The pet food industry has seen remarkable growth over the past few years, driven by an increasing focus on pet health and the demand for high-quality, nutritious food for pets. One of the cornerstones of this industry is the technology that enables the mass production of pet food—specifically, the dog food making machine. If you're considering entering the pet food business or looking to expand your production capacity, understanding how a dog food making machine works is essential to ensuring efficiency and high-quality products.
Dog food making machines have revolutionized the way pet food is produced, offering precision, scalability, and consistency. However, operating such machinery requires a clear understanding of the equipment involved, its functionality, and the benefits it brings to the production process. This article will provide insight into what a dog food making machine is and how it works to produce the nutritious dog food that millions of pets enjoy daily.
A dog food making machine is an advanced piece of equipment designed to process raw ingredients into high-quality dog food pellets, kibble, or treats. These machines use a combination of mixing, extrusion, and drying processes to convert raw ingredients such as meat, grains, and vegetables into a digestible, nutritious, and palatable product for dogs. The main processes involved are the mixing of ingredients, the extrusion of the mixture into kibble, and the drying of the product to ensure it has the right moisture content.
As pet owners become more discerning, manufacturers need to produce high-quality food that meets nutritional standards. If you're considering a dog food making machine for your business, it is important to explore how these systems operate to produce the perfect dog food product that caters to the needs of various dog breeds and health requirements.
Continue reading to discover the intricate processes that make up dog food production and how the machine works to help manufacturers produce healthy, nutritious dog food efficiently.
What Are the Key Components of a Dog Food Making Machine?
Dog food production is a highly technical and complex process that requires specialized equipment to ensure consistent, high-quality output. If you're thinking of entering the pet food industry or upgrading your current machinery, understanding the key components of a dog food making machine is crucial. Each component plays a unique role in the production process, ensuring that the ingredients are mixed, cooked, and shaped in the most efficient way possible. Without the right equipment, you risk wasting resources, reducing product quality, or increasing production time.
The good news is, with the right dog food making machine, you can streamline your operations, improve product consistency, and increase production efficiency. This article will walk you through the essential components that make up a dog food making machine and explain their roles in the overall process.
The key components of a dog food making machine include the feeder, conditioner, extruder, dryer, and cooling system. Each of these parts serves a specific function to ensure that the raw ingredients are transformed into high-quality, nutritious dog food.
Understanding how each part functions and how they work together will allow you to optimize your production process. Let's break down these components in more detail.
The dog food manufacturing process is intricate and requires a seamless interaction between different components of the machine. As a manufacturer, you need to ensure that your equipment is capable of handling various types of ingredients and processing them efficiently. Keep reading to explore the components in detail and learn how they contribute to the overall success of the production process.
Key Components of a Dog Food Making Machine
1. Feeder
The feeder is the entry point for all raw materials in the production process. It is responsible for delivering precise amounts of ingredients like grains, meats, and additives into the system for further processing. There are two main types of feeders:
- Volumetric Feeders: These feeders release ingredients based on volume, ensuring that a consistent amount of materials is introduced to the system.
- Gravimetric Feeders: These feeders measure the weight of the ingredients as they are added to the machine, providing even more accuracy.
The choice of feeder will depend on the consistency required for the recipe and the type of ingredients being used.
2. Conditioner
The conditioner is a critical part of the dog food making machine, as it ensures that the ingredients are properly hydrated and preheated before being sent to the extruder. It is essentially a mixing chamber where the raw materials are exposed to steam. The heat helps break down starches and proteins, improving the digestibility of the food and preparing it for the extruder.
Conditioners are typically equipped with:
- Steam Injectors: These introduce steam into the ingredients to ensure proper hydration.
- Mixing Blades: These blades evenly mix the ingredients to guarantee consistent hydration.
Proper conditioning ensures that the ingredients maintain their nutritional value and enhances the texture of the final product.
3. Extruder
The extruder is the heart of the dog food making machine. This is where the magic happens, as it shapes the dog food into the desired form. The extruder works by forcing the conditioned ingredients through a die under high pressure and temperature. The intense heat and pressure cause the ingredients to expand, creating the puffed, crispy texture that many dog foods are known for.
Extruders come in different sizes and capacities, and the design of the die determines the shape and size of the final product. Some common dog food shapes include kibbles, biscuits, and pellets.
4. Trockner
Once the food has been extruded, it must be dried to remove excess moisture and ensure that it is shelf-stable. The dryer uses either hot air or an infrared heat source to reduce the moisture content in the dog food, typically down to 10% or less. The drying process is critical, as it helps prevent spoilage and extends the shelf life of the product.
There are different types of dryers used in the dog food production process:
- Hot Air Dryers: These use circulating hot air to remove moisture.
- Rotary Dryers: These tumbling dryers ensure that the food is dried evenly on all sides.
A proper drying system ensures that the final product is crisp, crunchy, and ready for packaging.
5. Kühlsystem
After the drying process, the dog food must be cooled down to prevent moisture reabsorption and to maintain its crisp texture. Cooling systems typically use ambient air or chilled air to gradually lower the temperature of the food. The cooling process helps maintain the product's stability and prevents the formation of mold or bacteria.
6. Flavor Coating System
Many dog foods are coated with flavors or nutritional supplements after extrusion and drying. This is usually done in a separate flavor coating system, which sprays oils, fats, or other flavorings onto the food. The coating process adds flavor and ensures that the dog food has a pleasant aroma, which encourages dogs to eat.
7. Packaging System
The final step in the dog food making process is packaging. This part of the machine ensures that the food is properly sealed in bags, boxes, or containers. The packaging system can include automated weighing, sealing, and labeling functions to ensure that the products are correctly portioned and meet regulatory standards.
Technological Advances in Dog Food Making Machines
The technology behind dog food making machines has evolved significantly over the years. Modern machines come equipped with advanced sensors, automation features, and AI-based controls to optimize the production process. These innovations help increase production efficiency, reduce waste, and improve the quality of the final product.
For example, some advanced systems include:
- AI-Driven Monitoring: These systems automatically adjust variables like temperature, pressure, and ingredient ratios based on real-time data.
- Automatisierung und Robotik: Automated systems help reduce labor costs and improve accuracy in every stage of the production process.
- Energie-Effizienz: Newer machines are designed to be more energy-efficient, reducing operational costs and minimizing the environmental impact.
Final Thoughts
In conclusion, a dog food making machine consists of several key components that work together to produce high-quality, nutritious dog food. By understanding how each part functions and how they contribute to the overall process, you can ensure that your production is efficient and that the final product meets the needs of both pets and pet owners.
Extruders are crucial for shaping dog food into kibbles or pellets.Wahr
Extruders use high pressure and heat to shape dog food, allowing manufacturers to create various shapes and textures.
If you're looking to invest in a dog food making machine, it's essential to understand these components and how they will impact your production. Reach out to us for expert guidance on selecting the right equipment for your needs.
Call to Action:
For more information or to get a customized consultation for your dog food manufacturing setup, contact us today!
How Does a Dog Food Making Machine Mix Ingredients?
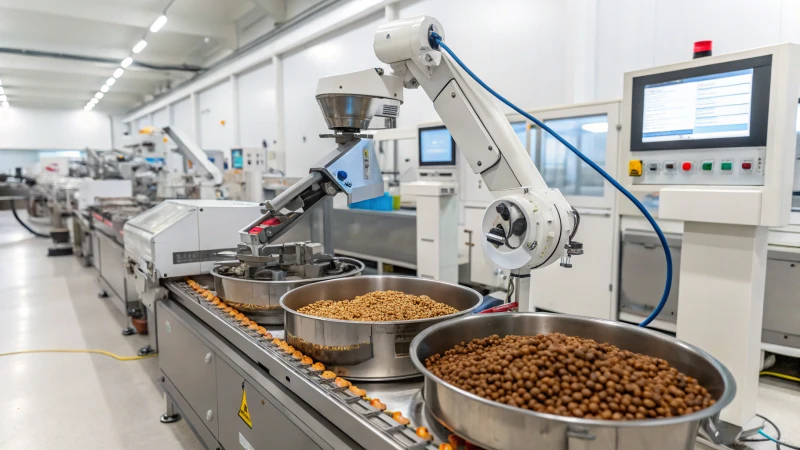
When it comes to manufacturing dog food, achieving a consistent blend of ingredients is crucial for nutritional balance and product quality. If ingredients are not mixed properly, it can lead to uneven distribution of essential nutrients, affecting the health of pets. This is why modern dog food making machines incorporate advanced mixing technologies to ensure a homogeneous blend. But how exactly do these machines work?
