La piscicultura es una industria en auge, pero uno de los mayores desafíos que enfrentan los piscicultores es garantizar un suministro constante de alimento de alta calidad. Sin el equipo adecuado, la producción de alimento para peces puede ser ineficiente, costosa e irregular, lo que provoca un crecimiento deficiente de los peces y un aumento de los gastos operativos. ¿La solución? Invertir en la máquina de alimento para peces adecuada para mejorar la eficiencia y la productividad.
Existen varios tipos de máquinas para la producción de alimento para peces, como extrusoras secas, extrusoras húmedas, máquinas de alimentación flotante, máquinas de alimentación sumergible y peletizadoras. Cada tipo tiene características, ventajas y aplicaciones específicas según la especie de pez, la escala de producción y la formulación del alimento. La selección de la máquina adecuada depende de factores como el tipo de pez, la consistencia del alimento y el presupuesto.
Comprender las diferencias entre estas máquinas de alimentación de peces es crucial para realizar una inversión informada. Exploremos los distintos tipos y sus funciones únicas en detalle.
¿Qué es una máquina de alimentación de peces y cómo funciona?
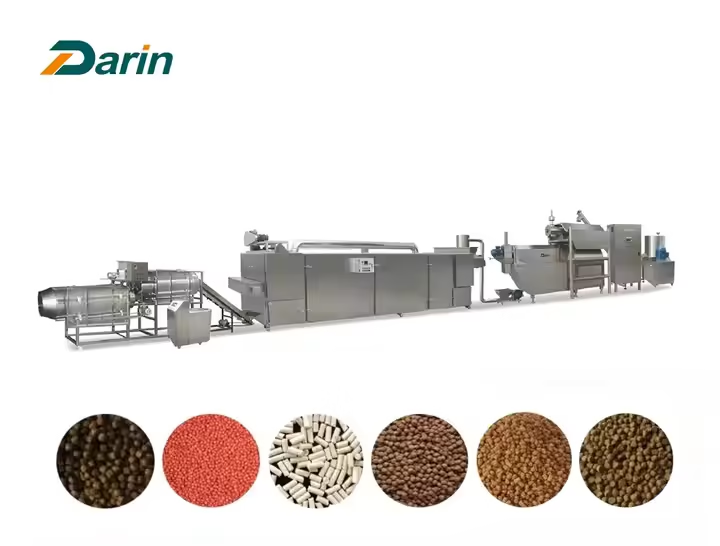
El rápido crecimiento de la industria acuícola ha incrementado la demanda de alimentos de alta calidad para peces. Los métodos tradicionales de preparación de alimentos suelen ser ineficientes y resultan en una nutrición inconsistente. máquina de alimentación de peces resuelve este problema automatizando la producción de alimento, garantizando una calidad óptima del pellet, un equilibrio nutricional y un desperdicio mínimo.
¿Qué es una máquina de alimentación de peces?
Una máquina de alimento para peces es un equipo especializado diseñado para procesar materias primas y convertirlas en pellets nutricionalmente equilibrados para peces y otros animales acuáticos. Utiliza procesos mecánicos, térmicos y de extrusión para crear pellets de alta calidad y digestibilidad en diversos tamaños y densidades. El objetivo principal de estas máquinas es mejorar el crecimiento de los peces, optimizar la eficiencia alimentaria y reducir los costos de producción en la piscicultura.
Las máquinas de alimento para peces se utilizan tanto en acuicultura a pequeña escala como comercial. Ayudan a producir pellets flotantes, que se hunden o se hunden lentamente, adecuados para diferentes especies de peces y hábitos alimenticios.
El propósito de una máquina de alimentación de peces
Los objetivos clave de utilizar una máquina de alimentación de peces incluyen:
- Mejorar la eficiencia alimentaria:La producción de pellets uniformes y nutricionalmente equilibrados mejora el crecimiento de los peces y minimiza el desperdicio.
- Reducción de costesLa fabricación interna de alimentos para peces reduce la dependencia de alimentos comerciales costosos.
- Formulación de alimento personalizable:Permite a los agricultores ajustar la composición de los ingredientes para especies de peces específicas.
- Mejor gestión de la calidad del aguaLos pellets de alta calidad reducen la contaminación del agua al minimizar la desintegración del alimento.
- Escalabilidad para granjas comercialesLas máquinas industriales pueden producir grandes cantidades de alimento para soportar altas densidades de población.
Descripción general del proceso de producción de alimentos para peces
Una máquina de alimento para peces sigue un proceso estructurado para convertir las materias primas en pellets de alta calidad. El proceso consta de varios pasos clave:
1. Selección y molienda de materia prima
El primer paso es seleccionar los ingredientes adecuados para satisfacer las necesidades nutricionales de la especie de pez objetivo. Los ingredientes comunes incluyen:
- Fuentes de proteínas: Harina de pescado, harina de soja, harina de carne, harina de camarón
- Carbohidratos:Maíz, trigo, salvado de arroz
- Grasas y aceites:Aceite de pescado, aceites vegetales
- Vitaminas y minerales:Premezclas para garantizar una nutrición equilibrada
Estas materias primas se muelen hasta obtener partículas finas mediante un molino de martillos o un pulverizador. La molienda fina mejora la digestibilidad y la aglutinación del alimento.
2. Mezcla y acondicionamiento
Los ingredientes molidos se mezclan en un mezclador de pienso para lograr una composición uniforme. Esto garantiza una nutrición uniforme en cada pellet.
- Mezcla en seco:Los ingredientes se mezclan en forma seca para distribuir los nutrientes de manera uniforme.
- Acondicionamiento húmedoSe agrega vapor o agua para mejorar la cohesión de los pellets, la gelatinización del almidón y la absorción de nutrientes.
3. Extrusión y formación de pellets
La extrusión es el proceso principal mediante el cual el material de alimentación se transforma en pellets. La extrusora consta de:
- Un sistema de tornillo y cañón que comprime y empuja la mezcla de alimento hacia adelante.
- Una zona de alta temperatura donde el calor y la presión alteran las propiedades físicas y químicas de los ingredientes.
- Una placa de matriz que determina el tamaño y la forma del pellet.
Dependiendo de la configuración de la máquina, el alimento se puede producir como:
Tipo de alimentación | Lo mejor para | Proceso de producción |
---|---|---|
Pellets flotantes | Tilapia, bagre, peces ornamentales | Extrusión de alta presión con expansión por humedad |
Pellets que se hunden | Camarón, pez que se alimenta en el fondo | Extrusión de menor presión con menor expansión |
Pellets de hundimiento lento | especies híbridas | Expansión media durante la extrusión |
4. Secado y enfriamiento
Los pellets recién extruidos contienen exceso de humedad y deben secarse para evitar la formación de moho. Un sistema de secado elimina el contenido de agua y preserva la integridad del pellet.
Una vez secos, los pellets se enfrían a temperatura ambiente para mejorar la durabilidad y la vida útil de almacenamiento.
5. Recubrimiento y embalaje
Para mejorar la calidad nutricional, los pellets pueden recubrirse con:
- Aceites y grasas para un mayor contenido energético.
- Vitaminas y minerales Para aumentar la inmunidad y la salud de los peces.
- Potenciadores del sabor para mejorar la palatabilidad.
Finalmente, el alimento terminado se envasa en bolsas y se almacena en un lugar seco para su distribución y alimentación.
Características principales de una máquina de alimentación de peces
Característica | Función |
---|---|
Sistema de extrusión | Garantiza una alta digestibilidad y estabilidad del pellet. |
Tamaños de matriz variables | Produce pellets de diferentes diámetros para distintas especies de peces. |
Control automatizado de temperatura | Previene la pérdida de nutrientes durante el procesamiento. |
Diseño energéticamente eficiente | Optimiza el uso de energía para una producción rentable |
Niveles de humedad y presión ajustables | Permite la personalización de la alimentación flotante y hundida. |
Tipos de máquinas de alimentación de peces
Las máquinas de alimentación de peces se clasifican en tipo seco y tipo húmedo extrusoras:
1. Máquina de alimentación de peces de tipo seco
- Utiliza el calor por fricción generado por el sistema de tornillo.
- No requiere caldera de vapor externa.
- Más asequible e ideal para explotaciones agrícolas de pequeña y mediana escala.
2. Máquina de alimentación húmeda para peces
- Requiere una caldera de vapor para inyectar humedad y calor en la mezcla de alimento.
- Produce pellets consistentes y de alta calidad con mejor digestibilidad.
- Adecuado para la producción de alimentos comerciales a gran escala.
Beneficios de usar una máquina de alimentación de peces
1. Rentabilidad
La producción de piensos in situ permite ahorrar hasta 30% comparado con la compra de piensos comerciales.
2. Mejor desempeño del crecimiento
Las fórmulas personalizables garantizan una nutrición óptima, lo que da como resultado Tasas de crecimiento más rápidas y mejor salud de los peces.
3. Reducción del desperdicio de alimento
Los pellets mantienen su forma en el agua, evitando la pérdida de nutrientes y reduciendo la contaminación ambiental.
4. Mayor capacidad de producción
Las máquinas modernas de alimentación de peces pueden producir cientos a miles de kilogramos de alimento por hora, lo que los hace ideales para operaciones de acuicultura a gran escala.
Alimento flotante o alimento que se hunde para peces: ¿cuál es mejor?
Aspecto | Alimentación flotante | Alimentación que se hunde |
---|---|---|
Lo mejor para | Alimentadores de superficie (tilapia, bagre) | Alimentadores de fondo (camarones, carpas) |
Monitoreo de feeds | Comportamiento de alimentación fácil de observar | Es más difícil controlar la ingesta |
Estabilidad del agua | Flota durante largos periodos | Se hunde inmediatamente |
Coste de producción | Mayor debido al proceso de extrusión | Menor costo |
El alimento flotante es siempre la mejor opción para la piscicultura.Falso
El alimento flotante es ideal para los peces que se alimentan en la superficie, pero los peces que se alimentan en el fondo requieren pellets que se hunden.
Cómo elegir la máquina de alimentación de peces adecuada para su granja
Al seleccionar una máquina de alimentación de peces, tenga en cuenta lo siguiente:
1. Escala de producción
- Pequeñas granjas: Extrusoras de tipo seco (10-200 kg/h)
- Granjas comerciales: Extrusoras de tipo húmedo (300-5000 kg/h)
2. Requisitos del tipo de alimentación
- Pellets flotantes: Extrusión de alta presión
- Pellets que se hunden: Extrusión de baja presión
3. Consumo de energía
- Los modelos energéticamente eficientes reducen los costos operativos.
4. Presupuesto y necesidades de automatización
- Las máquinas totalmente automatizadas minimizan la mano de obra pero tienen costos iniciales más elevados.
Conclusión
A máquina de alimentación de peces Es una inversión crucial para la piscicultura moderna, ya que permite una producción de alimentos eficiente, rentable y de alta calidad. Al comprender el funcionamiento de estas máquinas, los acuicultores pueden optimizar las formulaciones de los alimentos, mejorar el crecimiento de los peces y mejorar la productividad general de la granja.
¿Buscas la mejor máquina de alimentación para peces? ¡Contáctanos hoy mismo!
Ofrecemos una amplia gama de máquinas de alimentación para peces de alto rendimiento, adaptadas a sus necesidades de producción. ¡Contáctenos para obtener asesoramiento experto y precios competitivos!
¿Cuáles son los principales tipos de máquinas de alimentación de peces?
