In today’s rapidly evolving pet food market, manufacturers face increasing pressure to produce high-quality, nutritionally balanced products efficiently and cost-effectively. One of the major pain points is inconsistent product quality and limited flexibility in handling various ingredients. These limitations not only affect productivity but also hinder a company’s ability to meet market demands and nutritional compliance. However, the solution lies in a powerful and versatile piece of equipment—the twin-screw pet food extruder—which enables precise control, higher production rates, and greater flexibility in processing a wide variety of pet food types. This article provides a complete guide on what it is, how it works, and why it's indispensable.
A twin-screw pet food extruder is an industrial-grade machine used to cook, shape, and expand pet food ingredients through a continuous process involving two intermeshing screws. It offers excellent mixing, precise control of temperature and moisture, and consistent output quality, making it ideal for producing kibble, treats, semi-moist products, and specialized nutrition formulations.
This guide will help you understand why the twin-screw extruder is the heart of modern pet food manufacturing. Whether you're an R\&D team looking to develop new formulations or a large-scale producer seeking consistency and scalability, this machine is the answer. Keep reading to uncover the engineering details, production metrics, and real-world applications.
Twin-screw extruders are only suitable for high-moisture wet pet food production.Falso
Twin-screw extruders can produce a wide range of pet food types including dry kibble, semi-moist, and treats due to their excellent control over temperature, pressure, and moisture.
How Does a Twin-Screw Pet Food Extruder Work?
Twin-screw extruders work by continuously pushing pet food raw materials through a barrel using two rotating screws. These screws operate in tandem (co-rotating) to:
- Mix dry powders and wet ingredients thoroughly
- Apply heat via mechanical energy and external heaters
- Gelatinize starch, denature protein, and create product texture
- Shape and expand the product as it exits the die
Core Components
Componente | Descripción |
---|---|
Sistema de alimentación | Supplies raw materials into the extruder (can be gravimetric or volumetric) |
