Pet food manufacturers face numerous challenges, from ensuring nutritional quality to maintaining high production efficiency. Poorly selected or outdated equipment can lead to production delays, inconsistent product quality, and increased operational costs. To meet growing market demands and stringent safety regulations, investing in the right pet food processing equipment is crucial for success.
Pet food processing equipment includes a range of machinery used for mixing, grinding, extruding, drying, and packaging pet food products. Choosing the right equipment depends on factors such as production scale, ingredient types, nutritional requirements, and automation needs. High-quality pet food processing machines improve efficiency, ensure consistent product quality, and comply with safety and hygiene regulations.
To make an informed decision, you need to understand the different types of pet food processing equipment, their benefits, and how they fit into your production process. Keep reading to explore the key considerations when selecting the best machinery for your pet food manufacturing needs.
What Are the Main Types of Pet Food Processing Equipment?
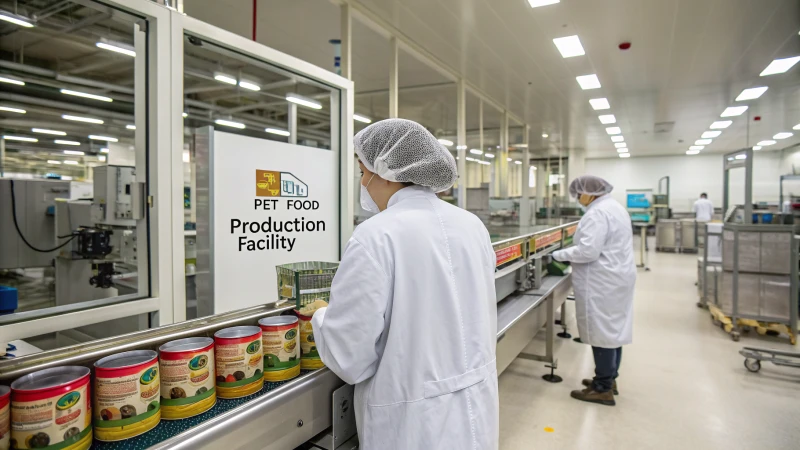
Pet food manufacturers face a major challenge in ensuring high-quality, nutritious, and palatable pet food while maintaining production efficiency and meeting regulatory requirements. Without the right processing equipment, achieving consistency in texture, nutritional content, and shelf stability becomes difficult, leading to quality control issues, waste, and increased operational costs. However, investing in the correct pet food processing machinery can optimize production, enhance product safety, and ensure consumer satisfaction.
The main types of pet food processing equipment include extrusion machines, grinding and mixing equipment, drying systems, coating machines, and packaging systems. Each type of machinery plays a critical role in transforming raw ingredients into high-quality pet food products, ensuring consistency, efficiency, and compliance with industry standards.
Understanding the core machinery involved in pet food production helps manufacturers make informed decisions to improve efficiency and product quality. Let’s explore the different types of pet food processing equipment and their roles in production.
1. Extrusion Machines
Extrusion is the most common method used in pet food manufacturing. These machines combine heat, pressure, and mechanical shear to cook and shape pet food into various forms, such as kibbles and treats.
Types of Extruders:
Extruder Type | Kuvaus | Sovellukset |
---|---|---|
Yksiruuvinen ekstruuderi | Uses one screw to mix and cook ingredients | Basic pet food production |
Kaksoisruuvinen ekstruuderi | Utilizes two intermeshing screws for better mixing and cooking | High-moisture, high-fat formulations |
Cold Extruder | Operates at lower temperatures to preserve nutrients | Soft treats and specialty diets |
Twin-screw extruders provide better mixing and higher efficiency than single-screw extruders.Totta
Twin-screw extruders allow better ingredient dispersion and uniform cooking, improving product quality.
2. Grinding and Mixing Equipment
Before extrusion, raw ingredients must be ground and mixed to achieve a consistent texture and nutrient distribution.
Key Machines in This Category:
Machine | Toiminto | Edut |
---|---|---|
Hammer Mill | Crushes dry ingredients into fine particles | Improves digestibility and extrusion efficiency |
Roller Mill | Uses rolling action to break down grains | Produces uniform particle sizes |
Paddle Mixer | Blends powders and liquids evenly | Ensures consistency in nutrient distribution |
Ribbon Blender | Uses helical ribbons to mix dry ingredients | Gentle blending without heat generation |
3. Drying Systems
After extrusion, pet food needs to be dried to reduce moisture content and enhance shelf stability.
Types of Dryers:
Dryer Type | Toiminto | Edut |
---|---|---|
Conveyor Dryer | Uses heated air to dry pet food on a conveyor belt | Continuous operation, high efficiency |
Rotary Dryer | Rotates pet food for even drying | Suitable for high-capacity production |
Vacuum Dryer | Uses low-pressure environments to remove moisture | Preserves heat-sensitive ingredients |
Vacuum drying helps retain more nutrients in pet food compared to conventional drying methods.Totta
The lower temperature of vacuum drying prevents excessive nutrient degradation.
4. Coating Machines
Coating equipment applies fats, oils, flavors, and vitamins to enhance the palatability and nutritional value of pet food.
Common Coating Equipment:
Koneen tyyppi | Toiminto | Key Feature |
---|---|---|
Batch Coater | Sprays liquids onto pet food in batches | Suitable for small-scale production |
Continuous Coater | Applies coatings in a continuous process | Higher throughput, consistent coverage |
Vacuum Coater | Infuses liquids deep into kibbles using vacuum technology | Better absorption of nutrients |
5. Packaging Systems
Once pet food is processed, it needs proper packaging to maintain freshness and safety.