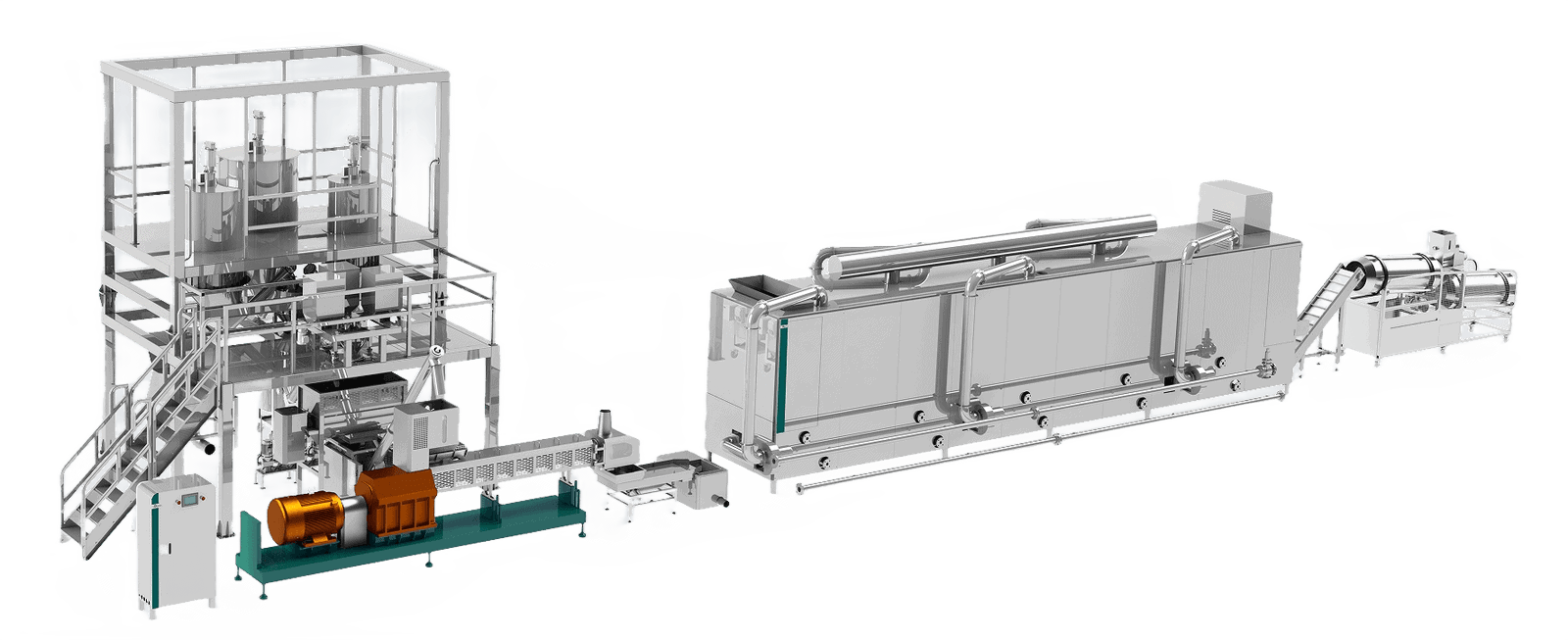
La industria acuícola mundial depende en gran medida de máquinas de alimentación de peces Para producir alimento de alta calidad para diferentes especies de peces. Estas máquinas están diseñadas para procesar ingredientes crudos en pellets que satisfacen las necesidades nutricionales específicas de los peces de cultivo. Sin embargo, no todas las máquinas de alimento para peces funcionan de la misma manera. Se pueden clasificar según... Tipo de alimentación (flotante vs. hundimiento) y Método de operación (manual, semiautomático y completamente automático).
Comprender estas clasificaciones es esencial para los piscicultores que buscan optimizar la eficiencia de la alimentación, reducir el desperdicio y mejorar las tasas de crecimiento de los peces.
Clasificación según el tipo de alimentación: máquinas de alimentación flotante y hundida
Una de las distinciones más importantes entre las máquinas de alimentación de peces es si producen flotante o hundimiento alimento. Esta clasificación depende del proceso de extrusión y la formulación del alimento.
1. Máquinas flotantes de alimentación de peces
Las máquinas de alimentación flotante están diseñadas para producir pellets flotantes que permanecen en la superficie del agua durante períodos prolongados, lo que las hace ideales para peces que se alimentan en la superficie, como la tilapia y el bagre. Estas máquinas utilizan un proceso de extrusión de alta temperatura y alta presión, que hace que el material de alimentación se expanda, reduciendo su densidad y haciéndolo flotar.
Ventajas de las máquinas de alimentación flotante para peces:
- Permite a los agricultores monitorear el comportamiento de alimentación de los peces., evitando la sobrealimentación.
- Reduce el desperdicio de alimento, ya que los pellets no consumidos se pueden retirar del agua.
- Mejora la digestión, ya que el alimento flotante es más fácil de consumir para ciertas especies de peces.
- Mayor estabilidad en el agua, evitando la lixiviación de nutrientes y reduciendo la contaminación.
Ideal para:
- Tilapia
- Bagre
- Pez de colores
- carpa koi
Característica | Máquinas de alimentación flotante |
---|---|
Densidad de pellets | Bajo (expandido y ligero) |
Estabilidad del agua | Flota durante horas |
Presión de extrusión | Alta |
Beneficios nutricionales | Fácilmente digerible, evita la sobrealimentación. |
Aplicación | Peces que se alimentan en la superficie |
2. Máquinas de alimentación de peces que se hunden
Las máquinas de alimentación por hundimiento producen pellets densos que se sumergen inmediatamente en el agua, lo que las hace ideales para especies que se alimentan en el fondo, como camarones y algunos tipos de carpas. Estas máquinas aplican una presión de extrusión más baja, lo que da como resultado pellets compactos que no flotan.
Ventajas de las máquinas de alimentación de peces que se hunden:
- Adecuado para especies que se alimentan naturalmente en el fondo de estanques o tanques.
- Evita la pérdida de alimento debido a las corrientes de agua.
- Es más rentable producirlo, ya que requiere temperaturas de procesamiento más bajas y menos expansión.
- Se puede personalizar para pellets de hundimiento lento o rápido.
Ideal para:
- Gambas
- Carpa
- Anguila
- Langosta
Característica | Máquinas de alimentación por hundimiento |
---|---|
Densidad de pellets | Alto (compacto y denso) |
Estabilidad del agua | Se hunde inmediatamente |
Presión de extrusión | Bajo |
Beneficios nutricionales | Evita que los residuos floten en aguas de movimiento rápido. |
Aplicación | Especies que se alimentan en el fondo |
El alimento flotante es adecuado para todas las especies de peces.Falso
El alimento flotante es ideal para los peces que se alimentan en la superficie, pero las especies que se alimentan en el fondo requieren alimento que se hunda.
Clasificación según el funcionamiento: máquinas manuales, semiautomáticas y totalmente automáticas
Las máquinas de alimentación de peces también difieren en su funcionamiento. La elección entre manual, semiautomático y completamente automático Las máquinas dependen de la capacidad de producción, la disponibilidad de mano de obra y el presupuesto de inversión.
1. Máquinas manuales de alimentación de peces
Las máquinas de alimentación manual requieren operación humana para alimentar materias primas, controlar la mezcla y monitorear la extrusión. Estas máquinas suelen ser de pequeña escala y son adecuadas para granjas con necesidades de producción limitadas.
Ventajas de las máquinas de alimentación manual de peces:
- Bajo costo, haciéndolo accesible para los pequeños piscicultores.
- Operación sencilla, con un mínimo de conocimientos técnicos requeridos.
- Compacto y portátil, ideal para piscifactorías pequeñas o de traspatio.
Desventajas:
- Trabajo intensivo, requiriendo supervisión humana constante.
- Capacidad de producción limitada, lo que lo hace inadecuado para granjas de gran escala.
- Menor consistencia en la calidad del alimento, ya que los ajustes manuales pueden variar.
Característica | Máquinas manuales |
---|---|
Requisito de mano de obra | Alta |
Capacidad de producción | Bajo |
Nivel de automatización | Ninguno |
Lo mejor para | Pequeñas granjas, instalaciones experimentales |
Costo de inversión | Bajo |
2. Máquinas semiautomáticas de alimentación de peces
Las máquinas de alimentación semiautomáticas integran algunos procesos automatizados, como mezcla y extrusión, pero aún requieren alimentación manual de ingredientes y monitoreo. Estas máquinas ofrecen un equilibrio entre asequibilidad y eficiencia.
Ventajas de las máquinas de alimentación de peces semiautomáticas:
- Mayor capacidad de producción que las máquinas manuales.
- Mejor consistencia de la alimentación, ya que la mezcla y la extrusión se controlan mecánicamente.
- Requerimiento de mano de obra moderado, reduciendo la carga de trabajo manual.
- Adecuado para piscifactorías de mediana escala. que necesitan una solución rentable.
Desventajas:
- Todavía requiere intervención humana, aunque menos que las máquinas manuales.
- Opciones de personalización limitadas en comparación con sistemas totalmente automatizados.
Característica | Máquinas semiautomáticas |
---|---|
Requisito de mano de obra | Medio |
Capacidad de producción | Medio |
Nivel de automatización | Parcial |
Lo mejor para | Explotaciones agrícolas de mediana escala |
Costo de inversión | Moderado |
3. Máquinas de alimentación de peces totalmente automáticas
Las máquinas de alimentación totalmente automáticas son sistemas de alta tecnología que manejan todo el proceso de producción de alimentos, desde el ingreso de la materia prima hasta la extrusión de pellets, el secado y el envasado. Estas máquinas son ideales para granjas piscícolas comerciales y empresas de producción de alimentos a gran escala.
Ventajas de las máquinas de alimentación de peces totalmente automáticas:
- Máxima eficiencia y alto rendimiento., capaz de producir varias toneladas por hora.
- Calidad de alimentación constante, garantizando un tamaño de pellet uniforme y un contenido nutricional.
- Reduce los costes laborales, ya que la automatización minimiza la intervención humana.
- Sistemas de control avanzados, including digital monitoring and programmable settings.
Desventajas:
- High initial investment, requiring significant capital.
- Complex setup and maintenance, requiring skilled operators.
- Not ideal for small-scale operations due to high operational costs.
Característica | Fully Automatic Machines |
---|---|
Requisito de mano de obra | Bajo |
Capacidad de producción | Alta |
Nivel de automatización | Full |
Lo mejor para | Large-scale commercial farms |
Costo de inversión | Alta |
Cómo elegir la máquina de alimentación de peces adecuada para su granja
Al seleccionar una máquina de alimentación de peces, tenga en cuenta lo siguiente:
1. Type of Feed Needed
- Floating feed → Choose a floating feed extruder.
- Sinking feed → Opt for a sinking feed machine.
2. Farm Size and Production Scale
- Small farms → Manual or semi-automatic machines (low investment).
- Granjas medianas → Semi-automatic machines (moderate investment).
- Large commercial farms → Fully automatic machines (high investment).
3. Budget Constraints
- Lower budget → Manual or semi-automatic options.
- Higher budget → Fully automated systems with digital control.
4. Labor Availability
- If you have limited manpower, go for automatic machines.
- Si labor is available and affordable, semi-automatic machines may be a cost-effective choice.
Conclusión
Fish feed machines play a crucial role in aquaculture by ensuring efficient and cost-effective feed production. Whether you need a floating or sinking feed machine o una manual, semi-automatic, or fully automatic model, selecting the right equipment depends on your farm's specific needs.
Need Help Choosing a Fish Feed Machine? Contact Us Today!
We offer high-quality fish feed machines tailored to your production needs. Get expert advice and competitive pricing—reach out now!
¿Qué es una extrusora de alimento para peces de tipo seco?
