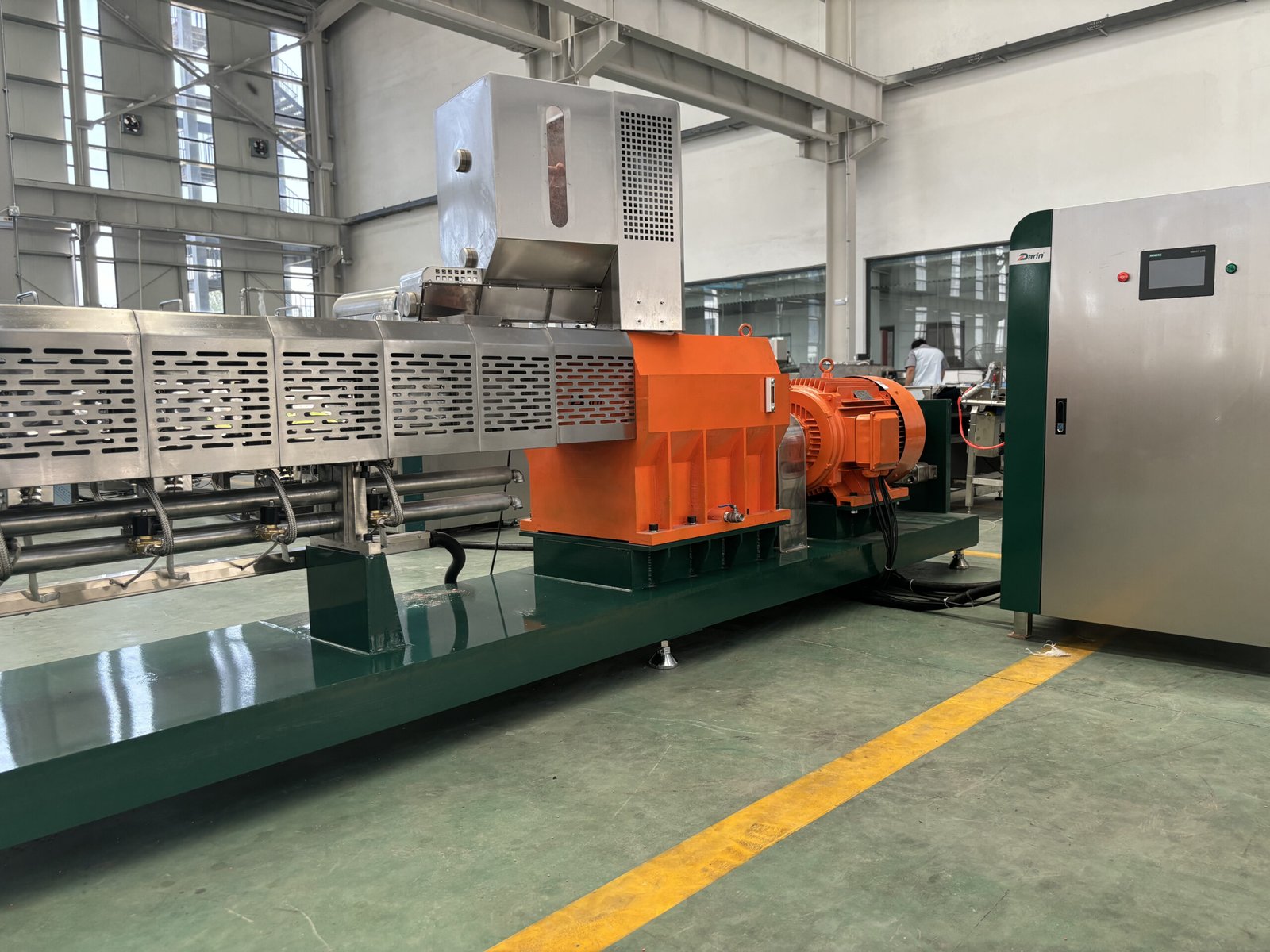
In today’s competitive pet food industry, manufacturers constantly seek ways to increase productivity, enhance product consistency, and reduce labor costs. One major hurdle is the complexity of managing numerous parameters in extrusion—temperature, pressure, moisture, screw speed, feed rate, and recipe control—all of which must be carefully balanced to achieve premium quality pet food. Manual operations make this difficult, error-prone, and inefficient. The solution? Automation. Automated pet food extruders eliminate these risks, improving consistency, efficiency, and output while minimizing human error and downtime. This article explains how automation is integrated into pet food extruders and the levels available.
