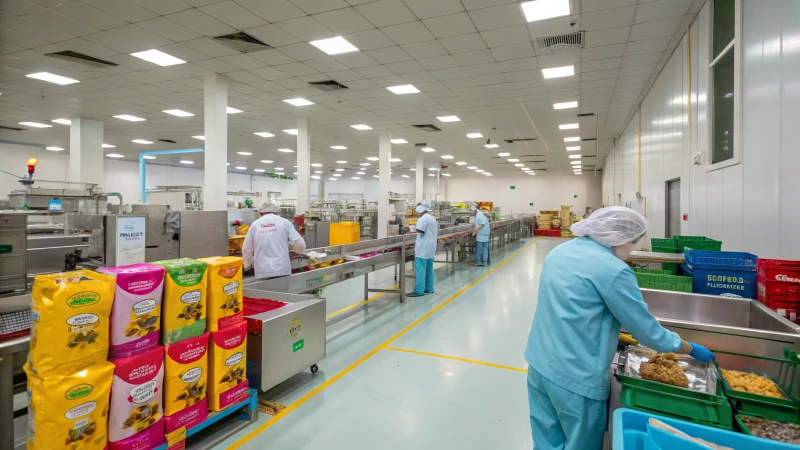
As the pet food industry continues to expand, the need for efficient and sustainable production methods has become more critical. Leading pet food manufacturers have invested in state-of-the-art facilities that not only increase output but also focus on product quality, safety, and innovation. These production facilities are designed to address the growing demand for premium, nutritionally balanced pet foods while also maintaining high standards in terms of production efficiency and environmental responsibility. But what lessons can be learned from the most successful pet food production facilities? In this article, we explore key practices, strategies, and technologies that set top-tier facilities apart.
The most successful pet food production facilities share several common factors: effective use of automation and robotics, strict quality control measures, sustainable practices, and continuous innovation. By learning from their successes, manufacturers can optimize their own operations and meet both consumer demand and regulatory requirements with increased efficiency and reliability.
Pet food production has become a highly sophisticated industry, with manufacturers continuously seeking new ways to refine their processes. Successful facilities don't just focus on scaling up production—they emphasize producing high-quality food in a way that is both sustainable and cost-efficient. Below, we explore some of the most crucial lessons that can be drawn from leading pet food production facilities.
1. The Power of Automation and Robotics in Streamlining Production
One of the most notable lessons from successful pet food production facilities is the extensive use of automation and robotics. Modern production lines have seen the integration of smart robots, automated conveyors, and AI-powered quality control systems. This has revolutionized the speed, precision, and flexibility of manufacturing processes.
Automation allows for significant reductions in labor costs, as machines handle repetitive tasks that were once performed manually. This can include tasks like sorting ingredients, mixing, portioning, and packaging. For instance, robotic arms can precisely measure and dispense ingredients, ensuring consistent recipe formulations every time. AI-based vision systems are also used to monitor the product as it moves down the production line, detecting defects or deviations that human workers might miss.
Lesson Learned: Integrating automation and robotics not only improves efficiency but also minimizes human error, ensuring more consistent and higher-quality products.
2. Emphasizing Strict Quality Control and Food Safety Measures
Top-tier pet food facilities prioritize quality control and food safety at every step of the production process. Stringent quality assurance (QA) protocols are in place, from the selection of raw ingredients to the final packaging. Manufacturers in the leading facilities understand that even minor lapses in quality can result in major risks, such as product recalls or damage to their brand reputation.
Many successful facilities use real-time monitoring systems to track temperature, humidity, and other critical factors that affect ingredient quality and safety. This includes ensuring that meat, vegetables, and other perishable ingredients are stored and processed under optimal conditions. Moreover, hazard analysis and critical control point (HACCP) systems are implemented to prevent contamination at any point during the production process.
For example, regular microbiological testing of products and production equipment is conducted to detect the presence of harmful pathogens like Salmonella or E. coli. By ensuring stringent testing protocols, these facilities can confidently claim that their pet foods meet or exceed all regulatory standards.
Lesson Learned: Maintaining high-quality standards and rigorous food safety practices is non-negotiable. A proactive approach to monitoring and testing can prevent costly recalls and ensure customer trust.
