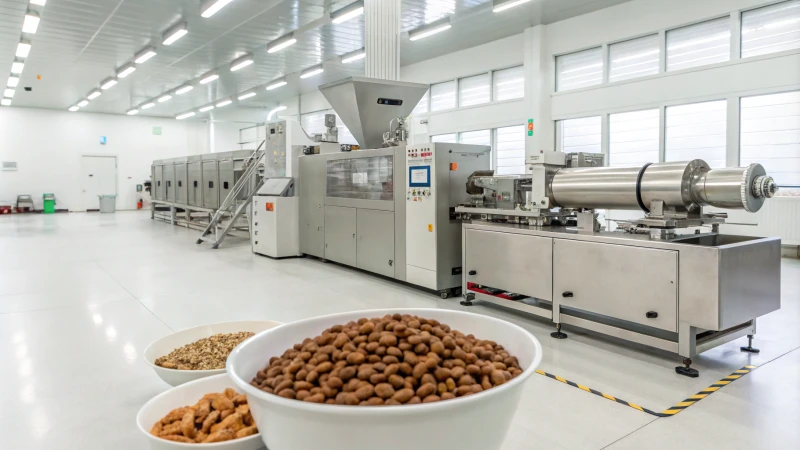
Ever wondered how your pet's kibble is made?
The pet food extrusion process involves mixing raw materials, cooking them under high heat and pressure, and then forcing them through a die to form specific shapes. This method ensures uniformity in texture and nutritional consistency across pet food products.
I remember when I first learned about the extrusion process; it was like peeking behind the curtain of a magic show. Seeing raw ingredients transform into those neat little kibble shapes fascinated me. While this process may sound straightforward, there's so much more happening under the hood. The attention to detail at each step ensures that every piece of kibble is safe, nutritious, and consistent. From selecting the right blend of raw materials to using precise equipment, manufacturers work hard to ensure our pets get the best quality food. It's this commitment to excellence that keeps me intrigued and appreciative of the science behind every bite our pets take.
Extrusion ensures uniform texture in pet food.True
Extrusion process mixes and cooks ingredients uniformly, ensuring consistent texture.
Pet food extrusion uses low heat and pressure.False
The extrusion process involves high heat and pressure to cook ingredients.
What Are the Key Steps in Pet Food Extrusion?
Ever wonder how those tiny kibbles in your pet's bowl are made? It’s a fascinating journey from raw ingredients to delicious meals. Let’s dive into the world of pet food extrusion and uncover the key steps!
Pet food extrusion involves preparing ingredients, cooking with heat and pressure, shaping through an extruder, drying, coating for flavor, and cooling. These steps ensure high-quality, nutritious pet food that meets industry standards.
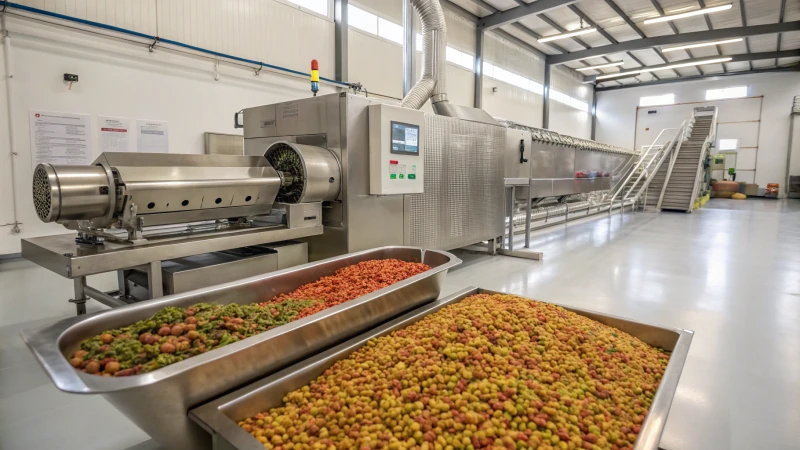
Ingredient Preparation
I remember the first time I watched the magic happen in our facility—it all starts with selecting just the right mix of ingredients. Imagine carefully choosing grains, meats, and those vital vitamin supplements1. Each ingredient is meticulously ground into a fine powder to ensure everything blends smoothly. It's like baking a cake; you want every bite to be perfectly balanced and full of nutrients.
