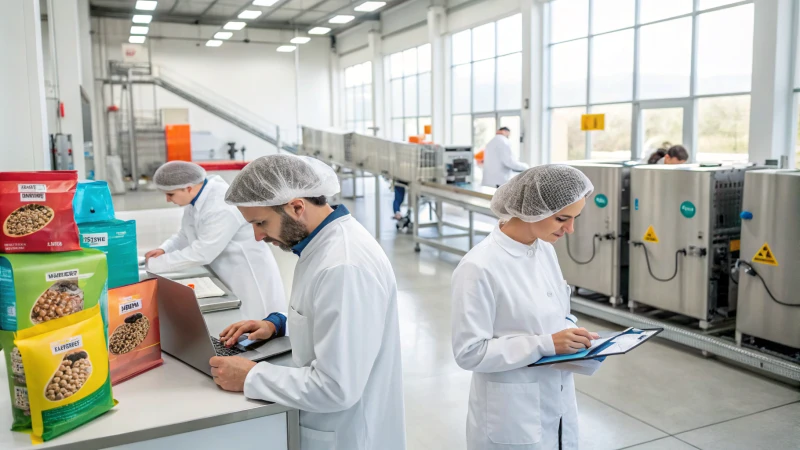
Extrusion processing is a critical technology in the pet food industry due to its ability to produce high-quality, palatable, and nutritious dog food efficiently. The process is influenced by key parameters such as moisture content, die temperature, and screw speed. These parameters directly impact the physical and textural properties of dog food, including bulk density, unit density, expansion ratio, hardness, crispiness, and specific mechanical energy (SME). Understanding the intricate relationships among these parameters and product quality traits is essential for optimizing production processes.
In this article, we provide a detailed analysis of how extrusion parameters affect dog food quality. We use comprehensive experimental data, including response surface regression analysis, to guide manufacturers in achieving the best processing outcomes.
How do extrusion process parameters impact dog food quality?
Extrusion process parameters—moisture content, die temperature, and screw speed—significantly affect the bulk density, unit density, expansion ratio, hardness, crispiness, and SME of dog food. Adjusting these parameters appropriately enhances the product's texture, palatability, and production efficiency while maintaining nutritional quality.
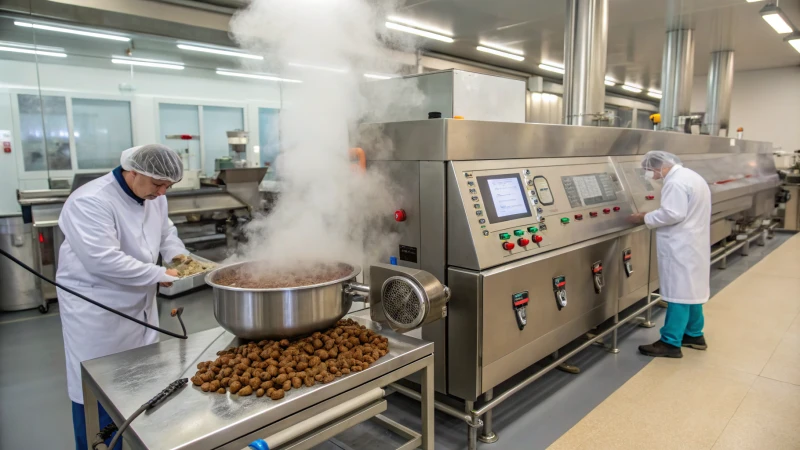
This study utilized a central composite design (CCD) to systematically analyze the effects of these parameters. The findings demonstrate how variations in moisture, temperature, and screw speed impact key quality traits, offering practical recommendations for optimizing extrusion processing conditions.
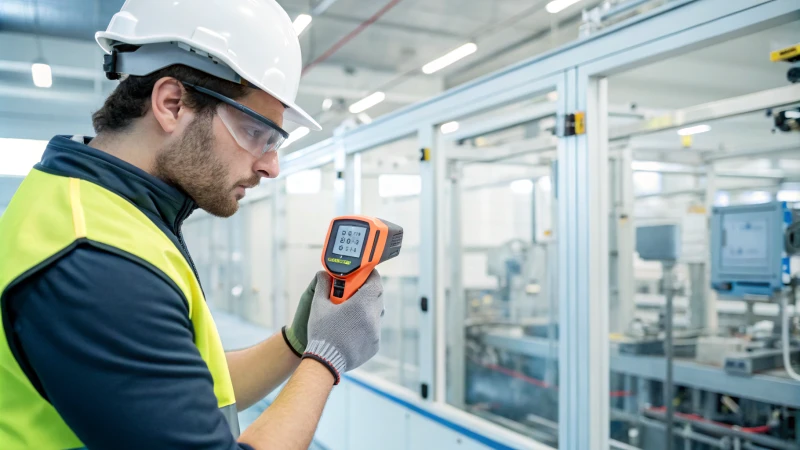
Materials and Methods
Experimental Design
A central composite design (CCD) with three independent variables—moisture content (A), die temperature (B), and screw speed (C)—was used to assess their effects on six quality indicators. Each variable was tested at five levels, with 20 experimental runs conducted.
