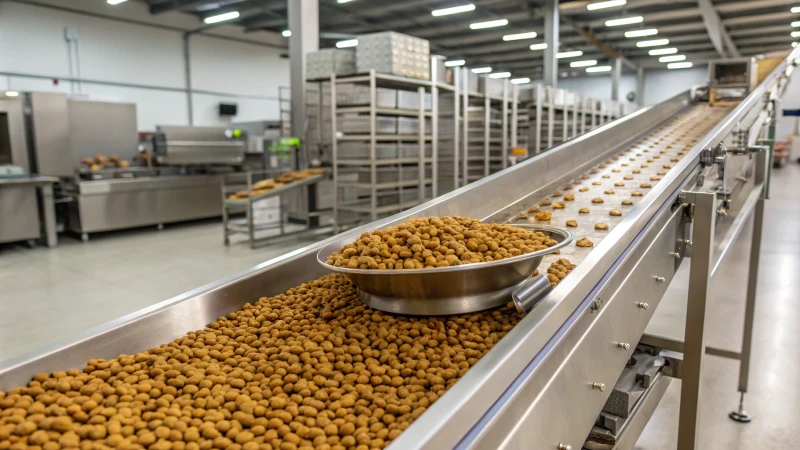
In the pet food industry, understanding the production capacity of a pet food production line is critical for manufacturers who want to meet market demand, ensure operational efficiency, and optimize profitability. Without proper insight into production capacity, companies could either overestimate their abilities and face excess inventory or underestimate them and struggle to meet consumer needs. The consequences of miscalculating production capacity can lead to production delays, loss of market share, and increased operational costs.
The production capacity of a pet food production line refers to the maximum amount of pet food the line can produce within a specific time frame, such as per hour, per day, or per month. This capacity is influenced by multiple factors including the type of pet food being produced, the complexity of the manufacturing process, the level of automation, and the scale of the production facility.
Understanding these factors and calculating the right production capacity is crucial for scaling up production, entering new markets, and maintaining a steady flow of products without compromising quality.
How Does Production Capacity Vary in Pet Food Manufacturing?
The production capacity of a pet food production line varies widely depending on several factors, such as the type of pet food being produced, the machinery and technologies used, and the facility's scale.
Here are the main factors that influence the production capacity of pet food production lines:
-
Type of Pet Food: Whether it’s dry food (kibble), wet food (canned or pouched), treats, or specialty diets, each type of pet food has different processing requirements that affect production capacity.
-
Level of Automation: The degree of automation in the production process (manual, semi-automated, or fully automated) directly influences the output of the production line. Fully automated lines can produce significantly more units per hour than manual or semi-automated systems.
-
Machine Specifications: The specific equipment used, such as extruders, ovens, filling machines, and packaging systems, plays a critical role in determining how much pet food can be produced within a given time frame.
-
Production Line Configuration: Lines that can process multiple types of pet food simultaneously or have advanced features (like faster extrusion speeds or more efficient drying processes) will have higher production capacities.
-
Product Size and Packaging: Larger production runs with simplified packaging options (bulk bags, for instance) can have higher output compared to smaller, more complex packaging formats (like single-serving packs or premium packaging).
Typical Production Capacities for Different Types of Pet Food
1. Dry Pet Food (Kibble)
Dry pet food is one of the most commonly produced types of pet food. These production lines are highly automated, with large extrusion systems that can process large quantities of ingredients at high speeds.
Production Capacity:
- Hourly Production: A dry pet food production line can typically produce between 3,000 to 15,000 kilograms of kibble per hour, depending on the complexity and scale of the line.
- Daily Production: On a 24-hour schedule, this can amount to anywhere from 72,000 to 360,000 kilograms of dry food per day.
Key Factors Influencing Capacity:
- Extruder size and type
- Mixer and ingredient handling capacity
- Drying and cooling time
- Packaging speed
2. Comida húmeda para mascotas (en lata o en bolsa)
Wet pet food production lines are often more complex, as they involve cooking, canning or pouching, sterilization, and sealing processes. These lines generally have lower throughput compared to dry food production lines, due to the time needed for sterilization and sealing.
Production Capacity:
- Hourly Production: Wet food production lines can typically produce between 1,000 to 5,000 cans or pouches per hour.
- Daily Production: In a 24-hour operation, the daily output can range from 24,000 to 120,000 cans or pouches per day.
Key Factors Influencing Capacity:
- Sterilization equipment efficiency
- Canning or pouching speed
- Ingredient preparation and mixing
- Packaging line setup and automation level
3. Pet Treats and Snacks
Pet treat production lines are highly versatile, with machinery that can handle a wide variety of treat formats such as biscuits, chews, dental sticks, and more. The capacity will depend on the type of treats being produced.
Production Capacity:
- Hourly Production: A typical pet treat production line can produce 2,000 to 10,000 kilograms of treats per hour, depending on the type of treats and the line’s automation level.
