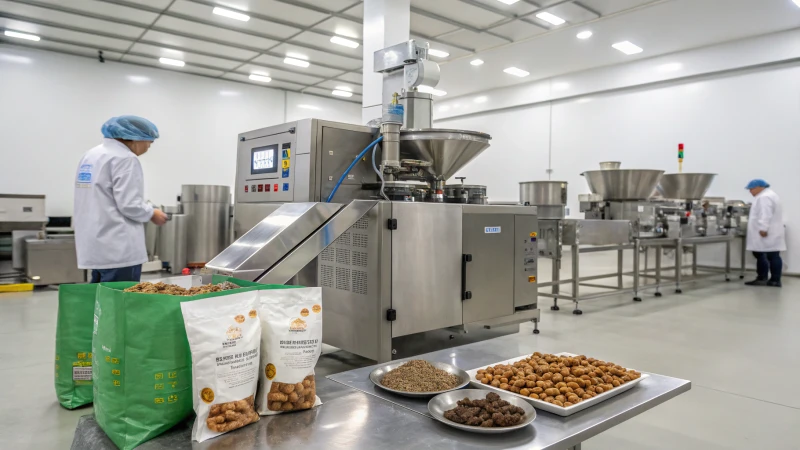
Installing a pet food production line is a complex but critical process that determines the efficiency and success of your production facility. Improper installation can lead to costly downtime, quality issues, and delays in production. So, what exactly is involved in the installation process for a pet food production line, and how can you ensure a smooth setup?
The installation process for a pet food production line involves six key steps: site preparation, equipment delivery and inspection, layout and positioning, system integration, testing and commissioning, and operator training. Proper planning, expert support, and adherence to safety standards are essential for ensuring a successful installation.
With a clear understanding of each step, businesses can streamline the process, minimize disruptions, and set up their production line for optimal performance. Let’s dive deeper into the detailed installation process and important considerations.
Steps to Install a Pet Food Production Line
1. Site Preparation
The first step is preparing your facility to accommodate the production line. This involves ensuring that the physical space, utilities, and infrastructure meet the requirements for the equipment.
Key Actions:
- Space Allocation: Measure and designate specific areas for raw material storage, equipment installation, finished product storage, and staff movement.
- Utilities Setup: Install or verify utility connections, including electricity, water, gas, and compressed air.
- Flooring and Ventilation: Ensure floors are level and durable, with proper drainage systems. Verify that the ventilation system complies with hygiene and safety standards.
Requirement | Details |
---|---|
Space | Must match production line layout dimensions. |
Power Supply | Check voltage and amperage compatibility. |
Hygiene Standards | Floors, walls, and ventilation should comply with food-grade standards. |
2. Equipment Delivery and Inspection
Once the site is ready, the production line equipment is delivered. Inspecting the equipment ensures that all components arrive undamaged and are complete.
Key Actions:
- Inventory Check: Match delivered items with the packing list provided by the manufacturer.
- Damage Inspection: Inspect all components for damage that may have occurred during shipping.
- Storage: Store components in a clean, dry area if installation will not begin immediately.
Common Equipment Delivered | Zweck |
---|---|
Extruder | For shaping and cooking pet food. |
Mixers and Grinders | For raw material preparation. |
Dryers and Coolers | For moisture removal and preservation. |
Verpackungsmaschinen | For final product packaging. |
3. Layout and Positioning
The next step is setting up the equipment according to the production line layout. This ensures proper workflow and operational efficiency.
Key Actions:
- Equipment Placement: Position machinery according to the pre-approved floor plan. Ensure spacing allows for maintenance and safety.
- Alignment: Use leveling tools to ensure machines are properly aligned.
- Connections: Connect equipment to utilities such as electricity, water, and compressed air.
Bewährte Methoden:
- Follow the layout provided by the equipment supplier or engineering team.
- Maintain clear pathways for workers and raw material transport.
Key Area | Positioning Considerations |
---|---|
Mixing and Grinding | Close to raw material storage for efficiency. |
Extrusion | Positioned centrally for streamlined flow. |
Trocknen und Kühlen | Near extrusion to minimize transport time. |
Verpackung | Located at the end of the production line. |
4. System Integration
System integration ensures that all machines and components work together as a cohesive production line. This step often involves connecting electrical systems, control panels, and automated processes.
Key Actions:
- Electrical Connections: Connect each piece of equipment to the central control system.
- Automation Setup: Program automated systems for synchronized operation.
- Communication Systems: Ensure sensors, alarms, and monitoring systems are functioning.
Expert Tip:
Work with the equipment supplier or an automation specialist during this phase to avoid errors in programming or connections.
5. Testing and Commissioning
Testing and commissioning are critical for verifying that the production line operates as expected. This involves running trial batches of pet food and identifying any issues.
Key Actions:
- Dry Runs: Test the mechanical movement of the equipment without materials.
- Trial Production: Process a small batch of raw materials to test functionality and performance.
- Calibration: Adjust settings for extruders, dryers, and other machines for optimal output and quality.
- Quality Checks: Ensure the final product meets specifications for size, texture, and nutritional content.
Testing Parameter | Beschreibung |
---|---|
Equipment Performance | Verify throughput and efficiency. |
Produktqualität | Ensure shape, size, and texture are correct. |
Safety Systems | Test emergency stops and alarms. |
6. Operator Training
Proper training of staff is essential to ensure smooth operation and maintenance of the production line. This step includes familiarizing operators with machine functions, safety protocols, and troubleshooting techniques.
Key Actions:
- Operational Training: Teach staff how to start, operate, and shut down each piece of equipment.
- Maintenance Training: Train technicians on routine maintenance tasks and basic repairs.
- Safety Training: Emphasize safe practices, emergency procedures, and food hygiene standards.
Expert Tip:
Request detailed manuals and support from the equipment supplier to enhance operator confidence.
Common Challenges During Installation
- Delays in Utility Connections: Ensure utilities are ready before equipment delivery to avoid installation delays.
- Equipment Damage: Conduct thorough inspections upon delivery to identify and address damages early.
- Alignment Issues: Use precision tools for alignment to avoid operational inefficiencies.
- Training Gaps: Insufficient training can lead to operational errors. Invest time in hands-on training sessions.
Estimated Installation Timeline and Costs
Step | Estimated Duration | Kostenbereich |
---|---|---|
Site Preparation | 2–4 weeks | $10,000–$50,000 |
Equipment Delivery/Inspection | 1–2 weeks | Included in equipment cost |
Layout and Positioning | 2–3 weeks | $5,000–$20,000 |
System Integration | 1–2 weeks | $5,000–$30,000 |
Testing and Commissioning | 1–2 weeks | $5,000–$20,000 |
Operator Training | 1 week | $2,000–$10,000 |
Total time for installation typically ranges from 6 to 12 weeks, depending on the size and complexity of the production line.
Fazit
The installation process for a pet food production line is a step-by-step procedure that requires careful planning, expert guidance, and attention to detail. From site preparation to operator training, each phase is crucial for ensuring efficient and trouble-free production.
If you’re planning to install a pet food production line, contact us for expert advice, customized layouts, and professional installation services. Our team will help you get started on the path to success!