Fish farming requires high-quality, nutritionally balanced feed to ensure the optimal growth and health of aquatic species. One of the most efficient ways to produce fish feed is by using an extrusora, a machine that processes raw ingredients into pellets with precise size, texture, and density. Among different types of extruders, the dry-type fish feed extruder stands out due to its cost-effectiveness, ease of operation, and ability to produce floating and sinking feed without requiring steam conditioning.
Working Principle and Mechanism of a Dry-Type Fish Feed Extruder
A dry-type fish feed extruder operates through mechanical friction and high-pressure extrusion, transforming raw materials into high-quality fish feed pellets. Unlike wet-type extruders, it does not require a steam boiler, making it more affordable and easier to install.
Key Components and Their Functions:
Componente | Función |
---|---|
Tolva de alimentación | Introduces raw materials into the extrusion chamber. |
Transportador de tornillo | Moves ingredients towards the extrusion chamber while applying mechanical pressure. |
Heating and Extrusion Barrel | Generates heat through friction to cook the feed mixture. |
Placa de troquelado | Shapes the pellets by forcing feed through specific hole sizes. |
Cutter Blade | Adjusts pellet length by slicing them as they exit the die. |
Discharge Outlet | Releases finished pellets for cooling and drying. |
How a Dry-Type Fish Feed Extruder Works:
- Raw Material Input: The dry ingredients (such as fishmeal, soybean meal, corn, wheat, and vitamins) are fed into the hopper.
- Mezclar y moler: The screw conveyor pushes materials forward while grinding them into a fine powder.
- Proceso de extrusión:
- The feed mixture is compressed and heated due to friction and high pressure.
- Starch gelatinization occurs, improving digestibility.
- The material expands as it exits the die plate, determining whether the feed will float or sink.
- Pellet Cutting: The rotating cutter blades adjust the pellet size based on the required specifications.
- Enfriamiento y secado: The hot pellets are cooled to remove excess moisture, enhancing shelf life.
- Final Packaging: The finished feed is packed and stored for distribution.
Advantages and Applications of a Dry-Type Fish Feed Extruder
Key Benefits of a Dry-Type Fish Feed Extruder:
Ventaja | Beneficio |
---|---|
No Need for Steam Boilers | Reduces equipment costs and simplifies installation. |
Energy-Efficient | Consumes less power compared to wet-type extruders. |
Compact and Portable | Ideal for small- and medium-scale fish farms. |
Adjustable Pellet Size | Customizable die plates allow pellet sizes from 0.9mm to 10mm, suitable for different fish species. |
Capable of Producing Floating Feed | The high-pressure process allows feed to float for 12-24 hours, reducing waste. |
Easy Operation and Maintenance | User-friendly controls with minimal technical expertise required. |
Lower Operational Costs | No need for steam generation lowers overall costs. |
A dry-type fish feed extruder requires steam for operation.Falso
Unlike wet-type extruders, dry-type extruders generate heat through mechanical friction and do not require a steam boiler.
Applications of Dry-Type Fish Feed Extruders:
- Small- and Medium-Scale Fish Farms: Ideal for farmers producing their own feed to reduce costs.
- Aquaculture Research Centers: Used for testing new feed formulations and improving fish nutrition.
- Feed Processing Factories: Employed in commercial feed production facilities.
- Fabricación de alimentos para animales de compañía: Can also be used for producing dog, cat, and livestock feed.
Suitable Fish Species and Feed Formulas
A dry-type extruder is highly versatile and can produce feed for a wide range of freshwater and marine fish species, as well as shrimp and other aquatic animals.
Best-Suited Fish Species for Dry-Type Extruded Feed:
Especies de peces | Tipo de pienso preferido | Pellet Size Range |
---|---|---|
Tilapia | Floating pellets | 2–4 mm |
Bagre | Floating and sinking pellets | 3–6 milímetros |
Carpa | Sinking pellets | 3–8 mm |
Trucha | Floating pellets | 2–5 mm |
Ornamental Fish (Goldfish, Koi) | Floating micro-pellets | 0.9–3 mm |
Shrimp & Prawn | Slow-sinking pellets | 1–3 mm |
Fórmulas de alimentación comunes para diferentes especies de peces:
1. Fórmula de alimento para tilapia (pellets flotantes, 3-5 mm)
Ingrediente | Porcentaje (%) |
---|---|
Harina de pescado | 25% |
Harina de soja | 35% |
harina de maíz | 20% |
salvado de trigo | 10% |
Aceite de pescado | 5% |
Vitaminas y minerales | 5% |
2. Fórmula de alimento para bagres (gránulos flotantes o hundibles, de 4 a 6 mm)
Ingrediente | Porcentaje (%) |
---|---|
Harina de pescado | 30% |
Harina de gluten de maíz | 20% |
Harina de soja | 25% |
salvado de arroz | 10% |
Aceite de pescado | 8% |
Vitaminas y minerales | 7% |
3. Fórmula de alimento para camarones (pellets de hundimiento lento, 1-3 mm)
Ingrediente | Porcentaje (%) |
---|---|
Harina de pescado | 35% |
harina de trigo | 20% |
Harina de soja | 15% |
Harina de calamar | 10% |
Aceite de pescado | 5% |
Vitaminas y minerales | 5% |
Las extrusoras de alimento para peces de tipo seco no pueden producir alimento que se hunda.Falso
Al ajustar la temperatura de extrusión y el contenido de humedad, las extrusoras de tipo seco pueden producir alimentos tanto flotantes como hundidos.
Cómo elegir la extrusora de alimento seco para peces adecuada
Al seleccionar una extrusora de alimento para peces de tipo seco, tenga en cuenta lo siguiente:
1. Capacidad de producción
- Pequeñas granjas: Extrusoras de 30-200 kg/h
- Fincas medianas: Extrusoras de 200-500 kg/h
- Producción a gran escala: Extrusoras de 500-2000 kg/h
2. Tipo de alimentación
- Alimentación flotante: Requiere configuraciones de temperatura y presión más altas.
- Alimentación que se hunde: Requiere menor temperatura y control de humedad.
3. Ajuste del tamaño del pellet
- Elige un modelo con placas de matriz intercambiables Para producir pellets de diferentes tamaños.
4. Consumo de energía
- Los modelos energéticamente eficientes ayudan a reducir los costos operativos.
Conclusión
A dry-type fish feed extruder Es una herramienta esencial para piscicultores y fabricantes de alimentos que buscan una solución de procesamiento de alimentos rentable, eficiente y fácil de usar. Elimina la necesidad de calderas de vapor y garantiza alimentos flotantes y sumergibles de alta calidad para diversas especies de peces.
Al comprender la Principio de funcionamiento, ventajas y especies de peces adecuadas.Los agricultores pueden optimizar su producción de alimentos y mejorar el crecimiento de los peces y reducir los costos.
¿Busca una extrusora de alimento seco para peces de alta calidad? ¡Contáctenos hoy mismo!
Ofrecemos una gama de Extrusoras de alto rendimiento y eficiencia energética Personalizado para las necesidades de su granja. ¡Contáctenos ahora para obtener recomendaciones de expertos y el mejor precio!
¿Qué es una extrusora de alimento para peces de tipo húmedo?
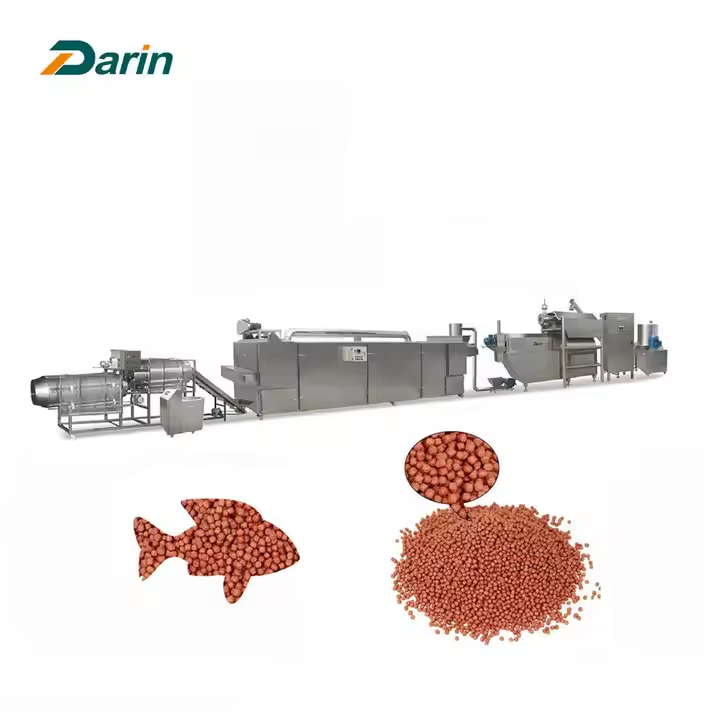
La piscicultura requiere alimentos nutricionalmente equilibrados y de alta calidad para un crecimiento, una salud y una eficiencia óptimos de los peces. Una extrusora de alimento para peces de tipo húmedo Es una máquina especializada que se utiliza en la producción de alimentos a gran escala para crear pellets de alimento para peces de alta calidad y digestibilidad. Utiliza un sistema de preacondicionamiento de vapor, lo que mejora la textura del alimento, mejora la absorción de nutrientes y permite un mejor control sobre la densidad del alimento (flotación o hundimiento).
Entendiendo el Diferencias clave entre extrusoras de tipo húmedo y de tipo seco, junto con sus ventajas, limitaciones y mejores casos de uso, ayuda a los piscicultores a seleccionar el mejor equipo para sus necesidades.
Diferencias clave entre las extrusoras de alimento para peces de tipo húmedo y de tipo seco
Las extrusoras de tipo húmedo se diferencian de las extrusoras de tipo seco principalmente en su Uso de una caldera de vapor para preacondicionamiento, lo que mejora las propiedades físicas y la calidad nutricional del alimento.
Tabla comparativa: extrusoras húmedas y secas
Característica | Extrusora de tipo húmedo | Extrusora de tipo seco |
---|---|---|
Preacondicionamiento con vapor | Sí (utiliza una caldera de vapor) | No (depende del calor por fricción) |
Capacidad de producción | Alto (mejor para granjas a gran escala) | Moderado (granjas de pequeña a mediana escala) |
Calidad de los pellets | Más uniforme, mejor digestibilidad | Bueno pero menos uniforme |
Tipo de alimentación | Flotando y hundiéndose | Flotando y hundiéndose |
Contenido de humedad | Más alto (mejor para almacenamiento prolongado) | Inferior (requiere secado) |
Coste | Mayor inversión inicial | Más asequible |
Consumo de energía | Más alto | Bajo |
Lo mejor para | Acuicultura comercial, grandes granjas | Explotaciones agrícolas de pequeña y mediana escala |
Cómo funciona una extrusora de tipo húmedo:
- Raw Material Input: Se introducen en la máquina ingredientes como harina de pescado, harina de soja y maíz.
- Preacondicionamiento con vapor: La mezcla se trata con vapor, ablandando los ingredientes e iniciando la gelatinización.
- Proceso de extrusión:
- La mezcla se comprime en una cámara de alta presión.
- El calor y la humedad mejoran el proceso de expansión.
- La placa de matriz da forma al alimento en pellets uniformes.
- Corte y secado de pellets: El sistema de corte ajusta la longitud del pellet y el exceso de humedad se elimina mediante el secado.
- Refrigeración y embalaje: El alimento terminado se enfría y se envasa para su distribución.
Las extrusoras de tipo húmedo no pueden producir alimento flotante.Falso
Las extrusoras de tipo húmedo pueden producir alimentos tanto flotantes como hundidos ajustando el contenido de humedad y la configuración de presión.
