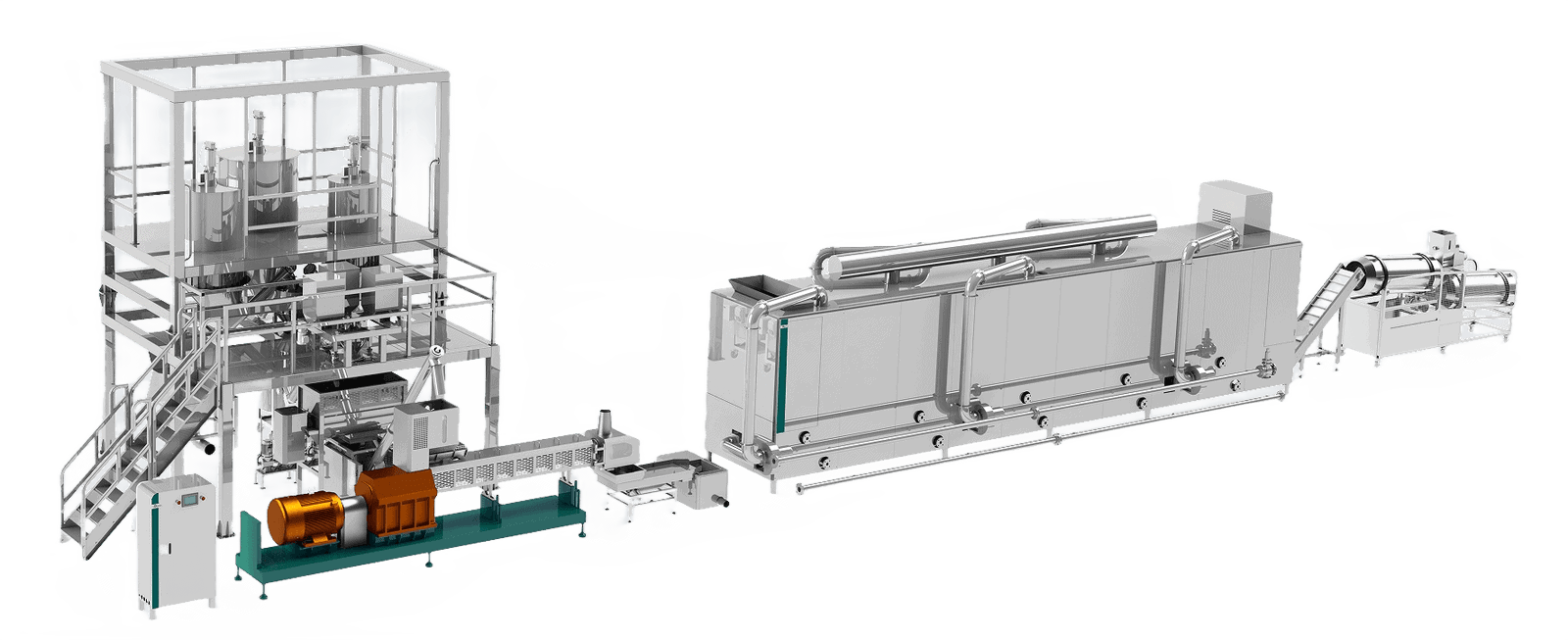
Starting a dog food production business without the right equipment can lead to serious setbacks: inconsistent product quality, production bottlenecks, hygiene concerns, and regulatory non-compliance. These issues result in wasted raw materials, failed product batches, and a loss of customer trust. However, by understanding exactly what equipment is needed to make dog food, you can build a streamlined, efficient, and compliant production line that supports high-quality output and business growth.
The essential equipment needed to make dog food includes raw material mixers, screw conveyors, extrusion machines, dryers, flavoring machines, cooling systems, packaging machines, and quality control devices. Each plays a crucial role in ensuring consistent, safe, and nutritious dog food production.