Twin screws | Intermeshing co-rotating screws for mixing, shearing, and conveying |
Barrel heating | Temperature-controlled zones for cooking and stabilization |
Die and knife | Shapes and cuts the extruded product to desired size |
Control panel | PLC or HMI interface for recipe and parameter control |
Functional Flowchart
Paso | Process Activity | Technical Features |
---|---|---|
Raw Material Input | Ground grains, proteins, fats, vitamins enter | Preconditioner optional for moistening and pre-cooking |
Transporte | Twin-screws convey and mix materials | Variable pitch screws for different shear intensities |
Cocinar | Heat and pressure applied inside barrel | Temperature: 90°C – 180°C; Pressure: 10–30 bar |
Extrusión | Product forced through die plate | High-speed rotary cutter controls final shape and length |
Drying/Cooling | Removes moisture post-extrusion | Final moisture < 10%; reduces microbial activity |
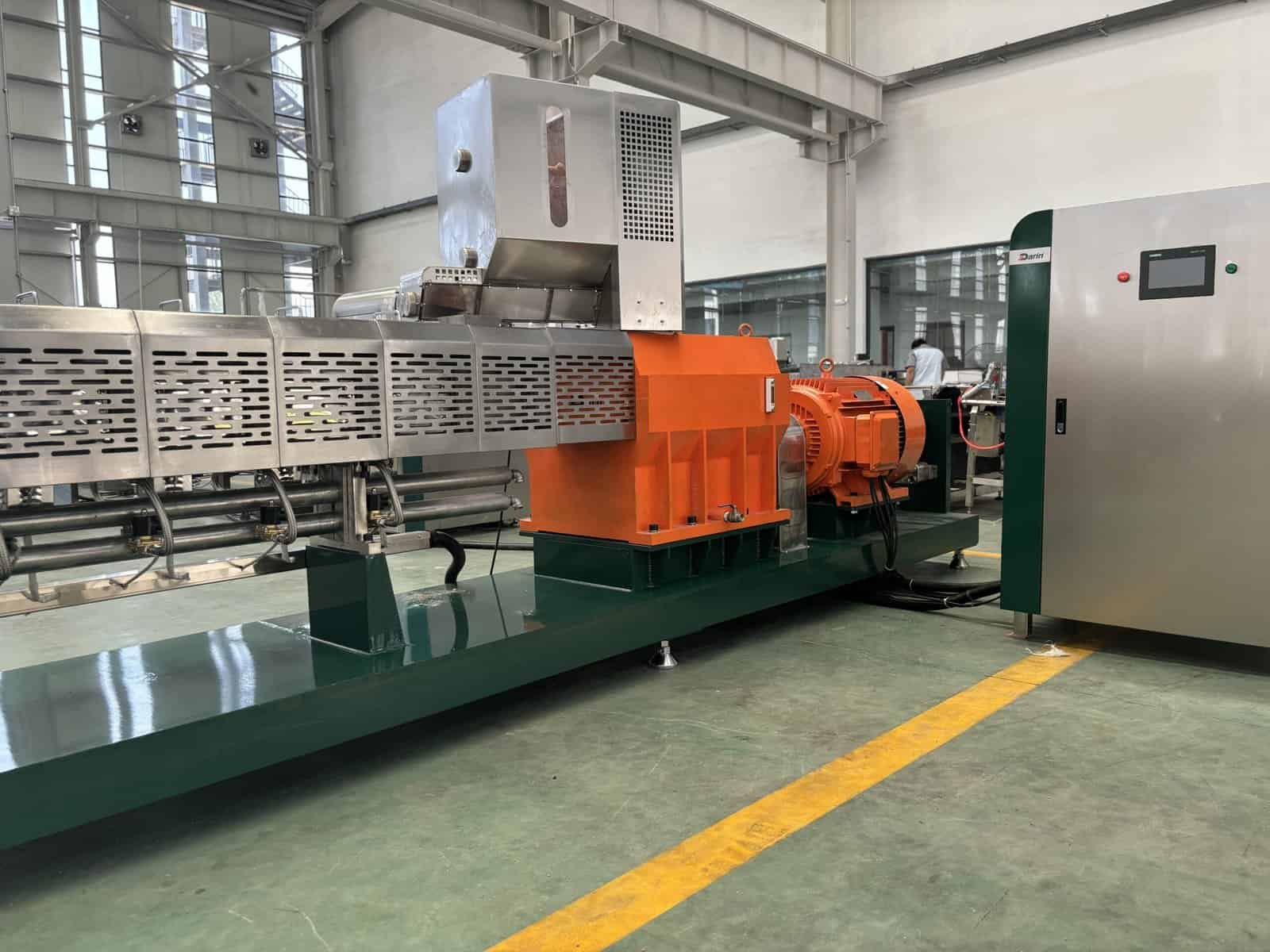
Advantages Over Single-Screw Extruders
Característica | Extrusora de doble husillo | Extrusora monohusillo |
---|---|---|
Flexibilidad de ingredientes | Excellent (handles high fat, fiber, moisture) | Limitado |
Mixing and Homogenization | Superior due to dual intermeshing screws | Inferior mixing |
Uniformidad del producto | High (precise control of density and size) | Inconsistent in high-throughput conditions |
Scalability and Throughput | 200–3000 kg/hr depending on model | Usually < 1000 kg/hr |
Recipe Versatility | Multi-phase cooking, multi-density capability | Mostly suited to one product type per setup |
Applications of Twin-Screw Pet Food Extruders
1. Dry Kibble (Complete & Balanced Diets)
- Used for dogs, cats, and small mammals
- Requires high expansion and uniform cooking
2. Functional Pet Treats
- Dental sticks, meat jerky shapes, and training snacks
- Requires precise shape control and inclusion of supplements
3. High-Protein Diets
- Often contain fresh meat, requiring low shear and controlled moisture
4. Grain-Free or Hypoallergenic Diets
- Specialized recipes with pea, lentil, or potato starch
- Twin-screw allows careful control to avoid overcooking
Technical Specifications of Darin Twin-Screw Pet Food Extruder
Modelo | Capacidad de salida (kg/h) | Main Power (kW) | Screw Diameter (mm) | Velocidad del tornillo (rpm) | Heating Method |
---|---|---|---|---|---|
DR-65 | 120–150 | 22 | 65 | 600 | Electric |