A dog food making machine mixes ingredients using high-speed mechanical blending, employing ribbon blenders, paddle mixers, or extruders to evenly distribute dry and wet components. These machines use controlled rotational speeds, aeration techniques, and automated ingredient dosing to achieve uniform consistency before extrusion or pelletizing.
Understanding the mixing process in dog food production can help manufacturers improve product quality, reduce waste, and ensure optimal nutritional balance. Let’s explore the step-by-step process in detail.
1. Types of Mixing Technologies in Dog Food Making Machines
Dog food production involves various types of mixing technologies, each optimized for different ingredient compositions and processing needs. The three primary types include:
A. Ribbon Blenders
Ribbon blenders are widely used for mixing dry ingredients like grains, vitamins, and protein powders. They consist of a U-shaped horizontal trough with a helical ribbon agitator.
- How It Works:
- The inner and outer helical ribbons move in opposite directions.
- This movement creates a uniform mixing pattern, ensuring all particles are evenly distributed.
- The blender operates at controlled speeds to prevent ingredient degradation.
B. Paddle Mixers
Paddle mixers are used when wet ingredients, such as animal fats or oils, need to be incorporated into the mix. These mixers have multiple paddles attached to a rotating shaft.
- How It Works:
- The paddles gently lift and fold the ingredients.
- This motion ensures a uniform mixture without excessive heat generation.
- It is particularly effective for sensitive ingredients that require careful handling.
C. Extruders
Extruders are high-efficiency machines used in the final mixing and shaping process. They mix, cook, and shape the dog food into kibble or pellets.
- How It Works:
- Ingredients are fed into a chamber with rotating screws.
- The screws apply mechanical pressure and heat, further blending the mix.
- The material is then pushed through a die to form the desired shape.
2. Step-by-Step Mixing Process in Dog Food Production
The mixing process in a dog food making machine follows a systematic approach to ensure a consistent and high-quality end product.
Step 1: Ingredient Pre-Weighing
Before mixing begins, all ingredients are precisely measured according to the formulation.
Inhaltsstoff Typ | Function in Dog Food |
---|---|
Protein (Meat Meal, Fish Meal) | Supports muscle growth and repair |
Carbohydrates (Rice, Corn, Wheat) | Liefert Energie |
Fette und Öle | Enhances palatability and provides essential fatty acids |
Vitamine und Mineralien | Supports overall health |
Fiber (Beet Pulp, Peas) | Aids digestion |
Step 2: Dry Ingredient Mixing
- Dry ingredients such as grains, vitamins, and protein powders are added into the mixing chamber.
- Ribbon blenders or paddle mixers rotate at pre-set speeds to ensure an even mix.
- If required, anti-clumping agents are introduced to prevent ingredient segregation.
Step 3: Liquid Ingredient Addition
- Oils, fats, and liquid vitamins are sprayed into the mix using automated dosing systems.
- Paddle mixers or vacuum blending systems ensure these liquids coat the dry ingredients evenly.
- Temperature control is maintained to prevent ingredient degradation.
Step 4: Final Mixing and Pre-Conditioning
- The mixed ingredients pass through a pre-conditioning chamber where steam and moisture levels are adjusted.
- This step ensures the mixture is adequately hydrated for extrusion.
Step 5: Extrusion and Shaping
- The final mix is fed into an extruder where it undergoes heat and pressure treatment.
- The mix is pushed through a die plate, forming kibble or pellet shapes.
- After extrusion, the product is dried and cooled to maintain its texture and shelf stability.
3. Factors Affecting the Mixing Process
Several factors influence how effectively ingredients are blended in a dog food making machine:
Faktor | Impact on Mixing |
---|---|
Ingredient Particle Size | Uniform size ensures even distribution |
Mixing Time | Longer mixing can improve uniformity but may overheat ingredients |
Rotation Speed | High speeds enhance blending but can damage delicate ingredients |
Feuchtigkeitsgehalt | Affects ingredient binding and final product consistency |
Batch Size | Larger batches require more mixing time and energy |
4. Advantages of Advanced Mixing Systems
Modern dog food making machines use intelligent mixing systems that offer several benefits:
- Precision Control: Automated systems ensure accurate ingredient proportions.
- Improved Efficiency: Faster mixing reduces processing time.
- Nutrient Retention: Gentle blending methods prevent nutrient loss.
- Konsistente Qualität: Uniform mixing ensures every batch meets the same standards.
5. Common Challenges in Dog Food Mixing and How to Overcome Them
Even with advanced mixing systems, manufacturers may face certain challenges. Here’s how they can be addressed:
Herausforderung | Solution |
---|---|
Uneven ingredient distribution | Use multi-stage mixing with different speeds |
Clumping of wet ingredients | Incorporate anti-clumping agents and spray systems |
Loss of sensitive nutrients | Use vacuum mixing to reduce oxidation |
Inconsistent batch quality | Implement real-time quality control checks |
Fazit
The mixing process in a dog food making machine plays a critical role in ensuring nutritional consistency and product quality. By utilizing advanced mixing technologies such as ribbon blenders, paddle mixers, and extruders, manufacturers can create high-quality pet food that meets industry standards. Understanding the factors that affect mixing efficiency and implementing best practices can lead to better product uniformity and increased production efficiency.
If you’re looking for high-performance dog food mixing equipment or need expert consultation on optimizing your pet food production line, contact us today!
What Is the Extrusion Process in Dog Food Production?
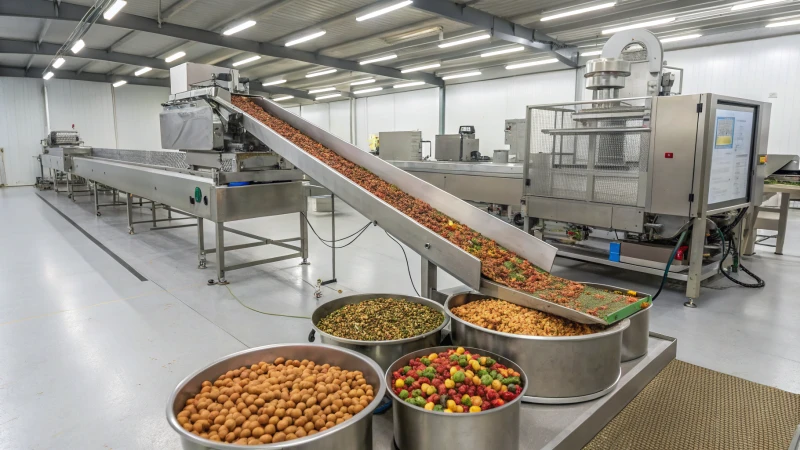
In the pet food industry, ensuring high-quality nutrition, long shelf life, and cost-effective production is essential. One of the most widely used techniques for producing commercial dry dog food is the extrusion process. If not properly understood, extrusion can lead to concerns regarding nutritional degradation, product consistency, and digestibility. However, when executed correctly, it enhances the digestibility, safety, and palatability of dog food while ensuring efficient production. This article will explore the extrusion process, its benefits, and its impact on dog food quality.