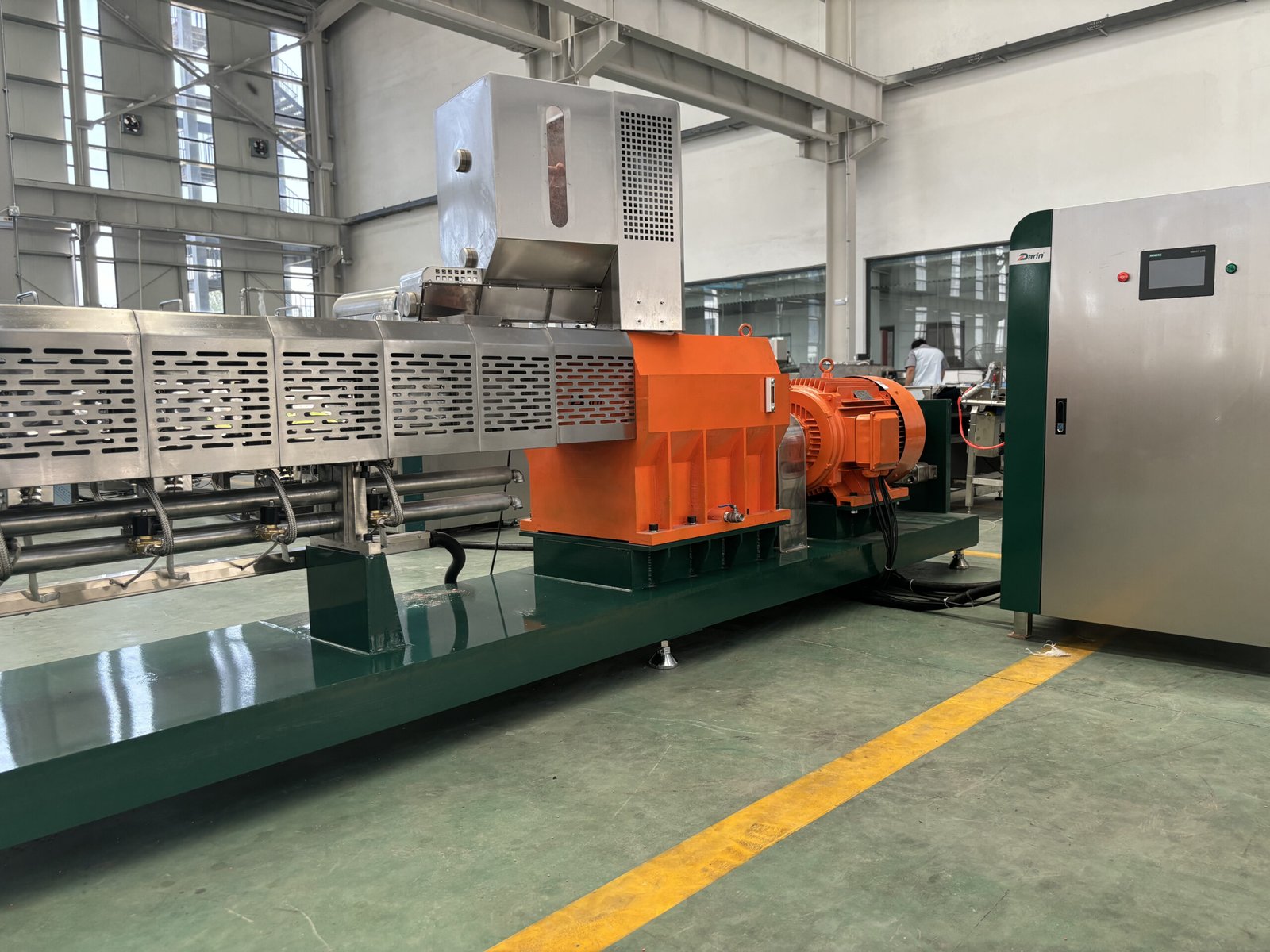
If you're considering setting up or expanding your dog food production line, keep reading. This comprehensive guide will provide you with in-depth insights on each piece of equipment, including technical details, functions, and how they contribute to an efficient manufacturing process.
Making dog food requires only a single extrusion machine.False
Dog food production requires multiple interconnected machines including mixers, conveyors, extruders, dryers, flavoring, and packaging equipment to ensure product quality and production efficiency.