Most modern pet food extruders offer a high level of automation, including automatic ingredient feeding, moisture and steam control, screw speed adjustment, recipe management, real-time monitoring, and self-diagnostics. The highest-end systems feature PLC (Programmable Logic Controller) integration, HMI (Human Machine Interface) touchscreens, SCADA systems, and even remote operation capabilities.
This level of automation in pet food extrusion enables facilities to run longer with fewer staff, maintain precise product quality, and reduce variability. But not all systems are created equal. The range of automation can vary from basic semi-automated machines requiring manual adjustments to fully automated, AI-integrated systems. Let’s explore the full spectrum and guide you in selecting the right setup.
Modern pet food extruders are fully automated and require no human intervention during operation.False
While modern extruders are highly automated, human oversight is still essential for quality assurance, maintenance, and handling exceptions.
Understanding Automation Levels in Pet Food Extruders
Level 1: Manual/Semi-Automated Systems
At the most basic level, some extruders offer manual control panels with analog settings. These systems typically require an operator to adjust parameters like:
- Screw speed
- Feeder rate
- Steam pressure
- Moisture injection
While they may include sensors for monitoring temperature or pressure, the user must make adjustments manually based on readouts. These systems are cost-effective but can lead to inconsistencies and longer setup times.
Table 1: Manual vs. Semi-Automated Pet Food Extruders
Feature | Manual System | Semi-Automated System |
---|---|---|
Ingredient feeding | Manual | Partially motorized |
Moisture/steam control | Manual valves | Timed solenoid control |
Recipe adjustment | Manual via knobs | Pre-programmed settings |
Data recording | Paper or none | Basic digital log |
Operator requirement | High | Moderate |
Semi-automated systems are a step up, often using basic PLCs with pre-set programs for standard recipes, allowing more reproducible results.
Level 2: Fully Automated Systems
Fully automated pet food extruders are equipped with integrated PLC+HMI systems that provide complete control over:
- Ingredient batching and pre-mixing
- Real-time extrusion parameter control (temperature, torque, pressure)
- Automatic lubrication and screw adjustment
- Integrated drying and coating systems
- Alarm and fault detection with self-correction protocols
These systems require minimal manual intervention once set up and can store hundreds of recipes for different product types.
Table 2: Key Automation Features in High-End Extruders
Automation Feature | Description | Benefit |
---|---|---|
PLC with touchscreen HMI | Central controller that monitors and adjusts extrusion process | Real-time adjustments and remote diagnostics |
Auto ingredient dosing | Load cells and conveyors control proportions | Consistent product quality |
Steam and moisture control | Inline sensors regulate based on feedback | Optimal texture and palatability |
Screw & die auto-alignment | Self-adjusting mechanisms | Less downtime and better throughput |
Data logging and analysis | Tracks every batch parameter | Enables traceability and continuous improvement |
Some extruders even feature SCADA integration, enabling plant-wide control and monitoring through a central server. These systems allow remote access, alert notifications, energy consumption tracking, and OEE (Overall Equipment Effectiveness) dashboards.
Integration with Upstream and Downstream Equipment
True automation also extends beyond the extruder itself. Modern plants integrate extrusion with upstream (grinding, mixing) and downstream (drying, coating, cooling, packaging) units. These can be linked through centralized automation systems to ensure harmony and timing.
