Dry pet food manufacturing is a highly efficient process that ensures the production of nutritionally balanced, shelf-stable food for pets. Understanding how a dry pet food production line works is essential for pet food manufacturers, suppliers, and even pet owners who want to know more about the food their pets consume. This article provides a comprehensive breakdown of the dry pet food production process.
A dry pet food production line is an automated system used for producing dry pet food, such as kibble, in large quantities. It involves multiple stages, including raw material preparation, mixing, extrusion, drying, coating, cooling, and packaging. The process ensures that the final product is nutritionally balanced, safe, and has a long shelf life.
To fully understand how a dry pet food production line functions, let’s explore its key components and working mechanisms.
What Are the Key Components of a Dry Pet Food Production Line?
The pet food industry is booming, with an increasing demand for high-quality, nutritious, and safe products for pets. Manufacturers must ensure efficiency, hygiene, and consistency in their production lines to meet regulatory standards and customer expectations. However, understanding the core components of a dry pet food production line is crucial for optimizing the production process and ensuring the final product meets the necessary nutritional and safety standards.
A dry pet food production line typically consists of key components such as raw material handling, grinding, mixing, extrusion, drying, cooling, coating, and packaging. Each stage plays a critical role in ensuring the production of high-quality pet food with the right texture, nutritional content, and shelf stability.
To optimize pet food manufacturing, it’s essential to understand the role of each component in the production line. This article provides an in-depth analysis of the essential equipment and technologies used in modern dry pet food production, along with best practices for efficiency and quality assurance.
1. Raw Material Handling and Storage
The first step in the production of dry pet food is handling and storing raw materials, which include grains, proteins, fats, vitamins, and minerals. Proper handling ensures the safety and quality of the final product.
Key Equipment:
- Storage Silos and Bins – Store bulk ingredients such as grains, corn, soy, and meat meal.
- Ingredient Conveyors – Transport raw materials to the processing area.
- Weighing and Batching Systems – Precisely measure ingredients for accurate formulation.
Best Practices:
- Maintain strict hygiene and temperature control to prevent contamination.
- Implement automated systems for precise weighing and batching.
2. Grinding and Milling
Grinding is a crucial step in breaking down raw materials into smaller particles to improve digestibility and facilitate uniform mixing.
Key Equipment:
- Hammer Mills – Crush and grind dry ingredients into a fine powder.
- Roller Mills – Used for more precise size reduction of grains and cereals.
- Sifting Systems – Ensure uniform particle size distribution.
Best Practices:
- Regularly inspect grinding machines to maintain efficiency.
- Use dust collection systems to improve workplace safety.
3. Mixing and Blending
Once ingredients are ground, they must be thoroughly mixed to ensure even distribution of nutrients.
Key Equipment:
- Ribbon Mixers – Provide efficient blending of dry ingredients.
- Paddle Mixers – Ensure uniform mixing of wet and dry ingredients.
- Liquid Sprayers – Add fats, oils, and vitamins.
Best Practices:
- Ensure proper mix time to avoid ingredient segregation.
- Implement quality control checks to verify batch consistency.
4. Extrusion and Cooking
Extrusion is the heart of dry pet food production. This process involves high-temperature and high-pressure cooking to gelatinize starches and sterilize the mixture.
Key Equipment:
- Extrusoras monohusillo – Suitable for basic pet food formulations.
- Extrusoras de doble husillo – Allow more flexibility in ingredient processing.
- Steam Conditioners – Pre-condition ingredients before extrusion.
Best Practices:
- Monitor temperature and moisture levels to prevent undercooked or overcooked products.
- Adjust screw speed and pressure to achieve the desired texture.
5. Drying and Cooling
After extrusion, pet food contains high moisture content and must be dried to ensure a long shelf life.
Key Equipment:
- Multi-Pass Dryers – Remove excess moisture efficiently.
- Conveyor Dryers – Ensure uniform drying by controlling airflow.
- Cooling Conveyors – Reduce product temperature before packaging.
Best Practices:
- Avoid over-drying to prevent nutrient loss.
- Implement real-time moisture monitoring to maintain consistency.
6. Coating and Flavoring
Dry pet food often undergoes a coating process where fats, palatants, and vitamins are added to enhance flavor and nutritional value.
Key Equipment:
- Liquid Coaters – Apply fats and oils uniformly.
- Vacuum Coaters – Improve ingredient absorption into kibbles.
- Drum Blenders – Ensure even coating distribution.
Best Practices:
- Use high-quality fats and palatants to enhance palatability.
- Control coating temperature to prevent ingredient degradation.
7. Packaging and Labeling
Proper packaging preserves product freshness and ensures compliance with regulatory standards.
Key Equipment:
- Form-Fill-Seal Machines – Automatically fill and seal pet food bags.
- Weighing and Filling Systems – Ensure accurate product measurement.
- Labeling Machines – Apply branding and nutritional information.
Best Practices:
- Use moisture-resistant packaging materials.
- Conduct regular weight verification to meet legal requirements.
8. Quality Control and Safety Measures
Quality control is critical in pet food production to ensure safety and compliance with regulations.
Key Equipment:
- Metal Detectors – Detect foreign materials.
- Near-Infrared Spectroscopy (NIR) – Analyze nutritional composition.
- Microbiological Testing Labs – Ensure pathogen-free production.
Best Practices:
- Implement Hazard Analysis and Critical Control Points (HACCP).
- Conduct routine equipment sanitation to prevent contamination.
Comparison of Key Equipment in Dry Pet Food Production
Process Step | Key Equipment | Propósito |
---|---|---|
Raw Material Handling | Silos, Conveyors, Weighing Systems | Storage and transportation |
Grinding | Hammer Mills, Roller Mills | Particle size reduction |
Mezclando | Ribbon Mixers, Paddle Mixers | Even ingredient distribution |
Extrusión | Single-Screw Extruders, Twin-Screw Extruders | Cooking and shaping |
Secado | Multi-Pass Dryers, Conveyor Dryers | Moisture removal |
Revestimiento | Liquid Coaters, Vacuum Coaters | Flavor and nutrition enhancement |
Envasado | Form-Fill-Seal Machines, Weighing Systems | Product preservation |
Efficiency Strategies for Dry Pet Food Production
Estrategia | Beneficio |
---|---|
Automatización | Reduces labor costs and improves consistency |
Real-Time Monitoring | Enhances quality control and minimizes waste |
Energy-Efficient Drying | Reduces production costs |
Precision Batching | Ensures nutritional accuracy |
Conclusión
A well-structured dry pet food production line ensures efficiency, safety, and consistency in delivering high-quality pet food. Each component, from raw material handling to packaging, plays a crucial role in the overall manufacturing process. By integrating advanced technologies, automation, and strict quality control, manufacturers can optimize production, reduce waste, and meet the growing demand for premium pet food.
Are you looking to improve your dry pet food production line? Contact us today for expert solutions and cutting-edge equipment recommendations!
What Raw Materials Are Used in Dry Pet Food Production?
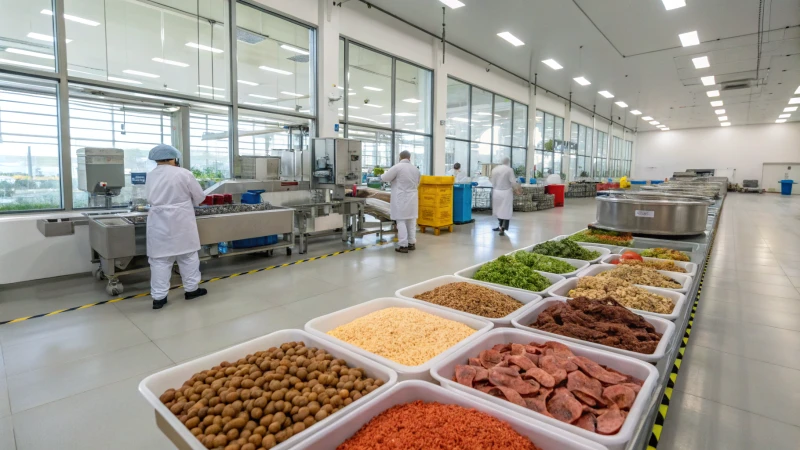
Dry pet food production is a highly specialized process that involves a wide range of ingredients carefully selected to ensure that the final product is nutritious, safe, and palatable for pets. Pet food manufacturers face the challenge of balancing the nutritional needs of animals with the need for efficient production processes and long shelf life. However, many consumers are unaware of the diversity and importance of the raw materials used in dry pet food. A lack of knowledge in this area can lead to misconceptions about what pets are actually eating. This article will walk you through the raw materials involved in dry pet food production, highlighting their roles, sources, and benefits.
In dry pet food production, a variety of raw materials are used to create a balanced diet that meets the nutritional needs of pets. These materials include animal proteins (such as chicken, beef, lamb, and fish), plant-based proteins (such as soy, peas, and corn), grains (such as rice, corn, and wheat), vegetables, fats and oils (such as chicken fat or fish oil), fiber sources (like beet pulp), vitamins, and minerals. Each of these ingredients plays a vital role in providing energy, building muscle, supporting digestion, and promoting overall health in pets.
