When it comes to choosing an extruder, the decision can feel like picking the perfect tool from a vast toolbox.
Single-screw extruders offer simplicity and cost-effectiveness but may struggle with complex formulations. Twin-screw extruders provide better mixing capabilities and flexibility but come with higher costs and maintenance needs.
Having spent years in the pet food processing industry, I've seen firsthand how the right extruder can transform a production line. It's not just about efficiency—it's about delivering consistent quality that meets the high standards our furry friends deserve. Let's dive deeper into the nuances of these machines, exploring how single-screw and twin-screw extruders stack up against each other, depending on what you're looking to achieve in your manufacturing process.
Single-screw extruders are more complex than twin-screw extruders.False
Single-screw extruders are simpler, not more complex, than twin-screw ones.
Twin-screw extruders offer better mixing capabilities.True
Twin-screw extruders are designed for superior mixing and processing flexibility.
How Do Single-Screw Extruders Work?
Ever wondered how your pet's kibble gets its perfect shape and texture? Let me share the magic behind it!
Single-screw extruders work by using a rotating screw inside a barrel to transport, mix, and shape materials. The process involves feeding, melting, and forming, essential for industries like pet food manufacturing.
The Basics of Single-Screw Extruders
Picture this: a giant screw inside a cylinder, tirelessly working away to create your pet's favorite treats. That's essentially what a single-screw extruder does. As the screw turns, it propels materials through different zones, each playing a vital role in heating and mixing. It reminds me of the time I first saw one in action – it was like watching a master chef whisking together ingredients for a culinary masterpiece.
This rotational motion1 is crucial for mixing and heating.
Key Components and Their Functions
The heart of this machine lies in its three main sections:
- Feeding Zone: This is where it all begins. Imagine tossing ingredients into a giant mixer – that's how materials enter the extruder.
- Compression Zone: Here, things get intense as the heat rises and everything blends together, much like when you knead dough until it's just right.
- Metering Zone: This zone ensures that the mixture flows out smoothly, kind of like pouring batter onto a griddle for perfectly shaped pancakes.
Every component works in harmony, ensuring that the temperature and pressure are just right.
Component | Function |
---|---|
Feeding Zone | Entry point for raw materials |
Compression | Melts and homogenizes material |
Metering | Controls flow rate of processed material |
Importance of Screw Design
The design of the screw can make or break the process – literally! Different geometries influence how well materials mix and the quality of the output. It's like choosing the right tool for baking; each design serves a specific purpose to optimize performance.
Understanding how screw geometry2 affects the process can optimize performance.
Applications in Pet Food Industry
In the realm of pet food, single-screw extruders are game-changers. They allow manufacturers to craft various textures and shapes, ensuring every bite meets high standards. It's akin to having a secret recipe that guarantees your dishes are always top-notch.
This precision is crucial for maintaining quality, which is why brands trust these machines to keep their reputation intact by producing high-quality products3 efficiently.
Advantages Over Twin-Screw Extruders
While twin-screw extruders might be flashier with their complex capabilities, single-screw extruders are reliable workhorses. They're cost-effective, easier to maintain, and ideal for straightforward tasks. Think of them as your trusty old car that never lets you down – simple yet effective for those who value consistency.
They require less maintenance and are easier to operate, making them ideal for companies focusing on standardized processes4.
Single-screw extruders have three primary zones.True
The feeding, compression, and metering zones are the main areas.
Twin-screw extruders are more cost-effective than single-screw.False
Single-screw extruders are generally more cost-effective for simpler tasks.
Why Choose Twin-Screw Extruders Over Single-Screw?
Ever wondered why twin-screw extruders are a game-changer in manufacturing? Let's dive into the magic behind their efficiency and versatility.
Twin-screw extruders offer superior mixing capabilities, increased flexibility, and higher throughput rates compared to single-screw extruders. They are ideal for applications requiring precise control over the extrusion process, resulting in consistent product quality.