Beneficios y limitaciones de las extrusoras de alimento húmedo para peces
Beneficios clave de las extrusoras de alimento húmedo para peces:
Beneficio | Descripción |
---|---|
Pellets de calidad superior | El preacondicionamiento con vapor mejora la digestibilidad y la estabilidad del agua. |
Mayor valor nutricional | Retiene más nutrientes debido a la exposición controlada al calor. |
Mayor control sobre la densidad del alimento | Puede producir pellets tanto flotantes como hundidos con alta precisión. |
Mejor expansión y textura | Produce pellets altamente expandidos, ideales para alimentos flotantes. |
Desgaste reducido | El vapor suaviza los materiales, reduciendo la tensión en los componentes de la máquina. |
Limitaciones de las extrusoras de alimento húmedo para peces:
Limitación | Descripción |
---|---|
Mayor coste inicial | Requiere una caldera de vapor, lo que aumenta la inversión general. |
Operación más compleja | Requiere mano de obra calificada para gestionar la configuración del vapor y la calibración de la máquina. |
Mayor consumo de energía | Utiliza más energía debido a la generación de vapor. |
Requiere más espacio | Ocupa más espacio que las extrusoras de tipo seco, por lo que necesita más espacio de instalación. |
Las extrusoras de tipo húmedo sólo son útiles para grandes piscifactorías comerciales.Falso
Si bien las extrusoras de tipo húmedo son las preferidas para operaciones a gran escala, también pueden ser utilizadas por granjas de tamaño mediano que requieren alimentos de mayor calidad.
Mejores casos de uso y requisitos de las piscifactorías
A extrusora de alimento húmedo para peces Es más adecuado para:
1. Granjas de peces comerciales a gran escala
- Granjas productoras más de 500 kg de alimento por hora beneficiarse de la alta eficiencia de extrusoras de tipo húmedo.
- Requiere Producción de piensos constante y de alta calidad para mantener el crecimiento óptimo de los peces.
- Adecuado para acuicultura intensiva donde se requieren altos índices de conversión alimenticia (FCR).
2. Fábricas de procesamiento de alimentos para peces
- Utilizado por fabricantes de alimentos comerciales para abastecer a empresas de acuicultura.
- Esencial para producir piensos de calidad de exportación con textura precisa y estándares nutricionales.
3. Centros de Investigación e Innovación en Acuicultura
- Utilizado en Prueba de fórmulas alimenticias para desarrollar nuevas dietas de alto rendimiento.
- Ofrece una mayor flexibilidad en Personalización de alimentos y optimización de ingredientes.
4. Granjas que crían especies de peces de alto valor
- Ideal para especies que requieren piensos de primera calidad, como el salmón, la trucha y especies híbridas.
- Asegura digestibilidad óptima y desperdicio mínimo, mejorando la rentabilidad.
Especies de peces adecuadas para alimento extruido húmedo:
Especies de peces | Tipo de alimentación | Pellet Size Range |
---|---|---|
Tilapia | Floating pellets | 2–5 mm |
Bagre | Floating and sinking pellets | 3–6 milímetros |
Carpa | Sinking pellets | 4–8 milímetros |
Trucha | Floating pellets | 2–5 mm |
Salmón | Alimento flotante de alto contenido proteico | 3–6 milímetros |
Gambas | Slow-sinking pellets | 1–3 mm |
Fórmulas de alimentación recomendadas para extrusión húmeda:
1. Fórmula de alimento para salmón (gránulos flotantes, 3-6 mm)
Ingrediente | Porcentaje (%) |
---|---|
Harina de pescado | 40% |
Harina de soja | 20% |
Gluten de maíz | 15% |
Aceite de pescado | 10% |
harina de trigo | 10% |
Vitaminas y minerales | 5% |
2. Fórmula de alimento para camarones (pellets de hundimiento lento, 1-3 mm)
Ingrediente | Porcentaje (%) |
---|---|
Harina de pescado | 35% |
Harina de calamar | 20% |
harina de trigo | 15% |
Harina de soja | 10% |
Aceite de pescado | 10% |
Vitaminas y minerales | 10% |
El alimento extruido de tipo húmedo tiene una vida útil más larga que el alimento extruido de tipo seco.Verdadero
Gracias al preacondicionamiento con vapor y a los niveles de humedad controlados, el alimento extruido de tipo húmedo mantiene su calidad nutricional durante períodos más prolongados.
Elegir entre extrusoras de tipo húmedo y de tipo seco: ¿cuál es la adecuada para usted?
Factor | Extrusora de tipo húmedo | Extrusora de tipo seco |
---|---|---|
Lo mejor para | Large commercial farms | Explotaciones agrícolas de pequeña y mediana escala |
Costo de inversión | Alta | Moderado |
Uso de la energía | Más alto | Bajo |
Calidad del alimento | Superior | Bien |
Nivel de automatización | Alta | Medio |
Requisitos de espacio | Más grande | Compacto |
Factores de decisión:
- Si ejecutas un Gran piscifactoría o planta de alimentos comerciales, a extrusora de tipo húmedo Ofrece calidad y eficiencia superiores.
- Si tienes una operación de pequeña a mediana escala, a dry-type extruder es más rentable.
Conclusión
A extrusora de alimento húmedo para peces Es una máquina de procesamiento de alimentos avanzada diseñada para la producción de alimentos de gran volumen y alta calidad. Es ideal para grandes granjas comerciales, fabricantes de alimentos y especies de peces premium que requieren una nutrición óptima. Si bien tiene un costo más alto, los beneficios en uniformidad, digestibilidad y eficiencia de los pellets lo convierten en una opción inversión valiosa para operaciones de acuicultura intensiva.
¿Necesita una extrusora de alimento húmedo para peces? ¡Contáctenos hoy mismo!
Nosotros proporcionamos extrusoras húmedas de alto rendimiento Adaptado a sus necesidades de acuicultura. Obtenga asesoramiento experto y precios competitivos. ¡Contáctenos ahora!
¿Cómo funcionan las máquinas de alimentación flotante para peces?
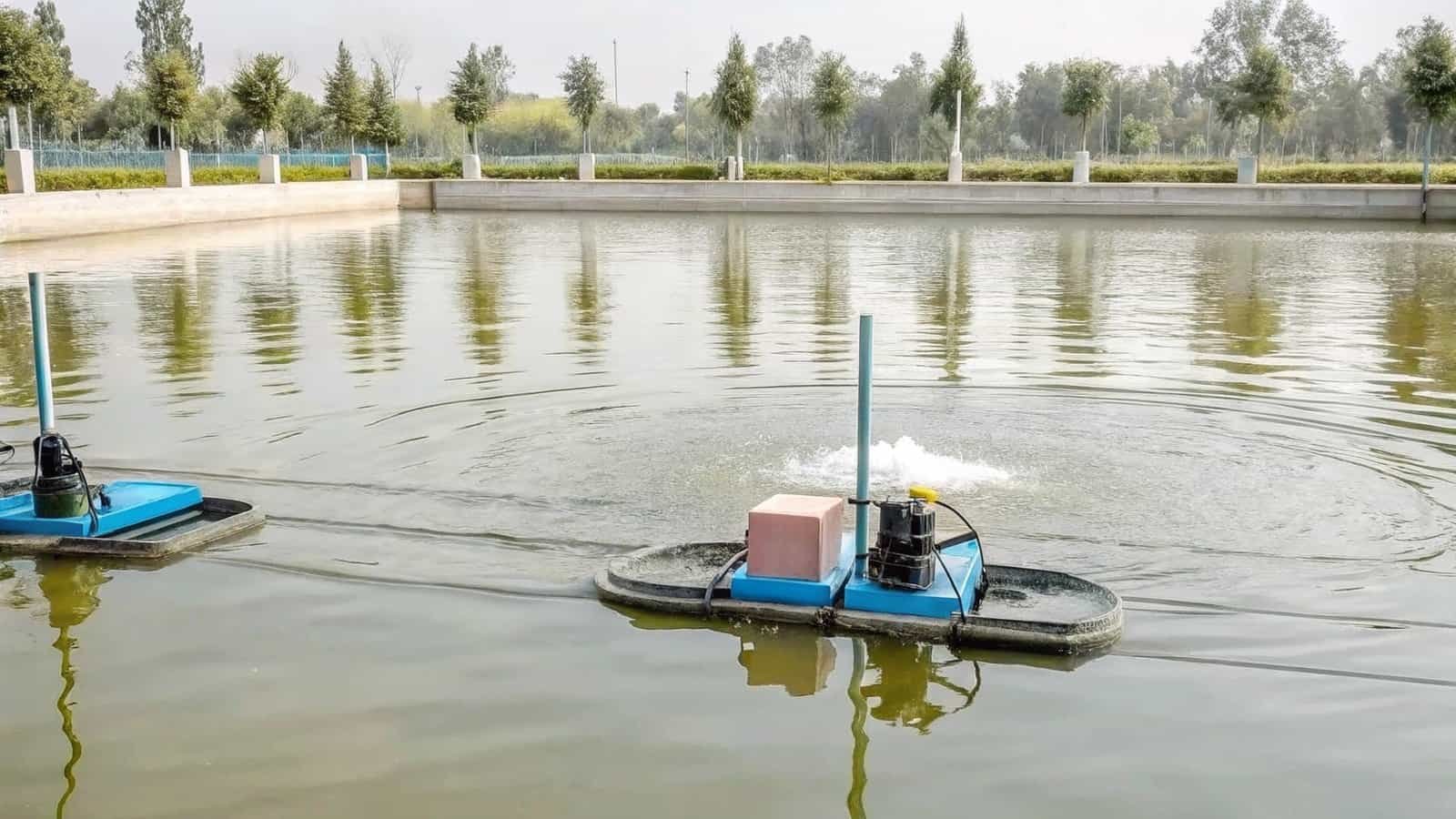
El éxito de piscicultura depende en gran medida de piensos de alta calidad, ya que afecta directamente el crecimiento, la salud y la rentabilidad de los peces. Uno de los tipos de alimento más eficientes y utilizados en la acuicultura es... alimento flotante para peces, que permanece en la superficie del agua, lo que permite un fácil monitoreo del consumo de peces y minimiza el desperdicio de alimento.
Para producir este alimento especializado, los agricultores y fabricantes utilizan máquinas de alimentación flotante para peces, que emplean tecnología de extrusión avanzada para crear pellets nutritivos y flotantes.
Proceso de producción de alimento flotante para peces
El alimento flotante para peces se produce a través de un proceso de extrusión paso a paso que convierte los ingredientes crudos en pellets livianos y expandidos capaces de flotar durante 12–24 horas.
Proceso de trabajo paso a paso de una máquina de alimento flotante para peces:
-
Preparación de la materia prima
- Los ingredientes comunes incluyen: harina de pescado, harina de soja, maíz, trigo, proteína vegetal, aceite de pescado, vitaminas y minerales.
- Las materias primas se muelen hasta obtener un polvo fino mediante un molino de martillos o pulverizador.
-
Mezcla y preacondicionamiento
- A mezclador de alimentos Mezcla bien los ingredientes para garantizar una nutrición uniforme.
- En extrusoras de tipo húmedo, preacondicionamiento con vapor Se aplica para mejorar la expansión y digestibilidad del pellet.
-
Proceso de extrusión
- La mezcla de alimento entra en el cámara de extrusión, donde se comprime mediante un tornillo giratorio dentro de un barril calentado.
- Alta presión y niveles de humedad controlados hacer que el material de alimentación gelatinizar y expandir, creando pellets porosos que flotan en el agua.
- El alimento sale por un placa de matriz, que da forma a los pellets en diferentes tamaños (0,9 mm–10 mm) según la especie de pez.
- A cuchilla de corte Corta el alimento en longitudes uniformes.
