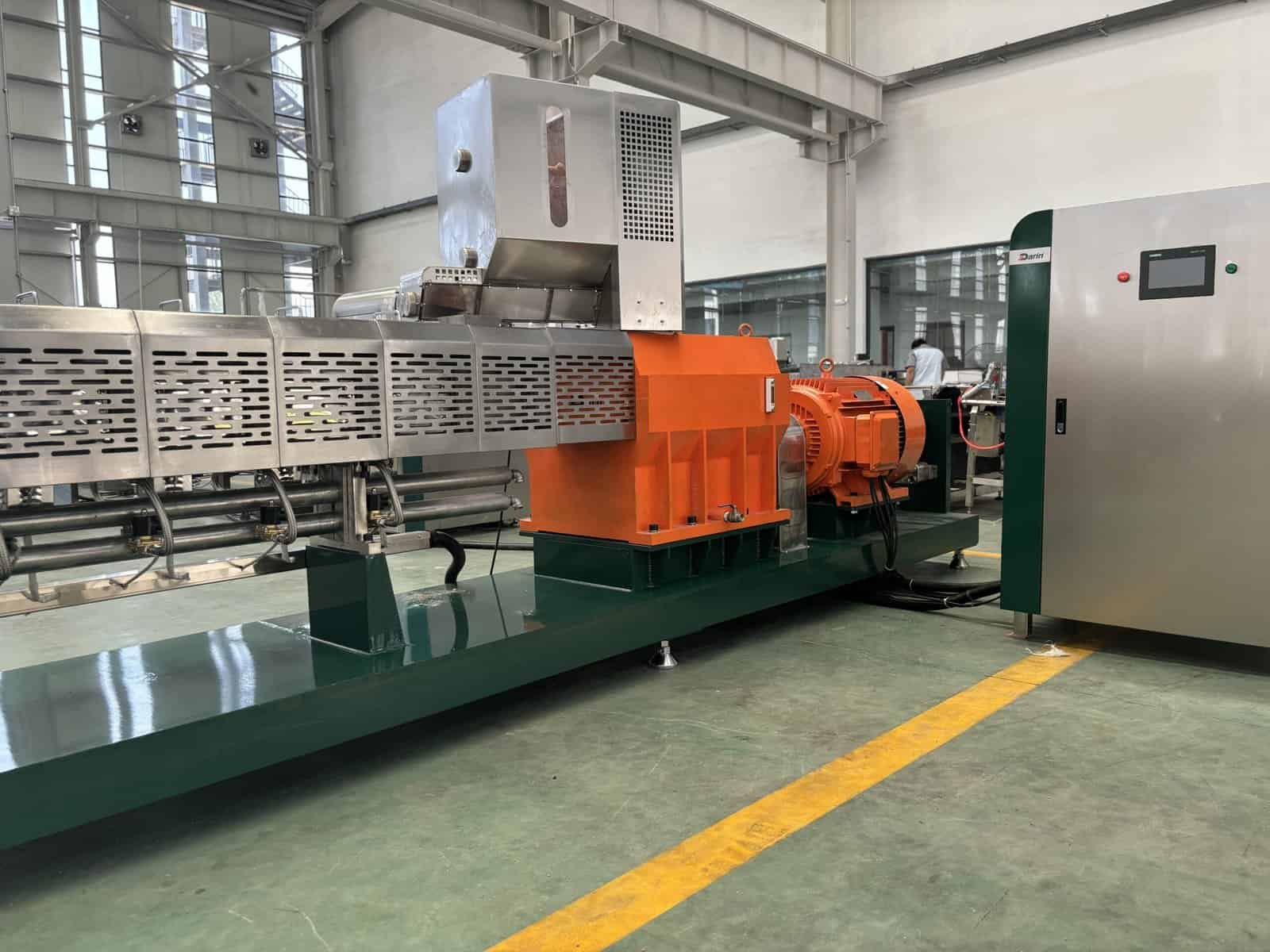
Twin-screw extruders are powerful and versatile machines used across industries—from pet food and snacks to bioplastics and chemical compounding. However, without knowing the real cost components and differences among models, buyers often face overbudgeting, low ROI, or mismatch in capacity. Selecting the wrong extruder can stall operations, inflate energy costs, or fail quality audits. In this article, we’ll walk you through how much a twin-screw extruder costs, what factors affect pricing, and how to make the most cost-effective investment.
The cost of a twin-screw extruder can range from $15,000 to over $500,000 depending on its size, output capacity, configuration, automation level, application (e.g., pet food, plastics, or pharmaceutical), and origin (e.g., China vs. Europe). Entry-level lab-scale models start from $15,000–$30,000, mid-range food-grade extruders cost $50,000–150,000, while high-capacity industrial extruders can exceed $300,000.
To fully understand the costs and make a sound investment, let’s examine the different cost tiers, key price drivers, and how Darin Machinery helps global customers balance budget with performance.
Twin-screw extruders cost the same across all industries and applications.Falso
The cost of twin-screw extruders varies significantly depending on application, capacity, build quality, and control systems.
Key Factors That Determine Twin-Screw Extruder Cost
Choosing a twin-screw extruder is not just about the base machine. You need to consider what you’re producing, the level of automation required, the expected lifespan, and regional after-sales service. The cost of ownership also includes energy consumption, maintenance, and spare parts availability.