- Daily Production: On a 24-hour cycle, this could result in 48,000 to 240,000 kilograms of treats per day.
Key Factors Influencing Capacity:
- Type of treats (baked, extruded, or dehydrated)
- Oven or drying capacity
- Packaging and labeling speed
- Multi-functional equipment (e.g., molding, shaping, and coating)
4. Freeze-Dried or Frozen Pet Food
Freeze-dried pet food production requires specialized equipment like freeze-dryers or blast freezers to preserve the nutritional content of the food. These lines are generally slower due to the time-consuming freeze-drying or freezing process.
Production Capacity:
- Hourly Production: The production rate for freeze-dried pet food can range from 100 to 1,000 kilograms per hour, depending on the freeze-drying equipment and the batch size.
- Daily Production: In a 24-hour period, production could be 2,400 to 24,000 kilograms por día.
Key Factors Influencing Capacity:
- Freeze-dryer size and cycle time
- Ingredient formulation and preparation
- Packaging requirements (vacuum-sealed or nitrogen-flushed packaging)
How to Calculate the Optimal Production Capacity for Your Pet Food Line
Calculating the optimal production capacity for a pet food line requires understanding the specific needs of your business and market demand. Here’s how you can approach it:
1. Estimate Market Demand
The first step is to estimate how much pet food you need to produce to meet current and projected market demand. Analyze historical sales data, seasonal trends, and consumer preferences.
2. Assess Available Equipment and Technology
Evaluate the equipment’s throughput capabilities, including extrusion speed, sterilization cycles, and packaging line speed. It’s also important to factor in downtime for maintenance and equipment changes.
3. Consider Product Variety
If your production line is designed to handle multiple types of pet food (e.g., dry food, wet food, and treats), it’s essential to assess how product changes (such as switching from kibble to canned food) will affect the overall throughput.
4. Factor in Quality Control and Packaging Time
Efficient quality control procedures and packaging time are key to maximizing production capacity. Products that require intricate packaging, such as individual pouches or premium packaging formats, may slow down production rates.
5. Balance Production Capacity and Flexibility
Overestimating capacity can result in overproduction, leading to wasted resources and increased operational costs. On the other hand, underestimating production capacity can result in missed sales opportunities.
Conclusion: What is the Ideal Production Capacity for Your Pet Food Production Line?
The ideal production capacity of a pet food production line depends on a variety of factors, including the type of pet food being produced, the level of automation, and the scale of the production facility.
A well-designed production line, capable of adjusting to market demands and varying product types, can help maximize efficiency and ensure consistent product quality. Manufacturers must consider both the volume of production y el flexibility of their lines to meet customer needs, minimize downtime, and optimize their profit margins.
To calculate the ideal production capacity, it's essential to factor in equipment specifications, product types, production schedules, and market demand. With the right approach, manufacturers can scale their production lines to meet growing demand while maintaining high-quality standards.
Darin® Pet food production line
Modelo | Capacity (kg/h) | Power (kW) | Dimension (m) |
---|---|---|---|
DR-65 | 120-150 kg/h | 80 kW | 18 x 5 x 3 m |
DR-70 | 200-300 kg/h | 90 kW | 20 x 5 x 3 m |
DR-85 | 500-600 kg/h | 150 kW | 30 x 5 x 4 m |
DR-90 | 800-1000 kg/h | 200 kW | 35 x 5 x 5 m |
DR-95 | 2000 kg/h | 250 kW | 40 x 10 x 16 m |
DR-120 | 3000 kg/h | 350 kW | 50 x 10 x 20 m |
DR-135 | 5000 kg/h | 450 kW | 60 x 10 x 24 m |
If you’re looking to optimize your pet food production line and ensure it meets your production goals, contact us today. Our team of experts can help you assess your needs and implement solutions tailored to your business.
External Footnotes & Recommended Reading
- How Extrusion Technology Increases Production Efficiency: Learn how extrusion can speed up the production of dry kibble while maintaining product consistency.
- The Role of Automation in Scaling Pet Food Production: Discover how automated lines can help increase output and reduce labor costs.
- Freeze-Drying for Pet Food: A Growing Trend: Understand the freeze-drying process and its advantages for premium pet food.
- Maximizing Efficiency in Pet Treat Production: Learn how to optimize your pet treat production line to produce high-quality snacks at high speed.
- Maintaining High Production Standards in Pet Food: Explore the importance of quality control in the pet food manufacturing process.
- Understanding Different Pet Food Packaging Options: Get insight into packaging technologies that influence production speeds and costs.
- Scaling Up Pet Food Production: From Small Batch to Large Scale: A comprehensive guide on how to scale your production facility.
- Packaging Innovations in Pet Food Manufacturing: Learn about the latest advancements in pet food packaging that improve efficiency and shelf life.
- The Economics of Pet Food Production: A detailed analysis of the costs associated with pet food manufacturing and how to reduce them.
- Future Trends in Pet Food Manufacturing: Discover what the future holds for the pet food industry, from sustainability to smart manufacturing.