The complexity of formulating a dry pet food recipe that is nutritionally complete and balanced requires careful sourcing and understanding of each raw material's nutritional profile. Whether you are a pet food manufacturer, a pet owner, or just someone curious about what goes into your pet’s food, understanding the raw materials involved is crucial. Let’s take a closer look at the key ingredients used in dry pet food and their respective roles.
Animal Proteins: The Foundation of Pet Nutrition
Animal-based proteins form the core of most dry pet foods. These proteins provide essential amino acids, which are crucial for building muscle, repairing tissues, and supporting the immune system. The most commonly used animal proteins include chicken, turkey, beef, lamb, pork, and fish. These proteins are often sourced from whole meat, meat meals, or by-products, with the latter being processed to remove excess moisture and fat.
Sources of Animal Protein:
- Chicken and Turkey: These are the most common and affordable sources of animal protein in pet food. They are rich in amino acids and easy for pets to digest.
- Beef and Lamb: Beef is another highly digestible protein that is used in many premium pet foods, while lamb is often used in specialized diets for pets with food sensitivities.
- Fish: Fish protein, especially from salmon or whitefish, is often included in recipes designed for pets with allergies to more common meats like chicken or beef.
Plant-Based Proteins: Supporting Digestive Health
In addition to animal proteins, plant-based proteins are often used to provide additional protein content and essential nutrients. Common plant proteins used in dry pet food include soy, pea protein, and lentils. These ingredients are valuable for boosting the protein content of pet food without increasing the cost or the environmental impact of animal farming.
Sources of Plant-Based Proteins:
- Soy: Soybean meal is a common protein source, though some pets may have sensitivities to soy.
- Peas and Lentils: These ingredients are becoming increasingly popular due to their rich amino acid profile and high fiber content, which supports healthy digestion.
Grains and Starches: Energy and Digestive Support
Grains like rice, corn, wheat, and barley are often used in dry pet food for their carbohydrate content, which provides a slow-releasing source of energy. In recent years, some pet owners have become concerned about grains in pet food, leading to a rise in grain-free diets. However, grains are generally safe and nutritious for most pets and provide essential fiber for healthy digestion.
Sources of Grains and Starches:
- Rice: Easily digestible and a common choice for pets with sensitive stomachs.
- Corn and Wheat: These are often included for their high energy content, but some pets may have sensitivities to gluten or corn.
- Barley: A good source of fiber and nutrients, barley helps maintain digestive health.
Fats and Oils: Essential for Coat and Skin Health
Animal fats, such as chicken fat or fish oil, are added to dry pet food to provide essential fatty acids, including Omega-3 and Omega-6. These fats contribute to the pet’s energy levels and promote healthy skin and a shiny coat.
Sources of Fats and Oils:
- Chicken Fat: High in energy and rich in Omega-6 fatty acids, chicken fat is commonly used in dry pet foods.
- Fish Oil: Rich in Omega-3 fatty acids, fish oil promotes healthy skin, a shiny coat, and joint health.
Fiber Sources: Supporting Digestive Health
Fiber is another essential ingredient in dry pet food. It aids in digestion, helps maintain healthy bowel movements, and can contribute to weight management. Fiber sources in pet food can come from both animal and plant ingredients.
Sources of Fiber:
- Beet Pulp: This by-product of sugar beet processing is a common source of fiber in pet food, helping to support digestion and regulate bowel movements.
- Sweet Potatoes and Pumpkin: These ingredients are not only rich in fiber but also offer vitamins and minerals that support overall health.
Vitaminas y minerales: cómo garantizar el equilibrio nutricional
Vitamins and minerals are crucial to ensuring pets receive a complete and balanced diet. These nutrients support bone health, immune function, and overall well-being. Commonly added vitamins and minerals include calcium, phosphorus, vitamins A, D, and E, and trace elements like zinc and selenium.
Sources of Vitamins and Minerals:
- Calcium and Phosphorus: These minerals are essential for strong bones and teeth.
- Vitamins: Many dry pet foods are fortified with additional vitamins, including vitamin A for vision health and vitamin E for its antioxidant properties.
Additives and Preservatives: Enhancing Shelf Life and Palatability
To extend the shelf life of dry pet food, manufacturers often add preservatives. Natural preservatives like tocopherols (Vitamin E) and ascorbic acid (Vitamin C) are commonly used, though synthetic preservatives like BHA and BHT may also be found in some brands. Additionally, flavor enhancers are sometimes added to make the food more palatable to pets.
Additives and Preservatives:
- Tocopherols and Ascorbic Acid: These natural preservatives help maintain the freshness of the food.
- Flavor Enhancers: Chicken or liver flavorings are often used to make the food more appealing to picky eaters.
Tables: Nutritional Breakdown of Common Raw Materials
Ingrediente | Primary Function | Nutritional Value |
---|---|---|
Chicken Meat | Animal Protein | High in amino acids, easily digestible |
Guisantes | Plant Protein | High in fiber and protein |
Rice | Carbohydrate | Easy to digest, energy source |
Aceite de pescado | Essential Fatty Acids | Rich in Omega-3 for skin/coat health |
Beet Pulp | Fiber Source | Supports digestion |
Key Considerations for Pet Food Manufacturing
Manufacturers need to ensure that these raw materials are sourced ethically and meet stringent quality standards. Pet food ingredients should be free from contaminants and meet the AAFCO (Association of American Feed Control Officials) guidelines for nutritional adequacy. Furthermore, consumer preferences are evolving, with an increasing demand for organic, grain-free, and environmentally sustainable pet food options.
Conclusión
The production of dry pet food is a complex process that relies on the careful selection of high-quality ingredients to meet the nutritional needs of pets. From animal proteins to fiber and essential fats, each ingredient plays an important role in maintaining your pet’s health and well-being. Understanding the raw materials used in pet food production can help you make informed decisions about the products you choose for your furry friends.
Interested in creating the perfect pet food for your brand? Contact us today to learn how we can help you with your dry pet food production needs!
How Does the Mixing and Pre-Conditioning Process Work in Dry Pet Food Production Line?
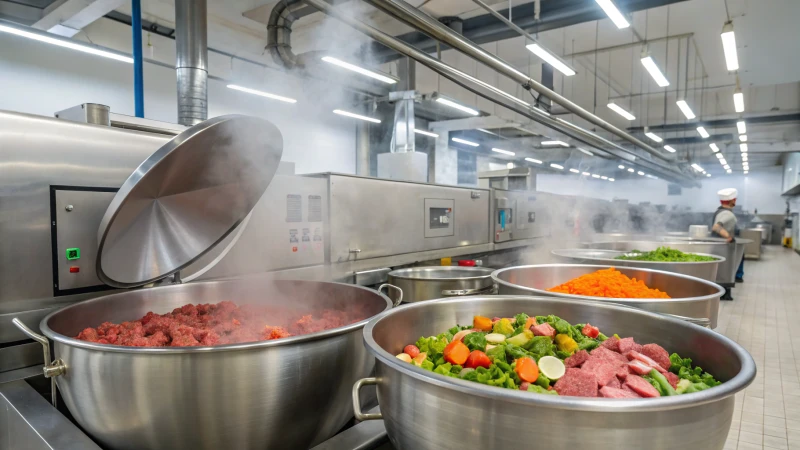
In the production of dry pet food, the mixing and pre-conditioning processes play a vital role in ensuring the consistency, quality, and digestibility of the final product. If these stages are not executed properly, the nutritional balance could be compromised, affecting the health of pets. On top of that, poor mixing can lead to uneven distribution of ingredients, making it hard to achieve the desired texture, flavor, and color. Understanding how the mixing and pre-conditioning process works in the dry pet food production line can help manufacturers improve efficiency and create superior products.
The mixing and pre-conditioning processes are crucial in dry pet food production as they ensure uniform distribution of ingredients, adequate moisture content, and activation of enzymes for proper cooking. These processes involve blending raw ingredients into a homogenous mixture and applying heat and moisture to prepare the ingredients for the extrusion process. This stage, when executed well, sets the foundation for the final dry food product, enhancing its digestibility and nutritional value.
Dry pet food production starts with the preparation of raw ingredients, which are then mixed and pre-conditioned before being extruded into pellets. The mixing stage involves combining dry ingredients such as cereals, proteins, vitamins, and minerals in large industrial mixers. The goal is to achieve a uniform mixture where each ingredient is evenly distributed. The quality of this mixture is vital for the texture and nutritional value of the final product. Inadequate mixing could result in a final product with uneven nutrient distribution, which could negatively affect pets’ health.
After mixing, the pre-conditioning process is essential to achieve the correct moisture and temperature levels. This stage ensures that the ingredients undergo initial cooking, softening, and hydration, which makes them easier to extrude. During pre-conditioning, the ingredients are exposed to steam or heated water in a controlled environment. This helps to activate enzymes in the ingredients, making them more digestible for pets. The process also improves the texture of the dry food, giving it the desired crunch and firmness.
ClaimReview fact check in the text
The mixing process ensures that ingredients are evenly distributed for the final product.Verdadero
Even distribution of ingredients in the mixing process is crucial for consistent texture, flavor, and nutritional content in the final dry pet food.
