retailers and pet owners in optimal condition.
Conclusion: Optimizing Wet Pet Food Production for Quality and Efficiency
A well-designed wet pet food production line is essential for delivering high-quality, nutritious, and safe pet food. From raw material handling to quality control, each component contributes to ensuring efficiency, hygiene, and regulatory compliance. Investing in state-of-the-art processing technology can significantly enhance productivity, reduce waste, and improve profitability.
Looking to upgrade your wet pet food production line? Contact us today to discuss high-efficiency solutions tailored to your business needs!
How Are Raw Ingredients Prepared for Wet Pet Food?
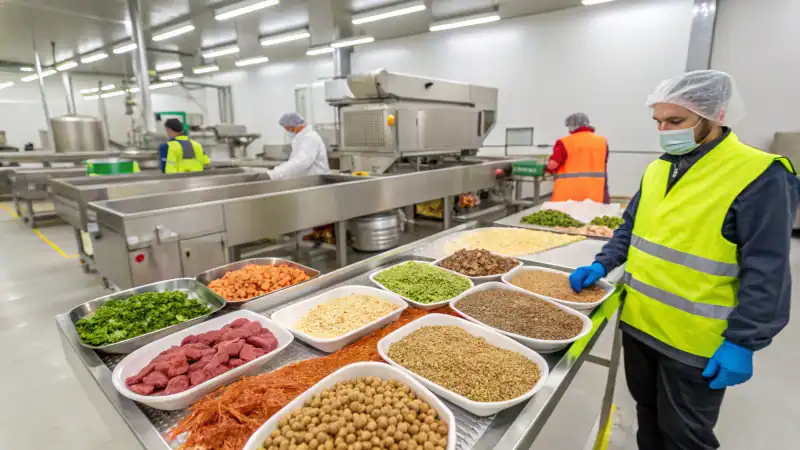
When it comes to wet pet food, pet owners expect high-quality, nutritious, and safe meals for their furry companions. However, many don’t realize the extensive preparation required to ensure these foods meet strict quality and safety standards. Raw ingredients must go through a rigorous series of steps, including sourcing, handling, processing, and sterilization, before they are transformed into the appetizing wet pet food found on store shelves. Failure to properly prepare these ingredients can lead to contamination, spoilage, or nutrient loss, impacting pet health. So, how exactly are raw ingredients prepared for wet pet food production? Let’s dive into the details.
Raw ingredients for wet pet food undergo a meticulous preparation process that includes selection, inspection, cleaning, grinding, mixing, cooking, and sterilization. High-quality meats, vegetables, and grains are sourced from trusted suppliers, tested for safety, and processed under strict hygiene standards to ensure optimal nutrition and shelf stability.
Understanding the full scope of wet pet food ingredient preparation will help pet owners make informed choices and appreciate the effort that goes into crafting safe and nutritious meals for their pets. Let’s explore the step-by-step journey from raw ingredient selection to the final wet pet food product.
1. Sourcing High-Quality Ingredients
The first step in preparing raw ingredients for wet pet food is sourcing high-quality raw materials. This includes:
- Meat and Animal Proteins: Chicken, beef, lamb, fish, and organ meats are commonly used. Some brands incorporate novel proteins like duck or rabbit for pets with dietary sensitivities.
- Vegetables and Grains: Carrots, peas, sweet potatoes, brown rice, and other grains provide essential vitamins and fiber.
- Graisses et huiles: Fish oil, chicken fat, and plant-based oils contribute to palatability and provide essential fatty acids.
- Supplements: Vitamins, minerals, and amino acids are often added to ensure complete and balanced nutrition.
These ingredients are procured from suppliers who must meet strict regulatory standards regarding food safety, sustainability, and ethical sourcing.
2. Inspection and Quality Control
Before entering the processing facility, raw ingredients undergo rigorous inspection and testing to ensure they are safe for consumption. This includes:
- Microbiological Testing: Screening for bacteria like Salmonella, E. coli, and Listeria.
- Chemical Testing: Checking for contaminants, pesticides, and heavy metals.
- Analyse nutritionnelle: Ensuring protein, fat, and vitamin content meet specifications.
If any raw ingredient does not meet quality standards, it is rejected and replaced with a safe alternative.
3. Cleaning and Preparation
Once approved, raw ingredients are cleaned and prepped for processing:
- Viandes et protéines animales: Excess fat, bones, and unwanted materials are removed.
- Vegetables and Grains: Washed thoroughly to remove dirt and contaminants.
- Frozen Ingredients: Thawed under controlled conditions to prevent bacterial growth.
Hygiene and sanitation are strictly maintained to prevent cross-contamination at this stage.
4. Grinding and Mixing
Next, the cleaned ingredients are processed into a uniform mixture:
- Grinding: Meats and vegetables are ground into smaller particles for better digestibility and texture.
- Blending: Ingredients are mixed with added vitamins, minerals, and other functional components.
- Moisture Control: Water or broth is added to achieve the desired consistency.
This ensures the final wet pet food has a consistent texture, flavor, and nutrient distribution.
5. Cooking and Heat Treatment
Cooking plays a crucial role in making wet pet food safe and palatable:
- Batch Cooking: Ingredients are cooked at controlled temperatures to eliminate harmful bacteria while preserving nutrients.
- Hydrolyzation: Some pet foods use hydrolyzed proteins for pets with food sensitivities.
- Temperature Monitoring: Cooking is carefully controlled to prevent nutrient degradation.
The cooking process enhances digestibility, flavor, and shelf stability.
6. Can Filling and Sealing
After cooking, the pet food mixture is transferred to cans, trays, or pouches:
- Precise Portioning: Automated systems ensure each package contains the correct amount.
- Vacuum Sealing: Helps preserve freshness and prevents contamination.
- Labeling: Each package is labeled with ingredient information and expiration dates.
The sealed containers protect the food from external contamination and oxidation.
7. Sterilization and Final Safety Checks
To ensure the product is completely safe, final sterilization is performed:
- Retort Processing: Canned pet food undergoes high-temperature pressure sterilization to kill any remaining bacteria.
- Shelf-Life Testing: Samples are tested to confirm stability over time.
- Quality Assurance Checks: Final tests are conducted for taste, texture, and safety compliance.
Sterilization ensures the pet food remains fresh and safe for consumption.
Comparison of Raw Ingredient Preparation Methods
Process Step | Objectif | Key Benefits |
---|---|---|
Sourcing | Obtaining high-quality ingredients | Ensures nutritional value and safety |
Inspection & Testing | Screening for contaminants | Prevents bacterial and chemical hazards |
Nettoyage | Washing and removing impurities | Reduces contamination risk |
Grinding & Mixing | Creating a uniform texture | Improves digestibility and nutrient balance |
Cooking | Heat treatment | Destroys pathogens and enhances flavor |
Filling & Sealing | Packaging the product | Extends shelf life and prevents spoilage |
Sterilization | Final safety measure | Ensures long-term food safety |
Key Nutrients Retained Through Processing
Despite heat processing, essential nutrients are preserved or added back through supplementation:
Nutriments | Source | Benefit for Pets |
---|---|---|
Protein | Meat, fish, poultry | Supports muscle development |
Omega-3 Fatty Acids | Fish oil, flaxseed | Promotes skin and coat health |
Vitamins A, D, E | Fortified supplements | Boosts immune function |
Fibre | Vegetables, grains | Aids digestion |
The preparation of raw ingredients for wet pet food involves a meticulous process designed to ensure safety, nutrition, and palatability. From sourcing high-quality ingredients to rigorous testing, cooking, and sterilization, manufacturers adhere to strict protocols to produce a wholesome product for pets. Understanding this process can help pet owners make more informed choices about the food they provide to their furry companions.