Types of Packaging Machines:
Koneen tyyppi | Toiminto | Edut |
---|---|---|
Form-Fill-Seal Machine | Forms pouches, fills with pet food, and seals them | Fully automated, high efficiency |
Weighing & Batching Machine | Ensures accurate portioning | Reduces waste, maintains consistency |
Vacuum Packaging Machine | Removes air to extend shelf life | Protects against oxidation |
Vacuum packaging significantly extends the shelf life of pet food.Totta
Removing air slows oxidation, preserving freshness for longer periods.
Choosing the right pet food processing equipment is crucial for achieving consistency, efficiency, and quality in pet food production. From grinding and mixing raw ingredients to extrusion, drying, coating, and packaging, each step requires specialized machinery to ensure optimal results. By investing in modern pet food processing equipment, manufacturers can enhance product quality, meet regulatory standards, and increase profitability.
Are you looking for reliable pet food processing equipment to optimize your production? Contact us today for expert guidance on selecting the best machinery for your needs!
How Does Pet Food Extrusion Work?
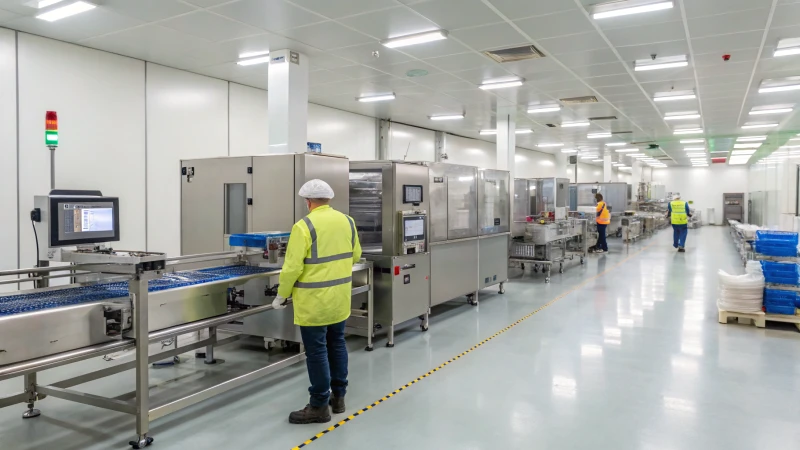
Ensuring high-quality, nutritious, and safe pet food is a major challenge for manufacturers. Without the right processing method, pet food can suffer from inconsistent texture, poor digestibility, and nutrient loss. Traditional cooking methods often fail to produce the desired product consistency and shelf stability. However, extrusion technology offers an efficient, scalable, and precise solution for producing high-quality pet food with optimized nutrition and texture.
Pet food extrusion is a process that uses heat, pressure, and mechanical shear to cook, shape, and texture pet food. The process involves ingredient mixing, pre-conditioning, high-temperature cooking through an extruder, and final drying and coating to enhance flavor and nutritional content. This method ensures consistency, digestibility, and extended shelf life in pet food products.
Understanding how pet food extrusion works can help manufacturers optimize production efficiency, maintain product quality, and meet industry regulations. Let’s dive into the extrusion process and its role in modern pet food manufacturing.
1. Key Steps in Pet Food Extrusion
Extrusion technology transforms raw ingredients into finished pet food through a series of carefully controlled steps. Each step is crucial for maintaining consistency, texture, and nutritional value.
Step 1: Ingredient Preparation and Mixing
Before extrusion, the raw materials—including grains, proteins, vitamins, and minerals—must be ground and blended to create a uniform mixture.
Equipment | Toiminto | Importance |
---|---|---|
Hammer Mill | Crushes dry ingredients into fine particles | Improves digestibility and uniform cooking |
Paddle Mixer | Evenly blends all ingredients | Ensures consistent nutrient distribution |
Ribbon Blender | Mixes powders and liquids | Prevents ingredient separation |
Pre-mixing ingredients before extrusion improves nutrient uniformity in pet food.Totta
Homogenized mixtures ensure balanced nutrition in every kibble.
Step 2: Pre-Conditioning
In the pre-conditioner, steam and water are added to soften the mixture before extrusion.
Toiminto | Edut |
---|---|
Partially cooks ingredients | Improves digestibility |
Adds moisture | Prevents dry, brittle kibble |
Enhances protein binding | Helps shape and texture formation |
Pre-conditioning ensures that the raw materials enter the extruder in an optimal state for cooking and shaping.
Step 3: Extrusion Cooking
The core of the extrusion process happens inside the extruder, where heat, pressure, and mechanical shear cook and shape the pet food.
Extruder Type | Kuvaus | Hakemus |
---|---|---|
Yksiruuvinen ekstruuderi | Uses one screw to mix and push ingredients through a die | Basic kibble production |
Kaksoisruuvinen ekstruuderi | Uses two intermeshing screws for better mixing and cooking | High-fat, complex formulas |
Cold Extruder | Operates at lower temperatures | Produces soft treats, fresh pet food |
Inside the extruder, ingredients are subjected to high pressure and temperatures (typically 90-200°C), breaking down starches and proteins to enhance digestibility.
Twin-screw extruders provide better ingredient mixing than single-screw extruders.Totta
Their intermeshing screws improve uniform cooking and texture.
Step 4: Shaping and Expansion
Once the mixture is fully cooked, it passes through a die, which determines the final shape of the pet food.
