I remember when I first considered buying a pet food extruder, feeling both excited and overwhelmed by the investment.
The cost of a pet food extruder ranges from $10,000 to over $100,000, depending on factors such as capacity, features, and brand reputation. It's crucial to assess these variables alongside your production needs to make an informed purchase.
While understanding the basic price range is essential, evaluating the true value of a pet food extruder involves more than just upfront costs. Having walked through this process myself, I realized it was about envisioning the long-term benefits and how such a machine could fuel my business growth. With this guide, let's explore not only what influences these costs but also how the right extruder could be a game-changer for your operations.
Pet food extruders cost over $100,000.True
High-end pet food extruders can exceed $100,000 due to features.
Brand reputation doesn't affect extruder cost.False
Brand reputation significantly impacts the pricing of pet food extruders.
What Factors Influence the Price of a Pet Food Extruder?
Ever wondered why a pet food extruder's price can vary so much? Let me take you through the key factors that influence these costs.
The price of a pet food extruder is influenced by factors like production capacity, technology integration, material quality, brand reputation, and market demand. These elements affect cost and should be considered when investing.
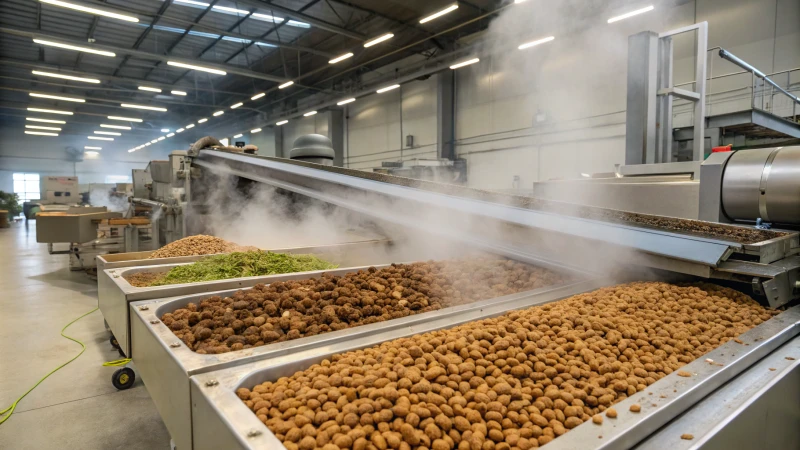
Production Capacity and Technology Integration
When I first started exploring the realm of pet food manufacturing, I was amazed by how much the production capacity of a pet food extruder could sway its price. Machines that pump out more kibble per hour naturally require more sophisticated engineering and materials. It's like comparing a compact car to a full-sized SUV. Sure, both will get you from point A to B, but the latter offers more room and power, albeit at a higher cost. Plus, when you throw in technology integration1—think automation and advanced controls—it feels like you're upgrading to a luxury model. While these bells and whistles might inflate the price tag, they promise efficiency and smoother operations in the long run.
Material Quality and Construction
In my journey with Darin Machinery, I've learned that not all materials are created equal. We pride ourselves on using top-notch materials like stainless steel, which might be pricier but offer unmatched durability. Imagine investing in cookware; you'd want pots and pans that last a lifetime without rusting or warping. Similarly, high-quality materials in our extruders ensure longevity and reliability, making them worth every penny.
Material Type | Impact on Cost |
---|---|
Stainless Steel | Higher (Durability) |
Plastic | Lower (Cost-effective) |
The precision with which these components are manufactured also plays a significant role in the final pricing.
Brand Reputation and Support
Reputation is everything in our line of work. When I think about it, partnering with giants like General Mills and Kellogg's has taught me the value of reliability and innovation. Established brands have built trust over decades, which allows them to command premium prices. But it's not just about the name; it's about the comprehensive support package that comes along—technical support2 and after-sales service that can often justify spending a little more upfront for peace of mind.
Market Demand and Geographical Considerations
Market dynamics are fascinating! Depending on where you're looking to set up shop, prices can fluctuate. In regions like the U.S. or Europe, where there's a high demand for premium pet food, extruder prices might tick upwards due to competitive pressures.
- High Demand Areas: U.S., Europe
- Emerging Markets: Southeast Asia, Latin America
On the flip side, if you're venturing into emerging markets like Southeast Asia or Latin America, you might find different pricing dynamics at play. Navigating these geographical differences is crucial for aligning your investments with your strategic goals.
