Have you ever wondered how your favorite snacks or pet foods are made? It all starts with a fascinating process called extrusion.
The food industry primarily uses two types of extruders: single-screw and twin-screw extruders. Single-screw extruders are typically used for straightforward processes, whereas twin-screw extruders offer more flexibility and control, making them ideal for complex formulations and products.
When I first learned about extrusion, I was amazed at how such technology could transform raw ingredients into delicious snacks or essential pet foods. Just like crafting a perfect recipe requires the right tools and techniques, producing these foods involves choosing the right type of extruder. Each type has its own strengths, catering to different needs in food production. Whether it's crafting the simplest treats or the most intricate blends, these machines play a crucial role. Let's delve deeper into their unique applications and see how they revolutionize what ends up on our tables.
Single-screw extruders are used for complex formulations.Falsk
Single-screw extruders are typically used for straightforward processes.
Twin-screw extruders offer more flexibility than single-screw.Sandt
Twin-screw extruders provide greater control and flexibility for complex products.
Hvordan fungerer ekstrudere med én skrue?
Ever wondered what makes a single-screw extruder tick? These machines are at the heart of transforming raw materials into amazing products, and I’m here to take you on a journey through their inner workings.
Single-screw extruders operate by feeding raw materials into a barrel where they are heated and mixed by a rotating screw. This process transforms the materials into a homogeneous melt, which is then shaped through a die.
The Fundamentals of Single-Screw Extruders
I remember the first time I saw a single-screw extruder in action; it was mesmerizing to watch the raw materials dance along the screw inside the barrel. At its core, the extruder has a barrel and screw1. The screw spins energetically, pushing materials forward as they heat up and blend together. This rotation is driven by a motor that’s finely tuned, much like a well-oiled orchestra, ensuring everything works in perfect harmony.
The Role of the Screw
The screw is like the unsung hero in this process. It’s divided into sections, each with its own job:
Section | Funktion |
---|---|
Feed Section | Gently nudges raw materials into the extruder |
Kompression | Cranks up heat and pressure to melt materials |
Måling | Keeps things steady before reaching the die |
Heating and Cooling Systems
Temperature control is crucial—I learned this the hard way during an early project when an oversight nearly cost us a batch! Heating elements2 are wrapped around the barrel to achieve just the right melting point, while cooling systems step in like guardians to prevent overheating disasters. It's all about finding that sweet spot through careful calibration.
Material Flow and Die Design
When the material is finally melted, it’s pushed through a die to take on its final shape. Die design isn’t just about looks; it’s about getting those dimensions and characteristics spot on. Different materials need unique die setups, and mastering these details can really boost production efficiency.
Advantages of Single-Screw Extruders
Although twin-screw extruders might steal the spotlight sometimes, single-screw models are often my go-to for their simplicity and cost-effectiveness. They excel in mixing and processing capabilities3 for a wide range of materials, making them ideal for straightforward manufacturing tasks. It’s like choosing a trusty, reliable friend who’s always got your back.
The screw in an extruder is powered by a motor.Sandt
The motor provides the necessary rotation for the screw to move materials.
Single-screw extruders are more complex than twin-screw models.Falsk
Single-screw extruders are simpler and more cost-effective than twin-screw models.
What are the advantages of twin-screw extruders?
Picture this: a world where your production process is not just efficient but almost magical in its versatility and output.
Twin-screw extruders offer superior mixing capabilities, flexibility in handling diverse materials, and enhanced control over process parameters compared to single-screw extruders. These advantages lead to improved product quality, higher output rates, and cost efficiency.
Enhanced Mixing and Homogenization
I remember the first time I saw a twin-screw extruder in action—it was like watching a perfectly choreographed dance. The intermeshing screws worked together seamlessly, ensuring every ingredient was mixed uniformly. This technology is a game-changer, especially in industries like pet food and plastics, where consistency is king. It's the difference between a product that's "good enough" and one that's outstanding.
Twin-screw extruders excel in mixing capabilities4 thanks to their intermeshing screw design. This ensures uniform distribution of materials, enhancing product consistency.
Versatility in Material Handling
When I first explored the capabilities of twin-screw extruders, I was amazed at how they could handle such a diverse range of materials. Imagine being able to switch between processing wet, dry, viscous, or even chunky ingredients without missing a beat. This flexibility is priceless for companies like mine that need to adapt quickly to market demands.
