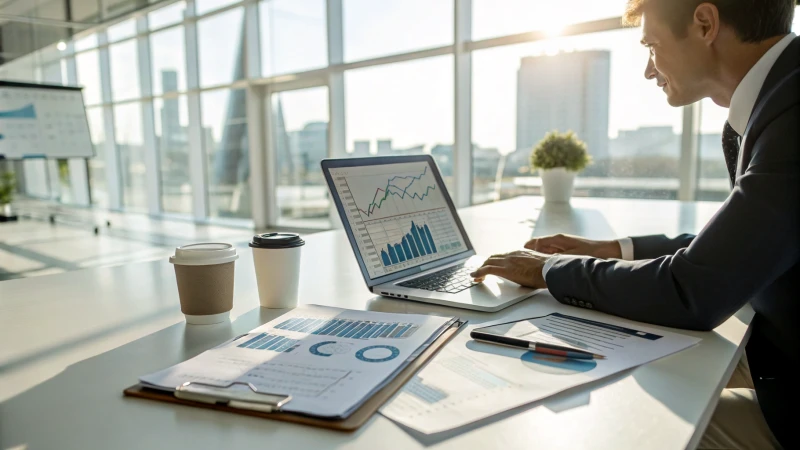
Selecting the right pet food production equipment is crucial for efficiency, product quality, and regulatory compliance. The wrong machinery can lead to production bottlenecks, inconsistent product quality, and increased operational costs. To avoid these pitfalls, manufacturers must consider factors such as product type, production scale, automation level, and regulatory requirements when choosing equipment.
The ideal pet food production equipment depends on factors such as production volume, product type (dry, wet, treats), automation level, and compliance with food safety standards. Key equipment includes mixers, extruders, dryers, packaging systems, and quality control units. A thorough facility assessment, budget analysis, and future scalability should guide the selection process.
Understanding the key aspects of pet food production equipment will help manufacturers optimize efficiency, maintain product integrity, and scale operations effectively. Let’s explore the essential factors and equipment required for an optimized production facility.
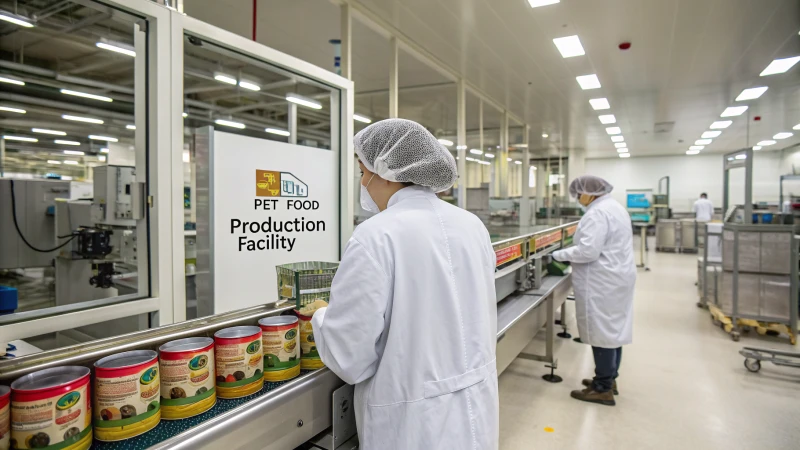
1. Key Factors to Consider When Choosing Pet Food Production Equipment
Before investing in machinery, manufacturers must assess their specific needs based on several critical factors:
1.1. Type of Pet Food Produced
The type of pet food significantly influences the equipment selection:
- Dry Pet Food (Kibble) – Requires extrusion, drying, cooling, and packaging equipment.
- Wet Pet Food (Canned, Pouched, or Fresh) – Requires mixing, cooking, sterilization, and filling machinery.
- Pet Treats & Snacks – Requires forming, baking, cooling, and packaging systems.
- Raw or Freeze-Dried Pet Food – Requires freeze-drying, vacuum sealing, and cold storage solutions.
1.2. Production Capacity & Scalability
- Small-scale production (1-5 tons per hour): Semi-automatic or modular equipment for flexibility.
- Medium-scale production (5-20 tons per hour): Fully automated lines with integrated quality control.
- Large-scale production (20+ tons per hour): High-speed, industrial-grade equipment with minimal downtime.
1.3. Automation & Integration
- Manual or semi-automated systems are suitable for small-batch or artisanal production.
- Fully automated production lines reduce labor costs and improve consistency.
- Smart manufacturing systems with IoT integration allow real-time monitoring and data tracking.
1.4. Compliance with Food Safety Regulations
Pet food production must comply with industry standards such as:
- FDA & AAFCO (U.S.) – Ensures safe and nutritious pet food formulations.
- FSMA (Food Safety Modernization Act) – Requires hazard analysis and critical control points (HACCP).
- BPF (Buenas prácticas de fabricación) – Standardizes hygienic processing conditions.