Overview of Dog Food Production Line Equipment
Below is a detailed overview of the essential equipment used in manufacturing dog food:
Equipment Name | Function |
---|---|
Raw Material Mixer | Homogenizes ingredients like grains, meats, vitamins |
Screw Conveyor | Transfers mixed ingredients to the extruder |
Twin-Screw Extruder | Shapes and cooks dog food under high pressure & heat |
Dryer (Multi-layer or Rotary) | Reduces moisture content to ensure shelf stability |
Flavoring Machine | Sprays oils, vitamins, and palatants for taste & nutrition |
Cooling Conveyor | Cools product to room temperature before packaging |
Packaging Machine | Packs finished dog food into bags with labeling |
Quality Control Equipment | Ensures product meets regulatory standards |
Let's explore each component in depth.
1. Raw Material Mixer
Purpose:
Combines various dry and wet ingredients (grains, meat powders, vitamins, oils) into a uniform mixture.
Technical Details:
Feature | Specification Example |
---|---|
Capacity | 200 kg/batch to 2000 kg/batch |
Mixing Time | 3-10 minutes per batch |
Type | Horizontal ribbon mixer or paddle mixer |
Material | SUS304 stainless steel for hygiene compliance |
Why It Matters:
Consistent mixing ensures even nutrient distribution and prevents clumping, directly impacting the quality of the final product.
2. Screw Conveyor
Purpose:
Transfers mixed ingredients to the extruder without contamination.
Technical Details:
Feature | Specification Example |
---|---|
Diameter | 100-400 mm |
Length | Customized based on factory layout |
Motor Power | 1-5 kW |
Material | Food-grade stainless steel |
Why It Matters:
Automated transfer improves efficiency and minimizes manual labor, reducing contamination risks.
3. Twin-Screw Extruder
Purpose:
Performs cooking, shaping, and texturizing of the dog food under controlled conditions.
Technical Details:
Feature | Specification Example |
---|---|
Screw Diameter | 62mm, 72mm, 92mm, etc. |
Capacity | 100 kg/h to 5000 kg/h |
Control System | PLC with touch screen |
Heating Zones | 4-12 controllable zones |
Material | Alloy steel screws, bimetallic barrel |
Why It Matters:
Precise control over temperature, pressure, and moisture ensures the dog food is properly cooked, digestible, and retains nutritional value.
4. Dryer (Multi-layer or Rotary)
Purpose:
Removes moisture content from extruded dog food to ensure shelf stability.
Technical Details:
Feature | Specification Example |
---|---|
Type | Multi-layer mesh belt dryer or rotary drum dryer |
Heating Source | Electric, gas, steam |
Temperature Range | 80°C to 180°C |
Capacity | 200 kg/h to 5000 kg/h |
Why It Matters:
Proper drying prevents mold growth and prolongs shelf life while maintaining kibble texture.
5. Flavoring Machine
Purpose:
Applies palatants, oils, fats, and vitamins uniformly over cooled kibbles to enhance taste and nutrition.
Technical Details:
Feature | Specification Example |
---|---|
Type | Single/double drum flavoring machine |
Spray System | Automatic with oil pump |
Drum Speed | Adjustable for even coating |
Material | SUS304 stainless steel |
Why It Matters:
Flavoring significantly affects product appeal to dogs and helps deliver essential nutrients.
6. Cooling Conveyor
Purpose:
Reduces product temperature to room levels before packaging.
Technical Details:
Feature | Specification Example |
---|---|
Length | 5m to 20m based on capacity |
Cooling Method | Ambient or air-blown cooling |
Conveyor Material | Food-grade mesh belt |
Why It Matters:
Prevents condensation in packaging and maintains product texture.
7. Packaging Machine
Purpose:
Automates bagging, sealing, labeling, and weighing of finished dog food.
Technical Details:
Feature | Specification Example |
---|---|
Bag Type | Pillow, gusseted, stand-up pouches |
Speed | 10-60 bags/min based on model |
Weighing Accuracy | ±0.1% |
Material | SUS304 frame |
Why It Matters:
Consistent packaging improves brand image, reduces manual labor, and ensures product safety.
8. Quality Control Equipment
Purpose:
Monitors product quality parameters.