What Happens During the Mixing and Formulation Stage in Wet Pet Food Production?
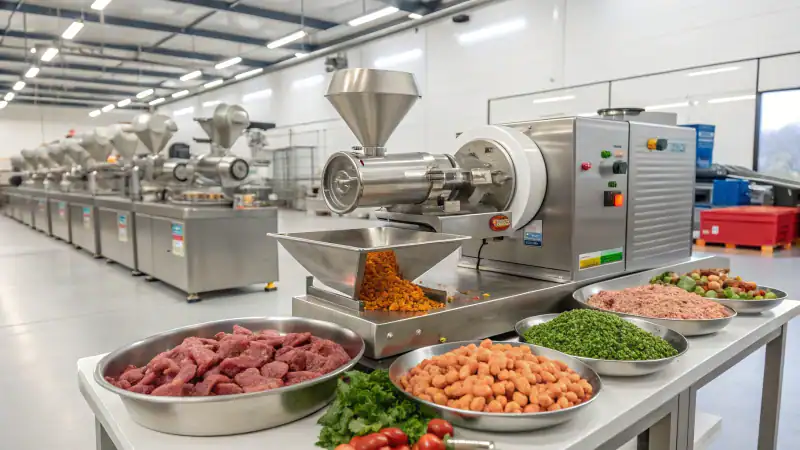
In the wet pet food industry, ensuring the highest quality, nutritional balance, and palatability of pet food starts with the mixing and formulation stage. This critical process determines the product’s texture, taste, and nutritional value. If improperly handled, issues such as nutrient imbalance, contamination, or inconsistent texture can arise, affecting both pet health and manufacturer reputation. Understanding this stage helps industry professionals improve efficiency, product quality, and compliance with safety standards.
The mixing and formulation stage in wet pet food production involves carefully selecting and blending raw materials, including meats, grains, vitamins, and minerals, to create a homogeneous mixture that meets specific nutritional profiles. This process ensures consistency, enhances digestibility, and optimizes texture before further processing.
To fully grasp this complex stage, let’s explore the step-by-step formulation and mixing process, le types of mixing equipment used, key mesures de contrôle de la qualité, and how modern technology is improving precision in wet pet food production.
1. Understanding Ingredient Formulation in Wet Pet Food
The formulation process begins by defining the nutritional requirements for the final pet food product. Nutritionists and food scientists develop precise recipes based on AAFCO (Association of American Feed Control Officials) or FEDIAF (European Pet Food Industry Federation) guidelines, ensuring a balanced diet for different pet species, breeds, and life stages.
Key Ingredients in Wet Pet Food Formulation:
Type d'ingrédient | Function in Pet Food | Exemples |
---|---|---|
Protein Sources | Essential for muscle growth, repair, and energy | Chicken, beef, fish, lamb, liver, organ meats |
Carbohydrates | Provides energy and fiber for digestion | Rice, sweet potatoes, barley, corn |
Fats & Oils | Supports skin, coat health, and energy levels | Fish oil, chicken fat, sunflower oil |
Vitamins & Minerals | Ensures proper metabolic functions and health | Calcium, phosphorus, zinc, vitamins A, D, E |
Binders & Gelling Agents | Controls texture and moisture retention | Guar gum, carrageenan, starches |
Formulation is done using computerized feed formulation software, ensuring the correct balance of macronutrients and micronutrients for specific pet needs.
2. The Mixing Process: Achieving Homogeneous Blends
Once ingredients are selected, they enter the mixing phase, where raw materials are blended into a uniform mixture. The goal is to ensure even distribution of nutrients, texture consistency, and optimal palatability.
Step-by-Step Mixing Process
-
Weighing and Pre-Blending:
- Ingredients are pre-weighed based on the formulation recipe.
- Dry and liquid components may be mixed separately before combination.
-
Batch Mixing:
- Large industrial mixers (e.g., ribbon blenders, paddle mixers) mix proteins, grains, and liquid components.
- A controlled mixing time and speed are maintained for uniformity.
-
Emulsification (If Required):
- High-speed emulsifiers break down meat and fat particles into a fine paste for smooth texture.
- This improves digestibility and product consistency.
-
Hydrocolloid Addition (Gelling Agents):
- Guar gum, carrageenan, or starches are added to create a gel-like consistency, which helps retain moisture.
- Proper dispersion prevents separation of ingredients.
-
Homogenization:
- The final blend is passed through homogenizers to eliminate large particles.
- This step enhances product stability and appearance.
Types of Mixing Equipment Used in Wet Pet Food Production
Type d'équipement | Fonction | Commonly Used For |
---|---|---|
Paddle Mixers | Gently blends wet and dry ingredients | Large batch production |
Ribbon Blenders | Uniformly mixes powders, proteins, and starches | Dry and semi-wet formulations |
Emulsifiers | Breaks down meat and fat into fine consistency | Pâté-style pet food |
Vacuum Mixers | Removes air for better texture and preservation | High-end pet food production |
3. Quality Control Measures in the Mixing and Formulation Stage
Maintaining strict quality control during this stage ensures product safety, consistency, and compliance with pet food regulations. Key quality control checkpoints include:
Critical Control Points (CCPs) During Mixing:
Quality Check | Objectif | Testing Methods |
---|---|---|
Ingredient Quality Check | Ensures raw materials meet safety and nutritional standards | Microbial testing, sensory evaluation |
Moisture Content Control | Prevents over-hydration or dehydration | Moisture analyzers |
Protein and Fat Analysis | Ensures compliance with guaranteed analysis | Near-infrared (NIR) spectroscopy |
Homogeneity Testing | Verifies even distribution of nutrients | Sample testing via lab analysis |
Microbial Safety Checks | Prevents contamination (Salmonella, E. coli) | Swab tests, PCR detection |
4. Technological Innovations in Pet Food Mixing and Formulation
Advancements in automation, precision dosing, and real-time quality monitoring are revolutionizing the pet food manufacturing industry.
Modern Innovations Improving Mixing & Formulation
L'innovation | Avantages |
---|---|
Automated Ingredient Dosing Systems | Eliminates human error, improves accuracy |
AI-Based Nutritional Optimization | Ensures balanced diets, reduces formulation costs |
Real-Time Quality Sensors | Detects inconsistencies in texture and nutrient distribution |
High-Pressure Processing (HPP) | Enhances safety without preservatives |
These technologies help manufacturers streamline production, reduce waste, and ensure product consistency.
Conclusion: Why Precision in Mixing & Formulation Matters
Le mixing and formulation stage in wet pet food production is crucial for ensuring quality, safety, and palatability. From ingredient selection to batch mixing and quality control, every step determines the final product’s nutritional value and appeal to pets. With the integration of automation and AI-driven systems, manufacturers can achieve greater efficiency, regulatory compliance, and superior pet food products.
For pet food manufacturers looking to enhance their formulation and mixing processes, adopting precision equipment and quality control technologies is the key to staying competitive in the industry.
Need expert guidance on optimizing your wet pet food production? Contact us today for advanced formulation and mixing solutions!
How Is Wet Pet Food Cooked and Industrially Processed?
