Choosing the right food extruder can feel like solving a complex puzzle. But with the right guidance, it’s a game-changer for your production line.
To choose the right food extruder, consider your production capacity, desired product type, and energy efficiency needs. Analyze single-screw versus twin-screw extruders based on your specific requirements and operational goals.
When I first started exploring food extruders, I was overwhelmed by the sheer variety and technical jargon. I remember standing in a bustling factory, trying to discern the subtle differences between single-screw and twin-screw models, and feeling like I was learning a new language. Over time, I realized that understanding ingredient versatility and staying updated with the latest extrusion technology were key. These insights not only helped me make informed choices but also improved my production efficiency dramatically. So, while the technical specs are crucial, personal experience and adaptability play a huge role in selecting the perfect extruder for your needs.
Twin-screw extruders are more energy efficient than single-screw ones.Falso
Energy efficiency depends on specific use cases, not screw type.
Single-screw extruders are suitable for lower production capacities.Verdadero
They are generally used for simpler, smaller-scale productions.
What Are the Key Differences Between Single-Screw and Twin-Screw Extruders?
Diving into the world of extruders, I realized the choice between single-screw and twin-screw models can make or break your production goals. Let's explore why.
Single-screw extruders are simpler and cost-effective, ideal for uniform material processing. Twin-screw extruders offer better mixing, flexibility, and are suited for complex formulations or materials requiring precise control.
Design and Functionality
When I first started exploring extruder technologies, I remember being quite overwhelmed. The single-screw extruder, with its straightforward design, seemed almost comforting. It's like the trusty old car that rarely breaks down—simple and cost-effective. This type thrives in settings where you need consistent results with minimal fuss, perfect for straightforward applications.
But then there's the twin-screw extruder—a bit like the multi-tool of extrusion equipment. With its two intermeshing screws, it offers enhanced control over mixing and kneading, making it indispensable for more complex tasks. If you're dealing with intricate formulations or sensitive materials, this is your go-to.
Processing Capabilities
Reflecting on my journey through various production lines, I found myself often comparing these two types across several key features:
Característica | Un solo tornillo | Tornillo doble |
---|---|---|
Mixing Quality | Básico | Alta |
Flexibility | Limitado | Excelente |
Material Range | Narrow | Wide |
Mixing Quality: For those simpler recipes, a single-screw extruder does just fine. But when I needed to ensure every little additive was perfectly blended, the twin-screw's superior mixing quality made all the difference.
Flexibility: In one project, I had to switch between materials of varying viscosities. That's when the adaptability of the twin-screw really shone, handling everything I threw at it with ease.
Applications and Suitability
In my line of work, I've seen how each extruder fits into its niche:
- Extrusoras monohusillo: Ideal for tasks like producing plastic films or basic pet food items—where you don't need fancy bells and whistles.
- Extrusoras de doble husillo: These are the heavy hitters for complex pet food formulations1 where precision and uniformity are non-negotiable.
Operational Considerations
Every time I evaluate machinery costs, I'm reminded of the budget-friendly nature of single-screw models. They’re a great fit for smaller operations that need to keep expenses in check.
But when it comes to large-scale or specialized manufacturing2, where maintaining consistency is key, investing in a twin-screw system pays off with its enhanced control capabilities.
Single-screw extruders are more cost-effective than twin-screw.Verdadero
Single-screw models are cheaper to purchase and maintain.
Twin-screw extruders have limited flexibility in material handling.Falso
Twin-screw extruders offer excellent flexibility for various materials.
How Does Production Scale Impact Extruder Selection?
Ever wondered how the scale of your production line can influence the type of extruder you need?
Production scale impacts extruder selection by dictating the required capacity, type, and specifications of the machinery. Larger scales demand robust, high-capacity extruders, while smaller operations might prioritize flexibility and cost-efficiency.
Understanding Production Volume Needs
When I first started out in the industry, the sheer number of decisions I had to make was overwhelming. One thing that quickly became clear is how crucial understanding production volume is when selecting an extruder. High-volume operations, like some of the large-scale pet food manufacturers I've worked with, often need industrial-scale extruders that can run continuously without a hitch. This is because efficiency is key; any downtime could mean significant losses.
For instance, large-scale manufacturers3 in the pet food industry often opt for twin-screw extruders. These machines are like workhorses with their high throughput capabilities—think of them as the marathon runners in the world of extrusion.