Ingredient | Function |
---|---|
Grains | Carbohydrates |
Meats | Proteins |
Fats & Oils | Energy |
Cooking and Mixing
The next step is where the real transformation begins. Mixing those ground ingredients with water and steam, we cook them under high pressure. This part always reminds me of making my grandma's famous stew—it's all about bringing out the flavors while ensuring everything is safe and easy to digest for our furry friends. The heat not only cooks but also brings together the elements into a harmonious blend.
Extrusion
Here's where the fun shapes come in! Our mixture is pushed through an extruder2 die, emerging as pellets or kibbles. The sudden release of pressure puffs them up, similar to how popcorn kernels burst open. Watching this transformation never gets old—it’s like witnessing a culinary ballet.
Drying
Once shaped, these nuggets need to be dried, kind of like sunbathing to lock in all their goodness. This step ensures they stay fresh for longer, just like drying out homemade jerky to preserve it. It's all about striking the right balance of heat and time to keep those nutrients intact.
Coating and Flavoring
The dried kibbles get a final touch with oils or palatants to make them irresistible. Think of it as adding the final drizzle of sauce on a dish to enhance its aroma and flavor. We might even sprinkle in extra vitamins or probiotics3 for that added nutritional boost.
Cooling
Finally, the kibble needs to cool down, much like letting cookies set after baking. This step ensures they remain crunchy and perfectly shaped when packed. Proper cooling prevents unwanted moisture build-up, keeping them fresh and tasty until they reach your pet's bowl.
Understanding these steps not only demystifies the extrusion process but also highlights the importance4 of quality control in producing nutritious pet food.
Grains provide protein in pet food extrusion.False
Grains primarily provide carbohydrates, not proteins, in the extrusion process.
Extrusion shapes pet food into pellets or kibbles.True
During extrusion, the mixture is shaped into forms like pellets or kibbles.
How Does Extrusion Affect Pet Food Nutrition?
Ever wondered how that bag of kibble gets its crunch while still being nutritious?
Extrusion affects pet food nutrition by altering nutrient digestibility and retention. While it can enhance protein digestibility, heat-sensitive nutrients like vitamins may degrade. Balancing temperature and time is crucial for optimal nutrient preservation.
Understanding Extrusion in Pet Food Manufacturing
When I first learned about extrusion, I was fascinated by how this method transforms raw ingredients into the crunchy, savory pet foods our furry friends adore. Imagine high-pressure cooking on a grand scale—this is extrusion. It not only shapes and cooks ingredients but also ensures efficiency in creating diverse textures and flavors. However, I've always been curious about the impact on nutrient retention5.
Impact on Protein Digestibility
One of the most intriguing aspects of extrusion is its ability to improve protein digestibility. The process breaks down complex proteins, making them more accessible for our pets' tummies. I remember reading a study that highlighted how extrusion enhances protein bioavailability, which is such a win for pet nutrition6.
Nutrient | Effect of Extrusion |
---|---|
Proteins | Increased digestibility |
Carbohydrates | Improved starch gelatinization |
Fats | Potential oxidation risk |
Challenges with Vitamin Retention
On the flip side, extrusion can be a bit harsh on vitamins. I’ve always had a soft spot for those delicate nutrients, like vitamins A, E, and some B-complex, which are susceptible to heat loss. It’s a real juggling act to preserve these during production. Thankfully, many manufacturers add them back after the extrusion or increase their initial concentration to compensate.
Balancing Temperature and Time
Getting the temperature and cooking time just right is like baking the perfect cake—too much heat and you lose valuable nutrients; too little and you end up with undercooked food that isn't easy to digest. Precision is key here, and manufacturers often employ advanced control systems to fine-tune these parameters.
Exploring Alternative Methods
In my journey to ensure every pet meal is as nutritious as possible, I've seen companies explore alternative methods. From adding antioxidant-rich ingredients to experimenting with low-temperature extrusion, these innovative techniques7 aim to maintain nutritional integrity without compromising on the benefits of extrusion.