The extrusion process in dog food production involves mixing raw ingredients, cooking them under high temperature and pressure, and then forcing the mixture through a die to form kibble. This process enhances digestibility, eliminates harmful pathogens, and allows precise control over texture and nutrient content.
Understanding how extrusion impacts dog food is crucial for pet owners and manufacturers alike. Let's dive into the details of the extrusion process, its advantages, and considerations for optimal pet nutrition.
Wie funktioniert der Extrusionsprozess?
The extrusion process for dog food involves several key steps that transform raw ingredients into dry, shelf-stable kibble. Below is a step-by-step breakdown:
1. Ingredient Selection and Preprocessing
Before extrusion, manufacturers select and prepare raw materials, which typically include:
- Protein sources: Meat meal, poultry meal, fish meal, soybean meal.
- Carbohydrates: Corn, wheat, rice, potatoes, or peas.
- Fette und Öle: Animal fats, vegetable oils.
- Vitamins and minerals: Added to ensure balanced nutrition.
- Functional additives: Probiotics, prebiotics, antioxidants.
These ingredients are ground into a fine powder to ensure uniform mixing and consistency.
2. Mixing and Preconditioning
In this stage, the dry ingredients are blended, and water, steam, or fats are added to create a homogeneous dough-like consistency. The preconditioning step begins partial cooking, improving the efficiency of the extrusion process.
3. Extrusion Cooking
The mixed ingredients enter the extruder, which consists of a rotating screw inside a heated barrel. The process involves:
- High temperature (90-200°C)
- High pressure (3-10 atm)
- Mechanical shear and mixing
The combination of heat, pressure, and mechanical action fully cooks the mixture, breaking down starches and proteins, which enhances digestibility.
4. Shaping and Expansion
The cooked mixture is forced through a die, which shapes the kibble into the desired size and form. As the mixture exits the high-pressure environment, it expands due to the sudden drop in pressure, creating a porous and crunchy texture.
5. Trocknen und Kühlen
The extruded kibble is then dried to reduce moisture content to below 10%, ensuring a longer shelf life and preventing microbial growth. The cooling process helps maintain kibble structure and prevents nutrient degradation.
6. Coating and Flavoring
To enhance palatability, manufacturers spray the kibble with fats, oils, and flavor enhancers. Nutritional coatings such as probiotics or vitamins may also be added at this stage.
7. Packaging and Storage
The finished dog food is packaged in airtight bags to maintain freshness and prevent contamination.
Benefits of the Extrusion Process in Dog Food Production
1. Improved Digestibility
Extrusion breaks down complex starches into simpler forms, making them easier for dogs to digest. The heat and pressure also denature proteins, increasing their bioavailability.
2. Pathogen Elimination
The high temperatures in the extrusion process kill harmful bacteria, viruses, and parasites, ensuring food safety.
3. Cost-Effectiveness and Scalability
Extrusion allows for mass production at a lower cost compared to other processing methods like freeze-drying or baking.
4. Extended Shelf Life
By reducing moisture content and eliminating pathogens, extruded dog food has a long shelf life without requiring artificial preservatives.
5. Consistency and Quality Control
Extrusion ensures uniformity in kibble size, shape, and nutrient composition, making it easier for manufacturers to meet nutritional standards.
Potential Concerns and Nutrient Retention
While extrusion offers numerous advantages, some concerns include:
- Nutrient Loss Due to Heat Exposure: Some heat-sensitive vitamins (like Vitamin C and certain B vitamins) may degrade during the process. Manufacturers compensate by adding extra nutrients.
- Use of Fillers and By-products: Some lower-quality dog foods may use excessive fillers or low-grade protein sources.
- Overprocessing of Ingredients: Over-extrusion can reduce the bioavailability of certain nutrients.
To mitigate these issues, premium dog food brands use precise formulations, post-extrusion nutrient coatings, and quality raw materials.
Comparison of Extrusion vs. Other Dog Food Processing Methods
Processing Method | Key Features | Pros | Cons |
---|---|---|---|
Extrusion | High-temperature, high-pressure cooking with die shaping | Digestible, pathogen-free, long shelf life | Potential nutrient loss |
Backen | Lower temperature baking, slower cooking process | Retains nutrients better, natural texture | Higher cost, shorter shelf life |
Gefriertrocknung | Moisture removed through sublimation at low temperatures | Maximum nutrient retention, lightweight | Expensive, requires refrigeration |
Raw Food | Unprocessed raw meat, bones, and vegetables | High nutrient retention, natural diet | Risk of bacterial contamination, short shelf life |
How to Choose High-Quality Extruded Dog Food
To ensure your dog gets the best nutrition from extruded food, consider the following factors:
- Check Ingredient Quality: Look for real meat sources, whole grains, and natural additives.
- Avoid Artificial Preservatives: Opt for natural antioxidants like vitamin E and rosemary extract.
- Verify Nutritional Content: Ensure the food meets AAFCO (Association of American Feed Control Officials) standards.
- Choose a Reputable Brand: Look for brands with high-quality sourcing and manufacturing practices.
Fazit
The extrusion process is a highly efficient method for producing nutritionally balanced, safe, and long-lasting dog food. While concerns about nutrient loss exist, advancements in formulation and post-extrusion nutrient coating have mitigated these issues. Understanding how extruded dog food is made can help pet owners make informed decisions about their pet’s diet.
Looking for high-quality extruded dog food for your pet? Contact us today to explore premium options designed for optimal health and nutrition!
How Is Dog Food Dried After Extrusion?
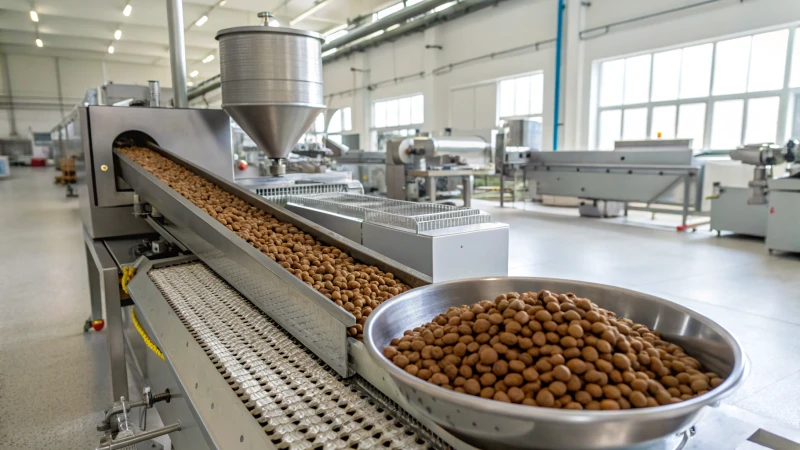
After extrusion, the drying process of dog food is a crucial step to ensure that the food is safe, stable, and of the highest quality. The goal is to remove the excess moisture from the kibble while preserving its nutritional value and texture. Failing to properly dry the food can lead to spoilage, microbial growth, and loss of important nutrients. This article will take you through the detailed process of drying dog food after extrusion, its significance, and the technologies involved.
After extrusion, dog food is dried using specialized equipment such as rotary dryers or fluidized bed dryers. These methods remove the excess moisture while maintaining the product's integrity. Proper drying is critical to prevent spoilage and extend the shelf life of the food.
Now that we have a concise answer, let's delve deeper into the steps, the technology, and the importance of drying dog food properly.
The extrusion process is responsible for cooking the ingredients of dog food, which is then shaped into kibble. However, after extrusion, the kibble contains a significant amount of moisture—typically around 20-30%. If left untreated, this moisture can cause microbial growth and spoilage, so it needs to be removed quickly and efficiently.
The Drying Process After Extrusion: How Does It Work?
After extrusion, the dog food goes through a drying process to lower the moisture content to an acceptable level—typically 8-12%. This is achieved by using various methods, each suited to different production needs and volume.