Understanding these factors helps businesses evaluate whether an extruder’s price aligns with their operational goals and budget constraints. The interplay of these elements dictates not only the initial investment but also long-term operational efficiency and product quality. By analyzing each factor carefully, companies can choose an extruder that best suits their needs and ensures optimal performance in the pet food market.
For more insights on how material quality impacts machine performance3, explore industry analyses that discuss the latest advancements in machinery design.
Higher production capacity increases extruder cost.True
Machines with higher output capabilities are more complex and robust.
Plastic construction raises the price of an extruder.False
Plastic is cost-effective, leading to lower prices compared to metals.
How Does Production Capacity Affect Extruder Costs?
Ever wondered how the size of your production line can impact your wallet?
Production capacity significantly affects extruder costs by altering the scale of operations. Higher capacities typically reduce cost per unit due to economies of scale, while smaller capacities might incur higher per-unit costs due to less efficient production.
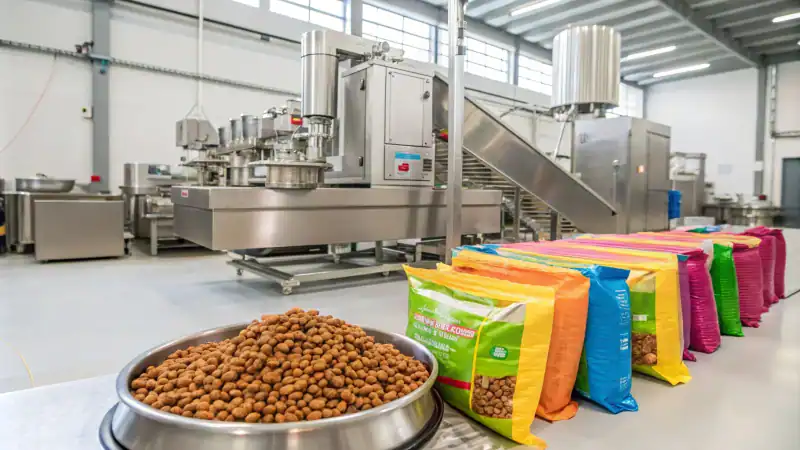
The Influence of Scale on Cost Efficiency
Picture this: I once had a project where I needed to scale up production from a small batch to something much larger. It was like turning a cozy home kitchen into a bustling restaurant kitchen overnight. One of the things I quickly learned was the magic of economies of scale. As I increased production, the cost per unit4 started to drop, similar to how buying ingredients in bulk saves money at the grocery store. Larger production capacities allow me to spread out those pesky fixed costs—like the initial investment in machinery and labor—over a greater volume.
For instance, if I run an extruder capable of churning out 10,000 units daily, it’s way more cost-effective than one that only produces 1,000 units. It's like having a super-efficient blender that doesn't use more energy or require more time just because you're making a bigger smoothie.
Production Capacity | Cost Per Unit |
---|---|
1,000 Units | Higher |
10,000 Units | Lower |
Impact of Operational Efficiency
Let me take you back to another time when I was figuring out how to get the most bang for my buck with high-capacity extruders. They’re usually equipped with advanced tech that speeds up production and minimizes waste, much like a well-oiled machine that never skips a beat. This efficiency translates into lower long-term costs, but there's a catch—having too much capacity without the demand can be like owning a sports car you never drive. It costs money but doesn’t bring in any returns. So, it's vital to strike a balance and ensure production aligns with market needs.
High-capacity extruders often incorporate advanced technologies that improve speed and consistency, leading to reduced waste and better energy efficiency5. However, it's crucial to balance production capacity with demand.
Customization and Flexibility Considerations
Here's another nugget from my experience: when dealing with high-capacity extruders, flexibility can sometimes take a back seat. These machines are fantastic at cranking out huge quantities of one product, but switching gears to produce something else often requires time and investment. It reminds me of trying to bake a cake in an oven set for pizza—possible but not optimal without adjustments.
Conversely, smaller-capacity extruders6 are like those nifty kitchen gadgets that can do a bit of everything. They offer the adaptability to change with market demands or introduce new products with minimal hassle.
In summary, understanding how production capacity affects extruder costs is about juggling several factors—economies of scale, operational efficiency, and the flexibility to pivot as needed. Navigating this balancing act ensures that I keep costs down while meeting business goals.