Types of Extruders for Different Scales
Single-Screw vs. Twin-Screw Extruders
Característica | Extrusora monohusillo | Extrusora de doble husillo |
---|---|---|
Rendimiento | Moderado | Alta |
Flexibility | Limited to specific product types | Versatile with wide product range |
Coste | Generally lower | Higher initial investment |
Choosing between a single-screw and a twin-screw extruder can feel a bit like deciding between a reliable old sedan and a flashy sports car. Each has its perks.
A smaller facility might lean towards a single-screw extruder for its lower costs and simpler operation. It's like getting a car that's perfect for city driving if you're not planning to go cross-country.
Evaluating Technological Advancements
Technology in extrusion is evolving faster than I can keep up sometimes! Modern extruders come with features that can dramatically boost production efficiency and product quality. If your production is scaling up, investing in tecnologías avanzadas4 like digital monitoring systems and energy-efficient motors can be a game changer. These improvements aren't just bells and whistles—they can really help reduce waste and keep product quality consistent.
Key Considerations for Emerging Markets
I've seen firsthand how emerging markets offer exciting opportunities for growth. When expanding into these areas, scalability becomes vital. You need to strike a balance between high-capacity equipment and flexibility for diverse product lines. For example, companies eyeing Southeast Asia might benefit from modular extruder designs5 that can easily be upgraded as demand increases.
Flexibility vs. Capacity
This balance between flexibility and capacity reminds me of my early days working with small, nimble teams versus larger, more robust ones. If you're anticipating rapid growth or frequent product changes, you might want to prioritize modular systems that can be easily adapted or expanded.
At the end of the day, choosing the right extruder boils down to understanding your specific production needs and future growth plans. It's about finding the right tool for the job—one that fits seamlessly into your vision for success.
Twin-screw extruders have higher throughput than single-screw.Verdadero
Twin-screw extruders are designed for high-volume operations, offering greater throughput.
Single-screw extruders are more costly than twin-screw ones.Falso
Single-screw extruders generally have a lower initial cost compared to twin-screw models.
Why Should Energy Efficiency Matter When Selecting an Extruder?
Choosing an extruder isn’t just about power; it’s about transforming your manufacturing into an eco-friendly powerhouse.
Energy efficiency in extruders is crucial because it reduces operational costs, minimizes environmental impact, and enhances productivity. Efficient extruders consume less energy while maintaining output quality, making them essential for sustainable manufacturing.
Cost Savings Through Energy Efficiency
Energy-efficient extruders consume less power, leading to reduced electricity bills. Over time, these savings can be substantial. A more efficient machine might initially cost more, but the reduced energy consumption can offset the initial investment.
For instance, if a standard extruder consumes 200 kWh daily and an energy-efficient model consumes only 150 kWh, at $0.10 per kWh, the savings would amount to $5 daily or over $1,800 annually.
Impacto medioambiental
Reducing energy consumption directly correlates with lowering carbon emissions. By choosing energy-efficient extruders, companies contribute to environmental sustainability by reducing their carbon footprint. This aligns with global initiatives to combat climate change.
Investing in energy-efficient technology6 can bolster a company's reputation as environmentally responsible, potentially attracting more eco-conscious clients and partners.
Improved Productivity
Energy-efficient extruders often incorporate advanced technology that enhances production speed and quality. This ensures that businesses can meet increasing demand without compromising quality or efficiency.
These extruders are designed to operate at optimal levels with minimal waste. They can quickly adjust to different materials and production requirements, ensuring consistent product quality.
Factors to Consider When Selecting an Extruder
- Energy Consumption Ratings: Examine the energy consumption ratings provided by manufacturers. Models with higher energy efficiency ratings can lead to substantial cost savings over time.
- Load Capacity and Output: An extruder should be capable of handling the required production volume without excessive energy use.
- Integración de la tecnología: Modern extruders offer features like real-time monitoring and automated adjustments, enhancing eficacia operativa7.
Aplicación de las mejores prácticas
- Regular maintenance ensures that machines operate at peak efficiency—think of it as a health check-up for your machines.
- Staff training on efficient operation techniques helps squeeze every bit of efficiency from your machinery.
- Monitoring systems that track energy use can identify areas for improvement, helping to optimize overall plant efficiency.
By prioritizing energy efficiency in extruder selection, companies not only benefit financially but also contribute positively to broader environmental goals. This approach reflects a commitment to sustainable practices that resonate with stakeholders across industries.