How the Mixing and Pre-Conditioning Processes Work
1. The Mixing Process:
The mixing stage is where dry ingredients are combined to form a consistent blend. In a dry pet food production line, this is typically done in a horizontal or vertical mixer. The ingredients that go into dry pet food usually include proteins (like chicken meal or beef meal), carbohydrates (like corn or wheat), vitamins, minerals, and fats. Some production lines also incorporate probiotics or flavor enhancers at this stage.
The goal is to ensure that all dry ingredients are thoroughly mixed together, resulting in a homogenous blend. If the mix is uneven, the final product could have inconsistencies in texture, nutritional content, and taste. This inconsistency can result in some pellets being too rich in certain nutrients, while others may lack essential nutrients.
The type of mixer used in this process depends on the specific needs of the production line. A paddle mixer, for example, is ideal for heavy or powdery ingredients, while a ribbon blender can be more effective for ingredients that tend to clump together. The mixer speed, duration, and consistency are carefully controlled to ensure optimal results.
2. Pre-Conditioning:
Once the dry ingredients are mixed, the next step is pre-conditioning. Pre-conditioning is critical as it introduces moisture and heat into the ingredient blend to prepare it for extrusion. The ingredients are transferred to a pre-conditioner, a specialized vessel that applies steam and water to the mixture.
The heat and moisture cause the starches in the grains to swell and soften, while proteins begin to break down, making them more digestible for pets. The pre-conditioning process is also essential for achieving the right texture in the final product. The moisture added during this process helps the ingredients bond together, forming a uniform consistency that will hold up during extrusion.
Steam treatment in the pre-conditioner also helps to kill any harmful bacteria or pathogens that may be present in the raw ingredients, contributing to the safety of the final product.
3. The Role of Temperature and Moisture Control:
Temperature and moisture control are fundamental in both mixing and pre-conditioning. Too much or too little moisture can affect the overall quality of the pet food. During pre-conditioning, the moisture level is carefully monitored to achieve a moisture content between 20% and 30%. This ensures that the ingredients are soft enough to be easily processed by the extruder but not too wet, which can cause issues during extrusion and lead to poor pellet formation.
The temperature in the pre-conditioner is also closely regulated. The ideal temperature is typically between 70°C and 90°C (158°F to 194°F), which helps to gelatinize the starches and activate any enzymes in the raw ingredients, making them more bioavailable for pets.
4. Quality Control:
Quality control plays a vital role in the mixing and pre-conditioning processes. At each stage, quality checks are performed to ensure that the mixture has the desired consistency, moisture, and temperature. This ensures that the final product will have the correct texture, taste, and nutritional content.
Various quality control measures are implemented, such as sampling and testing the mixture for uniformity, checking the moisture content, and performing laboratory tests to ensure the nutritional profile is accurate. This ensures that the final pet food meets both regulatory standards and the pet's dietary needs.
Tables:
Table 1: Typical Ingredients and Their Functions in Dry Pet Food
Ingrediente | Función |
---|---|
Comida de pollo | Fuente de proteínas |
Maíz | Carbohydrate source, energy source |
Aceite de pescado | Fat source, omega-3 fatty acids |
Vitamins & Minerals | Nutritional balance, immune support |
Beet Pulp | Fiber source, digestive health |
Table 2: Key Parameters for Pre-Conditioning Process
Parámetro | Ideal Range |
---|---|
Temperature (°C) | 70°C to 90°C |
Moisture Content (%) | 20% to 30% |
Steam Pressure (bar) | 2 to 3 bar |
Pre-conditioning Time (minutes) | 5 to 10 minutes |
5. Proceso de extrusión:
After the ingredients are mixed and pre-conditioned, they enter the extrusion process. Here, the mixture is forced through a die, creating the characteristic pellet shape. This process also involves high pressure and temperature, which further helps to cook the ingredients and gives the pet food its final texture.
The extrusion process is a crucial step in creating high-quality dry pet food. It improves the digestibility of the ingredients, stabilizes the nutrients, and enhances the food’s shelf life.
Conclusión:
In conclusion, the mixing and pre-conditioning processes in dry pet food production are essential for achieving a high-quality product. Proper mixing ensures that all ingredients are evenly distributed, while pre-conditioning ensures that the ingredients are hydrated and softened, making them easier to process and more digestible. These processes, combined with precise temperature, moisture, and quality control, result in a high-quality pet food that meets nutritional standards and is safe for pets to consume.
If you are looking for a reliable supplier of dry pet food or need assistance optimizing your pet food production line, don't hesitate to contact us today for more information!
What Is the Extrusion Process in Dry Pet Food Manufacturing?
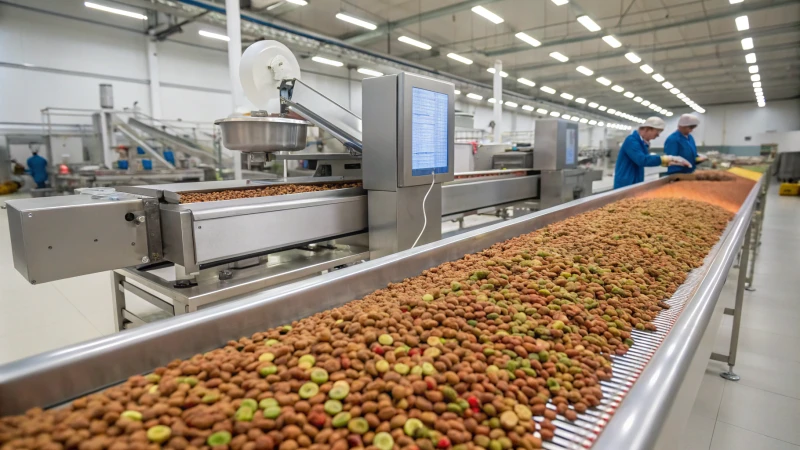
The extrusion process in dry pet food manufacturing is one of the most critical steps in the entire production line. This process involves forcing a mixture of raw ingredients through a machine under high pressure and temperature, transforming them into a uniform, easy-to-digest, and shelf-stable product. If not done correctly, the pet food could suffer from issues such as poor digestibility, inconsistent texture, or even spoilage, which could significantly impact pet health and brand reputation. Understanding the extrusion process is key to achieving high-quality, nutritious, and safe pet food that meets both regulatory standards and pet owners' expectations.
The extrusion process is a high-temperature, high-pressure cooking method that shapes and textures the pet food mixture into desired shapes, such as pellets, kibbles, or biscuits. During extrusion, the ingredients undergo a physical and chemical transformation, which increases their digestibility, enhances nutritional stability, and improves the final product's texture. This process plays an essential role in ensuring that the dry pet food is not only safe for consumption but also palatable and nutritionally balanced for pets.
In the dry pet food manufacturing process, extrusion follows the pre-conditioning stage, where raw ingredients are mixed and prepared for cooking. The combination of heat, moisture, and pressure during extrusion creates a highly structured product. This process also allows for the fortification of the pet food with essential vitamins and minerals, as they are infused into the product at this stage. The extrusion process, therefore, is not only about shaping the product but also about ensuring its nutritional integrity, taste, and long shelf life.
ClaimReview fact check in the text
The extrusion process ensures that pet food has a uniform texture and enhanced digestibility.Verdadero
By applying high pressure, temperature, and moisture, extrusion improves the digestibility of the food and ensures a consistent texture, making it easier for pets to eat and digest.
How Does the Extrusion Process Work in Dry Pet Food Manufacturing?
1. Pre-Extrusion Preparation:
Before the extrusion process begins, the ingredients must go through several stages to prepare them. The ingredients used in dry pet food production include proteins (such as chicken or fish meal), carbohydrates (corn, rice, or wheat), fats, fiber, and essential vitamins and minerals. These ingredients are first mixed and pre-conditioned, as discussed in earlier sections, to ensure they are homogenous and appropriately hydrated.
Once the pre-conditioning is complete, the prepared mixture is transferred to the extruder, where it will undergo the actual extrusion process. The mixture at this stage typically has a moisture content of around 20% to 30%.
2. Extruder Design and Function:
An extruder is a large, industrial machine that uses a rotating screw to force the ingredient mixture through a cylindrical barrel. The key parts of an extruder are:
- Feed Hopper: Where the pre-conditioned ingredients are fed into the extruder.
- Tornillo: The screw moves the ingredients along the barrel, where they are subjected to heat and pressure.
- Barril: The barrel contains the rotating screw and has heating elements that provide the necessary temperature for the extrusion process.
- Muere: The extruder die is the end point where the ingredients exit the extruder in a defined shape, such as pellets, kibbles, or biscuits. The shape of the die determines the shape of the final product.
The screw design is engineered to ensure that the ingredients are thoroughly mixed, compressed, and cooked during their passage through the barrel. The rotational speed of the screw, along with the pressure and temperature in the barrel, ensures the proper cooking of the mixture, breaking down starches, softening proteins, and enhancing the product's digestibility.
3. Heat, Moisture, and Pressure in the Extruder:
During the extrusion process, heat is applied to the ingredients, typically through electric heating elements, which raise the temperature of the mixture to between 90°C and 150°C (194°F to 302°F). This high temperature, combined with the pressure inside the extruder barrel, causes a process known as gelatinization. Gelatinization is when the starches in the ingredients absorb water and swell, creating a gel-like consistency. This is a key step because it increases the digestibility of the food and ensures that nutrients are more readily available for absorption by the pet.