Future Trends in Extruder Technology
Looking forward, I'm keeping my eyes peeled for emerging technologies that promise to reshape how we think about production capacity and extruder costs. With automation and digitalization on the rise, these advancements could potentially offer savings and enhanced production capabilities across both high- and low-capacity extruders. By staying informed about these trends, I aim to unlock new efficiencies and keep pace with industry demands.
In this ever-evolving landscape, strategic planning is key. By understanding current capabilities and anticipating future needs, I can maintain a competitive edge and ensure my business thrives financially.
For those eager to explore this topic further, there are numerous resources detailing how production capacity impacts manufacturing costs and efficiencies—perfect for guiding strategic decisions in aligning manufacturing processes with market demands.
Higher production capacity reduces extruder cost per unit.True
Economies of scale lower the cost per unit as fixed costs spread over more units.
Low-capacity extruders offer more product flexibility.True
Smaller extruders can switch products easily, adapting to market changes quickly.
What Are the Key Features to Consider in a Pet Food Extruder?
Choosing the perfect pet food extruder isn't just a technical decision; it's about crafting the best for our furry friends. But what should you really be looking for?
Key features to consider in a pet food extruder include flexibility in processing different feed types, precise temperature control, efficient energy use, robust construction, and easy maintenance. These factors ensure high-quality output and operational efficiency.
Flexibility in Processing
I remember when I first encountered the challenge of diversifying my product line to meet a rapidly changing market. It was like being a chef with a single recipe book in a world demanding culinary diversity. That's where the importance of flexibility in a pet food extruder became clear. A versatile extruder allows me to experiment and cater to various feed types—from dry kibble to semi-moist treats. This flexibility isn't just a business strategy; it's my way of ensuring every pet gets the unique blend they deserve. Look for extruders that offer adjustable settings; it's akin to having a multi-tool at your disposal.
Precise Temperature Control
Cooking is an art, and so is producing pet food. The first time I realized this was during a visit to a local manufacturer who showed me how precise temperature control could make or break the quality of the final product. It's not just about cooking but preserving those vital nutrients our pets need. With an extruder that offers precise temperature control, I can optimize cooking processes, ensuring that each batch retains the perfect texture and nutrition.
Energy Efficiency
Energy costs can feel like a never-ending saga. I used to dread the monthly bills until I discovered that an energy-efficient extruder could significantly reduce operational costs. It's like switching from a gas-guzzler to an electric car; you notice the difference right away. Look for machines equipped with energy-saving technologies; they're an investment that pays dividends over time.
Feature | Benefit |
---|---|
Flexible Settings | Product diversification opportunities7 |
Temperature Control | Nutrient retention and quality assurance8 |
Energy Efficiency | Lower operational costs9 |
Robust Construction
Imagine investing in something that doesn’t stand the test of time—frustrating, right? That's why I emphasize robust construction when selecting an extruder. A well-built machine is like a reliable old friend—always there when you need it, minimizing downtime with its durability. Check for high-quality materials and construction standards because these are your insurance against unexpected breakdowns.
Easy Maintenance
As much as I love getting hands-on, there's nothing worse than equipment that requires extensive training just to maintain it. Regular maintenance should enhance productivity, not hinder it. I learned this lesson after spending countless hours training staff on overly complex systems. Now, I seek out extruders designed for easy maintenance, featuring quick-access panels and easily replaceable parts. It keeps everything running smoothly and lets me focus on what truly matters—creating great products.
A versatile extruder can handle both dry and semi-moist feeds.True
Versatility in handling various feed types is crucial for product diversification.
Energy-efficient extruders increase operational costs significantly.False
Energy-efficient extruders reduce operational costs, not increase them.
Is Investing in a High-End Extruder Worth It for My Business?
Standing at the crossroads of investment decisions can feel daunting, especially when it involves something as crucial as a high-end extruder.
Investing in a high-end extruder can be beneficial for businesses focused on high-quality production and capacity. It enhances efficiency, ensures consistent quality, and may provide a competitive advantage in demanding markets.
Understanding High-End Extruders
When I first started looking into high-end extruders, it felt like diving into an ocean of technical specifications and jargon. But soon, I realized these machines are essentially the backbone of efficient and precise material processing. Equipped with cutting-edge technology, they offer unparalleled control over production—a game-changer for industries like ours that demand top-tier output.