It's amazing how much thought goes into crafting a bag of pet food! As manufacturers continue to research and develop new processes, it's reassuring to know they're committed to providing safe, nutritious meals for our beloved pets.
Extrusion enhances protein digestibility in pet food.True
Extrusion breaks down complex proteins, increasing their bioavailability.
Extrusion always preserves all vitamins in pet food.False
Heat-sensitive vitamins may degrade during extrusion, needing post-addition.
What Types of Equipment Are Used in Pet Food Extrusion?
Have you ever wondered how the kibble in your pet's bowl is crafted?
Pet food extrusion involves various specialized machines, such as pre-conditioners, extruders, dryers, and coaters. Each plays a crucial role in transforming raw materials into finished pet food products.
Understanding the Role of Pre-Conditioners
Imagine standing in a bustling kitchen as a chef, preparing to bake a cake. Pre-conditioners in pet food extrusion are like those key prep moments when you mix your ingredients just right. They blend raw materials with steam or water, starting the cooking process to ensure everything gels perfectly. I often recall the first time I saw a pre-conditioner in action and marveled at how something so simple could set the stage for delicious, nutritious pet food. For detailed insights, explore how pre-conditioners enhance ingredient preparation8.
Extruders: The Heart of the Process
Extruders are truly the heart of any pet food production line. Picture them as the culinary maestro conducting an orchestra of flavors and textures. They push the pre-conditioned mix through a die, shaping and cooking it simultaneously. Single-screw and twin-screw extruders each have their charm—kind of like choosing between a reliable sedan and a flashy sports car. Each offers unique benefits in flexibility and efficiency.
Table: Comparing Single-Screw vs. Twin-Screw Extruders
Feature | Single-Screw Extruder | Twin-Screw Extruder |
---|---|---|
Cost | Lower | Higher |
Versatility | Moderate | High |
Maintenance | Simpler | Complex |
Capacity | Limited | Extensive |
When I first learned about the different types, I realized how important it was to match the right extruder to specific production needs. Check out extruder types9 to see which might suit your production needs best.
Dryers and Their Importance
Once extruded, pet food isn't ready until it's perfectly dried—imagine hanging your laundry out on a breezy day. Dryers in pet food extrusion play this vital role, reducing moisture content to extend shelf life and ensure product safety. Horizontal band dryers and vertical dryers each have their perks, much like picking the best drying method for your clothes based on the weather forecast. Drying technology10 continues to evolve, providing more efficient solutions for manufacturers.
Coaters: Adding the Final Touch
Finally, coaters are like the pastry chef's delicate glaze, adding that irresistible final touch. They apply oils or flavors to boost taste and nutritional value. Whether drum-type or vacuum-type, each coater is designed to deliver a uniform finish. I remember the first time I observed this process—it was like watching an artist putting the final strokes on a masterpiece.
Learn about advanced coating techniques11 that ensure optimal product quality.
Understanding these equipment pieces not only helps me appreciate the intricacies of pet food manufacturing but also aids manufacturers in optimizing production lines for quality and efficiency.
Pre-conditioners hydrate ingredients in pet food extrusion.True
Pre-conditioners mix raw materials with steam or water for hydration.
Single-screw extruders offer higher versatility than twin-screw.False
Twin-screw extruders provide higher versatility than single-screw ones.
Why Is Quality Control Crucial in Pet Food Production?
Ever wonder why there's so much fuss about quality control in pet food production?
Quality control in pet food production ensures that every product is safe, nutritious, and consistent. It involves rigorous testing, adherence to safety standards, and continuous monitoring to prevent contamination and maintain brand trust.