The moisture content is also controlled during extrusion. The mixture is forced through the extruder under high pressure, which causes it to "cook" as it moves through. As the material exits the extruder, it rapidly cools, allowing it to take the shape created by the die.
4. Shaping and Cutting:
Once the cooked mixture exits the extruder, it is shaped into the desired form by the die. The die can produce a wide range of shapes, from round pellets to more intricate designs, depending on the needs of the pet food brand. After the product is shaped, it is cut into uniform pieces by a rotating knife.
At this stage, the pet food is still soft and hot, so it needs to cool down before further processing. The cooling process ensures that the product holds its shape and maintains the desired texture once it is dried.
5. Secado y enfriamiento:
Once the extrudate has been formed and cut, it is passed through a drying system. The drying process reduces the moisture content of the pet food, making it shelf-stable and safe for long-term storage. The drying temperature and time are critical to ensure that the product is not overcooked or too dry, which could negatively affect its taste, texture, and nutritional value.
After drying, the pet food is then cooled to prevent any further cooking or loss of nutritional content. Cooling is essential for maintaining the structure of the product and ensuring it does not become too brittle.
6. Coating and Fortification:
After the drying and cooling process, the pet food may be coated with oils, fats, or flavor enhancers. These coatings not only improve the palatability of the pet food but also add essential nutrients, such as omega fatty acids, that help maintain pet health. Fortification can also include the addition of vitamins and minerals to ensure that the pet food meets specific nutritional standards.
This is a critical stage as it allows manufacturers to tailor the nutritional profile of the pet food, ensuring it meets the dietary needs of different pets.
Tables:
Table 1: Key Parameters for the Extrusion Process in Dry Pet Food Manufacturing
Parámetro | Ideal Range |
---|---|
Temperature (°C) | 90°C to 150°C |
Moisture Content (%) | 20% to 30% |
Pressure (bar) | 20 to 30 bar |
Extrusion Time (minutes) | 1 to 3 minutes |
Table 2: Types of Pet Food Shapes Produced by Extruders
Shape Type | Descripción |
---|---|
Pellets | Small, round or oval-shaped pieces |
Kibbles | Larger, bite-sized pieces |
Galletas | Flat, crunchy shapes |
Extruded Snacks | Various fun, unique shapes |
Benefits of the Extrusion Process
-
Enhanced Digestibility: The combination of heat, pressure, and moisture improves the digestibility of proteins and carbohydrates, making it easier for pets to absorb the nutrients.
-
Improved Texture and Palatability: Extrusion ensures that the pet food has a consistent texture that is appealing to pets, encouraging better consumption.
-
Nutrient Retention: The extrusion process helps to preserve the nutritional value of the ingredients while enhancing their bioavailability. It also allows for the fortification of the food with vitamins and minerals.
-
Long Shelf Life: The high heat and moisture control during extrusion ensure that the pet food is safe for storage and consumption over a long period.
Conclusión:
The extrusion process is at the heart of dry pet food manufacturing, playing a pivotal role in shaping, cooking, and fortifying the product. By applying heat, moisture, and pressure, the ingredients are transformed into a palatable, digestible, and nutrient-rich food that meets the health needs of pets. The process ensures that pet food is not only safe for consumption but also optimized for the best taste, texture, and nutritional content.
If you're looking to improve your pet food production line or need assistance in formulating high-quality dry pet food products, feel free to reach out. We're here to help!
How Is Dry Pet Food Dried and Cooled?
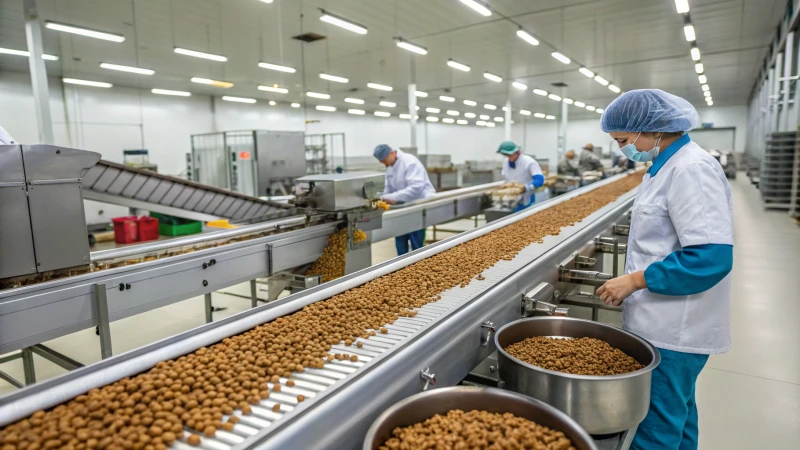
Once pet food has undergone the extrusion process, the next critical stages are drying and cooling. These two steps are vital to ensure the product reaches the desired moisture content, texture, and shelf stability. If not executed properly, there can be serious consequences, including product spoilage, texture degradation, and reduced palatability, which could ultimately affect pet health and the brand's reputation. Understanding how pet food is dried and cooled can help manufacturers optimize the process to create high-quality products.
Dry pet food is dried to reduce moisture content and enhance its shelf life, while cooling ensures that the product holds its shape and prevents further cooking. The process involves passing the food through controlled temperature and airflow systems to achieve the correct balance of moisture, texture, and stability. These stages are crucial in producing a product that not only meets nutritional standards but also remains safe for long-term storage without compromising its quality.
In this article, we will take an in-depth look at the drying and cooling processes, including their role in the overall pet food production line, and how they contribute to creating the perfect dry pet food.
ClaimReview fact check in the text
Drying and cooling are essential for maintaining the shelf life and texture of dry pet food.Verdadero
The drying process reduces the moisture content to prevent spoilage, while cooling stabilizes the product and helps maintain its structure, ensuring it remains safe and enjoyable for pets.
How Does Dry Pet Food Drying and Cooling Work?
1. The Importance of Drying in Pet Food Manufacturing:
Drying is an essential step in the production of dry pet food, and its primary purpose is to reduce the moisture content of the product. This step helps to:
- Prevent Spoilage: High moisture content in pet food can lead to microbial growth, which can cause spoilage. By reducing the moisture to a safe level (typically between 8% and 12%), the risk of bacterial or fungal contamination is minimized.
- Enhance Shelf Life: The reduction of moisture in the pet food increases its shelf life, allowing it to remain safe for long-term storage without the need for refrigeration.
- Improve Texture and Stability: Drying helps set the shape of the pet food, preventing it from becoming soggy or soft once it is packaged.
The drying process typically involves the use of large, industrial drying machines, which utilize either hot air, hot oil, or indirect heat to remove moisture from the extruded pet food. The process is carefully controlled to ensure that the pet food does not become overcooked or lose its nutritional value.
2. The Drying Methods Used in Pet Food Manufacturing:
Several methods can be employed to dry pet food. Each has its advantages and is selected based on the specific requirements of the product.
-
Tunnel Dryers: Tunnel dryers are one of the most common methods for drying dry pet food. In this system, the food travels through a long tunnel where hot air circulates around it. The heat evaporates the moisture from the pellets, and the air flow helps carry away the moisture. The temperature, humidity, and airflow are precisely controlled to ensure the food dries evenly.
-
Fluidized Bed Dryers: Fluidized bed dryers use a combination of air and heat to dry the food. In this method, the pellets are suspended in a bed of air that circulates around them. This results in a more uniform drying process. Fluidized bed dryers are ideal for products with a delicate texture or those that require quick drying.
-
Rotary Dryers: Rotary dryers are large cylindrical machines that rotate the pet food inside while applying heat. The rotation allows for more even drying, and the system can handle larger quantities of product at once.
-
Continuous Drying Systems: Continuous dryers are designed for high-volume production lines. They use conveyor belts to transport pet food through a series of heated zones, where the moisture is removed gradually. This system allows for a consistent and uninterrupted drying process.
The drying time and temperature settings vary depending on the type of pet food being produced and its moisture content. For example, a kibble-based pet food may take longer to dry compared to smaller pellet-shaped products.
3. The Cooling Process:
After the pet food is dried, it must undergo a cooling process to stabilize its temperature and prevent further cooking or texture changes. If the product is not adequately cooled, there is a risk that it may continue to cook, leading to overcooked or burnt food, or it may become too soft.
The cooling process is usually achieved by passing the dried pet food through cooling tunnels o fluidized bed coolers. These systems are designed to rapidly lower the temperature of the pet food while maintaining airflow to prevent the food from sticking together or becoming clumped.
-
Cooling Tunnels: In cooling tunnels, the dried pet food is transported along a conveyor belt through a chamber where cold air is blown over it. The cold air removes the heat from the pellets, bringing the temperature down to an ideal level. The cooling time is critical—too long, and the food may become brittle; too short, and it may remain too hot, affecting packaging and storage.
-
Fluidized Bed Coolers: Fluidized bed coolers work similarly to fluidized bed dryers, but with cold air. The pet food is suspended in the air stream, and the cooler allows the temperature to decrease rapidly, ensuring that the product does not continue cooking or become too warm for packaging.