Feature | Benefit |
---|---|
Precision | Consistent product quality |
Efficiency | Faster production cycles |
Durability | Long-term cost savings |
Benefits of High-End Extruders
Enhanced Efficiency: I recall speaking with a peer who upgraded their equipment and couldn’t stop raving about the increase in production speed. It’s amazing how optimizing material usage can slingshot your operational costs down. For us, that meant imagining higher profitability10 margins, especially when dealing with large volumes.
Product Quality: I remember being particularly impressed by the control these extruders offer over product dimensions and texture. It’s not just about making more; it’s about making better. In sectors like pet food, where quality is non-negotiable, this level of consistency is invaluable.
Technological Advancements: What truly excites me is the leap in technology—automated controls and real-time monitoring are not just buzzwords but realities that help us stay ahead. Embracing these features ensures we’re not just keeping pace with competitors but leading the charge.
Cost Considerations
I won’t sugarcoat it—the initial investment is hefty. But I like to think of it as planting a seed. You need to weigh factors such as:
- Return on Investment (ROI): I found it helpful to map out how quickly the extruder could pay for itself through increased productivity and lowered operational costs.
- Market Demand: Honestly, understanding our market was pivotal. If we're aiming for premium segments11, these machines aren't just beneficial—they're essential.
Industry Insights
In my conversations with others in the pet food manufacturing industry, I've learned that investing in high-end extruders often leads to significant improvements in production efficiency and innovation. Companies collaborating with giants like General Mills or Kellogg’s usually rely on such equipment to meet their rigorous standards.
Exploring how other businesses leverage these technologies through case studies or industry reports12 has been incredibly enlightening and inspiring.
High-end extruders improve production speed.True
High-end extruders enhance efficiency, increasing production speed and reducing waste.
Initial costs of high-end extruders are negligible.False
The initial investment is significant, but benefits may outweigh costs long-term.
How Can an Extruder Impact My ROI in the Pet Food Industry?
Let me tell you how a simple piece of machinery could revolutionize your pet food business, making it more efficient and profitable.
An extruder can significantly impact your ROI in the pet food industry by improving production efficiency, reducing waste, and enabling product innovation. This technology allows for precise control over ingredients, texture, and form, leading to cost savings and higher product quality.
Understanding Extrusion Technology
I remember the first time I saw an extruder13 in action; it was like witnessing magic in the pet food production process. Extrusion is this high-temperature, short-time marvel that mixes raw materials and shapes them under heat and pressure. It transforms ingredients into uniform pet food that's not only visually appealing but also packed with nutrients and easily digestible.
Benefits of Extruders on ROI
Think of extrusion technology as your secret weapon for boosting efficiency and profits. Here's how it can transform your business:
- Efficiency and Scalability: Extruders let you run a tight ship with continuous production, which means less downtime and lower labor costs. The more streamlined your operations, the better your economies of scale.
- Product Diversification: I once experimented with different flavors and textures using an extruder, and the results were fantastic! This kind of innovation can attract new customers and help you tap into new markets14.
- Quality Control: With an extruder, you gain laser-like precision over moisture content and texture, which means fewer batch rejections and a solid reputation for quality.
Benefit | Description |
---|---|
Efficiency | Continuous production, reduced labor costs |
Diversification | New flavors and textures meet consumer demand |
Quality Control | Consistent moisture content, texture, reduced batch rejections |
Reducing Costs and Waste
One of the surprises I had with extruders was how much they could cut down on raw material waste. By optimizing ingredient use, you not only save money but also contribute to sustainability15, which is becoming a big selling point for eco-conscious consumers.
Enhancing Product Quality
The ability to fine-tune cooking time and temperature ensures that pet foods retain their nutritional value while achieving that perfect texture. This control is essential for producing premium products that command higher price points, which ultimately increases your profit margins.
Challenges to Consider
Of course, it's not all sunshine and rainbows. The initial investment for extrusion technology can be steep. But here's what I recommend: conduct a thorough cost-benefit analysis to see if this investment aligns with your business model and growth strategy.
You'll also need skilled personnel to operate and maintain this machinery effectively. So consider training programs or hiring experienced staff to make the most out of your investment.
Introducing extrusion technology16 into your production line can be a game-changer. With the right approach, it can propel your business into new heights of efficiency, quality, and profitability.
Extruders reduce labor costs in pet food production.True
Extruders enable continuous production, decreasing the need for manual labor.
Extrusion technology increases batch rejections in pet food.False
Extruders improve quality control, reducing the likelihood of batch rejections.
What Are the Long-Term Maintenance Costs of a Pet Food Extruder?