Energy-efficient extruders save $1,800 annually in electricity.Verdadero
By reducing daily consumption from 200 kWh to 150 kWh at $0.10 per kWh.
All energy-efficient extruders have higher initial costs.Falso
While often true, some efficient models may not have higher upfront costs.
What Maintenance Factors Should Be Considered for Long-Term Use?
I still remember the first time I had to deal with an unexpected machinery breakdown—it was a wake-up call that maintenance isn't just an option; it's essential.
Key maintenance factors for long-term use include regular inspections, preventive maintenance, staff training, and adherence to manufacturer guidelines. These practices help ensure optimal performance and longevity of equipment.
Inspecciones regulares
Regular inspections are like those health check-ups we all dread but know we need. They’re the backbone of any effective maintenance strategy. Imagine catching a leak before it turns your day upside down or spotting unusual noises before they become an expensive melody of disaster. Using inspection checklists8 ensures thoroughness and consistency.
Preventive Maintenance
Preventive maintenance is my peace of mind in action. It’s like cleaning the gutters before the storm hits. This involves routine activities like lubrication and cleaning to keep everything running smoothly. Scheduling these tasks based on usage data9 can be a game-changer, optimizing both timing and efficiency.
Staff Training
Here’s a little story: once, a newly trained team member spotted an issue that I missed. Properly trained staff are invaluable. Their training should cover everything from equipment operation to emergency protocols. Continuous learning ensures they stay ahead of the curve with the latest avances tecnológicos10.
Adherence to Manufacturer Guidelines
Adhering to manufacturer guidelines is like following a recipe from your grandma—stray too far, and you might end up with something unrecognizable. These guidelines ensure you maintain warranty validity and optimal machinery performance. Always consult the manufacturer's manual11 before planning any maintenance tasks.
Using Advanced Tools and Techniques
Advanced maintenance techniques have been my secret weapon. Predictive maintenance, for instance, uses sensors and data analytics to catch problems before they happen. Investing in predictive tools12 not only saves me from unexpected headaches but also significantly cuts costs over time.
Maintenance Documentation
Keeping detailed records of all maintenance activities is like keeping a diary of your machinery’s life. This documentation helps track the equipment's history and spot patterns that could indicate future issues. A well-maintained maintenance log13 is not just paperwork; it’s your go-to for audits and compliance checks.
Maintenance Factor | Key Considerations |
---|---|
Inspecciones regulares | Checklists, frequency, thoroughness |
Preventive Maintenance | Scheduling, task optimization |
Staff Training | Comprehensive programs, continuous updates |
Adherence to Guidelines | Compliance with manufacturer's instructions |
Advanced Tools & Techniques | Predictive maintenance tools, cost analysis |
Maintenance Documentation | Record-keeping, audit preparedness |
Regular inspections prevent costly repairs.Verdadero
Regular inspections identify issues early, avoiding expensive repairs.
Ignoring manufacturer guidelines voids warranties.Verdadero
Following guidelines maintains warranty validity and proper operation.
How Do Extruder Features Influence Product Quality?
Ever wondered how the nuts and bolts of an extruder can make or break your product quality? Let's dive into the details!
Extruder features like screw design, barrel length, and temperature control play critical roles in determining product quality by affecting factors such as uniformity, consistency, and material properties.
The Role of Screw Design in Product Quality
I remember the first time I watched a twin-screw extruder in action. It was mesmerizing to see how the screw design could transform raw ingredients into a uniform, well-textured product. Just like a master chef tweaking recipes to perfection, a well-designed screw ensures consistent material flow, enhancing product uniformity14 and texture. Twin-screw extruders are particularly fascinating because they can handle complex formulations with ease, offering superior mixing compared to their single-screw counterparts. It’s like comparing a hand mixer to a full-on stand mixer—the latter can just do so much more!
Característica | Impact on Quality |
---|---|
Single-screw design | Suitable for simple processes with limited mixing. |
Twin-screw design | Offers superior mixing and temperature control. |
Barrel Length and Its Impact
The length of the extruder barrel is another game-changer. Imagine trying to bake a cake in half the time—it just doesn't work well. Similarly, a longer barrel allows the material to be exposed to heat and shear forces gradually, ensuring thorough mixing and homogeneity. But, just as over-baking can ruin a dessert, overextended exposure15 can degrade sensitive materials. I’ve learned the hard way that balance is key.