🔧 1. Application & Material Type
Tipo de aplicación | Typical Extruder Cost Range (USD) | Notas |
---|---|---|
Pet Food & Animal Feed | $40,000 – $150,000 | Requires food-grade stainless steel, precise control for nutrition and texture |
Snack Food (e.g. puffs) | $30,000 – $120,000 | Smaller capacity, needs accurate shaping |
Compuestos plásticos | $60,000 – $500,000+ | Needs precise temperature, torque, and wear-resistant barrels |
Pharmaceutical | $100,000 – $400,000 | GMP-compliant, high precision, often lab-scale |
Plásticos biodegradables | $80,000 – $250,000 | High temperature and specialized screw design |
Lab Research | $15,000 – $50,000 | Compact, experimental, variable L/D ratio |
Explanation: Machines for pet food, snacks, or aquafeed must comply with food hygiene regulations, use food-grade components, and integrate with drying and flavoring lines. Plastic or pharma extruders must handle corrosive or temperature-sensitive materials.
📊 2. Output Capacity
Capacidad de salida (kg/h) | Machine Scale | Estimated Cost Range (USD) |
---|---|---|
10–50 kg/h | Escala de laboratorio | $15,000 – $50,000 |
100–300 kg/h | Pilot/Small Batch | $35,000 – $90,000 |
300–1000 kg/h | Mid-Production | $70,000 – $180,000 |
1000–3000+ kg/h | Industrial Scale | $180,000 – $500,000+ |
Higher capacity machines are typically longer (higher L/D ratio), use more advanced gearbox systems, and require robust drive motors. Output consistency also depends on the screw design and control systems.
🔩 3. Screw Configuration & Barrel Design
- Co-rotating vs. Counter-rotating: Co-rotating is more common in food and plastic extrusion due to better mixing.
- Modular Barrel: Modular barrels increase cost but provide flexibility for different recipes and zones (e.g., feeding, kneading, venting, cooling).
- L/D Ratio (Length/Diameter): Longer L/D ratios allow more processing time and higher product quality but raise cost.
⚙️ 4. Automation, Control System & Sensors
Característica | Additional Cost (USD) |
---|---|
Basic Manual Control | Included in base price |
PLC + HMI Touchscreen | + $3,000 – $10,000 |
SCADA/Remote Monitoring | + $5,000 – $20,000 |
Automatic CIP System | + $5,000 – $15,000 |
AI-based Process Control | + $10,000 – $30,000 |
Automation not only reduces labor costs but ensures product consistency—especially important in high-value industries like pharmaceuticals or premium pet food.
🧰 5. Origin and Brand Reputation
- China: Offers cost-effective extruders with competitive specs. Prices typically 20–50% lower than European brands.
- Europe (e.g. Clextral, Bühler): Known for durability, precision engineering, and long-term reliability. Prices start around \$200,000.
- USA/Japan: High-quality with strong technical support, often priced similarly to European suppliers.
Darin Machinery, as a leading Chinese manufacturer, offers world-class twin-screw extruders at 30–50% lower cost than Western competitors, while maintaining ISO, CE, and FDA-compliant designs.
Breakdown of a Typical Mid-Range Food Extruder
Here’s a breakdown for a Darin DSE85 twin-screw extruder used in pet food production (300–800 kg/h):
Componente | Estimación de costos (USD) |
---|---|
Base Extruder Body | $50,000 |
Twin-Screw System (85mm diameter) | $12,000 |
Electrical Control Panel (PLC) | $8,000 |
Heating and Cooling System | $10,000 |
Stainless Steel Frame & Covers | $5,000 |
Optional Auto-Clean System | $7,000 |
Spare Parts Package | $5,000 |
Total Estimated Cost | $97,000 |
Energy Consumption and Operating Costs
- Power requirement: 75–110 kW for medium extruders
- Electricity cost (per hour): Approx. \$8–12/hour (based on global industrial rate)
- Annual maintenance: 3–5% of capital cost (approx. \$3,000–5,000/year)
- Expected lifespan: 8–15 years with proper maintenance
How to Choose the Right Twin-Screw Extruder for Your Budget
Here are some practical tips:
- Define Product Requirements: Do you need floating, sinking, or chewy pet food? Do you need fiber retention for functional snacks?
- Select Output Scale Wisely: Avoid overpaying for capacity you won’t use. Start small if needed.
- Choose Modular Designs: If product variety is key, modular barrels and screw elements are a wise investment.
- Compare Offers Side-by-Side: Request quotations with detailed BOM (Bill of Materials).
- Consider Total Cost of Ownership: Don’t forget power costs, operator training, spare parts access, and warranty.
Darin Machinery’s Advantage in Cost-Performance Balance
At Darin Machinery, we’ve been helping global brands and startups alike to:
- Customize twin-screw extruders for pet food, snacks, cereals, and specialty feed
- Lower capital investment by 30–50% without compromising quality
- Provide full turnkey lines including mixers, dryers, flavorers, and packaging machines
- Export CE- and FDA-compliant machines to over 70 countries
Notable Clients Using Our Twin-Screw Extruders
País | Application Field |
---|---|
India | Dog kibble production |
Vietnam | Cereales para el desayuno |
Colombia | Floating fish feed |
Italy | Functional pet treats |
These partners chose Darin not only for competitive pricing but for service, engineering support, and long-term reliability.
Reflexiones finales
Understanding the real cost of a twin-screw extruder requires more than checking a catalog price. It’s about evaluating your production scale, application demands, and future growth. Whether you're launching a new pet food line or upgrading your industrial compounder, the right machine should be a profit generator—not a cost sink.
Ready to Invest in a Twin-Screw Extruder?
Darin Machinery is your trusted expert in high-performance, cost-efficient extrusion solutions. Contact us today to get a free quotation tailored to your production goals, product type, and budget.
📩 Contact Darin Machinery Now:
Correo electrónico: darin4@darin.cn
Sitio web: www.darin.cn | www.petreatsmachine.com
Let’s build your extrusion line with precision, performance, and profitability.