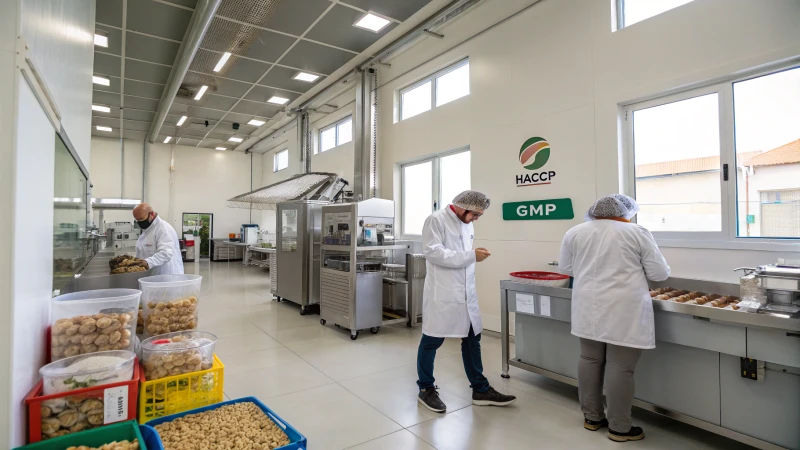
In the competitive world of pet food production, minimizing downtime is crucial for maintaining operational efficiency, reducing costs, and ensuring a consistent product supply. Unexpected halts in production can lead to missed deadlines, increased operational costs, and, ultimately, lost revenue. Therefore, it’s essential to implement strategies that streamline processes and enhance machine reliability. This article delves into actionable strategies that can minimize downtime, improve production efficiency, and boost profitability in pet food manufacturing.
To minimize downtime in pet food production, it is essential to implement a combination of proactive maintenance, proper equipment training, production monitoring, and process optimization. These strategies ensure the equipment is always running at peak performance, while potential issues are identified and corrected before they result in unscheduled stoppages.
By focusing on these areas, pet food manufacturers can not only reduce downtime but also create a more resilient production system capable of meeting customer demands consistently. In this article, we will explore several key approaches that can significantly reduce downtime and improve overall productivity. Keep reading to learn how to effectively optimize your production processes.
1. Proactive Maintenance and Predictive Analytics
One of the leading causes of downtime in pet food production is equipment failure. Malfunctioning machinery can halt the entire production line, creating long delays that affect delivery schedules. To prevent this, proactive maintenance is essential. Regular inspections and timely servicing of equipment can help identify issues early and fix them before they lead to unexpected breakdowns.
Additionally, predictive maintenance technologies are an effective way to minimize downtime. Predictive maintenance relies on advanced sensors, Internet of Things (IoT) devices, and data analytics to monitor equipment health in real-time. By analyzing trends in data, manufacturers can predict when a piece of equipment is likely to fail and schedule maintenance before it happens. This approach is not only cost-effective but also improves the lifespan of equipment, making it a smart long-term investment for pet food manufacturers.
2. Employee Training and Awareness
Employee errors are another significant cause of downtime in production environments. Operators may misuse machinery, leading to delays or even damage to the equipment. To minimize this risk, manufacturers should invest in comprehensive employee training programs. Proper training ensures that employees understand how to operate equipment correctly, troubleshoot minor issues, and adhere to safety protocols that prevent accidents and delays.
Furthermore, creating a culture of continuous learning and fostering awareness about the importance of minimizing downtime can make a significant difference. When workers are knowledgeable about the direct impact their actions have on production efficiency, they tend to be more cautious and proactive in their duties. Regular refresher courses and workshops can help maintain high skill levels and reduce human error.
3. Streamlining Production Processes
Streamlining production processes is an essential step in reducing downtime. Every stage of pet food production, from raw material storage to packaging, should be evaluated for inefficiencies that can slow down the entire operation. Implementing lean manufacturing principles, such as the 5S methodology (Sort, Set in order, Shine, Standardize, and Sustain), can help optimize workflows and eliminate wasteful practices.