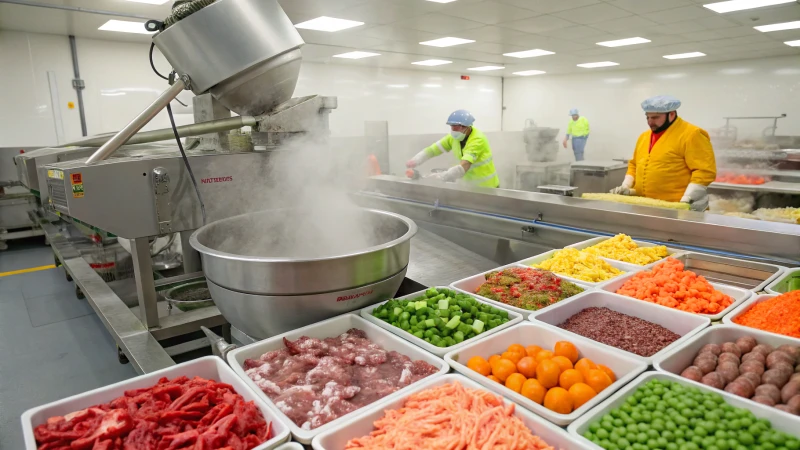
Wet pet food is a staple for pet owners looking to provide a high-moisture, nutrient-rich diet to their pets. However, many pet owners are unaware of the detailed industrial processes behind manufacturing wet pet food. Improper processing can lead to nutrient degradation, contamination, or spoilage, making it essential to understand the rigorous steps involved in its production. By learning about the production process, pet owners can make informed choices about their pet’s diet, ensuring they get the best quality food available.
How Is Wet Pet Food Processed?
Wet pet food is processed using a combination of ingredient selection, mixing, cooking, sterilization, and packaging. The process involves grinding raw materials, blending them into a homogenous mixture, heat-processing them in retort machines to ensure sterility, and sealing them in cans or pouches to extend shelf life while maintaining nutritional integrity.
To fully understand the industrial process behind wet pet food, let's break it down step by step and explore how manufacturers ensure safety, quality, and nutrition.
1. Raw Material Selection and Preprocessing
Before wet pet food is even mixed or cooked, raw materials go through a thorough selection and preparation process.
Types of Raw Ingredients Used in Wet Pet Food
Type d'ingrédient | Example Sources | Purpose in Pet Food |
---|---|---|
Protein Sources | Chicken, Beef, Fish, Lamb | Provides essential amino acids |
Carbohydrates | Rice, Potatoes, Peas | Supplies energy and fiber |
Graisses et huiles | Chicken fat, Fish oil | Enhances palatability and provides essential fatty acids |
Vitamins & Minerals | Vitamin A, Zinc, Calcium | Supports immune function, bones, and metabolism |
Gelling Agents | Agar, Carrageenan, Guar Gum | Helps maintain texture and consistency |
The raw ingredients undergo multiple quality control checks for contaminants, spoilage, and nutritional consistency. Meat and fish products are usually delivered frozen or refrigerated to maintain freshness.
2. Grinding and Mixing of Ingredients
Once raw materials are approved, they are ground into a fine consistency using industrial grinders. The goal of this step is to ensure uniformity in the final product.
- Grinding Process: Large pieces of meat, bones, and plant-based ingredients are ground down to a manageable texture.
- Mixing Process: A high-speed mixer blends proteins, carbohydrates, and other essential nutrients into a homogenous mixture. Water or broth is added to maintain moisture levels and improve palatability.
Nutrient Retention During Mixing
Factor Affecting Nutrition | Impact on Wet Pet Food | Solution |
---|---|---|
High Temperature | Can degrade heat-sensitive vitamins | Add vitamins after cooling |
Oxygen Exposure | May cause oxidation of fats | Use nitrogen-flushed packaging |
Uneven Mixing | Leads to inconsistent nutrient distribution | Automated precision mixing |
3. Cooking and Heat Processing
The cooking process is critical to ensuring pet food safety. It eliminates harmful bacteria and improves digestibility.
Cooking Methods Used in Wet Pet Food Manufacturing
- Steam Cooking: Ingredients are cooked at precise temperatures using steam to retain moisture and flavor.
- Batch Cooking: Large quantities are slowly cooked in industrial kettles for even heat distribution.
- Continuous Cooking: Automated systems move food through heated chambers to achieve consistent sterilization.
Cooking pet food at high temperatures destroys all essential nutrients.Faux While high heat can degrade some vitamins, manufacturers compensate by adding heat-stable vitamins and minerals after cooking.
4. Canning and Filling Process
After cooking, the wet pet food is portioned into cans, pouches, or trays. This step is essential for product consistency and long shelf life.
Filling and Sealing Methods
Method | Description | Common Uses |
---|---|---|
Hot Filling | Food is packed while hot to minimize bacterial growth | Canned wet pet food |
Retort Processing | Sealed containers are subjected to high heat and pressure | Ensures shelf stability |
Vacuum Sealing | Air is removed before sealing to prevent oxidation | High-end wet food pouches |
5. Sterilization and Quality Control
Once sealed, the pet food undergoes sterilization using traitement par autoclave, where high heat (240°F to 275°F) and pressure ensure all microbial contaminants are eliminated.
Mesures de contrôle de la qualité
- Microbial Testing: Checking for Salmonella, E. coli, and mold.
- Nutrient Analysis: Ensuring protein, fat, and vitamin levels meet regulatory requirements.
- Packaging Integrity Testing: Preventing leaks or compromised seals.
Retort sterilization destroys all probiotics in pet food.Vrai Heat sterilization eliminates live probiotics, so manufacturers often add them separately post-processing.
6. Labeling, Packaging, and Distribution
The final stage involves labeling and packaging for retail distribution.
- Nutritional Information: Labels must comply with AAFCO (Association of American Feed Control Officials) and FDA guidelines.
- Batch Tracking: Each product batch is assigned a code for traceability in case of recalls.
- Packaging Formats:
- Canned Wet Food (Long shelf life, easy storage)
- Pouch Wet Food (Convenient, single-serve)
- Tray-Packaged Food (Ready-to-serve portions)
Shelf Life and Storage Considerations
Storage Condition | Expected Shelf Life | Notes |
---|---|---|
Unopened (Room Temp) | 1-3 years | Store in a cool, dry place |
Opened (Refrigerated) | 2-5 days | Must be kept in a sealed container |
Frozen | Up to 6 months | Helps preserve freshness |
Conclusion: Why Understanding the Process Matters
Understanding how wet pet food is processed ensures pet owners can choose the best food for their pets' needs. Industrial processing prioritizes food safety, nutritional balance, and long-term storage, making wet pet food a reliable choice. By selecting high-quality brands that follow strict quality controls, pet owners can confidently provide their pets with nutritious, well-balanced meals.
How Is Wet Pet Food Packaged?
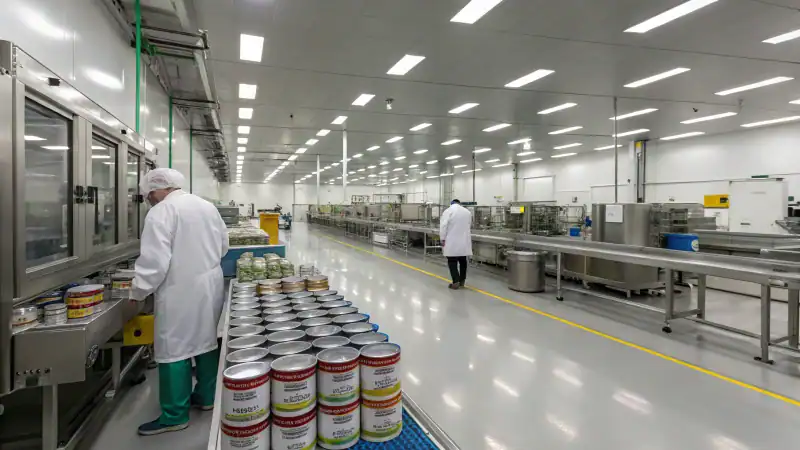
Wet pet food packaging is a critical aspect of pet nutrition, ensuring freshness, safety, and convenience for pet owners. Poor packaging can lead to contamination, spoilage, and nutrient loss, which can negatively affect a pet’s health. Choosing the right type of packaging helps manufacturers maintain product quality while also considering environmental sustainability. Understanding the packaging process is essential for pet owners and businesses alike to ensure pets receive high-quality, safe, and nutritious meals.