Unlike single-screw extruders, twin-screw versions can process a wider range of materials with varying viscosities and compositions. This makes them ideal for industries requiring flexibility in production processes, such as fødevareforarbejdning5 and materials engineering.
Improved Process Control
Having precise control over parameters like temperature and pressure feels like having a superpower in manufacturing. With twin-screw extruders, I can fine-tune each batch to perfection, reducing waste and boosting efficiency.
With twin-screw extruders, operators have greater control over process parameters like temperature, pressure, and feed rate. This precise control enables manufacturers to fine-tune production settings for optimal outcomes.
Higher Output Rates
In high-demand environments where the pressure to deliver is relentless, twin-screw extruders stand out. Their design allows for higher throughput without sacrificing quality.
Due to their design, twin-screw extruders typically offer higher throughput than single-screw models:
Funktion | Ekstruder med to skruer | Ekstruder med én skrue |
---|---|---|
Mulighed for at blande | Superior | Grundlæggende |
Material Range | Diverse | Begrænset |
Processtyring | Enhanced | Standard |
Output Rate | Højere | Moderat |
Omkostningseffektivitet
At first glance, the initial cost of a twin-screw extruder might seem steep. But trust me; the long-term savings are substantial. They use less energy and minimize material waste.
While initial investment costs for twin-screw extruders might be higher, their efficiency leads to lower operational costs through reduced energy consumption and minimized raw material waste.
Embracing twin-screw technology has been one of my best decisions. In an ever-evolving industry landscape, staying ahead means adopting tools that not only meet but exceed production demands.
Ekstrudere med to skruer giver overlegen blandingsevne.Sandt
Their intermeshing screw design ensures uniform material distribution.
Single-screw extruders handle a wider range of materials.Falsk
Twin-screw extruders can process materials with varying viscosities.
Can Co-rotating and Counter-rotating Extruders Be Used in Food Processing?
Have you ever wondered how your favorite snacks are made? Extrusion technology plays a key role!
Both co-rotating and counter-rotating extruders can be used in food processing. Co-rotating extruders are ideal for mixing and blending, while counter-rotating extruders offer precise control over shear and temperature, essential for certain textures.
Understanding Co-rotating Extruders in Food Processing
I remember the first time I saw a co-rotating extruder in action—it was like witnessing a culinary ballet. The screws, rotating in perfect harmony, were expertly mixing ingredients to create a smooth, uniform blend. These extruders are champions when it comes to mixing and blending materials6, making them indispensable for achieving that perfect crunch in snack foods and cereals.
Counter-rotating Extruders: Precision at Its Best
On the other hand, counter-rotating extruders remind me of those meticulous chefs who measure every ingredient down to the last grain of salt. With screws turning in opposite directions, they provide exquisite control over shear and temperature. This precision is crucial when crafting foods with specific textures, such as pasta or delicate pet treats. It's like having a gentle hand guiding sensitive materials through the process without losing their integrity.
Comparing Their Applications
Selecting the right type of extruder is like choosing the perfect tool from a chef's arsenal. Each offers unique advantages in food processing, from achieving uniform mixtures to maintaining product integrity during extrusion. Understanding their differences can significantly enhance production efficiency and product quality.
Funktion | Co-rotating Extruders | Counter-rotating Extruders |
---|---|---|
Shear Control | Høj | Moderat |
Temperaturkontrol | Moderat | Høj |
Ideel til | Mixing, Blending, High-Shear Processes | Sensitive Materials, Texture Precision |
I've learned that by knowing which tool to use, I can create magic in the kitchen—or rather, in the factory—every single time.
Co-rotating extruders are ideal for sensitive materials.Falsk
Co-rotating extruders are better for mixing, not handling sensitive materials.
Counter-rotating extruders offer high shear control.Falsk
Counter-rotating extruders provide moderate shear control, not high.
How Do Extruders Revolutionize Pet Food Production?
Ever wondered how those perfectly shaped pet kibbles come to be?
Extruders play a crucial role in pet food production by transforming raw ingredients into specific shapes and textures. They ensure uniform cooking and enhance the nutritional value and digestibility of pet foods.