Moreover, automating repetitive tasks wherever possible can significantly reduce human-induced downtime. Robotics and automated systems can handle tasks such as sorting, mixing, and packaging, ensuring that production moves smoothly without unnecessary interruptions. Automation also allows manufacturers to maintain consistent product quality and faster production rates.
4. Effective Inventory Management
A shortage of ingredients or packaging materials can bring production to a standstill. Effective inventory management is therefore a crucial element in minimizing downtime. Manufacturers should employ real-time inventory tracking systems to monitor stock levels of raw materials, ingredients, and packaging materials. These systems can alert production managers when stocks are running low, enabling them to order new materials in advance and avoid halting production.
It is also advisable to maintain buffer stock for key ingredients or materials that may have lead times for procurement. Strategic relationships with suppliers and a well-organized warehouse management system ensure that the necessary materials are always available when required.
5. Performance Monitoring and Key Performance Indicators (KPIs)
Establishing clear Key Performance Indicators (KPIs) is another effective way to monitor and reduce downtime. KPIs allow manufacturers to track and analyze different aspects of production, such as machine uptime, production cycle time, and yield loss. By reviewing these metrics regularly, manufacturers can identify bottlenecks and inefficiencies that cause delays and address them promptly.
Modern Manufacturing Execution Systems (MES) often come equipped with real-time performance monitoring tools that can track these KPIs. By leveraging these tools, manufacturers can quickly respond to problems, make data-driven decisions, and continuously improve production efficiency.
6. Scheduling and Batch Optimization
Downtime can also result from inefficient scheduling, such as overlapping tasks or lengthy changeovers. Pet food production lines often work in batch processes, and managing these batches efficiently is key to reducing downtime. Manufacturers can implement batch optimization techniques to ensure that each batch is produced as quickly as possible with minimal downtime between transitions.
Changeovers, when switching from one product type or flavor to another, can be time-consuming and costly. Reducing the time required for these changeovers through better scheduling and optimized equipment setups can help increase production uptime. Manufacturers can also explore equipment that supports faster changeovers, such as quick-release mechanisms and automated settings.
7. Emergency Response Plans
Despite all preventive measures, some downtime may still occur due to unforeseen circumstances. Having a well-established emergency response plan is essential for quickly addressing issues and getting production back on track. Emergency response teams should be well-trained and prepared to troubleshoot and resolve issues quickly.
The plan should include predefined procedures for common equipment failures, such as motor burnout, conveyor belt jams, or power outages. Regular emergency drills ensure that the team remains prepared and that equipment downtime is minimized.
8. Regular Audits and Continuous Improvement
Lastly, continuous improvement practices such as regular audits and root cause analysis of downtime events should be integrated into the company's culture. By regularly auditing production processes, manufacturers can identify recurring issues and areas for improvement. Root cause analysis helps identify the underlying reasons for downtime, whether related to equipment, materials, or human error. This approach allows manufacturers to make long-term changes that will prevent future disruptions.
Example of Downtime Cost Breakdown:
Downtime Cause | Average Time Lost | Cost Per Hour | Total Cost per Day |
---|---|---|---|
Equipment Failure | 3 hours | $500 | $1,500 |
Changeovers | 2 hours | $400 | $800 |
Operator Error | 1 hour | $350 | $350 |
Supply Chain Issues | 4 hours | $450 | $1,800 |
Total | 10 hours | $4,450 |
In the table above, you can see how different causes of downtime impact the cost of operations. By minimizing these issues, manufacturers can save a significant amount of money and increase overall profitability.
Fazit
Minimizing downtime in pet food production requires a multifaceted approach that includes preventive maintenance, employee training, production optimization, inventory management, and performance monitoring. By integrating these strategies, pet food manufacturers can enhance operational efficiency, reduce costs, and ensure consistent product availability. As the pet food market continues to grow, manufacturers who prioritize minimizing downtime will be better equipped to meet consumer demand and stay ahead of the competition.
If you're looking to improve your pet food production processes and reduce downtime, reach out to us. We specialize in providing tailored solutions that help businesses optimize their production lines and increase profitability. Contact us today to learn more!