Table 1: Central Composite Design Variable Table
Variable | Symbol | -α | -1 | 0 | 1 | α |
---|---|---|---|---|---|---|
Moisture Content (%) | A | 22 | 23.62 | 26 | 28.38 | 30 |
Die Temperature (°C) | B | 110 | 118 | 130 | 142 | 150 |
Screw Speed (r/min) | C | 180 | 204 | 240 | 276 | 300 |
Dog Food Formulation
The experimental dog food composition and nutritional profile are detailed in Table 2:
Table 2: Dog Food Composition and Nutritional Levels
Ingredient | Percentage (%) |
---|---|
Corn | 29 |
Wheat | 8 |
Rice | 8 |
Sweet Potato | 6 |
Soybean Meal | 12 |
Meat Meal | 27 |
Oil and Fat | 10 |
Total | 100 |
Nutritional Levels:
- Crude Protein: 28.0%
- Crude Fat: 14.0%
- Ash: 9.8%
- Calcium: 1.3%
- Phosphorus: 1.1%
Experimental Results
Experimental Data
The measured values for bulk density, unit density, expansion ratio, hardness, crispiness, and SME are summarized in Table 3.
Table 3: Experimental Results of Dog Food Quality Traits
Run | A (Moisture) | B (Temperature) | C (Screw Speed) | Bulk Density (g/L) | Unit Density (g/L) | Expansion Ratio | Hardness (g) | Crispiness (mm) | SME (kJ/kg) |
---|---|---|---|---|---|---|---|---|---|
1 | -1 | -1 | -1 | 547.3 ± 1.0 | 0.91 ± 0.13 | 1.56 ± 0.06 | 5,751 ± 1,023 | 0.71 ± 0.13 | 28.78 ± 1.27 |
2 | -1 | -1 | 1 | 509.2 ± 1.0 | 0.81 ± 0.15 | 1.62 ± 0.07 | 5,376 ± 575 | 0.67 ± 0.10 | 27.29 ± 1.57 |
3 | -1 | 1 | -1 | 509.6 ± 0.5 | 0.83 ± 0.06 | 1.65 ± 0.04 | 6,469 ± 542 | 0.74 ± 0.10 | 36.67 ± 1.24 |
4 | -1 | 1 | 1 | 524.1 ± 1.0 | 0.90 ± 0.23 | 1.62 ± 0.08 | 5,473 ± 867 | 0.71 ± 0.12 | 35.53 ± 2.21 |
5 | 1 | -1 | -1 | 336.5 ± 2.0 | 0.54 ± 0.10 | 1.99 ± 0.10 | 4,811 ± 773 | 0.74 ± 0.12 | 19.54 ± 1.71 |
6 | 1 | -1 | 1 | 314.6 ± 1.0 | 0.51 ± 0.16 | 2.07 ± 0.04 | 4,776 ± 832 | 0.67 ± 0.10 | 22.78 ± 1.40 |
7 | 1 | 1 | -1 | 333.0 ± 1.0 | 0.55 ± 0.12 | 2.02 ± 0.06 | 4,833 ± 647 | 0.68 ± 0.08 | 20.95 ± 1.50 |
8 | 1 | 1 | 1 | 331.1 ± 0.5 | 0.54 ± 0.10 | 2.03 ± 0.03 | 4,660 ± 332 | 0.66 ± 0.11 | 21.63 ± 1.12 |
9 | -1.682 | 0 | 0 | 531.1 ± 1.0 | 0.84 ± 0.13 | 1.55 ± 0.11 | 6,311 ± 587 | 0.74 ± 0.10 | 30.67 ± 1.84 |
20 | 0 | 0 | 0 | 425.5 ± 1.0 | 0.71 ± 0.09 | 1.80 ± 0.08 | 4,851 ± 986 | 0.61 ± 0.10 | 25.59 ± 1.82 |
Analysis of Variance (ANOVA)
The regression analysis results for the response variables are detailed in Table 4.