-
Secado y enfriamiento
- Los pellets frescos pasan a través de un secador de aire caliente para eliminar el exceso de humedad.
- Luego, los pellets secos se enfrían para garantizar que permanezcan firmes y resistente al desmoronamiento en el agua.
-
Recubrimiento y enriquecimiento de nutrientes
- Algunos pellets de alimento están recubiertos con aceite de pescado, potenciadores del sabor, vitaminas o antibióticos para mejorar la salud y la palatabilidad de los peces.
-
Embalaje y almacenamiento
- El alimento final se envasa en bolsas resistentes a la humedad y se almacena en un lugar fresco y seco Para mantener la frescura.
Diagrama de flujo de producción de alimento flotante:
Materias primas → Molienda → Mezcla → Preacondicionamiento → Extrusión → Secado → Enfriamiento → Recubrimiento → Envasado
Características y tecnología clave involucradas en las máquinas de alimentación flotante para peces
1. Tecnología de extrusión para la producción de piensos flotantes
Extrusión Es la tecnología principal que permite que el alimento para peces flote. Implica:
- Alta temperatura (120–180 °C) y presión para expandir el material de alimentación.
- Gelatinización del almidón, lo que mejora la digestibilidad.
- Niveles de humedad controlados, que determinan si el alimento flotará o se hundirá.
2. Tamaño y densidad de pellets ajustables
Las máquinas de alimentación flotante para peces permiten a los agricultores producir pellets que van desde 0.9mm to 10mm, adecuado para diferentes especies de peces en diversas etapas de crecimiento.
Tamaño del pellet (mm) | Especies de peces |
---|---|
0,9–1,5 mm | Alevines, peces ornamentales |
2–3 milímetros | Tilapia, bagre, trucha |
4–6 milímetros | Carpas, salmones y bagres más grandes |
7–10 milímetros | Peces depredadores grandes (por ejemplo, cabeza de serpiente) |
3. Ajuste de alimentación flotante vs. hundida
Mediante el ajuste temperatura, humedad y presión, la máquina puede producir:
- Alimento flotante (baja densidad, textura porosa)
- Pienso de hundimiento lento (densidad media)
- Alimentación por hundimiento (alta densidad, estructura compacta)
Las máquinas de alimento flotante para peces solo pueden producir alimento flotante.Falso
Ajustando los parámetros de extrusión, la máquina puede producir alimentos flotantes, de hundimiento lento o que se hunden.
4. Sistema de control totalmente automatizado
Las modernas máquinas de alimentación flotante están equipadas con:
- Paneles de control digitales Para una formulación precisa de piensos.
- Sensores de temperatura y humedad para garantizar la coherencia.
- Sistemas automatizados de alimentación y corte para mantener un tamaño de pellet uniforme.
5. Diseño energéticamente eficiente
- Extrusoras de tipo seco utilizan calor por fricción y son adecuados para explotaciones agrícolas de pequeña y mediana escala.
- Extrusoras de tipo húmedo utilizan preacondicionamiento con vapor y son Ideal para producción comercial a gran escala.
Beneficios del alimento flotante para peces en la acuicultura
El alimento flotante para peces ofrece varias ventajas económicas, ambientales y nutricionales, convirtiéndolo en la opción preferida de muchos piscicultores.
1. Mejor utilización del alimento y reducción del desperdicio
- Floating pellets no te hundas, lo que permite a los agricultores controlar el consumo de alimento y ajustar las tasas de alimentación en consecuencia.
- Evita la sobrealimentación, reduciendo la pérdida de alimento y mejorando la rentabilidad de la explotación.
2. Mejor salud y crecimiento de los peces
- Extrusión mejora la digestibilidad, permitiendo que los peces absorban más nutrientes.
- Los pellets permanecen intactos en el agua, Prevenir la lixiviación de nutrientes.
- Reduce los riesgos de enfermedades, ya que el alimento flotante no contamina el fondo del estanque.
3. Beneficios ambientales
- Minimiza la contaminación del agua, ya que los pellets flotantes no consumidos se pueden quitar fácilmente.
- A diferencia de los alimentos que se hunden, los alimentos flotantes no se degradan rápidamente, lo que mantiene mejor calidad del agua.
4. Ahorro de costes para los piscicultores
Factor | Alimentación flotante | Alimentación que se hunde |
---|---|---|
Índice de conversión alimenticia (ICA) | 1.2 – 1.5 | 1.5 – 2.0 |
Residuos de piensos | Bajo | Moderado |
Contaminación del agua | Bajo | Más alto |
Riesgo de enfermedad | Bajo | Más alto |
El alimento flotante para peces siempre es más caro que el que se hunde.Falso
Si bien el alimento flotante requiere procesamiento de extrusión, el menor desperdicio de alimento y un mejor FCR a menudo lo hacen más rentable a largo plazo.
5. Adecuado para una amplia gama de especies de peces.
El alimento flotante para peces es beneficioso para las especies que se alimentan en la superficie del agua, como:
Especies de peces | Mejor tipo de pellet |
---|---|
Tilapia | Floating feed |
Bagre | Alimento flotante o de hundimiento lento |
Trucha | Floating feed |
Peces ornamentales | Floating micro-pellets |
Salmón | Floating feed |
Conclusión
A máquina de alimentación flotante para peces es una herramienta esencial en la acuicultura, utilizando tecnología de extrusión para producir pellets flotantes de alta calidad y nutricionalmente equilibrados. Esta máquina avanzada ofrece control preciso sobre el tamaño y la densidad de los pellets, permitiendo a los piscicultores optimizar la utilización del alimento, reducir el desperdicio y mejorar la salud de los peces.
Con Operación energéticamente eficiente, controles automatizados y la capacidad de producir fórmulas de alimentación personalizablesUna máquina de alimentación flotante para peces es una Un punto de inflexión para las piscifactorías modernas.
¿Buscas la mejor máquina de alimentación flotante para peces? ¡Contáctanos hoy mismo!
Ofrecemos extrusoras de alta calidad Para piscifactorías pequeñas, medianas y grandes. Reciba recomendaciones de expertos y precios competitivos. ¡Contáctenos ahora!
¿Cómo funcionan las máquinas de alimentación de peces que se hunden?
La acuicultura requiere diferentes tipos de alimentos para peces dependiendo del comportamiento alimentario de las distintas especies de peces. Alimento para peces que se hunde es esencial para las especies que se alimentan en el fondo, como camarones, carpas, bagres y anguilas, ya que entrega nutrientes directamente a donde estos peces se alimentan naturalmente.
A máquina de alimentación de peces que se hunde Está especialmente diseñado para producir pellets compactos de alta densidad que se hunden inmediatamente al colocarlos en agua. Estas máquinas utilizan Ajustes controlados de humedad, presión y temperatura para crear pellets de alimento no expandido con estabilidad superior en agua.
Proceso de formación de pellets para piensos que se hunden
¿Cómo funciona una máquina de alimentación de peces que se hunde?
El alimento para peces que se hunde se produce utilizando tecnología de extrusión o peletización, según las características deseadas del alimento. El proceso sigue estos pasos clave:
1. Selección y molienda de materia prima
- Ingredientes de alta calidad como harina de pescado, harina de soja, gluten de maíz, salvado de trigo, aceite de pescado y premezclas de vitaminas están seleccionados.
- A molino de martillos o pulverizador Muele las materias primas hasta convertirlas en polvo fino, garantizando una textura uniforme y digestibilidad.
2. Mezcla y preacondicionamiento
- Los ingredientes molidos se mezclan en un mezclador de alimentos para distribución uniforme de nutrientes.
- En extrusoras de tipo húmedo, acondicionamiento de vapor Se aplica para mejorar la unión y la resistencia de los pellets.
- En extrusoras de tipo secoEn su lugar se utilizan humedad controlada y fricción mecánica.
3. Proceso de extrusión o peletización
- La mezcla de alimento entra en el extrusora o peletizadora, donde un El mecanismo de tornillo comprime el material. bajo alta presión.
- A diferencia de los alimentos flotantes, temperatura y presión más bajas Se aplican dando como resultado pellets densos y no expandidos.
- La mezcla se fuerza a través de un placa de matriz para dar forma a los pellets.
- A cuchilla de corte Corta los pellets a la longitud requerida.
4. Secado y enfriamiento
- Los pellets que se hunden recién extruidos contienen exceso de humedad y deben secarse.
- A sistema de secado reduce el contenido de humedad a por debajo de 12%, garantizando una larga vida útil.
- El enfriamiento se realiza para evitar la rotura de los pellets y mejorar la durabilidad.
5. Embalaje y almacenamiento
- El alimento final se envasa en bolsas resistentes a la humedad y se almacena en un lugar seco y fresco Para mantener la frescura.
Idoneidad para especies de peces que se alimentan en el fondo
¿Por qué algunos peces prefieren el alimento que se hunde?
Ciertas especies de forma natural alimentar cerca del fondo de estanques, lagos o tanques. El alimento flotante no es adecuado para estos peces, ya que están adaptados a alimentarse en el sustrato.
Especies de peces que se alimentan en el fondo | Mejor tipo de pellet | Tamaño del pellet (mm) |
---|---|---|
Carpa | Sinking pellets | 3–8 mm |
Bagre | Pellets de hundimiento lento o que se hunden | 3–6 milímetros |
Anguila | Sinking pellets | 2–5 mm |
Shrimp & Prawn | Slow-sinking pellets | 1–3 mm |
Tilapia (grande) | Sinking pellets | 4–6 milímetros |
Todas las especies de peces prefieren el alimento flotante.Falso
Muchas especies, como los camarones, las carpas y los bagres, se alimentan en el fondo y requieren alimento que se hunda.
Ventajas del alimento hundido para los alimentadores de fondo
- Asegura Los nutrientes llegan a los peces que viven en el fondo En lugar de flotar.
- Reduce competencia de las especies que se alimentan en la superficie, permitiendo una alimentación dirigida.
- Previene la pérdida de alimento en condiciones de agua turbulenta., donde el alimento flotante podría desplazarse.
Consideraciones de costo-eficacia y eficiencia
1. Costos de producción más bajos en comparación con el alimento flotante
Factor | Producción de alimento para hundimiento | Producción de pienso flotante |
---|---|---|
Presión de extrusión | Bajo | Alta |
Requisito de humedad | Moderado | Alta |
Consumo de energía | Bajo | Más alto |
Pretratamiento con vapor | Opcional | Requerido (para extrusoras húmedas) |
Coste de producción | Bajo | Más alto |
- El alimento que se hunde requiere menos expansión y temperaturas de procesamiento más bajas, haciéndolo más rentable para producir alimento flotante.
- Menor desgaste de la maquinaria debido a una menor fricción y estrés mecánico.
2. La alta estabilidad del agua reduce los residuos.
- Los perdigones que se hunden permanecen intactos durante mayores duraciones en el agua, previniendo lixiviación de nutrientes.
- A diferencia de los alimentos mal procesados, El alimento que se hunde, correctamente extruido, no se disuelve rápidamente, reduciendo la acumulación de desechos en el fondo del estanque.
3. Más eficiente para ciertas piscifactorías
- Las granjas de camarones y peces de fondo se benefician de una mayor utilización de alimento.
- Peces criados en estanques profundos donde es difícil monitorear el alimento flotante.
- Entornos con fuertes corrientes de agua, donde los pellets flotantes podrían ir a la deriva.
El alimento que se hunde se disuelve rápidamente en el agua, lo que genera desperdicio.Falso
El alimento sumergido extruido adecuadamente mantiene su integridad durante períodos prolongados, minimizando el desperdicio.