Forståelse af ekstruderingsprocessen
I remember the first time I stood next to one of these incredible machines. It was like watching a grand orchestra at work, each part playing its role to perfection. The extrusion process is pretty much a culinary symphony. Ingredients are mixed and then forced through a die, which shapes them into those familiar kibbles and bits our pets love. The whole process ensures that the food cooks uniformly, maintaining a consistent texture across each batch. This high-pressure cooking doesn't just look impressive—it also reduces anti-nutritional factors, making the food more digestible for our furry friends.
Enhancing Nutritional Value
Reflecting on my journey with extruders, I recall how this process has truly transformed pet nutrition. By gelatinizing starches, we make the nutrients more accessible, enhancing both digestibility and taste. It's like giving your pet a gourmet meal with every bite! We can tweak the process to preserve or boost specific nutrients tailored to different pet diets7. Whether it's for an energetic puppy or a senior cat, extrusion helps create the perfect meal.
Efficiency and Quality Control
Extruders are not just about making food; they're about making it better and faster. I’ve seen firsthand how they can streamline production, cutting down cooking times while minimizing waste. This precision ensures every morsel meets rigorous quality standards, crucial for manufacturers like us who aim to comply with international regulations. It's reassuring to know that each batch produced is consistent in quality and taste.
Funktion | Fordel |
---|---|
Consistent Cooking | Uniform texture |
Gelatinization | Enhanced digestibility |
High Pressure | Opbevaring af næringsstoffer |
Innovations in Extrusion Technology
One of the most exciting things I've witnessed in my career is the evolution of extruder technology. Modern extruders now use advanced systems like twin-screw technology, allowing us to experiment with a diverse array of ingredients. This innovation has opened doors to creating specialized products, from grain-free options to hypoallergenic diets.
By optimizing these variables, we can produce high-quality pet food that satisfies both pets and their owners.
Market Adaptability
The adaptability of extruders is something I find truly remarkable. They can handle a wide range of ingredients, making them indispensable as consumer demands shift towards more personalized pet diets. Manufacturers can quickly pivot to meet these trends and develop innovative products that keep pets happy and healthy.
By embracing extruder technology8, businesses in emerging markets can seize the growing demand for premium pet food products, carving out a competitive edge in the industry.
Extrusion increases pet food digestibility.Sandt
Extrusion gelatinizes starches, improving digestibility and palatability.
Extruders reduce nutritional value in pet food.Falsk
Extruders enhance nutrient bioavailability and retention through controlled cooking.
How Does Extruder Technology Enhance Product Innovation?
Imagine transforming everyday materials into innovative products that captivate consumers—extruder technology is doing just that.
Extruder technology enhances product innovation by providing versatile processing capabilities, enabling the creation of diverse textures, shapes, and formulations. This flexibility allows manufacturers to efficiently develop new products and optimize existing ones, meeting consumer demands for unique and customized offerings.
Versatile Processing Capabilities
When I first witnessed an extruder in action, it was like watching magic unfold. You feed in the raw materials, and out comes something entirely different—tailored to specific needs, whether that's a crunchy snack or a pet treat with a unique texture. The beauty of extruder technology lies in its ability to experiment with endless formulations. This means you can create something truly novel. I remember being amazed at how it could handle both dry and wet pet foods9 with ease. Imagine being able to craft a bespoke treat that your pet goes wild for!
Funktion | Beskrivelse |
---|---|
Fleksibilitet | Adapts to different materials and formulations |
Effektivitet | Streamlines production processes |
Tilpasning | Allows for unique product development |
Enhancing Product Quality and Consistency
I’ve always valued consistency, whether in life or in products. With extruder technology, achieving this in manufacturing is a given. The precise control over processing parameters ensures that each product not only looks the same but also tastes and feels just right. It reminds me of baking a cake where every ingredient must be perfectly measured to achieve that flawless slice every time. For example, snack foods10 can maintain their signature crunch and flavor, making them irresistible.
Fostering Sustainable Practices
Sustainability is more than just a buzzword; it's a necessity. I take pride in how extruders help reduce waste and energy use, paving the way for eco-friendly production. By incorporating sustainable ingredients, like alternative proteins or recycled materials, we’re not only innovating but also protecting our planet. In fields like biodegradable plastics, it’s empowering to see how extruders contribute to creating products that meet environmental standards.