4. Controlling the Drying and Cooling Process:
Both the drying and cooling processes must be carefully monitored to maintain the product’s quality. To achieve this, manufacturers typically employ sensors to monitor key parameters such as:
-
Temperature: The air temperature during drying must be optimized to prevent over-drying, while cooling must reduce the temperature to room levels without damaging the product.
-
Moisture Content: The moisture content is measured continuously during drying to ensure that the product reaches the desired level of dryness. Pet food should typically have a moisture content of around 8% to 12% after drying.
-
Airflow and Humidity: The airflow rate and humidity level are controlled during both drying and cooling to optimize the process and prevent condensation or moisture buildup.
5. The Role of Drying and Cooling in Final Product Quality:
The drying and cooling stages significantly impact the final product’s texture, appearance, and overall quality. If drying is not done properly, the food can become too hard, too brittle, or not dry enough, leading to a soggy or moist product. Similarly, inadequate cooling can lead to problems with packaging, as the product may generate heat during storage, potentially affecting its shelf life and safety.
By effectively drying and cooling dry pet food, manufacturers ensure that the food remains stable, shelf-stable, and easy to store. Moreover, the careful management of these processes ensures the pet food retains its original flavor, texture, and nutritional content.
Tables:
Table 1: Common Drying Methods in Pet Food Manufacturing
Drying Method | Ventajas | Desventajas |
---|---|---|
Tunnel Dryer | Even drying, large capacity | Longer drying time |
Fluidized Bed Dryer | Quick, uniform drying | Higher equipment cost |
Rotary Dryer | Handles large quantities | Less control over uniformity |
Continuous Dryer | High-volume production | Requires more space |
Table 2: Optimal Drying and Cooling Parameters for Pet Food
Parámetro | Ideal Range |
---|---|
Drying Temperature (°C) | 90°C to 110°C |
Moisture Content (%) | 8% to 12% |
Cooling Temperature (°C) | 25°C to 30°C |
Airflow (m/s) | 2 to 5 m/s |
Conclusión:
The drying and cooling processes are crucial to the production of high-quality dry pet food. By reducing moisture content and stabilizing the product's temperature, these processes ensure that the food remains safe for long-term storage, retains its flavor and texture, and meets nutritional standards. Whether using tunnel dryers, fluidized bed systems, or cooling tunnels, manufacturers must carefully monitor the drying and cooling stages to produce a premium pet food product.
If you are interested in improving your pet food production line or need expert advice on drying and cooling methods, please don’t hesitate to reach out. We're ready to help!
What Are the Coating and Flavoring Techniques Used in Dry Pet Food Production?
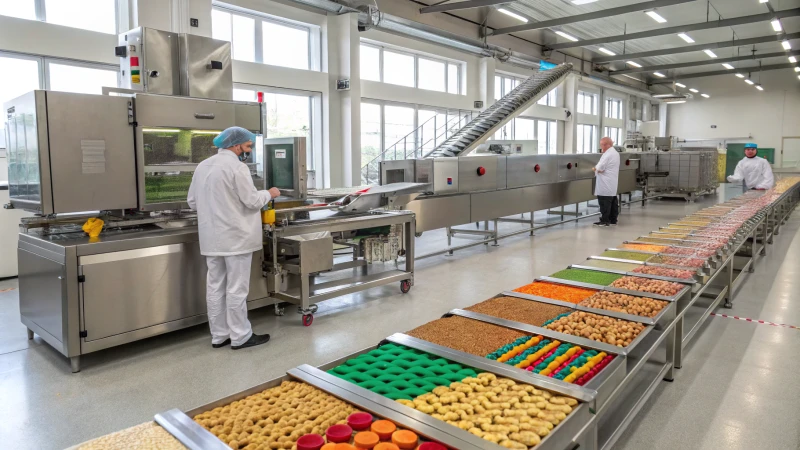
Dry pet food, commonly known as kibble, has become a popular option for pet owners due to its convenience, long shelf life, and nutritional benefits. One of the most important aspects of dry pet food is its appeal to the pet—both in terms of taste and smell. Coating and flavoring techniques play a crucial role in making kibble more palatable to pets while also ensuring the product's stability and nutritional value. However, these processes can be quite complex and require a deep understanding of the ingredients, technologies, and pet preferences.
This article delves into the various coating and flavoring techniques used in dry pet food production, exploring the methods and innovations that make kibble both delicious and nutritious for pets.
Coating and flavoring techniques used in dry pet food production are essential for enhancing taste, aroma, and overall pet palatability. Some of the most commonly used methods include fat and oil coating, spray-drying, and seasoning with natural or artificial flavors. These techniques are designed to not only improve the sensory qualities of kibble but also ensure the preservation of nutrients and extend shelf life.
The process of flavoring and coating pet food goes beyond just making it tasty; it’s about creating a balanced and enjoyable eating experience for pets. Understanding these techniques can help manufacturers create better products that satisfy both the nutritional needs of the animal and the preferences of the owner.
As we explore the different methods, we'll look into how each one works, its benefits, and its role in the overall quality of the pet food product.
Coating Techniques in Dry Pet Food Production
Coating plays a pivotal role in improving the texture, aroma, and palatability of dry pet food. These coatings are typically applied after the kibble has been cooked but before it is packaged. Here are the primary coating techniques used in the industry:
1. Oil and Fat Coating
Oil and fat coatings are among the most common methods used to enhance the flavor and texture of kibble. These coatings are applied in a variety of ways, including spraying oils or fats onto the surface of the kibble. This adds flavor and a crunchy texture that is highly attractive to pets.
- Animal Fats: Often used because of their strong, appealing smell to pets. Common fats include chicken, beef, or pork fat.
- Vegetable Oils: These are plant-based oils that can be used as a coating, often for pets with dietary restrictions.
Benefits:
- Increases the palatability of the kibble.
- Improves the texture and appearance of the product.
- Helps preserve the kibble, preventing it from becoming too dry.
2. Spray-Drying
Spray-drying is another technique that is used to apply coatings. This process involves spraying a mixture of fat, oil, and flavor compounds onto the kibble while it is being dried in a large chamber. This helps create a uniform coating around the kibble that is both flavorful and functional.
Benefits:
- Provides an even distribution of fats and flavors across the kibble.
- Allows for the addition of other nutrients or probiotics, which can be encapsulated during the drying process.
- Extends shelf life by sealing in nutrients and preventing oxidation.
3. Extrusion Coating
In extrusion coating, pet food ingredients are cooked in a high-temperature extruder. The extrusion process itself helps form the kibble’s shape and texture, while the addition of a coating during extrusion can further enhance flavor. The coating is often applied during the final stages of extrusion or after the product has been formed.
Benefits:
- Produces kibble with an appealing texture and increased flavor retention.
- Allows for the addition of functional ingredients, such as vitamins or antioxidants, that are protected during the cooking process.
- Reduces nutrient loss and ensures the stability of the coating.
Flavoring Techniques in Dry Pet Food Production
Flavoring is a critical part of dry pet food production, as it helps make the food more attractive to pets. Here are the primary methods used in flavoring:
1. Natural and Artificial Flavors
Flavoring agents, both natural and artificial, are used to give kibble a specific taste or scent. These flavors are added to the coating or directly into the kibble mixture. They are designed to mimic the taste of meats, poultry, or fish, all of which are highly appealing to pets.
- Natural Flavors: Derived from real meat, vegetables, or fruits, these flavors are considered safer and more natural for pets.
- Artificial Flavors: Synthetic flavor compounds that imitate natural flavors. While they are often more affordable, some consumers may prefer products with natural flavors.
Benefits:
- Enhances the sensory appeal of the kibble, encouraging pets to eat.
- Allows for a broader range of flavors to cater to various pet preferences.
- Ensures consistency in taste across batches of pet food.
2. Meat-Based Broths and Extracts
Meat-based broths or extracts are another common flavoring method. These are often incorporated into the kibble as a liquid or powder, providing a deep, savory taste. The broths may come from chicken, beef, lamb, or fish.
Benefits:
- Adds a strong, authentic taste that mimics real meat, making it more attractive to pets.
- Provides additional nutritional benefits, such as amino acids and minerals, which are naturally found in animal-based proteins.
3. Seasoning and Herbs
Seasonings and herbs, like garlic, rosemary, and turmeric, can be used to flavor dry pet food. These ingredients also offer additional health benefits due to their antioxidant properties.
Benefits:
- Increases flavor variety and adds nutritional value.
- Some herbs and seasonings, like rosemary and turmeric, are known for their anti-inflammatory and antioxidant properties.
- Helps maintain gastrointestinal health.
The Importance of Balancing Coating and Flavoring
In the production of dry pet food, it’s crucial to balance flavor and nutritional content. A coating can enhance the taste, but it should not overpower the nutritional benefits of the kibble. Similarly, flavoring should always complement the core ingredients rather than mask their natural qualities. Striking this balance ensures that pets enjoy their meals while receiving the necessary vitamins, minerals, and proteins to thrive.
Conclusión
Coating and flavoring techniques in dry pet food production are vital in improving the taste, texture, and appeal of kibble. These processes are designed not only to make the food more appetizing but also to preserve its nutritional integrity and extend shelf life. Whether through fat and oil coatings, spray-drying, or the addition of natural and artificial flavors, these techniques play a significant role in creating high-quality pet food that pets love.