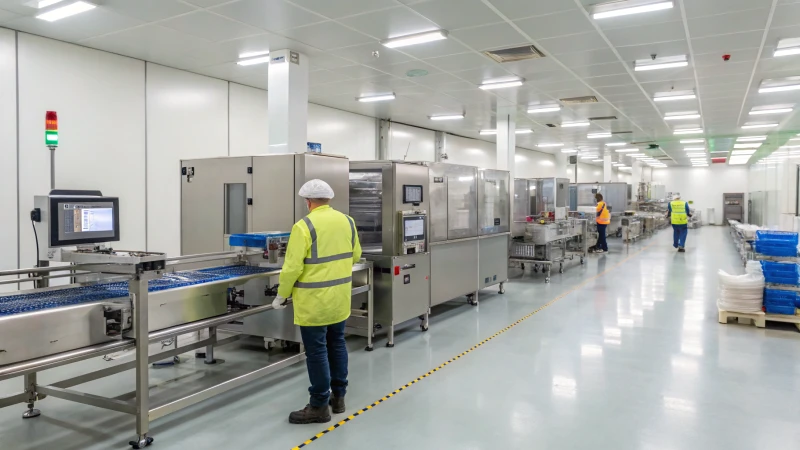
2. Essential Pet Food Production Equipment
A pet food production line consists of multiple stages, from raw material handling to packaging. Below are the critical equipment categories:
2.1. Raw Material Handling & Preparation
Efficient raw material processing ensures a consistent and high-quality final product.
Equipment | Función |
---|---|
Ingredient Storage Silos | Stores bulk raw materials such as grains, proteins, and additives |
Mixers & Blenders | Homogenizes ingredients for uniform consistency |
Grinding & Milling Machines | Reduces raw material size for better processing |
Recommended Equipment for Small vs. Large Facilities
Production Scale | Recommended Equipment |
---|---|
Pequeño | Batch mixers, manual feeders |
Medio | Semi-automated mixing & grinding systems |
Grande | Fully automated ingredient handling & dosing |
2.2. Extrusion & Cooking Equipment
Extrusion is the most common process for making dry pet food (kibble) and some pet treats.
Equipment | Función |
---|---|
Extrusoras monohusillo | Cost-effective but limited in processing flexibility |
Extrusoras de doble husillo | More versatile, capable of handling diverse ingredients |
Steam Cookers | Used in wet pet food production to ensure proper cooking |
Comparison of Extruders
Característica | Extrusora monohusillo | Extrusora de doble husillo |
---|---|---|
Versatilidad | Bajo | Alta |
Eficiencia energética | Alta | Moderado |
Variedad de productos | Limitado | Broad |
Coste inicial | Bajo | Más alto |
2.3. Drying & Cooling Systems
After extrusion, kibble must be dried and cooled properly to maintain shelf stability.
Equipment | Función |
---|---|
Belt Dryers | Gradually removes moisture for even drying |
Rotary Drum Dryers | High-speed drying for large-scale production |
Cooling Conveyors | Prevents condensation and spoilage |
Drying Process Parameters
Tipo de comida para mascotas | Ideal Drying Temperature | Moisture Level After Drying |
---|---|---|
Croquetas | 90-130°C | 8-10% |
Semi-Moist Treats | 60-90°C | 15-20% |
2.4. Coating & Flavoring Systems
To enhance taste and nutritional value, pet food is often coated with fats, flavors, and supplements.
Equipment | Función |
---|---|
Fat Coaters | Sprays fat or palatants for improved taste |
Vitamin & Supplement Applicators | Ensures even distribution of nutrients |
2.5. Packaging & Sealing Equipment
Packaging is vital for maintaining freshness and extending shelf life.
Equipment | Función |
---|---|
VFFS Machines | Forms, fills, and seals bags for dry pet food |
Can & Pouch Filling Machines | Used for wet food |
Vacuum Sealers | Preserves freeze-dried pet food |
Packaging Considerations
- Barrier materials prevent oxygen and moisture penetration.
- Resealable packaging enhances consumer convenience.
- Automated labeling ensures compliance with regulatory information.
3. Quality Control & Food Safety Measures
Maintaining high product quality is essential for consumer trust and regulatory compliance.
Equipment | Función |
---|---|
Metal Detectors | Detects foreign objects in the food |
X-Ray Inspection Systems | Identifies non-metallic contaminants |
Moisture Analyzers | Ensures optimal water content |
Food Safety Compliance Checklist
✔️ Ingredient traceability
✔️ Cross-contamination prevention
✔️ Sanitation and hygiene protocols
✔️ Regular equipment maintenance
4. Cost Analysis & Budget Considerations
Investing in pet food production equipment requires careful budget planning.
Tipo de equipo | Gama de costes | Best for |
---|---|---|
Mixing & Grinding Systems | $10,000 - $100,000 | Small to large-scale production |
Extrusoras | $50,000 - $500,000 | Dry pet food and treats |
Drying & Cooling Systems | $30,000 - $300,000 | High-speed production |
Máquinas de envasado | $20,000 - $250,000 | Wet and dry pet food |
Quality Control Systems | $10,000 - $150,000 | Ensures compliance |
5. Conclusion: Choosing the Right Equipment for Your Facility
Selecting the ideal pet food production equipment depends on production scale, product type, and automation needs. For dry pet food, extruders, dryers, and coating systems are essential. Wet pet food production requires cookers, canning, and sterilization equipment. Advanced packaging and quality control systems ensure food safety and longevity. Conducting a thorough facility assessment and scalability analysis will help in making the best investment decision.
Need Help Selecting the Right Pet Food Equipment?
Contact us today for expert recommendations and customized production solutions! 🚀