Wet pet food is commonly packaged in cans, pouches, and trays, each designed to preserve freshness, prevent contamination, and extend shelf life. These packaging types undergo sterilization processes such as retort processing to ensure the food remains safe for consumption. Packaging materials include aluminum, plastic, and multilayer films, offering durability, convenience, and recyclability.
Wet pet food packaging involves multiple steps, from filling and sealing to sterilization and labeling. To gain a deeper understanding of the technology, materials, and safety considerations behind this process, let's explore each packaging type and its benefits.
Types of Wet Pet Food Packaging
1. Canned Packaging
Cans are one of the most common packaging options for wet pet food. They provide a durable, airtight, and long-lasting solution for preserving pet food quality.
Advantages of Canned Packaging:
- Long shelf life: Properly sealed cans can last for years.
- Protection from light and oxygen: Prevents spoilage and maintains nutrient stability.
- Retort sterilization: The high-temperature process kills bacteria and ensures safety.
Materials Used in Cans:
- Aluminum: Lightweight, rust-resistant, and recyclable.
- Tin-plated steel: More durable but heavier than aluminum.
Packaging Process for Canned Wet Pet Food:
Étape | Description |
---|---|
Filling | Wet pet food is filled into pre-sterilized cans using automated machinery. |
Sealing | The lid is vacuum-sealed to remove oxygen and ensure freshness. |
Sterilization (Retort Processing) | Cans are exposed to high temperatures (121°C/250°F) under pressure to kill bacteria. |
Cooling & Labeling | Cans are cooled, dried, and labeled for distribution. |
2. Pouch Packaging
Pouches are a more modern alternative to cans, offering convenience and sustainability benefits. These flexible packages are made from multilayer materials that preserve freshness.
Advantages of Pouch Packaging:
- Lightweight & Portable: Easier to store and transport.
- Convenient for Single Servings: Ideal for portion control.
- Reduced Environmental Impact: Requires less material than cans.
Materials Used in Pouches:
- Multilayer Films: Combinations of plastic, aluminum, and paper to create a durable and lightweight barrier.
Packaging Process for Pouch Wet Pet Food:
Étape | Description |
---|---|
Filling | Pre-formed pouches are filled with wet pet food. |
Sealing | Heat-sealing ensures airtight protection. |
Pasteurization/Sterilization | Pouches undergo heat treatment to eliminate bacteria. |
Inspection & Distribution | Quality control checks before products are distributed. |
3. Tray Packaging
Tray packaging is another widely used option, especially for gourmet wet pet foods. These containers are typically made from plastic with foil lids.
Advantages of Tray Packaging:
- Attractive Presentation: Often used for premium products.
- Portion-Controlled Servings: Easy for pet owners to use.
- Microwave-Safe Options: Some trays are designed for convenient heating.
Materials Used in Trays:
- Plastic (PET or PP): Provides a lightweight and durable structure.
- Foil Lids: Helps maintain freshness and extends shelf life.
Packaging Process for Tray Wet Pet Food:
Étape | Description |
---|---|
Filling | Wet pet food is dispensed into individual trays. |
Sealing | A foil lid is heat-sealed to prevent contamination. |
Sterilization | Trays undergo pasteurization or retort processing. |
Labeling & Packing | Final quality checks before distribution. |
Comparison of Wet Pet Food Packaging Types
Fonctionnalité | Cans | Pouches | Trays |
---|---|---|---|
Matériau | Aluminum/Tin | Multilayer Films | Plastic & Foil |
Durée de conservation | 2-5 years | 1-2 years | 6 months - 2 years |
Portability | Heavy | Lightweight | Modéré |
Eco-Friendliness | Recyclable | Less Waste | Some Options |
Processing | Retort Sterilization | Heat Pasteurization | Pasteurization/Retort |
Sustainability Considerations in Wet Pet Food Packaging
Sustainability is becoming a significant focus in the pet food industry. Many manufacturers are adopting eco-friendly packaging solutions to reduce their environmental footprint.
Eco-Friendly Packaging Solutions
- Recyclable Cans: Many manufacturers use aluminum cans that can be fully recycled.
- Biodegradable Pouches: Some brands are introducing compostable or recyclable pouch materials.
- Reduced Plastic Use in Trays: Switching to plant-based plastics or minimal plastic trays.
Conclusion
Wet pet food packaging plays a vital role in ensuring food safety, freshness, and convenience. Whether it's cans, pouches, or trays, each packaging type has specific benefits tailored to different needs. As sustainability concerns grow, brands are working to develop eco-friendly packaging solutions.
If you're a pet owner or business looking for high-quality pet food packaging machine, contact us today to explore customized solutions that meet your needs!
Why Is Sterilization and Pasteurization Important for Wet Pet Food Production?
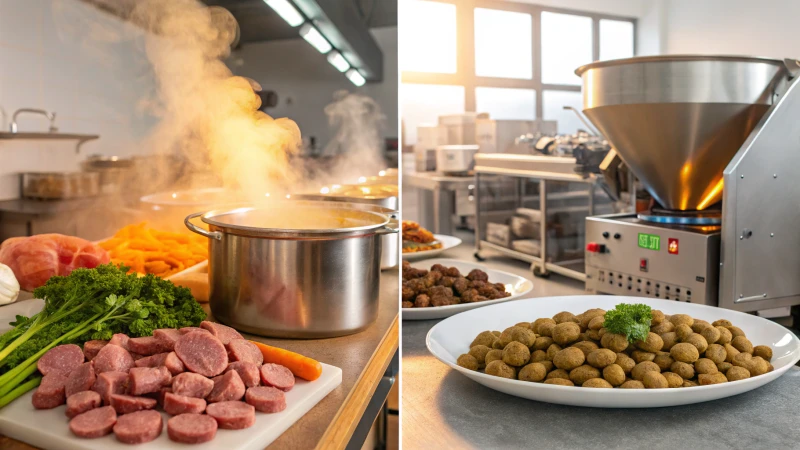
Ensuring the safety and quality of wet pet food is a top priority for manufacturers. Without proper sterilization and pasteurization, wet pet food can become a breeding ground for bacteria, mold, and other harmful pathogens. Contaminated pet food poses serious health risks, including foodborne illnesses that can affect both pets and their owners. To prevent spoilage and maintain food integrity, sterilization and pasteurization are essential in pet food production.
Sterilization and pasteurization are crucial in wet pet food production as they eliminate harmful microorganisms, extend shelf life, and ensure food safety. Sterilization involves high-temperature heat treatment to destroy all bacteria, while pasteurization uses moderate heat to kill most pathogens while preserving nutrients. These processes prevent contamination, maintain product stability, and comply with regulatory food safety standards.
Understanding the differences between sterilization and pasteurization, their applications, and the technologies used in wet pet food production can help pet owners and businesses ensure their products are safe and nutritious. Let’s explore these processes in detail.
What Is Sterilization in Wet Pet Food Production?
Definition and Purpose
Sterilization is a process that uses high temperatures (above 100°C) to eliminate all forms of microorganisms, including bacteria, spores, and fungi. This method ensures that wet pet food remains safe for long-term storage without refrigeration.
Key Benefits of Sterilization
- Kills all microorganisms – Prevents bacterial growth and spoilage.
- Extends shelf life – Allows storage for months or years without refrigeration.
- Ensures food safety – Meets regulatory standards for pet food production.
- Preserves food texture and quality – Maintains consistency in canned and pouch foods.