Enabling Rapid Prototyping and Development
The thrill of seeing an idea come to life quickly is unparalleled. With extruders, rapid prototyping means we can test and tweak ideas at lightning speed—essential when timing is everything. This agility reminds me of those eureka moments where you have to capture and refine an idea before it slips away. It’s all about staying ahead, adapting swiftly to feedback and trends, ensuring that the next big thing doesn’t pass us by.
By using extruders for rapid prototyping, companies can swiftly adjust formulations or designs based on feedback or market trends. This agility supports continuous innovation cycles11, allowing businesses to stay ahead of competitors.
Broadening Market Opportunities
Extruder technology isn’t just about creating products; it’s about opening doors to new markets. Take plant-based foods—Ekstruderingsteknikker12 have revolutionized this space by replicating meat-like textures. It’s fascinating to think how these advancements cater not only to dietary changes but also encourage culinary creativity.
By embracing the vast capabilities of extruder technology, we’re not just keeping pace with consumer demands—we’re setting the stage for groundbreaking innovations that excite and inspire.
Extruders only process dry pet food.Falsk
Extruders can process both dry and wet pet food, offering versatility.
Extruder technology reduces waste in production.Sandt
Extruders minimize resource usage, contributing to sustainable practices.
What Are the Latest Trends in Extruder Technology?
I've always been fascinated by how technology reshapes industries, especially in the world of extrusion. It's like watching a thrilling series where each season brings more exciting twists!
Emerging trends in extruder technology include advancements in sustainability, energy efficiency, and digital integration. These innovations are crucial for industries aiming to enhance productivity while reducing environmental impact.
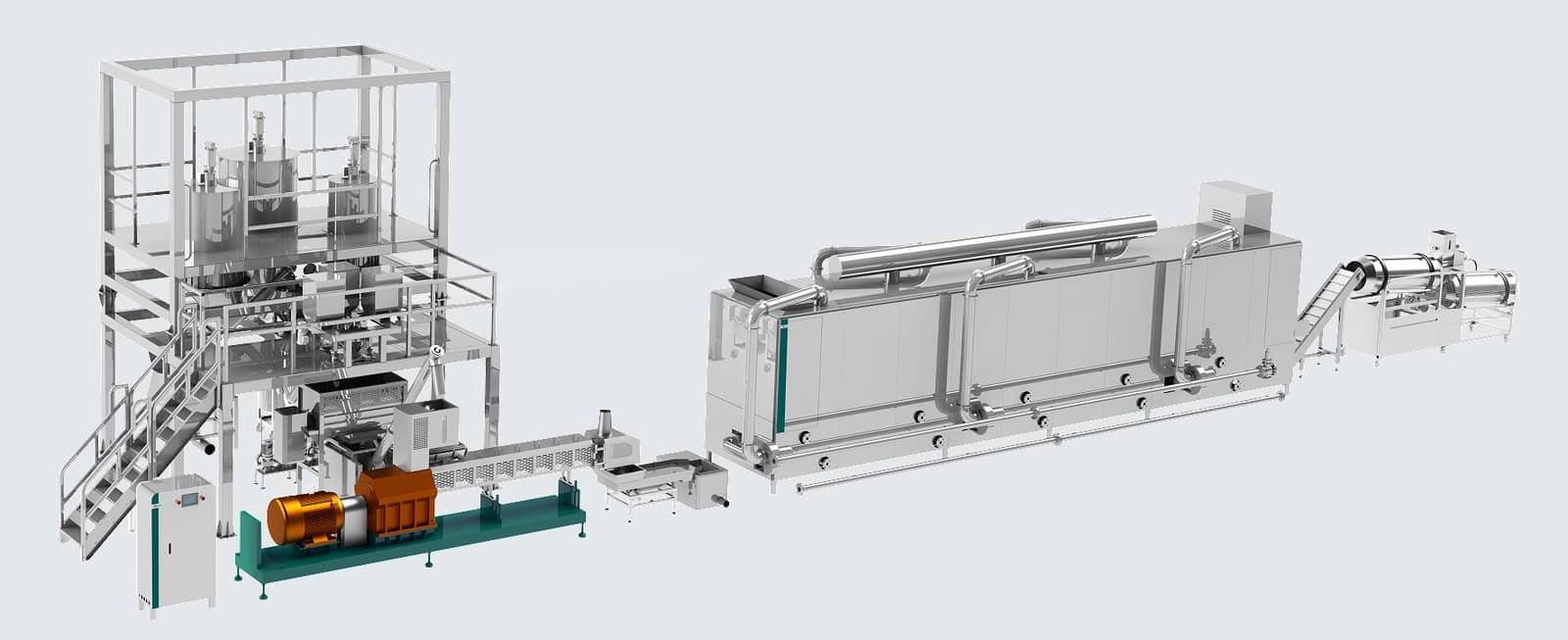
Sustainability in Extrusion
I remember visiting a manufacturing plant where the team was buzzing about their new sustainable extrusion line. The commitment to biodegradable materials13 was impressive, and seeing the reduced waste firsthand made me realize how far we've come. It's not just about being eco-friendly; it's about meeting a global call for more responsible production.