Temperature Control: A Crucial Parameter
Temperature control is like the unsung hero of extrusion. Too hot, and you might end up with a mess; too cold, and things just don’t come together properly. I’ve seen advanced extruders that boast multiple heating zones, ensuring precise temperature management. This is crucial in preventing overheating and ensuring that food products are cooked just right.
Operational Parameters: Feed Rate and Pressure
Finally, let's talk about feed rate and pressure—two factors that need constant attention. I've witnessed how high feed rates can lead to incomplete mixing while low rates might cause over-processing. It's all about striking the right balance to achieve that calidad constante del producto16 everyone’s after.
Twin-screw extruders offer better mixing than single-screw.Verdadero
Twin-screw extruders provide superior mixing capabilities due to their design.
Longer extruder barrels always improve product quality.Falso
While longer barrels enhance mixing, they can degrade sensitive materials.
What Trends in Extrusion Technology Should You Be Aware Of?
Navigating the ever-evolving world of extrusion technology can be quite the adventure, especially with groundbreaking trends redefining the landscape.
Key trends in extrusion technology include the integration of artificial intelligence for process optimization, the development of sustainable materials, and advancements in digital twin technology for enhanced operational efficiency and quality control.
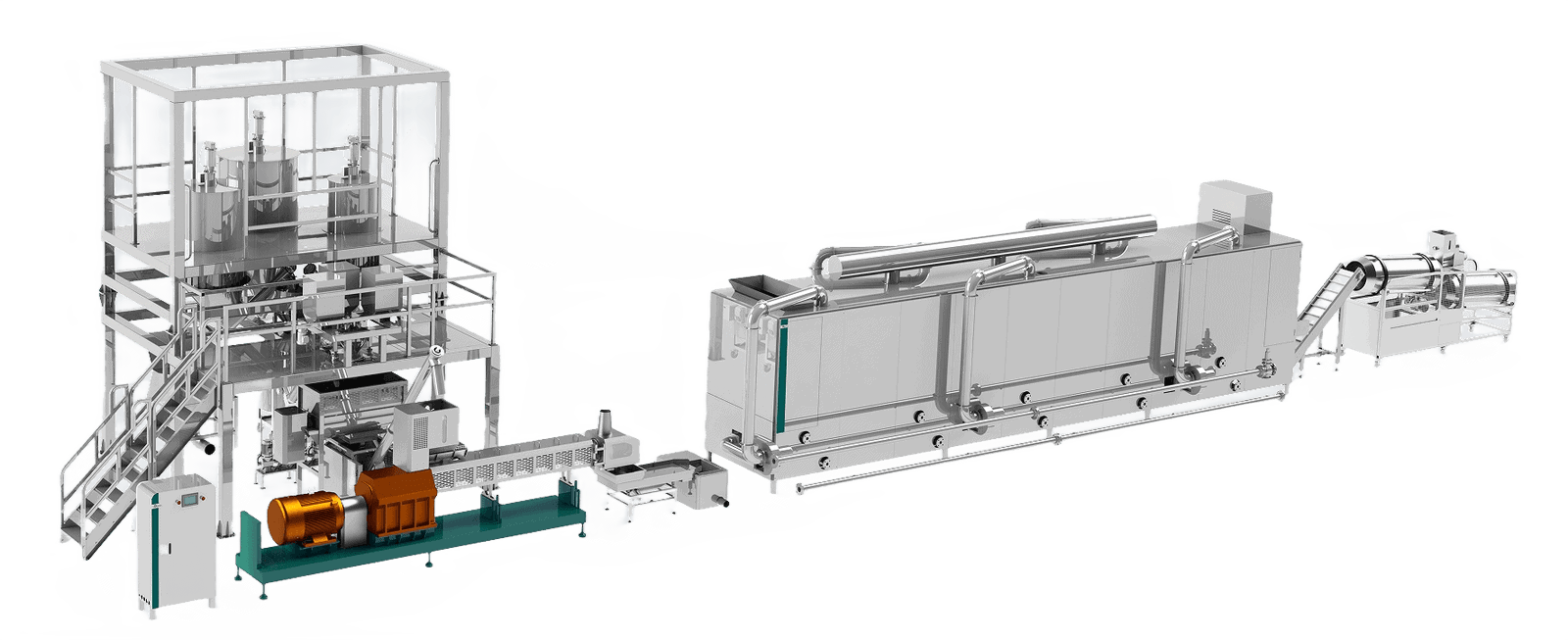
Artificial Intelligence in Extrusion Processes
Picture this: a world where machines can predict their own hiccups before they happen. That’s the magic of Artificial Intelligence (AI) in extrusion technology. I remember when I first heard about AI being able to foresee system failures—it was like peering into the future! With AI keeping tabs on things like temperature and pressure, it’s like having an extra set of hands ensuring everything runs smoothly and efficiently. Plus, it means less downtime, which is always a win in my book.