Die Type | Final Product |
---|---|
Circular die | Round kibbles |
Star-shaped die | Star-patterned treats |
Flat die | Biscuit-like treats |
The high pressure inside the extruder causes the mixture to expand rapidly upon exiting the die, creating a light, airy texture in dry kibbles.
Step 5: Drying
Extruded pet food contains high moisture content (15-30%), which must be reduced for shelf stability.
Dryer Type | Toiminto | Edut |
---|---|---|
Conveyor Dryer | Uses heated air to dry kibble as it moves along a conveyor | Continuous process, high efficiency |
Rotary Dryer | Rotates kibble for even drying | Suitable for large-scale production |
Vacuum Dryer | Uses low pressure to remove moisture | Preserves heat-sensitive nutrients |
Drying ensures pet food has a final moisture content of 8-12%, preventing microbial growth and spoilage.
Step 6: Coating and Flavoring
To enhance taste and nutrition, fats, vitamins, and palatability enhancers are applied after drying.
Coating Method | Toiminto | Edut |
---|---|---|
Liquid Sprayers | Sprays oils and flavors onto kibble | Even coating, cost-effective |
Vacuum Coating | Infuses liquids deep into kibble | Better absorption, longer-lasting flavor |
Batch Coaters | Applies coatings in small batches | Ideal for specialty diets |
Vacuum coating allows better absorption of fats and vitamins in pet food.Totta
The vacuum process enables deeper penetration of nutrients into kibbles.
Step 7: Cooling and Packaging
Before packaging, extruded pet food must be cooled to prevent condensation and spoilage.
Process | Purpose |
---|---|
Cooling tunnels | Reduce temperature to prevent moisture buildup |
Weighing & batching | Ensures accurate portioning |
Vacuum packaging | Extends shelf life |
Proper packaging maintains pet food freshness and prevents oxidation.
2. Benefits of Extruded Pet Food
Extrusion technology offers numerous advantages over traditional cooking methods.
Hyöty | Selitys |
---|---|
Enhanced Digestibility | Starch breakdown improves nutrient absorption |
Customizable Shapes & Textures | Different die molds create various kibble designs |
Longer Shelf Life | Moisture reduction prevents microbial growth |
Nutritional Control | Precise ingredient blending ensures balanced diets |
3. Comparison of Pet Food Processing Methods
Processing Method | Cooking Temperature | Texture | Säilyvyys |
---|---|---|---|
Puristaminen | 90-200°C | Crunchy kibble, expanded treats | 12+ months |
Baking | 120-180°C | Firm biscuits | 6-12 months |
Cold Pressing | 40-60°C | Softer kibble | 3-6 months |
Pakkaskuivaus | -40°C | Lightweight, retains nutrients | 12-24 months |
Extruded pet food has a longer shelf life compared to baked pet food.Totta
Lower moisture content in extruded pet food prevents spoilage.
Päätelmä
Pet food extrusion is a highly efficient and controlled process that ensures consistent quality, digestibility, and shelf stability. By optimizing extrusion parameters such as temperature, pressure, and die selection, manufacturers can produce a wide variety of pet food products tailored to different dietary needs.
Kehotus toimintaan
Looking for high-quality pet food extrusion equipment? Contact us today to find the best solutions for your manufacturing needs!
What Factors Should You Consider When Choosing Pet Food Processing Equipment?

Manufacturers in the pet food industry face significant challenges when selecting the right processing equipment. Without the right machinery, production inefficiencies, inconsistent product quality, and compliance issues can arise. Selecting improper equipment may lead to increased waste, higher operational costs, and difficulty meeting safety regulations. However, by carefully considering key factors when choosing pet food processing equipment, manufacturers can optimize production efficiency, maintain consistent product quality, and ensure regulatory compliance.
When choosing pet food processing equipment, manufacturers should consider factors such as production capacity, ingredient flexibility, automation level, energy efficiency, compliance with safety regulations, and ease of maintenance. Selecting the right equipment ensures efficient production, consistent quality, and cost-effectiveness in pet food manufacturing.
Understanding these factors can help pet food manufacturers make informed purchasing decisions that align with their production goals, budget, and quality standards.
1. Production Capacity and Scalability
One of the most critical factors when selecting pet food processing equipment is production capacity. Manufacturers should assess their current and future needs to ensure the equipment can handle growing demand.
Tekijä | Importance | Pohdintoja |
---|---|---|
Batch vs. Continuous Processing | Affects throughput efficiency | Batch systems are suitable for small-scale production, while continuous systems support high-volume operations |
Throughput Rate (kg/hour) | Determines how much pet food can be produced | Ensure the machine can meet current and projected production needs |
Scalability | Accommodates future growth | Choose modular systems that allow for easy expansion |
Continuous processing systems offer higher efficiency than batch processing in large-scale pet food manufacturing.Totta
Continuous systems minimize downtime and enhance production efficiency.
2. Ingredient and Formulation Flexibility
Different pet food products require varying ingredient formulations, including dry kibble, wet food, and specialty diets.
Equipment Feature | Importance | Hakemus |
---|---|---|
Multi-ingredient Handling | Supports a variety of protein, grain, and additive combinations | Required for manufacturers producing diverse pet food products |
High-Fat Formulations | Prevents clogging and inefficiencies | Needed for premium, high-protein pet foods |
Variable Mixing and Extrusion Settings | Allows precise control over texture and nutrient retention | Ideal for producing specialty diets (grain-free, high-fiber, or hypoallergenic pet food) |
Choosing equipment that can handle a broad range of ingredients ensures greater product versatility and market adaptability.
3. Automation and Control Systems
The level of automation in pet food processing equipment impacts labor costs, efficiency, and product consistency.