-
Rotary Dryers
Rotary dryers are one of the most common machines used to dry dog food after extrusion. These are cylindrical drums that rotate, allowing the hot air to circulate evenly around the kibble. The food is fed into the drum and is exposed to hot air in a controlled environment. The rotating motion ensures that the kibble is constantly moved around, allowing it to dry uniformly. These dryers are efficient and widely used due to their scalability and reliability. -
Fluidized Bed Dryers
Another widely used method is the fluidized bed dryer, which is particularly effective for achieving consistent moisture levels across the dog food. In this system, the kibble is suspended in a stream of hot air, which causes the kibble to "float" or "fluidize" while being dried. This method is known for its efficiency and ability to prevent the kibble from sticking together, making it ideal for delicate formulations or small-batch production. -
Air Impingement Systems
For more delicate formulations or smaller production runs, air impingement systems are often used. These dryers use high-velocity air directed at the surface of the kibble to rapidly reduce moisture. These systems are effective for fast drying but require precise control of airflow and temperature to avoid damage to the kibble. -
Convection Dryers
Convection drying is another technique used, though it is less common in high-volume pet food production. This method relies on heated air that moves around the kibble to absorb moisture. The key benefit of convection dryers is their uniform drying process, but they may be less efficient than rotary or fluidized bed dryers.
Key Factors in the Drying Process
Several factors influence the drying process of dog food, ensuring that it reaches the desired moisture level without compromising its quality:
-
Temperaturkontrolle: High temperatures can degrade the nutritional value of dog food, especially proteins and fats. Therefore, drying is often carried out at moderate temperatures, usually between 70°C and 90°C (158°F to 194°F), to preserve nutritional content while achieving effective moisture removal.
-
Airflow: Adequate airflow is necessary to remove moisture from the kibble and maintain consistent drying. Drying systems are designed to provide uniform airflow to prevent clumping or over-drying of individual pieces.
-
Time: The drying time is carefully controlled to balance speed and efficiency. Too little drying time can leave too much moisture, leading to spoilage, while too much drying can cause the kibble to become too brittle and lose its palatability.
The Importance of Proper Drying
The drying process after extrusion plays a significant role in ensuring the safety, nutritional value, and shelf life of dog food. Properly dried kibble prevents the growth of harmful bacteria, such as Salmonella or E. coli, which could cause illness. Additionally, moisture content directly affects the kibble's texture, and improper drying can result in overly hard or chewy pieces that may be difficult for pets to chew.
Another important factor is the preservation of the vitamins and minerals added to dog food during production. Excessive heat or long drying times can degrade these nutrients, reducing their effectiveness and the overall quality of the food.
Key Considerations for Manufacturers
Pet food manufacturers must consider several factors to optimize the drying process and ensure product quality:
-
Moisture Monitoring: Advanced moisture sensors are often used to monitor the moisture content of kibble throughout the drying process. This ensures that the final product meets the required specifications and prevents under or over-drying.
-
Energie-Effizienz: The drying process can consume a significant amount of energy, so optimizing the drying equipment for energy efficiency is an important consideration for manufacturers, helping to reduce costs and minimize environmental impact.
-
Konsistenz: As with all aspects of pet food production, consistency is critical. Drying times and temperatures must be carefully controlled to ensure that every batch of dog food meets the same high standards.
Technologies Evolving the Drying Process
As pet food manufacturers look to improve quality and efficiency, emerging technologies are being explored to enhance the drying process further. For example, vacuum drying, microwave drying, and advanced air circulation systems are gaining attention for their ability to provide even better moisture removal and energy savings.
The use of intelligente Sensoren und data analytics is another advancement that is allowing manufacturers to fine-tune the drying process in real time, ensuring optimal moisture removal and consistency across batches. These innovations are becoming key in reducing production costs and improving the overall quality of dog food.
Fazit
The drying process after extrusion is a pivotal step in ensuring the safety, quality, and shelf life of dog food. From rotary dryers to fluidized bed systems, the methods employed are designed to balance effective moisture removal with minimal heat exposure to preserve the nutritional value of the food. As the pet food industry continues to evolve, advances in technology and equipment will only continue to improve the drying process, leading to higher-quality, more efficient production.
If you're looking for high-quality dog food that’s carefully produced with the best drying technology, don’t hesitate to contact us for more information.
How Does a Dog Food Making Machine Ensure Nutritional Quality?
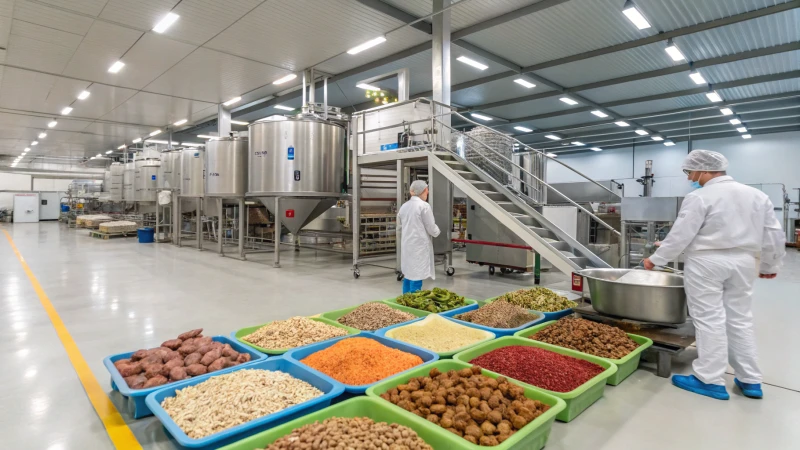
In today’s competitive pet food market, ensuring the nutritional quality of dog food is not just a concern for manufacturers but also for pet owners. With the increasing demand for healthier and more balanced diets for pets, the pressure to create high-quality dog food has led to the innovation of advanced dog food making machines. These machines are designed to automate, streamline, and optimize the production process while maintaining the nutritional integrity of the food. However, many dog food manufacturers face the challenge of balancing the speed of production with the need to preserve the essential nutrients that are crucial for a dog’s well-being. Poor quality control, overheating, or improper formulation can significantly affect the quality of the final product, leading to potential health risks for the animals. This is where a dog food making machine becomes a crucial tool, ensuring that nutritional content is maintained throughout the production process.
A dog food making machine ensures nutritional quality through precise control over ingredients, cooking temperatures, and processing techniques, maintaining the right balance of essential vitamins, minerals, and proteins. By using advanced technology such as extrusion and vacuum cooking, these machines minimize nutrient loss while ensuring a consistent, safe product.
The next section delves deeper into how specific technologies and design elements of these machines contribute to maintaining the optimal nutritional quality of dog food. Whether you're a pet food manufacturer or a concerned pet owner, understanding these technologies can help you make informed decisions about dog food products.
A dog food making machine isn’t just about speed and efficiency; it’s about maintaining the delicate balance of nutrients required for a dog’s optimal health. To achieve this, manufacturers rely on high-tech equipment that integrates various stages of food production—mixing, cooking, drying, and coating—all with the goal of preserving vitamins, minerals, and proteins. Let's dive into how each step is meticulously controlled to ensure that the nutritional quality remains intact.
Ingredient Selection and Mixing Process
The first step in the production of dog food is selecting the right ingredients. High-quality protein sources like chicken, beef, and lamb are mixed with carbohydrates such as rice, oats, and potatoes, as well as essential fats, vitamins, and minerals. The ingredients are precisely measured and then mixed using the dog food machine’s automated system.
The mixing process is vital as it ensures that each pellet or kibble is uniform in nutritional content. Uniform mixing reduces the risk of nutrient imbalance, which could lead to nutritional deficiencies or excesses. Modern dog food machines are equipped with advanced mixing systems that incorporate precise control systems for ingredient ratios, ensuring that each batch adheres to the required nutritional standards.