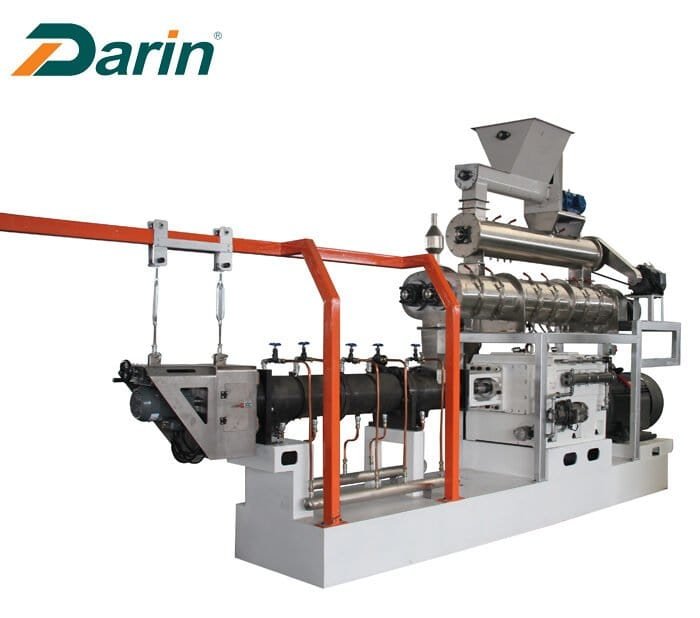
Enhanced Mixing and Flexibility
I remember the first time I witnessed a twin-screw extruder in action; it was like watching a perfectly choreographed dance. The two intermeshing screws work together5 seamlessly, blending materials with such finesse that it left me genuinely amazed. This precision is particularly vital when you're dealing with complex compounding processes6 where every ingredient must be perfectly melded.
The flexibility of these machines is another marvel. Imagine having the ability to process a variety of raw materials, from sticky to viscous, without a hitch. It's like having a superhero on your production line, saving the day by maintaining consistency no matter what you throw at it. This adaptability is why so many in the food production industry7, where ingredient variability is common, swear by these machines.
Feature | Twin-Screw Extruder | Single-Screw Extruder |
---|---|---|
Mixing Capability | High | Moderate |
Material Flexibility | High | Low |
Throughput Rates | High | Moderate |
Improved Throughput and Energy Efficiency
One of the biggest headaches in manufacturing is downtime. But with twin-screw extruders, higher throughput rates mean more efficient processing. I can't count the number of times I've seen production lines humming along smoothly, thanks to these ingenious machines.
And let's talk about energy efficiency—who doesn't love saving on energy bills? The design of twin-screw extruders means they require less energy per unit of production, which is not only a win for the bottom line but also a step towards greener manufacturing processes.
Consistent Product Quality
In industries like plastics and food manufacturing, consistent product quality isn't just a goal; it's a necessity. Twin-screw extruders offer precise control over the extrusion process, ensuring uniformity that translates into fewer defects and less waste.
Being able to adjust these machines on the fly to meet specific product requirements is a game-changer. Whether it's responding to changing market demands or customization requests8, this adaptability ensures you're always ready to innovate and succeed in competitive markets. That's something I've always valued in my own operations—having that reliable, versatile tool that lets me adapt and thrive.
Twin-screw extruders offer higher throughput rates.True
Twin-screw extruders are designed to process materials more efficiently, leading to higher throughput rates.
Single-screw extruders have superior mixing capabilities.False
Twin-screw extruders provide superior mixing due to their intermeshing screws, unlike single-screw extruders.
What Challenges Do Single-Screw Extruders Face?
I once found myself knee-deep in a sticky situation with a single-screw extruder, learning firsthand the challenges these machines face.
Single-screw extruders face challenges like limited material mixing, pressure consistency issues, and material flow constraints. These factors can impact the quality and efficiency of production processes.
Limited Material Mixing
Ah, the good old days of wrestling with a single-screw extruder! I remember the first time I realized that my extruder was having trouble mixing materials properly. It felt like trying to blend a smoothie with a fork instead of a blender. The machine's design inherently limited the homogeneity achievable, which sometimes resulted in uneven distribution of additives or fillers. Not exactly what you want when you're aiming for top-notch product quality.