Cómo elegir la máquina de alimentación hundible para peces adecuada
Características principales
Característica | Importancia |
---|---|
Control de densidad de pellets | Garantiza una velocidad de hundimiento correcta según las necesidades de la especie. |
Eficiencia energética | Reduce los costos operativos a lo largo del tiempo. |
Personalización del tamaño de los pellets | Apoya las diferentes etapas de crecimiento de los peces. |
Nivel de automatización | Las máquinas totalmente automatizadas mejoran la consistencia y reducen los costos laborales. |
Tipos de máquinas de alimentación de peces que se hunden
Tipo de máquina | Lo mejor para |
---|---|
Molino de pellets | Producción sencilla de piensos de hundimiento para pequeñas explotaciones |
Extrusora de tipo seco | Producción de alimento de hundimiento a costo moderado |
Extrusora de tipo húmedo | Producción de piensos de hundimiento de gran volumen para granjas comerciales |
Conclusión
A máquina de alimentación de peces que se hunde es una herramienta esencial para las explotaciones ganaderas especies que se alimentan en el fondocomo carpas, camarones, bagres y anguilasEstas máquinas procesan eficientemente pellets nutricionalmente equilibrados que se hunden inmediatamente, asegurando Mejor conversión alimenticia, reducción de desperdicios y ahorro de costos en comparación con el alimento flotante.
Por Ajuste de la humedad, la presión y la temperatura, las máquinas de alimentación de peces que se hunden producen Pellets duraderos y estables al agua Adecuado para sistemas de acuicultura de aguas profundas. El menores necesidades energéticas y costos de producción reducidos hazles un Solución rentable tanto para piscifactorías comerciales como de pequeña escala.
¿Buscas la mejor máquina de alimentación hundible para peces? ¡Contáctanos hoy mismo!
Ofrecemos Extrusoras de alimentación por hundimiento de alto rendimiento Para diferentes tamaños de granjas y capacidades de producción. Obtenga asesoramiento experto y precios competitivos. ¡Contáctenos ahora!
¿Cuáles son las diferencias entre los molinos de pellets y las extrusoras?
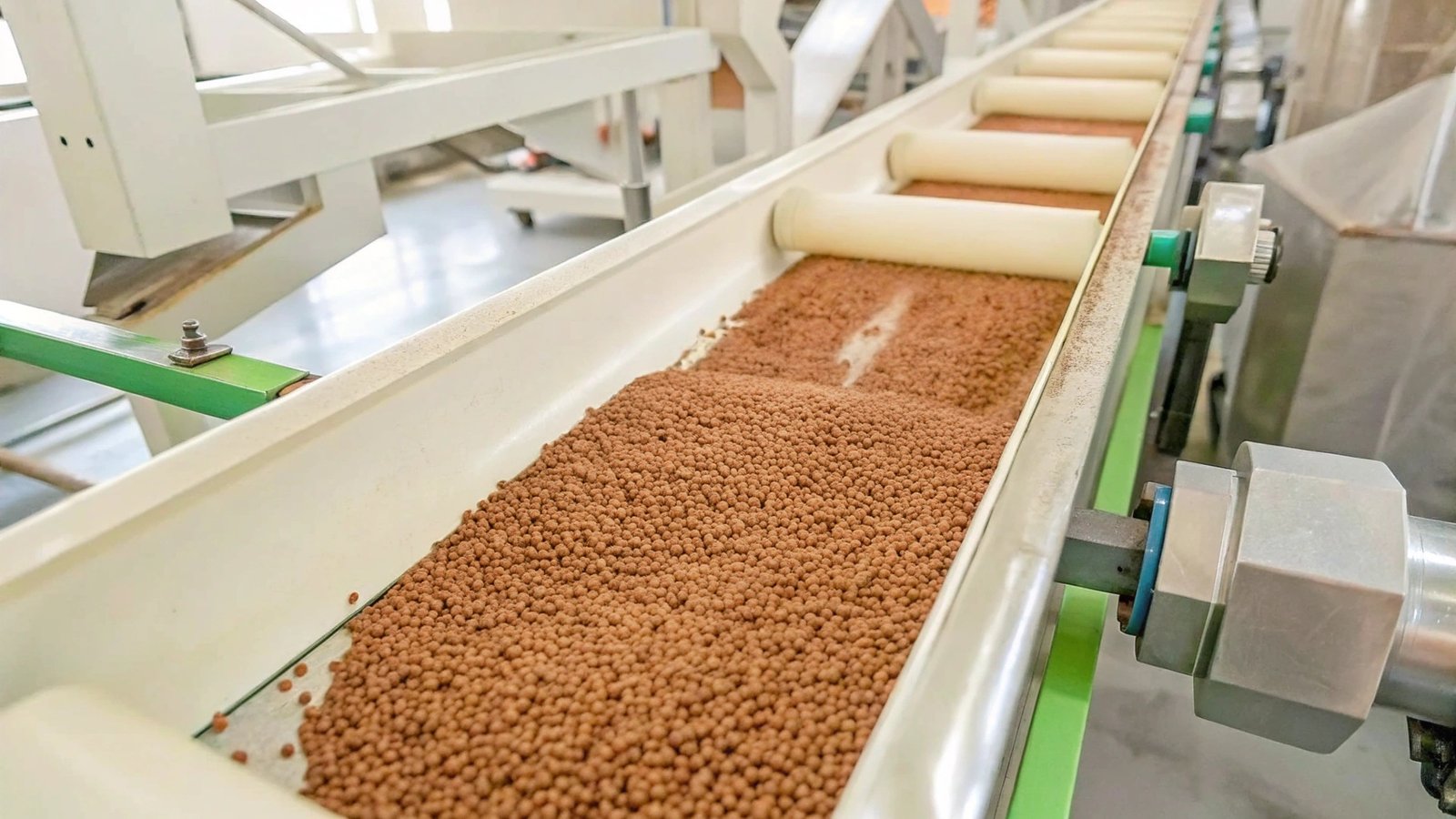
En la industria de la acuicultura, calidad del alimento para peces Desempeña un papel crucial en el crecimiento, la salud y la rentabilidad general de las granjas de peces. Se utilizan dos tecnologías principales para producir pellets de alimento para peces: molinos de pellets y extrusoras. Mientras ambas máquinas convierten los ingredientes crudos en alimento para peces, Difieren en los métodos de procesamiento, las características de los pellets y la eficiencia de producción.
Comprender estas diferencias ayuda a los piscicultores y fabricantes de alimentos. Seleccione la mejor máquina en función de sus necesidades específicas, especies de peces y escala de producción.
Tecnología de peletización vs. tecnología de extrusión
1. Cómo funciona una peletizadora
A molino de pellets utiliza un proceso de compresión mecánica Para formar pellets. Funciona de la siguiente manera:
- Las materias primas son molido y mezclado en una mezcla de alimento uniforme.
- La mezcla se introduce en la fábrica de pellets, donde Los rodillos presionan el alimento a través de una placa de matriz con pequeños agujeros.
- El presión y fricción generar algo de calor, que une los ingredientes en pellets compactos.
- Los pellets formados se cortan a la longitud deseada mediante un cuchilla de corte giratoria.
- Los pellets son enfriado y secado Para mejorar la durabilidad.
Las fábricas de pellets producen alimentos que se hunden porque no generan suficiente calor y presión para expandir el alimento y hacerlo flotar.
2. Cómo funciona una extrusora
En extrusora utiliza un proceso de alta temperatura y alta presión Para producir alimento para peces. El proceso implica:
- Molienda y mezcla: Los ingredientes se muelen finamente y se mezclan.
- Preacondicionamiento (para extrusoras húmedas): Se inyecta vapor para ablandar la mezcla de alimento.
- Extrusión: La mezcla se comprime y se empuja a través de un Transportador de tornillo dentro de un barril calentado, donde experimenta:
- Presión alta
- Calor intenso (120–180 °C)
- Gelatinización y expansión del almidón
- El feed es entonces forzado a través de una placa de matriz, dónde el agua se evapora, expandiendo los pellets.
- Los pellets expandidos son cortado, secado y enfriado Antes del embalaje.
Las extrusoras pueden producir alimentos tanto flotantes como hundidos ajustando la temperatura, la humedad y la presión.
Análisis comparativo de rendimiento y costo
1. Comparación entre molinos de pellets y extrusoras
Característica | Molino de pellets | Extrusora |
---|---|---|
Método de tratamiento | Compresión mecánica | Extrusión de alta temperatura y alta presión |
Tipo de pellet | Solo perdigones que se hunden | Pellets flotantes, de hundimiento lento y de hundimiento |
Generación de calor | Bajo a moderado | Alta |
Gelatinización del almidón | Parcial (menos digerible) | Completo (muy digerible) |
Durabilidad de los pellets | Medio | Alta |
Estabilidad del agua | Más corto (los pellets se descomponen más rápido) | Más largo (resistente a la desintegración por agua) |
Eliminación de humedad | Requiere secado | El alimento extruido pierde humedad de forma natural. |
Consumo de energía | Bajo | Más alto |
Coste inicial | Bajo | Más alto |
Capacidad de producción | Suitable for small- to medium-scale farms | Best for large-scale and commercial production |
Índice de conversión alimenticia (ICA) | Moderado | Better due to higher digestibility |
Extruders can only produce floating feed.Falso
Extruders can produce floating, slow-sinking, and sinking pellets by adjusting processing parameters.
2. Cost Comparison: Which is More Affordable?
Factor | Molino de pellets | Extrusora |
---|---|---|
Machine Cost | Lower ($2,000–$15,000) | Higher ($10,000–$100,000) |
Coste operativo | Lower (less energy use) | Higher (more electricity and steam) |
Requisito de mano de obra | Mínimo | More technical expertise needed |
Coste de mantenimiento | Lower (fewer parts wear out) | Higher (extruder parts like screws wear faster) |
Feed Waste Reduction | Moderado | Higher (extruded pellets last longer in water) |
Overall Long-Term Cost Savings | Inversión inicial más baja | Higher efficiency and feed utilization |
Pellet mills are always cheaper to operate than extruders.Falso
While pellet mills have lower energy consumption, extruders improve feed efficiency, reducing long-term costs.
Which Is Better for Different Fish Species?
1. When to Use a Pellet Mill
Pellet mills are best suited for bottom-feeding fish that require sinking pellets. These include:
Especies de peces | Mejor tipo de pellet | Recommended Pellet Size |
---|---|---|
Carpa | Sinking pellets | 3–8 mm |
Shrimp & Prawn | Slow-sinking pellets | 1–3 mm |
Anguila | Sinking pellets | 2–5 mm |
Large Catfish | Sinking pellets | 4–6 milímetros |
low-cost fish feed production
small and medium farms
floating feed is unnecessary
2. When to Use an Extruder
Extruders are preferred when floating or highly digestible sinking feed is required. These include:
Especies de peces | Mejor tipo de pellet | Recommended Pellet Size |
---|---|---|
Tilapia | Floating pellets | 2–5 mm |
Trucha | Floating pellets | 2–5 mm |
Ornamental Fish (Koi, Goldfish) | Floating micro-pellets | 0.9–3 mm |
Salmón | Floating high-protein feed | 3–6 milímetros |
high-value fish species
commercial-scale farms
reducing feed waste and improving FCR
Floating feed is better for all fish species.Falso
While floating feed is useful for surface feeders, bottom-feeding species require sinking pellets.
Conclusion: Which Machine Should You Choose?
Decision Factor | Molino de pellets | Extrusora |
---|---|---|
Best for Farm Size | Small- to medium-scale | Medium- to large-scale |
Initial Budget | Bajo | Más alto |
Tipo de alimentación | Sinking feed | Floating & sinking feed |
Feed Efficiency | Moderado | Alta |
Uso de la energía | Bajo | Alta |
Technical Complexity | Fácil de operar | Requires skilled labor |
Choose a Pellet Mill If:
- You produce only sinking feed.