Automation Level | Edut | Pohdintoja |
---|---|---|
Manual Systems | Lower initial investment | Requires more labor, prone to inconsistencies |
Semi-Automated Systems | Balances cost and efficiency | Suitable for medium-scale operations |
Fully Automated Systems | Maximizes efficiency and consistency | Reduces labor costs, higher upfront investment |
Modern processing equipment includes programmable logic controllers (PLCs) and real-time monitoring to optimize production efficiency.
Automated pet food processing systems improve product consistency and reduce labor costs.Totta
Automation eliminates human error and ensures precise control over production parameters.
4. Energy Efficiency and Sustainability
Energy consumption significantly impacts the cost-effectiveness and environmental footprint of pet food manufacturing.
Energy-Saving Feature | Impact on Operations |
---|---|
Low-Energy Dryers | Reduce electricity costs while maintaining drying efficiency |
High-Efficiency Extruders | Lower operational costs by optimizing heat and mechanical energy usage |
Recyclable Waste Management Systems | Improve sustainability by reducing ingredient waste |
Selecting energy-efficient machinery helps lower production costs and enhances sustainability efforts.
5. Compliance with Safety and Regulatory Standards
Pet food processing equipment must meet industry regulations to ensure food safety and quality.
Regulatory Standard | Requirement | Alue |
---|---|---|
FDA (Food and Drug Administration) | Ensures pet food safety and ingredient compliance | USA |
FSSC 22000 (elintarviketurvallisuusjärjestelmän sertifiointi) | Food safety management system for pet food | Global |
GMP (hyvät tuotantotavat) | Prevents contamination and ensures hygiene | Worldwide |
Pet food processing equipment must comply with FDA regulations to ensure product safety.Totta
FDA guidelines protect against contamination and maintain food quality.
6. Equipment Maintenance and Cleaning
Proper maintenance and sanitation are essential for preventing contamination and ensuring long-term equipment efficiency.
Ominaisuus | Hyöty |
---|---|
Easy Disassembly | Reduces downtime during cleaning |
Self-Cleaning Systems | Minimizes labor requirements |
Corrosion-Resistant Materials | Ensures longevity and prevents contamination |
Equipment designed for easy cleaning and maintenance reduces operational downtime and enhances hygiene.
7. Cost and Return on Investment (ROI)
Balancing cost and value is crucial when investing in pet food processing equipment.
Cost Factor | Pohdintoja |
---|---|
Initial Investment | Upfront purchase cost of machinery |
Operational Costs | Energy usage, maintenance, and labor expenses |
Long-Term ROI | Increased efficiency, product quality, and reduced waste |
While high-quality equipment may have a higher initial cost, it often results in lower operational expenses and improved product consistency.
Comparison of Key Pet Food Processing Equipment
Laitteen tyyppi | Primary Function | Best For |
---|---|---|
Puristimet | Cooking and shaping pet food | Dry kibble and treats |
Grinding & Mixing Equipment | Preparing raw ingredients | Consistency in formulations |
Kuivauskoneet | Moisture reduction | Shelf stability |
Coating Machines | Flavoring and nutrient application | Enhancing palatability |
Packaging Systems | Sealing and labeling | Extending freshness |
High-quality extruders improve pet food digestibility and texture.Totta
Extruders break down starches and proteins, making nutrients more bioavailable.
Päätelmä
Choosing the right pet food processing equipment requires careful consideration of production capacity, ingredient flexibility, automation, energy efficiency, regulatory compliance, maintenance, and cost. Investing in the appropriate machinery ensures high-quality pet food production, reduces operational costs, and improves product consistency.
Kehotus toimintaan
Need help selecting the best pet food processing equipment for your facility? Contact us today for expert recommendations tailored to your production needs!
What Are the Latest Technological Advances in Pet Food Processing?
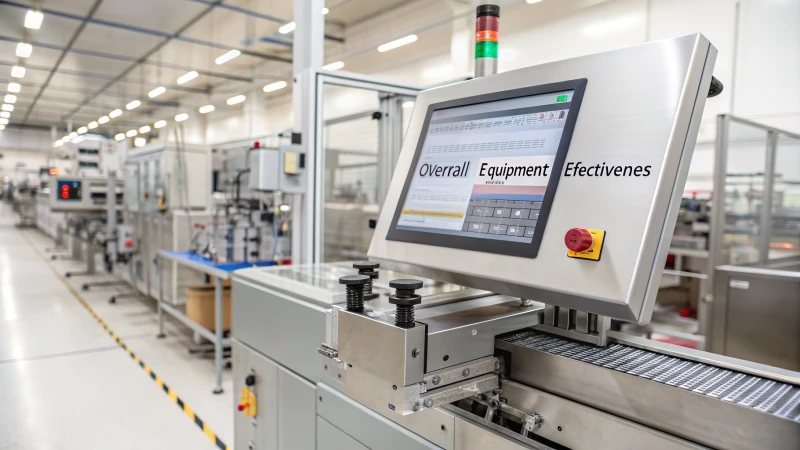
Pet food manufacturers face increasing challenges in maintaining high product quality, optimizing production efficiency, and meeting evolving consumer demands. Traditional pet food processing methods often struggle with inefficiencies, inconsistent nutrient retention, and rising production costs. However, the latest technological advancements in pet food processing have revolutionized the industry by improving automation, precision, sustainability, and ingredient innovation.