Automation Workflow in a Pet Food Production Line
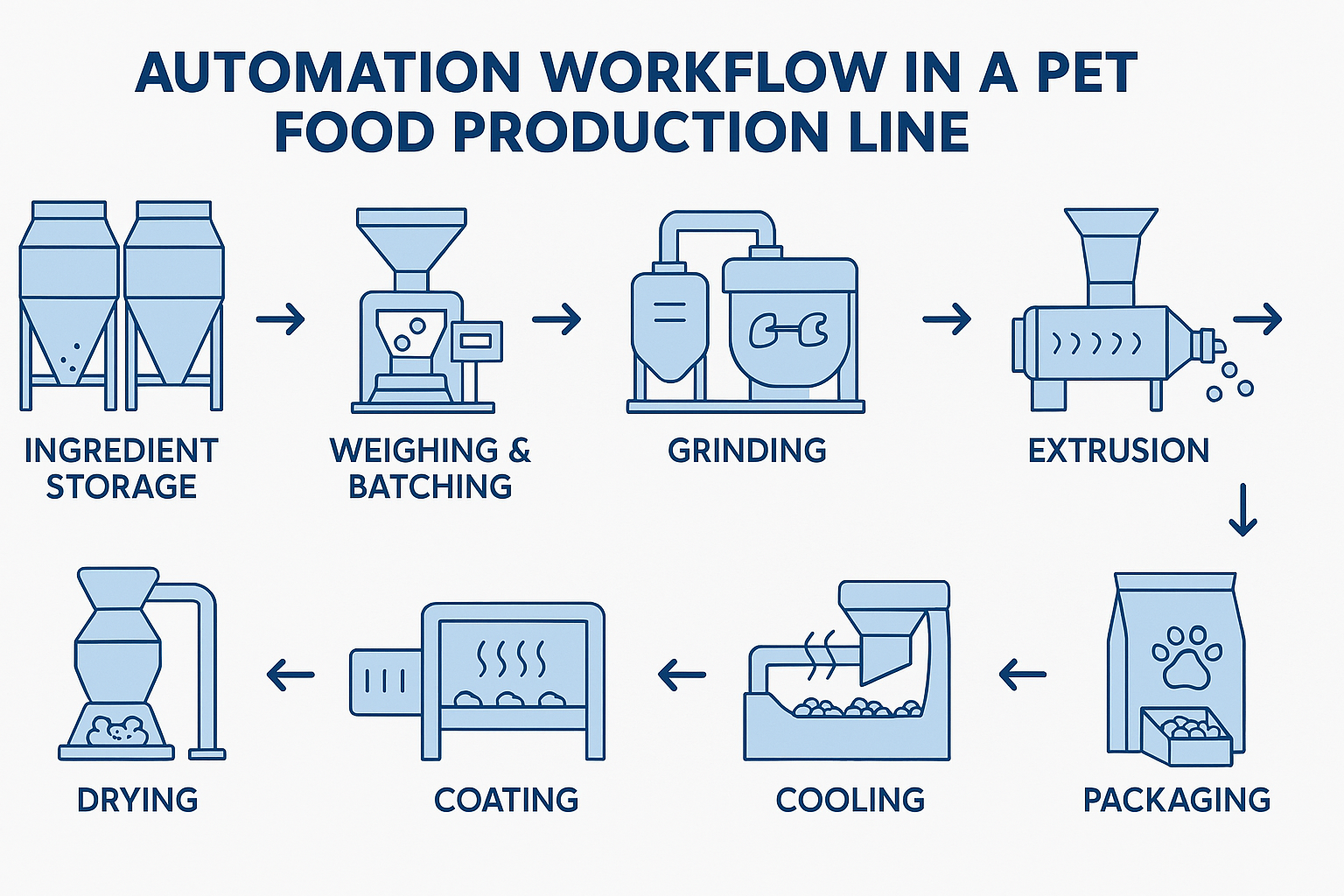
Each of these stages can be automated and synchronized using a master control system, often based on SCADA or MES (Manufacturing Execution System).
Case Study: Automation Benefits in a Medium-Sized Pet Food Facility
A mid-sized European pet food manufacturer upgraded from semi-automated to fully automated twin-screw extruders with integrated SCADA. Results included:
- 15% increase in throughput
- 25% reduction in labor costs
- Consistent moisture levels at ±0.2% tolerance
- Machine downtime reduced by 30%
- Energy usage monitored and reduced by 12% through feedback loops
Operators could monitor over 80 critical parameters in real-time, receive alerts, and adjust settings via tablets—even from outside the facility.
Benefits and ROI of Extruder Automation
Benefit | Description |
---|---|
Increased throughput | Automated machines optimize screw speed and feed rates based on real-time product behavior |
Reduced labor costs | Fewer operators required; one person can monitor multiple lines |
Consistent quality | Recipe management and sensor feedback ensure repeatable texture, shape, and density |
Faster changeovers | Recipes can be changed with one click; CIP (Clean-in-Place) can be automated |
Predictive maintenance | Self-diagnostics alert operators before breakdowns occur |
ROI Timeline: Many users report that investing in fully automated extruders pays off in 1.5 to 3 years, depending on production volume and local labor costs.
Future Trends in Pet Food Extruder Automation
- AI and Machine Learning: Systems learn optimal settings over time and suggest tweaks for energy efficiency or product improvement.