Integrating AI helps in predicting wear and tear of machinery parts, leading to timely replacements and avoiding unexpected breakdowns. This technology not only enhances eficacia operativa17 but also ensures high-quality output by minimizing human error.
Sustainable Materials and Green Extrusion
The push towards sustainability isn't just a trend; it's a revolution that’s taken over our industry. Every time I see new biodegradable materials being developed, it feels like we’re taking another step towards a greener planet. I recall the first time I worked with bioplastics made from renewable resources—it was a game changer. These materials not only help us meet those tricky regulatory standards but also make me proud to cater to eco-conscious consumers.
These materials not only help in meeting regulatory requirements but also cater to environmentally conscious consumers. Companies are investing in research to develop innovative materials that are both durable and eco-friendly. This shift towards green extrusion practices18 is becoming a standard across industries.
Digital Twin Technology
Digital twin technology is like having a crystal ball for your machinery. It allows us to create virtual replicas of physical processes, meaning we can test out new ideas without disrupting our production lines. I’ve found that using digital twins helps in making better decisions about equipment performance and improvements. It’s particularly handy for remote monitoring, especially in today’s globalized manufacturing world.
Digital twins facilitate better decision-making by providing insights into equipment performance and potential improvements. They also enable remote monitoring and management, which is crucial in today's global manufacturing landscape. The adoption of digital twin solutions19 is enhancing precision and efficiency in extrusion operations.
Table: Key Trends in Extrusion Technology
Tendencia | Descripción |
---|---|
Artificial Intelligence | AI aids in monitoring and optimizing extrusion processes |
Materiales sostenibles | Focus on eco-friendly, biodegradable, and recyclable materials |
Digital Twin Technology | Virtual modeling for enhanced process analysis and optimization |
Staying on top of these trends isn’t just about keeping up; it’s about leading the charge in innovation and maintaining that ever-important competitive edge.
AI can predict extrusion system failures.Verdadero
AI analyzes data to foresee failures, enabling preventive maintenance.
Bioplastics are not used in extrusion processes.Falso
Bioplastics, derived from renewables, are increasingly used in extrusion.
Conclusión
Choosing the right food extruder involves assessing production capacity, product type, and energy efficiency, with options like single-screw or twin-screw models tailored to specific operational needs.
-
Explore how twin-screw extruders enhance product quality with complex ingredient mixes. ↩
-
Learn about precision benefits of twin-screw extruders in large-scale productions. ↩
-
Twin-screw extruders excel in high-volume production due to their efficiency and flexibility, making them ideal for large-scale operations. ↩
-
Advanced technologies enhance efficiency by optimizing processes and reducing waste, crucial for scaling operations. ↩
-
Modular designs allow for easy upgrades and adaptation, ideal for growing businesses needing flexible production solutions. ↩
-
Explore how energy-efficient technologies reduce operational costs and support sustainable practices. ↩
-
Learn how real-time monitoring enhances operational efficiency and reduces waste. ↩
-
Checklists provide a structured approach to inspections, ensuring no aspect is overlooked. ↩
-
Optimizing task timing based on usage enhances efficiency and prolongs equipment life. ↩
-
Staying updated with advancements ensures staff use best practices. ↩
-
Manuals contain specific instructions crucial for proper upkeep. ↩
-
Predictive tools help prevent unexpected failures and reduce costs. ↩
-
Logs are essential for tracking history and ensuring compliance. ↩
-
Understanding screw design benefits can help improve mixing efficiency and product texture. ↩
-
This link explains the trade-offs in barrel length for optimal material processing. ↩
-
Balancing feed rate and pressure ensures consistent product quality. ↩
-
Explore how AI enhances operational efficiency by predicting system failures and optimizing processes. ↩
-
Learn about the environmental and regulatory benefits of adopting green extrusion practices. ↩
-
Discover how digital twins improve manufacturing precision and decision-making. ↩