The latest technological advances in pet food processing include AI-driven automation, precision extrusion technology, novel ingredient utilization, high-pressure processing (HPP), vacuum coating systems, and smart packaging solutions. These innovations enhance production efficiency, product quality, sustainability, and nutritional value in pet food manufacturing.
Understanding these emerging technologies helps manufacturers stay competitive, improve production efficiency, and meet modern pet food industry demands.
1. AI-Driven Automation in Pet Food Processing
Artificial intelligence (AI) and machine learning (ML) are transforming pet food manufacturing by optimizing operations, reducing waste, and improving product consistency.
AI Technology | Toiminto | Edut |
---|---|---|
AI-Powered Quality Control | Detects irregularities in size, texture, and composition | Reduces defective products |
Predictive Maintenance | Uses sensors to monitor equipment health | Prevents unexpected downtime |
Automated Process Optimization | Adjusts extrusion, drying, and coating in real time | Ensures consistent texture and nutrient retention |
AI-driven automation enhances consistency and reduces production waste in pet food manufacturing.Totta
AI systems continuously monitor and adjust processes, improving efficiency and quality control.
2. Precision Extrusion Technology
Extrusion remains the cornerstone of pet food processing, but recent advancements have improved efficiency, texture control, and nutrient retention.
Advanced Extrusion Feature | Improvement | Hakemus |
---|---|---|
Kaksoisruuviextruuderit | Better mixing, higher efficiency | High-protein and specialty diets |
Low-Temperature Extrusion | Retains more nutrients | Premium and fresh pet food |
Real-Time Parameter Adjustment | Optimizes moisture, pressure, and heat | Ensures consistent kibble quality |
Low-temperature extrusion retains more nutrients compared to high-temperature processing.Totta
Lower heat exposure prevents nutrient degradation, preserving essential vitamins and proteins.
3. Novel Ingredients and Alternative Proteins
Consumers increasingly demand healthier, sustainable, and allergen-free pet food, leading to innovations in ingredient selection.
Novel Ingredient | Reason for Use | Edut |
---|---|---|
Insect Protein (e.g., Black Soldier Fly Larvae) | Sustainable and high-protein | Eco-friendly alternative to meat |
Plant-Based Proteins (e.g., Pea, Lentil, Algae) | Hypoallergenic diets | Suitable for grain-free pet food |
Fermented Ingredients (e.g., Probiotic-Enhanced Feeds) | Improves gut health | Enhances digestion and immunity |
Insect protein is a sustainable alternative to traditional meat in pet food.Totta
Insect farming requires fewer resources and produces less carbon emissions compared to livestock farming.
4. High-Pressure Processing (HPP) for Fresh Pet Food
HPP is a non-thermal method used to eliminate pathogens while preserving nutrients and extending shelf life.
HPP Benefit | Impact on Pet Food |
---|---|
Retains Nutrients | No heat degradation of vitamins and enzymes |
Enhances Safety | Kills harmful bacteria without preservatives |
Extends Shelf Life | Fresh pet food remains safe for longer |
High-pressure processing (HPP) extends the shelf life of fresh pet food without preservatives.Totta
HPP eliminates pathogens while preserving natural nutrients, reducing the need for artificial preservatives.
5. Vacuum Coating for Enhanced Nutrient Absorption
Vacuum coating technology improves the absorption of fats, oils, and vitamins in kibble, enhancing taste and nutrition.
Vacuum Coating Feature | Hyöty |
---|---|
Deep Ingredient Infusion | Ensures better absorption of nutrients |
Even Coating Application | Enhances palatability |
Reduces Nutrient Loss | Improves retention of heat-sensitive vitamins |
Vacuum coating improves nutrient absorption in pet food compared to traditional spraying methods.Totta
The vacuum process ensures deep penetration of fats and vitamins, improving nutritional benefits.
6. Smart Packaging and Traceability Systems
The rise of smart packaging technology allows pet food brands to improve product safety, freshness, and traceability.
Smart Packaging Feature | Toiminto | Hyöty |
---|---|---|
QR Code Tracking | Provides detailed product information | Enhances transparency for consumers |
Freshness Sensors | Detects spoilage or contamination | Ensures food safety |
Biodegradable Packaging | Reduces environmental impact | Supports sustainability efforts |
Smart packaging with QR codes improves pet food traceability and consumer confidence.Totta
Consumers can scan QR codes to access product sourcing, manufacturing details, and expiration dates.
Comparison of Traditional vs. Advanced Pet Food Processing Technologies
Processing Aspect | Traditional Methods | Latest Technologies |
---|---|---|
Puristaminen | High-temperature, less precise | Low-temp, AI-optimized |
Ingredient Use | Traditional grains & meats | Insect protein, plant-based alternatives |
Food Safety | Heat sterilization, preservatives | High-pressure processing (HPP) |
Pinnoite | Surface spraying | Vacuum infusion |
Pakkaus | Basic plastic, no tracking | Smart sensors, QR traceability |
High-tech pet food processing enhances safety, nutrition, and sustainability compared to traditional methods.Totta
Innovations like AI monitoring, HPP, and smart packaging improve product quality and efficiency.
The latest technological advances in pet food processing are revolutionizing the industry by improving efficiency, sustainability, safety, and nutrition. From AI-driven automation and precision extrusion to novel ingredients and high-pressure processing, these innovations help manufacturers meet the growing demand for premium pet food.
Are you looking to upgrade your pet food processing technology? Contact us today for expert solutions tailored to your production needs!
How to Maintain and Optimize Your Pet Food Processing Equipment?