Sterilization Methods Used in Wet Pet Food Processing
Method | Description | Temperature Range | Application |
---|---|---|---|
Retort Sterilization | Uses high-pressure steam in an enclosed chamber to sterilize pet food. | 115-121°C (240-250°F) | Canned and pouch foods |
Aseptic Processing | Food is sterilized separately and then packaged in sterile conditions. | 135-150°C (275-300°F) | Liquid-based pet food |
Dry Heat Sterilization | High-temperature exposure in dry conditions. | 160-180°C (320-356°F) | Special dry packaging components |
Retort Sterilization Process for Canned and Pouched Wet Pet Food
- Filling: Pet food is placed in cans, pouches, or trays under hygienic conditions.
- Sealing: Containers are vacuum-sealed to prevent air contamination.
- Heat Processing: Products are exposed to pressurized steam inside a retort chamber.
- Refroidissement : Cans or pouches are cooled rapidly to prevent overcooking.
- Quality Inspection: Products are tested for microbial contamination.
What Is Pasteurization in Wet Pet Food Production?
Definition and Purpose
Pasteurization is a heat treatment process that eliminates most harmful bacteria while preserving food nutrients and taste. Unlike sterilization, pasteurization does not kill all microorganisms, but it significantly reduces their levels to safe limits.
Key Benefits of Pasteurization
- Kills most harmful bacteria – Reduces pathogens like Salmonella and E. coli.
- Maintains nutritional integrity – Preserves vitamins, proteins, and flavors.
- Enhances freshness – Ideal for refrigerated wet pet foods.
- Energy-efficient – Uses lower temperatures compared to sterilization.
Pasteurization Methods Used in Wet Pet Food Processing
Method | Description | Temperature Range | Application |
---|---|---|---|
Low-Temperature Pasteurization | Food is heated at low temperatures for a longer time. | 60-65°C (140-150°F) | Some refrigerated pet foods |
High-Temperature Short-Time (HTST) Pasteurization | Quick heating followed by rapid cooling. | 72-75°C (161-167°F) | Semi-moist pet food |
Ultra-Pasteurization (UHT) | Very high temperature for a few seconds. | 130-140°C (265-284°F) | Liquid-based pet foods |
High-Temperature Short-Time (HTST) Pasteurization Process for Wet Pet Food
- Heating: Food is quickly heated to 72°C (161°F) for 15 seconds.
- Refroidissement : Rapid cooling prevents further bacterial growth.
- Emballage : The product is sealed in sterilized containers.
- Refrigeration: Required for pasteurized pet food products to prevent spoilage.
Sterilization vs. Pasteurization: What’s the Difference?
Fonctionnalité | Sterilization | Pasteurization |
---|---|---|
Objectif | Destroys all microorganisms | Reduces harmful bacteria |
Température | 115-150°C (240-300°F) | 60-140°C (140-284°F) |
Durée de conservation | Long-term (up to 5 years) | Short-term (weeks to months) |
Application | Canned, pouch, and shelf-stable pet food | Refrigerated and fresh pet food |
Nutrient Preservation | Some loss due to high heat | Better nutrient retention |
Importance of These Processes for Pet Food Safety
Ensuring the safety of wet pet food requires a well-controlled production environment. Failing to sterilize or pasteurize properly can lead to:
- Bacterial contamination: Salmonella, Listeria, and E. coli outbreaks.
- Food spoilage: Shortened shelf life and loss of freshness.
- Nutrient degradation: Loss of essential vitamins and proteins.
- Pet health risks: Gastrointestinal issues, infections, and food poisoning.
Regulatory Compliance for Wet Pet Food Processing
To meet industry standards, pet food manufacturers must comply with strict food safety guidelines:
Organisme de réglementation | Country/Region | Standard |
---|---|---|
FDA (Food and Drug Administration) | ÉTATS-UNIS | Ensures pet food safety and proper sterilization |
AAFCO (Association of American Feed Control Officials) | ÉTATS-UNIS | Regulates pet food nutritional standards |
EFSA (European Food Safety Authority) | L'Europe | Sets microbiological safety standards |
FEDIAF (European Pet Food Industry Federation) | L'Europe | Guides pet food processing regulations |
Conclusion
Sterilization and pasteurization play a vital role in wet pet food production by ensuring food safety, extending shelf life, and maintaining product quality. While sterilization eliminates all bacteria and is ideal for canned and pouch foods, pasteurization reduces harmful microorganisms while preserving more nutrients. These processes help manufacturers comply with strict safety regulations and provide pet owners with healthy, risk-free food for their pets.
What Quality Control Measures Are Used in Wet Pet Food Production?
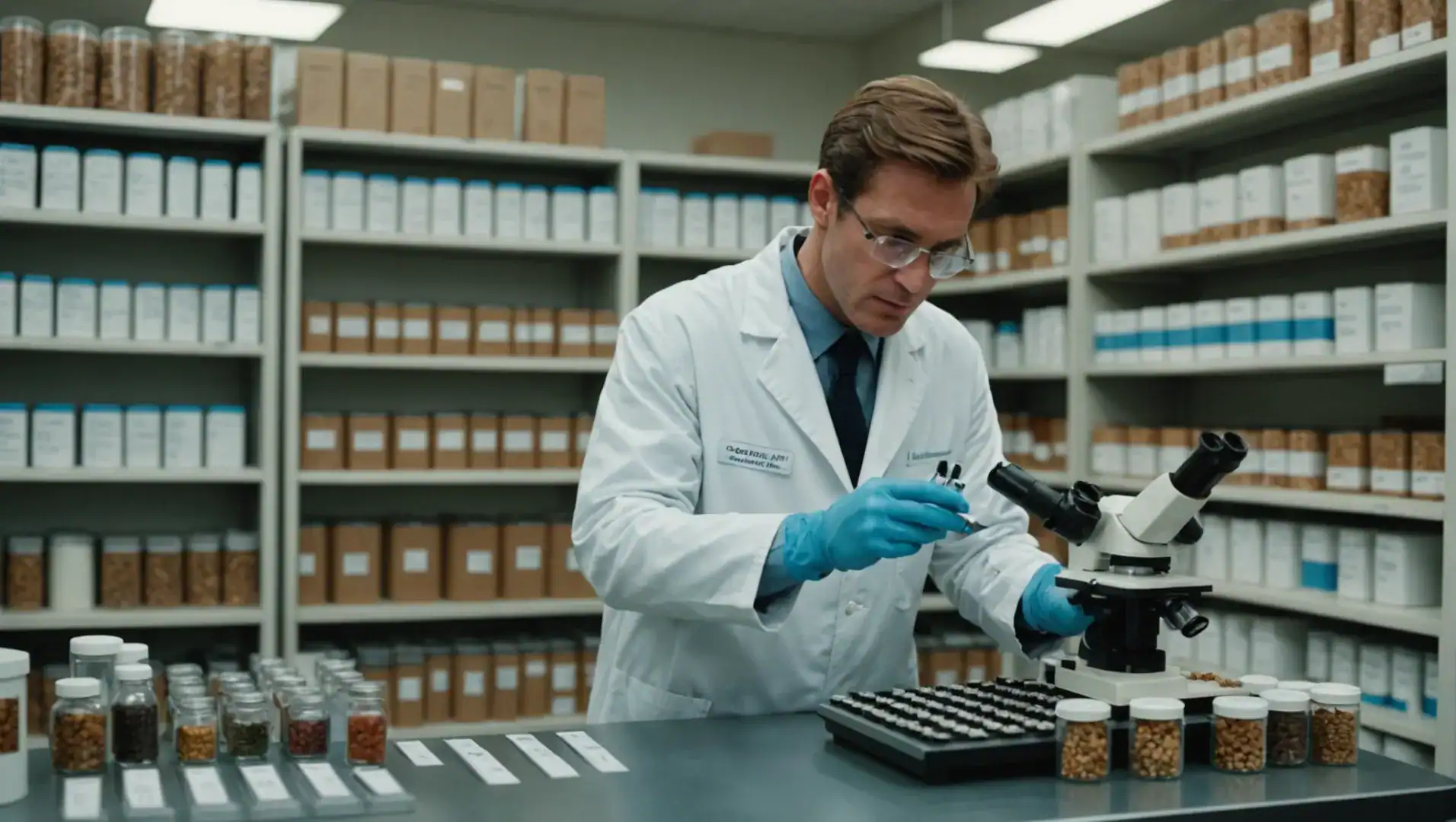
Wet pet food production is a highly regulated industry, where ensuring product safety and nutritional consistency is paramount. Any lapses in quality control can lead to contamination, nutritional deficiencies, or product recalls, all of which pose risks to pets and brands alike. Pet food manufacturers implement rigorous quality control measures to guarantee food safety, maintain high standards, and comply with global regulations.