Have you ever wondered what it really takes to keep a pet food extruder running smoothly for the long haul?
The long-term maintenance costs of a pet food extruder include routine inspections, replacement of worn parts, lubrication, and potential upgrades. These costs vary based on machine usage, quality, and maintenance practices.
Key Factors Affecting Maintenance Costs
When I first started working with pet food extruders, I quickly learned that understanding maintenance costs is like knowing your car's service schedule—essential for avoiding unexpected breakdowns. The expenses can differ widely depending on the machine's build quality, how intensely it's used, and how well it's maintained. Imagine catching a small leak in your roof before a storm hits; regular inspections do just that, helping us nip potential issues in the bud.
Essential Maintenance Practices
Routine Inspections
I remember my first day overseeing the maintenance team—armed with a checklist longer than my grocery list. Regular inspections help us spot wear and tear early on. Checking motors, bearings, and cutting blades might seem mundane, but it's like brushing teeth—essential to prevent bigger problems.
Replacement of Worn Parts
Think of worn parts like an old pair of shoes—eventually, they need replacing. Seals, gaskets, and bearings have their expiration dates. Keeping a stock of these parts is like having an emergency stash of chocolate—it keeps everything moving smoothly and minimizes downtime.
Predictive Maintenance Technology
Leveraging IoT for Maintenance
Integrating IoT technology has been a game-changer for us. It's like having a personal trainer who tracks our performance—sensors provide real-time data on temperature and vibration, alerting us to issues before they become costly headaches.
Component | Maintenance Frequency |
---|---|
Bearings | Every 6 months |
Cutting blades | Monthly |
Motors | Annually |
Cost-Saving Strategies
Implementing a proactive maintenance strategy isn't just smart—it's essential for saving costs. Predictive maintenance technologies reduce unexpected breakdowns and extend the equipment's lifespan. Using high-quality lubricants is like investing in good running shoes—it reduces wear and tear over time.
To understand the impact of predictive maintenance on costs better, I've looked into case studies17 where companies successfully used these technologies in the pet food industry. It’s fascinating how staff training plays a crucial role in minimizing operational costs, ensuring we’re all on the same page.
Considerations for Budgeting
When planning the budget for maintenance, I make sure to factor in both routine and unexpected expenses. Establishing a reserve fund is my safety net against unforeseen repairs. Plus, negotiating service contracts can lock in predictable costs and even get us discounts on parts and labor.
Understanding these components and strategies helps me ensure efficient operations and budget management for our pet food extruders. For more detailed guidance on setting up an effective maintenance program, I refer to resources about industrial maintenance best practices18 in pet food manufacturing.
Routine inspections reduce extruder repair costs.True
Regular checks detect wear early, preventing costly repairs.
IoT technology increases maintenance costs significantly.False
IoT reduces costs by predicting issues before breakdowns occur.
Conclusion
Pet food extruder costs range from $10,000 to over $100,000, influenced by capacity, technology, materials, and brand reputation. Investing wisely can enhance production efficiency and product quality.
Discover how integrating advanced technology into extruders can increase efficiency and affect pricing strategies. ↩
Explore how established brands justify higher costs through reliability and superior support services. ↩
Learn about the long-term benefits of investing in extruders made from superior materials. ↩
Understanding economies of scale helps identify how increased production lowers unit costs. ↩
Learn how advanced technology improves energy efficiency in large-scale operations. ↩
Explore how smaller-capacity extruders offer adaptability for diverse product lines. ↩
Discover how a versatile extruder can help diversify product lines, meeting various consumer needs. ↩
Understand why precise temperature control is vital for maintaining nutrient integrity during extrusion. ↩
Learn how energy-efficient equipment can significantly cut down manufacturing costs. ↩
Understand the financial benefits of investing in high-end extruders. ↩
Discover the demand dynamics for premium pet food products. ↩
Explore real-world examples of businesses benefiting from such investments. ↩
Discover the fundamental role of extruders in pet food manufacturing, including how they shape product consistency and quality. ↩
Learn how introducing varied products can attract new customers and expand your market presence. ↩
Understand the environmental benefits of using extruders in reducing waste and supporting sustainable practices. ↩
Find out about necessary skills and training programs for effectively managing extrusion equipment. ↩
Explore real-world examples of predictive maintenance to understand its benefits in reducing costs. ↩
Discover best practices in industrial maintenance to optimize pet food manufacturing processes. ↩