Equipment | Function |
---|---|
Metal Detector | Detects metal contaminants |
Moisture Analyzer | Ensures proper moisture content |
Lab Testing Equipment | Verifies nutritional values, ingredient composition |
Why It Matters:
Compliance with regulatory standards ensures marketability and customer trust.
Complete Dog Food Production Line Flow Chart
Process Stage | Equipment Involved |
---|---|
Ingredient Mixing | Raw Material Mixer |
Material Transfer | Screw Conveyor |
Cooking & Shaping | Twin-Screw Extruder |
Moisture Removal | Dryer |
Flavor Application | Flavoring Machine |
Cooling | Cooling Conveyor |
Packaging | Packaging Machine |
Quality Assurance | QC Devices (Metal Detector, Moisture Analyzer, Lab Tests) |
How to Choose the Right Equipment?
Consider:
- Production Capacity: Start with equipment that matches your daily/annual output targets.
- Automation Level: Higher automation reduces labor costs and improves consistency.
- Customization Options: Ability to adjust kibble size, shape, and formulation.
- Energy Efficiency: Modern machines with optimized energy consumption save long-term costs.
- Compliance Certifications: CE, ISO, and food safety standards.
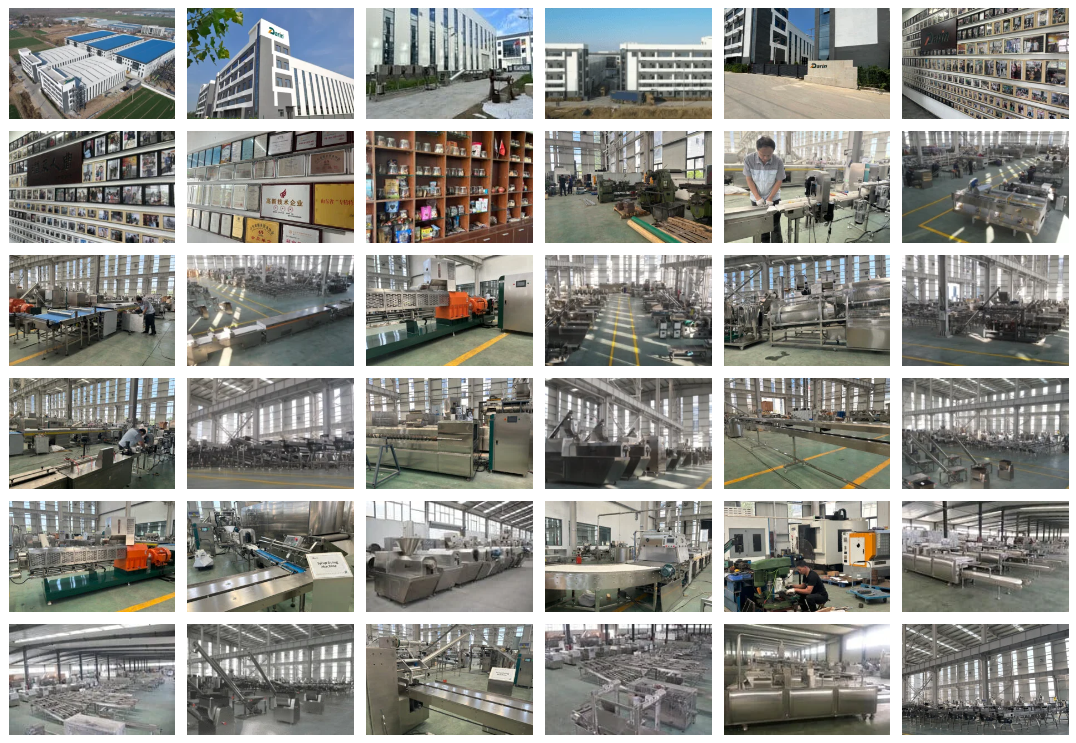
Final Thoughts
Building a successful dog food production line requires more than just a single machine. Each piece of equipment—from mixers to QC devices—plays a vital role in ensuring the final product is nutritious, safe, and appealing to both pets and their owners. Investing in high-quality, efficient equipment guarantees consistent output and smooth operation.