- Potential Solutions:
- After some trial and error, I discovered that using mixing elements like Maddock mixers made a world of difference.
- Optimizing the screw design can also enhance mixing efficiency, a lesson I learned the hard way!
Pressure Consistency Issues
Pressure consistency is another hurdle I've had to jump over more than once. Picture this: you're in the middle of a production run, and suddenly, due to variations in the feedstock or screw wear9, the pressure starts fluctuating wildly. It's like trying to drive on a road full of potholes, leading to inconsistent product dimensions or, worse yet, surface defects.
- Strategies to Mitigate:
- Regular maintenance and inspection of the screw became my mantra after experiencing these issues.
- Utilizing pressure control systems to monitor and adjust parameters was a game changer, ensuring smoother operations.
Material Flow Constraints
Then there’s the challenge of material flow constraints, especially when dealing with high-viscosity materials. I've had moments where the die wasn’t filled completely, resulting in defective products. It's akin to trying to pour honey through a narrow funnel without making a mess.
- Enhancement Techniques:
- Implementing a cooling system to manage heat generation helped mitigate this issue.
- Customizing screw configurations was another trick up my sleeve to accommodate specific material properties.
Challenge | Impact on Production | Mitigation Strategy |
---|---|---|
Limited Mixing | Uneven material distribution | Use of advanced mixing elements |
Pressure Inconsistency | Variability in product dimensions | Regular screw maintenance |
Material Flow Issues | Incomplete die filling | Custom screw design |
By understanding and addressing these challenges, I learned how industries can optimize their use of single-screw extruders for improved performance and product quality. For further insights into extrusion technologies10, examining case studies and industry reports can provide valuable knowledge.
Single-screw extruders have limited material mixing capabilities.True
Their design restricts homogeneity compared to twin-screw extruders.
Pressure consistency is not an issue for single-screw extruders.False
They often struggle with pressure fluctuations due to feedstock variations.
When Should You Use a Twin-Screw Extruder?
Have you ever wondered when a twin-screw extruder might be your secret weapon in manufacturing?
Use a twin-screw extruder when your process demands high flexibility, precise control over product quality, and the ability to handle complex formulations or achieve high throughput rates.
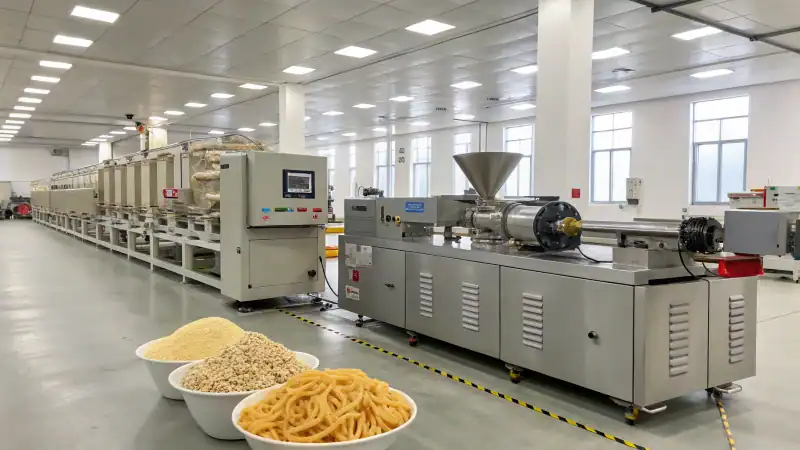
Understanding the Basics of Twin-Screw Extruders
I remember the first time I watched a twin-screw extruder in action—it was like witnessing a culinary master at work, blending ingredients seamlessly. These machines are the unsung heroes of versatility, especially when dealing with complex formulations11. Imagine two intermeshing screws dancing within a barrel, performing a delicate ballet to mix materials perfectly.