DR-70 | 200–250 | 37 | 70 | 500 | Electric |
DR-85 | 400–500 | 55 | 85 | 400 | Steam & Electric |
DR-95 | 800–1200 | 90 | 95 | 350 | Steam & Electric |
DR-135 | 1500–3000 | 132–160 | 133 | 300 | Steam |
Twin-Screw Extrusion Control Parameters
Parámetro | Alcance típico | Impacto en el producto |
---|---|---|
Temperatura del barril | 90–180 °C | Affects starch gelatinization and expansion |
Velocidad del tornillo | 200–600 rpm | Impacts shear, mixing, and cooking rate |
Nivel de humedad | 16–28% pre-extrusion | Determines texture (dry vs. semi-moist) |
Velocidad de alimentación | 100–3000 kg/hr | Controls throughput and retention time |
Knife Speed | 1000–3000 rpm | Determines product length and surface texture |
Maintenance and Cleaning Considerations
Maintaining high operational efficiency requires periodic disassembly, cleaning, and part replacement. Darin Machinery’s extruders feature:
- Quick-release barrel sections for easy cleaning
- Auto-lubrication of screw bearings
- Screw shaft extraction devices
- PLC maintenance alerts
Estudio de caso
Cliente: European Premium Dog Food Brand
Requisito: Produce both grain-free kibble and dental treats
Solución: DR-85 Twin-Screw Extruder + Continuous Dryer
Results:
- 35% increase in productivity
- Reduced downtime for recipe switching
- Achieved 98% consistency in product density
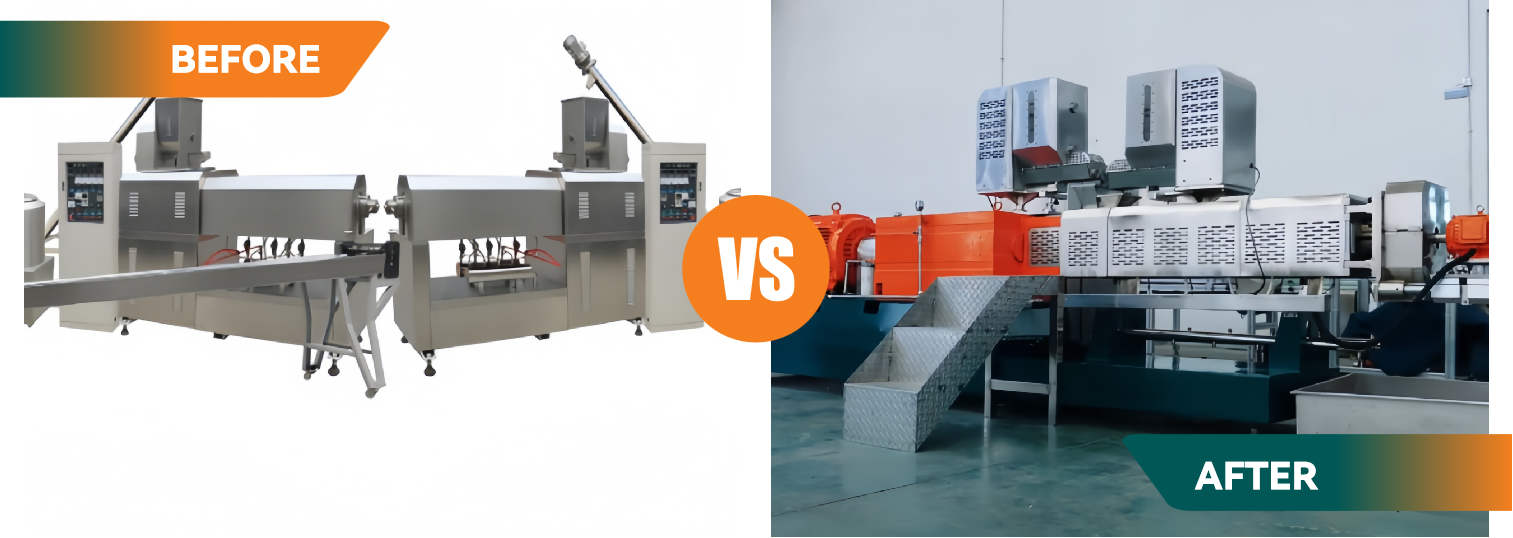
Resumen
Twin-screw pet food extruders are the backbone of modern pet food production, offering unmatched control, flexibility, and scalability. From protein-rich diets to allergen-free recipes, the twin-screw platform adapts seamlessly to evolving market needs while delivering consistent, high-quality output. With options ranging from compact 150 kg/hr models to industrial-grade 3,000 kg/hr machines, Darin Machinery’s extruders meet the full spectrum of industry demand—whether for startups or global brands.
Comuníquese con Darin Machinery para obtener soluciones de extrusión de doble tornillo personalizadas
Ready to elevate your pet food production with a high-performance twin-screw extruder? Maquinaria Darin provides turnkey extrusion lines, recipe engineering, installation support, and 24/7 technical assistance. Let us help you design the most efficient and reliable extrusion system for your needs.
📩 Contact us today to get a customized technical proposal and quotation.