- You have a low budget y necesitan cost-effective feed production.
- Your farm is small to medium-sized.
Choose an Extruder If:
- You need floating feed or high-quality sinking feed.
- You require better digestibility and feed conversion.
- Your farm is commercial-scale, and you want to maximize production efficiency.
Need Expert Advice? Contact Us Today!
Whether you need a pellet mill or an extruder, we provide high-performance fish feed machines tailored to your farm’s needs. Get expert recommendations and the best pricing—reach out now!
¿Qué factores debes considerar al elegir una máquina de alimentación de peces?
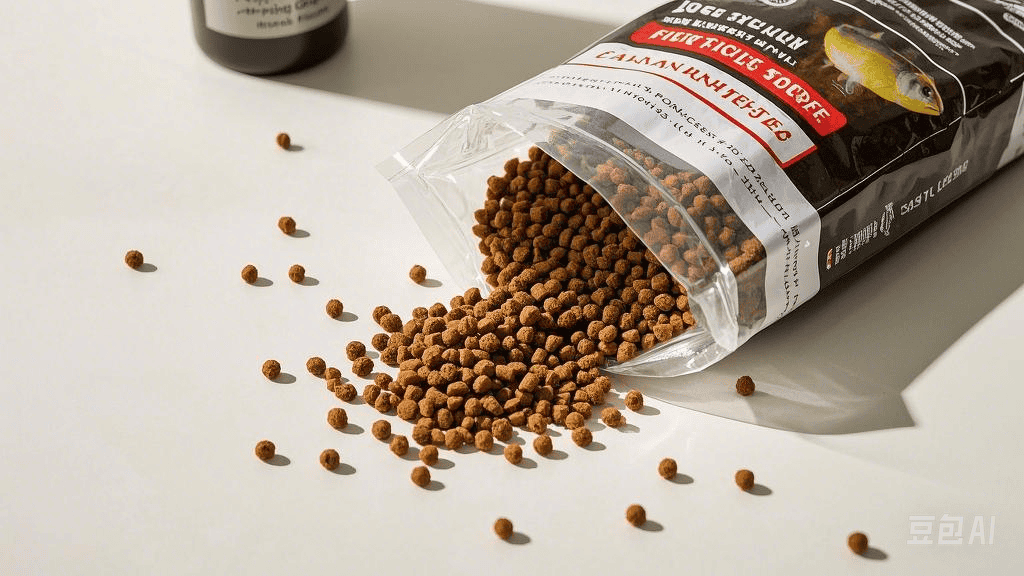
Selecting the right fish feed machine is crucial for ensuring efficient feed production, cost-effectiveness, and optimal fish growth. The type of machine you choose will directly impact feed quality, production costs, and farm profitability.
Several key factors must be considered when purchasing a fish feed machine, including production capacity, operational costs, maintenance requirements, feed quality, and compatibility with different fish species.
This guide provides an in-depth analysis of these factors to help fish farmers and feed manufacturers make the best decision.
1. Capacity and Production Requirements
Why Is Production Capacity Important?
The capacity of a fish feed machine determines how much feed you can produce per hour, which is essential for meeting the feeding demands of your farm or commercial operation.
Farm Size | Production Requirement | Tipo de máquina recomendada |
---|---|---|
Small-scale farm | 50–300 kg/h | Small pellet mill or dry-type extruder |
Medium-scale farm | 300–1000 kg/h | Dry-type extruder or medium pellet mill |
Large-scale farm or commercial factory | 1000–5000+ kg/h | Wet-type extruder or large automated feed plant |
Choosing the Right Machine Based on Farm Size
- For small farms: A compact pellet mill or small extruder (50–300 kg/h) is sufficient.
- For medium farms: A dry-type extruder (300–1000 kg/h) balances cost and efficiency.
- For large farms and factories: A wet-type extruder (1000–5000+ kg/h) provides high output and premium feed quality.
A high-capacity fish feed machine is always the best choice for any farm.Falso
The ideal machine depends on farm size and production needs; smaller farms may not require high-capacity machines.
2. Cost and Maintenance Needs
Upfront Investment vs. Long-Term Costs
Mientras que el initial cost of a fish feed machine is important, you must also consider long-term expenses, incluyendo:
- Consumo de energía
- Labor costs
- Machine wear and tear
- Spare parts availability
Cost Comparison: Pellet Mill vs. Extruder
Factor | Molino de pellets | Extrusora |
---|---|---|
Coste inicial | Lower ($2,000–$15,000) | Higher ($10,000–$100,000) |
Coste operativo | Lower energy usage | Higher power consumption |
Necesidades de mantenimiento | Bajo | Medium to high |
Spare Parts | Cheaper, less frequent replacement | More expensive, frequent part replacement |
Requisito de mano de obra | Bajo | Requiere operarios cualificados |
Maintenance Considerations
- Pellet mills requerir menos mantenimiento, ya que operan a temperaturas y presiones más bajas.
- Extrusoras requerir mantenimiento más frecuente, especialmente para tornillos, barriles y placas de matriz, que se desgastan con el tiempo.
- Extrusoras de tipo húmedo requerir mantenimiento de calderas de vapor, añadiendo costos operativos adicionales.
Las máquinas de alimentación de peces no tienen costos de mantenimiento después de la compra.Falso
Todas las máquinas de alimentación de peces requieren un mantenimiento regular para garantizar un funcionamiento eficiente y una larga vida útil.
3. Calidad del alimento y compatibilidad de especies de peces
1. Máquinas de alimentación flotantes vs. máquinas de alimentación hundidas
Diferentes especies de peces requieren: alimento flotante o hundidoSu máquina debe adaptarse al comportamiento alimentario de sus peces.
Tipo de alimentación | Lo mejor para | Tipo de máquina |
---|---|---|
Pellets flotantes | Peces que se alimentan en la superficie (tilapia, trucha, koi) | Extrusora |
Pellets de hundimiento lento | Alimentadores de aguas medias (especies híbridas) | Extrusor ajustable |
Pellets que se hunden | Peces de fondo (carpas, bagres, camarones) | Molino de pellets o extrusora controlada |
2. Eficiencia de conversión alimenticia
- El alimento extruido es más digerible debido a gelatinización del almidón, lo que lleva a mayores índices de conversión alimenticia (ICA).
- El alimento granulado es menos digerible, lo que significa que pueden perderse algunos nutrientes.
Tipo de alimentación | Índice de conversión alimenticia (ICA) |
---|---|
Alimento extruido | 1.2–1.5 |
Pienso granulado | 1,5–2,0 |
Una mayor digestibilidad reduce el desperdicio de alimento y mejora el crecimiento de los peces.
3. Personalización del tamaño del feed
Los peces requieren diferentes tamaños de pellets Dependiendo de su etapa de crecimiento, su máquina debería ser compatible. múltiples placas de matriz para tamaños de pellets que van desde 0.9mm to 10mm.
Etapa de crecimiento de los peces | Recommended Pellet Size |
---|---|
Alevines (peces juveniles) | 0,9–1,5 mm |
Alevines | 2–3 milímetros |
Peces de crecimiento | 4–6 milímetros |
Grandes peces depredadores | 7–10 milímetros |
Todas las especies de peces pueden comer el mismo tamaño y tipo de pellets.Falso
Diferentes especies de peces requieren tamaños y tipos de pellets específicos según su comportamiento alimentario y etapa de crecimiento.
Preguntas clave que debe hacerse antes de comprar una máquina de alimentación de peces
1. ¿Cuál es mi requerimiento de producción?
2. ¿Qué tipo de alimento necesito producir?
3. ¿Cuál es mi presupuesto?
inversión inicial y costos operativos a largo plazo.
4. ¿Cuánta automatización necesito?
Manual Las máquinas requieren más mano de obra pero cuestan menos.
Automático Las máquinas mejoran la eficiencia pero cuestan más.
5. ¿Cuáles son los requerimientos energéticos y de mantenimiento de la máquina?
modelo de eficiencia energética Si los costos de funcionamiento son una preocupación.
Hay repuestos disponibles para mantenimiento.
Comparación final: ¿Qué máquina de alimentación de peces es adecuada para usted?
Factor | Molino de pellets | Extrusora de tipo seco | Extrusora de tipo húmedo |
---|---|---|---|
Lo mejor para | Sinking feed | Floating & sinking feed | Alimento flotante y hundido de alta calidad |
Capacidad de producción | Bajo a medio | Medio | Alta |
Calidad del alimento | Moderado | Bien | Mejor |
Coste inicial | Bajo | Moderado | Alta |
Costo de operación | Bajo | Moderado | Alta |
Consumo de energía | Bajo | Medio | Alta |
Nivel de automatización | Manual/Semiautomático | Semiautomático | Completamente automático |
Necesidades de mantenimiento | Bajo | Medio | Alta |
Conclusión
Elegir lo correcto máquina de alimentación de peces depende de varios factores, entre ellos Capacidad de producción, costos, necesidades de mantenimiento, calidad del alimento y compatibilidad de especies de peces.
Pellet mills son adecuados para Pequeñas granjas que necesitan alimento para animales que se hunden a un costo menor.
Extrusoras de tipo seco son ideales para Granjas de escala media que producen piensos flotantes y sumergibles.
Extrusoras de tipo húmedo oferta la más alta calidad de alimento para grandes operaciones comerciales.
Invertir en la máquina adecuada garantiza Mejor crecimiento de los peces, menor desperdicio de alimento y mayor rentabilidad.
¿Necesita ayuda para elegir la mejor máquina de alimentación para peces? ¡Contáctenos hoy mismo!
Nosotros proporcionamos máquinas de alimentación de peces de alto rendimiento Adaptado a las necesidades de su explotación. Obtenga recomendaciones de expertos y... best pricing—reach out now!
¿Cómo se puede mantener y prolongar la vida útil de una máquina de alimentación de peces?
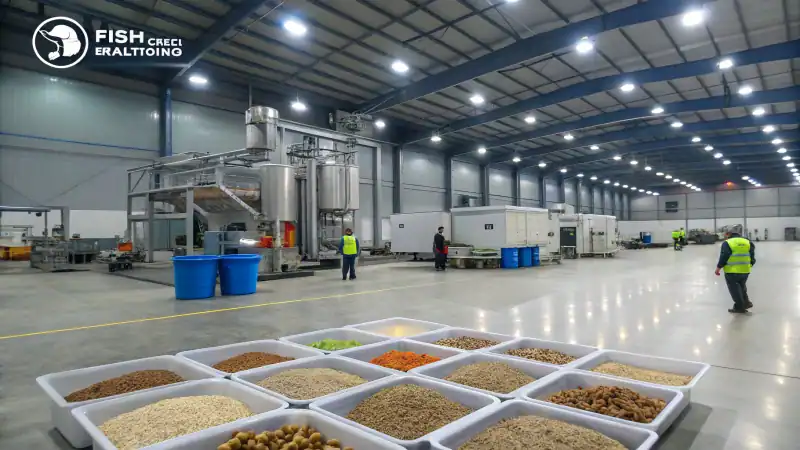
A máquina de alimentación de peces es una inversión importante para cualquier negocio de acuicultura. Asegurar su Larga vida útil y rendimiento óptimo Requiere un mantenimiento adecuado, limpieza regular, resolución de problemas oportuna y una gestión eficaz de las piezas de repuesto. Sin un mantenimiento regular, las máquinas pueden sufrir... Obstrucciones, reducción de la eficiencia, aumento del consumo de energía y averías prematuras.
Esta guía proporciona Consejos esenciales de limpieza y mantenimiento, soluciones de resolución de problemas y estrategias de gestión de repuestos para ayudar a prolongar la vida útil de su máquina de alimentación de peces.