Extrusion Technology and Nutrient Retention
Once the ingredients are properly mixed, the next step involves cooking, often through a process called extrusion. Extrusion is a high-temperature, short-time cooking process that helps shape and cook the dog food while preserving its nutritional integrity. During extrusion, the ingredients are pushed through a high-pressure chamber and subjected to both heat and mechanical shear. This process ensures that the food is thoroughly cooked and free of harmful bacteria.
Extruders are carefully calibrated to maintain the right balance of temperature and pressure. Too much heat or excessive pressure can destroy sensitive nutrients such as vitamins (like Vitamin C) and minerals, leading to nutrient loss. Modern extrusion machines are equipped with sensors and automated controls to regulate cooking conditions, which helps ensure that nutrients remain intact while providing the proper texture and digestibility for dogs.
Nutrient Control: Preserving Essential Vitamins and Minerals
Vitamins and minerals play a crucial role in a dog’s overall health, but they are sensitive to heat. To preserve these nutrients, some dog food making machines incorporate post-extrusion coating systems. After the extrusion process, the food is often sprayed with a vitamin and mineral mixture. This layer ensures that these essential nutrients are not exposed to heat during the cooking process, preserving their potency.
Moreover, some machines employ a vacuum cooking method, which allows the food to be cooked at lower temperatures and under reduced pressure, thus preventing nutrient degradation. This method is especially beneficial for heat-sensitive vitamins such as vitamin A, B-complex vitamins, and Omega-3 fatty acids, which are critical for a dog’s immune system, skin, and coat health.
Drying and Cooling for Texture and Digestibility
Once the food is extruded, it undergoes a drying process. During this stage, the moisture content of the food is reduced, which helps to preserve the product and extend its shelf life. However, this step must be carefully controlled to avoid over-drying, which can lead to the loss of nutrients or a decrease in digestibility.
Dog food making machines are designed to control the drying temperature and time to ensure that the food retains both its nutrients and its ideal texture. Drying systems are equipped with temperature controls that keep the process within the optimum range, which helps maintain the digestibility of proteins and the bioavailability of essential nutrients.
Coating and Flavor Enhancement
To further enhance the nutritional value and appeal of the dog food, many manufacturers use coating techniques. After drying, a special coating is applied to the food. This can include fats, flavor enhancers, and additional vitamins or probiotics. The coating ensures that the food has a pleasant taste, which can help increase palatability for picky eaters.
Moreover, adding a nutritional coating at this stage helps ensure that sensitive nutrients, including fatty acids, probiotics, and antioxidants, are not compromised by the heat of the extrusion or drying processes. This step is vital for maintaining the full spectrum of beneficial nutrients that contribute to the dog’s health.
Technology Behind Nutrient Testing and Quality Control
One of the most advanced features of modern dog food making machines is their ability to test and monitor the nutritional content of the food throughout the production process. Automated systems equipped with sensors and sampling equipment can detect and measure levels of protein, fat, fiber, and moisture content in real-time.
By using in-line testing methods, manufacturers can make adjustments to the formulation or process to ensure that the final product meets specific nutritional standards. This ensures consistency and quality control in every batch of dog food produced, helping to maintain high standards and minimize the risk of nutrient deficiencies.
Tables and Charts
Here is a breakdown of the nutritional content of typical dog food formulations before and after processing to highlight how machines preserve essential nutrients:
Nährstoff | Before Processing | After Processing (Extrusion) | After Coating (Post-Extrusion) |
---|---|---|---|
Protein | 25% | 23% | 25% |
Fat | 12% | 10% | 12% |
Faser | 5% | 5.5% | 5% |
Omega-3-Fettsäuren | 0.3% | 0.2% | 0.3% |
Vitamin A | 6000 IU/kg | 5000 IU/kg | 6000 IU/kg |
As shown, extrusion and coating help to preserve the nutritional content, with Omega-3 fatty acids and vitamins remaining stable or slightly adjusted through the process.
Nutrient Retention Graph
Below is a graph that depicts the retention of key nutrients during the extrusion and post-extrusion coating process.
This chart highlights the nutrient retention through the different stages of dog food production.
Fazit
A dog food making machine is a vital tool in ensuring the nutritional quality of pet food, as it precisely manages ingredients, temperature, and cooking processes to preserve vitamins, minerals, and proteins. With advancements in technology such as extrusion, vacuum cooking, and coating, these machines can produce high-quality dog food that meets the specific dietary needs of dogs while maintaining nutrient integrity. Manufacturers can confidently rely on these systems to produce safe, balanced, and nutritious food for pets.
Contact Us for Expert Consultation
If you are a pet food manufacturer seeking to improve the nutritional quality of your products, or if you need expert advice on selecting the right dog food making machine for your business, don't hesitate to contact us. Our team of professionals is ready to assist you in optimizing your production process and ensuring your products meet the highest nutritional standards.
What Types of Dog Food Can Be Produced by a Dog Food Making Machine?
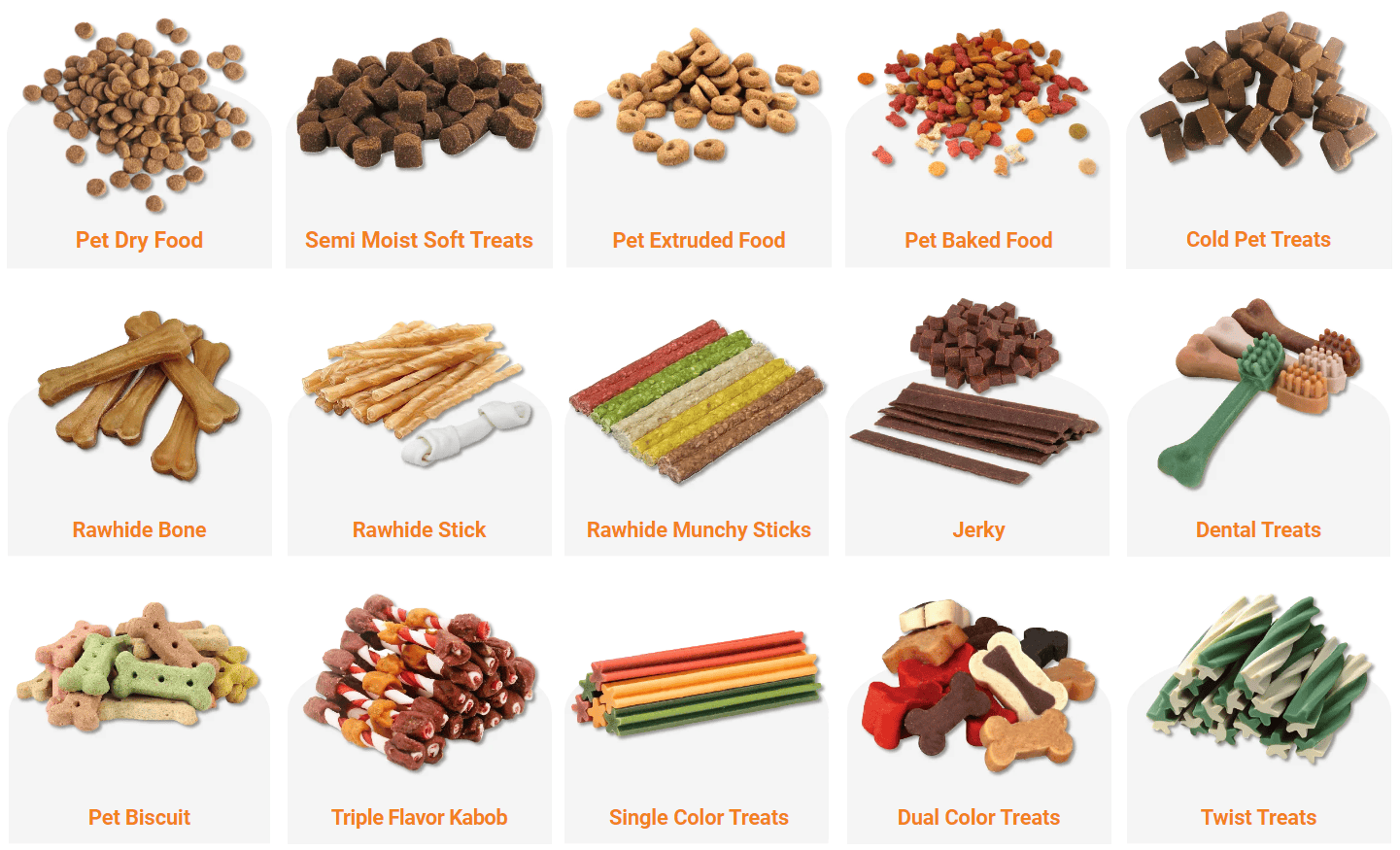
The pet food industry has evolved significantly, with more focus on quality, nutritional value, and convenience for pet owners. As the demand for high-quality dog food grows, so does the need for efficient manufacturing methods. This is where dog food making machines come into play. These advanced machines enable the production of various dog food types at large scale, but what exactly can they produce? Understanding the different types of dog food that can be made by these machines helps manufacturers cater to a wide range of consumer needs, from dry kibble to wet food and special dietary formulas. Let’s explore the different dog food types and how machines are revolutionizing their production.