Key Advantages:
Feature | Benefit |
---|---|
High shear mixing | Improved dispersion of ingredients, ideal for uniform product quality. |
Flexible operation | Accommodates a wide range of materials and formulations. |
Precise control | Enables consistent quality and optimal use of ingredients. |
Industrial Applications
In the pet food industry, where I’ve seen firsthand how high capacity12 and flexibility can transform production, twin-screw extruders prove invaluable. Whether crafting dry kibble for my own pets or developing gourmet moist treats, these machines adapt effortlessly to varied recipes by tweaking process parameters.
Use Cases:
- Pet Food Industry: Crafting different textures and nutrient profiles to suit diverse dietary needs.
- Plastic Manufacturing: Mixing complex blends and compounds with precision.
Comparing Twin-Screw and Single-Screw Extruders
I've often found myself in discussions weighing the merits of twin-screw versus single-screw extruders. While both have their place, there are clear distinctions:
Attribute | Twin-Screw Extruder | Single-Screw Extruder |
---|---|---|
Mixing Capability | Superior for challenging applications. | Limited to simpler formulations. |
Throughput | Generally higher and more consistent. | May struggle with high throughput tasks. |
Process Control | Highly controllable for precision tasks. | Offers basic control over processes. |
The choice really boils down to what you need—if it's advanced ingredient mixing13 or high-speed processing, a twin-screw might be your best bet.
Considerations for Selecting a Twin-Screw Extruder
When contemplating a twin-screw extruder, I recommend pondering over the materials you'll process, your desired throughput rate, and budgetary constraints. Seeking advice from industry experts or machinery suppliers has been invaluable for me, guiding me toward the right machine.
As industry trends14 shift towards innovation and efficiency, the demand for these machines grows. Aligning your choices with your production goals and quality standards can set you on the right path.
Twin-screw extruders offer superior mixing capabilities.True
They provide high shear mixing, enhancing dispersion and product uniformity.
Single-screw extruders are better for complex formulations.False
Twin-screw extruders are superior for challenging applications and complex formulations.
How do I choose between single-screw and twin-screw extruders?
Deciding between single-screw and twin-screw extruders is like choosing between two trusty companions for your manufacturing journey. Let me guide you through this crucial decision with insights that I’ve gathered over the years.
Single-screw extruders are cost-effective and simpler, ideal for basic extrusion tasks, whereas twin-screw extruders offer greater versatility and efficiency for complex and diverse applications, often justifying their higher cost.
Cost and Complexity
When I first started exploring extrusion technology, the decision seemed daunting. I remember grappling with budget constraints and complexity levels. Single-screw extruders quickly stood out as a reliable, cost-effective option for simpler tasks. They remind me of those days when I was more focused on getting things done without too many frills—just straightforward functionality.
Feature | Single-Screw | Twin-Screw |
---|---|---|
Cost | Lower | Higher |
Complexity | Simpler | More complex |
But as I delved deeper into more intricate processes, twin-screw extruders began to appeal more with their enhanced capabilities15. They are like the multi-tasking genius in the room, handling complex recipes and thorough mixing with ease.
Efficiency and Versatility
Think of twin-screw extruders as the Swiss Army knife of extrusion. They can tackle anything from challenging materials to processes that require multiple steps. Their co-rotating screws ensure that everything gets mixed just right, a feature I found invaluable when working with diverse material needs in pet food production.
Product Quality
Quality is paramount for me, especially when crafting customized pet foods. Both extruder types can deliver high-quality results, but I've found twin-screws provide more control over the process. This extra control translates into consistency, which is key in maintaining standards across batches.
Application-Specific Considerations
Every project has its unique requirements. In simpler applications like forming or basic mixing, a single-screw extruder might be all you need. But if your work involves complex formulations16 or requires precision in mixing ingredients, investing in a twin-screw extruder is worthwhile.
To make the best choice for your needs, it helps to evaluate your production goals closely. I often consult with industry experts and study how leaders utilize these technologies—insights that have been invaluable in refining my approach to choosing the right equipment.
Single-screw extruders are cheaper than twin-screw extruders.True
Single-screw extruders have a simpler design, reducing manufacturing costs.