Wet pet food production undergoes strict quality control measures, including raw material inspection, microbiological testing, hazard analysis (HACCP), process monitoring, metal detection, and final product testing to ensure safety, nutritional accuracy, and compliance with regulatory standards. These measures prevent contamination, maintain consistency, and uphold pet health.
Understanding the quality control measures in wet pet food production provides valuable insight into the industry's commitment to pet safety and food excellence. Below, we delve into the critical checkpoints, technologies, and methodologies manufacturers use to ensure the highest quality standards.
1. Raw Material Sourcing and Inspection
The first step in wet pet food production is the careful selection of raw materials. High-quality ingredients ensure the final product is nutritious and safe for consumption. Quality control measures at this stage include:
- Supplier Audits: Manufacturers conduct supplier audits to verify compliance with food safety standards, such as GMP (Good Manufacturing Practices) and ISO 22000.
- Ingredient Testing: Incoming raw materials are tested for:
- Microbiological contamination (Salmonella, Listeria, E. coli)
- Chemical residues (pesticides, heavy metals)
- Nutritional composition (protein, fat, vitamins, and minerals)
- Temperature Control: Meat and poultry ingredients must be stored under specific temperature conditions to prevent spoilage.
Raw Material Quality Standards
Type d'ingrédient | Mesures de contrôle de la qualité |
---|---|
Meat & Poultry | Microbiological testing, temperature monitoring, supplier certification |
Légumes | Pesticide residue analysis, freshness inspection |
Grains & Starches | Mycotoxin screening, allergen testing |
Fats & Oils | Oxidation checks, free fatty acid analysis |
2. HACCP (Hazard Analysis and Critical Control Points) Implementation
HACCP is a critical food safety system that identifies, evaluates, and controls potential hazards throughout the production process. It involves:
- Hazard Identification: Determining physical, chemical, and biological risks.
- Critical Control Points (CCPs): Identifying key processing stages where hazards can be eliminated (e.g., cooking, sterilization).
- Monitoring Procedures: Regular inspections and real-time tracking of production parameters.
- Corrective Actions: If a deviation occurs, corrective actions are implemented immediately.
3. Processing and Cooking Standards
Once raw materials pass inspection, they are processed under strict guidelines to ensure food safety and product consistency.
Key Quality Control Checks in Processing
- Grinding & Mixing: Ensuring uniform distribution of ingredients.
- Cooking Temperature Monitoring: Wet pet food must be cooked at specific temperatures to destroy harmful bacteria.
- pH and Moisture Testing: Ensuring product stability and shelf life.
Process Quality Control Data
Processing Stage | Quality Check |
---|---|
Grinding & Mixing | Ingredient homogeneity |
Cooking & Sterilization | Temperature validation (minimum 121°C for 3 minutes) |
pH Monitoring | pH 4.5 - 6.5 (prevents microbial growth) |
Teneur en humidité | 70% - 80% (ideal texture and preservation) |
4. Packaging and Sterilization
Packaging plays a crucial role in maintaining the integrity of wet pet food. Key measures include:
- Can Seaming Integrity Checks: Ensuring airtight seals to prevent contamination.
- Retort Sterilization: Canned wet pet food undergoes retort sterilization, a high-temperature process that eliminates bacteria and extends shelf life.
- Oxygen and Vacuum Testing: Packaging is tested for air leaks to prevent spoilage.
5. Final Product Testing and Batch Release
Before products reach consumers, they undergo final testing to verify compliance with quality standards.
- Microbiological Testing: Samples are tested for harmful bacteria such as Salmonella and Clostridium.
- Nutritional Analysis: Protein, fat, fiber, and moisture levels are analyzed to ensure consistency.
- Shelf Life Stability Tests: Products undergo accelerated aging tests to predict their long-term quality.
Microbial Testing Standards
Microorganism | Acceptable Limit |
---|---|
Salmonella | Absent in 25g sample |
E. coli | < 10 CFU/g |
Listeria | Not detectable |
6. Traceability and Recall Preparedness
In the event of a quality issue, manufacturers must have a system in place for traceability and recall management. This includes:
- Batch Coding: Each product has a unique batch code for tracking.
- Digital Record Keeping: Detailed records of ingredient origins, processing steps, and quality tests.
- Recall Protocols: Swift removal of defective products from the market if needed.
Conclusion
Ensuring the highest quality standards in wet pet food production requires meticulous attention to raw materials, processing, packaging, and final product testing. Manufacturers implement stringent quality control measures such as HACCP, microbiological testing, and packaging integrity checks to maintain food safety and nutritional consistency. By adhering to these rigorous protocols, pet food companies can provide safe, nutritious meals that contribute to pet health and well-being.
For more information about our wet pet food quality control processes, contact us today to learn how we ensure top-tier safety and nutrition in every batch.
What Are the Latest Innovations in Wet Pet Food Production?