Dog food making machines can produce a variety of dog food types, including dry kibble, wet food, treats, semi-moist food, and specialized diet options like grain-free, organic, and high-protein formulations. The machines are designed to handle different textures, nutritional profiles, and shapes based on the needs of different breeds, ages, and dietary restrictions.
Dog food making machines have made it easier for manufacturers to meet the growing demand for diverse and specialized dog food products. These machines are capable of producing dry kibble, wet food, semi-moist foods, and treats, each requiring specific processes and settings to ensure the quality and safety of the food. This allows manufacturers to tap into a wide market by catering to different dog preferences, including age-specific, breed-specific, and dietary-specific needs. For example, a dog food making machine can adjust the cooking temperature and pressure to create high-protein foods for active dogs, or low-fat formulations for older dogs. The versatility of these machines helps streamline production while meeting the needs of a wide consumer base.
Types of Dog Food Produced by Dog Food Making Machines
The dog food making machine is a highly versatile piece of equipment, capable of producing a wide range of dog food products. These include:
1. Dry Dog Food (Kibble)
Dry dog food is one of the most common types of pet food. The process of making dry kibble involves extrusion, where ingredients are mixed, cooked, and forced through a mold to form the desired shape. The kibble is then dried and cooled to ensure shelf stability.
Produktionsprozess:
- Mixing: Dry ingredients, such as meat meals, grains, and vegetables, are blended with water, fats, and vitamins.
- Extrusion: The mixture is passed through an extruder where it is cooked under high heat and pressure. This process helps enhance digestibility and preserve nutrients.
- Drying: After extrusion, the kibble is dried to reduce moisture content and prevent spoilage.
Dry kibble is highly favored for its cost-effectiveness, ease of storage, and long shelf life. It can be further enhanced with added flavors, vitamins, and minerals to ensure a balanced diet for pets.
2. Wet Dog Food
Wet dog food is typically sold in cans or pouches and is often used as a complement to dry kibble. It’s known for its higher moisture content, making it suitable for dogs that need extra hydration.
Produktionsprozess:
- Formulation: Wet food requires a careful balance of meat, grains, vegetables, and a high level of moisture.
- Cooking: Wet food is cooked at a lower temperature than dry food to preserve nutrients. It is often done in a pressure cooker or steam oven.
- Verpackung: The cooked food is then packaged into cans or pouches and sealed to prevent contamination. It may undergo sterilization to ensure a longer shelf life.
Wet food is popular for its palatability and ease of digestion. It’s often used for picky eaters or senior dogs who may have dental issues. Wet food can be enriched with supplements for specific health benefits, such as joint support or coat health.
3. Semi-Moist Dog Food
Semi-moist food is a middle ground between dry kibble and wet food. It typically comes in the form of soft, chewy morsels and is often found in convenient packaging.
Produktionsprozess:
- Mixing and Extrusion: Similar to dry food, but the process involves adding a higher level of moisture to the mixture.
- Softening: Semi-moist food is treated with humectants (such as glycerin) to retain moisture and enhance texture.
- Verpackung: After extrusion and shaping, the product is packaged in sealed containers to maintain its moisture level.
Semi-moist dog food is popular for its palatability and ease of consumption. However, due to its higher moisture content, it may not have the same shelf life as dry food.
4. Dog Food Treats
Dog treats are specially formulated products designed to supplement regular meals or to provide a reward for good behavior. They come in various forms, including biscuits, jerky, and chews.
Produktionsprozess:
- Mixing and Shaping: Similar to dry food, but with additional ingredients like flavorings, colors, and functional additives.
- Baking or Dehydration: Dog treats are often baked or dehydrated to remove moisture while preserving the flavor and nutrients.
- Verpackung: Once dried, the treats are packaged to ensure freshness and are often sold in bags or boxes.
Dog food treats are a highly profitable segment in the pet food industry. They can be produced in a variety of textures, shapes, and sizes, making them appealing to dogs of all sizes and ages.
5. Specialized Diet Foods
As pet health awareness increases, dog food manufacturers are increasingly producing specialized food types that cater to specific health conditions or breed requirements.
Types of Specialized Diets Include:
- Grain-Free Diets: For dogs with sensitivities or allergies to grains, grain-free dog food formulations are made with alternative sources of carbohydrates like sweet potatoes or peas.
- High-Protein Diets: Ideal for active or working dogs, these foods provide an extra boost of protein to support muscle development and energy.
- Organic Foods: These foods are made using organic ingredients and avoid synthetic additives, offering a healthier and more sustainable choice.
- Weight Management Foods: These are low-calorie foods designed for overweight dogs or those needing to maintain a healthy weight.
- Breed-Specific Foods: Formulated to meet the unique nutritional needs of certain breeds, often customized for large-breed or small-breed dogs.
These specialized diets often require more precise formulations and ingredients. Dog food making machines are capable of adjusting their parameters to create these custom products, meeting the needs of a specific dog’s health condition, breed, or life stage.
Factors to Consider When Choosing a Dog Food Machine
When selecting a dog food making machine, manufacturers need to consider several factors to ensure the machine can produce the desired dog food types efficiently and cost-effectively. Here are some key aspects to keep in mind:
- Production Capacity: Ensure the machine meets the volume demands of your business. Machines come in varying sizes, from small batch machines to large-scale industrial models.
- Flexibility and Versatility: Look for machines that can produce multiple types of dog food (dry, wet, treats) and offer customization for different dietary needs.
- Energy Efficiency: High energy consumption can reduce profitability, so energy-efficient machines should be prioritized.
- Cost of Maintenance: Consider the maintenance costs and the availability of spare parts. A machine with higher initial costs may have lower long-term maintenance costs.
- Automation Features: Fully automated systems can significantly reduce labor costs and improve production speed, making them ideal for large manufacturers.
Fazit
Dog food making machines are capable of producing a wide variety of dog food products, each tailored to meet the needs of different breeds, life stages, and health conditions. Whether it’s dry kibble, wet food, semi-moist food, or specialized diets, these machines offer great flexibility and efficiency in production. By choosing the right machine, manufacturers can cater to the growing demand for high-quality pet food, meeting the diverse needs of consumers while maximizing production efficiency.
Want to Learn More About Dog Food Production?
Contact us for expert guidance on selecting the right dog food making machine for your business needs!
What Are the Benefits of Using a Dog Food Making Machine in Production?