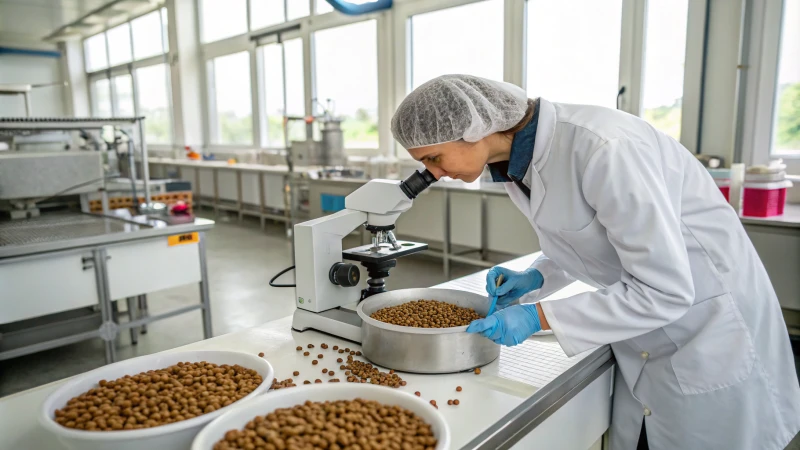
Ensuring Safety and Compliance
I still remember the time when my neighbor's dog fell sick because of contaminated pet food. The panic and worry in her eyes were palpable, and it drove home the importance of safety in the food we give our furry companions. That's why pet food manufacturers must comply with rigorous safety standards and regulations. These measures are there to prevent contamination and ensure pet foods are safe for consumption. Quality control processes include testing for harmful pathogens like Salmonella and toxins such as aflatoxins. By sticking to these safety standards12, companies can avoid recalls and protect our beloved pets from harm.
Maintaining Nutritional Consistency
There's something reassuring about pouring out the same high-quality kibble day after day, knowing it's packed with the right nutrients. As a pet owner, I expect consistency in the nutritional content of the foods I purchase. Quality control systems are key here—they ensure each batch meets the specified nutritional requirements. This involves routine analysis of ingredients and final products to verify their composition. Not only does consistent nutrition keep pets healthy, but it also builds my trust in a brand's reliability.
Protecting Brand Reputation
Imagine a single batch of contaminated pet food reaching the shelves—it could spell disaster for a brand's reputation. I've seen companies face massive backlash due to such slip-ups. But with robust quality control in place, these risks are significantly reduced. Companies often utilize advanced technologies like automated inspection systems13 to catch discrepancies early in the production process, ensuring only safe and high-quality products make it to market.
Enhancing Traceability and Transparency
There's a growing demand for transparency, and rightly so. By incorporating traceability measures into quality control, manufacturers can track ingredients from source to finished product. This transparency is crucial for swiftly addressing any quality issues. It also reassures consumers—like me—that they are feeding their pets responsibly sourced and produced food.
Utilizing Advanced Technologies
I'm always fascinated by how modern technology is revolutionizing industries, and pet food production is no exception. From employing AI for predictive analytics to using IoT devices for real-time monitoring, technology significantly boosts accuracy and efficiency in quality control. Companies that invest in these innovations often gain a competitive edge14 in the industry.
Quality Control Aspect | Purpose | Benefit |
---|---|---|
Safety Testing | Ensures product safety | Prevents contamination risks |
Nutritional Analysis | Verifies nutritional consistency | Builds consumer trust |
Automated Inspection | Detects production discrepancies | Protects brand reputation |
Traceability Measures | Tracks ingredient sourcing | Enhances transparency |
Advanced Technology | Improves process efficiency | Provides competitive advantage |
Quality control prevents pet food contamination.True
Quality control involves testing for pathogens and harmful substances to ensure safety.
Nutritional consistency is not a focus in pet food production.False
Quality control ensures each batch meets nutritional requirements to maintain health.
How Does the Extrusion Process Differ for Various Pet Foods?
Ever wondered how that crunchy kibble or savory wet food makes it into your pet's bowl?
The extrusion process varies by pet food type due to differences in ingredient composition, moisture levels, and desired texture. Dry foods undergo high-temperature extrusion, while wet foods may use lower temperatures with preconditioning steps.