Ready to Set Up Your Dog Food Production Line?
Contact us today to receive expert consultation and customized equipment recommendations tailored to your production goals and budget. We provide complete solutions—from raw material processing to final packaging—ensuring your success in the pet food industry!
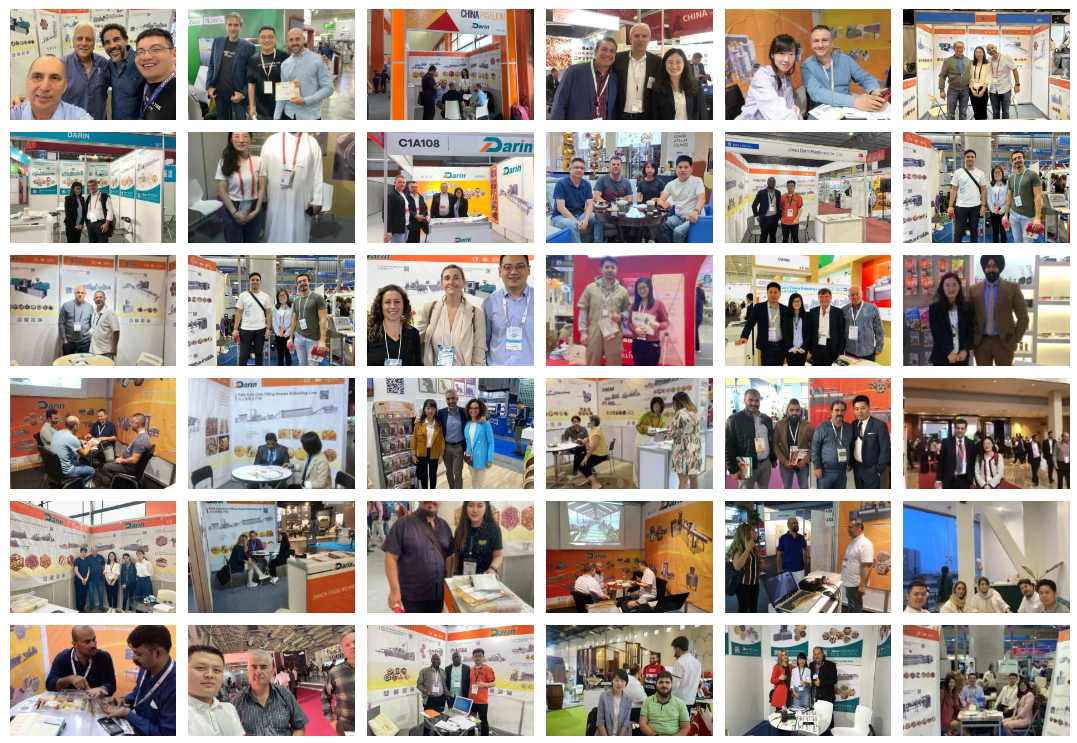
FAQ
Q1: What are the essential machines required to produce dog food?
A1: The key equipment needed includes raw material grinders, mixers, extruders, dryers, cooling conveyors, flavoring machines, and packaging machines. Each machine has a specific role in processing ingredients, shaping, cooking, and packaging the final dog food product.
Q2: What is the function of a dog food extruder?
A2: A dog food extruder cooks and shapes the ingredients under high pressure and temperature, creating kibble with uniform size and texture. It’s essential for ensuring product consistency and nutritional quality.
Q3: Why is a mixer important in dog food manufacturing?
A3: A mixer ensures all raw materials, vitamins, and additives are blended uniformly, which guarantees balanced nutritional content in each batch of dog food. Homogeneous mixing improves the final product's quality.
Q4: What role do dryers and cooling conveyors play in dog food production?
A4: Dryers remove excess moisture from the extruded kibble, preventing spoilage and extending shelf life. Cooling conveyors reduce the temperature of the dog food after drying to prepare it for flavoring and packaging.
Q5: Is packaging equipment necessary in dog food production?
A5: Yes, packaging machines seal the final product in bags or containers, ensuring hygiene, preserving freshness, and providing clear labeling for consumers. Automated packaging also increases production efficiency and reduces contamination risk.