Understanding the variety of coating and flavoring methods used can help manufacturers produce better products that are both appealing and nutritious. When done right, these techniques make a significant difference in the quality of pet food and in the overall pet care experience.
ClaimReview
Flavoring agents in pet food can affect both taste and health.Verdadero
Flavors are carefully chosen to ensure pets enjoy the food, and some ingredients like herbs and meat broths can also provide health benefits.
If you’re interested in creating a custom solution for your pet food products, reach out to our experts today for more information.
How Is Dry Pet Food Packaged and Stored?
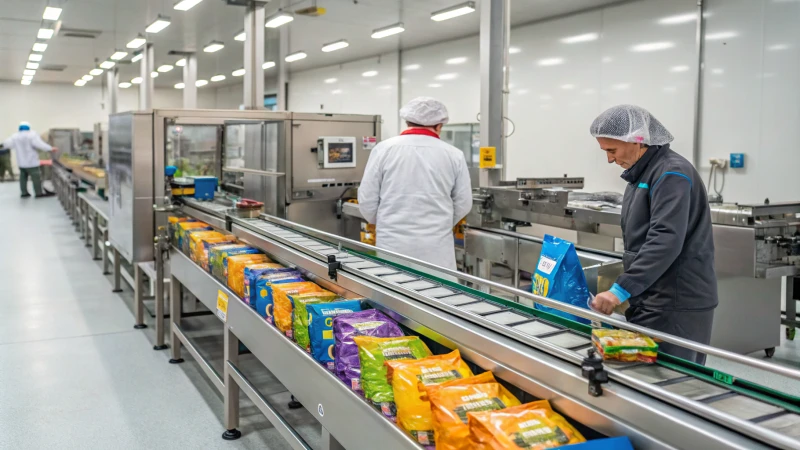
Dry pet food packaging and storage is a crucial process that impacts the product’s quality, freshness, and longevity. If not handled correctly, pet food can degrade, losing essential nutrients and becoming susceptible to contamination. This can lead to a potential health risk for your pet, causing gastrointestinal issues or even poisoning. So, how exactly is dry pet food packaged and stored to prevent such issues? In this article, we will explore the entire process, from production to shelf life, providing you with key insights into maintaining your pet food’s integrity.
Dry pet food is packaged in airtight bags or containers that are designed to maintain the food's freshness, protect it from moisture and air, and extend its shelf life. The packaging process typically involves filling the bags with kibble, sealing them to prevent contaminants, and storing them in cool, dry environments to preserve the nutrients and prevent spoilage.
The storage of dry pet food is as important as the packaging process. If exposed to heat, light, or moisture, the food can deteriorate quickly, affecting the taste and nutritional value. To keep the food fresh, manufacturers store it in temperature-controlled warehouses, away from direct sunlight, and ensure that it is sealed until it reaches the consumer. Moreover, some brands opt for resealable bags, which allow pet owners to keep the food fresh for a longer period once opened.
In this article, we will dive into the steps involved in dry pet food packaging, explore how storage plays a role in preserving quality, and discuss the best practices for pet owners to follow when handling and storing dry food at home.
The Packaging Process of Dry Pet Food
Dry pet food is typically manufactured in large batches using a variety of raw ingredients such as meat, grains, and vegetables. After mixing and cooking, the food is shaped into kibbles, which are then carefully packed. The packaging process involves several key steps to ensure that the food stays fresh and uncontaminated throughout its journey from the factory to your pet’s bowl.
-
Filling: The kibble is fed into automated packaging machines, which fill bags with the correct amount of food. The bags can vary in size, depending on the product and brand.
-
Sealing: After filling, the bags are sealed tightly to prevent air, moisture, and contaminants from entering. Heat-sealing machines are typically used to ensure a strong, airtight seal.
-
Oxygen Absorbers or Nitrogen Flushing: Some manufacturers may use oxygen absorbers or nitrogen flushing during the sealing process to reduce oxygen levels in the bag. This helps to slow down oxidation, which can spoil the food and reduce its shelf life.
-
Labeling and Expiry Dates: Labels are applied to each package, indicating product details like the ingredients, nutritional information, and expiry dates. This ensures transparency and lets consumers know when to use the product by.
Storage Conditions for Dry Pet Food
The way dry pet food is stored after packaging plays a significant role in determining how long it stays fresh and nutritious. Improper storage can cause the food to go stale, lose nutrients, or even become infested with pests.
-
Temperature Control: Dry pet food should be stored in a cool environment, ideally between 50°F and 70°F (10°C to 21°C). Storing it in a location that’s too hot or cold can lead to issues like fat oxidation, which affects the flavor and quality of the food. Exposure to high heat can also cause nutrient loss and spoilage, while freezing can change the texture of the food.
-
Humidity Control: Humidity is another important factor. Dry food should be kept in a low-humidity environment to avoid mold growth and bacterial contamination. In humid conditions, even well-sealed packages can become susceptible to water vapor, which can deteriorate the food over time.
-
Protection from Light: UV rays and direct sunlight can cause vitamins and nutrients in the food to degrade. As such, dry pet food should be stored away from light sources. Some manufacturers use opaque or foil-lined bags to block out light and preserve the food’s nutritional content.
-
Warehouse Storage: Large batches of dry pet food are usually stored in temperature-controlled warehouses before being shipped out to retailers. These warehouses are designed to meet specific guidelines that keep the food safe until it’s ready to be sold. For consumer-level storage, it’s important to avoid storing pet food in areas that are subject to fluctuations in temperature or high humidity, such as near windows, heating units, or kitchens.
How to Store Dry Pet Food at Home
Once you bring dry pet food home, you need to ensure that it remains fresh and safe for your pet to consume. Here are some key tips to properly store dry pet food:
-
Use Airtight Containers: After opening the original bag, it’s best to transfer the food into a high-quality airtight container. This will help maintain freshness and prevent the food from being exposed to air, moisture, or pests.
-
Reseal the Bag: If you prefer to keep the food in its original bag, make sure the bag is resealed tightly after each use. You can use clips or vacuum-sealed bags to create a better seal.
-
Avoid Storing in the Kitchen: Store the pet food in a cool, dry place away from any sources of heat or moisture. Avoid keeping it in the kitchen, especially near ovens or refrigerators, where temperature fluctuations can affect the food.
-
Do Not Store Near Chemicals: Keep dry pet food away from household cleaners, chemicals, or strong-smelling substances, as these can alter the food’s flavor and freshness.
Shelf Life of Dry Pet Food
The shelf life of dry pet food varies depending on the brand, the ingredients used, and how the food is packaged. Most dry pet foods have a shelf life of 12 to 18 months from the manufacturing date. To ensure that the food stays within its best-before period, always check the expiry date printed on the packaging.
Once opened, the shelf life can be affected by the storage conditions. Generally, dry food can last for up to six weeks after opening, provided it is stored correctly in an airtight container. Beyond this period, the food may begin to lose its flavor, and its nutritional value can deteriorate.
Conclusión
Proper packaging and storage of dry pet food are essential to maintain its quality, safety, and nutritional content. Whether you are a manufacturer or a pet owner, understanding the packaging process and storage conditions can help ensure that your pet’s food remains fresh and healthy for as long as possible. Always store pet food in a cool, dry, and dark place, and use airtight containers to preserve its quality once opened.
Need Assistance?
For more tips on pet food packaging, storage, and keeping your furry friend’s meals fresh, don’t hesitate to contact us! We provide expert advice and quality solutions to ensure your pet’s well-being.
What Quality Control Measures Ensure Safe and Nutritious Dry Pet Food?