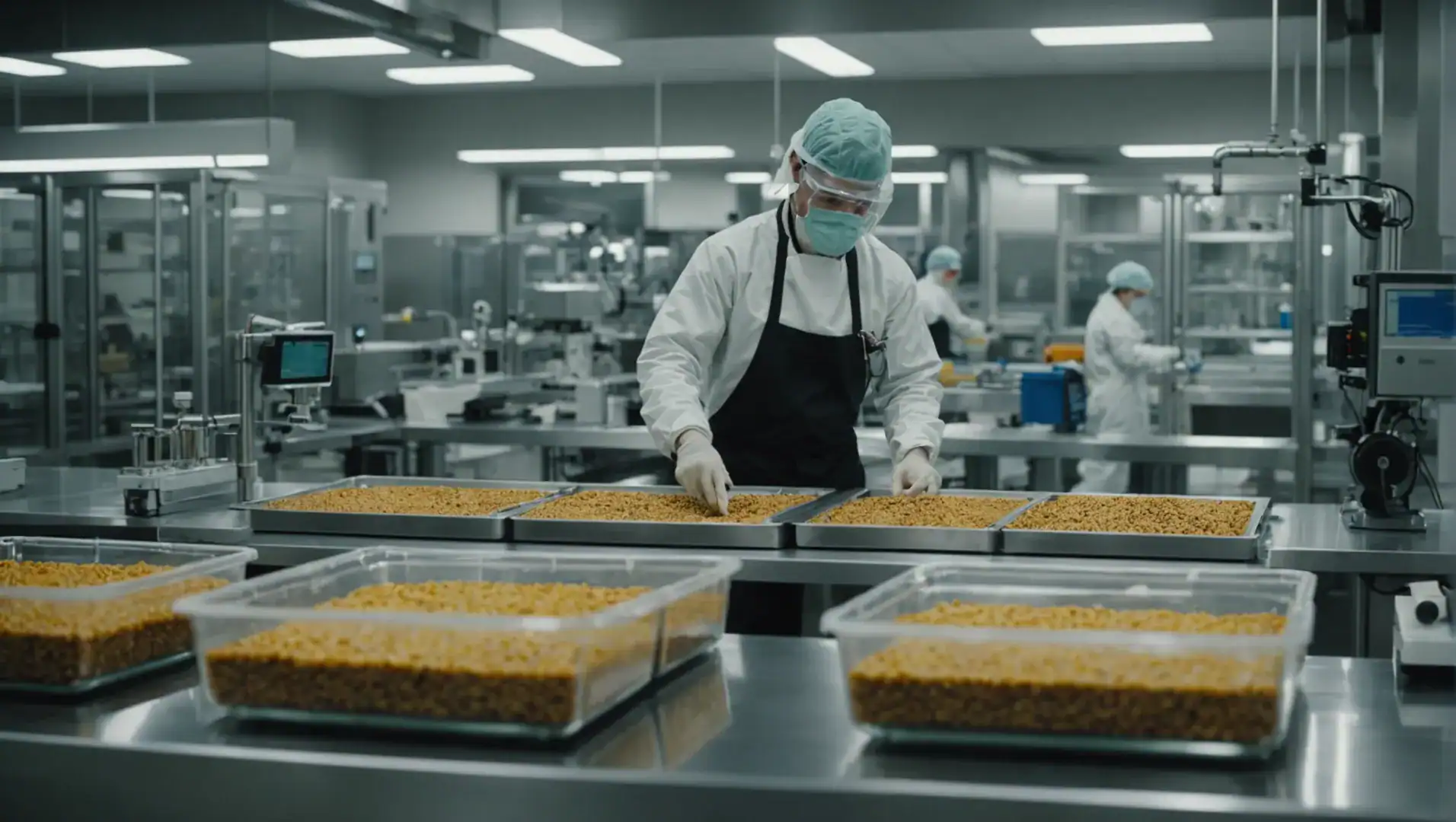
The pet food industry has evolved significantly in recent years, driven by increasing consumer demand for high-quality, nutritious, and safe products. Traditional wet pet food production relied heavily on manual processes, but automation and smart technology are now revolutionizing the industry. The latest innovations ensure higher efficiency, enhanced product consistency, and better compliance with stringent food safety standards. Manufacturers adopting these advancements gain a competitive edge by reducing waste, optimizing production costs, and improving product quality.
The latest innovations in wet pet food production include AI-driven automation, real-time quality control using IoT sensors, robotic processing systems for ingredient handling, and advanced sterilization techniques. These innovations enhance efficiency, reduce waste, and ensure consistency in texture, flavor, and nutritional value. Additionally, blockchain traceability solutions and smart packaging technology are improving transparency and freshness control.
With pet owners increasingly concerned about ingredient transparency, food safety, and premium nutritional content, automation and smart technology are playing a crucial role in transforming wet pet food manufacturing. Keep reading to explore the key advancements shaping the industry and how they benefit both manufacturers and pet owners.
1. AI-Driven Automation in Wet Pet Food Processing
Artificial Intelligence (AI) is reshaping pet food manufacturing by streamlining production workflows, optimizing ingredient blending, and improving consistency in texture and flavor. AI-driven automation can analyze vast datasets to make real-time decisions, reducing manual intervention and minimizing production errors.
How AI Enhances Wet Pet Food Production:
AI Feature | Bénéfice |
---|---|
Maintenance prédictive | Prevents machine failures and reduces downtime |
Automated Quality Control | Detects inconsistencies in texture, moisture, and ingredient distribution |
Supply Chain Optimization | Ensures precise ingredient sourcing and waste reduction |
Recipe Customization | Enables personalized pet food production based on pet dietary needs |
AI-driven automation ensures that wet pet food products maintain consistent quality while reducing ingredient wastage and production costs.
2. IoT-Enabled Quality Control and Safety Monitoring
The Internet of Things (IoT) is revolutionizing quality control in wet pet food manufacturing. Smart sensors embedded in production lines can monitor parameters such as moisture content, temperature, and pH levels in real time.
Benefits of IoT in Wet Pet Food Production:
- Real-time Data Analytics: Sensors provide instant feedback, allowing manufacturers to make adjustments on the fly.
- Automated Safety Checks: AI-integrated IoT devices detect contaminants and prevent product recalls.
- Remote Monitoring: Factory managers can oversee operations from anywhere using cloud-based dashboards.
By leveraging IoT technology, pet food manufacturers can ensure that every batch meets the highest quality and safety standards.
3. Robotics in Ingredient Handling and Processing
Robotic automation is becoming a game-changer in wet pet food production. Robotic arms and AI-powered mixing systems handle precise ingredient measurements, ensuring uniformity across production batches.
Key Robotics Applications in Wet Pet Food Processing:
Robotics Application | Fonction |
---|---|
Automated Ingredient Dispensing | Ensures accurate portioning and reduces human error |
Mixing and Blending Robots | Creates consistent textures and flavors in wet food recipes |
Automated Packaging | Speeds up sealing and labeling for extended product shelf life |
Case Study: Smart Robotics in Pet Food Processing
A leading pet food manufacturer implemented robotic ingredient handling and reduced batch inconsistencies by 30%. This technology minimized labor costs and improved production efficiency by 40%.
4. Advanced Sterilization and Preservation Techniques
With wet pet food requiring strict sterilization to prevent contamination, the industry is adopting high-pressure processing (HPP) and UV sterilization as safer, chemical-free alternatives.
Latest Sterilization Innovations:
- HPP (High-Pressure Processing): Uses extreme pressure to eliminate bacteria without altering nutritional integrity.
- UV Light Sterilization: Kills pathogens in pet food surfaces without heat exposure.
- Modified Atmosphere Packaging (MAP): Uses gas mixtures to extend product shelf life while maintaining freshness.
These sterilization techniques ensure that wet pet food remains safe and nutritious without excessive reliance on preservatives.
5. Blockchain and Smart Packaging for Enhanced Transparency
Consumers are demanding greater transparency regarding pet food ingredients and sourcing. Blockchain technology is now enabling pet owners to trace ingredients back to their origins, ensuring ethical sourcing and quality control.
Blockchain Benefits for Wet Pet Food Production:
- Traceability: Tracks every ingredient from farm to finished product.
- Fraud Prevention: Prevents counterfeiting and ingredient mislabeling.
- Consumer Trust: Allows pet owners to verify quality certifications.
Smart packaging integrates freshness indicators, NFC (Near Field Communication) tags, and QR codes, providing pet owners with real-time product information through smartphone scans.
Future Trends in Wet Pet Food Production
L'innovation | Expected Impact |
---|---|
AI-Driven Recipe Personalization | Enables tailored diets for pets with specific health needs |
Impression 3D d'aliments | Customizes portion sizes and textures for different pet breeds |
Emballage durable | Reduces plastic waste with biodegradable and recyclable materials |
Automated Allergen Detection | Prevents cross-contamination in pet food production |
As the pet food industry advances, manufacturers must continue embracing automation, smart technologies, and sustainability to meet evolving consumer expectations.
Conclusion: The Future of Wet Pet Food Manufacturing
The latest innovations in wet pet food production are transforming the industry, making processes more efficient, safer, and highly precise. AI-driven automation, IoT-enabled quality control, robotics, and blockchain traceability are setting new standards for transparency and product consistency. Additionally, advanced sterilization and smart packaging technologies are enhancing food safety and freshness.
By adopting these cutting-edge solutions, manufacturers can meet growing consumer demands while reducing waste and improving operational efficiency. As automation and AI continue to evolve, the pet food industry is set to become more innovative, ensuring that pets receive high-quality, nutritious meals with unparalleled safety and consistency.