Table 4: ANOVA Results for Dog Food Quality Traits
Factor/Model | Bulk Density | Unit Density | Expansion Ratio | Hardness | Crispiness | SME |
---|---|---|---|---|---|---|
A (Moisture) | < 0.0001 | < 0.0001 | < 0.0001 | < 0.0001 | 0.847 | < 0.0001 |
B (Temperature) | 0.930 | 0.807 | 0.794 | 0.0004 | 0.847 | 0.0003 |
C (Screw Speed) | 0.938 | 0.997 | 0.776 | 0.0007 | 0.106 | < 0.0001 |
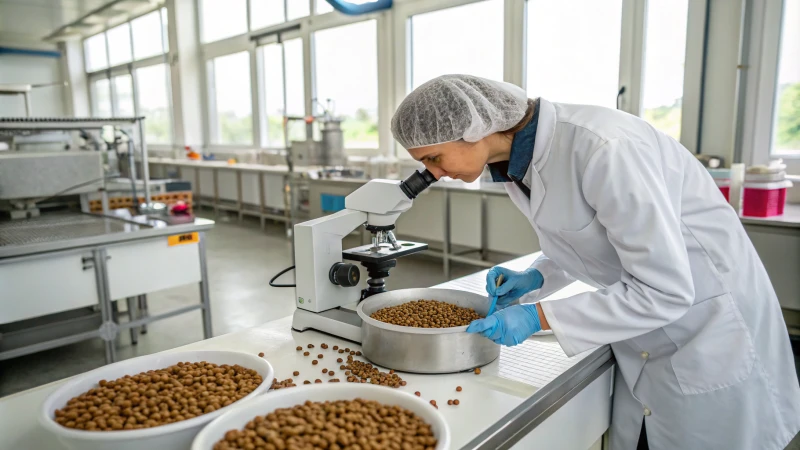
What are the critical extrusion parameters that influence the quality of dog food?
Understanding the impact of moisture content, die temperature, and screw speed on the final product’s quality is essential in optimizing dog food production. This section explores how these extrusion parameters play a crucial role in shaping the physical and sensory properties of dog food.
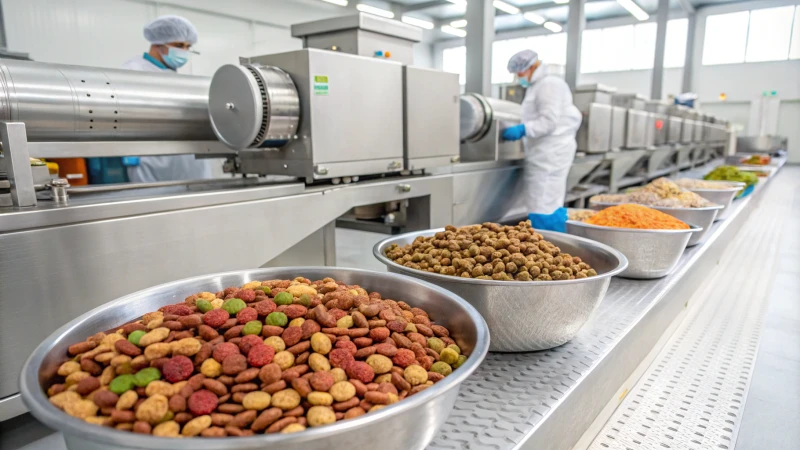
The extrusion process is an integrated system where raw ingredients are subjected to heat, pressure, and mechanical force. As a result, the raw materials undergo chemical reactions like starch gelatinization and protein denaturation. The extrusion parameters—moisture content, die temperature, and screw speed—are pivotal in controlling the degree of these transformations.
1. Moisture Content:
Moisture content is one of the most influential parameters in extrusion. It affects the food’s expansion ratio, hardness, crispiness, and overall structure. Water acts as a medium for heat transfer and enables starch gelatinization, which is critical for achieving the desired texture and expansion. Research indicates that a higher moisture content results in a greater expansion ratio and a lower bulk density. However, if the moisture content is too high, it may cause the product to become dense and chewy, negatively impacting the food's texture.
2. Die Temperature:
Die temperature influences the starch gelatinization and protein denaturation processes. At higher temperatures, starch is more likely to gelatinize, leading to increased expansion and lower bulk density. However, excessively high temperatures may cause over-cooking, leading to nutrient degradation. The key is finding the right temperature to ensure optimal starch gelatinization without damaging the nutritional value of the ingredients.