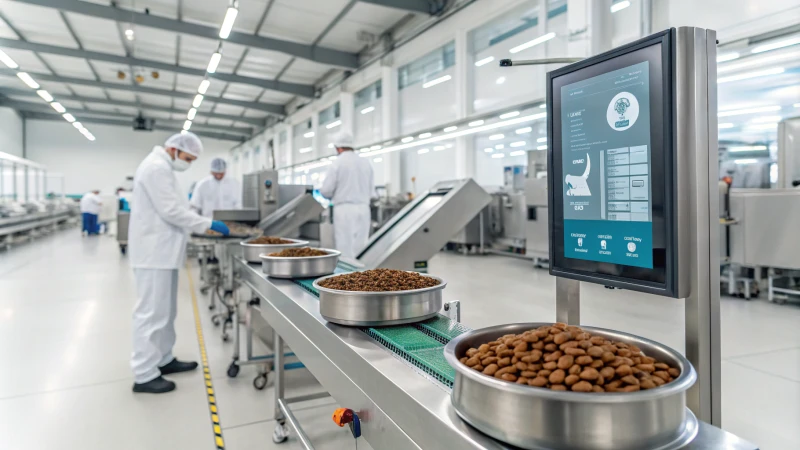
Understanding the Basics of Extrusion
Let's talk about one of the most fascinating yet complex aspects of pet food manufacturing: extrusion. This manufacturing process15 is like baking, except on an industrial scale. Imagine pushing ingredients through a giant pasta maker, shaping them under intense pressure and heat to create that perfect bite your pet loves.
Different types of pet foods, such as dry kibble and wet or semi-moist foods, require distinct extrusion techniques. The differences come down to their unique ingredient and moisture profiles, which I find utterly intriguing. Imagine trying to make bread and stew with the same cooking method—it just wouldn't work!
Dry vs. Wet Food Extrusion
Pet Food Type | Temperature Range | Key Ingredient Characteristics | Moisture Levels |
---|---|---|---|
Dry Kibble | 150-200°C | High in carbohydrates | 10% or less |
Wet Food | 90-120°C | Higher protein and fat | 60-80% |
Dry Kibble Extrusion
For dry kibble, high temperatures ranging from 150 to 200°C are used. This heat not only puffs up carbohydrates, giving kibble its irresistible crunch, but also acts like a safety net, eliminating any unwanted bacteria. It reminds me of baking cookies at home—just that satisfying crunch with every bite!
High-starch ingredients, like cereals, are the star players here because they expand beautifully during cooking. Plus, with such low moisture content, the final product can last on shelves for ages without losing quality.
Wet and Semi-Moist Food Extrusion
Now, wet and semi-moist foods take a gentler approach. They’re extruded at lower temperatures (90-120°C), preserving the rich flavors and the integrity of proteins. It's almost like simmering a stew to keep those juices flowing. Sometimes we even precondition these ingredients with extra moisture—keeping them juicy and delectable.
These products rely heavily on meats and fats, so without proper techniques, they could spoil faster than you can say "dinner time!"
The Role of Ingredient Composition
The composition of ingredients is like the secret recipe for determining the perfect extrusion settings. For instance, handling high-fat content16 can be tricky; it’s all about finding that sweet spot in temperature and pressure to prevent oil from separating.
Technological Innovations
Thanks to technological advances, we've got some pretty nifty tools to handle these diverse formulations. Customizable production lines now allow us to tweak temperature, pressure, and moisture content to perfection for each type of product.
These innovations have opened doors to niche markets, like grain-free diets17, which need special attention due to their distinct ingredient profiles. It’s like having a custom kitchen designed just for your pet’s dietary needs!
Every day in this industry feels like a new adventure with exciting challenges and rewarding outcomes. It’s not just about making pet food; it’s about crafting meals that pets will thrive on.
Dry kibble extrusion uses temperatures over 150°C.True
Dry kibble extrusion requires high temperatures, typically 150-200°C.
Wet food extrusion involves high moisture levels of 10%.False
Wet food extrusion involves moisture levels between 60-80%, not 10%.
What Are the Latest Innovations in Pet Food Extrusion Technology?
Ever wondered how your pet's food gets that perfect crunch or chewy texture?
Recent innovations in pet food extrusion technology include advanced twin-screw extruders, customized die designs for unique shapes, and enhanced automation for precision control. These developments ensure better nutritional profiles, unique textures, and increased production efficiency.