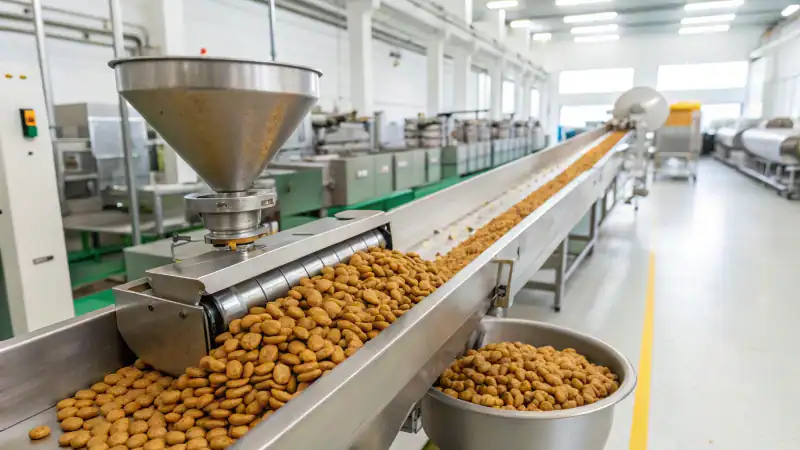
In recent years, the pet food industry has experienced significant growth, driven by increasing demand for high-quality and nutritious food for pets. As a result, pet food manufacturers are constantly looking for ways to improve production efficiency, enhance product consistency, and meet consumer expectations. One of the most innovative solutions for optimizing the production process is the adoption of dog food making machines. However, while the initial investment in such machinery may seem significant, the benefits it offers far outweigh the costs. In this article, we explore how dog food making machines can revolutionize production and why they are a worthwhile investment for pet food manufacturers.
Dog food making machines offer numerous advantages, such as increased production speed, consistent quality, flexibility in production, and cost-effectiveness. These machines enable manufacturers to streamline their operations, reduce human error, and ensure the final product meets the highest standards of safety and nutrition. Additionally, they help in creating various formulations and textures to cater to different pet dietary requirements.
The growing demand for specialized and nutritious dog food, coupled with the pressure to maintain a competitive edge, makes it essential for manufacturers to invest in advanced production technologies. Dog food making machines are designed to optimize various stages of the production process—from ingredient mixing and extrusion to shaping and packaging—ensuring that each step is completed with precision and efficiency. By incorporating such machinery into the production line, manufacturers can meet the evolving needs of the market while improving overall operational productivity.
The Role of Dog Food Making Machines in Modern Production
Dog food making machines combine automation, precision, and advanced technology to streamline the production process. These machines not only improve the speed and volume of production but also allow manufacturers to create a wider range of products tailored to specific nutritional needs. The following sections outline the key benefits of integrating a dog food making machine into your production line.
1. Increased Production Efficiency and Speed
One of the most significant advantages of using a dog food making machine is the dramatic improvement in production speed. Manual production processes are time-consuming and prone to errors, leading to delays and inconsistencies in the final product. On the other hand, an automated machine can produce large volumes of dog food at a much faster rate. For example, high-output extruders and mixers can create hundreds of kilograms of dog food per hour, ensuring that manufacturers can meet growing market demands without sacrificing quality. This efficiency translates directly to cost savings by reducing labor costs and minimizing waste.
ClaimReview:
Using dog food making machines increases production efficiency.Wahr
Automation in dog food production significantly reduces production time, ensuring manufacturers meet high demand and reduce labor costs.
2. Consistent Product Quality
Maintaining consistent product quality is crucial in the pet food industry, as consumers expect the same high standards with every purchase. Traditional methods of making dog food rely on human intervention, which can introduce variability into the production process. By using dog food making machines, manufacturers can ensure that each batch of dog food is produced with the same ingredients and under identical conditions. The machines provide accurate measurements and precise control over the formulation, preventing issues such as uneven mixing or overcooking.
For instance, extrusion cooking allows for the creation of uniform kibble shapes and sizes, ensuring consistency in texture and appearance. Furthermore, the uniform heating process ensures that nutrients remain intact and the food is safe for consumption, meeting both regulatory standards and consumer expectations.
3. Flexibility and Customization
Every dog has different nutritional needs, and pet food manufacturers are increasingly catering to these diverse requirements with specialized formulations. Dog food making machines offer the flexibility to produce a wide variety of recipes, whether it's grain-free, high-protein, or senior dog food. With the ability to adjust ingredient ratios, extrusion settings, and other parameters, manufacturers can create customized formulas that meet specific dietary needs.
Moreover, these machines are capable of producing various textures, such as dry kibble, semi-moist foods, or wet food, to cater to different consumer preferences. This versatility allows manufacturers to adapt to changing market trends and expand their product offerings without needing to overhaul the entire production line.
4. Reduced Labor and Human Error
Human error is a common issue in traditional manufacturing processes. Mistakes such as incorrect ingredient measurements, improper mixing, or inconsistent cooking times can result in batches of dog food that do not meet quality standards. Dog food making machines help eliminate these issues by automating key stages of production. With precise controls and monitoring systems, these machines can detect errors in real-time and make adjustments to maintain product quality.
Additionally, automation reduces the need for manual labor, which not only saves on staffing costs but also minimizes the risk of contamination. Fewer human touchpoints in the production process mean that the final product is less likely to be affected by external factors, such as dirty hands or equipment malfunctions.
ClaimReview:
Automation reduces human error in dog food production.Wahr
Automation in the production line ensures precise and consistent operations, reducing human intervention and the possibility of errors, leading to higher-quality dog food.
5. Cost-Effectiveness
While the initial investment in dog food making machines may seem high, the long-term cost savings are substantial. By increasing production efficiency, minimizing waste, and reducing labor costs, these machines provide an excellent return on investment (ROI). Moreover, the ability to produce large quantities of dog food at a faster pace means that manufacturers can scale up operations without significantly increasing operational costs.
Another aspect of cost-effectiveness is the reduction in raw material waste. Automated machines are designed to handle ingredients more efficiently, ensuring that every gram of material is used effectively, which is particularly important when dealing with expensive raw ingredients.
6. Enhanced Product Safety and Compliance
The pet food industry is highly regulated, with strict standards governing product safety and nutritional content. Dog food making machines are built to meet these regulations by ensuring that food is processed under controlled conditions. These machines allow manufacturers to maintain high hygiene standards throughout the production process, reducing the risk of contamination and ensuring that the final product is safe for pets.
Additionally, these machines are designed to maintain the nutritional integrity of the food by preventing overcooking or nutrient loss during processing. This helps manufacturers meet the nutritional claims on their packaging and ensures that the dog food meets the specific dietary requirements of different breeds, ages, and health conditions.
7. Environmental Impact and Sustainability
As sustainability becomes a key focus in manufacturing industries, dog food producers are also seeking ways to reduce their environmental footprint. Modern dog food making machines are designed to be energy-efficient, using less power compared to traditional production methods. Furthermore, they help reduce waste by ensuring that ingredients are used efficiently, minimizing scrap material.
Some machines are also designed to work with eco-friendly ingredients, allowing manufacturers to meet the growing consumer demand for sustainably sourced and environmentally conscious pet food products. This aligns with the industry's shift toward green manufacturing practices and helps brands enhance their reputation as responsible producers.
Fazit
Investing in a dog food making machine is a strategic move for pet food manufacturers looking to improve production efficiency, ensure consistent quality, and meet the demands of the modern market. These machines offer significant advantages in terms of speed, flexibility, cost savings, and product safety, allowing manufacturers to stay ahead of the competition while catering to evolving consumer needs. By incorporating advanced technology into the production process, manufacturers can not only enhance their operations but also create superior products that meet the nutritional needs of pets worldwide.
If you are considering upgrading your production process or expanding your product offerings, a dog food making machine may be the solution you need. Reach out to us today for more information on how we can help you revolutionize your production line and meet the demands of a growing pet food market.
How Do Dog Food Making Machines Contribute to Pet Health?