3. Screw Speed:
The screw speed dictates the shear force and mechanical energy applied to the ingredients, which affects the texture and expansion of the dog food. At higher screw speeds, the increased shear force helps create a lighter, fluffier product, as it encourages the formation of air bubbles. However, excessively high screw speeds can lead to over-shearing, which may result in a denser product and loss of crispiness. It is crucial to balance screw speed with other factors like moisture content and die temperature to achieve the desired texture and expansion.
Higher moisture content leads to better expansion in dog food extrusion.False
Moisture content plays a critical role in starch gelatinization, which directly affects the expansion ratio of the final product.
How do extrusion parameters affect the bulk density of dog food?
Bulk density is a key factor in determining the final product’s texture and mouthfeel. It is closely related to expansion ratio and is influenced by extrusion parameters such as moisture content, screw speed, and die temperature. This section investigates how these factors contribute to the bulk density of dog food.
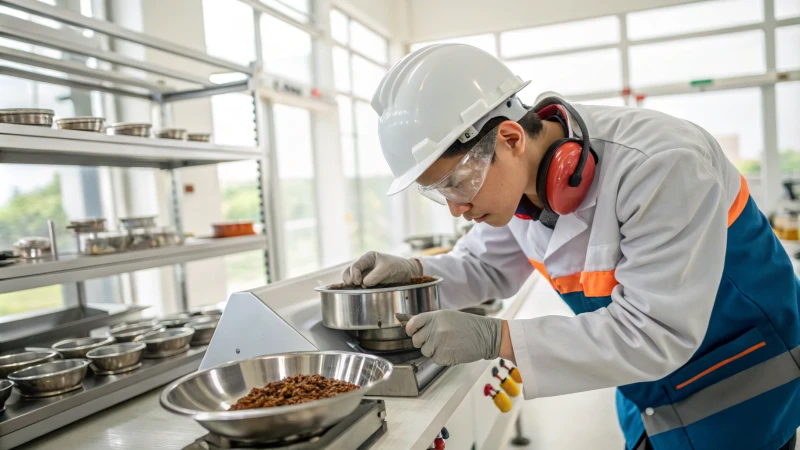
Bulk density is inversely related to expansion, which means that a higher expansion ratio typically leads to a lower bulk density. Moisture content has the most significant effect on bulk density, as it influences the formation of air pockets within the dog food during extrusion. The increased moisture content enables better starch gelatinization, which creates a more porous structure with lower bulk density.
The screw speed also affects the bulk density by influencing the shear force and the rate at which air bubbles form within the product. Higher screw speeds typically lead to more intense shear forces, causing the product to expand more and resulting in a lower bulk density. However, at excessively high screw speeds, the product may lose its expansion, resulting in a denser and harder texture.
Bulk density decreases with higher screw speed and moisture content.False
As screw speed and moisture content increase, the expansion ratio improves, leading to a decrease in bulk density.
What role does hardness and crispiness play in the sensory appeal of dog food?
Hardness and crispiness are critical attributes that influence a dog’s enjoyment and willingness to eat. These characteristics are heavily influenced by extrusion parameters such as moisture content, screw speed, and die temperature. In this section, we examine how these factors affect the hardness and crispiness of dog food.
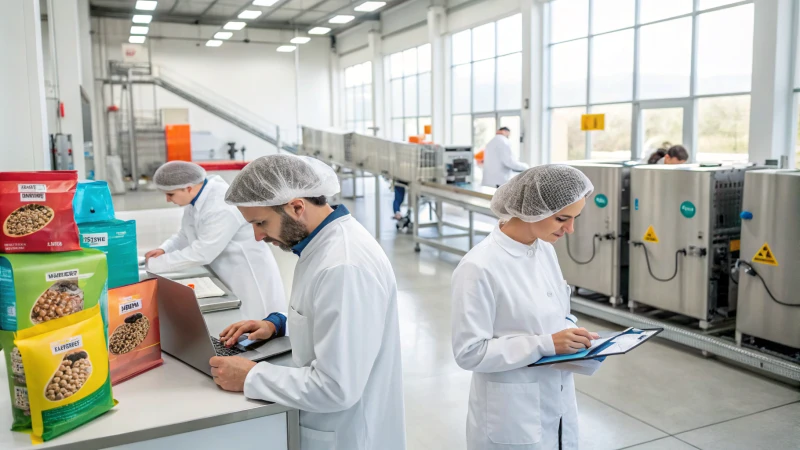
Hardness and crispiness are both texture attributes that play a significant role in the palatability of dog food. As moisture content increases, the hardness of the dog food typically decreases. This is because water acts as a medium for starch expansion and gelatinization, leading to a more delicate and soft structure. However, if the moisture content is too high, the product may become overly soft and lose its crispiness.