3. Sustainable Manufacturing Practices and Waste Reduction
Sustainability is an increasing focus for many manufacturers, and the best facilities are leading the way in reducing their environmental footprint. From sourcing ingredients responsibly to adopting energy-efficient production techniques, sustainability has become a key driver in pet food production.
Leading facilities have implemented several green initiatives that reduce waste, conserve water, and lower carbon emissions. For example, some pet food manufacturers use closed-loop systems to recycle water and minimize water waste during the cooking and cleaning processes. Others use biologisch abbaubare Verpackung to reduce plastic waste, in line with growing consumer demand for eco-friendly packaging options.
Another crucial aspect of sustainability is waste reduction. Many successful facilities have adopted practices such as by-product utilization, where scraps or unused ingredients are turned into animal feed, compost, or energy through biomass systems. By reducing waste, these facilities not only save on material costs but also contribute to a circular economy.
Lesson Learned: Incorporating sustainability practices into the production process can not only help the environment but also reduce costs, improve brand reputation, and align with consumer preferences for eco-friendly products.
4. Flexibility and Agility in Production
The pet food market is constantly evolving, driven by shifting consumer preferences and new dietary trends. Successful pet food production facilities are designed to be flexible and agile, enabling manufacturers to quickly adapt to new product demands or adjust production schedules to meet seasonal fluctuations.
For instance, manufacturers may need to shift from producing dry kibble to wet food or vice versa based on market demand. Leading facilities are equipped with modular production lines that can be easily reconfigured for different products. This enables them to offer a wide range of pet food types, such as organic, grain-free, or breed-specific formulas, without significantly increasing overhead costs.
Additionally, these facilities often implement just-in-time (JIT) manufacturing, where production schedules are closely tied to inventory needs. This reduces excess inventory and ensures that only the required quantities are produced, leading to better resource utilization and less waste.
Lesson Learned: To remain competitive, facilities must be adaptable. The ability to quickly switch between product types and adjust production schedules allows for better responsiveness to changing consumer trends.
5. Data-Driven Decision Making and Continuous Improvement
In today’s data-driven world, the most successful pet food production facilities use advanced analytics to track performance and identify areas for improvement. By collecting and analyzing data at every step of production, manufacturers can uncover inefficiencies, forecast demand, and optimize the entire supply chain.
Many facilities use Internet der Dinge (IoT) devices to collect real-time data from machinery, sensors, and production lines. This data is then analyzed to identify patterns and trends, which can inform decisions about everything from raw material procurement to energy consumption.
Moreover, continuous improvement programs like Six Sigma oder Lean Manufacturing are commonly employed to drive process optimization and eliminate waste. These methodologies focus on reducing variation and improving processes, helping companies meet their goals for quality, efficiency, and cost reduction.
Lesson Learned: Leveraging data analytics for decision-making and continuously improving operational processes is essential for staying ahead of competition and maintaining a high standard of production.
6. Employee Training and Engagement
While automation and robotics have transformed pet food production, human expertise is still crucial. Successful facilities understand that their employees are the backbone of the operation, and they invest in continuous training and skill development.
Workers are trained in the latest manufacturing technologies, food safety standards, and operational procedures. Additionally, successful facilities foster a culture of innovation, encouraging employees to identify inefficiencies or suggest improvements to existing processes.
Moreover, cross-functional collaboration is a key feature in these facilities. Production workers, engineers, and quality control teams often work together to troubleshoot problems and improve production workflows, creating a more cohesive and productive environment.
Lesson Learned: A well-trained and motivated workforce is essential to ensure that production runs smoothly, quality standards are maintained, and continuous improvement is achieved.
Fazit
The most successful pet food production facilities provide valuable lessons for manufacturers looking to improve their operations. Key takeaways include the importance of automation, rigorous quality control, sustainability, flexibility, data-driven decision-making, and employee engagement. By focusing on these areas, manufacturers can enhance operational efficiency, meet consumer demands for high-quality products, and stay competitive in a rapidly changing market.
Call to Action:
If you're looking to optimize your pet food production line and implement the latest best practices, contact us today. Our team of experts can guide you through the process, helping you integrate cutting-edge technologies and strategies that will improve efficiency, product quality, and sustainability. Reach out to learn more!