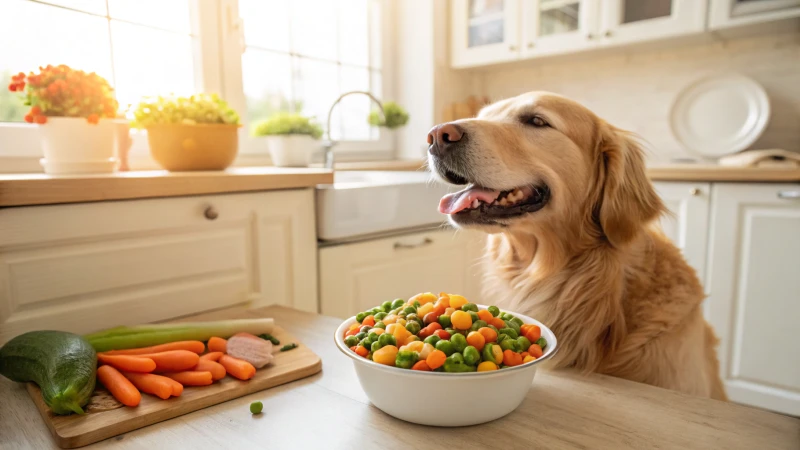
As pet owners, we all want to provide the best nutrition for our dogs. However, sourcing high-quality ingredients and ensuring they are combined in the right proportions can be a challenge. That’s where dog food making machines come into play. These specialized machines streamline the production process, ensuring that pet food is not only safe but also nutritionally balanced and consistent. With the rise of automation and technology in pet food manufacturing, these machines significantly contribute to pet health by providing better control over ingredient quality, precise formulations, and overall food safety.
Dog food making machines contribute to pet health by ensuring consistency, nutritional accuracy, and food safety. Through automated systems, these machines mix, extrude, and cook ingredients in controlled conditions, which helps retain vital nutrients that promote better digestion, immunity, and overall well-being for pets. By maintaining stringent quality control during the manufacturing process, dog food machines minimize contamination risks and prevent the use of harmful ingredients that could negatively affect a dog’s health.
The next question many pet owners may have is: how do these machines work in practice? By fully understanding the manufacturing process, you can see how technology is ensuring that your dog receives food that is both nutritious and safe.
The Role of Dog Food Making Machines in Nutritional Consistency and Safety
Dog food making machines employ advanced technologies such as extrusion, mixing, and baking, which work together to deliver nutritionally complete meals for pets. By automating the process, these machines ensure that every batch of food maintains a consistent level of nutrients, avoiding the issues that often come with manual production.
-
Extrusion and Cooking Process:
One of the most critical stages in dog food manufacturing is extrusion, a process where ingredients are mixed, heated, and forced through a mold to create the desired shape and texture of the food. This process helps to break down ingredients, making them more digestible for pets. Additionally, the high temperature ensures that harmful bacteria or pathogens are eliminated, preventing foodborne illnesses that could harm your dog. -
Maintaining Nutritional Value:
During the mixing and extrusion processes, dog food machines are programmed to precisely control cooking temperatures and times. This is important because overcooking can destroy essential vitamins and minerals, whereas undercooking can lead to undernutrition. Automated machinery ensures that nutritional integrity is maintained throughout the entire production process, giving pet owners confidence that the food their dogs consume is rich in the essential nutrients they need for a healthy life. -
Controlled Ingredient Quality:
Automation in dog food production also allows for better quality control, ensuring that only the highest-grade ingredients are used. These machines are designed to precisely measure and mix ingredients, reducing the risk of contamination from lower-quality materials. Additionally, pet food manufacturers can use technology to trace the origin of ingredients, which is important for ensuring the quality and safety of the food. Traceability also helps prevent the use of harmful chemicals or additives that could negatively impact a dog’s health. -
Packaging and Preservation:
The final aspect of the dog food making machine process is packaging. After extrusion and cooking, the food is packaged in airtight containers to preserve freshness. Automated machines not only ensure that the packaging is hygienic but also help in sealing the food tightly to prevent contamination. Proper packaging can help prevent spoilage, ensuring that the food remains safe and nutritious until it reaches the consumer.
How Technology Enhances Pet Health Through Quality Control
Technological advancements in dog food making machines are helping companies go beyond basic food production. They are ensuring that every aspect of pet food manufacturing is optimized for the health and well-being of dogs.
1. Precision in Ingredient Formulation:
The software used in modern dog food making machines can automatically calculate the correct proportions of vitamins, minerals, proteins, fats, and carbohydrates to meet the specific nutritional needs of various dog breeds, sizes, and life stages. By adjusting formulas according to these variables, machines help create tailored diets that support optimal health. For example, puppies, senior dogs, and active breeds all have unique dietary requirements that can be met with precision through automated production systems.
2. Elimination of Human Error:
When dog food is produced manually, there is a risk of human error in ingredient measurements, mixing, and cooking times, which can affect the nutritional quality of the final product. Dog food making machines eliminate these risks by automating these processes, reducing the likelihood of errors that could result in imbalanced or unsafe food for pets. The consistency of the food ensures that dogs receive a reliable and predictable source of nutrition with every meal.
3. Enhanced Food Safety Measures:
Food safety is a critical concern for both pets and pet owners. Dog food making machines use advanced features such as automatic temperature control, ingredient verification systems, and contamination detection mechanisms to ensure that food is safe to eat. These machines can also monitor and maintain ideal environmental conditions throughout the production process, reducing the chances of contamination from external factors such as moisture, dust, or foreign objects.
Case Study: How Automation Has Improved Pet Food Safety and Nutrition
Consider the example of a large-scale dog food manufacturer that implemented automated food making machines in their production line. Prior to automation, they faced challenges with ingredient consistency, quality control, and the risk of contamination. However, after integrating automated systems, the company saw a significant improvement in the consistency of their product's nutritional content and food safety.
1. Consistent Nutrient Retention:
Using extruders, the company was able to keep cooking times and temperatures uniform across all production batches, which allowed them to retain more nutrients in the food. This not only improved the overall quality of the dog food but also enhanced its digestibility, making it easier for dogs to absorb essential vitamins and minerals.
2. Increased Food Safety:
Automation also led to tighter food safety controls. The machines automatically detect foreign objects and ensure that the food is cooked at the right temperature to eliminate pathogens. These safety measures significantly reduced the chances of contamination, ensuring that the food remained safe and healthy for pets.
Conclusion: The Future of Pet Food Manufacturing
The future of dog food manufacturing lies in increased automation and precision. As technology continues to evolve, we can expect dog food making machines to become even more efficient in producing nutritionally complete and safe meals for pets. With benefits such as enhanced food safety, consistent quality, and tailored formulations, these machines are playing a vital role in promoting better pet health.
For pet owners, it is reassuring to know that advancements in food manufacturing technology are making it easier to provide their dogs with the best nutrition possible. As we look toward the future, these machines will continue to evolve, ensuring that pets live longer, healthier lives.
Kontakt
If you're interested in learning more about how our dog food making machines can enhance the nutritional quality and safety of your pet food production, feel free to contact us today! We're here to help you create the healthiest food for your dogs.
Dog food making machines improve the nutritional quality and safety of pet food.Wahr
Through precision automation, these machines ensure the consistency of nutrients, eliminate human error, and maintain food safety standards, which are essential for pet health.
Fazit
In conclusion, understanding the inner workings of a dog food making machine is key for anyone in the pet food production industry. These machines are not just essential tools but are also the backbone of high-quality, mass-produced dog food. By ensuring optimal ingredient mixing, extrusion, and drying processes, they allow manufacturers to meet the growing demand for nutritious and consistent pet food products.
If you're considering investing in a dog food making machine for your production line, it's important to assess your production needs, including the types of food you wish to produce, the machine's capabilities, and the scale of your operation.
Kontakt
If you have any questions or are interested in learning more about dog food making machines, feel free to reach out to us. We offer professional consultation and high-quality machinery to help your pet food production business thrive!