Screw speed also plays a critical role in determining the hardness of the food. At low screw speeds, the ingredients are not subjected to enough shear force, which results in a harder product. At higher screw speeds, the increased shear force disrupts the ingredient structure, reducing the hardness and increasing the crispiness of the final product. However, excessively high screw speeds can lead to over-shearing, making the product less crispy and more brittle.
Hardness decreases as moisture content increases, but too much moisture can affect crispiness.False
Moisture content is crucial for texture, but it must be carefully controlled to ensure a balance between hardness and crispiness.
How do extrusion parameters affect the Specific Mechanical Energy (SME) in dog food production?
Specific Mechanical Energy (SME) is a measure of the energy used during extrusion and is essential for understanding the efficiency of the extrusion process. SME is influenced by extrusion parameters such as screw speed and moisture content. This section explores how SME affects the quality and energy efficiency of dog food production.
SME is a critical factor in determining how much mechanical energy is required to process the ingredients during extrusion. Higher moisture content generally reduces SME, as the water helps lubricate the material, reducing friction and shear forces. On the other hand, increasing the screw speed leads to higher SME, as the shear forces and torque applied to the material are greater. Therefore, controlling SME is crucial for optimizing energy consumption and ensuring the production of high-quality dog food with the desired texture and expansion.
Higher screw speed increases SME, but moisture content reduces SME.False
Screw speed increases shear forces and energy consumption, while higher moisture content reduces the friction and energy required during extrusion.
This comprehensive analysis of extrusion parameters will assist manufacturers in refining their processes for better-quality dog food, providing valuable insights into the relationship between process settings and product characteristics.
Conclusion
This study demonstrates that extrusion process parameters—moisture content, die temperature, and screw speed—significantly affect the physical and textural qualities of dog food. Optimal conditions include:
- Moisture Content: 26%–28%
- Die Temperature: 130°C–142°C
- Screw Speed: 240–276 rpm
By optimizing these parameters, manufacturers can achieve dog food with:
- Low bulk density
- High expansion ratio
- Desirable crispiness and hardness
- Energy-efficient SME values
Extrusion is a key process in dog food production, and understanding the effects of extrusion parameters is essential for optimizing the quality of the final product. Moisture content, die temperature, and screw speed all play significant roles in determining the bulk density, expansion ratio, hardness, crispiness, and SME of the dog food. The goal is to find the optimal combination of these parameters to produce high-quality, palatable, and nutritious dog food.
With this understanding, manufacturers can adjust extrusion conditions to meet the specific needs of their products and consumers, ensuring that dogs enjoy their meals and receive the best possible nutrition.
Call to Action
Need help optimizing your dog food extrusion process? Contact us today to enhance your production efficiency and deliver superior-quality dog food.
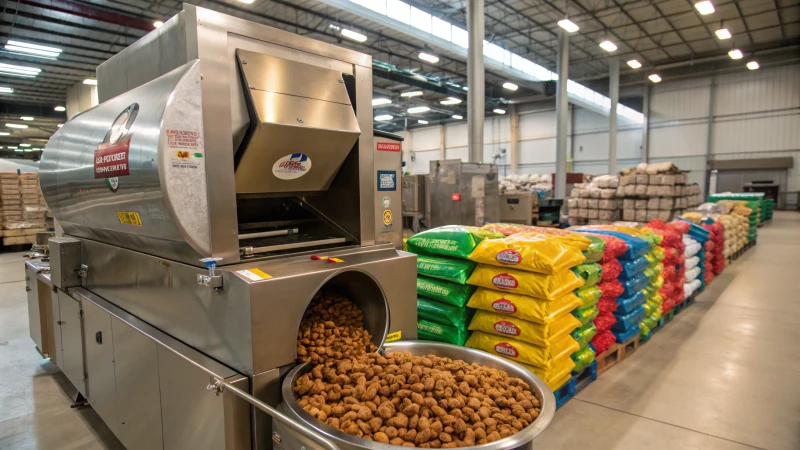