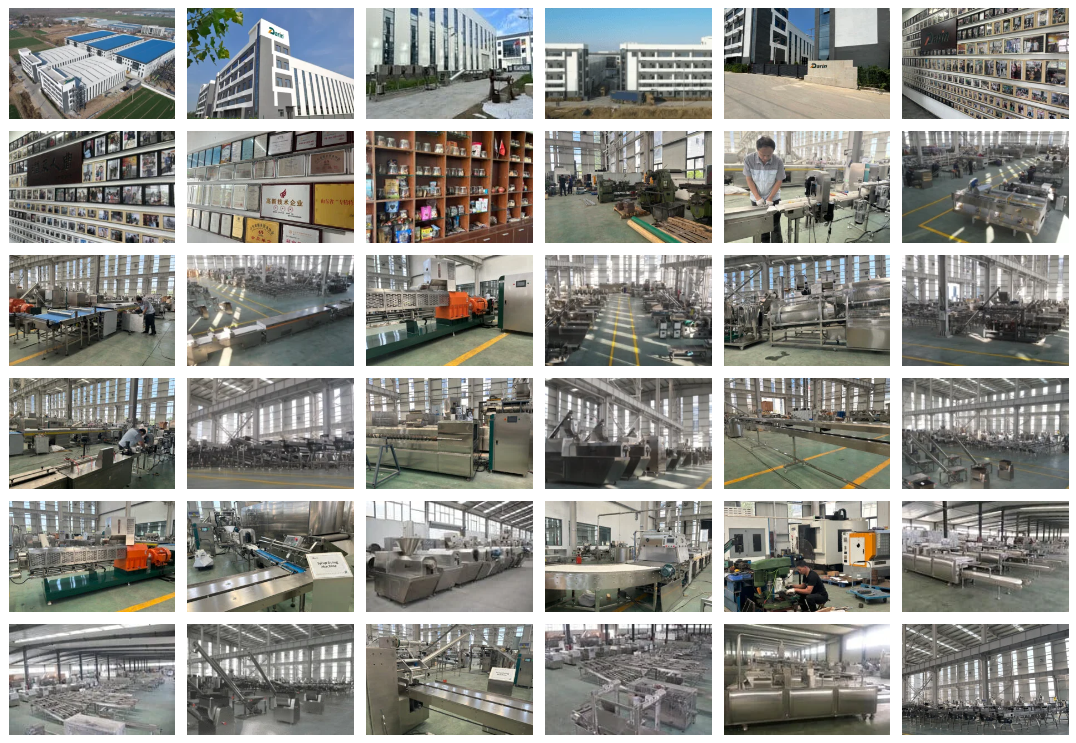
References
- Dog Food Manufacturing Equipment Overview - https://www.petfoodindustry.com/articles/10650-dog-food-equipment-guide - Pet Food Industry
- Essential Machines for Pet Food Production - https://www.feedstrategy.com/pet-food/key-pet-food-machines - Feed Strategy
- Role of Extruders in Dog Food Production - https://www.bakerperkins.com/pet-food-extrusion-guide - Baker Perkins
- Importance of Mixers in Pet Food Processing - https://www.foodprocessing.com/articles/2020/pet-food-mixers-guide - Food Processing
- How Dryers and Cooling Systems Work in Pet Food Plants - https://www.meatpoultry.com/articles/25150-drying-and-cooling-pet-food - Meat & Poultry
- Automation in Dog Food Packaging - https://www.petfoodprocessing.net/articles/14450-pet-food-packaging-equipment - Pet Food Processing
- Pet Food Processing Line Components - https://www.allaboutfeed.net/market-trends/pet-food-production-line-components - All About Feed
- Maintenance of Pet Food Manufacturing Equipment - https://www.foodengineeringmag.com/articles/98750-pet-food-equipment-maintenance - Food Engineering
- Safety Standards for Pet Food Equipment - https://www.automationworld.com/industries/food-beverage/article/21045000 - Automation World
- Dog Food Production Process Explained - https://www.petfoodprocessing.net/articles/14650-dog-food-production-process - Pet Food Processing