- IoT and Cloud Connectivity: Secure remote access and cloud-based analytics are becoming standard.
- Augmented Reality (AR) Maintenance: Technicians use AR glasses for hands-free diagnostics and repair instructions.
- Green Automation: Monitoring and reducing emissions, water use, and energy per batch.
These technologies push the boundaries of automation, delivering smarter, more sustainable production.
Summary: Choosing the Right Level of Automation
Not every pet food facility needs the highest-end automation from day one. Consider:
- Production scale
- Product diversity
- Labor availability
- Quality requirements
- Budget
Work with your equipment supplier to determine a modular approach. Start with essential automation like auto dosing and HMI control, and scale up to SCADA or AI-based control as your production grows.
Contact Us to Upgrade Your Extruder System
Looking to automate your pet food production line? Whether you're starting with basic automation or aiming for full SCADA integration, we manufacture and supply the industry's leading extrusion systems with tailored automation solutions. Reach out to our expert engineering team today for a free consultation and customized proposal.
FAQ
Q1: What is the level of automation in modern pet food extruders?
A1: Modern pet food extruders feature high levels of automation, integrating programmable logic controllers (PLCs), touch-screen interfaces, real-time monitoring, and data analytics. Automation manages critical processes like ingredient dosing, temperature and pressure control, screw speed, moisture levels, and die shaping. These systems reduce human error, improve consistency, and enhance production efficiency. High-end extruders often include AI-assisted decision-making, remote diagnostics, and cloud-based performance tracking for predictive maintenance and operational optimization.
Q2: How does automation improve pet food extrusion efficiency?
A2: Automation increases efficiency by streamlining production, ensuring consistent quality, and minimizing downtime. Automated systems can quickly adjust parameters in real-time to maintain optimal extrusion conditions. This reduces waste, lowers energy usage, and boosts throughput. Recipes and operating settings can be pre-programmed, allowing faster product changeovers and reducing reliance on manual labor. These benefits make automated extruders essential for high-volume pet food manufacturers.
Q3: What are the main automated features in pet food extruders?
A3: Key automated features include:
- Ingredient batching and dosing systems
- Real-time temperature and pressure control
- Automated moisture addition
- Variable screw speed and torque regulation
- Integrated quality control sensors
- Recipe storage and recall
- Remote monitoring and diagnostics
These features ensure a seamless, responsive production environment with minimal human intervention.
Q4: Is it possible to retrofit older pet food extruders with automation?
A4: Yes, many manufacturers offer automation upgrade kits or retrofit services for older extruder models. These upgrades can include new control panels, PLC integration, sensor systems, and SCADA (Supervisory Control and Data Acquisition) software. While not all legacy equipment may support full automation, partial upgrades can significantly improve performance, reduce labor demands, and extend machine life.
Q5: What are the benefits of fully automated pet food extrusion systems?
A5: Fully automated systems offer several benefits:
- Improved product quality and consistency
- Lower labor and operational costs
- Enhanced safety and compliance
- Predictive maintenance and reduced downtime
- Real-time data insights and reporting
These advantages contribute to better scalability, profitability, and regulatory adherence for pet food producers in a competitive market.
References
- Automation in Extrusion – https://www.buhlergroup.com/content/buhlergroup/global/en/industries/pet-food.html – Bühler Group
- Smart Pet Food Processing – https://www.petfoodprocessing.net/articles/13697-automation-and-innovation – Pet Food Processing
- Extrusion Control Systems – https://www.extru-techinc.com/technologies/control-systems – Extru-Tech
- Pet Food Production Technology – https://www.petfoodindustry.com/topics/223-pet-food-processing – Pet Food Industry
- Twin Screw Automation – https://www.clextral.com/technology/twin-screw-extrusion/ – Clextral
- SCADA in Food Manufacturing – https://www.scada.systems/industries/food-beverage/ – SCADA Systems
- PLC in Pet Food Processing – https://www.controleng.com/articles/plcs-key-to-pet-food-processing-efficiency/ – Control Engineering
- Advanced Automation in Extruders – https://www.bakerperkins.com/food/pet-food/extrusion/ – Baker Perkins
- Retrofit Automation for Legacy Systems – https://www.rockwellautomation.com/en-us/solutions/services/modernization.html – Rockwell Automation
- AI and Industry 4.0 in Food – https://www.ifm.com/gb/en/shared/landingpages/food-industry-4-0 – ifm Industry 4.0