Twin-screw extruders are less versatile than single-screw ones.False
Twin-screw extruders excel in versatility due to better material handling.
What Are the Latest Innovations in Extruder Technology?
Remember the time when screeching machines and endless troubleshooting were the norm? Extruder technology has come a long way since then, transforming industries with its efficiency and precision.
The latest innovations in extruder technology focus on improving efficiency, precision, and versatility. This includes advancements in screw design, energy-efficient motors, and integration with smart technologies for real-time monitoring and control.
Advanced Screw Designs
I remember the first time I witnessed a modern extruder's screw design in action—it was like watching an artist at work. These designs boost mixing and shearing capabilities, ensuring perfect material consistency17. Industries like food processing and plastics manufacturing rely heavily on this precision.
Energy-Efficient Motors
Switching to energy-efficient motors felt like upgrading from a bicycle to a high-speed train. These motors cut down power consumption without compromising output levels, which not only slashes operational costs but also aligns with my commitment to sustainability goals18.
Integration with Smart Technologies
Imagine a world where your extruder tells you what it needs before it even hiccups. Thanks to IoT and AI, real-time monitoring systems now provide detailed analytics on machine performance, enabling predictive maintenance that keeps everything running smoothly.
Feature | Benefit |
---|---|
Smart Sensors | Continuous performance tracking |
AI-Driven Adjustments | Optimized process parameters |
Versatility in Material Processing
The thrill of watching a new extruder handle everything from biodegradable plastics to specialized pet food ingredients is unmatched. This versatility means manufacturers can explore new market opportunities19 and expand their product lines with ease.
Modular Design for Customization
The beauty of recent extruders lies in their modular components—like building blocks for adults! Businesses can customize machinery to meet specific production needs, enhancing operational efficiency and adaptability. It's like having a wardrobe you can endlessly mix and match.
Manufacturers can upgrade or modify parts without replacing the entire system, which is fantastic for adapting to new technological trends20 or market demands. This flexibility is something I truly value in this ever-evolving industry.
Modern extruders reduce energy consumption by 30%.False
While modern extruders are more energy-efficient, a specific 30% reduction is not universally documented.
AI enhances extruder maintenance through predictive analytics.True
AI-driven systems analyze performance data to predict maintenance needs, reducing downtime.
Conclusion
This article compares single-screw and twin-screw extruders, highlighting their advantages and disadvantages in pet food manufacturing, including cost, complexity, mixing capabilities, and suitability for various applications.
Learn how rotational motion in extruders facilitates efficient mixing and material movement. ↩
Discover how different screw designs impact extrusion efficiency and product quality. ↩
Explore why single-screw extruders are favored in creating diverse pet food products. ↩
Understand the differences and advantages of single versus twin-screw extruders. ↩
Discover how intermeshing screws improve material mixing in twin-screw extruders, enhancing product quality. ↩
Learn about compounding processes and how twin-screw extruders excel in combining materials. ↩
Explore the versatility of twin-screw extruders in handling diverse food ingredients efficiently. ↩
Understand how twin-screw extruders allow for quick adjustments to meet specific product needs. ↩
Understanding screw wear helps in diagnosing pressure-related issues, aiding in maintenance strategies. ↩
Staying updated on technological advancements enhances strategic planning for machinery upgrades. ↩
Explore how twin-screw extruders enhance material mixing, especially for complex formulations. ↩
Discover how twin-screw extruders are used in high-capacity industrial applications. ↩
Learn about the benefits of using twin-screw extruders for advanced ingredient mixing. ↩
Stay updated on the latest trends in twin-screw extrusion technology across industries. ↩
Learn about the advanced capabilities of twin-screw extruders for complex processing needs. ↩
Find out why twin-screw extruders are ideal for intricate processing requirements. ↩
Learn how advanced screw designs enhance material consistency in extruder technology. ↩
Explore how energy-efficient motors reduce operational costs and support sustainability goals. ↩
Discover new market opportunities with versatile extruder models handling diverse materials. ↩
Understand how modular components in extruders improve flexibility and efficiency. ↩