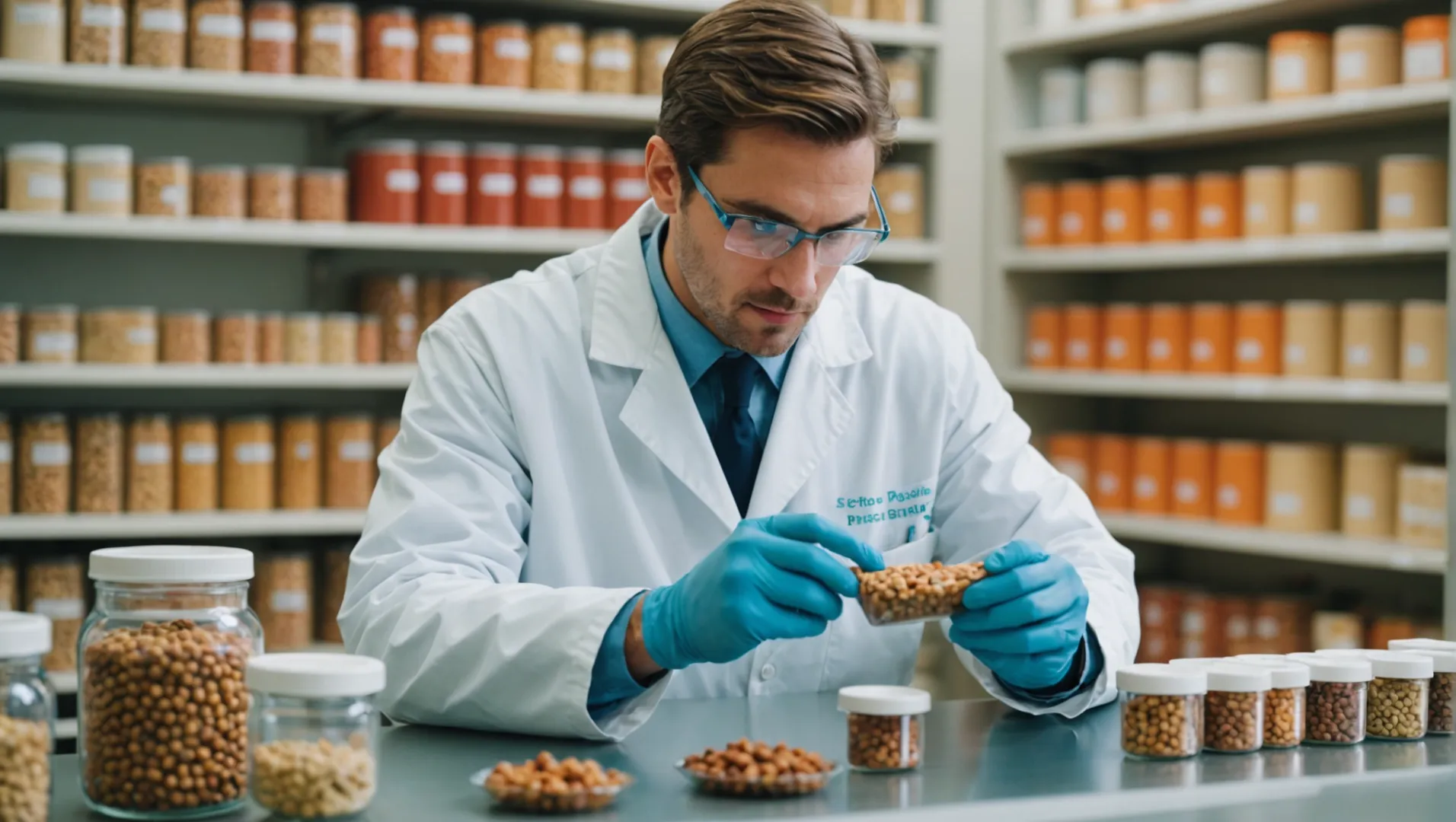
The pet food industry has come under increasing scrutiny over the years as pet owners become more concerned with the safety, quality, and nutritional value of the food they are providing for their pets. Dry pet food, one of the most popular forms of pet nutrition, must adhere to strict quality control standards to ensure both the safety and the health benefits of the product. Without these measures, pets could be exposed to risks such as contamination, imbalanced diets, and even harmful chemicals. In this article, we will explore the essential quality control measures that help ensure dry pet food is both safe and nutritious for your pet.
Ensuring safe and nutritious dry pet food requires a multi-layered approach involving stringent quality control measures across the entire production process. These measures include careful sourcing of ingredients, regular testing for contaminants, adherence to strict manufacturing practices, and comprehensive quality assurance checks at every stage of production. In addition, effective monitoring systems are essential to guarantee that nutritional profiles meet regulatory standards and that food safety standards are continuously met, minimizing any potential health risks for pets.
As pet food production is complex and involves numerous steps, from ingredient procurement to packaging, understanding the entire process and how these checks are integrated can reassure pet owners that their furry friends are getting the highest quality food possible. Let’s take a closer look at the various stages of quality control that contribute to the safety and nutritional value of dry pet food.
Key Stages in Quality Control for Dry Pet Food
Quality control begins long before the pet food reaches your local pet store. Here are some of the major stages where quality control measures are implemented:
Ingredient Sourcing and Testing
The first stage in the production of high-quality dry pet food begins with sourcing ingredients. Pet food manufacturers work with trusted suppliers who provide raw materials such as meat, grains, vegetables, vitamins, and minerals. Each ingredient is tested for safety and nutritional content before it is approved for use in production.
Key quality control actions in this stage include:
- Supplier Audits: Manufacturers regularly audit suppliers to ensure their operations meet safety and quality standards.
- Ingredient Testing: Raw materials are often tested for contaminants, including pathogens, pesticides, heavy metals, and mycotoxins (fungal toxins).
- Nutritional Analysis: Ingredients are tested to ensure they meet the nutritional profiles outlined by regulatory bodies like the Association of American Feed Control Officials (AAFCO).
Manufacturing Process Control
Once ingredients are approved, the production process begins. This stage involves multiple steps such as grinding, mixing, cooking, and drying the ingredients. The following quality control measures ensure that the final product is safe and nutritious:
- Hazard Analysis Critical Control Point (HACCP): HACCP is a systematic preventive approach to food safety that identifies potential hazards in the production process. In dry pet food manufacturing, this system identifies critical points where contamination can occur, such as during mixing or cooking, and provides solutions to control those risks.
- Batch Monitoring: Each batch of pet food is carefully monitored for consistency. This includes tracking temperatures, mixing times, and other variables to ensure uniformity in the final product.
- Ingredient Proportions: Correct proportions of ingredients are crucial for the balanced nutrition of pets. Regular sampling and testing ensure that ingredient ratios are followed accurately.
Quality Testing During Production
Throughout the production process, quality testing is conducted to detect issues early. Some of the tests performed include:
- Microbial Testing: To ensure that harmful bacteria such as Salmonella, E. coli, and Listeria are not present in the food.
- Moisture and Texture Testing: Dry pet food must have a specific moisture content to ensure it is safe for long-term storage and palatable for pets. Testing the texture and dryness of kibble helps maintain the consistency and longevity of the product.
- Nutritional Testing: Samples from every batch are tested for protein, fat, fiber, vitamins, and minerals to confirm that the nutritional levels meet regulatory standards and manufacturer claims.
Post-Manufacturing Quality Assurance
After the food is manufactured, it enters the packaging phase, where additional quality assurance checks take place:
- Packaging Integrity: The packaging must maintain the freshness of the pet food and protect it from contamination. Manufacturers test the integrity of packaging materials, ensuring they are secure and do not leak or tear easily.
- Expiration Dates and Storage Conditions: Food is stored under optimal conditions to maintain quality. Expiration dates are carefully marked to ensure pets are consuming fresh food.
- Final Nutritional Verification: Before the food is released to the market, it undergoes final nutritional verification to ensure it meets the specific dietary requirements for pets, including correct energy levels, protein content, and micronutrient balances.
Regulatory Oversight and Compliance
In addition to the in-house quality control measures, dry pet food manufacturers must comply with various regulations to ensure product safety. These include:
- AAFCO Guidelines: In the United States, the AAFCO sets the nutritional standards for pet food. Manufacturers must follow these standards to ensure the food is safe and provides balanced nutrition.
- FDA Regulations: The U.S. Food and Drug Administration (FDA) regulates the safety of pet food, including the approval of ingredients and the monitoring of manufacturing processes to prevent contamination and adulteration.
- Global Standards: For international companies, compliance with global food safety standards, such as the Codex Alimentarius, ensures that their products are safe for pets worldwide.
Quality Control Tools and Technologies
Modern quality control methods rely heavily on technology to ensure the consistency and safety of pet food. Some of the tools used in dry pet food production include:
- Automation and Sensors: Automated systems with sensors help to measure key variables such as temperature, moisture content, and ingredient quantities in real time.
- Barcoding and Traceability: Each ingredient and batch is tracked using barcodes, making it easy to trace the product’s history and identify potential problems quickly.
- Robotic Inspection: Robots equipped with cameras and sensors are used to inspect packaging for defects and ensure uniformity.
Quality Control Metrics for Dry Pet Food
To assess the quality of dry pet food and its nutritional value, manufacturers track several key performance indicators (KPIs):
- Moisture Content: Ideally, dry pet food should contain less than 10% moisture to avoid spoilage and ensure a long shelf life.
- Crude Protein: Protein levels are checked to ensure that the food provides sufficient amino acids for pet health.
- Fat and Fiber Levels: These metrics are crucial for a pet’s energy and digestive health.
Sample Table of Quality Control Metrics in Dry Pet Food Production
Métrico | Target Value | Acceptable Range | Testing Frequency |
---|---|---|---|
Contenido de humedad | < 10% | 8-10% | Each batch |
Crude Protein | 20-30% | 18-35% | Random sampling |
Crude Fat | 8-20% | 5-25% | Every production run |
Crude Fiber | 2-5% | 1-6% | Every batch |
Ash Content | 5-8% | 4-9% | Weekly |
Conclusión
Quality control in dry pet food production is not just a regulatory requirement, but a fundamental process that ensures the safety, nutrition, and overall well-being of pets. From ingredient sourcing to final packaging, each step is carefully monitored to provide pet owners with high-quality, nutritious food that supports their pets’ health. The integration of advanced technologies and adherence to rigorous standards ensures that dry pet food manufacturers can consistently deliver safe and balanced products.
If you're concerned about the quality of your pet's food, make sure to choose brands that prioritize stringent quality control measures and comply with regulatory standards to guarantee the best nutrition for your furry companion.
Interested in learning more about pet food safety? Contact us today to discover how we can help you provide your pets with the best food, every time.