1. Consejos de limpieza y mantenimiento rutinario
Lista de verificación de mantenimiento diario
Realizar estas tareas después de cada ciclo de producción Para evitar la acumulación de residuos de alimento y garantizar un funcionamiento sin problemas:
Tarea de mantenimiento | Propósito | ¿Con qué frecuencia? |
---|---|---|
Limpiar el alimentador y la tolva | Previene el bloqueo del material | Después de cada uso |
Limpie la cámara de extrusión | Evita la acumulación de alimento viejo | Después de cada uso |
Inspeccione la placa de matriz y las cuchillas de corte | Garantiza un tamaño de pellet uniforme | Diario |
Compruebe el motor y las correas | Previene el desgaste mecánico | Diario |
Lubricar las piezas móviles | Reduce la fricción y el sobrecalentamiento. | Diario |
Lista de verificación de mantenimiento semanal
Se debe realizar una inspección más exhaustiva cada semana Para evitar el desgaste:
Tarea | Por qué es importante |
---|---|
Compruebe el tornillo y el cañón | Los tornillos desgastados pueden reducir la eficiencia y afectar la calidad de los pellets. |
Inspeccionar cojinetes y rodillos | Los cojinetes dañados provocan vibraciones y ruidos. |
Apriete los pernos y conexiones flojos | Previene desalineaciones y posibles averías. |
Lavar el sistema de lubricación | Mantiene los componentes internos funcionando sin problemas |
Mantenimiento preventivo mensual
Se debe realizar una inspección y un mantenimiento más profundos. una vez al mes Para detectar cualquier fallo potencial de forma temprana:
- Inspeccionar los elementos calefactores en extrusoras por inconsistencias de temperatura.
- Verifique el cableado eléctrico y los paneles de control. para detectar cualquier signo de desgaste o daño.
- Calibrar sensores y configuraciones de control para mantener una formulación precisa del alimento.
- Examinar el sistema de enfriamiento y secado. para garantizar una calidad uniforme de los pellets.
Las máquinas de alimentación de peces no requieren una limpieza regular.Falso
La limpieza regular evita la acumulación de residuos de alimento, mejora la eficiencia y prolonga la vida útil de la máquina.
2. Problemas comunes de resolución de problemas y soluciones
Incluso con un mantenimiento adecuado, Pueden ocurrir problemas operativosA continuación se presentan algunos problemas comunes y cómo resolverlos.
1. Sobrecalentamiento de la máquina de alimentación
Causa:
- Falta de lubricación
- Fricción excesiva en las piezas móviles
- Ventilación bloqueada
Solución:
- Aplicar lubricantes de alta calidad a partes móviles.
- Limpio áreas de ventilación para permitir un flujo de aire adecuado.
- Reducir la carga de la máquina y dejarla funcionar enfriarse periódicamente.
2. Tamaño o forma irregular de los pellets
Causa:
- Desgastado placa de matriz o cuchillas de corte
- Contenido de humedad desigual en la mezcla de alimento
Solución:
- Reemplazar las placas de matriz desgastadas regularmente.
- Asegúrese Mezcla adecuada de ingredientes y control de la humedad en la fórmula del alimento.
3. Los pellets de alimento se desmoronan o rompen fácilmente
Causa:
- Agentes aglutinantes insuficientes en la mezcla de pienso
- Baja presión de compresión en la extrusora
Solución:
- Agregar agentes aglutinantes como el aceite de pescado o el almidón.
- Ajustar el ajustes de presión del extrusor para aumentar la densidad de los pellets.
La durabilidad de los pellets solo está determinada por la mezcla de alimentación.Falso
Los ajustes de la máquina, como la presión de compresión y la calidad de la placa de matriz, también afectan la durabilidad de los pellets.
4. Obstrucción en la cámara de extrusión
Causa:
- Mezcla de alimento excesivamente seca o pegajosa
- Materias primas de baja calidad que provocan acumulación de residuos
Solución:
- Ajustar niveles de humedad en la fórmula del alimento.
- Regularmente Limpiar la cámara de extrusión y los tornillos para evitar la acumulación de residuos.
5. Máquina que produce ruido o vibraciones excesivas
Causa:
- Tornillos o pernos sueltos
- Cojinetes desgastados
Solución:
- Apriete todas las conexiones y comprobar si hay desalineaciones.
- Reemplace los cojinetes dañados para evitar más daños mecánicos.
El ruido y las vibraciones en una máquina de alimentación de peces son normales y no requieren atención.Falso
El exceso de ruido y vibraciones indican problemas mecánicos como pernos flojos o cojinetes desgastados, que requieren una inspección inmediata.
3. Gestión y servicio de repuestos
Acuerdo repuestos esenciales lata a mano evitar costosos tiempos de inactividad y garantizar un funcionamiento sin problemas.
Repuestos esenciales para tener en stock
Pieza de recambio | Función | Frecuencia de reemplazo |
---|---|---|
Placa de troquelado | Formas de pellets de alimentación | Cada 3 a 6 meses |
Transportador de tornillo | Mueve el material a través del extrusor. | Cada 6 a 12 meses |
Cuchillas de corte | Corta pellets a medida | Cada 3 a 6 meses |
Rodamientos y rodillos | Reduce la fricción y el desgaste. | Cada 6 a 12 meses |
Elementos calefactores | Controla la temperatura de extrusión | Cada 12 meses |
Mejores prácticas para la gestión de repuestos
- Stock de piezas reemplazadas con frecuencia para evitar retrasos en la producción.
- Compre repuestos originales del fabricante de la máquina para mantener la eficiencia.
- Etiquetar y organizar las piezas de repuesto para un fácil acceso cuando se necesitan reemplazos.
Puntos clave para prolongar la vida útil de las máquinas
Mantenimiento diario y semanal Previene la obstrucción y el desgaste mecánico.
Lubricación regular Reduce la fricción y el sobrecalentamiento.
Monitoreo de componentes eléctricos y de calefacción garantiza un funcionamiento consistente.
Reemplazo oportuno de piezas desgastadas evita averías costosas.
Almacenamiento de repuestos esenciales minimiza el tiempo de inactividad.
Un mantenimiento adecuado puede prolongar la vida útil de una máquina de alimentación de peces por varios años.Verdadero
La limpieza rutinaria, la lubricación y la gestión de repuestos ayudan a prevenir averías y mejorar la longevidad de la máquina.
Conclusión
Regular mantenimiento y resolución de problemas adecuada son esenciales para ampliar la vida útil y eficiencia de una máquina de alimentación de peces. Siguiendo las rutinas de limpieza diarias, abordando los problemas comunes con prontitud y gestionando eficazmente las piezas de repuesto, puede... reducir el tiempo de inactividad, minimizar los costos de reparación y maximizar la eficiencia de la producción.
¿Necesita asistencia de mantenimiento o repuestos? ¡Contáctenos hoy mismo!
Nosotros proporcionamos Servicio profesional, repuestos de alta calidad y asesoramiento experto. para mantener su máquina de alimentación de peces funcionando al máximo rendimiento. ¡Contáctenos ahora para obtener asistencia personalizada!
¿Dónde puedo comprar máquinas de alimentación de peces de alta calidad?
Invertir en una máquina de alimentación de peces de alta calidad Es crucial para las empresas acuícolas que buscan producir alimentos nutritivos y rentables. Seleccionar el equipo adecuado implica evaluar fabricantes de renombre, comprender las consideraciones clave de compra y comparar precios y garantías.
Los mejores fabricantes y proveedores
A continuación se presentan algunos fabricantes y proveedores de renombre conocidos por sus máquinas de alimentación de peces de alta calidad:
1. Maquinaria Darin
Fundada en 2011, Darin Machinery es una empresa de alta tecnología especializada en el desarrollo y la venta de máquinas para la producción de alimento para mascotas, máquinas para snacks inflados, máquinas para la producción de barras de granola energéticas y equipos de apoyo. Su línea de extrusión de alimento flotante para peces es ideal para producir alimento flotante para peces en diversos tamaños y formas.
2. Maquinaria para alimentación de peces
Con años de experiencia, Fish Feed Machinery se especializa en la fabricación y el diseño de plantas de alimento para peces y extrusoras personalizadas. Se han ganado una excelente reputación en países como Nigeria, Kenia, Uganda y Sudáfrica.
3. Máquina de alimentación de peces
Esta empresa ofrece una gama de extrusoras de alimento para peces, tanto secas como húmedas, así como líneas completas de producción de alimento para peces. Sus máquinas son reconocidas por su fabricación de calidad y su comercialización fiable.
4. Alibaba
Alibaba es una plataforma global donde numerosos proveedores ofrecen máquinas para alimentar peces. Las opciones varían desde equipos de acuicultura de pequeña escala hasta los de gran escala, lo que permite a los compradores encontrar máquinas que se ajusten a sus necesidades específicas.
5. Hecho en china
Esta plataforma conecta a los compradores con fabricantes chinos que ofrecen diversas máquinas de alimentación de peces, incluidas máquinas de alimentación de peces flotantes y extrusoras de alimentos para mascotas.
6. Maquinaria Yuda
Liyang Yuda Machinery Co., Ltd. es una empresa de alta tecnología especializada en la fabricación de maquinaria para la producción de granos, aceite, piensos y fertilizantes. Ofrece máquinas para el procesamiento de piensos para peces y líneas de producción completas.
Qué buscar al comprar
Al seleccionar una máquina de alimentación de peces, tenga en cuenta los siguientes factores:
1. Capacidad de producción
Ensure the machine's capacity aligns with your production needs. Machines range from small-scale (50–300 kg/h) to large-scale (over 1000 kg/h).
2. Feed Type Compatibility
Determine whether you need to produce floating or sinking feed, as some machines are designed specifically for one type.
3. Nivel de automatización
Decide between manual, semi-automatic, or fully automatic machines based on your labor resources and desired efficiency.
4. Consumo de energía
Consider the machine's energy requirements to ensure they are compatible with your facility's capabilities and budget.
5. Build Quality and Materials
High-quality materials and robust construction enhance machine durability and longevity.
6. Asistencia posventa
Reliable technical support and availability of spare parts are essential for ongoing maintenance.
Comparing Prices and Warranties
Prices and warranties vary among manufacturers and models. Here's a general comparison:
Manufacturer/Supplier | Gama de precios | Garantía |
---|---|---|
Maquinaria Darin | Custom pricing based on specifications | 1 año |
Maquinaria para alimentación de peces | Custom pricing based on specifications | Information not specified |
Máquina de alimentación de peces | Custom pricing based on specifications | Information not specified |
Alibaba Suppliers | $140 – $15,415 depending on model and capacity | Typically 1 year |
Made-in-China Suppliers | Varies widely; specific prices upon request | Varies by manufacturer |
Maquinaria Yuda | Custom pricing based on specifications | Information not specified |
Nota: Prices are indicative and subject to change. It's advisable to contact suppliers directly for the most accurate and up-to-date information.
Conclusión
Selecting the right fish feed machine requires careful consideration of reputable manufacturers, machine specifications, and after-sales support. By evaluating your production needs and comparing options, you can invest in equipment that enhances your aquaculture operations.
Ready to Invest in a High-Quality Fish Feed Machine? Contact Us Today!
We offer expert guidance and a range of top-tier fish feed machines tailored to your specific requirements. Reach out now to explore the best options for your aquaculture business!
Conclusión
Choosing the right fish feed machine can significantly impact fish growth, farm productivity, and cost efficiency. By understanding the various machine types and their functionalities, you can make an informed decision that ensures optimal feed production for your aquaculture needs.
Póngase en contacto con nosotros
Need help selecting the best fish feed machine for your business? Contact us today for expert advice and high-quality equipment!