Energy Efficiency Enhancements
On another trip, I had a fascinating chat with an engineer who showed me how they've cut energy use in half with their new extruders. It's like switching from a gas-guzzler to a hybrid car! These advances aren't just green; they make financial sense, reducing costs while helping the planet.
Funktion | Traditional Extruders | Modern Extruders |
---|---|---|
Energiforbrug | Høj | Lav |
Material Waste | Significant | Minimal |
Product Consistency | Variabel | Høj |
Digital Integration and Automation
The other day, I watched a technician using smart sensors to monitor an extruder system from his tablet. Imagine predicting maintenance needs before breakdowns occur! This digital leap forward means less downtime and higher consistency—music to any manufacturer's ears.
Customization and Flexibility
I recall visiting a pet food company that catered to those picky eaters with unique flavors and textures. Their extruders could handle everything from crunchy kibble to chewy treats. This flexibility is a game-changer, allowing manufacturers to meet diverse consumer demands without missing a beat.
The Role of AI in Extruder Technology
Finally, let me tell you about the jaw-dropping moment when I first saw AI in action on the production floor. It was like having a super-smart assistant fine-tuning every detail for maximum efficiency. With AI14, companies aren't just saving on materials; they're optimizing entire operations, setting new standards for precision and output.
Keeping up with these trends is essential for anyone looking to maintain a competitive edge in the ever-evolving field of extrusion technology. As I continue to explore these advancements, I'm excited to see what the future holds—and I'm eager to share these insights with anyone interested in this dynamic industry!
Modern extruders use more energy than traditional ones.Falsk
Modern extruders are designed to be energy-efficient, reducing power use.
AI in extrusion reduces material waste significantly.Sandt
AI optimizes settings for precise specifications, minimizing waste.
Konklusion
The food industry utilizes single-screw and twin-screw extruders, each serving distinct purposes in processing ingredients for snacks and pet foods, enhancing product quality and efficiency.
-
Discover detailed insights into the key components that make up a single-screw extruder. ↩
-
Learn about the essential role of heating systems in maintaining material integrity during extrusion. ↩
-
Explore why single-screw extruders might be more advantageous for certain production needs. ↩
-
Understand the unique design features that enhance mixing capabilities, leading to better product consistency. ↩
-
Discover the flexibility and adaptability of twin-screw extruders in handling diverse food ingredients. ↩
-
Learn how co-rotating extruders excel in mixing and blending, offering advantages in high-shear processes. ↩
-
Discover how extrusion enhances nutrient retention and digestibility in pet foods. ↩
-
Understand how extrusion supports market adaptability and innovation. ↩
-
Explore how extruders efficiently handle both dry and wet pet food production, offering insights into process optimization. ↩
-
Learn about how extruder systems ensure consistent quality in snack foods like chips and puffs. ↩
-
Discover how extruders facilitate rapid prototyping and development for quicker time-to-market. ↩
-
Understand how extrusion techniques create meat-like textures in plant-based foods, enhancing culinary diversity. ↩
-
Discover eco-friendly manufacturing methods that reduce waste and costs, aligning with industry sustainability goals. ↩
-
Learn how AI optimizes extrusion settings, enhancing precision and efficiency in production processes. ↩