Advanced Twin-Screw Extruders
I remember the first time I saw a twin-screw extruder in action. The precision and control it offered were nothing short of mesmerizing. It allowed for complex ingredient mixtures that I could never have imagined possible before. With these machines, I can process diverse recipes, enhancing the nutritional value of the final product. This flexibility ensures that the food I produce not only meets but exceeds nutritional standards. Learn more about greater flexibility18
Benefits:
- Enhanced mixing capabilities
- Improved nutrient retention
- Versatility in ingredient processing
Feature | Benefit |
---|---|
Flexibility | Diverse recipe processing |
Efficiency | Faster production times |
Customized Die Designs
One of my favorite parts of this journey has been witnessing how innovative die designs transform simple ingredients into playful shapes that pets adore. It's like crafting art, where each piece is unique yet equally nutritious. Customized dies are not just about aesthetics; they help me maintain the quality and integrity of the food while allowing brands to stand out in a crowded market. Explore specific consumer preferences19
Key Innovations:
- Unique shape creation
- Texture enhancement
- Brand differentiation opportunities
Enhanced Automation Systems
Automation has been a game changer for me. The ability to monitor production in real-time and make precision adjustments has significantly reduced waste and operational costs. I can now ensure that every batch of pet food meets the highest quality standards, consistently and efficiently. It's like having a reliable assistant who never tires, always ready to optimize production processes. Discover more about adjustments20
Automation Features:
- Real-time monitoring
- Precision adjustments
- Reduced operational costs
Future Trends in Pet Food Extrusion
As I look ahead, the future of pet food extrusion is exciting. Consumers are increasingly seeking tailored nutrition for their pets, pushing us to innovate further. Imagine personalized pet diets crafted with specific nutrient profiles or eco-friendly production methods paving the way for a more sustainable future. Integrating AI could soon offer predictive analytics, helping me fine-tune production like never before. Staying informed on these advancements21 is crucial to remaining competitive and meeting evolving consumer expectations.
Technology | Impact |
---|---|
AI Integration | Predictive analytics |
Sustainability | Eco-friendly production |
Twin-screw extruders offer enhanced mixing capabilities.True
Twin-screw extruders improve mixing, allowing complex ingredient combinations.
Customized dies reduce the nutritional value of pet food.False
Customized dies maintain nutritional integrity while creating unique shapes.
Conclusion
The pet food extrusion process combines raw ingredients, high heat, and pressure to create nutritious kibble, ensuring safety, consistency, and appealing textures for pets.
Learn about common vitamin supplements used in pet food production to ensure balanced nutrition. ↩
Explore how extruders shape pet food into various forms for different dietary needs. ↩
Discover how adding probiotics can enhance pet health by supporting digestion. ↩
Find out why rigorous quality control is essential for ensuring safe, nutritious pet food. ↩
Explore the effects of extrusion on different nutrients in pet food, focusing on retention rates and potential improvements. ↩
Learn how extrusion can enhance protein digestibility in pet food, improving nutritional absorption for pets. ↩
Discover innovative techniques that aim to preserve nutritional integrity while utilizing extrusion. ↩
Explore how pre-conditioners prepare ingredients for extrusion by mixing and hydrating them, improving texture. ↩
Discover different extruder types and their applications in pet food production, aiding in selecting suitable machinery. ↩
Understand advancements in drying technology that improve efficiency and product quality in pet food manufacturing. ↩
Learn about innovative coating techniques that enhance flavor and nutrition in pet foods. ↩
Understanding these standards ensures products meet safety guidelines, avoiding recalls and protecting pets. ↩
Learn how these systems enhance product quality by detecting discrepancies early in production. ↩
Discover how technological advancements can improve efficiency and ensure product quality. ↩
Learn how extrusion shapes pet food manufacturing by exploring technical details of the process. ↩
Discover how high-fat ingredients affect the extrusion process and what adjustments are necessary. ↩
Find out how grain-free diets are processed differently due to their unique formulations. ↩
Learn how twin-screw extruders improve ingredient processing, enhancing nutritional value in pet food. ↩
Explore how customized dies create unique shapes and textures, helping brands stand out. ↩
Discover how automation systems improve precision and efficiency through real-time data monitoring. ↩
Stay updated on future trends and innovations shaping pet food manufacturing. ↩