How Can Manufacturers Optimize Their Dry Pet Food Production Line?
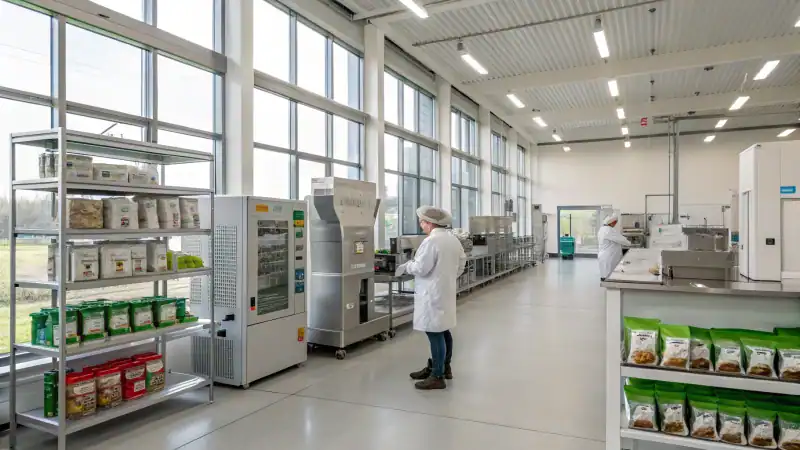
In today's competitive pet food industry, manufacturers must ensure that their production processes are efficient, cost-effective, and adaptable to market changes. A dry pet food production line is a complex system requiring high levels of automation, precision, and flexibility. Poorly optimized production lines can lead to inefficiencies, delays, and product quality issues that ultimately affect profits and customer satisfaction. However, with the right strategies and technological advancements, manufacturers can optimize their dry pet food production line to achieve better outcomes. This article explores how manufacturers can streamline their operations to improve efficiency, reduce waste, and enhance product consistency.
Manufacturers can optimize their dry pet food production line by focusing on automation, ingredient handling, quality control, energy efficiency, and production scheduling. Key steps include upgrading machinery, integrating advanced data analytics, ensuring precise mixing and extrusion processes, and continuously monitoring quality.
To stay ahead in the industry, manufacturers must regularly assess their production processes to identify bottlenecks, inefficiencies, and potential areas for improvement. The aim is to increase throughput, improve product quality, and lower operational costs. By making small but impactful changes, manufacturers can significantly boost their overall productivity.
Understanding the Key Challenges in Dry Pet Food Production
Dry pet food manufacturing involves several stages, including ingredient mixing, extrusion, drying, and packaging. At each of these stages, inefficiencies can arise, causing production delays, product inconsistencies, and excess costs. For instance, an inefficient extrusion process may lead to poor texture and taste, affecting the final product quality. Additionally, inadequate energy management can result in high operational costs, particularly in energy-intensive stages like drying and cooking. These issues not only impact the profitability of the business but can also harm the brand’s reputation if consumers experience issues with the food's quality.
Key pain points in dry pet food production include:
- Inconsistent quality: Variations in texture, flavor, and nutrient distribution can occur due to improper mixing or extrusion techniques.
- High energy consumption: Energy-intensive processes like drying and cooking can inflate costs if not properly managed.
- Slow production speeds: Bottlenecks in machinery, inefficient batch sizes, or delays in the supply chain can reduce throughput.
- Waste generation: Excessive raw material wastage or product rejects increase costs and environmental impact.
By identifying these challenges early on, manufacturers can implement strategies to optimize their production lines.
How to Optimize Your Dry Pet Food Production Line?
Now that we’ve identified the challenges, let’s dive into some key optimization strategies.
1. Invest in Advanced Machinery and Automation
To improve the speed, consistency, and efficiency of the production line, manufacturers should focus on automation and machinery upgrades. Key technologies such as automated ingredient feeders, mixing systems, and high-efficiency extruders can help streamline production. Automated systems can handle precise ingredient measurements, ensuring that the final product meets exact nutritional standards.
For instance, high-precision extrusion machines help manufacturers control the cooking and shaping process more efficiently, leading to better consistency in texture and nutrient retention. Additionally, integrating robotics in packaging and material handling can reduce labor costs and improve output speed.
2. Improve Ingredient Handling and Storage Systems
Raw material handling is a critical aspect of dry pet food production. Manufacturers can optimize ingredient handling by implementing automated systems for sorting, storing, and transporting materials. For example, smart silos equipped with sensors can monitor ingredient levels and prevent overstocking or shortages. Moreover, ingredient pre-mixing systems can speed up the batching process and reduce the chances of human error.
3. Integrate Data Analytics for Real-Time Monitoring
Using data analytics, manufacturers can track key performance indicators (KPIs) in real time. This allows for continuous monitoring of the production process, helping to detect inefficiencies or faults early on. For example, tracking extrusion temperature and pressure in real time can help identify deviations from optimal conditions and adjust settings on the fly to ensure consistent product quality.
Implementing a centralized data management system also enables manufacturers to analyze production data for insights on improving operational efficiency. By using data-driven decisions, manufacturers can enhance their production scheduling, reduce downtime, and optimize inventory levels.
4. Enhance Quality Control Systems
Quality control is paramount in dry pet food manufacturing. Small deviations from quality standards can significantly affect the final product's taste, texture, and nutritional value. Manufacturers should adopt automated quality control systems that can detect inconsistencies in real-time, such as changes in color, texture, and size. Optical sensors and near-infrared spectroscopy (NIR) technology can help monitor raw materials and finished products, ensuring they meet specified quality standards.
By integrating real-time quality control systems into the production line, manufacturers can significantly reduce the likelihood of producing subpar products and improve customer satisfaction.
5. Focus on Energy Efficiency
Energy consumption is one of the highest operational costs in dry pet food production. The drying and cooking stages are particularly energy-intensive, so it's crucial to focus on improving energy efficiency. Manufacturers can install energy-efficient dryers that use less power while maintaining optimal moisture levels. Moreover, sistemas de recuperación de calor can be implemented to capture excess heat and repurpose it in other parts of the production process, reducing overall energy demand.
Additionally, manufacturers can explore renewable energy sources, such as solar panels o wind turbines, to further reduce energy costs and minimize environmental impact.
6. Optimize Production Scheduling and Batch Sizes
Efficient production scheduling is key to reducing idle time and ensuring that production runs smoothly. By using demand forecasting tools, manufacturers can better predict production needs and align the production schedule with market demand. Additionally, optimizing batch sizes to match demand can help prevent both overproduction and stockouts.
Employing just-in-time (JIT) production can also reduce the need for large inventories, minimizing storage costs and reducing the chances of excess product wastage.
7. Reduce Waste with Lean Manufacturing
Incorporating lean manufacturing principles into the production process can significantly reduce waste. Lean practices focus on eliminating non-value-added activities, such as excessive transportation, inventory, and defects, while improving process flow. Techniques like Six Sigma y Kaizen can be used to identify areas of waste and implement continuous improvement strategies.
By reducing waste, manufacturers not only improve their bottom line but also contribute to environmental sustainability.
Data-Driven Insights for Optimizing the Production Line
A crucial part of optimization is the ability to analyze key performance metrics to identify patterns and inefficiencies. Below is a table illustrating common production metrics, their significance, and potential improvements.
Métrico | Importancia | Potential Improvements |
---|---|---|
Throughput Rate | Measures the amount of product produced per unit of time | Increase line speed with automated systems |
Consumo de energía | Tracks energy usage per unit of production | Implement energy-efficient machinery, heat recovery |
Material Waste | Percentage of raw materials wasted during production | Streamline ingredient handling and mixing systems |
Quality Control Pass Rate | Measures the percentage of products passing QC tests | Upgrade automated QC systems, improve extrusion control |
Production Downtime | Time lost due to machine failures or setup changes | Implement predictive maintenance and real-time monitoring |
Conclusion: The Future of Dry Pet Food Production
In conclusion, optimizing a dry pet food production line requires a combination of automation, data analytics, energy efficiency, and continuous quality monitoring. By upgrading machinery, improving ingredient handling, and embracing real-time analytics, manufacturers can drastically improve both production speed and product quality. This holistic approach not only boosts productivity but also helps reduce costs, enhance customer satisfaction, and foster long-term business growth.
ClaimReview fact check in the text.
Energy-efficient dryers can reduce overall energy costs in pet food production.Verdadero
Energy-efficient dryers utilize less power while maintaining optimal drying conditions, leading to reduced operational costs.
Manufacturers looking to take the next step should start by evaluating their current processes, identifying key inefficiencies, and investing in the latest technology to stay competitive in an ever-evolving market.
If you are looking to optimize your dry pet food production line, don’t hesitate to reach out. Our team of experts can guide you through the latest technologies and strategies to streamline your production process and improve product quality. Contact us today to learn more about our tailored solutions.
Conclusión
A well-designed dry pet food production line ensures consistency, efficiency, and high-quality output. By understanding the working principles behind each stage, manufacturers can improve their production processes while ensuring pet owners receive safe and nutritious products for their pets.
Póngase en contacto con nosotros
Interested in setting up or optimizing a dry pet food production line? Contact us for expert guidance and advanced manufacturing solutions!