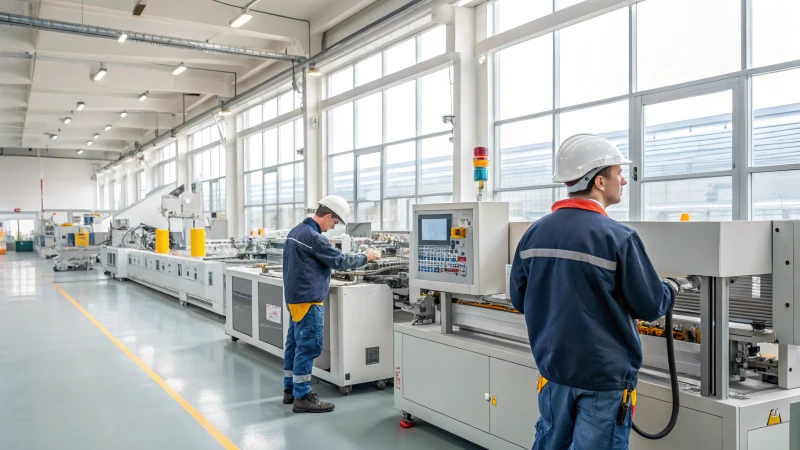
Maintaining and optimizing pet food processing equipment is a significant challenge for manufacturers. Poor maintenance can lead to unexpected downtime, contamination risks, increased operational costs, and inconsistent product quality. Equipment failures can cause delays, product recalls, and safety hazards. However, with proper maintenance and optimization strategies, manufacturers can maximize efficiency, prolong equipment lifespan, and ensure consistent high-quality pet food production.
To maintain and optimize pet food processing equipment, manufacturers should implement a preventive maintenance schedule, ensure proper lubrication and cleaning, monitor equipment performance with IoT technology, train staff on best practices, and upgrade outdated components. Regular inspections and real-time monitoring help prevent breakdowns, improve efficiency, and maintain product quality.
By following structured maintenance procedures and leveraging modern optimization techniques, pet food manufacturers can reduce costs, increase productivity, and improve food safety compliance.
1. Implement a Preventive Maintenance Schedule
A well-planned preventive maintenance (PM) schedule is essential for reducing unplanned downtime and extending equipment life.
Maintenance Task | Frequency | Hyöty |
---|---|---|
Lubrication of moving parts | Viikoittain | Prevents wear and tear |
Cleaning and sanitation | Päivittäin | Reduces contamination risk |
Inspection of mechanical components | Kuukausittain | Detects early signs of failure |
Software and firmware updates | Quarterly | Ensures optimal automation performance |
Calibration of sensors and controls | Bi-annually | Maintains accuracy in measurements |
Preventive maintenance reduces equipment downtime and extends the lifespan of pet food processing machinery.Totta
Routine maintenance prevents unexpected failures and ensures consistent production efficiency.
2. Proper Cleaning and Sanitation Procedures
Cleaning and sanitation are critical for preventing contamination and ensuring product safety in pet food processing.
Cleaning Method | Purpose | Best for |
---|---|---|
Dry Cleaning (Brushing & Vacuuming) | Removes dry residues | Dry ingredient processing areas |
Wet Cleaning (Hot Water & Detergents) | Eliminates grease and protein buildup | Extruders, mixers, and conveyors |
CIP (Clean-in-Place) Systems | Automatic cleaning of pipes and tanks | Liquid and wet pet food processing |
Steam Cleaning | Kills bacteria and removes stubborn residues | High-risk contamination areas |
Proper cleaning and sanitation prevent cross-contamination in pet food processing facilities.Totta
Effective cleaning protocols eliminate harmful bacteria and maintain product safety.
3. Lubrication and Wear Prevention
Lubrication reduces friction and prevents premature wear in high-speed pet food processing equipment.
Komponentti | Recommended Lubricant | Frequency |
---|---|---|
Extruder Screws | Food-grade grease | Viikoittain |
Bearings and Rollers | Synthetic lubricant | Kuukausittain |
Conveyor Belts | Light oil | Bi-weekly |
Pneumatic Systems | Silicone-based oil | Every 3 months |
Use only food-grade lubricants to prevent contamination in pet food manufacturing.
Using food-grade lubricants in pet food processing prevents contamination and ensures safety.Totta
Standard industrial lubricants can introduce harmful chemicals into food products, making food-grade options essential.
4. Monitoring Equipment Performance with IoT and AI
The integration of IoT (Internet of Things) and AI-powered monitoring systems enhances real-time performance tracking and predictive maintenance.
Technology | Toiminto | Hyöty |
---|---|---|
IoT Sensors | Monitor temperature, pressure, and vibration | Detects early signs of failure |
AI-Based Predictive Maintenance | Analyzes equipment performance trends | Prevents breakdowns before they occur |
Remote Monitoring Systems | Allows real-time equipment supervision | Reduces on-site maintenance costs |
IoT monitoring systems help detect early signs of equipment failure in pet food processing.Totta
Real-time data analysis prevents unexpected downtime and extends machinery lifespan.
5. Staff Training and Best Practices
Well-trained personnel are essential for maintaining equipment efficiency and preventing operational errors.
Training Focus | Importance | Frequency |
---|---|---|
Standard Operating Procedures (SOPs) | Ensures consistent operation | Bi-annually |
Troubleshooting Common Issues | Reduces downtime | Quarterly |
Safety and Hygiene Compliance | Prevents contamination | Kuukausittain |
Equipment Handling and Maintenance | Improves longevity | Annually |
Providing hands-on training and up-to-date manuals helps employees maintain equipment properly.