Looking to upgrade your wet pet food production with the latest smart automation? Contact us today to explore advanced solutions for your manufacturing needs!
How Can Manufacturers Optimize Wet Pet Food Production Efficiency?
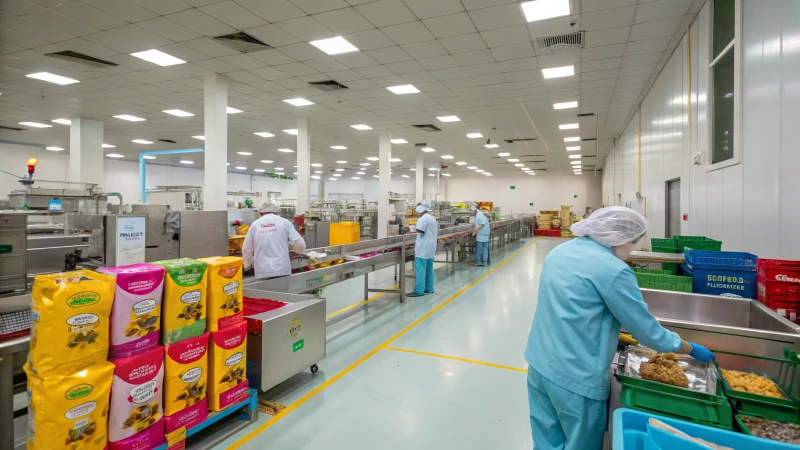
Wet pet food manufacturing is a complex process requiring precise formulation, high-quality ingredients, and strict compliance with safety and hygiene standards. However, inefficiencies in production can lead to increased costs, product waste, and potential contamination risks. To remain competitive in the pet food industry, manufacturers must optimize their production efficiency through automation, process improvement, and waste reduction strategies. In this article, we will explore the best methods for maximizing wet pet food production efficiency while maintaining product quality and safety.
How to Optimize Wet Pet Food Production Efficiency?
To optimize wet pet food production efficiency, manufacturers should focus on automation, ingredient standardization, process streamlining, energy efficiency, and waste reduction. Implementing advanced mixing and cooking technologies, improving packaging operations, and utilizing real-time monitoring systems can significantly enhance production speed, reduce downtime, and improve overall cost-effectiveness.
Optimizing wet pet food production is not just about reducing costs; it is also about maintaining product consistency, ensuring safety, and meeting the growing demand for high-quality pet nutrition. By leveraging technology and efficient production strategies, manufacturers can significantly improve productivity while minimizing waste. Let’s explore the key aspects of efficiency optimization in detail.
1. Streamlining Ingredient Handling and Preparation
Efficient wet pet food production begins with optimizing ingredient handling and preparation. Raw materials such as meat, grains, and vitamins need to be processed quickly and accurately to maintain nutritional value.
Key Strategies:
- Automated Ingredient Dosing: Using automated dosing systems ensures precise ingredient measurement, reducing waste and improving consistency.
- Preprocessing Optimization: Grinding, blending, and emulsifying should be performed efficiently to maintain uniform texture.
- Temperature-Controlled Storage: Keeping ingredients at optimal temperatures prevents spoilage and extends shelf life.
Impact of Efficient Ingredient Handling:
Facteur | Traditional Process | Optimized Process |
---|---|---|
Ingredient Accuracy | Manual weighing, prone to errors | Automated weighing, high precision |
Processing Time | Labor-intensive, slow | Automated mixing, faster processing |
Cohérence | Variation in quality | Uniform texture and quality |
2. Improving Cooking and Thermal Processing
Cooking is a critical step in wet pet food production, ensuring the product is safe, digestible, and flavorful.
Best Practices for Cooking Optimization:
- Batch vs. Continuous Cooking: Continuous processing reduces downtime and energy consumption.
- Steam Injection Cooking: Provides faster heat penetration, improving energy efficiency.
- Precision Temperature Control: Maintaining optimal cooking temperatures ensures food safety and preserves nutrients.
Comparative Efficiency of Cooking Methods
Cooking Method | Vitesse de traitement | Efficacité énergétique | Qualité des produits |
---|---|---|---|
Conventional Batch Cooking | Slow | High energy use | Inconsistent |
Continuous Cooking | Fast | Lower energy use | Consistent |
3. Enhancing Canning and Packaging Efficiency
Packaging efficiency impacts product shelf life, transportation, and overall production speed.
Solutions for Packaging Optimization:
- Automated Filling and Sealing: Reduces manual labor and increases speed.
- Vacuum Sealing: Extends shelf life by preventing oxidation.
- Smart Packaging Systems: Sensors detect leaks and ensure quality control.
Effect of Packaging Automation:
Paramètres | Manual Packaging | Automated Packaging |
---|---|---|
Speed | Slow | Fast |
Réduction des déchets | Haut | Faible |
Product Consistency | Variable | Uniform |
4. Reducing Waste and Enhancing Sustainability
Minimizing waste in wet pet food production leads to cost savings and environmental benefits.
Strategies for Waste Reduction:
- Byproduct Utilization: Repurpose trimmings and leftovers for secondary products.
- Water Recycling Systems: Reduce water consumption by reusing treated water.
- Energy Recovery Systems: Convert waste heat into usable energy.
Sustainability Impact Analysis
Initiative | Réduction des déchets | Cost Savings | Environmental Benefit |
---|---|---|---|
Byproduct Reuse | Haut | Modéré | Réduction des déchets en décharge |
Water Recycling | Modéré | Haut | Saves water resources |
Energy Recovery | Haut | Haut | Lowers carbon footprint |
5. Implementing Smart Manufacturing Technologies
Industry 4.0 technologies can further enhance efficiency through real-time data monitoring and predictive maintenance.
Technology Applications:
- IoT Sensors: Monitor machine performance to prevent breakdowns.
- AI-Based Quality Control: Detects defects in real time.
- Automated Data Analysis: Optimizes production scheduling.
Impact of Smart Manufacturing
Technologie | Efficiency Boost | Cost Savings | Quality Improvement |
---|---|---|---|
IoT Sensors | Haut | Modéré | Prevents downtime |
AI Quality Control | Modéré | Haut | Reduces defects |
Data Analytics | Haut | Haut | Optimizes workflow |
6. Workforce Training and Operational Excellence
An efficient workforce is crucial for streamlined operations.
Key Training Initiatives:
- Cross-Training Employees: Reduces reliance on specialized labor.
- Lean Manufacturing Principles: Eliminates inefficiencies.
- Safety and Compliance Training: Ensures regulatory adherence.
Workforce Efficiency Metrics
Training Program | Productivity Increase | Error Reduction | Compliance Improvement |
---|---|---|---|
Cross-Training | Modéré | Haut | Modéré |
Lean Manufacturing | Haut | Haut | Modéré |
Safety Training | Modéré | Modéré | Haut |
Final Thoughts: Maximizing Efficiency in Wet Pet Food Production
Optimizing wet pet food production requires a multi-faceted approach, integrating automation, sustainability, and workforce efficiency. By adopting advanced cooking technologies, refining packaging operations, reducing waste, and leveraging smart manufacturing, companies can significantly enhance productivity and cost-effectiveness.
Would you like expert guidance on optimizing your pet food production facility? Contact us today to explore customized solutions for your manufacturing needs!
Conclusion
A well-designed wet pet food production line ensures that pet food is nutritious, safe, and appealing to pets. By understanding the different stages of production and the latest innovations, manufacturers can enhance product quality and operational efficiency.
Appel à l'action
Looking for high-quality wet pet food production equipment or expert guidance? Contact us today for customized solutions tailored to your needs!