6. Upgrading Outdated Components
Replacing worn-out or outdated parts enhances efficiency and prevents sudden failures.
Komponentti | Signs of Wear | Recommended Action |
---|---|---|
Extruder Screws | Decreased throughput, inconsistent texture | Replace annually |
Conveyor Belts | Fraying, misalignment | Inspect monthly, replace as needed |
Bearings | Unusual noise, overheating | Lubricate regularly, replace if damaged |
Sensors and Controls | Erratic readings | Calibrate or upgrade periodically |
Investing in modern, energy-efficient parts can reduce power consumption and increase output.
7. Optimizing Production Efficiency
To maximize performance, optimize processing equipment settings based on production demands.
Optimization Strategy | Vaikutus |
---|---|
Adjust Extrusion Parameters | Improves texture and digestibility |
Optimize Drying Time and Temperature | Reduces energy usage while maintaining quality |
Enhance Ingredient Blending Techniques | Ensures uniform nutrient distribution |
Use Smart Automation Systems | Increases consistency and reduces labor costs |
Optimizing extrusion parameters improves the texture and digestibility of pet food.Totta
Properly adjusted temperature, pressure, and moisture levels enhance product quality and palatability.
Comparison of Maintenance Strategies
Strategy | Edut | Best For |
---|---|---|
Preventive Maintenance | Reduces unplanned downtime, extends lifespan | All processing equipment |
Predictive Maintenance (IoT-Based) | Detects failures before they occur | High-tech, automated facilities |
Corrective Maintenance | Fixes unexpected breakdowns | Emergency repairs |
Proactive Component Replacement | Prevents costly failures | High-wear parts (extruders, conveyors) |
Predictive maintenance using IoT reduces sudden equipment failures in pet food processing.Totta
Real-time monitoring helps detect wear and prevent major breakdowns before they happen.
Maintaining and optimizing pet food processing equipment is essential for ensuring efficiency, safety, and product quality. By implementing preventive maintenance schedules, optimizing lubrication and cleaning, utilizing IoT monitoring, training staff, upgrading outdated parts, and optimizing production settings, manufacturers can improve operational efficiency and reduce downtime.
Need expert advice on maintaining and optimizing your pet food processing equipment? Contact us today for customized solutions to enhance your production efficiency!
How to Ensure Compliance with Pet Food Industry Regulations?
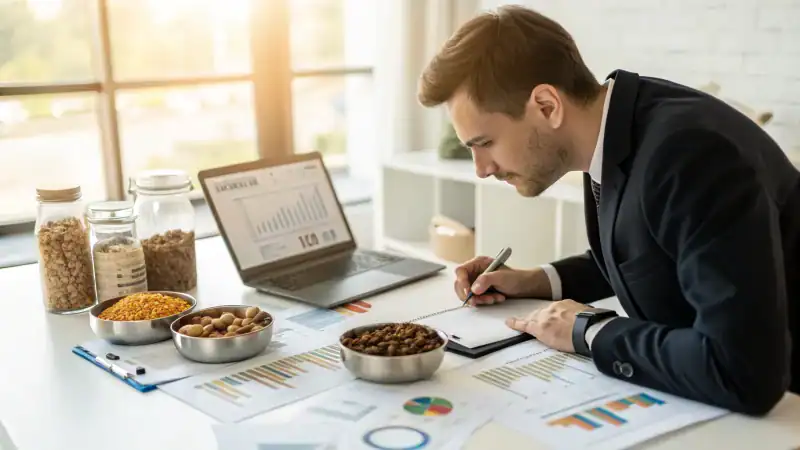
Compliance with pet food industry regulations is a major challenge for manufacturers. Failure to meet safety, labeling, and quality standards can result in product recalls, legal penalties, and damage to brand reputation. With increasing consumer demand for transparency and stringent regulatory requirements, ensuring compliance has become a critical aspect of pet food production. However, by implementing proper regulatory frameworks, quality control measures, and traceability systems, manufacturers can guarantee safe, high-quality pet food that meets industry standards.
To ensure compliance with pet food industry regulations, manufacturers should adhere to FDA, AAFCO, FSSC 22000, and GMP guidelines, implement Hazard Analysis and Critical Control Points (HACCP) protocols, establish rigorous quality control testing, and use traceability systems for ingredient tracking. Regular audits and staff training further help maintain compliance and product safety.
By following these best practices, pet food manufacturers can meet legal requirements, prevent contamination, and build consumer trust.
1. Understanding Key Regulatory Standards
Different countries and regions have specific regulatory requirements for pet food safety, labeling, and production standards.
Regulatory Body | Alue | Key Requirements |
---|---|---|
FDA (Food and Drug Administration) | USA | Ensures safety, proper labeling, and ingredient approval |
AAFCO (Association of American Feed Control Officials) | USA | Sets nutritional standards for pet food formulation |
FSSC 22000 (elintarviketurvallisuusjärjestelmän sertifiointi) | Global | Certifies food safety management systems |
GMP (hyvät tuotantotavat) | Worldwide | Enforces hygiene and process control standards |
EU Pet Food Regulations (Regulation EC 767/2009 & 183/2005) | Europe | Regulates pet food labeling and hygiene standards |
ISO 22000 (International Food Safety Standard) | Global | Covers risk management and traceability |
Compliance with FDA and AAFCO regulations is required for pet food manufacturers in the United States.Totta
The FDA regulates pet food safety and labeling, while AAFCO provides nutritional standards for pet food formulations.
2. Implementing Hazard Analysis and Critical Control Points (HACCP)
HACCP is a globally recognized system for identifying and controlling food safety hazards in pet food manufacturing.
HACCP Principle | Implementation in Pet Food Processing |
---|---|
Conduct a Hazard Analysis | Identify biological, chemical, and physical risks (e.g., Salmonella, mycotoxins, foreign objects) |
Determine Critical Control Points (CCPs) | Monitor key points where hazards can be prevented (e.g., cooking temperatures, metal detection) |
Establish Critical Limits | Define acceptable limits (e.g., minimum heat treatment temperature for pathogen elimination) |
Monitor CCPs | Implement sensors and automated tracking for real-time monitoring |
Corrective Actions | Define response procedures for non-compliance |
Verification Procedures | Conduct regular testing and audits |
Record Keeping | Maintain logs of production batches, inspections, and corrective actions |
HACCP implementation helps prevent contamination and ensures pet food safety.Totta
HACCP systems identify potential hazards and establish controls to minimize risks in pet food production.
3. Establishing Rigorous Quality Control Testing
Regular quality control (QC) testing ensures pet food meets safety and nutritional standards.
Testing Type | Purpose | Frequency |
---|---|---|
Microbiological Testing | Detects Salmonella, E. coli, and mold contamination | Per batch |
Nutritional Analysis | Confirms protein, fat, fiber, and vitamin levels | Kuukausittain |
Heavy Metal Testing | Ensures pet food is free from lead, mercury, and arsenic | Quarterly |
Mycotoxin Screening | Detects fungal toxins in grains and cereals | Per batch |
Foreign Material Inspection | Identifies plastic, glass, and metal contaminants | Continuous with automated detection |
Automated sensors and AI-powered testing systems help streamline the quality assurance process.
Microbiological testing is essential to prevent bacterial contamination in pet food.Totta
Regular pathogen testing ensures compliance with food safety regulations and protects animal health.
4. Ensuring Proper Labeling and Ingredient Transparency
Accurate and compliant labeling is essential for regulatory approval and consumer trust.
Labeling Requirement | Regulation | Esimerkki |
---|---|---|
Ingredient List | Must follow AAFCO guidelines | "Chicken meal, brown rice, peas, fish oil, vitamins" |
Guaranteed Analysis | Required for protein, fat, fiber, and moisture | "Crude Protein (Min) 25%, Crude Fat (Min) 15%" |
Nutritional Adequacy Statement | Declares pet food suitability for life stages | "Complete and balanced nutrition for adult dogs" |
Feeding Directions | Provides portion guidance | "Feed 1 cup per 10 lbs. of body weight per day" |
Manufacturing & Expiration Date | Ensures traceability | "Manufactured: 2025-01-15, Best Before: 2026-01-15" |
AAFCO-compliant pet food labeling ensures accurate nutritional information for consumers.Totta
AAFCO regulations require guaranteed analysis and ingredient listing to inform pet owners about pet food content.
5. Implementing Ingredient Traceability and Supply Chain Management
Traceability ensures ingredient sourcing meets safety and ethical standards.
Traceability Method | Toiminto | Hyöty |
---|---|---|
Batch Coding | Assigns unique codes to production lots | Allows recall tracking |
QR Code Tracking | Provides supply chain transparency | Enhances consumer trust |
Blockchain Integration | Creates tamper-proof ingredient records | Prevents fraud in organic or grain-free claims |
Supplier Audits | Ensures raw material compliance | Maintains consistency and quality |
Ingredient traceability systems help prevent contamination and ensure quality control in pet food production.Totta
Traceability allows manufacturers to track ingredients from sourcing to final product, ensuring safety and compliance.
6. Conducting Regular Internal and External Audits
Audits help verify compliance with regulatory and safety standards.
Audit Type | Purpose | Frequency |
---|---|---|
Internal Audits | Ensures internal SOPs align with regulations | Kuukausittain |
Third-Party Certification Audits | Verifies compliance with GMP, FSSC 22000, and ISO 22000 | Annually |
Regulatory Inspections | Confirms adherence to FDA/AAFCO standards | As required by law |
Automated compliance management software can streamline audit scheduling and documentation.
Regular audits ensure pet food manufacturing compliance with safety regulations.Totta
Audits help identify compliance gaps and improve food safety management systems.
Comparison of Compliance Strategies
Compliance Approach | Impact on Pet Food Safety | Best For |
---|---|---|
HACCP-Based Food Safety Plans | Prevents contamination risks | All pet food manufacturers |
Automated Quality Control Testing | Ensures batch consistency | Large-scale production facilities |
Blockchain Traceability Systems | Increases supply chain transparency | Premium and organic pet food brands |
Third-Party Certification Audits | Strengthens regulatory compliance | Global market expansion |
Third-party certification audits improve pet food industry compliance and consumer confidence.Totta
External audits validate adherence to regulatory standards, ensuring higher safety and quality control.
Ensuring compliance with pet food industry regulations requires a structured approach, including adherence to FDA, AAFCO, and GMP standards, implementation of HACCP food safety plans, rigorous quality control testing, proper labeling, and ingredient traceability. Regular audits and supply chain management further help maintain compliance and improve food safety.
Need assistance in achieving full compliance with pet food industry regulations? Contact us today for expert guidance and customized compliance solutions!
Päätelmä
Investing in the right pet food processing equipment is essential for producing high-quality, nutritious pet food efficiently and cost-effectively. By understanding the different types of machinery, technological advancements, and industry regulations, manufacturers can optimize their production processes and stay competitive in the market.
Get Expert Advice
Looking for the best pet food processing equipment for your business? Contact us today for expert recommendations and customized solutions!